3.2.2及3.2.3 浇注位置,分型面的确定
端盖铸造工艺设计

湖南科技大学课程设计课程设计名称:端盖铸造工艺设计学生姓名:学院:专业及班级:学号:指导教师:2015 年7 月7 日铸造工艺课程设计任务书一、任务与要求1.完成产品零件图、铸件铸造工艺图各一张,铸造工艺图需要三维建模(完成3D图)。
2.完成芯盒装配图一张。
3.完成铸型装配图一张。
4. 编写设计说明书一份(15~20页),并将任务书及任务图放置首页。
二、设计内容为2周1. 绘制产品零件图、铸造工艺图及工艺图的3D图(2天)。
2. 铸造工艺方案设计:确定浇注位置及分型面,确定加工余量、起模斜度、铸造圆角、收缩率,确定型芯、芯头间隙尺寸。
(1天)。
3. 绘制芯盒装配图(1天)。
4. 绘制铸型装配图、即合箱图(包括流道计算共2天)。
5. 编制设计说明书(4天)。
三、主要参考资料1. 张亮峰主编,材料成形技术基础[M],高等教育出版社,2011.2. 丁根宝主编,铸造工艺学上册[M] ,机械工业出版社,1985.3. 铸造手册编委会,铸造手册:第五卷[M] ,机械工业出版社,1996.4. 沈其文主编, 材料成形工艺基础(第三版)[M],华中科技大学出版社,2003.摘要本设计是端盖的铸造工艺设计。
端盖的材料为QT400-15,结构简单,无复杂的型腔。
根据端盖的零件图进行铸造工艺性分析,选择分型面,确定浇注位置、造型、造芯方法、铸造工艺参数并进行浇注系统、冒口和型芯的设计。
在确定铸造工艺的基础上,设计模样、芯盒和砂箱,并利用CAD、Pro/E等设计软件绘制端盖零件图、芯盒装配图。
关键词:铸造;端盖;型芯ABSTRACTThis design is about the casting process of end cap. The material of end cap is QT400-15. The end cap without complex cavity owns simple structures. Select the right parting line, pouring position, modeling method ,core making method, parameters of casting by analyzing the part drawing, then design gating system, riser, core. After the design of casting process, accomplish the part drawing of end cap and assembly drawing of core box with the aid of design software such as CAD and Pro/E.Keywords:Cast; End cap; Core目录第一章零件工艺性分析 (1)1.1零件分析 (1)1.2铸造工艺性分析 (1)第二章铸造合金和造型材料的选择 (2)2.1铸造合金的选用 (2)2.2造型和造芯材料 (2)第三章浇注位置及分型面的确定 (3)第四章铸造工艺参数设计 (5)4.1加工余量的选择 (5)4.2 铸件孔是否铸出的确定 (5)4.3起模斜度的确定 (6)4.4铸造圆角的确定 (6)4.5铸造收缩率的确定 (7)第五章造型方法设计 (8)第六章浇注系统和冒口设计 (10)6.1浇注系统的选择 (10)6.2 冒口的选择 (11)第七章装配图设计 (13)7.1铸型装配图 (13)7.2芯盒装配图 (13)第八章总结 (14)参考文献 (15)第一章零件工艺性分析1.1 零件分析轴承端盖起轴向固定作用,同时防尘密封,避免污染。
确定分型面的方法.

上 下
3、下箱带砂胎,上箱带吊砂。也可以采用型 芯形成内孔 4、两个半型内孔与外圆的同轴度依靠模样保 证,整体上难以保证同轴度 5、可能会出现错箱缺陷
讲解
确定分型面方案六
1、平直分型面,竖直浇注位置 2、分模造型,铸件在上、下箱各半 3、采用型芯形成内孔,无砂胎和吊砂 4、两个半型内孔与外形的位置关系依靠模样 保证,整体上依靠合箱保证 5、可能会出现错箱缺陷
讲解
确定分型面的方法
• 分型面:两半铸型相互接触的表面,一般与合箱面一致。
• 分型面决定着分模面的位置、内浇道引入位置、横浇道开设
位置,直接影响能否顺利起模,铸件位置精度等。
• 一般与浇注位置同时确定。
讲解
确定分型面方案一
1、平直分型面。
上 下
2、整模造型,铸件全部在下箱。 3、下箱带砂胎,无型芯。 4、内孔与外圆的同轴度依靠模样保证。
5、不出现错箱缺陷。
Hale Waihona Puke 讲解确定分型面方案二上 下
1、曲折分型面。 2、整模造型,铸件全部在下箱。 3、上箱带吊砂,无型芯。 4、内孔与外圆的同轴度依靠模样保证。 5、不出现错箱缺陷。
讲解
确定分型面方案三
1、曲折分型面。
上 下
2、整模造型,铸件全部在下箱。 3、上箱带吊砂,下箱带砂胎,无型芯。 4、内孔与外圆的同轴度依靠模样保证。
讲解
确定分型面方案七
1、平直分型面,竖直浇注位置。 2、分模造型,铸件在上、下箱各半。 3、采用型芯形成内孔,无砂胎和吊砂。 4、两个半型内孔与外形的位置关系依 靠模样保证,整体上依靠合箱保证。 5、可能会出现错箱缺陷。 6、砂箱高度大。
确定浇注位置的方法
铸件上的表面朝上或朝下
铸造工艺学课件(浇注位置的确定)

非加工面起模斜度有3种形式。
必须加工时,只能增加壁厚, 且在加工余量基础上给出斜度
4)收缩率 由于合金的收缩,为保证铸件应有的尺寸,在模
型上必须比铸件放大一个该合金的收缩量。 它取决于合金种类、铸件结构、尺寸等因素
灰铸铁为0.7~1.0%, 铸钢为1.5~2.0%, 铝硅合金为0.8%~1.2% 锡青铜为1.2%~1.4%
此铸件可供选择的主要铸造工艺方案有两种。
方案一:采用分模造型 。铸件轴线为水平位置,过中心轴线 得纵剖面为分型面 。
优点:1)两端加工面置于侧壁位置,质量较易得到保证; 2)内孔表面虽有一侧位于上面,但对铸造质量影响不大 3)浇注时熔融金属充型平稳 。
缺点:由于分模造型,易产生错型缺陷,铸件外形精度较差。
上 中
中 下
【相关知识】-----斜度要一致,
使砂芯的起模斜度和模样的起模斜度 大小、方向一致,保证铸件壁厚均匀
保证铸件壁厚均匀
a) 不合理
b) 合理
4.浇注系统设计
引导金属液体流入铸型型腔的通道。 1)浇口杯:承受金属液,防飞溅
外溢,分离熔渣,避免对型腔的直接 冲击。
2)直浇道:提供充型压力,控制 充型能力和流速。
铸件精度高,余量小;零件精度高,则余量大
加工余量的确定:确定铸件尺寸公差等级和加工余量等级后查表即可。 铸件尺寸公差CT分1-16级,精度低减; 加工余量等级RMA分AB。。JK共10级精度低减
零件、铸件和模样三者在尺寸与形状上的区别:
比模样小一个加工余量和收缩量
零 比铸件小一加工余量 铸 比模样小一收缩量
且不错箱 。 1)为便于起模,分型面应选在最大截面处,
铸造工艺学课件浇注位置的确定
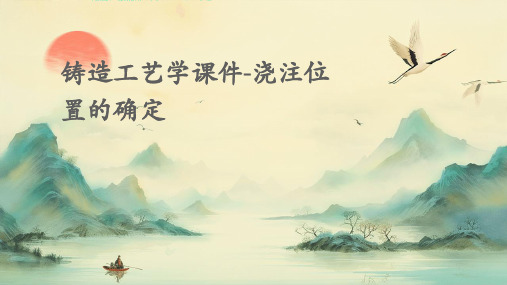
按铸件在铸型中的位置和金属 液的流动方向组合分类:可分 为上后浇注、下前浇注、侧底
浇注等。
02
浇注位置的选择原则
铸件结构的考虑
铸件结构
浇注位置应有利于金属液的流动和填充,同时要 考虑到铸件的结构,如壁厚、肋条、凸台等。
减少缺陷
浇注位置应尽量减少铸件内部和表面的缺陷,如 气孔、夹渣、冷隔等。
简化模具
浇注位置应有利于模具的 设计和制造,降低模具成 本。
冷却效果
浇注位置应有利于提高模 具的冷却效果,缩短铸件 冷却时间。
脱模方便
浇注位置应有利于脱模, 避免卡模或损坏铸件。
铸造工艺的考虑
工艺适应性
浇注位置应有利于铸造工艺的实 施,如砂型铸造、金属型铸造等 。
质量控制
浇注位置应有利于质量控制和检 测,便于发现问题和解决问题。
要点二
人工智能技术的应用
通过训练神经网络模型,实现对浇注位置的自动优化。该 方法可以大幅提高优化效率和准确性,减少人工干预和试 错成本。
THANKS
感谢观看
详细描述
在确定飞机起落架的浇注位置时,需 要考虑以下几点
实例三:飞机起落的浇注位置确定
浇口位置应避开起落架的承力部位和连接部位,以免影响起 落架的强度和稳定性。
浇口位置应与起落架的材料和冷却系统相配合,保证起落架 在铸造过程中能够得到充分的冷却,防止出现铸造缺陷。同 时,考虑到飞机起落架的使用环境和安全性要求,浇注位置 应尽量减小对起落架外观和质量的影响。
基于铸造工艺的确定方法
总结词
根据铸造工艺的特点,选择合适的浇注位置,以确保金属液能够顺利填充型腔并获得完整、清晰的铸件。
详细描述
铸造工艺的特点对浇注位置的选择具有重要影响。对于采用底注式浇注的铸造工艺,应选择将金属液从底部注入 型腔的位置作为浇注口。对于采用顶注式浇注的铸造工艺,应选择将金属液从顶部注入型腔的位置作为浇注口。
浇注位置-分型面选择

有利于补缩
避免用吊砂、吊芯或悬臂式砂芯,便 于下芯、合箱及检验
2.2.4 分型面的确定
分型面是指两半铸型相互接触的表面 1. 应使铸件全部或大部置于同一半型内; 2. 尽量减少分型面的数量; 3. 分型面应尽量采用平面; 4. 便于下芯、合箱合检查型芯尺寸; 5. 不使砂箱过高; 6. 减少铸件清理和机械加工的工作量
•
1、有时候读书是一种巧妙地避开思考 的方法 。20.1 2.1320. 12.13Sunday, December 13, 2020
•
2、阅读一切好书如同和过去最杰出的 人谈话 。07:5 6:5907: 56:5907 :5612/ 13/2020 7:56:59 AM
•
3、越是没有本领的就越加自命不凡。 20.12.1 307:56: 5907:5 6Dec-20 13-Dec-20
铸件下部金属在上部金属的静压力作 用下凝固并得到补缩,组织致密
机床导轨是重要面,浇注时要朝下。这是因 为铸件上部凝固速度慢,晶粒较粗大,易在 铸件上部形成砂眼、气孔、渣孔等缺陷。铸 件下部的晶粒细小,组织致密,缺陷少,质 量优于上部。机床床身导轨和铸造锥齿轮的 锥面都是主要的工作面,浇注时应朝下。
2.2.2造型及制芯方法的选择
1. 优先采用湿砂型 2. 与生产批量相适应 3. 适合工厂条件 4. 兼顾精度与成本
各种铸造方法应用范围
2.2.3 浇注位置的确定
——铸件在浇注时的位置
1. 铸件的重要部位置于下部; 2. 重要的加工面朝下或呈直立状态; 3. 铸件的大平面朝下; 4. 保证铸件充满; 5. 有利铸件的补缩; 6. 避免使用吊芯,便于下芯。
•
8、业余生活要有意义,不要越轨。20 20年12 月13日 星期日 7时56 分59秒0 7:56:59 13 December 2020
材料成形技术基础知识点总结

材料成形技术基础第一章1-1一、铸造的实质、特点与应用铸造:将熔融的液体浇注到与零件的形状相适应的铸型型腔中,冷却后获得逐渐的工艺方法。
1、铸造的实质利用了液体的流动形成。
2、铸造的特点A适应性大(铸件重量、合金种类、零件形状都不受限制);B成本低C工序多,质量不稳定,废品率高D力学性能较同样材料的锻件差。
力学性能差的原因是:铸造毛胚的晶粒粗大,组织疏松,成分不均匀3、铸造的应用铸造毛胚主要用于受力较小,形状复杂(尤其是腔内复杂)或简单、重量较大的零件毛胚。
二、铸造工艺基础1、铸件的凝固(1)铸造合金的结晶结晶过程是由液态到固态晶体的转变过程。
它由晶核的形成和长大两部分组成。
通常情况下,铸件的结晶有如下特点:A以非均质形核为主B以枝状晶方式生长为主。
结晶过程中,晶核数目的多少是影响晶粒度大小的重要因素,因此可通过增加晶核数目来细化晶粒。
晶体生长方式决定了最终的晶体形貌,不同晶体生长方式可得到枝状晶、柱状晶、等轴晶或混合组织等。
(2)铸件的凝固方式逐渐的凝固方式有三种类型:A逐层凝固 B糊状凝固 C中间凝固2、合金的铸造性能(1)流动性合金的流动性即为液态合金的充型能力,是合金本身的性能。
它反映了液态金属的充型能力,但液态金属的充型能力除与流动性有关,还与外界条件如铸型性质、浇注条件和铸件结构等因素有关,是各种因素的综合反映。
生产上改善合金的充型能力可以从一下各方面着手:A选择靠近共晶成分的趋于逐层凝固的合金,它们的流动性好;B 提高浇注温度,延长金属流动时间;C 提高充填能力D 设置出气冒口,减少型内气体,降低金属液流动时阻力。
(2)收缩性A 缩孔、缩松形成与铸件的液态收缩和凝固收缩的过程中。
对于逐层凝固的合金由于固液两相共存区很小甚至没有,液固界面泾渭分明,已凝固区域的收缩就能顺利得到相邻液相的补充,如果最后凝固出的金属得不到液态金属的补充,就会在该处形成一个集中的缩孔。
适当控制凝固顺序,让铸件按远离冒口部分最先凝固,然后朝冒口方向凝固,最后才是冒口本身的凝固(即顺序凝固方式),就把缩孔转移到最后凝固的部位——冒口中去,而去除冒口后的铸件则是所要的致密铸件。
综合分析手工造型和机器造型浇注位置和分型面选择原则

综合分析手工造型和机器造型浇注位置和分型面选择原则浇注位置的确定:浇注位置是指浇注时铸件在型内所处的状态(姿态)和位置。
也就是说:哪个部位在上或在下,哪个面朝上、呈侧立状态,或朝下。
浇注时,朝下的铸件表面比较光洁、干净;而朝上的表面,空易有砂孔,渣孔、夹砂等缺陷,表面粗糙度差;铸件下部的金属在凝固时,受到上部金属压力作用和补缩,比较致密,力学性能容易得到保证。
因此,浇注位置的确定是工艺设计中重要环节。
它关系到铸件的内在品质、铸件的尺寸精度及造型工艺过程的难易。
浇注公交车与造型(合型)位置、铸件冷却位置可以不同。
生产中常以浇注时分型面是处于水平、垂直或倾斜位置,分别称贷为水平浇注、垂直浇注或倾斜浇注,但这不代表铸件的浇注位置的含义。
浇注位置一般于选择造型方法之后确定。
应指出,确定浇注位置在很大程度上着眼于控制铸件的凝固。
实现顺序凝固的铸件,可消除缩孔、缩松,保证获得致密的铸件。
内应力小,变形小,金相组织比较均匀一致,不用或很少采用冒口,节约金属,减小热裂倾向。
但铸件内部可能有缩孔或轴线缩松存在。
因此多应用于薄壁铸件或内部出现轻微轴线缩松不影响使用的情况下。
这时,如铸件有局部肥厚部位,可置于浇注位置的底部,利用冷铁或其他激冷措施,实现同时凝固。
灰铸铁件、球墨铸铁件常利用凝固阶段的共晶体膨胀来消除收缩缺陷,因此,可遵循顺序凝固条件而获得健全铸件。
浇注位置可根据对合金凝固理论的研究和生产经验确定,确定浇注位置时诮考虑以下原则:1) 浇注位置应有利于所确定的凝固顺序。
2) 铸件的重要部分应尽时置于下部。
3) 重要加工面应朝下或呈直立状态。
4) 使铸件的大平面朝下,避免夹砂结疤类缺陷。
对于大的平板类铸件,可采用倾斜浇注,以便增大金属液面的上升速度,防止夹砂结疤类缺陷。
5) 应保证铸件能充满。
对具有薄壁部分的铸件,应把薄壁部分放在内浇道以下或置于铸型的下部,以免出现浇不到、冷隔等缺陷。
6) 避免用吊砂、吊芯或悬臂式砂芯,便于下芯、合型及检验。
分型面的确定

模县上用以取出制品及浇注系统凝料的RJ分离的接触表面称为分型面,常常是注射模定模和动模两部分的接触面。
在制品设计时,必须考虑成型时分型山的形状和位置,否则无法用模具成型。
在设计模具时首先需要确定分型面的位置,然后才能选择模具的结构。
分型面的设计是否合理对制品质量、AVX钽电容丁艺操作难易程度和模具的设计制造有很大的影响。
冈此,分型面的正确设计需要塑料产品设计人员和模具设计成员的共同努力和配合。
3.2.1 分型面的形状和方位分型面的形状应尽可能简单,以便于制品脱模和模具的制造。
分型面可以是平面、阶梯面或者曲面,如图3—11所尔。
一般只采用一个与注射机开模方向相垂也的分型面,而且尽可能采用简单的平团作为分型面,在特殊情况下才采用较多的分型面。
应尽量避免与开模运动方向垂直的侧向分型和侧向抽芯,因为这会增加模具结构的复杂性。
如图3—12所示,若按图3—12(a)设置型腔,内于与开模运动垂直的方向有侧凹,必须增加侧向分型的分型面,使模具结构复杂化,而按图3—12(b)采用斜分型面,便可避免在垂直方向上有侧凹。
根据分型而的不同方位,塑料制肋可以全部在动模内成型,也可以全部在定模内成型,还可以在动、定模内同时成型。
具体采用哪种形式成型要根据制nun的几何形状、浇注系统、椎们机构以及制品质量要求等因素综合加以考虑。
3.2.2 分型面位置的选择原则(1)分型凹必须开设在制品断面轮廓最大的部位才能使制品顺利地脱模。
(2)因为分型6J不tJJ避免地耍在制思上留下痕迹,所以分型团最好不选在制品光滑的外表团或带圆弧的转角处,如图3—13所示。
如图3—14(h)所示。
峭制风的壁很捏且内孔较小时,制品对型芯的包紧力不大,往往不能确切判断制品留在型芯上还是型腔内,故应将型腔和型;趣的主要部分都设齐动模一边,如司3—14(c)所示。
肖制佩的孔内行非螺纹连接的金属嵌件时,民件不会对型心产生包紧力,此时应将型腔设公动模一边,型芯既可没在动模一边,也可设在定模一边,如图3—14 ((1)所水。
- 1、下载文档前请自行甄别文档内容的完整性,平台不提供额外的编辑、内容补充、找答案等附加服务。
- 2、"仅部分预览"的文档,不可在线预览部分如存在完整性等问题,可反馈申请退款(可完整预览的文档不适用该条件!)。
- 3、如文档侵犯您的权益,请联系客服反馈,我们会尽快为您处理(人工客服工作时间:9:00-18:30)。
图3.24起重臂的分型面 图3.25 规则的曲面 分型面
ቤተ መጻሕፍቲ ባይዱ
③平直分型面和曲折分型面的选择:要可能选择平直 分型面以简化工装结构及其制造等。 但有些情况下必须选择曲面分型:
a)为了有利于清理和机加工而采用曲面分型
图3.29 摇臂铸件的分型面
b)利用通用砂箱时有时要采用曲面分型
④选择分型面时不要使某一砂箱过高。
图3.27 托架分型面的选择
⑤机器造型大批量生产时,要尽可能减少砂芯数目。 在保证铸件质量的前提下可利用台砂或吊砂代替砂芯, 这样可以提高生产率和经济效益。
⑥选择分型面要时要尽可能将全部砂芯,或至少将重 要砂芯放在下型内,便于下芯、验箱和合型。
图3.26 减速器箱盖的手工造型方案(两个分型 面便于验箱
⑤对含有砂芯的铸件,应保证砂芯的定位稳固、
排气通畅及下芯检验方便。尽量不使用吊砂、 吊芯及悬臂砂芯。
⑥使铸件的大平面位置朝下,避免夹砂结疤类缺陷
图3.16 大平面铸件的 正确浇注位置
图3.17 大平板类铸件的倾 斜浇注
⑦应使合箱位置、浇注位置和铸件冷却位置一致
第3章
铸造工艺设计
3.2.3 铸件分型面 铸件分型面(parting face or plane)的选择 的选择 分型面:砂型造好后,要将铸型分开来才能 取出模样,得到使金属液成型为铸件的空腔。 这种将铸型分割开来便于起模的面叫分型面。 或者 两个铸型相互接触的表面叫分型面 选择次序:一般在确定浇注位置后再选择 选择依据:结构特点,技术要求,生产批量, 生产条件,并结合浇注位置来考虑。
耐磨面、受力部位等)应朝下面或侧面;铸件 的大平面应朝下。
①质量要求高的铸件表面(如重要的机加工面、
耐磨面、受力部位等)应朝下面或侧面;铸件 的大平面应朝下。
图3.14铸铁床身的正确浇注位置(导轨面 是关键表面)
①质量要求高的铸件表面(如重要的机加工面、
耐磨面、受力部位等)应朝下面或侧面;铸件 的大平面应朝下。
⑦受力件的分型面的选择不应削弱铸件结构强度
图3.28 工字梁分型面的选择
summarize
图3.15 起重机卷筒的浇注位置(重要表 面是内外圆柱面) (a) 不合理; (b) 合理
②圆周表面要求高的轮形件、圆筒形件一般采
用立浇。
③较大而壁薄的铸件部分应朝下、侧立或倾斜
以保证金属液的充填。
图3.18曲轴箱的浇注位置
④有利于收缩大的铸件实现顺序凝固和安放冒
口,即:使铸件的热节或最厚实的部位在浇注 时处于顶部或分型面附近的侧面,以便安放冒 口。
第3章
铸造工艺设计
3.2.2 铸件浇注位置 铸件浇注位置(pouring position of casting)的确定 的确定 浇注位置:浇注时铸件在砂型中所处的位置(即哪个 面朝上的问题)
选择依据:铸件大小,结构特点,合金性能,生产批 量,现场生产条件等 原则: ①质量要求高的铸件表面(如重要的机加工面、
选择原则: ①尽可能使铸件全部或大部分,或者加工基准面与重 要加工面处于同一半型内。
图3.22管子堵头的分型方案 图3.21后轮毂的分型方案 (a) 不合理; (b) 合理
②机器造型的大批量生产中,要尽可能减少分型面数 目,并且最好不用活块。
图2-64 确定分型面数目的实例
③平直分型面和曲折分型面的选择:要尽可能选择平 直分型面以简化工装结构及其制造等。
④有利于收缩大的铸件实现顺序凝固和安放冒
口,即:使铸件的热节或最厚实的部位在浇注 时处于顶部或分型面附近的侧面,以便安放冒 口。
图3.19双排链轮铸钢件的正确浇注位置
⑤对含有砂芯的铸件,应保证砂芯的定位稳固、
排气通畅及下芯检验方便。尽量不使用吊砂、 吊芯及悬臂砂芯。
图3.20 便于合箱的浇注位置 (a) 不合理; (b) 合理