复合电镀工艺的简介
表面工程--复合电镀

BaSO4、SrSO4
Co
Al2O3、Cr2O3、Cr3C2、WC、TaC、BN、ZrB2、Cr3B2、金刚石
Fe
Al2O3、Fe2O3、SiC、WC、B、PTFE、MoS2
Cr
Al2O3、CeO2、ZrO2、TiO2、SiO2、UO2、SiC、WC、ZaB2、TiB2
Au
Al2O3、Y3O3、SiO2、TiO2、ThO2、CeO2、TiC、WC、Cr3B2、BN
Ag
Al2O3、TiO2、BeO、SiC、BN、MoS2、刚玉、石墨、La2O3
Zn
ZrO2、SiO2、TiO2、Cr2O3、SiC、TiC、Cr3C2、Al
Ni-Mn Al2O3、SiC、Cr3C2、BN
性质
复合电镀中某些基质金属的性质
Cr Fe Co Ni Cu Zn Ag Au
Pb
密度(g/cm3) 7.19 7.86 8.90 8.90 8.94 7.13 10.4 19.23 11.34 9
a. DC coating
b. f=50Hz,r=0.2
(SEM×1000)
Surface morphologies of RE-Ni-W-P-SiC coatings
a. DC coating
b. f=50Hz,r=0.4
(SEM×1000)
Surface morphologies of RE-Ni-W-P-SiC-MoS2 coatings
<3>镀液的性质要有利于固体粒子带正电荷,即利于粒 子吸附阳离子表面活性剂及金属离子。
<4>粒子的粒度要适当。粒子过粗,易于沉淀, 且不易被沉积金属包覆,镀层粗糙;粒子过 细,易于结团成块,不能均匀悬浮。通常使 用0.1~10um的粒子,但以0.5~3um最好。
化学复合镀技术综述

化学复合镀技术综述摘要:本文旨在介绍化学复合镀技术的现状及未来发展方向。
对其历史和发展进行了简要综述,重点介绍了其原理、步骤和正在发展的技术。
此外,本文还讨论了化学复合镀技术的优缺点,并提出了未来发展方向。
总之,化学复合镀技术具有优良的特性和广泛的应用前景,有望在未来拓展更广泛的应用领域。
化学复合镀技术已经成为电子工业中重要的表面处理技术。
它以一种严格的步骤以及复杂的试验过程来处理多种金属材料的表面。
它是一种可以在短时间内获得良好表面质量的技术。
化学复合镀技术是一种成熟的技术,已经在电子工业领域得到了广泛应用和投入使用。
本文将对这一技术的历史演进、原理、步骤以及发展趋势进行详细阐述。
一、关于化学复合镀技术的历史化学复合镀技术最早发源于20世纪50年代晚期,当时称为“多金属镀技术”。
随着科学技术的发展,这项技术在当今的应用领域中得到了广泛的运用,今天的化学复合镀技术已经发展到先进的水平,改善了多金属镀层的质量,大大提高了其精度和耐久性。
二、化学复合镀技术的原理化学复合镀技术是一种专门用于表面处理的技术,它用于处理各种金属材料的表面,主要使用氧化物、碳化物和薄膜等复合物来将金属材料与基体融合在一起,形成一种保护性链接。
它可以有效增强金属材料的表面硬度、耐磨性和耐腐蚀性,从而提高其加工精度和性能。
三、化学复合镀技术的步骤化学复合镀技术主要包括五个步骤:表面预处理、洗涤、清洗、喷涂和烘干。
首先,采用软钝处理去除材料表面的污渍和多余的金属物质;其次,用清水洗涤;然后采用碱洗涤去除油污;最后,在表面喷涂化学复合物,将化学复合物烘干,得到理想的表面形貌。
四、化学复合镀技术发展趋势随着科技的发展,化学复合镀技术日益兴起。
今天的化学复合镀技术可以提供更大的范围覆盖,包括钝化、光亮化、抗腐蚀处理、保护处理和形态调节等。
未来,这种技术将不断完善,以适应现代工业的需求,以期更广泛的应用。
五、化学复合镀技术的优缺点化学复合镀技术具有优点和缺点。
复合电镀技术

复合电镀技术
复合电镀技术是一种将两种或多种金属或非金属材料在同一种电解液中电镀到基材上的技术。
复合电镀技术不仅仅可以提高基材的表面性能,而且可以制备出具有特殊性能或者外观的复合材料。
该技术在电子、航空航天、汽车、船舶等众多领域都有广泛的应用。
复合电镀技术的主要原理是利用不同金属或非金属之间的电化学差异,将它们在同一电解液中同时电化学反应,并在基材表面上沉积出复合膜。
在此过程中,电解液中的金属离子被还原而沉积到基材表面上,从而形成了具有特殊性能的复合膜。
与传统单一金属电镀技术不同,复合电镀技术可以制备出不同金属之间或金属与非金属之间的复合膜。
这些复合膜具有比单一金属膜更高的硬度、耐磨性、耐腐蚀性、导电性、导热性、耐高温性等优异的性能。
同时,复合电镀技术还可以制备出具有特殊观感和色泽的复合膜,使得基材具有更高的价值和美观度。
在实际应用中,复合电镀技术的操作过程相对简单,但需要对材料的选择、电化学参数的控制、工艺流程的优化等方面进行充分的研究和优化。
此外,复合电镀技术也需要进行合理的后处理,以保证复合膜的质量和性能。
总的来说,复合电镀技术是一种具有广泛应用前景的表面处理技术,可以为各种领域的高科技产业提供高性能、高质量、高附加值的表面材料。
金刚石复合电镀
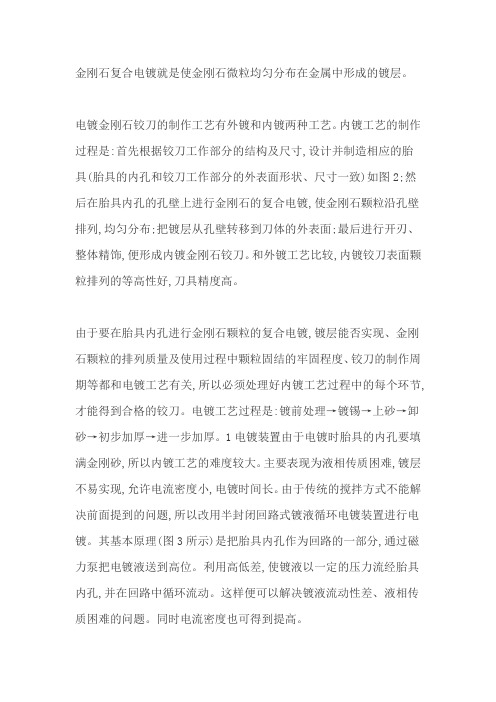
金刚石复合电镀就是使金刚石微粒均匀分布在金属中形成的镀层。
电镀金刚石铰刀的制作工艺有外镀和内镀两种工艺。
内镀工艺的制作过程是:首先根据铰刀工作部分的结构及尺寸,设计并制造相应的胎具(胎具的内孔和铰刀工作部分的外表面形状、尺寸一致)如图2;然后在胎具内孔的孔壁上进行金刚石的复合电镀,使金刚石颗粒沿孔壁排列,均匀分布;把镀层从孔壁转移到刀体的外表面;最后进行开刃、整体精饰,便形成内镀金刚石铰刀。
和外镀工艺比较,内镀铰刀表面颗粒排列的等高性好,刀具精度高。
由于要在胎具内孔进行金刚石颗粒的复合电镀,镀层能否实现、金刚石颗粒的排列质量及使用过程中颗粒固结的牢固程度、铰刀的制作周期等都和电镀工艺有关,所以必须处理好内镀工艺过程中的每个环节,才能得到合格的铰刀。
电镀工艺过程是:镀前处理→镀锡→上砂→卸砂→初步加厚→进一步加厚。
1电镀装置由于电镀时胎具的内孔要填满金刚砂,所以内镀工艺的难度较大。
主要表现为液相传质困难,镀层不易实现,允许电流密度小,电镀时间长。
由于传统的搅拌方式不能解决前面提到的问题,所以改用半封闭回路式镀液循环电镀装置进行电镀。
其基本原理(图3所示)是把胎具内孔作为回路的一部分,通过磁力泵把电镀液送到高位。
利用高低差,使镀液以一定的压力流经胎具内孔,并在回路中循环流动。
这样便可以解决镀液流动性差、液相传质困难的问题。
同时电流密度也可得到提高。
2.镀前处理镀前处理主要包括金刚石颗粒和胎具内孔表面的处理。
金刚石在电镀前如果不经过仔细的净化和亲水性处理,容易产生上砂困难或使颗粒与金属镀层结合力下降,造成铰刀使用过程中金刚石颗粒过早脱落。
具体处理方法如下:将NaOH和金刚石以重量为2∶1的比例放入坩埚中,在电炉上加热至680~700℃煮15min倒出冷却。
然后用蒸馏水冲洗至中性,之后,用15%稀硝酸煮沸约30min,冷却后用蒸馏水冲洗至中性。
然后浸泡在镀液中待用。
对胎具镀前处理的目的是除去表面污物和表面的不良组织,暴露出基体金属的正常晶格结构,便于在活化状态下金属晶体表面实现电沉积。
纳米复合电镀
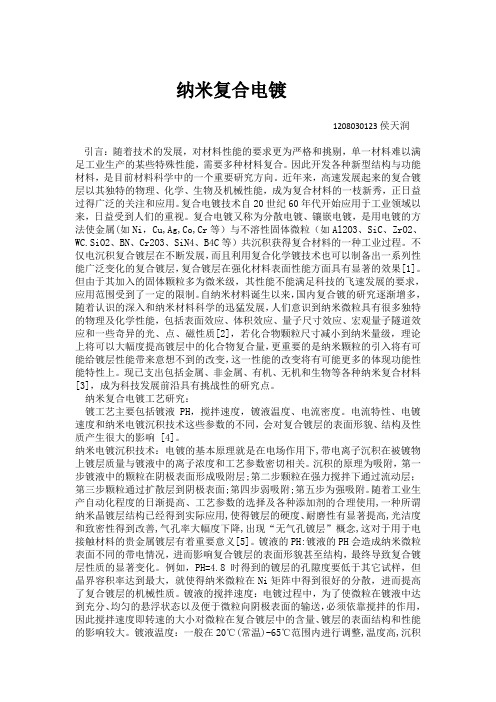
纳米复合电镀1208030123侯天润引言:随着技术的发展,对材料性能的要求更为严格和挑剔,单一材料难以满足工业生产的某些特殊性能,需要多种材料复合。
因此开发各种新型结构与功能材料,是目前材料科学中的一个重要研究方向。
近年来,高速发展起来的复合镀层以其独特的物理、化学、生物及机械性能,成为复合材料的一枝新秀,正日益过得广泛的关注和应用。
复合电镀技术自20世纪60年代开始应用于工业领域以来,日益受到人们的重视。
复合电镀又称为分散电镀、镶嵌电镀,是用电镀的方法使金属(如Ni,Cu,Ag,Co,Cr等)与不溶性固体微粒(如Al2O3、SiC、ZrO2、WC.SiO2、BN、Cr2O3、SiN4、B4C等)共沉积获得复合材料的一种工业过程。
不仅电沉积复合镀层在不断发展,而且利用复合化学镀技术也可以制备出一系列性能广泛变化的复合镀层,复合镀层在强化材料表面性能方面具有显著的效果[1]。
但由于其加入的固体颗粒多为微米级,其性能不能满足科技的飞速发展的要求,应用范围受到了一定的限制。
自纳米材料诞生以来,国内复合镀的研究逐渐增多,随着认识的深入和纳米材料科学的迅猛发展,人们意识到纳米微粒具有很多独特的物理及化学性能,包括表面效应、体积效应、量子尺寸效应、宏观量子隧道效应和一些奇异的光、点、磁性质[2],若化合物颗粒尺寸减小到纳米量级,理论上将可以大幅度提高镀层中的化合物复合量,更重要的是纳米颗粒的引入将有可能给镀层性能带来意想不到的改变,这一性能的改变将有可能更多的体现功能性能特性上。
现已支出包括金属、非金属、有机、无机和生物等各种纳米复合材料[3],成为科技发展前沿具有挑战性的研究点。
纳米复合电镀工艺研究:镀工艺主要包括镀液 PH,搅拌速度,镀液温度、电流密度。
电流特性、电镀速度和纳米电镀沉积技术这些参数的不同,会对复合镀层的表面形貌、结构及性质产生很大的影响 [4]。
纳米电镀沉积技术:电镀的基本原理就是在电场作用下,带电离子沉积在被镀物上镀层质量与镀液中的离子浓度和工艺参数密切相关。
表面工程复合电镀 PPT

Surface morphology of electrodes
(c) pulse Pb-WC-PANI composite electrode
表面工程复合电镀
与熔渗法,热挤压法,粉末冶金法相比,复合电 镀具有明显的优越性:
➢ <1>不需要高温即可获得复合镀层:用热加工法
一般需要500~1000℃或更高温度处理或烧结,
故很难制取含有有机物的材料,而复合电镀法大
多gt;操作简单,成本低:大多数情况可在一般电 镀设备、镀液、阳极、操作条件等基础上略加改 造(主要是增加使固体颗粒在镀液中充分悬浮的 措施等),就能用来制备复合镀层。
表面工程复合电镀
15
➢ <3>同一基质金属可以方便地镶嵌一种或 数种性质各异的固体颗粒,同一种固体颗 粒也可以方便地镶嵌到不同的基质金属中。 而且,改变固体颗粒与金属共沉积的条件, 可使颗粒在复合镀层中的含量从0~50%或 更高些的范围内变动,从而使镀层性质也 发生相应的变化。
Surface morphonogies of the coatings
Fig.1 Ni-W alloy
Fig.2 Ni-W-SiC composite coating
表面工程复合电镀
(a) Ni-W-P-B4C
(b) Ni-W-P-B4C-PTFE
(SEM×400)
表面工程复合电镀
Surface morphologies of Ni-W-P-SiC composite
a. DC coating
b. f=50Hz,r=0.2
(SEM×1000)
表面工程复合电镀
a. DC coating
b. f=50Hz,r=0.4
复合电镀(Ni-Fe)-金刚石工艺

会形 成溶 解 度较 小 的硫酸 镍铵 沉 淀 。
1 电镀镍一 合金工艺规范 铁
1 1 镀 液组 成及 工艺 条件 .
Ni O4 ・7H2 S O Ni 2 ・6H2 C1 O FS e O4 ・7H2 O 20g 0 /L 6 /L 0g 3 /L 0g
的阴极 电流 密度 。
N C6 O7・ 3 H6 2H2 O
H3 BO3 C6 COS 2 H4 O NH
3 /L 0g
4 /L 0g 3g /L
7 1光亮 剂 9
C1H2S Na 2 5 O4
3mL L /
0. /L 2g
0
pH
5 0~7 ℃ 0
复 合 电 镀 ( iF ) 金 刚 石 工 艺 N—e 一
王 敏
10 0 ) 120 ( 宁省 辽 中县辽 河化 工 厂 , 宁 辽 中 辽 辽
摘 要 : 介 绍 电镀 N — e 金镀 液 组成 、 艺条件 、 液及 镀层 性 能 的基 础上 , 述 了复合 电镀 ( i 在 iF 合 工 镀 叙 N—
F )金 刚石的镀液组成 、 e一 工艺条件、 工艺操作过程 、 方法及注意事项。用( i e 一 N— )金刚石复合 电镀 F
工 艺制 造金 刚石磨具 、 刃具 , 具有很 好 的 应 用前景 。
关 键 词 :复合 电镀 ;( iF ) 金 刚石 ; 刚石 ; N—e 一 金 ‘
中图分 类号 : Q13 T 5
上。
1 镀层 韧 性 好 。从 不 锈 钢 上 揭 下 的厚 度 为 l ) 1
m, 对折后用两指搓捻 , 不破不碎 ; 厚度为 8 0 镀层 对折 不断 。
第10讲 复合电镀-简介

1复合镀层的沉积机理
固体微粒先经过消除杂质、润湿处理和表面活 性剂处理后,加入镀液中,形成均匀的悬浮液 。
分散粒子会吸附表面活性剂和镀液中各种离子 ,包括将被沉积的金属离子。当微粒子表面净 吸附结果是正离子占优势时,即微粒子表面带 正电荷后,才有可能与金属离子共沉积形成复 合镀层。
在电镀法实施的复合镀过程中,共沉积大致经 历如下的步骤:
复合镀层的性能由镀层金 属的特性和粒子特性共同 决定。这里着重讨论由于 粒子性质不同,引起镀层 性能最明显变化的特点及 其应用。
耐磨性镀层
将硬质粒子加入到Ni,Co,Cr,Co-Ni,Ni-P, Ni-B等镀层中,可大幅度地提高金属或合金镀 层的耐磨性,例如 Ni-P-SiC的耐磨性随SiC含量 增加而迅速升高(即磨损量减少).
但在有些情况下,固体粒子却可提高镀层的耐蚀性。 例如在钢件上,用铝粉和锌共沉积形成Zn-AI复合镀层 ,Zn是阳极性镀层,Zn镀层中的AI粉表面包裹着氧化 膜,在腐蚀电池中仍为阴极,导电性差,故抑制了Zn 的腐蚀。
④微粒吸附的金属离子及未被吸附的金属离子 在阴极上放电沉积进入晶格,固体微粒子被沉 积金属埋没而镶嵌在镀层中,形成金属/固体 微粒复合镀层。微粒被沉积金属掩埋固定所需 时间愈短,微粒的共沉积量愈大。
2 复合镀的条件
要制备复合镀层,需满足下述基本条件: ①粒子在镀液中是充分稳定的,既不会发生任何
将剪切强度低。摩擦系数小的固体粒子加入到某 些金属和合金中,可形成具有自润滑功能的减摩 复合镀层。
常用Ni,Cu,Pb等作基体金属,用石墨, 氟化石墨,聚四氟乙烯(PTFE),MoS2和六 方氮化硼等作分散剂。
耐蚀复合镀层
通常,固体粒子加入镀层中形成复合镀,层,镀层的 孔隙率会明显增大。粒子量愈高,粒子愈粗,孔隙率 愈高。这就降低阴极性镀层的防护功能,耐蚀性降低 。
- 1、下载文档前请自行甄别文档内容的完整性,平台不提供额外的编辑、内容补充、找答案等附加服务。
- 2、"仅部分预览"的文档,不可在线预览部分如存在完整性等问题,可反馈申请退款(可完整预览的文档不适用该条件!)。
- 3、如文档侵犯您的权益,请联系客服反馈,我们会尽快为您处理(人工客服工作时间:9:00-18:30)。
复合电镀工艺的简介
现代电镀网讯:
1、复合电镀的发展历程及特点
复合电镀是20世纪20年代发展起来的一种新的电镀镀种,到1949年才出现了第一个专利,这就是美国人西蒙斯(Simos)利用金刚石与镍共沉积制作切削工具的金刚石复合镀技术。
此后复合镀获得各国电镀技术工作者的重视,研究和开发都十分活跃,发展到今天则成为电镀技术中一个非常重要的分支领域。
复合电镀的特点是以镀层为基体而将具有各种功能性的微粒共沉积到镀层中,来获得具有微粒特征功能的镀层。
根据所用微粒不同而分别有耐磨镀层、减摩镀层、高硬度切削镀层、荧光镀层、特种材料复合镀层、纳米复合镀层等。
几乎所有的镀种都可以用作复合镀层的基础镀液,包括单金属镀层和合金镀层。
但是常用的复合镀基础镀液多以镀镍为主,近来也有以镀锌和合金电镀为基础液的复合镀层用于实际生产。
复合微粒早期是以耐磨材料为主,比如碳化硅、氧化铝等,现在则发展为有多种功能的复合镀层。
特别是纳米概念出现以来,冠以纳米复合材料的复合镀层时有出现。
这正是复合镀层具有巨大潜力的表现。
2、复合电镀原理
复合电镀也叫包覆镀、镶嵌镀,是在金属镀层中包覆固体微粒而改善镀层性能的一种新工艺。
根据被包覆的固体微粒的性质,而制作出不同功能的复合镀层。
在研究复合电镀共沉积的过程中,人信曾提出3种共沉积机理,即机械共沉积、电泳共沉积和吸附共沉积。
目前较为公认的是由N.Guglielmi在1972年提出的两段吸附理论。
Guglielmi提出的模型认为,镀液中的微粒表面为离子所包围,到达阴极表面后,首先松散地吸附(弱吸附)于阴极表面,这是物理吸附,是可逆过程,微粒逐步进入阴极表面,继而被沉积的金属所埋入。
该模型对弱吸附步骤的数学处理采用Langmuir吸附等温式的形式。
对强吸附步骤,则认为微粒的强吸附速率与弱吸附的覆盖度和电极与溶液界面的电场有关。
一些研究耐磨性镍金刚石复合镀层的共沉积过程显示,镍-金刚石共沉积机理符合Guglielmi的两步吸附模型,其速度控制步骤为强吸附步骤。
到目前为止,复合电沉积和其他新技术、新工敢一样,实践远远地走在理论的前面,其机理的研究正在不断的发展中。
3、复合电镀的添加剂
复合电镀的基体镀层往往可以采用本镀种原有的添加剂系列,比如镀镍为载体的复合镀层,可以用到低应力的镀镍光亮剂等。
但是根据复合电镀的原理,复合电镀本身也需要用到一些添加剂,以促进复合和微粒的共沉积,这些添加剂依其作用而分别有微粒电性能调整剂、表面活性剂、抗氧化剂、稳定剂等。
(1).电荷调整剂
由于微粒在电场作用下与镀层共沉积是复合镀的重要过程,让微粒带有正电荷有利于共沉积,但是大多数微粒是电中性的,需要通过一定处理让其表面吸附带正电荷的离子,从而成为荷电微粒,某些金属离子如Ti+、Rb+等可以在氧化铝等表面吸附,从而形成带正电荷的微粒,有利于与镀层共沉积。
某些络盐、大分子化合物也有调整微粒电荷的功能。
为了使微粒表面能与相应的化合物有充分的结合,所有复合镀都要求添加到镀液中的微粒进行表面处理,类似电镀过程中的除油和表面活化,以利以获得有利于共沉积的电性能。
(2).表面活性剂
在以碳化硅为复合微粒的复合镀中,加入氟碳型表面活性剂,有利于微粒的共沉积。
因此有些表面活性剂也是一种电位调整剂。
但表面活性剂还有分散剂的作用,这对于微粒在镀液中的均匀分布也是很重要的。
还有一些表面活性剂由于有明显的电位特征而在特定的电位下才有明显的作用,这对梯度结构的复合镀是有利的。
(3).辅助添加剂
还有一些络合剂、抗氧化剂等对基础液有稳定作用的添加剂,在有利于复合镀液的稳定性的同时,可以有利于微粒的共沉积。
同时,电镀过程中的添加剂与许多复配添加剂一样,
中存在鸡尾酒效应的。
有很多单独使用时作用不明显的添加剂和一些无机盐、有机化合物在共同添加时,反而可以起到良好的作用,这正是一些辅助添加剂所具有的魅力。