模具分型面
分型面和分模面的异同点
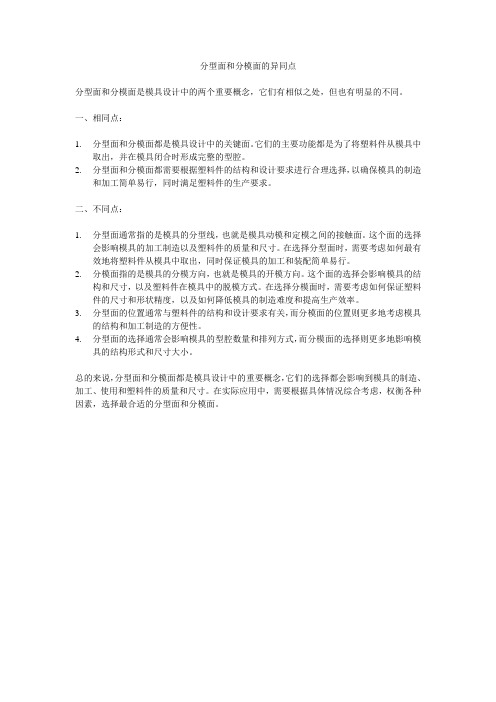
分型面和分模面的异同点
分型面和分模面是模具设计中的两个重要概念,它们有相似之处,但也有明显的不同。
一、相同点:
1.分型面和分模面都是模具设计中的关键面。
它们的主要功能都是为了将塑料件从模具中
取出,并在模具闭合时形成完整的型腔。
2.分型面和分模面都需要根据塑料件的结构和设计要求进行合理选择,以确保模具的制造
和加工简单易行,同时满足塑料件的生产要求。
二、不同点:
1.分型面通常指的是模具的分型线,也就是模具动模和定模之间的接触面。
这个面的选择
会影响模具的加工制造以及塑料件的质量和尺寸。
在选择分型面时,需要考虑如何最有效地将塑料件从模具中取出,同时保证模具的加工和装配简单易行。
2.分模面指的是模具的分模方向,也就是模具的开模方向。
这个面的选择会影响模具的结
构和尺寸,以及塑料件在模具中的脱模方式。
在选择分模面时,需要考虑如何保证塑料件的尺寸和形状精度,以及如何降低模具的制造难度和提高生产效率。
3.分型面的位置通常与塑料件的结构和设计要求有关,而分模面的位置则更多地考虑模具
的结构和加工制造的方便性。
4.分型面的选择通常会影响模具的型腔数量和排列方式,而分模面的选择则更多地影响模
具的结构形式和尺寸大小。
总的来说,分型面和分模面都是模具设计中的重要概念,它们的选择都会影响到模具的制造、加工、使用和塑料件的质量和尺寸。
在实际应用中,需要根据具体情况综合考虑,权衡各种因素,选择最合适的分型面和分模面。
模具分型面的设计和模仁大小的确定

一,分型面的设计分型面的设计和模仁的大小确定。
为了将产品从模具中取出,模具必须分成两个或数个部分,这些分离部分的接触表面通称为分型面分型面在模具中占有非常重要的位子,在设计模具时,首先考虑的就是这套模具分型面怎么做,如果连模具的分型都不知道,哪后须的工作也没法做了.到企业应聘模具设计时,往往要现场动手的就是做分型面,这关过不了,哪被录取的希望基本为零,如分型面做的又快又好,那你的成功率就大了.二.外观件的分型面的选取:1.肉眼观看.2.客户2D图纸指定.3.要保证母模胶位少,公模胶位多.如何利用UG软件选取分型面:1.利用拔模分析选择(粉红色与深兰色交界处或粉红色与绿色交界处)2.利用注塑模向导,自动抽取分型线.三.内置件的分型面的选取:1.要保证母模胶位少,母模尽量不要有机构.2.利用拔模分析分型面通常分为1.水平分型.2.垂直分型.3.倾斜分型(如图)4.台阶型分型面三,模仁和模架的确认。
产品的分模面大致确定以后,接下来就是确定模仁和模架的尺寸了模架尽量采用标准模架和标准配件,这样有利于缩短模具的制造周期和降低成本设计界经常用的模架品牌有:龙记(LKM),富得吧(FUTABA),名利,天祥,重村等当模具比较特殊或客户特别要求时,须对模架得形状,尺寸,材料作更改时,就需重新设计模架,这种情况下,定购模架时就需要向供应商提供详细得图面,并标注上与标准模架得不同之处,当然,这样得模架单价也较贵,供应商一般可以给客户提供架初加工和精加工,一般我们都要求进行粗加工及粗掏模穴即可一.模架和模仁尺寸的确定模架的大小主要取决于产品的大小和结构,对模具而言,在保证足够的强度下,模具设计的越紧凑越好.根据产品的外形(投影面积和高度)和结构(侧向分型和抽芯)来确定模仁的尺寸,确定好模仁的尺寸以后,就可以确定模架的尺寸了以下是模仁和模架尺寸确定的参考图表以上数据,只是作为设计时的一个参考,在设计时还要注意一下几点;1.当产品高度过高时(X>=D时),应适当加大D,加大值=(X-D)/2.2.有时为了冷却水道和固定螺丝的需要,也要对尺寸加以调整.3.当产品结构复杂,须特殊分型或顶出机构,或须加滑块等机构时,也应对模仁和模架尺寸进行修改.应适当加大模架和厚度.2.方铁高度的确定:方铁的高度应保证有足够的顶出行程和5-10MM预留量,以保证产品完全顶出,并且上顶板不会碰到公模板顶部3.模架整体尺寸的确定:模具定好以后,因对模架整体结构进行校核,看模架是否适合,所选定的或客户指定的注塑机的型号,包括外形尺寸,厚度,最大开模行程,及顶出方式和顶出行程等.4.模仁材料的选定;制品为一般的塑胶,如ABS,PP,PC,等,模仁因选用P20,NAK80,718.等预硬钢,如用高光洁度或透明的塑料制品,如PMMA,PS,AS,等因选用420等耐腐蚀不锈钢,含玻纤增强的塑胶,因选用H13,SKD61等热处理钢,当制品材料为PVC或POM和加了阻燃剂时因选用420,2316等不锈钢.具体在"模具用钢材"一节再详细学习。
注塑模具分型面的选择
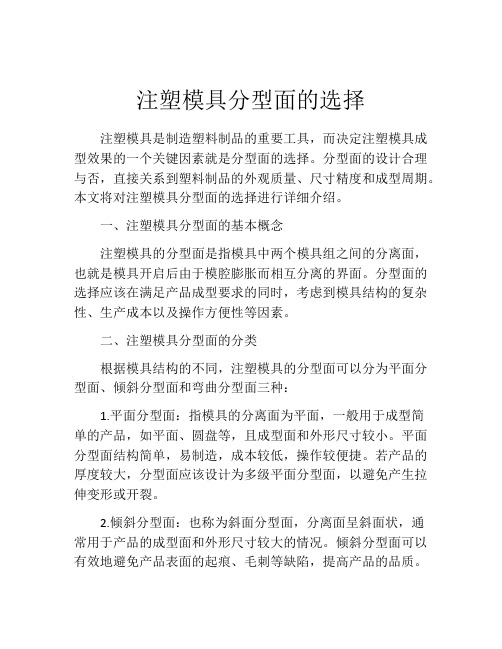
注塑模具分型面的选择注塑模具是制造塑料制品的重要工具,而决定注塑模具成型效果的一个关键因素就是分型面的选择。
分型面的设计合理与否,直接关系到塑料制品的外观质量、尺寸精度和成型周期。
本文将对注塑模具分型面的选择进行详细介绍。
一、注塑模具分型面的基本概念注塑模具的分型面是指模具中两个模具组之间的分离面,也就是模具开启后由于模腔膨胀而相互分离的界面。
分型面的选择应该在满足产品成型要求的同时,考虑到模具结构的复杂性、生产成本以及操作方便性等因素。
二、注塑模具分型面的分类根据模具结构的不同,注塑模具的分型面可以分为平面分型面、倾斜分型面和弯曲分型面三种:1.平面分型面:指模具的分离面为平面,一般用于成型简单的产品,如平面、圆盘等,且成型面和外形尺寸较小。
平面分型面结构简单,易制造,成本较低,操作较便捷。
若产品的厚度较大,分型面应该设计为多级平面分型面,以避免产生拉伸变形或开裂。
2.倾斜分型面:也称为斜面分型面,分离面呈斜面状,通常用于产品的成型面和外形尺寸较大的情况。
倾斜分型面可以有效地避免产品表面的起痕、毛刺等缺陷,提高产品的品质。
不过倾斜分型面制造难度较大,同时增加了模具的成本和加工难度。
3.弯曲分型面:也称为曲面分型面,在分离面呈曲面状的情况下,它可以用来制造外形复杂且不规则的产品。
弯曲分型面制造难度和成本都比平面分型面和倾斜分型面高,但能够制造更高精度的产品。
三、注塑模具分型面的选择原则1.分型面尽可能选择简单,以降低制造成本及操作难度,同时提高模具的寿命。
2.分型面应该尽量避免在成型面上留下痕迹和印记。
对于防止痕迹和印记的问题,可以选择倾斜分型面或弯曲分型面。
3.考虑产品的工艺特点和成型要求。
例如,对于薄壁弱结构的产品,分型面应该选择为多级平面分型面。
对于大型产品,可以选择倾斜分型面或弯曲分型面来保证产品的成型精度。
4.尽量选择产品表面朝上的分型面,以方便后续产品加工和涂装。
5.考虑成型周期和生产效率,尽可能选择简单的分型面结构,降低模具的制造和开发周期,提高生产效率。
模具分型面

模具分型面模具术语。
一般来说,模具都有两大部分组成:动模和定模(或者公模和母模),分型面是指两者在闭和状态时能接触的部分,也是将工件或模具零件分割成模具体积块的分割面,具有更广泛的意义。
分型面的设计直接影响着产品质量、模具结构和操作的难易程度,是模具设计成败的关键因素之一。
确定分型面时应遵循以下原则:(1)应使模具结构尽量简单。
如避免或减少侧向分型,采用异型分型面减少动、定模的修配以降低加工难度等。
(2)有利于塑件的顺利脱模。
如开模后尽量使塑件留在动模边以利用注塑机上的顶出机构,避免侧向长距离抽芯以减小模具尺寸等。
(3)保证产品的尺寸精度。
如尽量把有尺寸精度要求的部分设在同一模块上以减小制造和装配误差等。
(4)不影响产品的外观质量。
在分型面处不可避免地出现飞边,因此应避免在外观光滑面上设计分型面。
(5)保证型腔的顺利排气。
如分型面尽可能与最后充填满的型腔表壁重合,以利于型腔排气。
5-1-3 模具型腔分型面的确定本节重点:分型面确定本节难点:分型面确定原则分型面是指注射模具中用以取出塑件或浇注系统凝料的可分离的接触表面,是决定模具结构形式的一个重要因素。
分型面的类型、形状及位置与模具的整体结构、浇注系统的设计、塑件的脱模和模具的制造工艺等有关,不仅关系到模具结构的复杂程度,而且也关系到塑件的成型质量。
一分型面的形式及标示方法有的注射模只有一个分型面,而有的注射模有多个分型面。
当注射模具有两个或两个以上的分型面时,常将脱模时取出塑件的分型面称为主分型面,其它分型面称为辅助分型面。
分型面的形式如图5-1-4所示。
图5-1-4a为平直分型面;图5-1-4b为倾斜分型面;图5-1-4c为阶梯分型面;图5-1-4d为曲面分型面;图5-1-4e为瓣合分型面,也称垂直分型面。
图5-1-4分型面的形式在模具的装配图上,分型面的标示一般采用如下方法。
当模具分型时,若分型面两边的模板都移动,用“←|→”表示;若其中一方不动,另一方移动,用“|→”表示,箭头指向移动的方向;当有多个分型面时,应按先后次序,标出“A”、“B”,“C”等。
有关模具的分型面基本原则
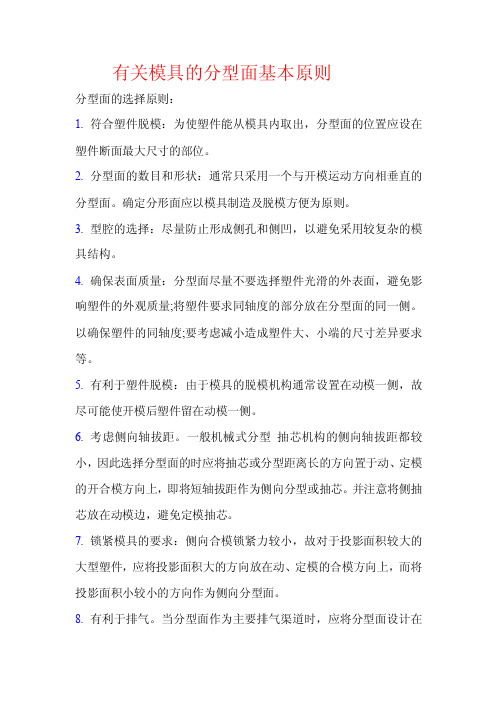
有关模具的分型面基本原则分型面的选择原则:1.符合塑件脱模:为使塑件能从模具内取出,分型面的位置应设在塑件断面最大尺寸的部位。
2. 分型面的数目和形状:通常只采用一个与开模运动方向相垂直的分型面。
确定分形面应以模具制造及脱模方便为原则。
3.型腔的选择:尽量防止形成侧孔和侧凹,以避免采用较复杂的模具结构。
4.确保表面质量:分型面尽量不要选择塑件光滑的外表面,避免影响塑件的外观质量;将塑件要求同轴度的部分放在分型面的同一侧。
以确保塑件的同轴度;要考虑减小造成塑件大、小端的尺寸差异要求等。
5.有利于塑件脱模:由于模具的脱模机构通常设置在动模一侧,故尽可能使开模后塑件留在动模一侧。
6.考虑侧向轴拔距。
一般机械式分型抽芯机构的侧向轴拔距都较小,因此选择分型面的时应将抽芯或分型距离长的方向置于动、定模的开合模方向上,即将短轴拔距作为侧向分型或抽芯。
并注意将侧抽芯放在动模边,避免定模抽芯。
7.锁紧模具的要求:侧向合模锁紧力较小,故对于投影面积较大的大型塑件,应将投影面积大的方向放在动、定模的合模方向上,而将投影面积小较小的方向作为侧向分型面。
8.有利于排气。
当分型面作为主要排气渠道时,应将分型面设计在塑料的流动末端,以利于排气。
9.模具分型面的选择和设计应该利于加工。
如: 1、主分型面为平面的情况,分型面设计时要考虑方便于磨床加工。
2、主分型面为复杂曲面,分型面设计时要考虑方便于NC加工,避免EDM加工。
分型面在不同情况下的设计要求<一>、主要分型面为平面的情况:主要分型面与开模方向垂直时,分型面可直接拉伸而成。
(见图一)*对于这种分型面用自动分模时常会在一些转角位有一些微小的起伏(高度方向几个丝的变化),对制作Fit模有一定的影响,应注意用平面替换,以利于磨床磨出。
<二>、主要分型面为斜面的情况:主要分型面与开模方向不垂直时,分型面沿斜面延伸一段后在分型面两端做平位,以利于加工定位及Fit模。
注塑模具之分型面的选择

注塑模具之分型面的选择分型面的选择分型面为动模与定模的分界面,是取出塑件或者浇注系统凝料的面.它的合理选择是塑件能完好成型的条件,不仅关系到塑件的脱模,而且涉及摸具结构与制造成本. 合理的分型面不但能满足制品各方面的性能要求 ,而且使模具结构简单,成本亦会令人满意.选择分型面时有下面一些原则能够遵循:.分型面应选择在塑件的最大截面处(圖二),否则给脱模与加工带来困难(圖一).此点可说是选择的首要原则.图一(無法脫模)图二(順利脫模).尽可能地将塑件留在公模侧,因在公模侧设置脱模机构简便易行..在安排制件在型腔中方位时,尽量避免侧向分型或者抽芯以利于简化模具结构.结合以上原则还要综合考虑塑件的尺寸精度、外观质量、使用要求及是否有利于浇注系统特别是浇口的合理安排, 是否有利于排气。
所设计的模具的塑件电话机的上面板(图示),由图能够看出,不能将侧面作为分型面,由于那将导致不合理的模具高度与模腔深度。
关于这一模具,分型面没有太多的选择。
它的侧边是有斜度的,下端面为最大截面,可考虑将整个外观面作为分型面。
电话机的上面板外观表面质量的要求很高,顶杆不能在外观面侧顶出,否则顶出痕迹会影响表面质量,因此外观面最好在母模侧成产品外观图型。
在结构方面,(如图所示)内侧面有很多小直径的BOSS,这些结构宜用顶管(套筒顶针)成型且便于脱模。
那么,这一部分应在公模侧。
如此布置,党制品冷却时,会因收缩作用而包覆在公模仁上,有利于制品滞留在公模一側。
根据以上分析,分型面的选择为整个外观面,内部结构在公模侧成型,外观面成型与母模侧(与图二相似)。
这样易于脱模,使模具结构相对简化,且分型面有一靠破处可设置浇口亦利于浇注系统的安内部结构图靠破 BOSS排。
综上,此选择可行。
型腔数目的确定注射模可设计成一模一腔也可设计成一模多腔。
其数目的确定要从下列几个方面考虑:.注塑产品的尺寸及结构的复杂性.塑件的尺寸精度—型腔越多,精度也相对降低。
模具分型面避空标准

此产品有 255MM 长.
注意避空部分尖角倒圆 角.
产品分型面分胶位留 25-30MM
模型边缘留 10MM, 绿 色部份避空 0.15MM.
.15MM. 3。100 以下的产品整圈排气槽内边缘离产品外缘 6-8MM 为好,分型接触面 20-30MM 或以上。 (见图示)避空时要千万注意流道。
此产品 52MM 长.
注意避空部分尖角倒圆角.
产品分 型面分 胶位 留 15-20MM 模型边缘留 10MM, 红色部份避空 0.15MM.
4.AB 成型类。(见图示) 5.异型分型面的避空。(见图示)
2.
100-200MM 的产品整圈排气槽内边缘离产品外缘 8-10MM 为好,分型接触面 30-40MM
或以上。(见图示)避空时要千万注意流道。
此产品有 124MM 长.
注意避空部分尖角倒圆 角.
产 品 分 型 面 分胶 位 留 20-25MM
模型边缘留 10MM,红色 部份避空 0
注意避空部分尖角倒圆 角.
产品分 型面分 胶位 留 30-50MM
些模具分型面比 较异型。高低落 差比较大。
这些只要留 25MM 分胶位 ,后面 可以 避空。
这个地方 R 角都没有 壁空的,
有此产品的碰 穿位,如 果面积比较 大,边 缘留 10-15MM,中间红色避空 0。15MM。 方便钳工
分型面的设计

1.分型面:模具上用以取出塑件和浇注系统凝料的可分离的接触表面;简 言之分开模具取出塑件的面;也叫合模面。 一副模具可以有一个或两个以上的分型面。 2.分型面的位置: *水平分型面:垂直于合模方向或与工作台面平行的面 *垂直分型面:平行于合模方向或与工作台面垂直的面 *斜分型面:倾斜于合模方向的面 注意:水平、垂直的参照系是开合模方向
概述
3.分型面的表示法:有方向性,有先后次序
4.分型面的形状:平面、斜面、阶梯面、曲面;
概述
5.分型面与型腔的相对位置:
二、分型面选择的一般原则
1、有利于脱模 2、保证塑件的外观、质量和精度 3、利于成型零件的加工
4、尽可能减少塑件在分型面上的投影面积
5、应有利于侧面抽芯 6、尽可能避免在外形或带圆弧的转角处分型 7、尽可能与料流末端重合,利于排气 8、考虑飞边在塑件上的位置
1、有利于脱模
1、分型面应取在塑件尺寸最大处:
有利于脱模
2、分型面应使塑件留在动模或下模:
3、拔模斜度小或塑件较高时,为便于脱模可将分型面选在塑件的中 间部位,但塑件外形有痕迹。
有利于脱模
4、满足塑件的使用要求
有利于脱模
5、考虑对塑件造成的脱模阻力大小
2、保证塑件外观、质量和精度
保证塑件外观、质量和精度
实例(解决办法)
1.采用侧浇口:料流先封住分型面,在型腔内形成气囊,影响质量。 2.改变浇注系统位置,如图所示:开模高度可降到508.但不利于 塑件外观. 3.采用HALF成型.
1.调整脱模斜度法
2.调整表面粗糙度
3.采取结构措施
四、实例
有时分型面的位置也取决于成型机的技术特征,在涉及注射模时应特别注意: 如:注射成型直径φ102,深:254的圆柱形容器。 闭合高度:457;脱模时:分型面先开254使型芯脱开型腔,再开254留出塑件推出空 间,再开51留出浇注系统推出空间。 开模高度(注射机最小压板间距)为:457+254+254+51=1016(mm) 塑件容积为216cm3,选择250cm3的注射机,但其最注射机最小压板间距为700,故 要选择更大的注射机,可能单位无更大的注射机,必造成浪费。
- 1、下载文档前请自行甄别文档内容的完整性,平台不提供额外的编辑、内容补充、找答案等附加服务。
- 2、"仅部分预览"的文档,不可在线预览部分如存在完整性等问题,可反馈申请退款(可完整预览的文档不适用该条件!)。
- 3、如文档侵犯您的权益,请联系客服反馈,我们会尽快为您处理(人工客服工作时间:9:00-18:30)。
华威模具设计规范
模具分型面的设计
在设计模具分型面时必须考虑以下几个方面: 1, 2, 3, 模具分型面的位置 模具分型面的有效宽度 模具分型面要求光滑平顺
一, 模具分型面的位置
一般情况下模具分型面处于产品最大外形轮廓处。
拿到产品后首 先分析产品的分模线的位置,确定模具大的结构。
模具分模结束 后一定要对每一只零部件进行脱模斜度分析检查。
确保分型面等 模具大的结构准确无误。
二, 1,
根据产品的特性确定分型面的宽度尺寸。
外形尺寸小于等于 200*200*25 的小产品,模具分型面的有效
宽度为 25mm 左右。
如果因为冷却水管位置尺寸不够时,模具分 型面的有效宽度可以放大到 30mm 左右。
2, 外形尺寸小于等于 200*200,但是深度大于 25mm, 模具分型
面的有效宽度接近产品的深度尺寸(适用与动定模是镶拼结构) 。
3, 外形尺寸小于等于 300*300*30 的产品,模具分型面的有效宽
度为 30mm 左右。
如果因为冷却水管位置尺寸不够时,模具分型 面的有效宽度可以放大到 35mm 左右。
华威模具设计规范
4,
外形尺寸小于等于 300*300,但是深度大于 30mm, 模具分型
面的有效宽度接近产品的深度尺寸(适用与动定模是镶拼结构) 。
5, 外形尺寸小于等于 400*400*35 的产品,模具分型面的有效宽
度为 35mm 左右。
如果因为冷却水管位置尺寸不够时,模具分型 面的有效宽度可以放大到 40mm 左右。
6, 外形尺寸小于等于 400*400,但是深度大于 40mm, 模具分型
面的有效宽度接近产品的深度尺寸(适用与动定模是镶拼结构) 。
7, 外形尺寸小于等于 500*500*40 的产品,模具分型面的有效宽
度为 40mm 左右。
如果因为冷却水管位置尺寸不够时,模具分型 面的有效宽度可以放大到 45mm 左右。
8, 外形尺寸小于等于 500*500,但是深度大于 50mm, 模具分型
面的有效宽度接近产品的深度尺寸(适用与动定模是镶拼结构) 。
9, 外形尺寸小于等于 600*600*50 的产品,模具分型面的有效宽
度为 50mm 左右。
10, 外形尺寸小于等于 600*600,但是深度大于 50mm, 模具分型 面的有效宽度接近产品的深度尺寸。
(适用与动定模是镶拼结构) 11, 外形尺寸大于 600*600*60 的产品,模具分型面的有效宽度为 60mm 左右 12, 外形尺寸大于 600*600,但是深度大于 50mm, 模具分型面的 (适用与动定模是镶拼结构) 有效宽度接近产品的深度尺寸。
华威模具设计规范
三,
模具分型面要求光滑平顺,方便钳工配模及机加工。
分型面可以通过简单扫描,平行与基准面扫描,同一张面延伸, 相切与表面延伸,垂直与基准面延伸等方法进行设计。
尽可能避 免转折和突变。
对插分型面尽可能设计较大的配合斜度,转角处 尽可能设计工艺 R 角,避免出现锋利锐角。
四, 模具非配合分型面避空间隙 模具承压面太宽,需要较大的注塑机,承压面过小,影响模具 的使用寿命。
一般情况下,承压面的宽度为 30MM,超过 30MM 的 部分请设计避空间隙 1MM,型腔侧、型芯侧分别设计 0.5MM,同时 可以有效减少数控铣加工工时。
。