分型面的选择
分型面的选择

第二节分型面的选择一、分型面及其基本形式为了塑件的脱模和安放嵌件的需要,模具型腔由两部分或更多部分组成,这些可分离部分的接触表面即称为分型面。
一副塑料模具根据需要可能有一个或两个以上分型面。
分型面可能是垂直于合模方向或倾斜于合模方向,也可能是平行于合模方向。
合模方向通常是指上模与下模、动模与定模闭合的方向.通常分型面的形状有平面、斜面、阶梯面、曲面几种形式。
二、分型面选择的一般原则分型面的选择很重要,它对塑件的质量、操作难易、模具结构及制造影响很大。
在选择分型面时应遵循以下基本原则:1。
分型面应选在塑件外形最大轮廓处,才能使塑件顺利地脱模。
2。
确定有利的留模方式,便于塑件顺利脱模。
在注射成型时,因推出机构一般设置在动模一侧,故分型面应尽量选在能使塑件留在动模内的地方。
3. 当孔间距较小时,却难以设置有效的推出机构,若按图(b)分型,只需在动模上设置一个简单的推件板作为脱模机构,故较为合理。
4。
保证塑件的精度要求。
对于同轴度要求高的塑件,在选择分型面时,最好把要求同轴部分放在分型面的同一侧(见右下图),避免由于合模精度的影响而引起形状和尺寸上的偏差.5.满足塑件的外观质量要求。
因为分型面不可避免地要在塑件上留下痕迹,所以分型面最好不要选在塑件光滑的外表面或带圆弧的转角处.6.便于模具加工制造。
7。
考虑成型面积和锁模力。
为了可靠地锁模以避免胀模溢料现象的发生,选择分型面时应尽量减少塑件在合模分型面上的投影面积。
8。
对侧向抽芯的影响。
一般侧向分型抽芯机构的侧向抽拔距离都较小,故选择分型面时,应将抽芯或分型距离长的一方放在动、定模开模的方向上,而将短的一方作为侧向分型的抽芯.9. 考虑排气效果。
分型面应尽量与型腔充填时塑料熔体的料流末端所在的型腔内壁表面重合,以利于把型腔内的气体排出。
思考与练习1。
分型面选择的一般原则有哪些?试举例说明。
2。
分析(作业)产品零件图,确定分型面的位置。
3给图中两个塑件选择分型面,并注明动模和定模的方向。
简述分型面的选择原则

简述分型面的选择原则分型面是指在地质勘探中,根据地层内部岩性、构造特征以及地下水分布等因素,将地下岩石分为不同的类型,从而对地下岩石进行分类和划分的方法。
在实际的勘探工作中,分型面的选择是非常重要的,它直接关系到勘探结果的准确性和可靠性。
本文将从几个方面来介绍分型面的选择原则。
地层的岩性是选择分型面的重要因素之一。
岩性是指岩石的物理和化学性质,包括岩石的成分、结构和纹理等。
不同的岩性具有不同的物理特征和岩石学特征,在地质勘探中,可以通过分析岩性来判断地下岩石的性质和分布。
因此,在选择分型面时,应根据地层的岩性特征来确定分型面的位置和方向。
构造特征也是选择分型面的重要考虑因素之一。
构造特征是指地层中的断裂、褶皱、岩层倾角等地质构造现象。
构造特征会对地下岩石的分布和性质产生重要影响,因此,在选择分型面时,应考虑地层的构造特征,选择能够反映地层构造特征的分型面。
地下水分布也是选择分型面的重要因素之一。
地下水是地下岩石中的水分,它对地层的物理特性和化学特性有着重要影响。
在地质勘探中,地下水的分布和流动状况对地下岩石的性质和分布具有重要影响,因此,在选择分型面时,应考虑地下水的分布情况,选择能够反映地下水分布的分型面。
地层的厚度和密度也是选择分型面的重要因素之一。
地层的厚度和密度会对地层的物理特性和化学特性产生重要影响,因此,在选择分型面时,应考虑地层的厚度和密度,选择能够反映地层厚度和密度的分型面。
综合考虑以上因素,选择能够反映地下岩石性质和分布的分型面。
在实际的勘探工作中,需要根据具体的勘探目的、勘探区域的地质条件和勘探方法等因素,综合考虑以上因素,选择合适的分型面。
选择分型面时,要尽量减小误差,提高勘探的准确性和可靠性。
分型面的选择原则主要包括地层岩性、构造特征、地下水分布、地层厚度和密度等因素。
在选择分型面时,需要综合考虑以上因素,选择能够反映地下岩石性质和分布的分型面,以提高勘探的准确性和可靠性。
7-分型面的选择
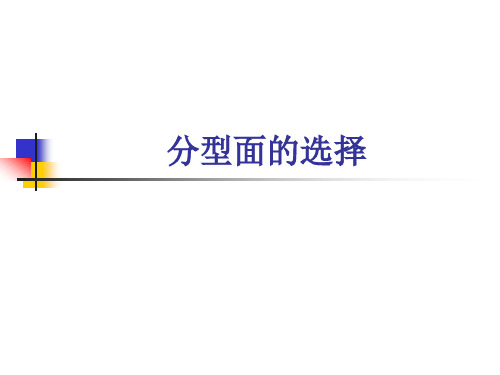
2、分型面应保证塑料件尺寸精度要求。
提高模具制造精度外,与分型面的选择 有很大关系。如选择图20(b)设置分型 面则大小齿轮同在动模内,动、定模合 模误差没有影响,而且在加工大小齿轮 在同一动模型腔内,有较好的加工工艺, 能有效提高大小齿轮同轴度。
3、应考虑塑料件外观质量。
在分型面的位置都会留有一圈飞边。飞边
7、有利于塑料注射模分型面的加工。 分型面选择时,考虑模具零件制造
的难易程度,分型面精度是整个模具精 度的重要部分,力求平面度和动、定模 配合面的平行度在公差范围内。如选择 分型面是斜面或曲面,加工的难度增大, 并且精度得不到保证,易造成溢料飞边 现象。
分型面的选择
一、复习旧课引入新课
定义:模具用以取出塑件和(或) 浇注系统凝料的可分离的接触表面。
二、分型面的形状
(1)分型面的表达方法:如图18所示 用短,粗实线标出分型面位置,箭 头表示分离动作方向。
Байду номын сангаас
图18 分型面的表达方法 (2)分型面的形状有平面、斜面、阶梯面和曲面。
三、分型面选择的一般原则
不容易清除彻底,会影响塑料件外观质量,
即使这些毛边脱模后立即割除,但仍会在
塑料件上留下痕迹,影响塑料件外观,故
分型面应避免设在塑料件光滑表面上,如
图21所示,图21(b)较合理,产生的飞
边不影响塑料件外观。
图
21 分型面对塑料件外观质量的影响
5、有利于塑料注射模型腔内排气。
分型面应尽量设置在塑料熔体充满末端 处,这样分型面就可以有效排除型腔内 积聚的空气。对中、小型塑料件因型腔 较小,空气量不多,可借助分型面的缝 隙排气。如图22(a)所示的结构,排气 效果较差;图22(b) 所示的结构,排气 效果较好。
分型面的选择原则
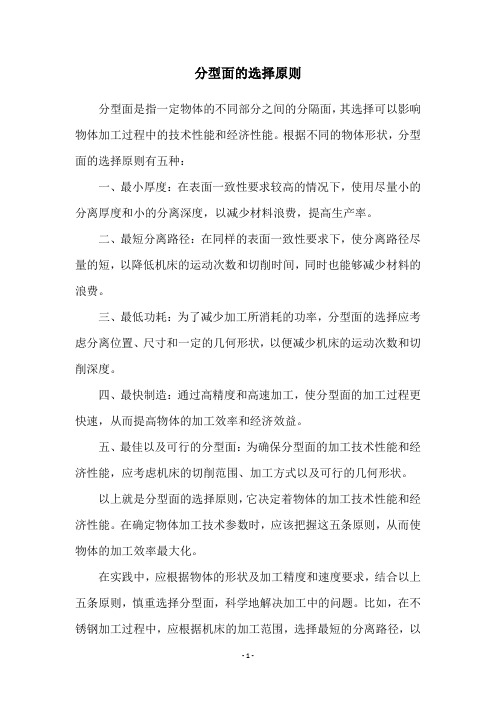
分型面的选择原则
分型面是指一定物体的不同部分之间的分隔面,其选择可以影响物体加工过程中的技术性能和经济性能。
根据不同的物体形状,分型面的选择原则有五种:
一、最小厚度:在表面一致性要求较高的情况下,使用尽量小的分离厚度和小的分离深度,以减少材料浪费,提高生产率。
二、最短分离路径:在同样的表面一致性要求下,使分离路径尽量的短,以降低机床的运动次数和切削时间,同时也能够减少材料的浪费。
三、最低功耗:为了减少加工所消耗的功率,分型面的选择应考虑分离位置、尺寸和一定的几何形状,以便减少机床的运动次数和切削深度。
四、最快制造:通过高精度和高速加工,使分型面的加工过程更快速,从而提高物体的加工效率和经济效益。
五、最佳以及可行的分型面:为确保分型面的加工技术性能和经济性能,应考虑机床的切削范围、加工方式以及可行的几何形状。
以上就是分型面的选择原则,它决定着物体的加工技术性能和经济性能。
在确定物体加工技术参数时,应该把握这五条原则,从而使物体的加工效率最大化。
在实践中,应根据物体的形状及加工精度和速度要求,结合以上五条原则,慎重选择分型面,科学地解决加工中的问题。
比如,在不锈钢加工过程中,应根据机床的加工范围,选择最短的分离路径,以
最短的时间完成加工;在铝合金加工过程中,应根据铝合金的表面要求,选择最小的分离厚度,以提高加工的精度。
总之,分型面的选择不仅考虑物体的形状,加工方式和精度要求,而且要考虑加工中的技术性能和经济性能,以便提高物体的加工速度和效率,改善加工品质,降低生产成本。
分型面的选择原则

分型面的选择原则
分型面的选择可以根据以下原则来进行:
1、比较传统的方法是根据价钱、位置、形态、质量和功能来选择分型面。
这些方面可以用一定的数字或者等级来衡量,让不同的分型面更容易对比。
2、分型面的选择也可以根据对未来的调查和分析考虑,比如将要做的分析和调研,包括技术参数、生产能力、效率、品质、可靠性等因素,在把这些要素都考虑进去的情况下,选择当前最能满足未来发展的分型面。
3、分型面的选择还要考虑生产中的特殊环境,比如噪声、温度、湿度、物料种类、重量、尺寸以及其他特殊要求,只有找准最能满足生产条件的分型面,才能够正确的生产。
4、分型面的选择还要考虑可操作性,在设计时,要将操作简便、人性化作为首要考虑,对工作人员的指导及操作程度也要考虑入内。
5、分型面的选择还要考虑可靠性,要求分型面的失效率低,故障率低,使用寿命长,能适应一定的变化,保证能够正常生产。
分型面的选取

8
圖2
主分型面
9
比較圖1與圖2﹕ 圖1﹕主分型面取在成品中心﹐母模仁凸出 了母模板﹐滑塊依靠后跟塊來逼緊﹐模板 強度減弱
圖2﹕主分型面位于母模仁的最低面上﹐滑 塊依靠母模板自然逼緊(省去了耐磨塊)﹐ 模板強度增加
10
3﹑依特殊模具結構來確定主分型面
11
上圖所示為爆炸式滑塊結構﹐主分型面的 選取要分別考慮滑塊及模板的強度問題
17
總結﹕ 以上兩種方法所能解決的問題有限﹐都 不能達到很完美的效果﹐因此﹐我們采 取以下方式加以改善:
18
母模側
放大后
PL面 公模側
左圖紅色線所 示為分模線﹐ 公母模仁在此 靠破
19
注﹕1.此種分模方式成品的1/3在母模﹐2/3在 公模
2.為了確保成品最終留在公模側﹐母模 側的拔模角度要大于公模側
品質
23
4﹑盡量減少側向倒勾,簡化模具結構
見下圖
24
此產品外觀形狀怪異﹐通
過多個靠破與插破面﹐可用公母模仁直接 成型。圖中紅色線所示為分模線
25
無法直接脫模
可順利脫模
26
5﹑便于加工
母模側 PL面
公模側
此處必須放電加工浪 費加工工時
27
母模側 PL面
公模側
將PL面改在成品底部﹐便于加工
28
3
分型面﹕我們通常稱为PL面﹐它是公模 (动模)与母模 (定模)的分界面,是取出塑件 或浇注系统凝料的面
主分型面﹕公母模板的分界面 分型面
次分型面﹕模仁部分﹐涉及成品 的分界面
4
分型面﹐在一些制品中客戶已作具體規 定﹐但在很多的模具設計中要由模具設計 人員來確定。一般來講﹐在平面上的分型 面比較容易處理﹐但碰到立體形式的分型 面就應當特別注意。分型面的選擇應遵照 以下原則﹕
3.3.1分型面选择.
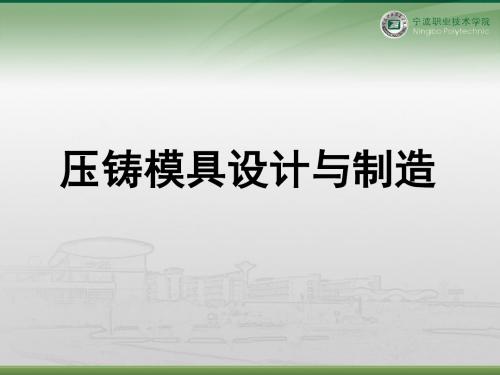
1
分型面选择
• 3.管接头分型面的确定
确定管接头铸件分型面
结束语
谢
谢
压铸模具设计与制造
任务描述
分型面选择
主讲人:柯春松
1
分型面选择
•1.分型面的概念及类型 • 分型面就是动、定模分开的面,按
照分型面的形状,分型面一般可分为平 直分型面、倾斜分型面、阶梯分型面和 曲面分型面,如图所示。
1
分型面选择
分型面的基本形式
1
分型面选择
2.选择分型面的基本原则
• (1)分型面应选择在压铸件外形轮廓尺寸最大处; • (2)选择的分型面应使压铸件在开模后留在动模; • (3)分型面选择应保证压铸件的尺寸精度和表面质量; • (4)分型面应尽量设置在金属液流量动方向的末端; • (5)分型面选择应便于模具加工。
分型面的选用原则知识目标

分型面的选用原则知识目标一、什么是分型面分型面是指用于加工工件外轮廓的切削工具。
它们通常由高速钢或硬质合金制成,具有不同的形状和尺寸,用于加工不同形状的工件。
二、分型面的分类根据形状和用途的不同,分型面可以分为以下几类:1. 平面刀:用于加工平面和平面上的凹槽,常见的有平面铣刀、T 型槽刀等。
2. 锥面刀:用于加工锥面、圆锥孔等,常见的有圆锥铣刀、锥度刀等。
3. 面铣刀:用于加工工件的平面,常见的有面铣刀、立铣刀等。
4. 压面刀:用于加工工件的压面,常见的有球头铣刀、圆弧铣刀等。
5. 镗削刀:用于加工孔的内表面,常见的有直柄镗刀、螺纹镗刀等。
三、分型面的选用原则在选择分型面时,应根据具体的加工要求和工件的形状来确定。
以下是一些常见的选用原则:1. 加工要求:根据工件的加工要求选择合适的分型面。
比如,当需要加工平面时,应选择平面刀;当需要加工锥面时,应选择锥面刀。
2. 工件形状:根据工件的形状选择合适的分型面。
比如,当需要加工圆锥孔时,应选择圆锥铣刀;当需要加工平面时,应选择平面铣刀。
3. 材料选择:根据被加工材料的硬度和性质选择合适的分型面。
对于硬度较高的材料,应选择耐磨性好的硬质合金刀具;对于软性材料,可以选择高速钢刀具。
4. 刀具尺寸:根据工件的尺寸确定刀具的尺寸。
刀具尺寸应与工件的尺寸相匹配,以确保加工质量。
5. 刀具刃数:根据工件的加工要求和切削条件选择合适的刀具刃数。
一般来说,刀具刃数越多,加工效率越高,但刃数过多也会增加切削阻力。
6. 切削速度:根据被加工材料的硬度和性质选择合适的切削速度。
切削速度过高会导致切削刃磨损加剧,速度过低则会降低加工效率。
7. 切削深度:根据工件的硬度和性质选择合适的切削深度。
切削深度过大会增加切削力和切削温度,降低刀具寿命。
8. 切削条件:根据工件的加工要求和切削条件选择合适的切削方式和切削液。
不同的切削方式和切削液适用于不同的加工要求和材料。
四、总结分型面的选用原则是根据工件的形状、加工要求和材料的硬度等因素来确定的。
- 1、下载文档前请自行甄别文档内容的完整性,平台不提供额外的编辑、内容补充、找答案等附加服务。
- 2、"仅部分预览"的文档,不可在线预览部分如存在完整性等问题,可反馈申请退款(可完整预览的文档不适用该条件!)。
- 3、如文档侵犯您的权益,请联系客服反馈,我们会尽快为您处理(人工客服工作时间:9:00-18:30)。
内容简介:
本模块讲述分型面的形式和选择;注塑模的 排气系统设计;成型零部件的结构设计; 成型零 部件工作尺寸计算;注塑模具型腔壁厚计算要求 和计算方法。
学习目的和要求:
1、会运用塑料模具分型面的基本原则, 针对不同塑件选择分型面。
2、掌握成型零件尺寸的计算方法。 3、会运用公式和查表选择数据确定型 腔壁厚和底板厚度;
斜分型面的型腔部分比平直分型面的型腔更容易加工
图示叠形螺母,如选用b-b分型面,则机械加工困难,只 能采用特殊的加工方式加工模具,且不易抛光。如改为a- a分型,则加工简单,机械和钳工结合即可以完成。
7、侧向分型面与主分型面协调
有侧凹或侧孔的塑件,当采用自动侧向分型抽芯机构时,除了液压 抽芯能获得较大的侧向抽拨距外,一般分型抽芯机构侧向抽拨距都 较小,取分型面时应首先考虑将抽芯或分型距离长的一边放在动、 定模的开模方向,而将短的一边作为侧向分型抽芯,
为了弥补这个缺陷,常采用如下两种方法:
在型腔一侧设置斜契式镶块
两个模腔对称布置
三、分型面的选择原则
分型面的位置关系到成型零部件的结构形状、塑件的正常成型与脱模 以及模具制造成本,因此,在选择分型面时,尽量遵守以下原则:
1、有利于塑件的顺利脱模
2、保持塑件的外观整洁
3、便于排气
4、应考虑开模时塑件留动模
由于模具制造误差,导致动、定模偏移不易保证塑件质量。采用 右图结构,则可通过锥面精确定位,保证壁厚要求。
图示塑件要求保证高度h值,左图结构会因为模具合模的紧密程 度影响h值大小;右图塑件h值则可直接通过型腔深度来保证, 与合模无关。
6、要有利于模具成型零件的 加工
图示右图采用平面式分型面,看似简单,实际上型芯、型腔加工都十 分困难,采用左图形式(斜面式分型面)则使加工简单。
塑件不止有一个抽芯的时候,在选择分型面时要使较大的 型芯与开模方向一致
8、分型面应与注塑机参数相一致
一般情况下,应尽量减少塑件在分型面上的投影面积,以
防止溢料 当塑料的投影面积接近注塑机的最大注射面积的临界情况时,应采用右图 形式。
当能够满足注塑机参数要求,且模具闭合高度过大时,可采用右图形式。
9、考虑脱模斜度的影响
2、保持塑件的外观整洁 塑料熔体容易在分型面上产生飞边,影响外观质量,因 此,在光滑平整表面或圆弧曲面上应尽量避免选择分型 面。
分型面的选择要满足塑件表面质量的要求
3、便于排气
即尽量和料流的末端相重合。
图示A处形成盲肠状,不易排气,容易发生充填 不满,出现气泡现象。可改为右图形式。
当分型面作为主要排气面 时,应将分型面设在料流 的末端,以利排气。一般 常在分型面的凹模一侧开 设一条深0.025~0.lmm、 宽1.5—6mm的排气槽,也 可利用顶杆、型腔或型芯 镶块进行排气。
5、应能够保证塑件的精度要求
同心度要求高的塑件,取分型面时最好把要求同心的部分放在模具分型 面的同一侧,如图所示的双联齿轮,要求大齿轮、小齿轮和内孔三者有 很好的向小度,为此把齿轮凹模和型芯都设在动模一边,
要满足塑件的精度要求,比如同心度、同轴度、平行度等等
要求壁厚均匀塑件如图所示,如采用左图形式分型面,型腔、 型芯的同心度只能依靠导向零件来保证,
应避免或减少脱模斜度形成的塑件两端尺寸差异过大而形成 的塑件壁厚补均匀现象,这在较长塑件中较为明显。
采用左图形式,塑件两端壁厚不均,而且脱模困难。如果塑件外观 无严格要求,可采用左图形式,将分型面设在塑件中间位置,可弥 补塑件壁厚不均现象,且便于脱模。
10嵌件及活动型芯便于安放
图示左图嵌件安放,由于嵌件没有包紧力,而塑件端部对动模的包紧 力很小,开模时,定模型腔会将塑件带出无法脱模。右图形式使塑件 留动模一侧,然后顶出。
思考与练习: 1.分型面选择的一般原则有哪些?试举例说明。 2.分析(作业)产品零件图,确定分型面的位置。
重点:
分型面选择原则和案例分析。 成型零件的设计与制造(含公式的运用)。 难点:
分型面的选择和运用。 成型零部件工作尺寸计算和型腔壁厚计算。
塑料模具分型面的选择
一、分型面的定义及表示方法
分型面—— 模具上用以取出塑件和浇注系统凝料 的可分离的接触表面称为分型面,也叫合模面。
根据塑件情况,一套模具中可以只有一 个分型面,也可以同时设定两个或多个 分型面。常见的取出塑件的主分型面与 开模方向垂直,也有采用与开模方向一 致的侧向主分型面。
分型面的表示
分型面的选择好坏对塑件质量、操作难易、模具结构及制造都有很大的影响
二、分型面的形状
平面 阶梯面
斜面 曲面
选用阶梯式分型面,则会造成一侧受力较大,从而引起 模腔两侧于开模方向垂直的F不平衡,引起定模与动模 间有相对滑移的倾向。如果这种不平衡的注射力较小, 可通过导柱来支撑;但如果这种偏心力较大,则会引起 导柱、导套的过度磨损而引起塑件制品质量下降或模具 报废。
4、应考虑开模时塑件留动模
一般情况下,在开模时,将塑件留在设有顶出装置的动模一侧,以方 便塑件顶出、脱模。
按这一要求,一般都是将主型芯装在动模一侧,使塑件收缩包紧在主型芯 上,这时型腔可以设在定模一侧,
但当塑件内含有带孔的嵌件,或当塑件上根本无孔时,或者由于塑 件外形复杂对型腔粘附力较大时,为了使塑件不致于留在定模一侧, 应该将型腔设置在动模一侧,分别如(a)(b)(、分型面应便于模具的加工
7、侧向分型面与主分型面协调 8、分型面应与注塑机参数相一致
9、考虑脱模斜度的影响
10嵌件及活动型芯便于安放
1、有利于塑件脱模 1)分型面位置应设在塑件截面尺寸最大的部位,便 于脱模和加工型腔,这是分型面选择的首要原则。
分型面要取在塑件的最大截面处