模具分型面的设计原则
模具设计分型面的选择及设计原则

模具设计分型面的选择及设计原则一、分型面的选择分型面的选择也是模具设计的第一步,它受到产品的形状,外观,壁厚,尺寸精度,模穴数等很多因素的影响。
一般的产品拿到手里,大分型面确定我相信大家对这个基本没什么问题。
可对于很多有侧抽芯,或者涉及到枕位,碰穿,插穿时。
这些就有争论了,怎么去选择有时候还真不是个简单的事,因此,咱们这里来聊聊如何去选择分型面。
一般来说分型面的选择都会遵循以下的几个原则:1:符合产品脱模要求分型面也就是为了产品能顺利取出模具的。
因此,分型面的位置应该选在产品断面尺寸最大的部位,这是一条最基本的原则。
2:方位的确定在决定产品在模具里面的方位时,分型面的选择应该尽量防止产品形成侧孔或者侧扣位,应避免采用复杂的模具结构。
3:分型面的形状一般的产品,常常采用一个与注塑机开模运动方向垂直的分型面,特殊情况下才采用其它形状的分型面。
分型面的形状以方便加工和脱模为原则。
像某此弯曲的产品,分型时就得根椐它弯曲的曲率来。
4:确保产品外观和质量分型面不要选择在产品光滑的'外表面。
外观面一般来说是不允许有夹线及其它影响美观的线条出现的;有些有同心度要求的产品,得把有同心度要求的部分全部放到同一侧,这样才能保证其同心度。
5:有利于脱模一般的模具的脱模机构都是在动模的,所以选择分型面时应尽可能的使开模后产品留在动模。
因此对于有些有可能粘住定模的地方,我们往往会加做定模辅助脱模机构。
6:考虑侧向开模距离一般的侧向机械式开模的距离都是比较小的。
因此选择分型面时应把抽芯距长的方向选择在前后模开合的方向上,将短的方向做为侧向分型。
7:锁模力的考虑模具的侧向锁模力相对来说比较小,所以对于投影面积较大的大型产品,应将投影面积大的方向放在前后模开合模方向上,而将侧投影面积较小的作为侧向分型。
8:利于排气当把分型面做为主要排气时,应该把分型面设计在塑料流动的末端,以利于排气。
9:模具零件易于加工选择分型面时,应把模具分割成易于加工的零件,减小机加工难度。
模具分型面的设计和模仁大小的确定

一,分型面的设计分型面的设计和模仁的大小确定。
为了将产品从模具中取出,模具必须分成两个或数个部分,这些分离部分的接触表面通称为分型面分型面在模具中占有非常重要的位子,在设计模具时,首先考虑的就是这套模具分型面怎么做,如果连模具的分型都不知道,哪后须的工作也没法做了.到企业应聘模具设计时,往往要现场动手的就是做分型面,这关过不了,哪被录取的希望基本为零,如分型面做的又快又好,那你的成功率就大了.二.外观件的分型面的选取:1.肉眼观看.2.客户2D图纸指定.3.要保证母模胶位少,公模胶位多.如何利用UG软件选取分型面:1.利用拔模分析选择(粉红色与深兰色交界处或粉红色与绿色交界处)2.利用注塑模向导,自动抽取分型线.三.内置件的分型面的选取:1.要保证母模胶位少,母模尽量不要有机构.2.利用拔模分析分型面通常分为1.水平分型.2.垂直分型.3.倾斜分型(如图)4.台阶型分型面三,模仁和模架的确认。
产品的分模面大致确定以后,接下来就是确定模仁和模架的尺寸了模架尽量采用标准模架和标准配件,这样有利于缩短模具的制造周期和降低成本设计界经常用的模架品牌有:龙记(LKM),富得吧(FUTABA),名利,天祥,重村等当模具比较特殊或客户特别要求时,须对模架得形状,尺寸,材料作更改时,就需重新设计模架,这种情况下,定购模架时就需要向供应商提供详细得图面,并标注上与标准模架得不同之处,当然,这样得模架单价也较贵,供应商一般可以给客户提供架初加工和精加工,一般我们都要求进行粗加工及粗掏模穴即可一.模架和模仁尺寸的确定模架的大小主要取决于产品的大小和结构,对模具而言,在保证足够的强度下,模具设计的越紧凑越好.根据产品的外形(投影面积和高度)和结构(侧向分型和抽芯)来确定模仁的尺寸,确定好模仁的尺寸以后,就可以确定模架的尺寸了以下是模仁和模架尺寸确定的参考图表以上数据,只是作为设计时的一个参考,在设计时还要注意一下几点;1.当产品高度过高时(X>=D时),应适当加大D,加大值=(X-D)/2.2.有时为了冷却水道和固定螺丝的需要,也要对尺寸加以调整.3.当产品结构复杂,须特殊分型或顶出机构,或须加滑块等机构时,也应对模仁和模架尺寸进行修改.应适当加大模架和厚度.2.方铁高度的确定:方铁的高度应保证有足够的顶出行程和5-10MM预留量,以保证产品完全顶出,并且上顶板不会碰到公模板顶部3.模架整体尺寸的确定:模具定好以后,因对模架整体结构进行校核,看模架是否适合,所选定的或客户指定的注塑机的型号,包括外形尺寸,厚度,最大开模行程,及顶出方式和顶出行程等.4.模仁材料的选定;制品为一般的塑胶,如ABS,PP,PC,等,模仁因选用P20,NAK80,718.等预硬钢,如用高光洁度或透明的塑料制品,如PMMA,PS,AS,等因选用420等耐腐蚀不锈钢,含玻纤增强的塑胶,因选用H13,SKD61等热处理钢,当制品材料为PVC或POM和加了阻燃剂时因选用420,2316等不锈钢.具体在"模具用钢材"一节再详细学习。
有关模具的分型面基本原则
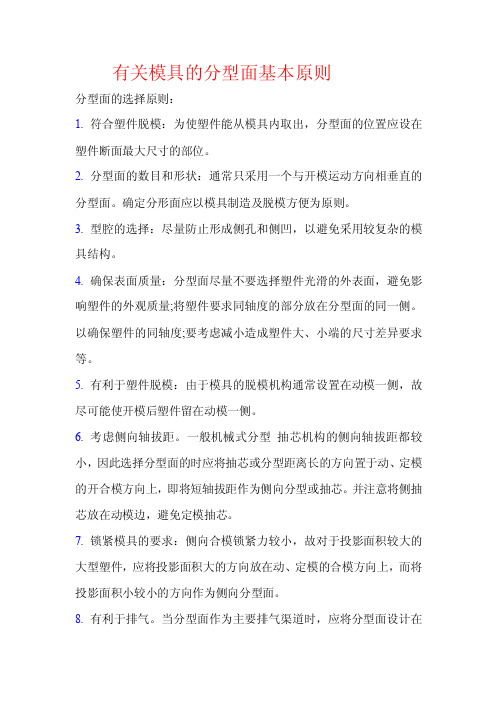
有关模具的分型面基本原则分型面的选择原则:1.符合塑件脱模:为使塑件能从模具内取出,分型面的位置应设在塑件断面最大尺寸的部位。
2. 分型面的数目和形状:通常只采用一个与开模运动方向相垂直的分型面。
确定分形面应以模具制造及脱模方便为原则。
3.型腔的选择:尽量防止形成侧孔和侧凹,以避免采用较复杂的模具结构。
4.确保表面质量:分型面尽量不要选择塑件光滑的外表面,避免影响塑件的外观质量;将塑件要求同轴度的部分放在分型面的同一侧。
以确保塑件的同轴度;要考虑减小造成塑件大、小端的尺寸差异要求等。
5.有利于塑件脱模:由于模具的脱模机构通常设置在动模一侧,故尽可能使开模后塑件留在动模一侧。
6.考虑侧向轴拔距。
一般机械式分型抽芯机构的侧向轴拔距都较小,因此选择分型面的时应将抽芯或分型距离长的方向置于动、定模的开合模方向上,即将短轴拔距作为侧向分型或抽芯。
并注意将侧抽芯放在动模边,避免定模抽芯。
7.锁紧模具的要求:侧向合模锁紧力较小,故对于投影面积较大的大型塑件,应将投影面积大的方向放在动、定模的合模方向上,而将投影面积小较小的方向作为侧向分型面。
8.有利于排气。
当分型面作为主要排气渠道时,应将分型面设计在塑料的流动末端,以利于排气。
9.模具分型面的选择和设计应该利于加工。
如: 1、主分型面为平面的情况,分型面设计时要考虑方便于磨床加工。
2、主分型面为复杂曲面,分型面设计时要考虑方便于NC加工,避免EDM加工。
分型面在不同情况下的设计要求<一>、主要分型面为平面的情况:主要分型面与开模方向垂直时,分型面可直接拉伸而成。
(见图一)*对于这种分型面用自动分模时常会在一些转角位有一些微小的起伏(高度方向几个丝的变化),对制作Fit模有一定的影响,应注意用平面替换,以利于磨床磨出。
<二>、主要分型面为斜面的情况:主要分型面与开模方向不垂直时,分型面沿斜面延伸一段后在分型面两端做平位,以利于加工定位及Fit模。
模具设计分型面的选择及设计原则

模具设计分型面的选择及设计原则
模具,是将塑料或金属按照产品设计图纸要求的形状和尺寸加工出来
的工具。
模具的设计和制造是任何塑料或金属制品的有效生产的必要环节,型面的选择和设计原则对模具的质量和成型效果有着重要的影响。
一、模具型面选择
1、了解加工工件材料特性,首先要了解加工工件的材料特性,以便
根据材料的性能、加工精度需求等,决定模具的塑料型面类型。
模具的材
料种类有:定型塑料、半定型塑料、硬质塑料、弹性体塑料、铝热模塑料等。
2、根据产品型号和尺寸,确定型面形状和尺寸;
3、根据成型材料的特性,确定模具型面料的厚度;
4、根据产品成型过程尺寸的变化,确定型面的设计模式;
5、根据成型方式及模具结构,确定腔体的形状;
6、根据负压上模原理,确定模具型口的设计;
7、确定附件的设计,包括定位件、导流件等;
8、根据设计要求,制定模具的总体尺寸和技术要求;
9、根据成型工艺需要,确定模具表面处理方式。
二、模具设计原则
1、重点考虑模具的结构及制作的简单方便性,便于模具的调整和维护;。
注塑模具分型面的选择原则
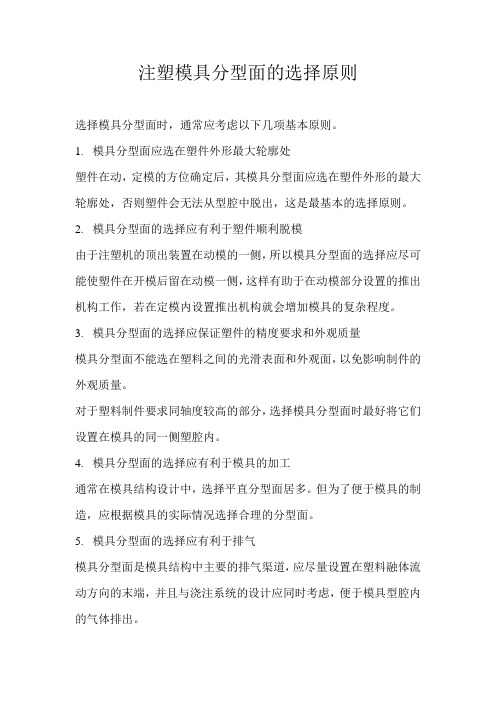
注塑模具分型面的选择原则
选择模具分型面时,通常应考虑以下几项基本原则。
1. 模具分型面应选在塑件外形最大轮廓处
塑件在动,定模的方位确定后,其模具分型面应选在塑件外形的最大轮廓处,否则塑件会无法从型腔中脱出,这是最基本的选择原则。
2. 模具分型面的选择应有利于塑件顺利脱模
由于注塑机的顶出装置在动模的一侧,所以模具分型面的选择应尽可能使塑件在开模后留在动模一侧,这样有助于在动模部分设置的推出机构工作,若在定模内设置推出机构就会增加模具的复杂程度。
3. 模具分型面的选择应保证塑件的精度要求和外观质量
模具分型面不能选在塑料之间的光滑表面和外观面,以免影响制件的外观质量。
对于塑料制件要求同轴度较高的部分,选择模具分型面时最好将它们设置在模具的同一侧塑腔内。
4. 模具分型面的选择应有利于模具的加工
通常在模具结构设计中,选择平直分型面居多。
但为了便于模具的制造,应根据模具的实际情况选择合理的分型面。
5. 模具分型面的选择应有利于排气
模具分型面是模具结构中主要的排气渠道,应尽量设置在塑料融体流动方向的末端,并且与浇注系统的设计应同时考虑,便于模具型腔内的气体排出。
6. 模具分型面的选择应考虑模具的侧向抽芯
为了保证侧向抽芯的放置容易和抽芯机构的动作顺利,选择模具分型面时,应以浅的侧向凹孔或短的侧向凸台作为抽芯方向,将较深的凹孔或较高的凸台放置于合模的方向,并尽量把侧向抽芯机构放置在动模一侧。
以上信息由:金马泰模具厂提供。
塑料成型工艺及模具设计 简答题(全)复习要点

c.承受一定的侧向压力 保证模具正常工作。
11. 何为分子定向?分子定向与什么有关?其会产生什么影响?
答:塑料中的聚合物大分子、细而长的纤维状填料分子在成型过程中由于受到应力作用而产生分子整齐、平行排列的现象,这种现象称之为分子取向。
答:
a、 实现推落塑件或将塑件推至所要求的高度。
b、 不造成塑件变形和损坏。
c、 不损坏塑件外观和使用性能。
d、 机构运行安全可靠
6、稳定剂的作用是什么?
答:为了抑制和防止塑料在加工成型或使用过程中,因受热、光、氧等作用而发生降解、氧化断链、交链等现象而致使塑料性能遭到破坏,加入适当的稳定剂,使塑料的性能稳定。
答:塑件的尖角部位在成型时会产生应力集中,当受到冲击振动时易开裂(4分);塑件设计成圆角,不仅避免产生应力集中,提高了塑件强度,还有利于塑件的充模流动(3分);同时模具型腔对应部位亦呈圆角,这样使模具在淬火和使用时不致因应力集中而开裂,提高了模具的坚固性(3分)
13.为什么模具温度及其调节具有重要性?(8分)
c、 机构运行安全可靠
9、为什么说塑件的壁厚不能过小或过大?
塑件壁厚最小值应以满足塑件在使用时要求的强度和刚度,并能使塑料熔体顺利充满整个型腔为限。
a、壁厚过小,因流动阻力极大,因而成型形状复杂或大型塑件困难。
b、壁厚过大,不但塑料用得多,而且制件易出现内部空孔,外部凹陷缺陷,成型周期延长。
4\ 什么是热固性塑料的固化特性,与哪些因素有关?
固化特性是热固性塑料特有的性能,是指热固性塑料成型时完成交联反应的过程。固化速度不仅与塑料品种有关,而且与塑件形状、壁厚、模具温度和成型工艺条件有关,采用预压的锭料、预热、提高成型温度,增加加压时间都能加快固化速度。此外,固化速度还应适应成型方法的要求
模具分型面的设计原则

模具分型面的设计原则1.参考工艺要求:模具的分型面必须符合产品的工艺要求。
分析产品的形状特点、结构特点、尺寸精度要求等,确定各个分型面的位置和形状。
2.尽量少的分型面:分型面越少,模具的制造成本越低,生产效率越高。
因此,在设计时应尽量减少分型面的数量,采用合理的设计来实现尽量少的分型面。
3.分型面的尺寸精度要求:分型面的尺寸精度要求直接影响模具的生产成本和加工难度。
因此,应根据实际需要合理确定分型面的尺寸精度要求。
4.考虑模具的制造工艺:在设计分型面时,需要考虑到模具的制造工艺,特别是模具的加工、组装和调试工艺。
尽量避免出现难于加工和调试的分型面,以减少模具的制造周期。
5.尽量采用直线分型面:直线分型面易于加工,可减少模具制造周期和成本。
因此,在设计分型面时,应尽量采用直线分型面,避免采用曲线或复杂的形状。
6.尽量采用平面分型面:平面分型面易于加工和调试,且模具的使用寿命较长。
因此,在设计分型面时,应尽量采用平面分型面,避免采用曲面或复杂的形状。
7.考虑产品的浇注和冷却:在设计分型面时,应考虑产品的浇注和冷却。
合理设计分型面的位置和形状,可使产品的浇注平稳,避免产生气泡或缺陷;同时,也能保证产品的冷却效果良好,使产品达到预期的性能和质量。
8.考虑模具的维护和维修:在设计分型面时,应考虑模具的维护和维修。
合理设计分型面的位置和形状,可使模具的保养和修复更加方便,减少模具的损耗和维修成本。
9.考虑产品的脱模:在设计分型面时,应考虑产品的脱模。
合理设计分型面的位置和形状,可使产品的脱模更加容易,减少脱模力和脱模损伤,提高模具的使用寿命。
总之,模具分型面的设计需要考虑到产品的形态特征和结构特点,参考工艺要求和模具制造工艺,以及产品的浇注、冷却和脱模等因素。
合理设计分型面,可提高模具的生产效率和成形质量,降低模具的制造成本和维护成本。
压铸模分型面的选择原则

压铸模分型面的选择原则压铸模是制造压铸件的关键工具,它的设计和制造质量直接影响到压铸件的质量。
而压铸模的分型面选择是决定压铸模结构的重要一环。
正确选择分型面可以有效解决压铸件的脱模问题,提高生产效率和产品质量。
本文将介绍压铸模分型面选择的原则和注意事项。
一、分型面的基本原则1. 简洁原则:分型面应尽量简洁,避免过多的分型面,以减少模具制造和调试的难度。
2. 平面原则:分型面应选择平整、光滑的面,以确保模具的脱模性能,并减少模具磨损和维护成本。
3. 压铸件结构原则:分型面应尽量选择与压铸件结构相连的面,以保证模具的脱模性能和压铸件的几何形状。
4. 经济原则:分型面应尽量选择便于加工和调试的面,以降低模具制造成本和生产成本。
二、分型面的具体选择1. 压铸件外形面:压铸件的外形面是最基本的分型面,一般情况下应选择与外形最接近的面作为分型面。
如有需要,可以适当增加分型面以保证脱模性能。
2. 内部凸起面:压铸件中的内部凸起面需要选择与之相对的面作为分型面,以确保模具能够顺利脱模。
3. 内部凹陷面:压铸件中的内部凹陷面需要选择与之相对的面作为分型面,并适当增加分型面以保证脱模性能。
4. 斜面:斜面是用来顺利脱模的重要分型面,压铸件中的斜面应选择与之相对的面作为分型面,并注意斜面的倾斜角度和长度。
5. 滑动面:滑动面是用来顺利脱模的重要分型面,压铸件中的滑动面应选择与之相对的面作为分型面,并注意滑动面的平整度和润滑性。
6. 长条形面:压铸件中的长条形面需要选择与之相对的面作为分型面,并适当增加分型面以保证脱模性能。
三、分型面的注意事项1. 分型面的选择应结合压铸件的结构特点和工艺要求进行综合考虑,以确保模具能够顺利脱模,并满足产品的几何形状和表面质量要求。
2. 分型面的位置应尽量靠近压铸件的表面,以减少模具的开合力和磨损。
3. 分型面的设计应考虑模具的制造和维护成本,尽量简化分型面的结构,并减少模具的加工难度。
- 1、下载文档前请自行甄别文档内容的完整性,平台不提供额外的编辑、内容补充、找答案等附加服务。
- 2、"仅部分预览"的文档,不可在线预览部分如存在完整性等问题,可反馈申请退款(可完整预览的文档不适用该条件!)。
- 3、如文档侵犯您的权益,请联系客服反馈,我们会尽快为您处理(人工客服工作时间:9:00-18:30)。
a 不合理,因为这样的 分型,型芯的加工比 较困难,而图(b)就 比较合理。
a不合理,因为塑料熔 体的末端未贴合分型 面,故会产生排气不 良而引起塑件困气, 烧黑的现象,而图 (b)就比较合理。
P3/3
举 例 说 五明 、:
制 品 模 号 1、 :
制 品 E R 20 E 分 型 面 写 真 , 如 图 ( 一 2、 )
倾 斜 分 型 面 ( 见 图 2、 b)
阶 梯 分 型 面 ( 见 图 3、 c)
曲 面 分 型 面 ( 见 图 4、 d)
简 图 如 下 :
分 型 面 设 计 的 原 四则 、:
序
号
原则
分型面应选择在塑 1 件外形的最大轮廓
处
分型面的选取应有 2 利于塑件的留模方
式
简图
说明
b合理,因为分型面取 在最大轮廓处,能顺 利脱模;
求
a不合理,因为这样很 容易产生夹口披锋, 影响塑件的外观,而b
就比较合理。
分型面的选取应能 4 保证塑件的精度要
求
5
分型面的选取应有 利于模具的制造。
6
分型面的选取应有 利于模具的排气。
a不合理,因为这样不 能保证双联塑胶齿轮 的同轴度要求,通常 在模具设计时应将有 同轴度要求的部分设 计在同一模板内,如 (图b)所示,比较合
P2/3
b合理,因为分型面取 在动模上,开模后, 塑件由于收缩会包紧 在动模的型芯上,而 且模具的推出机构一
b合理,因为分型面取
在动模上,开模后,
分型面的选取应有
塑件由于收缩会包紧
2 利于塑件的留模方
在动模的型芯上,而
式
且模具的推出机构一
般设在动模上,所以
脱模容易。
动模板 定模板 动模板 定模板
分型面的选取应能 3 满足塑件的外观要
模 具 分 型 面 的 设 计 原 则
引 一言 、:
在设 计塑 料成 型模 具 时, 分型 面的 选择 是一 个重 要的 设计 内 容, 分型 面
CRD
200 5.8.4 16:09 :39
'05.8.04
張国平
2005/7/8 作成:CRD陈利文
P1/3
选择 合 理, 模具 结构 简 单, 塑件 容易 成形 、脱 模, 并且 塑件 品质 高, 如 果分 型面 选择 不合 理, 模具 结构 变得 复 杂, 塑件 成形 困 难, 塑件 的品 质
ER20E
此处为 ER20E制 品 的分型面
模 具 分 型 面 的 写 真 , 见 图 ( 二 3、 )
图 (一)
此面为 ER20E模 具的分型 面
(动 模)
左图 已放大
图(二)
确 定 制 品
E
R
20
E 分 型 面 的 依 据 4、 :
分型面选 择在制品 ER20E的 1 最大轮廓 、 处。 分型面的 选择有利 于制品 ER20E留 在动模, 2 便于脱模 、。 分型面的 选择有利 于金属镶 3 件的安装 、。
以上
差, 可 见, 分型 面的 选择 相对 于模 具结 构的 设计 非常 重要 。
分 型 面 的 概 二念 、:
分型 面是 模具 动模 和定 模的 结合 处, 通常 是塑 件最 大外 形 处, 是为 了塑 件和 冷
凝料 取出 而设 计的 。
分 型 面 的 形 三式 、:
平 面 分 型 面 ( 见 图 1、 a)