汽车塑料件涂装工艺
塑料件涂装

塑料件的修复
6)将这块包含环氧树脂的布贴到面罩背面,再把另外的胶粘剂充填 进布的织网里。 7)将背面加强件固定到位后,在砂纸打磨过的面罩下面修理部位涂 一层助粘剂,并将其干透。 8)在坡口内充填胶粘剂,并按说明书要求进行固化。 9)先用F80砂纸,再用F180砂纸,最后用F240砂纸打磨修理部位。 6.擦伤、撕伤和孔洞的修复方法 1)用清除蜡、油脂和硅质等污物的溶剂彻底清洗损坏部位。 2)用直径为75mm的中粒度砂轮在损伤部位边缘制作坡口,坡口宽度 为6~9mm。 3)打磨配合表面。
塑料件的修复
图2-100 典型的热空气塑料焊接焊炬
2.热空气塑料焊炬的焊嘴 (1)定位焊焊嘴 用于断裂板件的定位焊。 (2)圆形焊嘴 用于充填小的孔眼或形成短焊缝,也可用于难以靠近 部位的焊接和尖角部位的焊接。 (3)快速焊嘴 用于直而长的接缝的焊接。 3.使用热空气塑料焊炬的基本步骤
塑料件的修复
涂装作业程序
(6)刮第二道腻子 填不平的地方,需刮第二道腻子,腻子厚度应不 超过2mm,刮完20min后进烘房,烘干温度40~80℃,烘干时间40m in。
涂装作业程序
(7)初次打磨 用F2铁砂布包在木板上进行初磨,磨后去掉灰尘,在 涂刮腻子的地方涂刷H06—2底漆,再用红外线灯照射烘烤。
图3-4 砂磨腻子的方法
塑料件的修复
4)用细一点的砂轮修整坡口边缘,打磨掉涂膜层,但要尽量少磨掉 塑料材料,并使涂膜层逐渐过渡到塑料层。 5)进行烧燎处理,用以改善粘结效果。 6)在修理部位粘上铝质车身胶带,用溶剂清洗内表面,然后粘贴上 铝质车身胶带,将操作部位全部盖住。 7)在涂敷结构胶粘剂前,应将零件背面彻底清理干净,然后粘贴上 铝质车身胶带起支撑作用。 8)胶粘剂的准备应按说明书的要求进行。 9)用橡胶刮板或塑料抹子将胶粘剂抹到孔洞处,这个过程要求既迅 速又仔细,胶粘剂将在3min之内开始固化。 10)打磨第一次涂抹的胶粘剂,用细砂轮磨掉过高的部位,清除粉末, 然后清理干净。
汽车塑料保险杠喷涂工艺流程
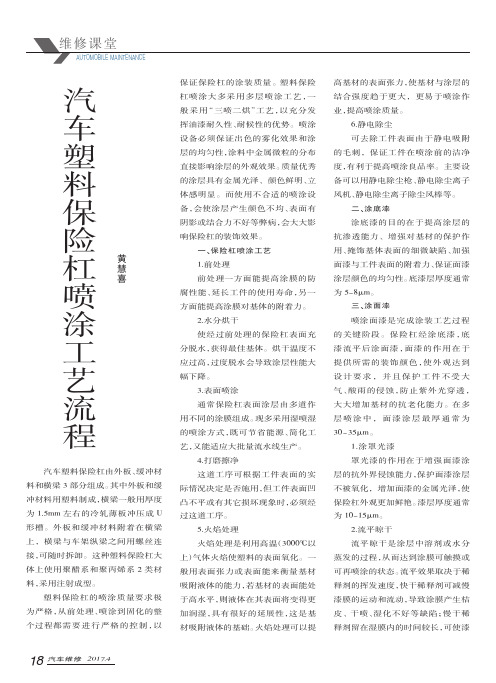
AUTOMOBILE MAINTENANCE
汽 车 塑 料 保 险 车塑料保险杠由外板、缓冲材
料和横梁 3 部分组成。其中外板和缓
冲材料用塑料制成,横梁一般用厚度
为 1.5mm 左右的冷轧薄板冲压成 U
形槽。外板和缓冲材料附着在横梁
上,横梁与车架纵梁之间用螺丝连
3.烘烤固化
喷 涂 好 的 保 险 杠 经 流 平 后 ,需 进入固化炉进行固化处理。涂料的烘 烤固化是 1 个熔融和化学反应过程, 它使涂膜变硬、耐摩擦,是涂装工艺 中重要的一个环节。烘烤的时间和温 度将决定涂膜的性能和特性,烘烤不
足可导致涂膜厚度不均匀、附着力 差、耐候性差、强度和硬度下降;烘烤 过度,轻则涂膜失色,重则涂膜焦化, 机械强度严重下降。
接,可随时拆卸。这种塑料保险杠大
体上使用聚醋系和聚丙烯系 2 类材
料,采用注射成型。
塑料保险杠的喷涂质量要求极
为严格,从前处理、喷涂到固化的整
个过程都 需 要 进 行 严 格 的 控 制 ,以
保 证 保 险 杠 的 涂 装 质 量 。塑 料 保 险 杠 喷 涂 大 多 采 用 多 层 喷 涂 工 艺 ,一 般 采 用“ 三喷二烘”工艺,以充分发 挥油漆耐久性、耐候性的优势。喷涂 设备必须保证出色的雾化效果和涂 层的均匀性,涂料中金属微粒的分布 直接影响涂层的外观效果。质量优秀 的涂层具有金属光泽、颜色鲜明、立 体感明显。而使用不合适的喷涂设 备,会使涂层产生颜色不均、表面有 阴影或结合力不好等弊病,会大大影 响保险杠的装饰效果。
学生判断是 X51A 保险丝盒损坏及 高速 GMLAN 通信线路故障。
学生判断故障的依据:
图 1 灯光系统电源电路图
!!!!!!!!!!!!!!!!!!!!!!!!!!!!!!!!!!!!!!!!!!!!!!!!
汽车用塑料件的涂装的介绍

汽车用塑料件的涂装介绍时间:2009-3-6 编辑:,来源:.21-plastic.1.汽车用塑料件的涂装特点用和外用塑料件涂装的不同点是:用塑料件一般采用半光泽或完全无光泽涂装,方法是将涂料中加入一定比例的平光剂;外用塑料件有的采用无光泽涂装,有的采用有光泽涂装,视具体情况而定。
硬性和软性塑料件涂装的不同点是:由于软性塑料本身具有柔韧性,它所用的涂料基本上都是烘烤型弹性磁漆,所谓“弹性”是指涂层具有较大的柔韧型,类似弹性体、橡胶,也可以弯曲、折叠、拉伸,然后还可以回复到原来的尺寸和形状而不会被破坏。
方法就是用专用的涂料,该涂料中加入柔软剂。
2.塑料件涂装用材料1)塑料表面清洁剂清洁剂的作用是清除塑料件表面的脱膜剂,增强对油漆的附着力。
使用方法是:先用灰色打磨布彻底清洁塑料件的表面,再用以1份清洁剂与2份~4份清水混合后的混合液清洁整件工件,然后用清水清洗干净,待工件完全干燥后才可喷涂塑料底漆。
塑料表面清洁剂的溶解性适中,不会损伤塑料表面,而且抗静电,所以塑料工件不会因摩擦而产生静电,影响涂装。
2)塑料平光剂为消除汽车部塑料件一定比例的光泽而使其呈现半光泽或完全无光泽,一般都采用不同光泽的涂料装饰。
平光剂有聚氨酯用和非聚氨酯用两大类,选用时务必小心。
其使用方法是:将喷涂面漆后的塑料件的光泽与原车的光泽作比较,以决定是否需要用平光剂,如果需要的话,先在面漆中加入平光剂,然后搅拌均匀,并作喷涂样板对比试验,在认为光泽达到一致时可正式喷涂施工。
单层涂装消光,直接将平光剂加入漆中即可,而双层涂装的消光,平光剂不要加在色漆,要加在清漆。
3)PVC表面调整剂调整剂的作用是对PVC表面进行处理,使其有利于重涂。
它由强溶剂配制而成,具有强烈的渗透性,而且能够软化PVC 表面并产生轻微的溶胀。
这样,涂装时修补涂料就能很容易地渗透进入塑料表面,这就是人们所说的“锚链效应”。
它可以大大提高涂料对基材的附着力。
4)汽车塑料件用底漆(1)软塑料件。
汽车塑料件涂装工艺及涂膜弊病(内部培训)

塑料件涂装工艺及涂膜弊病近代以来,塑料工业取得了突飞猛进的发展,各类工程塑料以其质轻、耐腐蚀、易加工成型等特点而被广泛应用。
20世纪60年代,为提高汽车的碰撞安全性,开始使用塑料保险杠;近年来,为了满足汽车轻量化以及汽车零部件材料回收(环境保护要求可循环利用)的需要,汽车零部件塑料化的比例越来越大,目前一辆车的塑料件用量已达到200kg左右,日本汽车则占到了整车质量的30%~40%。
外饰塑料件也从保险杠扩大到后视镜壳、门把手、扰流板、侧裙护板、水箱格栅、牌照灯护板、防擦条、轮毂罩等(见图1)。
也有报导:在国外一些大汽车公司的新车设计中,发动机罩、行李箱盖、叶子板等部件也有采用塑料件,塑料化趋势很明显。
245316图1典型的汽车塑料件1—保险杠;2—门玻璃护板、防擦条;3—脚踏板、裙边;4—后视镜罩;5—门把手;6—轮毂盖汽车外饰使用较多的塑料种类有:PP、ABS、PA、GFP等几种。
常见的表面处理方式有:模压上色、喷涂油漆、装饰防护性亮镀(铬)等,而在塑料表面喷涂一层或多层油漆的工艺应用最多。
下面将就塑料件油漆的功能要求、涂装工艺、质量评价项目以及常见的失效模式等进行探讨。
塑料件涂装的目的尽管塑料件本身不会生锈,具有耐腐蚀性和一定的装饰性,但在塑料件上喷涂合适的涂料,可以延长使用寿命,提高相关性能,总的来说塑料件涂装的目的主要有以下3方面:(1)装饰作用:达到外观高光泽、与车身同色或异色等高装饰性效果;(2)保护作用:提高塑料件的耐紫外线、耐溶剂、耐化学品、耐光老化等性能;(3)特种功能:通过涂装耐划伤涂料,提高零件表面的抗划伤性能等。
典型塑料件涂装工艺目前,国内的大部分汽车塑料件涂装线采用的都是手工喷涂,涂层结构大多为“底漆+色漆+清漆”三涂层体系,如保险杠等;也有对于ABS等表面能高的材料直接喷涂色漆+清漆的两涂层结构,如后视镜罩等。
典型的塑料件涂装工艺流程如下:①前处理(除油、除脱模剂、清洗等)———喷底漆(1K:kind底漆晾干或2K底漆烘干)———喷色漆———喷清漆(2K清漆)———烘干———面漆修饰———交检。
汽车塑料件喷涂工艺

汽车塑料件喷涂工艺以汽车塑料件喷涂工艺为标题,本文将介绍汽车塑料件喷涂的工艺流程、喷涂技术以及相关注意事项。
一、工艺流程汽车塑料件喷涂工艺主要包括以下几个步骤:1. 表面处理:汽车塑料件在喷涂之前需要进行表面处理,以确保喷涂后涂层的附着力和耐久性。
常用的表面处理方法有喷砂、化学处理和打磨等。
2. 底漆喷涂:底漆是塑料件喷涂中的重要一步,它能够填充塑料表面的微小孔洞和不平整,提高涂层的附着力和平整度。
3. 砂光处理:底漆干燥后,需要进行砂光处理,以消除底漆涂层的瑕疵和不平整,使表面更加光滑。
4. 静电喷涂:在砂光处理后,进行静电喷涂。
静电喷涂技术可以使涂料均匀地附着在塑料件表面,提高涂层的质量和附着力。
5. 烘干:喷涂完成后,将塑料件放入烘干室进行烘干,以使涂层快速固化和干燥。
6. 表面处理:烘干后,可以进行表面处理,如抛光、清洁等,以提高涂层的光泽和质感。
二、喷涂技术1. 喷涂设备:汽车塑料件喷涂通常使用高压喷涂设备。
高压喷涂设备能够产生较高的喷涂压力,使涂料均匀地附着在塑料件表面。
2. 涂料选择:根据塑料件的材质和要求,选择合适的涂料类型。
常见的涂料有丙烯酸漆、聚酯漆和环氧漆等。
不同的涂料有不同的特性和用途,需要根据实际情况选择。
3. 喷涂技巧:喷涂时需要注意喷涂距离、喷涂速度和喷涂角度等因素。
喷涂距离一般为20-30厘米,喷涂速度要匀速且均匀。
喷涂角度要根据塑料件的形状和结构来确定,以保证涂料能够均匀地覆盖整个表面。
三、注意事项1. 环境控制:喷涂过程中需要保持工作环境的洁净和通风良好,以避免灰尘和杂质附着在涂层上。
2. 温度控制:喷涂时要控制好工作环境的温度,过高或过低的温度都会影响涂层的质量和附着力。
3. 涂料搅拌:在使用涂料之前,需要充分搅拌均匀,确保涂料中的颜料和溶剂充分混合。
4. 喷涂厚度:喷涂时要控制好涂层的厚度,过厚会导致涂层开裂,过薄则会影响涂层的耐久性。
5. 涂层质量检查:喷涂完成后需要对涂层进行质量检查,包括涂层的平整度、附着力和颜色等。
汽车塑料件及各类漆涂装工艺
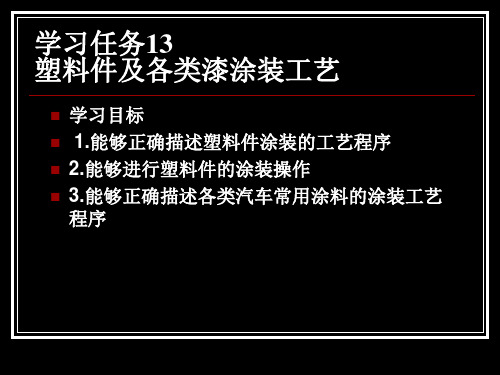
1.氨基醇酸涂料的涂装工艺
1)普通(A05—9)氨基烘漆施工工艺 (1)刷涂或喷涂磷化底漆,自干120min。 (2)喷涂底漆1~2道,60℃温度下烘干。 (3)刮涂3道环氧腻子(第一道烘干后磨平)。 (5)修平腻子缺陷。 (6)喷涂二道底漆1道,烘干. (7)打磨(200~280#水砂纸)。 (8)喷涂氨基烘漆1道,烘干后用细砂纸(P600)打磨。 (8)喷涂第2道氨基烘漆,烘干。 (9)用氨基清烘漆和氨基烘漆按l :1的比例混合罩光,烘干。
硬质塑料部件的预处理
硬质塑料的涂前预处理程序: 1)清洁(更换的新板材必须使用专用的脱模剂清 洗液进行清洗或用软布蘸上酒精等进行全面的擦拭, 以去除掉脱模剂成分)。 2)除油(塑料清洁剂)。 3)打磨(P80~120号干磨砂纸,注意不要磨穿树 脂层)。 4)二次清洁(塑料清洁剂) 。
2.硝基涂料施工说明
(1)底漆要彻底干透 (2)每打磨一次腻子表面后,应刷涂或喷涂一道 底漆,以使涂层牢固 (3)面漆一般喷涂三道,最多喷涂9~12道 (4)喷涂第一道硝基漆时宜少宜薄 (5)喷完最后一道漆,在常温下干燥12h以上为 好,待涂膜有一定的硬度再打磨抛光。
1.过氯乙烯涂料喷涂工艺
学习任务13 塑料件及各类漆涂装工艺
学习目标 1.能够正确描述塑料件涂装的工艺程序 2.能够进行塑料件的涂装操作 3.能够正确描述各类汽车常用涂料的涂装工艺 程序
学习任务13 塑料件及各类漆涂装工艺
学习内容 一、塑料件的涂装 二、各类涂料的涂装工艺
一、塑料件的涂装工艺
2.施工注意事项
汽车外饰塑料件涂装及涂料质量评价分析
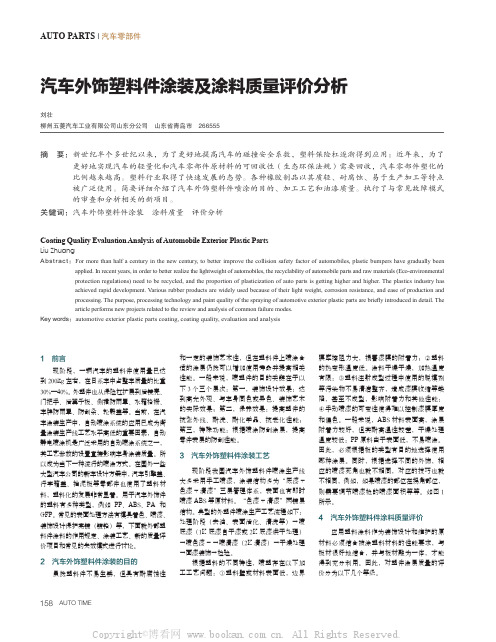
AUTO PARTS | 汽车零部件汽车外饰塑料件涂装及涂料质量评价分析刘壮柳州五菱汽车工业有限公司山东分公司 山东省青岛市 266555摘 要: 新世纪半个多世纪以来,为了更好地提高汽车的碰撞安全系数,塑料保险杠逐渐得到应用:近年来,为了更好地实现汽车的轻量化和汽车零部件原材料的可回收性(生态环保法规)需要回收,汽车零部件塑化的比例越来越高。
塑料行业取得了快速发展的态势。
各种橡胶制品以其质轻、耐腐蚀、易于生产加工等特点被广泛使用。
简要详细介绍了汽车外饰塑料件喷涂的目的、加工工艺和油漆质量。
执行了与常见故障模式的审查和分析相关的新项目。
关键词:汽车外饰塑料件涂装 涂料质量 评价分析1 前言现阶段,一辆汽车的塑料件使用量已达到200kg左右,在日系车中占整车质量的比重30%—40%。
外塑件也从保险杠扩展到后镜壳、门把手、后翼子板、侧裙防雨罩、水箱格栅、车牌防雨罩、防刮条、轮毂盖等。
当前,在汽车涂装生产中,自动喷涂系统的应用已成为衡量涂装生产线工艺水平高低的重要因素,自动静电喷涂机是广泛采用的自动喷涂系统之一,其工艺参数的设置直接影响车身涂装质量。
所以成为当下一种流行的喷涂方式。
在国外一些大型汽车公司的新车设计方案中,汽车引擎盖、行李箱盖、挡泥板等零部件也使用了塑料材料,塑料化的发展非常显着。
用于汽车外饰件的塑料有多种类型,例如 PP、ABS、PA 和 GFP。
常见的表面处理方法有模具着色、喷漆、装饰设计保护亮镀(镀铬)等,下面就外部塑料件涂料的作用规定、涂装工艺、新的质量评价项目和常见的失效模式进行讨论。
2 汽车外饰塑料件涂装的目的虽然塑料件不易生锈,但具有耐腐蚀性和一定的装饰艺术性,但在塑料件上喷涂合适的涂层仍然可以增加使用寿命并提高相关性能。
一般来说,喷塑件的目的关键在于以下3个三个层次:第一,装饰设计效果:达到高光外观、与车身同色或异色、装饰艺术的实际效果;第二,保养效果:提高塑件的抗紫外线、耐洗、耐化学品、抗老化性能;第三,特殊功能:根据喷涂防刮涂层,提高零件表层的防刮性能。
汽车钣金项目十六 塑料制品表面涂装的施工

外用塑料制 品的施工
软性塑料涂装 难度较大
内用硬塑料 制品的施工
1/19/2021
聚丙烯塑料 制品:保险杠
硬塑料件的喷涂方法
硬塑料件的喷涂大多数不需使用底漆或中涂漆以及封闭剂, 需要则应选用底色漆为丙烯酸涂料或聚氨酯涂料。
特殊塑料的喷涂需使用底漆和中涂漆,应与面漆配套。 切记不可使用磷化涂料、侵蚀底漆、金属处理剂和柔软剂。
中涂底漆 加柔软剂
喷涂一 次中涂
干燥
准备喷 涂面漆
砂纸整平
砂纸打磨
1/19/2021
两种方法 :
面漆的喷涂
双组分丙烯酸聚氨酯涂料
第一种
按供应商喷涂要求调配 加入柔软剂
使用纹理添加剂产生纹理
1/19/2021
面漆的喷涂
两种方法 :
第二种
1/19/2021
乙烯高黏度面
④
漆加稀释剂 稍干后喷涂一层
①
透明乙烯基涂料层
修补过划痕的漆面为何易断裂、脱落?
您有过? 什么原 因呢?
这样的经历: 车上的划痕刚 修好时效果挺好, 使用一段时间后, 修补过的漆面就 会发生断裂、
脱落现象。
这种现象大多发生在 裙边、保险杠等塑料 件部位。这是由于一 些修理厂偷减工艺流 程造成的。
1/19/2021
漆面易断裂、脱落的原因
外用硬塑料的施工:清洁塑料件,
用脱脂剂擦净待修补区域
内用硬塑料的施工:
(如有损坏部位应用腻子修平整), 先确定塑料制品材料的质地,
修补区域用P400砂纸粗化表面, 修补区与旧涂层接口部位 用P600以上细砂打磨粗化,
完工后将表面擦拭干净,喷涂
如制品为硬质或刚性的ABS塑料, 施工时不宜使用底漆, 中涂漆和封闭剂。
- 1、下载文档前请自行甄别文档内容的完整性,平台不提供额外的编辑、内容补充、找答案等附加服务。
- 2、"仅部分预览"的文档,不可在线预览部分如存在完整性等问题,可反馈申请退款(可完整预览的文档不适用该条件!)。
- 3、如文档侵犯您的权益,请联系客服反馈,我们会尽快为您处理(人工客服工作时间:9:00-18:30)。
汽车塑料件涂装工艺
摘要:通过介绍汽车塑料件的涂装工艺过程,分析塑料件的涂装特点及注意事项,并展望未来复合材料的涂装发展方向。
随着全球性的能源危机,节能减排是汽车技术一个主要的发展方向,而减轻汽车自身的重量是降低汽车排放,提高燃油效率的最有效措施之一。
汽车的自重每减少10%,燃油耗可降低6%~8%。
为此,增加塑料类材料在汽车中的使用量便成为降低整车成本及其重量、提高燃油利用率、减轻汽车排放的关键。
在我国,塑料件约占汽车自重的7%~10%,与汽车工业发达国家相比存在很大差距,德国、美国、日本等国的汽车塑料用量达到10%~15%,有的甚至已达到20%以上。
1、塑料件与金属件的涂装区别
随着塑料件的日益推广,越来越多的车身外饰件及内饰件开始塑料化,随之而来的对这些塑料件的装饰性和耐久性的要求也越来越高。
部分零件要求与车身同色且要具有与车身寿命相同年限的防腐能力,而单纯依靠塑料件原材料自身的颜色是不能满足越来越高的装饰性要求。
主要原因有两点:一是塑料件原料自身成型所带出的颜色只能是一种,难以实现颜色的多样化;二是塑料件依靠色母成型出来的颜色无论是从鲜亮性、饱满度,还是从光泽度来讲,都很难同涂料的效果相媲美。
所以,随着塑料件的日益推广,其成型后的涂装工序就显得越来越重要,且必不可少。
塑料件与金属件的涂装区别主要表现在:
1)金属件在涂装之前的处理是通过脱脂、酸洗除去表面的油脂及锈迹,然后通过磷化生成的磷化膜增强油漆与金属表面的附着力。
2)塑料件的涂装前处理。
首先,塑料件的脱脂不能采用碱性的脱脂液,那样易造成零件局部应力开裂,只能采用中性脱脂液进行脱脂;其次,塑料件不能进行酸洗、磷化处理,它只能通过特定的处理方法来增强油漆在零件表面的附着力。
2、汽车塑料件涂装的主要流程
汽车塑料件涂装的流程由以下几个主要的工艺步骤组成:
工件上线→ 脱脂(60℃中性清洗剂喷洗)→循环水洗(喷)→ 表调→ 干燥(60℃热风)→ 静电除尘→ 喷底漆→ 干燥(60℃,20~30 min)→底漆打磨→喷面漆→干燥(60℃,20~30 min)。
1)脱脂。
由于塑料件在成型过程中,其内外表面会存在残留的脱模剂,这些脱模剂会严重影响涂膜的附着力,所以涂装前的脱脂工序是至关重要的。
很多厂家采用醇类溶剂清洁塑料件表面,这种工艺方法并不能保证脱脂效果,涂膜附着力有时较差,并使工人的操作条件恶化。
最好还是采用中性脱脂剂喷洗的工艺方式,涂层质量比较稳定可靠。
具体的脱脂工艺步
骤如下:
①预脱脂。
选用中性或弱碱性脱脂剂喷淋1 min。
脱脂剂的pH值控制在6.0 ±1.0;考虑到塑料件不能耐高温,脱脂剂的处理温度控制在60±5℃。
在选型时,要考虑脱脂剂在该温度区间内的实际处理效果。
脱脂过程中,必须保证工件在线上流转时有足够的喷淋时间,喷淋时间太短会造成工件脱脂不到位,喷淋方式采用压力喷淋,喷淋管路采用环形布置,保证工件各个面能得到彻底喷洗。
喷淋压力一般控制在0.1~0.2MPa 之间,脱脂液在压力作用下与工件接触充分,工件表面的油脂可以清除充分。
②脱脂。
具体施工工艺同上。
2)水洗。
需要进行两道水洗,主要目的是洗净工件表面残留的脱脂液、表面的颗粒杂质和有害离子,每道用自来水喷淋30 s,喷淋压力为0.2~0.4 MPa。
3)表调。
表调的目的是活化塑料本体表面,使得涂料能够与本体表面有效结合。
表调槽液是在去离子水中添加表面活性剂,一般槽液的电导率控制在30μs /cm以下,表调液喷淋时间为30 s,喷淋压力为0.2~0.4MPa。
随着生产的正常进行,槽液中需不断补加表面活性剂,以弥补产品对表面活性剂的消耗。
4)干燥。
采用烘房热空气循环强制干燥。
由于塑料件不能耐高温烘烤,故烘烤的温度控制在60±5℃,烘烤时间为15~30 min。
5)静电除尘。
利用静电除尘器产生离子化压缩空气对产品表面进行除尘,目的是除去工件表面由于静电吸附的杂质和纤维,确保后道喷漆工序的表面质量。
6)喷底漆。
采用空气喷涂,水帘式吸风喷漆房。
由于绝大部分塑料材质的耐溶剂性都较差,直接喷涂面漆,塑料件表面易被涂料中强溶剂溶胀而使涂膜失去光泽,甚至
产生“吸涂料”现象。
因此,要在塑料件表面先行喷涂一层硬而快干的丙烯酸底漆打底,对塑料件表面起到封闭作用,同时也能提高面漆的附着力。
底漆喷涂时力求快而薄,漆层厚度不宜过厚,以防涂料中的溶剂不能及时挥发而对塑料件本体产生溶胀作用。
建议涂膜厚度在20~30μm,分两道喷涂,第一道喷涂后闪干50 s,再喷第二道。
7)底漆干燥。
待底漆表面指干后,将工件进烘房烘干。
烘烤温度在60±5℃,烘烤时间20~30 min。
注意,不能在底漆一喷好后就将工件进烘房烘烤,那样会造成底漆中的溶剂挥发较快而在油漆表面产生针孔,而且油漆表面得不到充分流平,势必会影响底漆的表面质量。
8)底漆表面打磨。
底漆烘干后,待其自然冷却,用800 #的水砂纸对底漆表面进行打磨。
一方面可以消除底漆表面的一些轻微缺陷;另一方面也可以通过将底漆表面磨毛来增强底漆与后道面漆的结合力。
9)喷面漆。
①喷底色漆。
绝大多数面漆由两道漆层组成,即底色漆和罩光清漆。
底色漆一般有素色漆、金属漆和珠光漆等,喷涂工艺同底漆工艺。
漆膜的厚度视不同的漆种而略有不同,金属漆和珠光漆的厚度一般在20μm左右,而素色漆的厚度一般在30μm左右。
②喷罩光清漆。
喷清漆时采用湿碰湿工艺,待底色漆闪干5 min左右时间喷清漆。
喷涂底色漆和罩光清漆时,涂料的黏度和喷涂间隔时间应控制好,防止咬底现象发生。
另外,罩光清漆宜采用硬而饱满的双组分聚氨酯清漆,保证涂膜有良好、持久的质感和抗划伤性。
10)面漆干燥。
面漆干燥工艺同底漆。
待面漆表面指干后,将工件进烘房烘干,烘烤温度60±5℃,烘烤时间20~30 min。
3、塑料件涂装常见问题
1)涂膜多针孔、局部失光。
这主要是油漆中的溶剂对塑料产生溶解和溶胀作用,塑料件发生了应力开裂现象。
要解决这个问题,首先考虑油漆与塑料件的配套性问题。
塑料件的涂装应该选用专用涂料,以免涂料中的溶剂对塑料产生不良影响。
其次,塑料件的涂装最好要用硬而快干的丙烯酸底漆封底,这样可以避免面漆对塑料件的进一步渗透。
2)涂膜附着力差。
对于高结晶度的材质,如PP、PE、PTFE等,材料表面极性小、润湿性差,涂料在其表面几乎不产生微溶胀,涂料的附着力较差。
遇到这种情况,需要对材料表面进行专门的处理,或换用共混改性材料(如PP/EPDM 共混料)来赋予其涂料的施工性。
3)同种类型材料涂装施工性有差异。
由于热塑性材料的合成是一个非常复杂的反应过程,其反应温度、压力、时间等任何一个参数的变动均会影响聚合物的分子量、微观链型结构。
所以同种材质、不同牌号往往表现出来的物理特性是不一样的。
就拿一般都认为涂装施工性良好的ABS塑料来说,有高冲击性型和通用型之分,高冲击性型的ABS塑料的表面涂膜附着力较差。
另外,产品成型时注塑工艺条件的变化也会造成塑料件表面某种成分的偏析,所以通用型ABS 塑料有时也会产生涂膜附着力差及吸涂料等问题。
所以塑料件涂装施工性的好坏有赖于塑料原材料的不同以及选择合适的涂装前处理工艺和涂料品种。
4、结束语
随着材料技术的飞速发展,无论是在汽车行业、机械行业、民用行业,还是在航天领域,大量轻质高强的合成材料用来替代金属材料,这同时也催生了复合材料涂装工艺的飞速发展。
光固化涂料及固化工艺、VIC涂料的胺蒸气快固化工艺、IMC涂料和模内注射涂装技术、模内粉末涂料及涂装工艺等新涂料、新工艺随着复合材料的不断推广应运而生。
这些新材料、新工艺的应用将给塑料件的涂装带来更为广阔的市场空间和应用前景。