最新版煤矿车场设计方案
煤矿车场设计方案

矿井采区车场设计方案编制:日期:采区车场设计方案说明一概述伊宁市财荣煤业为0.6Mt/a机械化改造矿井,矿井共分为两个区段进行采煤。
为了满足矿井运输要求,分别布置+646m、+612m两个采区车场和+580m矿井底部车场,二设计步骤1.轨道与轨型2 .道岔选择选择原则:(1)与基本规矩相适应;(2)与基本轨型相适应;(3)与行驶车辆类别相适应;(4)与行车车速相适应道岔选型表3.轨距与线路中心距目前我国矿井采用的标准轨距为600 mm、762 mm和900 mm三种,其中以600 mm、和900 mm轨距最为常见。
1t固定式矿车、3t 底卸式矿车和10t架线电机车均采用600mm轨距。
为了设计和施工方便,双轨线路有1200 mm、1300mm、1400mm、1600mm和1900mm等几中标准中心距。
一般情况下不选用非标准值。
但在双轨曲线巷道(即弯道)中,由于车辆运行时发生外伸和内伸现象,线路中心距一般比直线巷道还加宽一定数值。
线路中心距2曲线半径3.线路长度确定空、重车线宜为1.0——1.5倍列车长,此处取1.2倍L=1.2(mn L K)+ NL j式中:L——副井空、重车线,m;m ——列车数目,1列;n——每列车的矿车数,8辆;L K——每辆矿车带缓冲器的长度,缓冲器长取0.3m ;N——机车数,1台;L j——每台机车的长度,m;所以:L=1.2×8×(2+0.3)+4.5=26.58m 取L=20m(2)材料车线有效长度材料车线并列布置在副井空车线一侧长度按列材料车长度确定L=mn L K+ NL j式中:L——材料车线有效长度,m;n c——材料车数,10辆;L K ——每辆矿车带缓冲器的长度,缓冲器长取0.3m ;N ——机车数,1台;L j ——每台机车的长度,m ;所以: L =10×(2+0.3)+4.5=27.5m 取L=20m4 车场通过能力计算井下采用机车运输时,井底车场年通过能力按下式计算:T Q T N a 15.1 (5-11)式中 N —— 井底车场年通过能力,t ;Q —— 每一调度循环进入井底车场的所有列车的净载煤重,t ;T —— 每一调度循环时间,min ;T a —— 每年运输工作时间等于矿井设计工作日数与日生产时间的乘积,min ;1.15 —— 运输不均衡系数。
采区下部车场设计

采区下部车场设计
采区下部车场通常是指矿山下方的一个大型停车场,用于停放矿工的车辆和设备。
设计时需要考虑以下因素:
1. 位置:车场应该位于采区的下方,便于矿工下班后直接到达。
2. 大小:车场应该足够大,能够容纳所有矿工的车辆和设备。
3. 停车标准:车场应该设置停车标准,以确保每个车辆都能有足够的空间停放,且不会妨碍其他车辆。
4. 照明:车场需要充足的照明,以确保夜间停车的安全。
5. 安全性:车场需要设置防盗装置,以确保车辆和设备的安全。
6. 排放:车场应该设置排放设施,以便矿工可以排放废气和废水。
以上是一个采区下部车场的设计要点,具体细节需要根据矿山的实际情况进行调整和改进。
采区下部车场设计
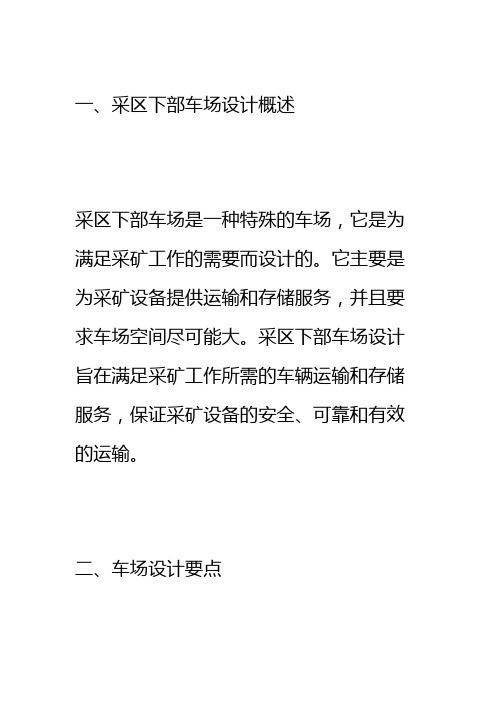
一、采区下部车场设计概述采区下部车场是一种特殊的车场,它是为满足采矿工作的需要而设计的。
它主要是为采矿设备提供运输和存储服务,并且要求车场空间尽可能大。
采区下部车场设计旨在满足采矿工作所需的车辆运输和存储服务,保证采矿设备的安全、可靠和有效的运输。
二、车场设计要点1、车场空间设计:采区下部车场的空间设计要求尽可能大,以满足采矿设备的运输需求。
车场的空间设计应考虑车辆运输的安全性和高效性,以及设备的配置和维护。
2、车辆设备:采区下部车场的车辆设备要求安全、可靠,并能够满足采矿工作的需要。
车辆设备应具备安全可靠的行驶和操作性能,能够满足采矿设备的运输需求。
3、车辆管理:采区下部车场的车辆管理要求安全、高效,并能够满足采矿工作的需要。
车辆管理应采用有效的管理措施,确保车辆安全行驶和操作,同时记录车辆的运行情况,并及时发现和处理车辆问题。
4、车辆安全:采区下部车场的车辆安全要求安全、可靠,并能够满足采矿工作的需要。
车辆安全应采取有效的安全措施,确保车辆安全行驶和操作,同时记录车辆的安全情况,并及时发现和处理车辆安全问题。
五、车场设计方案1、车场空间设计:采区下部车场的空间设计应考虑车辆运输的安全性和高效性,以及设备的配置和维护。
车场空间应有足够的宽度和长度,以便车辆运输,同时应考虑车辆的安全性和高效性,并配备足够的车位,以便采矿设备的存放和维护。
2、车辆设备:采区下部车场的车辆设备要求安全、可靠,并能够满足采矿工作的需要。
车辆设备应采用高性能的柴油机、液力变矩器等设备,以满足采矿工作的需要,同时应具备安全可靠的行驶和操作性能,以便满足采矿设备的运输需求。
3、车辆管理:采区下部车场的车辆管理要求安全、高效,并能够满足采矿工作的需要。
车辆管理应采用有效的管理措施,确保车辆安全行驶和操作,同时记录车辆的运行情况,并及时发现和处理车辆问题。
车辆管理应采用计算机管理系统,实现车辆的远程控制,并可以实时监控车辆的运行情况。
煤矿车场设计方案

矿井采区车场设计方案编制:日期:采区车场设计方案说明一概述伊宁市财荣煤业为0.6Mt/a机械化改造矿井,矿井共分为两个区段进行采煤。
为了满足矿井运输要求,分别布置+646m、+612m两个采区车场和+580m矿井底部车场,二设计步骤1.轨道与轨型钢轨型号选择2 .道岔选择选择原则:(1)与基本规矩相适应;(2)与基本轨型相适应;(3)与行驶车辆类别相适应;(4)与行车车速相适应道岔选型表3.轨距与线路中心距目前我国矿井采用的标准轨距为600 mm 、762 mm 和900 mm 三种,其中以600 mm 、和900 mm 轨距最为常见。
1t 固定式矿车、3t 底卸式矿车和10t 架线电机车均采用600mm 轨距。
为了设计和施工方便,双轨线路有1200 mm 、1300mm 、1400mm 、1600mm 和1900mm 等几中标准中心距。
一般情况下不选用非标准值。
但在双轨曲线巷道(即弯道)中,由于车辆运行时发生外伸和内伸现象,线路中心距一般比直线巷道还加宽一定数值。
线路中心距2曲线半径曲线半径选择3.线路长度确定空、重车线宜为1.0——1.5倍列车长,此处取1.2倍 L =1.2(mn L K )+ NL j式中: L ——副井空、重车线,m ; m ——列车数目,1列; n ——每列车的矿车数,8辆;L K ——每辆矿车带缓冲器的长度,缓冲器长取0.3m ; N ——机车数,1台; L j ——每台机车的长度,m ; 所以: L =1.2×8×(2+0.3)+4.5 =26.58m 取L=20m (2)材料车线有效长度材料车线并列布置在副井空车线一侧长度按列材料车长度确定 L =mn L K + NL j式中: L ——材料车线有效长度,m ; n c ——材料车数,10辆;L K ——每辆矿车带缓冲器的长度,缓冲器长取0.3m ; N ——机车数,1台; L j ——每台机车的长度,m ; 所以: L =10×(2+0.3)+4.5 =27.5m 取L=20m4车场通过能力计算井下采用机车运输时,井底车场年通过能力按下式计算:TQT N a 15.1 (5-11)式中 N —— 井底车场年通过能力,t ;Q —— 每一调度循环进入井底车场的所有列车的净载煤重,t ; T —— 每一调度循环时间,min ;T a——每年运输工作时间等于矿井设计工作日数与日生产时间的乘积,min;1.15 ——运输不均衡系数。
煤矿矿井设计井底车场设计井底车场
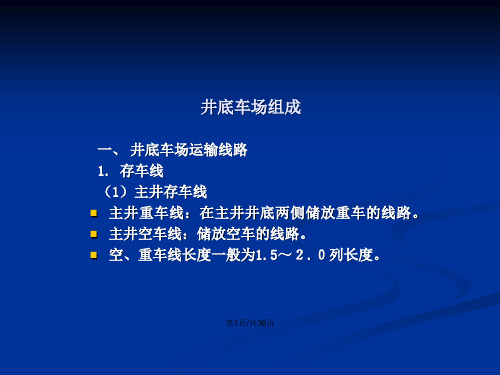
第24页/共36页
井底车场的形式及其选择
(二)折返式井底车场特点:空、重列车在车场内同一巷道的两股线路上折返运行,可简化井底车场的线路结构,减少巷道开拓工程量。分为梭式和尽头式两种类型。1、立井梭式车场(井筒距主要运输巷道较近时采用)
1-主井重车线;2-主井空车线;3-副井重车线;4-副井空车线;5-材料车线;6-调车线;7-通过线
第18页/共36页
井底车场的形式及其选择
(2)立井斜式环行井底车场
1-主井重车线;2-主井空车线;3-主要运输巷道;4-调车线;5-巷道回车线
第19页/共36页
特点:主副井存车线与主要运输巷道斜交,并利用主要运输巷道作为调车线及部分回车绕道。优缺点及使用条件:a、 开拓工程量小;b、 调车方便,通过能力较大;c、 安全性好些,弯道角度小,顶推车有利,机车不过翻车机硐室;d、 巷道交叉点较少,施工较易;井筒距大巷较近(小于一列车长)且地面出车方向 a、 也要求大巷斜交时采用。
第4页/共36页
井底车场调车方式及通过能力
一、 调车方式井底车场调车的主要任务是如何将由运输大巷驶来的重列车调入主井重车线。 (一) 顶推调车法当电机车牵引重列车驶入调车场后,停车摘钩,电机车通过调车线道岔(如上图),由列车头部转向尾部,推顶列车进入重车线,这种方法称为错车线入场法。其过程是:拉—停—摘—错—顶;另一种是三角入场法,其过程为:拉—停—摘—顶。
井底车场的形式及其选择
第17页/共36页
井底车场的形式及其选择
优缺点及使用条件:a、利用主要运输巷作绕道及调车线,开拓工程量小;b、调车较方便,通过能力大;c、安全性差:机车在弯道上顶车,减速,不安全;d、交叉点及弯道多,施工不便;e、机车不过翻车机硐室,安全;f、用于主井筒距主要运输巷道很近(约一列车长)的条件下。
矿井井底车场设计案例

矿井井底车场设计案例引言矿井井底车场是矿井生产调度系统的重要组成部分。
在煤炭、金属矿山等采矿作业中,井底车场起着运输煤炭、矿石和废石的重要作用。
矿井井底车场设计的合理与否直接关系到矿井的工作效率、安全性和经济效益。
本文将以某矿井井底车场设计案例为例,探讨矿井井底车场的设计原则、优化方法和实施过程。
设计原则矿井井底车场的设计需要遵循以下原则:1.安全性原则: 矿井井底车场设计应符合国家安全生产法规和矿井安全标准,保障员工的生命安全和财产安全。
2.高效性原则: 矿井井底车场设计应考虑煤炭或矿石的运输效率,合理配置车辆和设备,以提高工作效率。
3.可持续发展原则: 矿井井底车场设计应以可持续发展为目标,减少环境污染和资源浪费。
设计方案1. 车辆配置根据矿井的产量、井斜度和地质条件,合理配置井底车辆。
根据井口的生产能力,确定矿井输入车辆的数量和类型。
根据井底的输送能力,确定井底车辆的数量和类型。
2. 车道布置根据车辆的转弯半径、最大速度和运行轨迹,设计合理的车道布置。
考虑到井底的空间限制,采用合理的车道宽度和道路设置,确保车辆在井底的安全运行。
3. 装载系统设计合理的装载系统,根据井底车辆的运输需求,确定装载点的数量和位置。
可采用自动化装载系统,提高装载效率和精度。
4. 通信与监控系统设计完善的通信和监控系统,实时监控井底车辆的位置、状态和运行情况。
利用物联网技术,建立车辆调度中心,实现车辆调度的智能化和自动化。
5. 照明系统设计合理的照明系统,确保井底的良好照明条件,提高工作效率和安全性。
采用LED照明技术,减少能耗和维护成本。
优化方法1. 数据分析通过对矿井生产数据的分析,了解矿井的产量、生产周期和峰谷时间段,优化井底车辆的调度计划。
采用数据挖掘和机器学习算法,建立预测模型,提高调度的准确性和效率。
2. 车辆调度优化基于车辆的实时位置、状态和任务,采用最优化算法,确定最优的车辆调度方案。
考虑到井底车辆的数量和类型,优化车辆之间的距离和路线,减少车辆的等待时间和排队长度。
矿井井底车场设计案例

图5-26 坡度划分
井底车场设计
空车从摇台出车以24‰的下坡滑过对称道岔、至基本轨起点末速度为1.42 m/s。取5 ~ 6段坡度为0.009,空车在6点的速度为:
取i = 0.007,空车滑行距离
为使空车滑行到7点,6-7段坡度
其余坡度计算表5-25。 本车场线路长度1 001.7 m、掘进体积14 400.2 m3、硐室长度1 545.0 m、掘进体积19 334.9 m3。
对于大型矿井或高瓦斯矿井在确定井底车场型式时,应尽量减少交岔点的数量和减小跨度。
井筒与大巷距离近、入井风量大的矿井,如果有条件应尽量与大巷结合在一起布置井底车场,以便缩短运距、减少调车时间、减少井巷工程。
井底车场长度较大的直线巷道之间应保持一定的距离,避免相互之间的不利影响,深井中相连接的巷道必须具有不小于45°的交角。
表7-1 采区方案技术比较表
项 目
方案一双岩上山
方案二双煤上山
方案三一煤一岩上山
7 采区巷道布置方案示例
表7-2 采区方案经济比较表
0
7 采区巷道布置方案示例
表7-3 采区方案经济比较汇总表 单位:元
井底车场富裕通过能力,应大于矿井设计生产能力的30%。当有带式输送机和矿车两种运煤设备向一个井底车场运煤时,矿车运输部分井底车场富裕通过能力,应大于矿车运输部分设计生产能力的30%。
井底车场设计时,应考虑增产的可能性。
尽可能地提高井底车场的机械化水平,简化调车作业,提高井底车场通过能力。
在初步设计时,井底车场需考虑线路纵断面闭合,以免施工图设计时坡度补偿困难。
应考虑主、副井之间施工时便于贯通。
在开拓方案设计阶段,应考虑井底车场的合理形式,特别要注意井筒之间的合理布置避免井筒间距过小而使井筒和巷道难于维护、地面绞车房布置困难。
车场设计
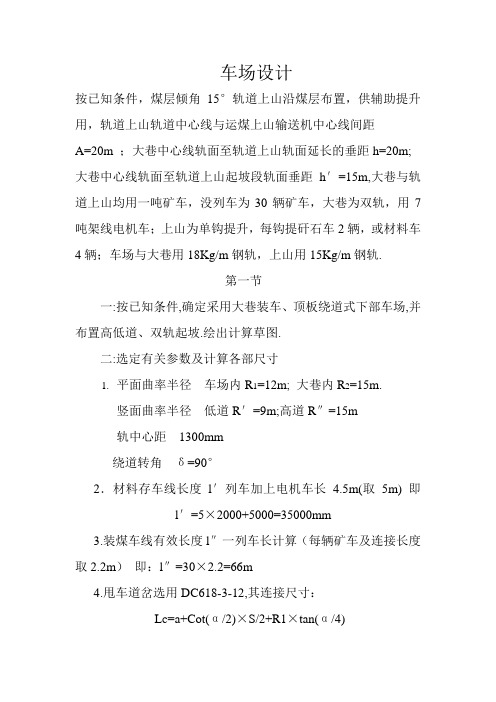
车场设计按已知条件,煤层倾角15°轨道上山沿煤层布置,供辅助提升用,轨道上山轨道中心线与运煤上山输送机中心线间距A=20m ;大巷中心线轨面至轨道上山轨面延长的垂距h=20m; 大巷中心线轨面至轨道上山起坡段轨面垂距h′=15m,大巷与轨道上山均用一吨矿车,没列车为30辆矿车,大巷为双轨,用7吨架线电机车;上山为单钩提升,每钩提矸石车2辆,或材料车4辆;车场与大巷用18Kg/m钢轨,上山用15Kg/m钢轨.第一节一:按已知条件,确定采用大巷装车、顶板绕道式下部车场,并布置高低道、双轨起坡.绘出计算草图.二:选定有关参数及计算各部尺寸1.平面曲率半径车场内R1=12m; 大巷内R2=15m.竖面曲率半径低道R′=9m;高道R″=15m轨中心距1300mm绕道转角δ=90°2.材料存车线长度l′列车加上电机车长4.5m(取5m) 即l′=5×2000+5000=35000mm3.装煤车线有效长度l″一列车长计算(每辆矿车及连接长度取2.2m)即:l″=30×2.2=66m4.甩车道岔选用DC618-3-12,其连接尺寸:Lc=a+Cot(α/2)×S/2+R1×tan(α/4)=077+1300×Cot(18°55′30″/2)+12000×tan(18°55′30″/4)=6977m其水平投影l c=L c×Cosθ=6977×Cos25°=6317mm5.材料车存车线道岔选用DK618-4-12,其平行线路连接尺寸:L1=a+S×Cotα+R1×tan(α/2)=3472+1300×Cot14°15′+12000×tan(14°15′/2)=10091MM6.材料绕道石门道岔选用DK618-4-12,其非平行线路连接尺寸:m=a+{b+R2×tan[(δ-α)/2] }×Sin(δ-α)/ Sinδ=3472+{3328+15000×tan[(90°-14°15′)]} ×Sin(90°-14°15′)/Sin90°=18172mmn=( R2×Cosα+b×Sinα- R2×Cosδ)/Sinδ=(15000×Cos14°15′+3328×Sin14°15′-15000×Cos90°)/Sin90°=15400mm7.装煤车线道岔选用DX618-4-1213,其连接尺寸:l2=2a+S/tanα=2×3472+1300/tan14°15′=12063mm三计算线路布置尺寸1 低道起坡点至运输大巷中心线的间距LA=h′/Sinθ+R′×tan(θ′/2)=15000/Sin25°+9000×tan(25°34′23″/2)=37528mm式中θ=25°(轨道上山起坡角)θ′= θ+ 34′23″=25°34′23″(低道竖曲线起坡角,低道坡度为10‰)2 低道起坡点至材料车线内侧轨道中心线间距L4=C1+R1=2500+12000=14500mm式中 C1=2500mm (起坡点至曲线间插入缓和线)γ3 起坡段长度L2=[(h-h c)/Sinβ-L A+R×tan(θ/2)]×Sinβ/Sinγ=[(20000-320)/Sin15°-37528+9000×(25°34′23″ /2)]×Sin15°/Sin10°=60810mm式中h c=320mm (轨道上山底板至轨面高度)γ=θ-β=25°-15°=10°(起坡段与上山延线夹角)4 轨道上山轨道中心线至绕道石门道中心线间距X=S/2+R1+l1+L3+C2+R2=13000/2+13654+100991+2000+15000=53395mm式中L3=l-kp1-C1=35000-18846-2500=13654mmC2=2000mm (单开道岔与弯道间缓和线长度)5 装煤车场插入段长度(1)绕道石门轨中心线至煤仓下口渡线道岔起点间距x=X-A-B-l2=53395-20000-5000-12063=16332mm 式中 B=5m (煤仓中心至渡线道岔间距)(2)绕道石门单开道岔起点至装煤车线渡线道岔终点间距x′=l′-x-m=70000-16332-18172=35496mm6 绕道石门插入线长度y=L A-d+L4-R2-n=37528-530+14500-15000-15400=21098mm式中 d=530mm (大巷中心线至内侧轨中心间距)四高低道计算1 确定高低道型式为一次变坡,取高道竖曲率半径R″=15m,取低道竖曲率半径R′=9m 如图2 取低道自溜坡度10‰(δ′=34′23″);高道自溜坡度8‰(δ″=27′30″);3 低道竖曲线计算起坡角θ′=θ+δ′=25°+34′23″=25°34′23″弧长K′p=π×9000×25°34′23″/180°=4016mm切线长T′=9000×tan(25°34′23″/2)=2043mm4 高道竖曲线计算起坡角θ″=θ+δ″=25°-27′30″=24°32′30″弧长K″p=π×15000×24°32′30″/180°=6424mm切线长T″=15000×tan(24°32′30″/2)=3261mm5 竖曲线的相对位置OA=35000mm (空线长度)OO ′=[(OA+T′)/Sinθ]×Sinθ′=[(35000=2043)/Sin25°)]Sin25°34′23″=37840mmEO′=[(OA+T′)/Sinθ]Sinθ×Sinδ′= [(35000=2043)/Sin25°)]Sin34′23″=867mmO′F=OO′×Sinδ″/Sinθ″=37840×Sin27′30″/Sin24°32′30″=729mmOF=OO′×Sinδ″/Sinθ= 37840×Sin27′30″/Sin25°=38498mm两竖曲线水平投影起点间距l AB=(OF-T″)×Cosδ″-OA×Cosδ′=(38498-3261)×Cos27′30″-35000Cos34′23″) =237mm两竖曲线水平投影起点间距l CD=(T″+O′F+EO″+T′)×Cosθ=(3261+729+867-2043)×Cos25°=2551mm6 竖曲线水平投影长度低道l AC=T′×Cosδ′+T′×Cosθ=2043(Cos34′23″+Cos25°)=3893mm高道l BD=T″×Cosδ″+T″×Cosθ=2043(Cos27′30″+Cos25°)=4735mm7 标高计算设高道低道起点相对标高为 h1=0mm低道起坡点的相对标高为 h2=-OA×Sinδ′=-35000×Sin34′23″=-346mm低道起坡点曲线终点相对标高为h3=h2+(-T′×Sinδ′)+T′×Sinθ=-346-2043×Sin34′23″+2043×Sin25°=+197mm低道起坡点的相对标高为 h2′=h3′-T″×(Sinθ+Sinδ″)=1686-3261 ×(Sin25°+Sin27′30″) =282mm高道起坡点曲线终点相对标高为h3′=h3+l CD×tanθ=497+2551 ×tan25°=1686mm验算高道起坡点标高 h1=h2′-OB Sinδ″=282-35237×Sin27′30″=0验算结果,完全闭合.其他线路按3‰铺设.下部车场平面图下部车场剖面图甩车道坡度图。
- 1、下载文档前请自行甄别文档内容的完整性,平台不提供额外的编辑、内容补充、找答案等附加服务。
- 2、"仅部分预览"的文档,不可在线预览部分如存在完整性等问题,可反馈申请退款(可完整预览的文档不适用该条件!)。
- 3、如文档侵犯您的权益,请联系客服反馈,我们会尽快为您处理(人工客服工作时间:9:00-18:30)。
最新版
矿井采区车场设计方案
一概述
采区车场设计方案说明
伊宁市财荣煤业为0.6Mt/a 机械化改造矿井,矿井共分为两个
区段进行采煤。
为了满足矿井运输要求,分别布置+646m 、+612m
两个采区车场和 +580m 矿井底部车场,
二设计步骤
1. 轨道与轨型
钢轨型号选择
使用地点运输设备钢轨型号 /kg. m3
综采支架等30 采区、井底车场
综采支架等30
2 . 道岔选择
选择原则:
(1))与基本规矩相适应;
(2))与基本轨型相适应;
(3))与行驶车辆类别相适应;
(4))与行车车速相适应
道岔选型表
轨距大巷及采区下部车场采区上中部车场
/钢轨/
mm kg ?m -1 600 18 ~ 30
道岔
相应轨型
4 号道岔
钢轨/
kg ?m -1
30
道岔
主提升相应轨型4、5 号道岔。
辅助提升用相应轨型的 3 、4
号道岔
3. 轨距与线路中心距
目前我国矿井采用的标准轨距为 600 mm 、762 mm 和 900 mm 三种,其中以 600 mm 、和 900 mm 轨距最为常见。
1t 固定式矿车、3t 底卸式矿车和 10t 架线电机车均采用 600mm 轨距。
为了设计和施工方便,双轨线路有 1200 mm 、1300mm
、
1400mm
、1600mm
和 1900mm
等几中标准中心距。
一般情况下
不选用非标准值。
但在双轨曲线巷道(即弯道)中,由于车辆运行时 发生外伸和内伸现象,线路中心距一般比直线巷道还加宽一定数值。
线路中心距
设备类型及有关参数/ mm
线路中心距/ mm
设备类型 轨 距 车 宽 直线段 曲线段机车或 3t 矿车
1 t 矿 车
2 曲线半径
曲线半径选择
运输设备
轨距 曲线轨道半径 /m 牵引设备 矿车 mm 最小
最大
建议综采设备
2.5t
600
12
15 —— 20
12
3. 线路长度确定
空、重车线宜为 1.0 —— 1.5 倍列车长,此处取 1.2 倍
L =1.2 (mn L K )+ NL j
式中: L —— 副井空、重车线, m ;
m —— 列车数目, 1 列;
n —— 每列车的矿车数,
8 辆 ; 600 1060 1300 1600 600 1200 1600 1900 600
880
1100
1300
L K——每辆矿车带缓冲器的长度,缓冲器长取0.3m ;
N——机车数, 1 台;
L j ——每台机车的长度,m;
所以:L=1.2 ×8×(2+0.3 )+4.5
=26.58m 取L= 20m
(2)材料车线有效长度
材料车线并列布置在副井空车线一侧长度按列材料车长度
确定
L=mn L K+ NL j
式中:L——材料车线有效长度, m ;
n c——材料车数, 10 辆;
L K——每辆矿车带缓冲器的长度,缓冲器长取0.3m ;
N——机车数, 1 台;
L j——每台机车的长度,m;
所以:L=10 ×(2+0.3 )+4.5
=27.5m 取L= 20m
4 车场通过能力计算
井下采用机车运输时,井底车场年通过能力按下式计算:
N
T
a
Q
1.15T
(5-11 )
式中N ——井底车场年通过能力,t;
Q ——每一调度循环进入井底车场的所有列车的净载煤重,t;
T ——每一调度循环时间,min ;
T a——每年运输工作时间等于矿井设计工作日数与日生产时间的乘积, min ;
1.15 ——运输不均衡系数。
井年产量 60 万 t ,年工作日按 330 天计算,则日产 1818t ,每日净提升时间为 18 小时。
矸石量按煤产量的 20% , 364t/ 掘日;进出煤为 5% ,90.9t/ 日。
则煤矸混合列车中煤和矸石比为 4:1 ,每日1t 煤矸混合列车数为(364+90.9 )/10=45.49 列。
每日 3t 底卸式矿车列车数为 1818/16*3=37.875 列。
则每一调度循环中包括 2 列3t 煤列车和 1 列 1t 煤矸混合列车,调度循环时间为 4 分钟。
矿井通过能力N=330 ×18 ×10 ×(16 ×3+5 ) /(1.15 ×
4)=68.5
万 t
车场通过能力应考虑留有一定的备用(储备)能力,一般应大于
矿井设计生产能力的 30 %。
68.5 万 t/60 万 t=1.142>1.3 符合设计要求
故车场双轨巷选择长度为 20m 满足矿井运输要求。
三矿井现状
目前矿井 +646m 、+612m 、+580m 石门已经基本形成,经设计
院沟通,确保矿井风流稳定及保安煤柱不受破坏,矿井甩车场尽可能
使用已有巷道。
四巷道断面及支护方式
单轨巷断面为宽×高=3m ×2.9m 的半圆拱断面;
双轨巷断面为宽×高 =4.5m ×3.65m 的半圆拱断面;
交叉点牛鼻子宽度不得小于500mm ,采用砌碹支护,基础深度不得小于 500mm ,必须砌在实地。
所有巷道均采用锚网喷支护,锚杆采用?20 ×2200mm 的高强锚杆,网子采用?6mm 的钢筋焊接,规格为长×宽 =1000mm ×2000mm ;喷射混凝土标号不小于C20 ,喷浆厚
度为150mm 。
附:三个车场设计图。
五存在问题及难点
由于副斜井没有施工到位,没有具体的测量数据支撑,无法准确确定副斜井与石门在同一标高时的位置关系,不能确定甩车方向。
暂定选择为正向甩车,后根据实际情况再做调整。