煤直接液化反应机理
煤直接液化概述

4.煤直接液化工业化
21世纪
神华煤直接液化项目
4.煤直接液化工业化
中国
神华煤直接 液化工艺
500万
2018~至今
——
——
>60
5.煤直接液化前景
[1]韩来喜.煤直接液化工业示范装置运行情况及前景 分析[J].石油炼制与化工,2011,42(08):47-51.
5.煤直接液化前景
谢 谢
煤直接液化(DCL)
汇报人:xie
化工学院
主要内容
1.煤-石油化学基础 2.煤直接液化基本原理
3.煤直接液化工艺 4.煤直接液化工业化 5.煤直接液化前景
1.煤-石油化学基础
原因:①我国总的能源特征是“富煤、贫油、少气”,
煤炭在我国石化能源总储量中居于首位,高达90%, 而石油和天然气储量总共不到10%。②促进煤炭产业 转型,实现煤炭清洁高效利用。
3.煤直接液化工艺
4 个主要工艺单元:
① 煤浆制备单元。将煤破碎至 0. 15 mm 以下,与溶剂、催
化剂制备成均匀的油煤浆。
② 反应单元。高温高压条件下在反应器内进行煤直接加氢反 应生成液体物。 ③ 分离单元。分离出加氢液化反应生成的气体、液化油和固 体残渣。
④ 提质加工单元。对液化油进行加氢精制,进行芳环饱和和
煤:高等植物在泥炭沼泽中持续生长和死亡,其残
骸不断堆积,经过长期而复杂的生物化学和物理化
学作用,逐步演化成泥炭、褐煤、烟煤和无烟煤。 由植物转化为煤要经历复杂而漫长的过程。一般需 要几千万年到几亿年的时间,整个成煤作用过程可 分为两个阶段,即由植物残骸转变为泥炭的泥炭化 作用阶段和泥炭转变为褐煤,烟煤,无烟煤的煤化 作用阶段。
2.煤直接液化基本原理
煤制油工艺
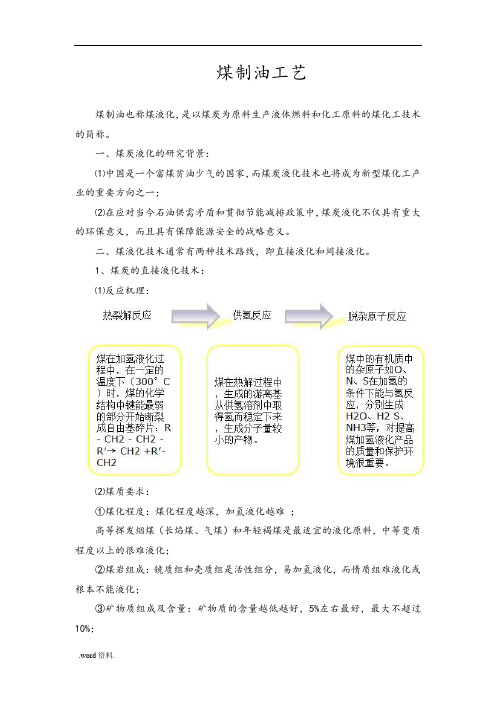
煤制油工艺煤制油也称煤液化,是以煤炭为原料生产液体燃料和化工原料的煤化工技术的简称。
一、煤炭液化的研究背景:⑴中国是一个富煤贫油少气的国家,而煤炭液化技术也将成为新型煤化工产业的重要方向之一;⑵在应对当今石油供需矛盾和贯彻节能减排政策中,煤炭液化不仅具有重大的环保意义,而且具有保障能源安全的战略意义。
二、煤液化技术通常有两种技术路线,即直接液化和间接液化。
1、煤炭的直接液化技术:⑴反应机理:⑵煤质要求:①煤化程度:煤化程度越深,加氢液化越难;高等挥发烟煤(长焰煤、气煤)和年轻褐煤是最适宜的液化原料,中等变质程度以上的很难液化;②煤岩组成:镜质组和壳质组是活性组分,易加氢液化,而惰质组难液化或根本不能液化;③矿物质组成及含量:矿物质的含量越低越好,5%左右最好,最大不超过10%;⑶催化剂的选择:①钴(Co)、钼(Mo)、镍(Ni):这类催化剂的催化活性较高。
但是这类金属催化剂的价格比较昂贵而且丢弃对污染比较严重,因此用后要回收;②金属卤化物:如ZnCl2、SnCl2等,属酸性催化剂,裂解能力强,但是对煤液化装置设备有较强的腐蚀作用;③铁系催化剂:包括含铁的天然矿石、含铁的工业残渣和各种纯态铁的化合物(如铁的氧化物、硫化物和氢氧化物)。
⑷供氢溶剂的作用:①提供和传递转移活性氢作用;②溶胀分散作用;③对煤粒热裂解生成的自由基起稳定保护作用;④溶解作用;⑤稀释液化产物作用。
⑸直接液化工艺:①德国IGOR工艺:该工艺以炼铝赤泥为催化剂,催化剂加入量为4%,不进行催化剂回收。
反应压力为30MPa,反应温度为465C。
现已完成0.2t/d和200t/d规模的试验研究。
采用减压蒸馏(即闪蒸)方法进行固一液分离,液化粗油不经降温而直接进行提质加工,将难以加氢的沥青质留在残渣中用作气化制氢的原料。
②日本NEDOL工艺:该工艺以黄铁矿为催化剂,催化剂加人量为4%,也不进行催化剂回收。
反应压力为19 MPa,反应温度为460℃。
浅析煤直接液化加氢反应影响因素
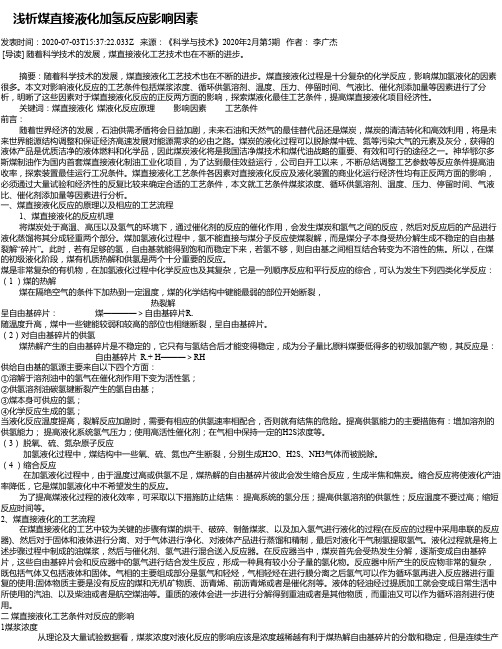
浅析煤直接液化加氢反应影响因素发表时间:2020-07-03T15:37:22.033Z 来源:《科学与技术》2020年2月第5期作者:李广杰[导读] 随着科学技术的发展,煤直接液化工艺技术也在不断的进步。
摘要:随着科学技术的发展,煤直接液化工艺技术也在不断的进步。
煤直接液化过程是十分复杂的化学反应,影响煤加氢液化的因素很多。
本文对影响液化反应的工艺条件包括煤浆浓度、循环供氢溶剂、温度、压力、停留时间、气液比、催化剂添加量等因素进行了分析,明晰了这些因素对于煤直接液化反应的正反两方面的影响,探索煤液化最佳工艺条件,提高煤直接液化项目经济性。
关键词:煤直接液化煤液化反应原理影响因素工艺条件前言:随着世界经济的发展,石油供需矛盾将会日益加剧,未来石油和天然气的最佳替代品还是煤炭,煤炭的清洁转化和高效利用,将是未来世界能源结构调整和保证经济高速发展对能源需求的必由之路。
煤炭的液化过程可以脱除煤中硫、氮等污染大气的元素及灰分,获得的液体产品是优质洁净的液体燃料和化学品,因此煤炭液化将是我国洁净煤技术和煤代油战略的重要、有效和可行的途径之一。
神华鄂尔多斯煤制油作为国内首套煤直接液化制油工业化项目,为了达到最佳效益运行,公司自开工以来,不断总结调整工艺参数等反应条件提高油收率,探索装置最佳运行工况条件。
煤直接液化工艺条件各因素对直接液化反应及液化装置的商业化运行经济性均有正反两方面的影响,必须通过大量试验和经济性的反复比较来确定合适的工艺条件,本文就工艺条件煤浆浓度、循环供氢溶剂、温度、压力、停留时间、气液比、催化剂添加量等因素进行分析。
一、煤直接液化反应的原理以及相应的工艺流程1、煤直接液化的反应机理将煤炭处于高温、高压以及氢气的环境下,通过催化剂的反应的催化作用,会发生煤炭和氢气之间的反应,然后对反应后的产品进行液化蒸馏将其分成轻重两个部分。
煤加氢液化过程中,氢不能直接与煤分子反应使煤裂解,而是煤分子本身受热分解生成不稳定的自由基裂解“碎片”。
煤的直接加氢液化技术

自由基碎片加氢(一)
可用如下方程式表示加氢反应
R-CH2-CH2-R’→ RCH2·+R’CH2· RCH2·+R’CH2·+2H·→ RCH3+R’CH3
煤加氢液化过程包括一系列的顺序反应和平行反 应,但以顺序反应为主,每一级反应的分子量 逐级降低,结构从复杂到简单,杂原子含量逐 级减少,H/C原子比逐级上升。
直接液化工艺流程简图
催
化
剂
H2
煤煤
反
浆
应
分
提
离
质
循环溶剂
残渣
汽油 柴油
其它
工艺过程
该工艺是把煤先磨成粉,再和自身组的部分液 化油(循环制剂)配成煤浆,在高温(450oC) 和高压(20—30MPa)下直接加氢,获得液化油, 然后再经过提质加工,得到汽油柴油等产品.1t 无水无灰煤可产500—600Kg油,加上制氢用 煤,约3—4t原料煤产1t油。
催化剂作用
催化剂的作用是吸附气体中的氢分子,并将其 活化成活性氢以便被煤的自由基碎片接受。一 般选用铁系催化剂或镍、钼和钴类催化剂。硫 是煤直接液化的助催化剂,有些煤本身含有较 高的硫,可少加或不加助催化剂。
催化剂的影响
催化剂是煤直接液化过程的核心技术 优良的催化剂可以降低煤液化温度,减少副
煤的直接加氢液化技术
煤直接液化反应机理
把固体煤转化为液体油,就必须采用增加温 度或其他化学方法以打碎煤的分子结构,使大 分子物质变成小分子物质,同时外界要供给足 够量的氢,提高其H/C原子比。
煤直接液化反应比较复杂,大致可分为热解、 氢转移、加氢三个反应步骤
氢源
煤在热解过程中外界不提供氢 煤在热解过程中外界不提供氢,煤热解
煤炭液化技术包括煤炭直接液化和煤炭间接液化

成绩中国矿业大学2011 级本科课程考试试卷考试科目学科前沿讲座考试时间2014年12月学生姓名彭玉斌学生学号06112931所在院系化工学院任课教师周敏教授等多名教师题目:煤炭液化技术煤炭液化技术摘要;煤炭液化技术包括煤炭直接液化和煤炭间接液化,是属于洁净煤技术的一种。
文章简要论述了煤炭直接接液化技术和煤炭间接液化技术的化学反应机理和化学反应过程;回顾了液化技术的发展历史,国外煤液化技术的发展状况;介绍了我国煤碳液化的现状;展望今后煤炭液化的发展方向。
关键字:煤炭;直接液化;间接液化所谓煤炭液化是指,固体煤炭通过化学加工过程,使其转化成为液体燃料、化工原料和产品的先进洁净煤技术。
根据不同的加工路线,煤炭液化可分为直接液化和间接液化两大类。
1煤炭直接液化概述煤与石油都是由碳、氢、氧为主的元素组成的天然有机矿物燃料。
只是煤中氢含量及H/C原子比,较石油相比要低很多。
要将煤转化为液体产物,必须在适当的温度、氢压、溶剂和催化剂的条件下,将煤中的大分子裂解为小分子,进而加氢稳定,降低H/C原子比,从而得到液体产物。
1.1煤直接液化的化学反应一般认为煤直接液化的过程是煤在溶剂、催化剂和高压氢气存在下,随着温度的升高,煤开始在溶剂中膨胀形成胶体体系。
煤进行局部溶解,并发生煤有机质的分裂、解聚,同时在煤有机质与溶剂间进行氢分配,于350~400℃左右生成沥青质含量较高的高分子物质。
在此过程中主要发生煤的热解、自由基加氢稳定、自由基缩合以及氮、氧、硫元素杂元素的脱除等一系列反应。
其主要反应是自由基的生成和加氢稳定。
自由基稳定后可生成分子量小的馏分油,分子量大的沥青烯,及分子量更大前沥青烯。
前沥青烯可进一步分解为分子量较小的沥青烯、馏分油和烃类气体。
同样沥青烯通过加氢可进一步生成馏分油和烃类气体。
如果煤的自由基得不到氢而它的浓度又很大时,这些自由基碎片就会互相结合而生成分子量更大的化合物甚至生成焦炭。
图1表示了煤热解产生自由基以及溶剂向自由基供氢、溶剂和前沥青烯、沥青烯加氢的过程:1.2煤直接液化技术的发展历程煤直接加氢液化一般是在较高温度,高压,氢气(或CO+H2, CO+H2O)、催化剂和溶剂作用下,将煤进行解聚、裂解加氢,直接转化为液体油的加工过程。
煤直接液化机理与动力学

煤直接液化机理与动力学contents •煤直接液化概述•煤直接液化机理•煤直接液化工艺流程•煤直接液化动力学模型•煤直接液化技术发展现状与趋势•研究展望与未来发展目录0102这一过程主要包含四个步骤:煤的破碎和干燥、氢气和催化剂的混合、高温高压下的反应以及产物的分离和提纯。
煤直接液化是一种将煤在氢气和催化剂的作用下,通过高温高压反应转化为液体燃料的过程。
煤直接液化技术的研究始于20世纪初,德国率先进行了研究和开发。
在随后的几十年中,这项技术在日本、美国、加拿大等国家得到了广泛的研究和应用。
中国也从20世纪80年代开始进行了煤直接液化的研究和开发,并成功建成了多套工业规模的煤直接液化装置。
1 2 3煤直接液化是一种将煤炭资源转化为液体燃料的有效途径,对于解决我国的能源安全问题具有重要意义。
与传统的煤炭燃烧方式相比,煤直接液化可以更有效地利用煤炭资源,减少环境污染,并且具有更高的能源利用效率。
同时,煤直接液化还可以生产出多种高附加值的化学品和燃料,进一步拓展了煤炭资源的利用途径。
煤直接液化的重要性煤的化学结构与性质煤是由多种有机化合物组成的复杂混合物,具有高分子量、多官能团和三维交联结构等特点。
煤的性质取决于其化学结构、分子量和官能团含量等因素,这些因素又受到煤的成因、变质程度和沉积环境等因素的影响。
煤在溶剂中溶解的过程是煤中有机物质向溶剂中扩散和溶解的过程,其溶解度受到溶剂的性质、温度和压力等因素的影响。
热解是煤在高温下裂解的过程,主要分为低温热解和高温热解两种。
低温热解主要发生在较低的温度下,主要生成液态产物;高温热解主要发生在较高的温度下,主要生成气态产物。
煤在溶剂中的溶解与热解氢供体与催化剂的作用氢供体是煤直接液化过程中的重要组分,主要提供氢原子以促进煤中有机物质的加氢反应。
催化剂是加速煤直接液化反应速度和提高液化油收率的的关键因素,主要分为酸性催化剂、金属催化剂和金属氧化物催化剂等。
煤直接液化工艺的原料是煤炭,需要确保煤炭的来源和品质符合要求,并进行必要的破碎、磨细等预处理。
煤直接液化基础

褐煤油收率低, 重油多
3.5 煤种液化特性评价方法
液化产物-固液分离
3.5 煤种液化特性评价方法
液化产物-气体
杂原子气体:H2O, H2S, NH3, CO2, CO 气态烃: C1-C4 气体分析: GC (气相色谱)
实验结果计算
♫ 转化率:固体煤转化为气、液体的百分数
固
油
体
、
燃
汽
料
油
、
等
重
发
质
动
燃
机
脱 灰 、 脱 硫
化 工 原 料
料
燃
油
料
3.1.2 煤直接液化的可能性
☻ 煤和石油的差别
化学组成:H/C比(煤 0.2~1,石油 1.6~2.0),N、
S、O含量,无机矿物质
分子结构:烷烃、环烷烃(石油),芳香烃(煤)
☻ 煤和石油的相似性
都是由C、H元素组成
大分子 小分子 断键
0.1t/d小型连续实验装置工艺过程
3.7 煤直接液化催化剂
3.7.1 概述
1)催化剂定义
催化剂: 能改变化学反应速度, 而本身在反应前后变化不大的物质 。
H2 + O2 200oC,No cat.,不反应,少量Cu,立刻有水产生。但上述 表述不完善
如:
PdCl2-CuCl2 C2H4 + 1/2 O2 常压, 270oC
在供氢溶剂四氢萘中, Fe(CO)5进一步提高煤的转化率及油的产率。 ③用X光衍射检查液化残渣,没有S时,Fe(CO)5转化为Fe3O4;加入S时
Fe(CO)5转化为Fe1-xS(磁黄铁矿,催化活性物种、非化学剂量的铁硫 化合物)。
煤的直接液化

4、操作条件 温度和压力是影响煤直接液化反应进行的 两个因素,也是直接液化工艺两个最重要 的操作条件。 煤的液化反应是在一定温度下进行的,不 同工艺的所采用的温度大体相同,一般为 440~460º C。当温度超过450º C时,煤转化 率和油产率增加较少,而气产率增多,因 此会增加氢气的消耗量,不利于液化。
2、直接液化的溶剂 在煤液化过程中,溶剂起着溶解煤、溶 解气相氢向煤或催化剂表面扩散、供氢或 传递氢、防止煤热解的自由基碎片缩聚等 作用。 煤的直接液化必须有溶剂存在,这也是 与加氢热解的根本区别。 通常认为在煤的直接液化过程中,溶 剂能起到如下作用:
a)将煤与溶剂制成浆液的形式便于工艺过程 的输送。同时溶剂可以有效地分散煤粒、 催化剂和液化反应生成的热产物,有利于 改善多相催化液化反应体系的动力学过程。 b)依靠溶剂能力使煤颗粒发生溶胀和软化, 使其有机质中的键发生断裂。 c) 溶解部分氢气,作为反应体系中活性氢的 传递介质;或者通过供氢溶剂的脱氢反应 过程,可以提供煤液化需要的活性氢原子。
d)在有催化剂时,促使催化剂分散和萃取出 在催化剂表面上强吸附的毒物。 在煤液化工艺中,通常采用煤直接液化后 的重质油作为溶剂,且循环使用,因此又 称为循环溶剂。
3、催化剂 选用合适的催化剂对煤的直接液化至关重要, 一直是技术开发的热点之一,也是控制工艺成 本的重要因素。 催化剂的作用机理,有两种观点:(1)催化剂 的作用是吸附气体中的氢分子,并将其活化成 为易被煤的自由基团接受的活性氢;(2)催化 剂是使煤中的桥键断裂和芳环加氢的活性提高, 或是使溶剂加氢生成可向煤转移氢的供氢体等。
对压力而言,理论上压力越高对反应越有 利,但这样会增加系统的技术难度和危 险性,降低生产的经济性,因此,新的 生产工艺都在努力降低压力条件。 早期液化反应(如德国工艺)压力 高达 30~70MPa ,目前常用的反应压力 已经降到了 17~25MPa ,大大减少了设 备投资和操作费用。
- 1、下载文档前请自行甄别文档内容的完整性,平台不提供额外的编辑、内容补充、找答案等附加服务。
- 2、"仅部分预览"的文档,不可在线预览部分如存在完整性等问题,可反馈申请退款(可完整预览的文档不适用该条件!)。
- 3、如文档侵犯您的权益,请联系客服反馈,我们会尽快为您处理(人工客服工作时间:9:00-18:30)。
煤直接液化反应机理
煤和石油主要都是由C、H、O等元素组成,不同的是:煤的氢含量和H/C 原子比比石油低,氧含量比石油高;煤的分子量大,一般大于5000,而石油约为200,汽油约为110;煤的化学结构复杂,一般认为煤有机质是具有不规则构造的空间聚合体,它的基本结构单元是缩合芳环为主体的带有侧链和官能团的大分子,而石油则为烷烃、环烷烃和芳烃的混合物。
煤还含有相当数量的以细分散组分的形式存在的无机矿物质和吸附水,煤也含有数量不定的杂原子(氧、氮、硫)、碱金属和微量元素。
要把固体煤转化为液体油,就必须采用增加温度或其他化学方法以打碎煤的分子结构,使大分子物质变成小分子物质,同时外界要供给足够量的氢,提高其H/C原子比。
煤直接液化反应比较复杂,大致可分为热解、氢转移、加氢三个反应步骤, 如果煤在热解过程中外界不提供氢,煤热解产生的自由基碎片只能靠自身的氢再分配,使少量的自由基碎片形成低分子油和气,而大量的自由基碎片则发生缩聚反应生成固体焦。
如果煤在热解过程中外界供给氢,而且煤热解产生的自由基碎片与周围的氢结合成稳定的H/C原子比较高的低分子物(油和气),这样就能抑制缩聚反应,使煤全部或绝大部分转化成油和气。
一次加氢液化的实质是用高温切断化学结构中的C-C键,在断裂处用氢来饱和,从而使分子量减少和H/C原子比提高。
反应温度要控制合适,温度太低,不能打碎煤分子结构或打碎的太少,油产率低。
一般液化工艺的温度为400℃~470℃[4]。
与煤自由基碎片结合的氢必须是活化氢。
活化氢的来源:(1)煤分子中的氢再分配;(2)供氢溶剂提供;(3)氢气中的氢分子被催化活化;(4)化学反应放出氢,如系统中供给CO+H2O,则发生变换反应(CO+H2O→CO2+H2)放出氢。
据研究证明:系统中供CO+H2O或CO+H2的液化效果比单纯供H2的效果好,这主要是CO+H2O的变化反应放出的氢容易与煤的自由基碎片结合。
为保证系统中有一定的氢浓度,使氢容易与碎片结合,必须有一定的压力(氢分压)。
目前的液化工艺的一般压力为5MPa~30MPa。
对自由基碎片的加氢是液化反应的关键,可用如下方程式表示加氢反应[5]
R-CH2-CH2-R’→ RCH2·+R’CH2·
RCH2·+R’CH2·+2H·→ RCH3+R’CH3
煤加氢液化过程包括一系列的顺序反应和平行反应,但以顺序反应为主,每一级反应的分子量逐级降低,结构从复杂到简单,杂原子含量逐级减少,H/C原子比逐级上升。
在发生顺序反应的同时,又伴随有副反应,即结焦反应的发生。
煤加氢液化反应历程如图1-2所示。
从沥青烯向油和气的转化是一个相当缓慢的过程,是整个反应的控制步骤。
煤焦
C1 自由基碎片前沥青烯沥青烯液化油和气体
煤C2
C3基本不反应
C1为有机质的主体;C2为存在于煤中的低分子化合物;C3为惰性组分
图1-2 煤炭直接液化反应机理图
催化剂的影响
循环油是主要的供氢载体,催化剂的功能是促进溶于液相中的氢与脱氢循环油间的反应,使脱氢循环油加氢并再生。
在直接液化过程中,煤的大分子结构首先受热分解,而使煤分解成以结构单元缩合芳烃为单个分子的独立的自由基碎片。
在高压氢气和催化剂存在下,这些自由基碎片又被加氢,形成稳定的低分子物。
自由基碎片加氢稳定后的液态物质可分成油类、沥青烯和前沥青烯等三种不同成分,对其继续加氢。
前沥青烯即转化成沥青烯,沥青烯又转化为油类物质。
油类物质再继续加氢,脱除其中的氧、氮和硫等杂原子,即转化为成品油。
成品油经蒸馏。
按沸点范围不同可分为汽油、航空煤油和柴油等。
催化剂的作用是吸附气体中的氢分子,并将其活化成活性氢以便被煤的自由基碎片接受。
一般选用铁系催化剂或镍、钼和钴类催化剂。
硫是煤直接液化的助催化剂,有些煤本身含有较高的硫,可少加或不加助催化剂。
催化剂是煤直接液化过程的核心技术,在煤液化过程中起着非常重要的作用。
优良的催化剂可以降低煤液化温度,减少副反应并降低能耗,提高氢转移效率,增加液体产物的收率。
在用于煤液化工艺的各种催化剂中,铁基催化剂以其高效、廉价及低污染而倍受青睐。
专利技术集中在改善铁基催化剂的性能、开发新型高效的催化剂、催化剂制备工艺改进和催化剂的预处理等。
煤炭直接液化中使用的催化剂通常有三大类第一类是钴(Co)、钼(Mo)、镍(Ni)催化剂,这类催化剂催化活性较高,但这类金属催化剂价格比较昂贵而且丢弃对环境污染比较严重,因此用后需要回收第二类是金属卤化物催化剂如等属酸性催化剂。
如ZnCl2、SnCl2等,属酸性催化剂,裂解能力强,但对煤液化装置的设备有较强的腐蚀作用。
第三类是铁系催化剂,包括含铁的天然矿石、含铁的工业残渣和各种纯态铁的化合物(如铁的氧化物、硫化物和氢氧化物)[18]。
催化剂活性、价格比高。
进入灰渣对环境没有污染是目前煤炭直接液化催化剂研究的重点和方向。
铁系催化剂中天然含铁矿石和工业含铁残渣的催化活性受自身物质性质的影响较大,这方面的研究工作主要集中在寻找高活性的含铁天然矿物和含铁工业废渣上。
这类催化剂存在的问题是添加量较大增加了残渣的处理和影响了液化油的收率。
煤直接液化高效催化剂活性组分以其纳米级的颗粒均匀地分布在煤粒表面最大限度地发挥其催化活性,因而其用量只是常规催化剂的1/4。
煤液化油收率可高出常规铁系催化剂5个百分点左右,其经济效益十分明显。
神华集团决定在其煤直接液化示范工程第一条示范生产线中采用高效催化剂。
目前已将高效催化剂工业化生产装置纳入全厂的总图设计之中并正在进行工程设计工作。
该成果要得到工程化应用,需要进一步解决工程化放大过程中的一些关键技术和设备问题主要是煤直接液化高效催化剂反应器。
该成果的经济效益和社会效益与煤炭直接液化的产业化息息相关,煤炭直接液化一旦形成产业。
煤炭直接液化催化剂作为煤炭直接液化的关键技术,成果应用具有广阔的市场并产生显著的经济效益。
煤直接液化催化剂的研究和开发是降低液化成本、提高液化油收率的关键技术之一。
具有自主知识产权的煤直接液化高效催化剂研发成功,并将在未来的直接液化工程中得到应用。
这将极大地推动我国煤直接液化技术的发展,为该技术的工程化实施莫定良好的基础。
溶剂的影响
在煤的直接液化工艺中,用到的溶剂的作用有:1、一般溶剂的作用:在煤炭液化过程中,溶剂作为一种介质,具备以下几种作用:(1)溶解作用;(2)溶胀分散作用;(3)对煤粒热裂解生成的自由基起稳定保护作用;(4) 提供和传递转移活性氢作用;(5)对液化产物起烯释作用;2、溶剂的供氢作用;3、溶剂的传递氢作用。
常见的溶剂有:四氢萘、萘、蒽、菲、甲酚、萘酚等;煤焦油和石油渣油等重质油作溶剂;废塑料和废橡胶及废油脂作溶剂。
[19]
溶剂在煤液化反应过程中起非常重要的作用,它可以溶解溶胀、烯释分散煤粒,使气、液、固三相反应系统处于一个相对均匀的体系。
这对于煤的热裂解反应,煤的热裂解生成的自由基的保护作用,自由基碎片的加氢反应以及抑制煤液化的副反应——缩聚反应都起着积极的作用。
进一步研究煤液化过程中溶剂的作用,尤其是混合溶剂的作用,必定会对研究煤液化机理,进而促进提高煤液化转化率产生积极的作用。
当前,国内外对煤直接液化产物再次液化的研究较少,而产物中的沥青烯和前沥青烯含量较多,如果利用此产物再次液化。
将会大大提高油的产率,实验中使用储氢物质与其反应。