回转窑作业指导书
回转窑工段岗位作业指导书
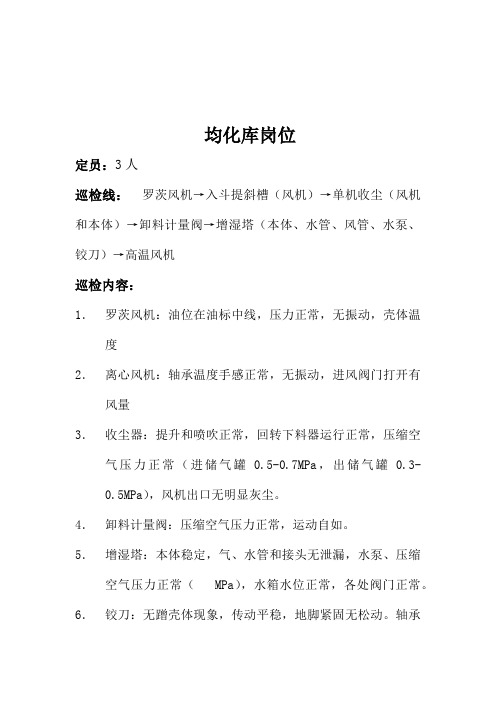
均化库岗位定员:3人巡检线:罗茨风机→入斗提斜槽(风机)→单机收尘(风机和本体)→卸料计量阀→增湿塔(本体、水管、风管、水泵、铰刀)→高温风机巡检内容:1.罗茨风机:油位在油标中线,压力正常,无振动,壳体温度2.离心风机:轴承温度手感正常,无振动,进风阀门打开有风量3.收尘器:提升和喷吹正常,回转下料器运行正常,压缩空气压力正常(进储气罐0.5-0.7MPa,出储气罐0.3-0.5MPa),风机出口无明显灰尘。
4.卸料计量阀:压缩空气压力正常,运动自如。
5.增湿塔:本体稳定,气、水管和接头无泄漏,水泵、压缩空气压力正常( MPa),水箱水位正常,各处阀门正常。
6.铰刀:无蹭壳体现象,传动平稳,地脚紧固无松动。
轴承温度正常。
翻板阀动作灵活。
7.高温风机:风机油站油压正常(),温度正常(可通过调冷却水量来调节),油位正常。
轴承温度正常,风机无振动,进轴承油量正常,冷却水正常,无漏油漏水现象。
巡检频次:每小时一次预热器岗位定员:3人巡检线:入窑入库斗提地坑→窑尾斜坡→各级翻板阀→各级空气炮→均化库顶→入库提升机机头→入窑斗提机头→入窑系统巡检内容:1.提升机:底部有无跑灰,有无振动,空载时检查斗子运行情况(有无变形、跑偏、松动、接料板位置),机头地脚紧固情况,轴承温度是否正常,减速机温度、油位、声音正常。
2.翻板阀:动作灵活,无物料泄漏。
3.空气炮:管路无泄漏,压力正常(储气罐0.5-0.7MPa),工作正常。
4.离心风机:轴承温度手感正常,无振动,进风阀门打开有风量5.收尘器:提升和喷吹正常,回转下料器运行正常,压缩空气压力正常(进储气罐0.5-0.7MPa,出储气罐0.3-0.5MPa),风机出口无明显灰尘。
6.入窑系统:回转下料器运行正常,轴承温度正常,气动阀动作自如,液动阀动作自如油液无泄漏,分料阀动作自如,斜槽连接部位防雨罩完好。
巡检频次:每小时一次窑系统岗位定员:5人巡检线:窑主减油站→液压挡轮站→主电机冷却风机→窑尾密封→窑主减速机→窑大小齿轮→液压挡轮→各档轮带托轮→筒体冷却风机→窑头密封→喷煤管→一次风机→篦冷机一二三段油缸→空气炮→风机群→各室蓖下→液压站→锤破机→弧形阀巡检内容1.液压和稀油站:油位油压油温正常,过滤器压差正常,冷却水正常,管路无泄漏。
焙烧作业区回转窑停窑转窑操作作业指导书

焙烧作业区回转窑停窑转窑操作作业指导书
①、临时停窑,因生产故障迫使回转窑临时停窑时,一般应先停止喂料,相应减少用风和燃料用量,直至停窑。
停窑后应关闭排风闸,打开冷风阀,保持窑温,为再次开窑创造条件。
停窑后为了防止筒体弯曲,应每隔一定时间转窑1/3圈。
15分钟内转一次窑,再过20分钟转一次,再过30分钟转一次,再过一小时转一次,四小时内不能恢复生产,则应按停窑来处理。
停窑过程中如遇大雨、中雨,则应连续翻窑。
②、因检修或长时间停窑,在停窑前1~3小时内将喂料量减到正常下料的50~70%,减料30分钟后,再逐步降低窑速,并拉长火焰。
为防止窑尾温度过高,应减小排风量,同时应减少进料量,直至停止喂料,待窑内物料转空时才停窑。
这一过程中应控制预热器出口温度不超过250℃。
否则会损坏电除尘设备。
停窑后,为防止筒体弯曲变形,辅助电机连续翻窑1小时,停后2小时内,每隔20分钟转窑1/3转,2小时后可将每次翻窑间隔逐渐扩大,停窑6小时后,每小时翻窑1/3转,12小时后,每2小时翻窑1/3转,直到窑体完全冷却为止。
③、回转窑停电时的操作:回转窑停电后,应迅速起动备用电源转窑,避免停窑时间长,而导致筒体弯曲变形。
转窑按临时停窑处理。
焙烧作业区回转窑上料预热岗位作业指导书

焙烧作业区回转窑上料、预热岗位作业指导书
5.3.1工艺生产操作要求
5.3.1.1如预热器料位偏低时,应立即通知主控室带料,否则废气温度及电除尘入口温度过高,造成设备事故。
5.3.1.2正常操作时,在观察推杆动作是否正常,要注意站位,预防煤气中毒。
5.3.1.3上料振动给料机的频率要根据产量进行调整,原则上要控制筛面上的料层,影响筛分效果。
5.3.1.4岗位人员每班必须及时清理上料振动筛筛网,保证入窑的筛分效率。
5.3.1.5要时刻关注转运仓的矿石的料位变化,发现料位偏低时要及时报告,并且及时与破碎联系,满足生产供应。
5.3.2安全生产操作要求
5.3.2.1禁止横跨或乘坐、站立在皮带上,防止皮带突然启动造成伤害,禁止用手或任何工具在运转皮带机头、尾轮上清扫、刮料、扒料等作业,防止造成机械伤害。
5.3.2.2若皮带被卡住,应立即停机,报告仪表室,并将机旁箱上的转换开关打至零位,挂好“禁止合闸”的警示牌,方可作业。
5.3.2.3皮带运行时,不得隔着皮带传递物件,长发者必须将头发挽入帽内系牢,防止被皮带缠住造成人身伤害事故。
5.3.2.4更换挡皮、清扫器、托辊时,要有两人以上配合作。
回转窑作业指导书

沾益县通途工贸公司廻转窑挥发法生产氧化锌技术操作规程批准:晏崇云审核:吴金星编写:缪维纲2007年9月19日一、引言1.1锌的性质和用途铅是兰灰色金属,硬度1.5,比重11.34,熔点327℃,沸点1525℃;能与锌、锡、锑、砷等金属组成合金。
铅的展性良好,延性甚微;在干燥空气中,铅不发生化学变化;在潮湿空气中,易形成氧化铅薄膜覆盖其表面;常温下,铅几乎不溶于稀盐酸和硫酸,但溶于硝酸,铅对碱、氨、氰酸及有机盐具有较好的防腐蚀能力。
锌是兰白色金属,硬度2.0,熔点419℃,沸点906℃,加热至100-150℃时,具有良好压延性,压延后比重为7.19,锌能与铅、锡、锑、镍、铜等金属组成合金。
在常温下的干燥空气中,锌不起变化;在潮湿空气中,其表面生成致密的碱性碳酸锌薄膜,可保护锌金属内部和镀锌金属表面不再氧化受腐蚀。
由于铅、锌具有上述特性,因此被广泛用于电气工业、机械工业、军事工业、冶金工业、化学工业以及轻工业和医药工业等部门,铅金属还在核工业和石油工业等部门有所应用。
镉的性质镉是一种银白带蓝色光泽的金属。
密度为8.64克/厘米3,熔点320.9℃。
镉比锌更容易挥发,其沸点为767℃,镉的分子量为112.4。
1.2 锌精矿质量标准(表3)锌精矿质量标准(YB114—81)表3品级锌不小于(%)一二三四五六七八九59 57 55 53 50 48 45 43 40杂质不大于(%)Cu Pb Fe As SiO2 F0.8 1.0 6 0.2 3.0 0.20.8 1.0 6 0.2 3.5 0.20.8 1.0 6 0.2 4.0 0.20.8 1.0 7 0.3 4.5 0.21.0 1.5 8 0.4 5.0 0.21.0 1.5 13 0.5 5.5 0.21.52.0 14 协议 6.0 0.21.52.5 15 协议 6.5 0.22.03.0 16 协议7.0 0.21.3 锌精矿的杂质铜:在精矿中常呈铜的硫化物状态存在,焙烧时,主要形成不同形式的氧化亚铜,残余的硫化铜易形成冰铜,降低炉料的熔点。
焙烧作业区回转窑点火转窑操作作业指导书
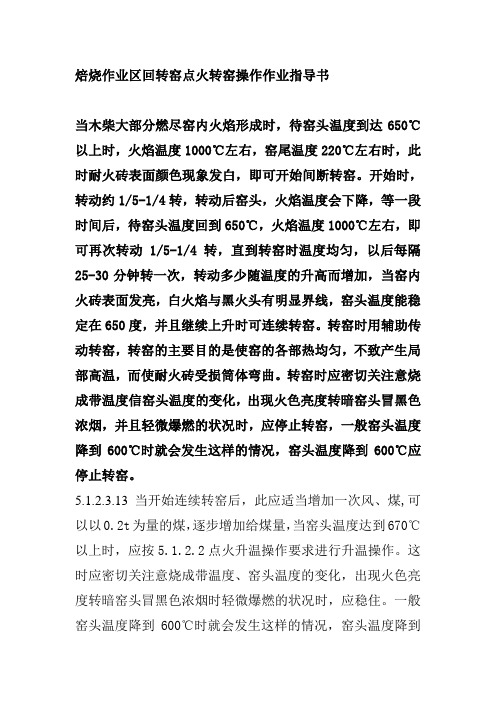
焙烧作业区回转窑点火转窑操作作业指导书当木柴大部分燃尽窑内火焰形成时,待窑头温度到达650℃以上时,火焰温度1000℃左右,窑尾温度220℃左右时,此时耐火砖表面颜色现象发白,即可开始间断转窑。
开始时,转动约1/5-1/4转,转动后窑头,火焰温度会下降,等一段时间后,待窑头温度回到650℃,火焰温度1000℃左右,即可再次转动1/5-1/4转,直到转窑时温度均匀,以后每隔25-30分钟转一次,转动多少随温度的升高而增加,当窑内火砖表面发亮,白火焰与黑火头有明显界线,窑头温度能稳定在650度,并且继续上升时可连续转窑。
转窑时用辅助传动转窑,转窑的主要目的是使窑的各部热均匀,不致产生局部高温,而使耐火砖受损筒体弯曲。
转窑时应密切关注意烧成带温度信窑头温度的变化,出现火色亮度转暗窑头冒黑色浓烟,并且轻微爆燃的状况时,应停止转窑,一般窑头温度降到600℃时就会发生这样的情况,窑头温度降到600℃应停止转窑。
5.1.2.3.13当开始连续转窑后,此应适当增加一次风、煤,可以以0.2t为量的煤,逐步增加给煤量,当窑头温度达到670℃以上时,应按5.1.2.2点火升温操作要求进行升温操作。
这时应密切关注意烧成带温度、窑头温度的变化,出现火色亮度转暗窑头冒黑色浓烟时轻微爆燃的状况时,应稳住。
一般窑头温度降到600℃时就会发生这样的情况,窑头温度降到600℃应适当降一点排风。
5.1.2.3.14给煤量至2.0T,一次风逐步增加到38HZ(使用萝茨风机应达到50HZ)后应稳定操作一段时间,待窑尾烟气变淡,并且已能正常投料生产,才增加给煤量进一步的提温、提产。
如给煤量增加过快,会导致窑头窑尾温度控制不住,并且窑内煤粉燃眉之急烧不完全,窑尾冒浓浓的黑烟,影响电除尘的安全。
5.1.2.3.15在加煤的过程中应注意要防止下煤粉过多,燃烧不完全被排到窑外冒黑烟,使点火时间延长。
点火后,如情况正常,窑内即呈现出通红的火焰,火舌微倒向窑的尾部,废气大部分顺窑壁向窑尾流动,小部分流向窑头,从排风机烟囱冒白烟或微灰烟。
水泥厂中控室(回转窑)操作员作业指导书

通过本岗位认真操作完成以下目标:
1、无人为的责任操作事故;
2、设备各处均无正压现象,环保设备达到要求标准;
3、在保证产量的基础上减小系统的用风量,降低生产成本;
4、及时发现操作上不正常的现象,及时处理,处理不了的及时上报;
5、在稳产、高产的基础上,使其产量、质量、电耗、成本达到较高的水平。
职位权限:
8、对公司内不符合安全规定的行为,有制止权、否决权;
对相关部门岗位工作有监督权、建议权;
业绩考核
主要指标:
1、操作事故;
2、安全操作
3、台时产量
安全责任:
真遵守公司的安全政策及各项安全规章制度;
及时制止发现的各种安全违章行为。
工艺流程简介
一、生料均化库及入窑喂料设备简介
参照:工艺设备表
二、生料均化库及入窑喂料工艺图
参照工艺设备表
八、烧成系统工艺流程简介
参照工艺流程总图
九、烧成系统工艺流程简介
预热器由双系列五级旋风预热器和管道型分解炉构成,生料在C1—C2的风管处进入预热器。生料自上而下与热气体悬浮换热升温,入分解炉进行碳酸盐分解后,经C5收集后,从窑尾烟室喂入回转窑。入窑物料经回转窑高温煅烧,在1250-1280℃产生液相,物料在高温液相的情况下产生物理化学变化,形成高温熟料。高温熟料出窑入篦冷机快速冷却。在回转窑内煤粉燃烧后,生成高温废气经烟室从分解炉底部入炉。在分解炉内,煤粉、三次风、预热后的生料及回转窑的高温废气,通过旋流和喷腾,实现气体充分混合,完成燃烧、分解。分解炉排出的气料,在C5内气料分离,物料入窑,废气经各级旋风筒,自下而上与生料悬浮换热降温,最后从C1排出,窑尾高温风机将废气送入废气处理系统,或部分入生料磨烘干用。
回转窑作业指导书
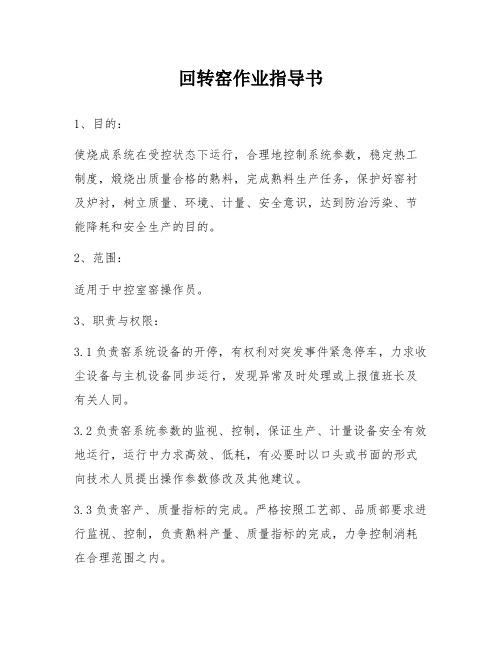
回转窑作业指导书1、目的:使烧成系统在受控状态下运行,合理地控制系统参数,稳定热工制度,煅烧出质量合格的熟料,完成熟料生产任务,保护好窑衬及炉衬,树立质量、环境、计量、安全意识,达到防治污染、节能降耗和安全生产的目的。
2、范围:适用于中控室窑操作员。
3、职责与权限:3.1负责窑系统设备的开停,有权利对突发事件紧急停车,力求收尘设备与主机设备同步运行,发现异常及时处理或上报值班长及有关人同。
3.2负责窑系统参数的监视、控制,保证生产、计量设备安全有效地运行,运行中力求高效、低耗,有必要时以口头或书面的形式向技术人员提出操作参数修改及其他建议。
3.3负责窑产、质量指标的完成。
严格按照工艺部、品质部要求进行监视、控制,负责熟料产量、质量指标的完成,力争控制消耗在合理范围之内。
3.4负责窑系统操作过程中出现的安全、环境、计量等不符合体系要求情况的调整、处理,并及时通知巡检工检查。
3.5熟悉并理解ISO9001、GB/T28001、ISO14001、GB/T28001各质量体系的名词术语、方针、目标。
3.7熟悉本系统或本岗位环境因素、危险源,熟悉应急与响应方案。
3.8完成管理人员临时交办的任务。
3.9记录书写工整、规范,交接班清楚。
3.9、负责搞好本班卫生。
3.10.检修时参与检修工作。
4、技术要求:4.1、参数控制:4.1.1、投料量165-180t/h。
4.1.2、一级预热器出口≤360℃。
4.1.3、五级预热器出口温度850-890℃。
4.1.4、分解炉出口温度860-900℃。
4.1.5、窑尾烟室温度950-1050℃。
4.1.6、窑头电收尘温度≤250℃。
4.1.7、三次风温≥800℃。
4.1.8、出篦冷机熟料温度<100℃,不见红料。
4.1.9、220℃<窑筒体温度<350℃。
4.1.10、一级预热器负压4500-6000Pa。
4.1.11、窑尾烟室负压100-300Pa。
4.1.12、窑头负压20-60Pa。
回转窑安装作业指导书

回转窑安装作业指导书1.概述1.1回转窑是水泥生产工艺线中的最关键的设备之一,其安装质量的优劣,直接关系到全厂工艺线是否正常运行和企业经济效益的好坏。
因此,施工中采用先进的施工方法和检测手段,严格控制每一道工序的施工质量是确保回转窑安装质量的关键。
1.2回转窑主要组成部件:支承装置、筒体、传动装置、液压挡轮装置、窑尾密封装置、窑头密封罩及液压润滑系统。
其中:支承装置的托轮轴承有滚动轴承和滑动轴承两种结构;窑体斜度有3.5%和4%两种形式;传动形式有开式单边边缘传动和双边边缘传动;挡轮装置有液压挡轮和机械挡轮之分。
1.3进口设备的安装,其技术规范应按国外提供的指导书的技术标准实施,如无标准,应经专家认可采用国内标准,标准实施时,需做好专家许可记录。
2.回转窑施工工序流程:其工序流程见图一:图一回转窑施工工序流程图3.回转窑安装及其技术要求3.1基础验收与划线3.1.1基础验收:应在设备安装前,以厂方为主,会同土建单位共同验收,合格后交安装施工,并要求做好验收签证记录。
3.1.1.1基础外型尺寸、中心线、标高、地脚螺栓孔以及相互位置实测尺寸与图纸设计尺寸要相一致,其偏差应符合下表要求:3.1.1.2清除基础上外露的钢筋头、施工模板等杂物,并把地脚孔内脏物清除干净。
3.1.1.3要求厂方应把基础四周的回填土夯实,增强其地面抗压强度,保证窑筒体的吊装作业场地。
3.1.2基础划线:(以3个基础墩为例)3.1.2.1窑基础基准线的确定前的准备工作。
⑴按工艺图规定的位置为依据,在1#、2#墩各埋设4块中心标板,3#墩埋设8块,埋设要牢固。
⑵中心标板埋设要求:斜度为3.5%(或4%),标板间纵横向水平度不超过0.5mm,相对标高误差不超过0.5mm。
⑶在每个基础墩的横向中心线上的左下侧部位预埋一个基础标高点,其标高点与厂区基准标高点相对偏差在0.5mm之内。
⑷在每个基础墩纵向墩壁两侧埋设沉降标板,其标板在+1000mm处为宜(注:上述标板埋设位置见图二示意)。
- 1、下载文档前请自行甄别文档内容的完整性,平台不提供额外的编辑、内容补充、找答案等附加服务。
- 2、"仅部分预览"的文档,不可在线预览部分如存在完整性等问题,可反馈申请退款(可完整预览的文档不适用该条件!)。
- 3、如文档侵犯您的权益,请联系客服反馈,我们会尽快为您处理(人工客服工作时间:9:00-18:30)。
金九水泥文件编号:JJSN—ZKS01 №:版本:1修定状态:0重庆金九水泥有限公司中控室作业指导书2007年08月20日发布 2007年08月20日实施起草人: 张春涛审核人: 批准人:起草日期:2007年 8月01日审核日期: 2007年 8月15日批准日期: 2007年 8月15日中控室窑操作员作业指导书1、目的:使烧成系统在受控状态下运行,合理地控制系统参数,稳定热工制度,煅烧出质量合格的熟料,完成熟料生产任务,保护好窑衬及炉衬,树立质量、环境、计量、安全意识,达到防治污染、节能降耗和安全生产的目的。
2、范围:适用于中控室窑操作员。
3、职责与权限:3.1负责窑系统设备的开停,有权利对突发事件紧急停车,力求收尘设备与主机设备同步运行,发现异常及时处理或上报值班长及有关人同。
3.2负责窑系统参数的监视、控制,保证生产、计量设备安全有效地运行,运行中力求高效、低耗,有必要时以口头或书面的形式向技术人员提出操作参数修改及其他建议。
3.3负责窑产、质量指标的完成。
严格按照工艺部、品质部要求进行监视、控制,负责熟料产量、质量指标的完成,力争控制消耗在合理范围之内。
3.4负责窑系统操作过程中出现的安全、环境、计量等不符合体系要求情况的调整、处理,并及时通知巡检工检查。
3.5熟悉并理解ISO9001、GB/T28001、ISO14001、GB/T28001各质量体系的名词术语、方针、目标。
3.7熟悉本系统或本岗位环境因素、危险源,熟悉应急与响应方案。
3.8完成管理人员临时交办的任务。
3.9记录书写工整、规范,交接班清楚。
3.9、负责搞好本班卫生。
3.10.检修时参与检修工作。
4、技术要求:4.1、参数控制:4.1.1、投料量165-180t/h。
4.1.2、一级预热器出口≤360℃。
4.1.3、五级预热器出口温度850-890℃。
4.1.4、分解炉出口温度860-900℃。
4.1.5、窑尾烟室温度950-1050℃。
4.1.6、窑头电收尘温度≤250℃。
4.1.7、三次风温≥800℃。
4.1.8、出篦冷机熟料温度<100℃,不见红料。
4.1.9、220℃<窑筒体温度<350℃。
4.1.10、一级预热器负压4500-6000Pa。
4.1.11、窑尾烟室负压100-300 Pa。
4.1.12、窑头负压20-60 Pa。
4.1.13、一室篦下压力<6000 Pa。
4.1.14、四室篦下压力2400-2900 Pa。
4.1.15、窑速3.60-3.90r/min.4.2、质量标准:4.2.1、熟料f-CaO≤1.5%;合格率≥85%。
4.2.2、立升重=目标值±75g/L,合格率≥85%。
4.2.3、熟料三天抗压强度≥28Mpa,合格率≥85%。
5、系统开车操作规程:5.1、点火前的准备:5.1.1、向工艺部索要升温曲线图。
5.1.2、通知窑、煤磨系统的巡检工进行点火前的检查准备。
5.1.3、接到各有关巡检人员检查完毕的通知后,确认系统各设备是否已备妥。
5.1.4、确认系统各管道阀门开关灵活、位置方向是否与中控一致。
5.1.5、确认柴油储备是否充足,清理油枪管道。
5.1.6、通知巡检工开启空压机、循环水泵。
5.1.7、通知窑系统巡工准备点火工具。
5.1.8、通知巡检工将工业电视推入窑头罩内并启动该装置。
5.2、窑点火和升温操作规程:5.2.1、调节预热器点火烟囱帽开度到20%,使窑系统产生微负压。
5.2.2、启动窑头一次风机G19AC,正常后,转速调至20HZ左右。
5.2.3、将火把点燃后,从窑头罩观察孔伸进至喷煤管嘴处,启动油泵点火并根据燃烧情况调节供油压力,一般供油压力在1Mpa左右。
5.2.4、确认柴油点燃正常后,可进一步调整窑头一次风机转速和燃烧器内外风比例至得到较理想的火焰形状。
5.2.5、按规定的升温曲线制度进行转窑和升温。
窑升温时应根据窑内温度情况进行间隔慢转窑。
5.2.6、在尾温达260℃时,启动窑头煤粉输送罗茨风机K22M,启动头煤粉研称K23AC,喂煤量为0.5吨/小时。
根据窑头火焰情况及尾温升高情况,增加喂煤量,尾温500℃以下时, 0.1吨/小时的幅度增加,并保证火焰稳定燃烧。
刚开始喷煤时操作要平稳,注意调节一次风量,做到即能保证煤粉充分燃烧,风量又不能过大,避免燃烧器熄火。
当尾温升到600℃左右时,逐渐减小供油压力至1Mpa内。
5.2.7、当尾温升到550℃时,启动窑尾一次风机F22M,冷却窑尾燃烧器。
5.2.8、当尾温升到800℃左右时进行辅传连续慢转窑,窑头油泵可试着停止供油.根据温升情况和窑头负压情况,适当调整预热器点火烟囱帽开度,保持窑头负压5-20 Pa。
观察火焰的燃烧情况调整喂煤,保持火焰稳定燃烧。
5.2.9、当窑头喂煤量达1.5t/h时即可开篦冷机一室平衡风机G21M、固定篦床风机G22和G23M来补充煤粉燃烧所需氧气。
若窑头明显有正压,可开启窑尾后排风机并调节高温风机进口号阀门的开度。
5.2.10、当窑尾温度900℃左右,窑头油泵应完全停止供油,停窑辅传,开启窑主电机冷却风机、窑主电机,主传低速转窑,转速为0.5rpm,根据升温曲线及时观察火焰燃烧情况进行加煤,同时调整风量使燃烧充分,避免烟囱冒黑烟。
5.2.11、联系现场开启熟料输送设备:槽式输送机G3M,熟料破碎机G31ASP,二段蓖床G33ARC,一段蓖床G32ARC。
5.2.12、窑主传启动正常后,开启窑头冷风套风机和窑尾喂料舌冷却风机。
5.2.13、当窑尾温度900℃左右,关闭窑尾高温风机进口阀和液偶执行器,联系现场启动窑尾高温风机。
启动顺序:启动窑尾高温风机稀油站F17AC1和F28ALC,启动窑尾高温风机F18M, 待电流恢复正常后将进口风阀全打开,然后根据窑内通风情况调节液力偶合器阀门开度。
5.3、投料前的准备工作:5.3.1、投料前一小时通知窑系统巡检工清理烟室,检查各级预热器旋风筒是否有积存料,并保证其处于通畅状态,并调轻各级重锤翻板阀。
5.3.2、启动窑尾喂料设备:启动回转下料器F24M,启动塔架斜槽风机F25M,启动入窑提升机F26M,启动入窑提升机斜槽收尘器F31ALC、F30M,启动斜槽风机F32M, 启动FDLD冲击流量称,启动吹仓罗茨风机F35M, 启动均化库底收尘器F37ALC、风机F38M ,手动启动任意相对的两个大区的电磁阀,若称重仓低于40吨,启动吹库罗茨风机F33M,并给定两个大区执行器阀门开度(也可自动控制,直接设定仓重,投料初期应设低一些)。
5.3.3、根据篦冷机和窑内出料量情况启动活动梁风机G24M、G25M和二室风机G26M。
5.5.4、启动窑头排灰组:启动螺旋输送机G4M,回转下料器G5M、G6M,绞刀G7M、G8M,收尘器控制箱G13AC。
5.3.5、通知现场巡检工准备投料。
5.4、窑系统投料操作规程:5.4.1、窑尾温度升至1000℃以上、窑前看火工业电视看到明亮清晰的火焰,和明亮清晰的熟料出窑,可准备进行投料。
5.4.2、逐渐提高窑转速:窑皮完整的窑况,窑速提到1.6rpm以上,新砌窑砖窑速提到1.2rpm以上时准备进行投料。
5.4.3、提高窑尾高温风机转速。
5.4.4、根据进(出)增湿塔废气的温度高低,调节烟囱帽开度。
5.4.5、逐步增大窑头喂煤量,逐步增大高温风机液力耦合器开度,使拉风与喂煤匹配,保持窑内火焰的正常燃烧,液偶开度可逐渐提高至50%左右。
根据窑系统拉风情况酌情开启篦冷机热端风机:三室风机G27 M、四室风机G28M,保持窑头负压10-50 Pa。
5.4.6、当一级出口负压达2000Pa以上时开启分解炉喂煤设备,启动窑尾粉研称罗茨风机K20M(或备用罗茨风机K21M),启动尾煤粉研称,喂煤量为0.5吨/小时,根据炉温升高情况,增加喂煤量。
5.4.7、通知生料磨操作员调整废气处理系统。
5.4.8、当分解炉温度达820℃以上,一级预热器负压达2500Pa以上时投料。
投料量80-100t/h,窑速1.2-2.4r/min。
5.4.9、篦冷机连续推动后通知品质部控制室取熟料。
5.4.10、投料后要注意窑内火焰情况、预热器的温度和负压情况,要及时调整风、煤,保持系统温度稳定,五级预热器下料温度<900℃。
5.4.11、一级预热器出口温度<400℃时关闭烟囱帽。
5.5、窑系统加料操作规程:5.5.1、投料40分钟内是窑、预热器系统较易发生故障阶段,操纵控制力求平稳,并根据窑尾温度情况逐渐提高窑速、调控前后煤量。
40分钟后如窑工况稳定,窑尾温度已由投料后温度下降转变为温度不断增高,并且窑速已达2.4r/min以上,此时可进行加料,每次加料应在10t/次以内。
加料以后应注意观察系统温度的变化情况,稳定分解炉和五级预热器温度,如窑尾烟室温度能保持上升的趋势则可进行再一次加料。
如果需补挂窑皮,保持140t/h、2.8r/min稳定操作,等工艺部通知后再进行加料。
5.5.2、根据出窑熟料冷却情况,依次启动五室风机G29M、六室风机G30M,启动窑头电场G10ASR、G11ASR、G12ASR和窑头排风机G9M,同时调节窑头电收尘器风机风门开度,使窑头罩呈微负压。
5.5.5、最终加料到设计能力,投料量165-180t/h,拉风量一级出口负压4500-6000Pa,窑速3.60-3.90r/min。
5.5.6、调整窑头喂煤量和分解炉喂煤量,使窑头与分解炉用煤实际比例为4-3.5比6-6.5注意风煤要素的匹配。
5.5.7、操作过程中随时观察筒体扫描仪,稳定操作确保窑皮均匀稳定,根据情况及时开停胴体冷却风机。
6、系统异常情况处理:6.1、窜生料:(1)、现象:工业电视观察窑内气氛浑浊,窑尾温度下降,窑主电机电流下降,篦冷机一室篦下压力增大。
(2)、处理:减料、减窑速,适当增快篦速,适当增加窑头喂煤量。
(3)、恢复:待窑内气氛清亮、窑尾温度回升到正常范围后可考虑加料:加料前先加窑速,适当加煤然后加料,加料的幅度一般控制在10t/次内,并应防止再次窜生料。
6.2、窑尾烟室负压高:烟室斜坡积料:通知巡检工用压缩空气清吹。
窑内结圈:调整二、三风的比例,调整喷煤管内外风的比例,调整喷煤管位置,通过温度交替变换和火点位置的变化使窑圈垮落。
注意窑电流的变化,并观察窑口、篦冷机的监视镜头和胴扫情况,发现窑皮塌落,应适当减料,降低窑速,加大前煤喂煤量,通知窑头巡检工测量胴体温度。
6.3、C5级预热器堵塞:现象:预热器C5锥体出现正压或负压急剧下降。
处理:止料,通知巡检工清理。
6.4、窑胴体温度偏高:处理:1、利用筒体冷却风机对高温区域进行冷却;2、降低喂料量到正常喂料量的70-80%,降低窑速到正常窑速的70-80%,保持正常的煅烧温度,补挂窑皮。