挤压流程工艺
挤压铸造工艺流程
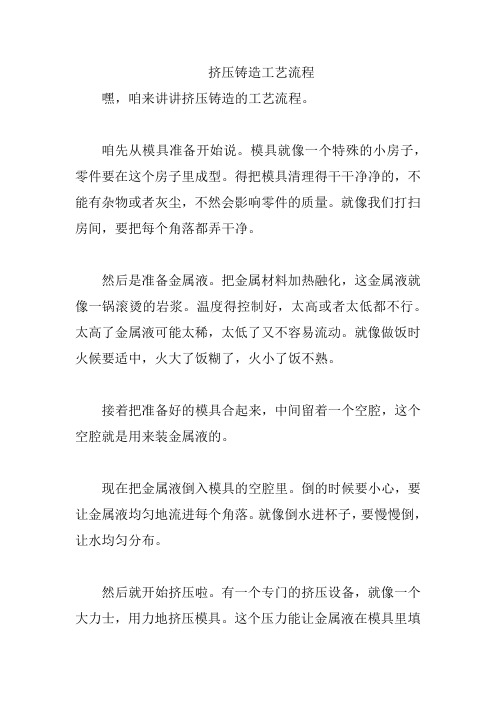
挤压铸造工艺流程嘿,咱来讲讲挤压铸造的工艺流程。
咱先从模具准备开始说。
模具就像一个特殊的小房子,零件要在这个房子里成型。
得把模具清理得干干净净的,不能有杂物或者灰尘,不然会影响零件的质量。
就像我们打扫房间,要把每个角落都弄干净。
然后是准备金属液。
把金属材料加热融化,这金属液就像一锅滚烫的岩浆。
温度得控制好,太高或者太低都不行。
太高了金属液可能太稀,太低了又不容易流动。
就像做饭时火候要适中,火大了饭糊了,火小了饭不熟。
接着把准备好的模具合起来,中间留着一个空腔,这个空腔就是用来装金属液的。
现在把金属液倒入模具的空腔里。
倒的时候要小心,要让金属液均匀地流进每个角落。
就像倒水进杯子,要慢慢倒,让水均匀分布。
然后就开始挤压啦。
有一个专门的挤压设备,就像一个大力士,用力地挤压模具。
这个压力能让金属液在模具里填得更紧实。
压力的大小很关键,如果压力不够,零件可能会有气孔或者不密实;压力太大了,模具可能会受不了。
就像我们按东西,太轻了按不紧,太重了东西可能会坏掉。
在挤压的过程中,金属液在模具里慢慢冷却。
这时候模具就像一个大冰箱,让金属液凝固成我们想要的形状。
等金属液完全凝固了,就可以打开模具了。
把成型的零件取出来,就像从模具这个小房子里把宝贝拿出来一样。
取出来的零件还得进行一些后续处理。
比如说把零件上一些多余的部分去掉,就像修剪树枝一样,让零件看起来更规整。
有时候还需要对零件进行一些表面处理,让零件的表面更光滑或者更有光泽。
挤压铸造的工艺流程虽然有点复杂,但是它能做出质量非常好的零件。
在汽车、航空等很多领域都有应用。
就像一个神奇的魔法,把金属液变成了一个个精致的零件。
挤压制粒工艺流程
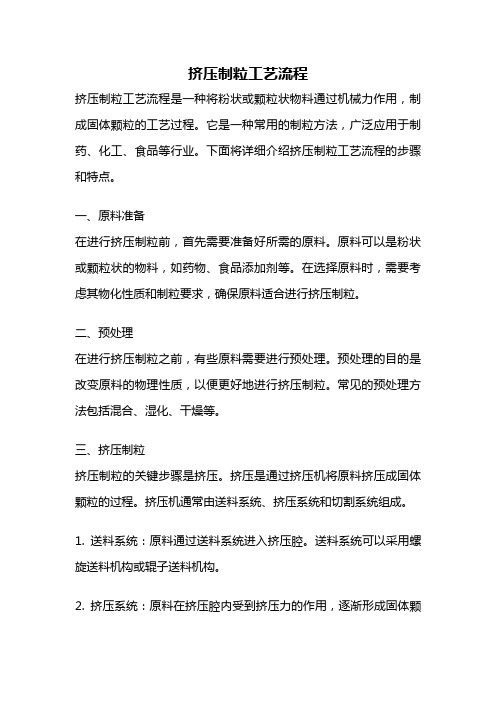
挤压制粒工艺流程挤压制粒工艺流程是一种将粉状或颗粒状物料通过机械力作用,制成固体颗粒的工艺过程。
它是一种常用的制粒方法,广泛应用于制药、化工、食品等行业。
下面将详细介绍挤压制粒工艺流程的步骤和特点。
一、原料准备在进行挤压制粒前,首先需要准备好所需的原料。
原料可以是粉状或颗粒状的物料,如药物、食品添加剂等。
在选择原料时,需要考虑其物化性质和制粒要求,确保原料适合进行挤压制粒。
二、预处理在进行挤压制粒之前,有些原料需要进行预处理。
预处理的目的是改变原料的物理性质,以便更好地进行挤压制粒。
常见的预处理方法包括混合、湿化、干燥等。
三、挤压制粒挤压制粒的关键步骤是挤压。
挤压是通过挤压机将原料挤压成固体颗粒的过程。
挤压机通常由送料系统、挤压系统和切割系统组成。
1. 送料系统:原料通过送料系统进入挤压腔。
送料系统可以采用螺旋送料机构或辊子送料机构。
2. 挤压系统:原料在挤压腔内受到挤压力的作用,逐渐形成固体颗粒。
挤压腔内的温度、压力和转速等参数需要根据原料的性质和制粒要求进行调节和控制。
3. 切割系统:挤压后的颗粒通过切割系统进行切割。
切割系统可以采用切割刀、切割板等形式,将挤压出的长条状颗粒切割成所需长度的颗粒。
四、干燥挤压制粒后的颗粒含有一定的水分,需要进行干燥处理。
干燥的目的是去除颗粒中的水分,提高颗粒的稳定性和质量。
常用的干燥方法包括自然风干、烘箱干燥、流化床干燥等。
五、筛分和包装经过干燥处理后的颗粒需要进行筛分和包装。
筛分是将颗粒按照一定的粒径范围进行分级,得到所需的颗粒尺寸。
包装是将制粒好的颗粒按照一定的重量或容量进行包装,以便存储和销售。
挤压制粒工艺流程的特点:1. 操作简单:挤压制粒工艺流程相对简单,操作方便,适用于大批量生产。
2. 颗粒均匀:挤压制粒能够使原料均匀地分布在挤压腔内,从而制得颗粒均匀、一致。
3. 粒径可调:通过调节挤压机的参数,可以控制颗粒的粒径范围,满足不同的制粒要求。
4. 节能环保:挤压制粒过程中不需要加热和添加溶剂,能够节约能源,减少环境污染。
挤压模具工艺流程
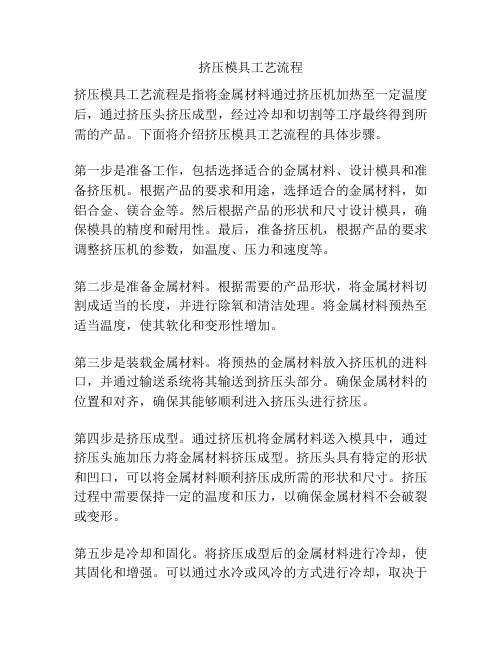
挤压模具工艺流程挤压模具工艺流程是指将金属材料通过挤压机加热至一定温度后,通过挤压头挤压成型,经过冷却和切割等工序最终得到所需的产品。
下面将介绍挤压模具工艺流程的具体步骤。
第一步是准备工作,包括选择适合的金属材料、设计模具和准备挤压机。
根据产品的要求和用途,选择适合的金属材料,如铝合金、镁合金等。
然后根据产品的形状和尺寸设计模具,确保模具的精度和耐用性。
最后,准备挤压机,根据产品的要求调整挤压机的参数,如温度、压力和速度等。
第二步是准备金属材料。
根据需要的产品形状,将金属材料切割成适当的长度,并进行除氧和清洁处理。
将金属材料预热至适当温度,使其软化和变形性增加。
第三步是装载金属材料。
将预热的金属材料放入挤压机的进料口,并通过输送系统将其输送到挤压头部分。
确保金属材料的位置和对齐,确保其能够顺利进入挤压头进行挤压。
第四步是挤压成型。
通过挤压机将金属材料送入模具中,通过挤压头施加压力将金属材料挤压成型。
挤压头具有特定的形状和凹口,可以将金属材料顺利挤压成所需的形状和尺寸。
挤压过程中需要保持一定的温度和压力,以确保金属材料不会破裂或变形。
第五步是冷却和固化。
将挤压成型后的金属材料进行冷却,使其固化和增强。
可以通过水冷或风冷的方式进行冷却,取决于金属材料的特性和要求。
第六步是切割和下料。
将冷却固化后的金属材料切割成所需的长度和形状,以便后续加工和使用。
切割可以使用剪切机、锯床或其他切割设备进行。
第七步是产品检验和修整。
对切割下料后的产品进行检验,检查其外观和尺寸是否符合要求。
如有需要,进行修整和打磨,以使产品的表面光滑和精致。
最后一步是包装和储存。
对已经完成的产品进行包装,以防止其受到损坏和腐蚀。
然后将产品储存到合适的地方,并做好相应的记录和管理。
以上就是挤压模具工艺流程的具体步骤。
通过合理的设计和操作,可以生产出高质量和精确的挤压产品,满足市场和客户的需求。
镁合金挤压工艺流程

镁合金挤压工艺流程
镁合金挤压工艺流程是指将镁合金加热到一定温度后,通过挤压机将其挤压成所需形状的过程。
具体流程如下:
1. 材料准备:选择合适的镁合金材料,并根据挤压产品的规格和要求进行切割和加工。
2. 加热处理:将镁合金加热到一定温度,通常在250-400℃之间,以使其具有足够的可塑性。
3. 挤压成型:将加热后的镁合金放入挤压机中,通过挤压机的压力,使其逐渐挤出成所需的形状。
4. 冷却处理:将挤压成型的镁合金放入冷却槽中,快速冷却以消除残余应力和提高硬度。
5. 精密切割:按照产品要求进行精密切割和加工,以达到所需的尺寸和形状。
6. 表面处理:对挤压成型的镁合金进行表面处理,如喷涂、抛光等,以提高其外观和耐腐蚀性。
通过以上步骤,镁合金挤压工艺流程完成,得到的产品具有高强度、轻质、良好的抗腐蚀性和可塑性,广泛应用于航空航天、汽车制造、电子设备等领域。
- 1 -。
挤压工艺的流程知识点总结
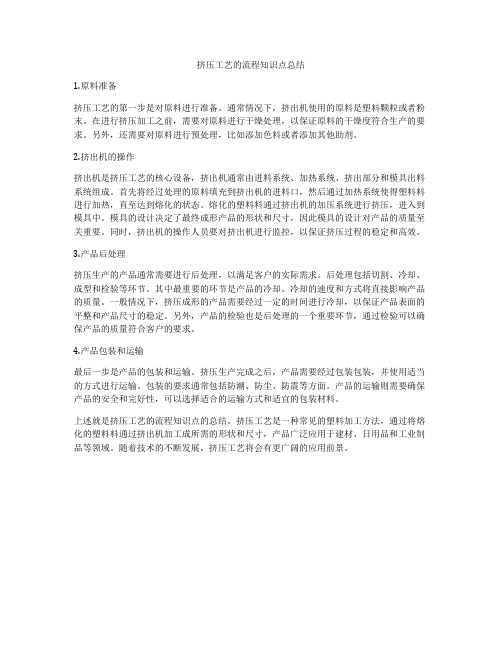
挤压工艺的流程知识点总结1.原料准备挤压工艺的第一步是对原料进行准备。
通常情况下,挤出机使用的原料是塑料颗粒或者粉末。
在进行挤压加工之前,需要对原料进行干燥处理,以保证原料的干燥度符合生产的要求。
另外,还需要对原料进行预处理,比如添加色料或者添加其他助剂。
2.挤出机的操作挤出机是挤压工艺的核心设备,挤出机通常由进料系统、加热系统、挤出部分和模具出料系统组成。
首先将经过处理的原料填充到挤出机的进料口,然后通过加热系统使得塑料料进行加热,直至达到熔化的状态。
熔化的塑料料通过挤出机的加压系统进行挤压,进入到模具中。
模具的设计决定了最终成形产品的形状和尺寸,因此模具的设计对产品的质量至关重要。
同时,挤出机的操作人员要对挤出机进行监控,以保证挤压过程的稳定和高效。
3.产品后处理挤压生产的产品通常需要进行后处理,以满足客户的实际需求。
后处理包括切割、冷却、成型和检验等环节。
其中最重要的环节是产品的冷却。
冷却的速度和方式将直接影响产品的质量。
一般情况下,挤压成形的产品需要经过一定的时间进行冷却,以保证产品表面的平整和产品尺寸的稳定。
另外,产品的检验也是后处理的一个重要环节,通过检验可以确保产品的质量符合客户的要求。
4.产品包装和运输最后一步是产品的包装和运输。
挤压生产完成之后,产品需要经过包装包装,并使用适当的方式进行运输。
包装的要求通常包括防潮、防尘、防震等方面。
产品的运输则需要确保产品的安全和完好性,可以选择适合的运输方式和适宜的包装材料。
上述就是挤压工艺的流程知识点的总结。
挤压工艺是一种常见的塑料加工方法,通过将熔化的塑料料通过挤出机加工成所需的形状和尺寸,产品广泛应用于建材、日用品和工业制品等领域。
随着技术的不断发展,挤压工艺将会有更广阔的应用前景。
冷挤压工艺流程

冷挤压工艺流程冷挤压工艺是一种常用的金属成型方法,通过将金属坯料置于模具中,在受到一定压力的作用下,使得金属坯料在模具的作用下发生塑性变形,从而得到所需形状和尺寸的工件。
冷挤压工艺流程主要包括原料准备、坯料加热、挤压成形、冷却退火等步骤。
首先,原料准备是冷挤压工艺流程的第一步。
在进行冷挤压之前,需要准备好金属坯料,通常采用的是圆形、方形或者多边形的金属坯料。
这些坯料需要经过清洗、除油、预加热等处理,以确保坯料表面清洁,并且达到适合挤压成形的温度。
接下来是坯料加热。
在冷挤压工艺中,坯料需要在一定温度范围内进行加热处理,以提高金属的塑性和可变形性。
加热温度的选择需要根据金属的种类和成分来确定,通常会在金属的再结晶温度以上进行加热,使得金属内部的晶粒得以再结晶,从而提高金属的延展性和塑性。
然后是挤压成形。
在坯料加热到适当温度后,将坯料放入挤压机的模具中,施加一定的压力,使得金属坯料在模具的作用下发生塑性变形,从而得到所需形状和尺寸的工件。
在挤压成形的过程中,需要控制好挤压速度、挤压压力和模具温度,以确保成形工件的质量和尺寸精度。
最后是冷却退火。
在完成挤压成形后,需要对工件进行冷却和退火处理。
冷却可以通过水冷、风冷等方式进行,以快速降低工件温度,防止工件变形和晶粒长大。
而退火则是通过加热和保温的方式,使得工件内部的晶粒得以再结晶和调整,从而提高工件的塑性和韧性。
冷挤压工艺流程是一种常用的金属成型方法,通过原料准备、坯料加热、挤压成形、冷却退火等步骤,可以得到形状和尺寸精度高的工件。
在实际应用中,需要根据具体的金属材料和产品要求,合理设计和控制冷挤压工艺流程,以确保生产出符合要求的工件。
挤压模具设计说明书

由于B0=1.4㎜.本设计△=0.1
故Tk=1.4+0.1=1.5㎜
7.模孔工作带长度hg的确定
由于本型材制品的对称性较好,外形相对较小,一般可取2~6㎜,生产实践中对铝合金常用6~15㎜
本设计取hg=6mm
8.模芯的设计
一般伸出下模工作带3-5mm,本设计取4mm,模腔外形按空心型材的空心部分确定。
序号
(mm)
(mm)
单重wd
填充系数K
填充后长度Le
压余厚hy
(mm)
切压余后的有效长度Ld
挤压比
λ
制品长
L制
(m)
成品数
nx6
(m)
成品重
W制(kg)
成材率
W制/Wd
(%)
1
Φ95
Φ90
270
4.64
1.114
242
20
222
54.65
13.512×6m3.89 Nhomakorabea83.84%
2
Φ95
Φ90
320
5.50
因为本设计采用孔道式分流组合模
故:取H上=48H下=40模垫厚10㎜
5.组合模相关参数的确定:
1).分流孔的个数取4个,形状为扇形
2).扇形面积的确定:
因为分流孔面积与制品断面积的比值∑F分/F型=K,K即为分流比,,一般K对于空心型材时,取K=10~30。本设计取K=10
分流孔的面积∑F分=K. F型=10×241=2410 mm2
图7
依据经验a一般取2~5㎜,有的取8㎜.本设计取8㎜
图8
关于α的计算,由上图知
h=H/2+8=38.1/2+8=27.05㎜
铝、铜材连续挤压工艺
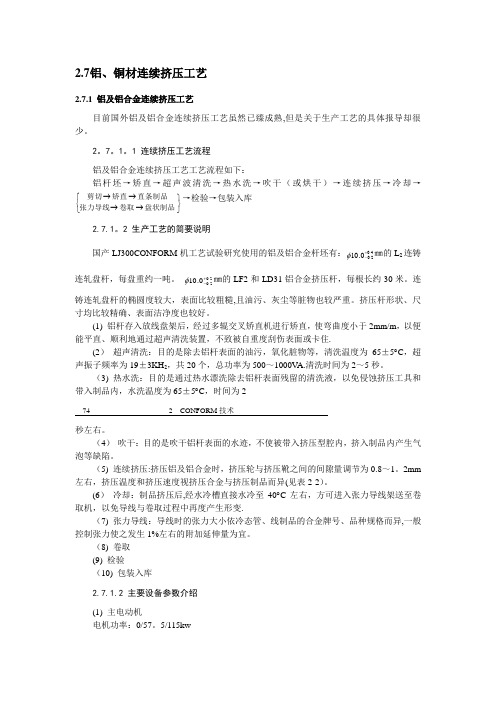
2.7 铝、铜材连续挤压工艺2.7.1 铝及铝合金连续挤压工艺目前国外铝及铝合金连续挤压工艺虽然已臻成熟,但是关于生产工艺的具体报导却很少。
2。
7。
1。
1 连续挤压工艺流程铝及铝合金连续挤压工艺工艺流程如下:铝杆坯→矫直→超声波清洗→热水洗→吹干(或烘干)→连续挤压→冷却→⎭⎬⎫⎩⎨⎧→→→→盘状制品卷取张力导线直条制品矫直剪切→检验→包装入库 2.7.1。
2 生产工艺的简要说明国产LJ300CONFORM 机工艺试验研究使用的铝及铝合金杆坯有:4.02.00.10+-φ㎜的L 2连铸连轧盘杆,每盘重约一吨。
2.02.00.10+-φ㎜的LF2和LD31铝合金挤压杆,每根长约30米。
连铸连轧盘杆的椭圆度较大,表面比较粗糙,且油污、灰尘等脏物也较严重。
挤压杆形状、尺寸均比较精确、表面洁净度也较好。
(1) 铝杆存入放线盘架后,经过多辊交叉矫直机进行矫直,使弯曲度小于2mm/m ,以便能平直、顺利地通过超声清洗装置,不致被自重度刮伤表面或卡住.(2) 超声清洗:目的是除去铝杆表面的油污,氧化脏物等,清洗温度为65±5︒C ,超声振子频率为19±3KH 2,共20个,总功率为500~1000V A.清洗时间为2~5秒。
(3) 热水洗:目的是通过热水漂洗除去铝杆表面残留的清洗液,以免侵蚀挤压工具和带入制品内,水洗温度为65±5︒C ,时间为274 2 CONFORM 技术秒左右。
(4) 吹干:目的是吹干铝杆表面的水迹,不使被带入挤压型腔内,挤入制品内产生气泡等缺陷。
(5) 连续挤压:挤压铝及铝合金时,挤压轮与挤压靴之间的间隙量调节为0.8~1。
2mm 左右,挤压温度和挤压速度视挤压合金与挤压制品而异(见表2-2)。
(6) 冷却:制品挤压后,经水冷槽直接水冷至40︒C 左右,方可进入张力导线架送至卷取机,以免导线与卷取过程中再度产生形变.(7) 张力导线:导线时的张力大小依冷态管、线制品的合金牌号、品种规格而异,一般控制张力使之发生1%左右的附加延伸量为宜。
- 1、下载文档前请自行甄别文档内容的完整性,平台不提供额外的编辑、内容补充、找答案等附加服务。
- 2、"仅部分预览"的文档,不可在线预览部分如存在完整性等问题,可反馈申请退款(可完整预览的文档不适用该条件!)。
- 3、如文档侵犯您的权益,请联系客服反馈,我们会尽快为您处理(人工客服工作时间:9:00-18:30)。
挤压流程工艺
挤压流程工艺是一种通过将材料加热至可塑性状态并通过挤压机将其挤出成型的工艺。
下面是一个常见的挤压流程工艺:
1. 材料准备:选择适合挤压的材料,通常是塑料、金属或橡胶等。
将材料切割成适当的长度或形状,并进行预处理,例如加热或混合。
2. 加热预处理:将材料加热至可塑性状态,使其软化、融化或变得更加适合挤压。
加热的方式可以是直接加热或间接加热,具体取决于材料的性质和要求。
3. 模具准备:准备好挤压机所需的模具,模具的形状和尺寸将决定最终产品的形状。
4. 挤压成型:将加热处理后的材料送入挤压机的料斗中,通过旋转或螺旋式进料系统将材料推入机器。
在进料系统中,材料将被高压齿轮齿条或螺杆挤压,通过模具的形状将材料挤出成型。
5. 冷却和固化:一旦材料经过模具形成所需的形状,它将进入冷却和固化阶段。
在这个阶段,产品被冷却,使其固化,并获得期望的强度和稳定性。
6. 切割和后处理:完成冷却和固化后,产品将经过切割和修整等后处理工序,以得到最终的产品形态和尺寸。
以上是一个常见的挤压流程工艺的基本步骤,具体的工艺流程可能会根据不同的材料和产品要求而有所不同。