球化衰退及球化不良
球墨铸铁件产生缺陷的原因有哪些?

球墨铸铁件产生缺陷的原因有哪些?球墨铸铁件产生缺陷的原因不单是球化处理问题,那么还有什么问题?在球墨铸铁件生产中,常见的铸件缺陷除有灰铸铁件的一般缺陷外,还有球化不良、球化衰退、夹渣、缩松、石墨漂浮、皮下气孔等。
通常,产生这些缺陷的原因不单是球化处理问题,有时还有造型制芯、熔炼浇注、配砂质量、落砂清理等许多生产工序的问题,因此必须具体分析。
以便采取相应的合理措施加以解决。
(1)球化不良特征:在铸件或试棒断面上分布有明显可见的小黑点,愈往中心愈密。
金相组织中.有聚集分布的厚片状石墨原因分析:1.原铁液硫含量过高2.铁液氧化3.残余球化剂量不足4反球化元素的干扰防止方法:1.尽量选用低硫的焦炭和新生铁。
若原铁液含硫量过高,应采用炉内、炉外脱硫或相应提高球化剂的加入量。
交界铁液一定要分离干净,灰铸铁的铁掖不应混入球墨铸铁中。
球化处理时,防止炉渣出到浇包中2.操作中严防铁液氧化3.熔制配比适当、成分稳定的中间合金,并采用合适的处理温度,注意球化处理操作。
防止铁液与合金作用过分激烈或“结死”在包底4镁球墨铸铁中。
加人少量的稀土,可中和反球化元素的干扰(2)球化衰退特征:球墨铸铁铁液,停留一定时间后,球化效果会消失原因分析: 铁液的残余镁量和残余稀土量随着时间的延长会逐渐减少,过了一定时间后。
球化剂残余量已减少到不足以保证铸件球化时,就造成球化衰退镁量和稀土量逐渐减少的原因是:1. 在铁液表面的MgS、CeS与空气中氧作用,发生下列反应:2MgS+O2=2MgO气↑+2S2CeS+ O2=2CeO气+2S烟状的MgO和CeO在空气中逸损,S返回铁液与Mg、Ce作用又生成MgS、CeS,这样循环,Mg、Ce不断损失2.镁在铁液中溶解度极小,大部分镁以微小的气泡悬浮在铁液中。
当有搅拌、回包、浇注、机械振动等情况时,镁气泡会集聚上浮,并穿出铁液表面。
遇空气燃浇而损失3.镁、稀土与氧有极大的亲和力。
铁液表面的镁和稀土要逐渐氧化、镁还有蒸发损失等防止方法:1.经球化处理的铁液应有足够的球化剂残余量2.降低原铁液硫含量,并防止铁液氧化3.球化处理后应扒净渣子4.缩短铁液经球化处理后的停留时间5.在铁液表面加覆盖熔剂,如石墨粉、木炭粉、冰晶石粉等(3)夹渣(黑渣)特征: 在铸件断面上呈现暗黑色,没有光泽,主要由琉化镁、硫化锰、氧化镁、二氧化硅、氧化铁、氢化镁等所组成,是一种非金属夹杂物,可用硫印、氧印等方法显示出来。
实战专家总结球化不良缺陷的13条原因,预防措施该如何做?
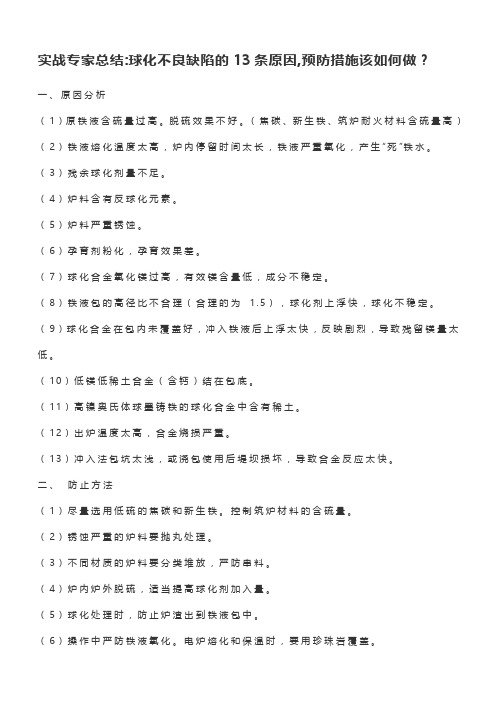
实战专家总结:球化不良缺陷的13条原因,预防措施该如何做?一、原因分析(1)原铁液含硫量过高。
脱硫效果不好。
(焦碳、新生铁、筑炉耐火材料含硫量高)(2)铁液熔化温度太高,炉内停留时间太长,铁液严重氧化,产生“死”铁水。
(3)残余球化剂量不足。
(4)炉料含有反球化元素。
(5)炉料严重锈蚀。
(6)孕育剂粉化,孕育效果差。
(7)球化合金氧化镁过高,有效镁含量低,成分不稳定。
(8)铁液包的高径比不合理(合理的为 1.5),球化剂上浮快,球化不稳定。
(9)球化合金在包内未覆盖好,冲入铁液后上浮太快,反映剧烈,导致残留镁量太低。
(10)低镁低稀土合金(含钙)结在包底。
(11)高镍奥氏体球墨铸铁的球化合金中含有稀土。
(12)出炉温度太高,合金烧损严重。
(13)冲入法包坑太浅,或浇包使用后堤坝损坏,导致合金反应太快。
二、防止方法(1)尽量选用低硫的焦碳和新生铁。
控制筑炉材料的含硫量。
(2)锈蚀严重的炉料要抛丸处理。
(3)不同材质的炉料要分类堆放,严防串料。
(4)炉内炉外脱硫,适当提高球化剂加入量。
(5)球化处理时,防止炉渣出到铁液包中。
(6)操作中严防铁液氧化。
电炉熔化和保温时,要用珍珠岩覆盖。
(7)在保证球化的前提下,尽量降低出炉温度。
(8)注意球化处理操作,调整铁液包的高径比,球化剂和硅铁上面要覆盖铁销或珍珠岩,防止铁液与球化剂作用过分激烈或“结死”包底。
(9)镁球化处理中,加入少量稀土,可中和反球化元素的干扰。
(10)包坑与堤坝按要求,损坏后要及时修复。
(11)使用配比合适、成分稳定的中间合金采用随流孕育和二次孕育。
(12)交界铁液要分离干净。
(13)厚大件球化处理时可冲入一些钼、铜、锑、铋等合金元素。
也可采用重稀土合金球化剂。
(14)使用低镁、低稀土合金,使球化处理反应平缓;减少镁的烧损。
(15)高镍奥氏体球墨铸铁处理用不含稀土的镍镁或硅镁合金。
(16)采用喂丝处理铁水包的出铁量要适当,或适当加高铁水包,留下喂丝时铁液反应空间。
低蠕化率蠕铁与球化不良及衰退球铁的区别

墨和团絮状石墨较多,严重时有片状石墨,组织粗大;球化良好的铸铁,球墨圆整,极少团絮状和蠕虫状石墨,没有片状石
墨,组织细密。力学性能的区别是:球化衰退球铁的力学性能已明显下降,低蠕化率蠕铁的力学性能则远高于规定要求,如
果采用适当的热处理方法,在冷热交变环境下服役能显示优异性能,因此,不能笼统地将其判为废品。
67.8 924:;<
(92=2> ?4@>AB C D=E><3@ F>42GHIJ KH1LM@J1,92=2> *+*&%%,KE24>)
>?@+&4(+:,EB J2GGBNB4OB3 PB@;BB4 IH;:QBNR2O<I>N2@S QBNR2O<I>N 2NH4,THHN 4HJ<I>N2UBJ 4HJ<I>N 2NH4 >4J JBVB4BN>@B 4HJ<I>N 2NH4 ;BNB 24@NHJ<OBJ 24 JB@>2I1 ,EB J2GGBNB4OB HG R2ONH3@N<O@<NB ;>3 >3 GHIIH;3:@EB IH;:QBNR2O<I>N2@S QBNR2O<I>N 2NH4 E>J VN>TE2@B 4HJ<IB HG VHHJ NH<4J4B33,@E2OA >4J 3EHN@ QBNR2O<I>N VN>TE2@B,> QBNS I2@@IB HG W<>32 4HJ<I>N:@BRTBN VN>3TE2@B,4H GI>AB VN>TE2@B, >4J JB43B:G24B R>@N2= 3@N<O@<NB1 ,EB J2GGBNB4OB HG RBOE>42O>I TNHTBN@2B3 ;>3 >3 GHIIH;3:@EB JBVB4BN>@B 4HJ<I>N 2NH4 E>3 HPQ2<H3IS JBONB>324V RBOE>42O>I TNHTBN@23,@EB IH;:QBNRO<I>N2@S QBNR2O<I>N 2NH4 E>3 RBOE>42O>I TNHTBN@2B3 R<OE E2VEBN @E>4 3@2T<I>@BJ NBW<2NBRB4@31 ?G >JHT@24V TNHTBN EB>@ :@NB>@24V TNHOB33,@EB IH; :QBNR2O<I>N2@S QBNR2O<I>N 2NH4 OH<IJ 3EH; B=OBIIB4@ TNHTBN@2B3 <4JBN @EB OHIJ:EB>@ >I@BN4>@24V O2NO<R3@>4OB,@EBNBGHNB,2@ ;H<IJ PB 4H@ TNHTBN @H OH432JBN 2@ VB4BN>IIS >3 @EB <4W<>I2GBJ O>3@24V1 A*5 ,.&:@:IH;:QBNRO<I>N2@S QBNR2O<I>N 2NH4;THHN 4HJ<I>N2@S;JBVB4BN>@B 4HJ<I>N2@S;OHIJ:EB>@ >I@BN4>@24V O2NO<R3@>4OB
我公司球化不良问题汇总及措施供大家分享
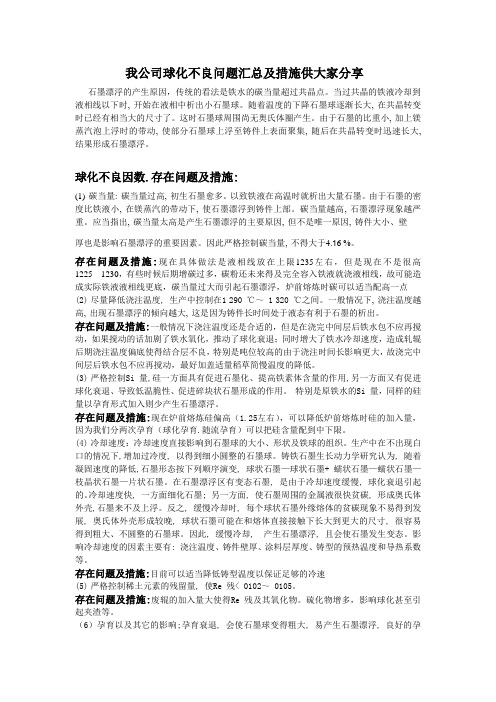
我公司球化不良问题汇总及措施供大家分享石墨漂浮的产生原因,传统的看法是铁水的碳当量超过共晶点。
当过共晶的铁液冷却到液相线以下时, 开始在液相中析出小石墨球。
随着温度的下降石墨球逐渐长大, 在共晶转变时已经有相当大的尺寸了。
这时石墨球周围尚无奥氏体圈产生。
由于石墨的比重小, 加上镁蒸汽泡上浮时的带动, 使部分石墨球上浮至铸件上表面聚集, 随后在共晶转变时迅速长大, 结果形成石墨漂浮。
球化不良因数.存在问题及措施:(1) 碳当量: 碳当量过高, 初生石墨愈多。
以致铁液在高温时就析出大量石墨。
由于石墨的密度比铁液小, 在镁蒸汽的带动下, 使石墨漂浮到铸件上部。
碳当量越高, 石墨漂浮现象越严重。
应当指出, 碳当量太高是产生石墨漂浮的主要原因, 但不是唯一原因, 铸件大小、壁厚也是影响石墨漂浮的重要因素。
因此严格控制碳当量, 不得大于4.16 %。
存在问题及措施:现在具体做法是液相线放在上限1235左右,但是现在不是很高1225---1230,有些时候后期增碳过多,碳粉还未来得及完全容入铁液就浇液相线,故可能造成实际铁液液相线更底,碳当量过大而引起石墨漂浮,炉前熔炼时碳可以适当配高一点(2)尽量降低浇注温度, 生产中控制在1 290 ℃~ 1 320 ℃之间。
一般情况下, 浇注温度越高, 出现石墨漂浮的倾向越大, 这是因为铸件长时间处于液态有利于石墨的析出。
存在问题及措施:一般情况下浇注温度还是合适的,但是在浇完中间层后铁水包不应再搅动,如果搅动的话加剧了铁水氧化,推动了球化衰退;同时增大了铁水冷却速度,造成轧辊后期浇注温度偏底使得结合层不良,特别是吨位较高的由于浇注时间长影响更大,故浇完中间层后铁水包不应再搅动,最好加盖适量稻草简慢温度的降低。
(3)严格控制Si 量,硅一方面具有促进石墨化、提高铁素体含量的作用,另一方面又有促进球化衰退、导致低温脆性、促进碎块状石墨形成的作用。
特别是原铁水的Si 量,同样的硅量以孕育形式加入则少产生石墨漂浮。
浅谈球墨铸铁及其球化不良缺陷
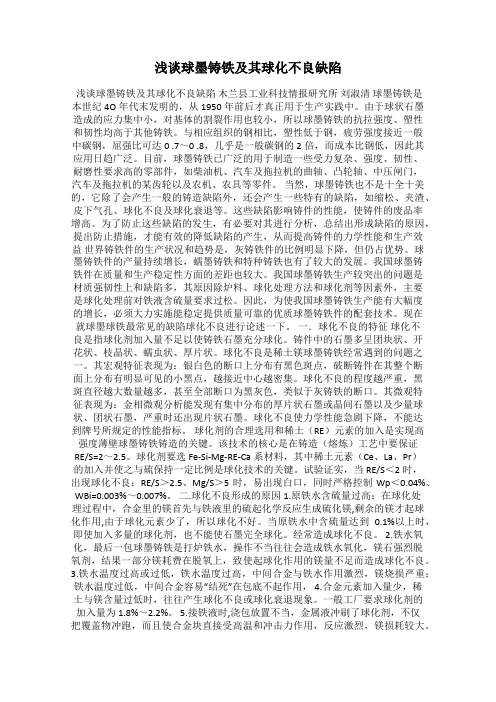
浅谈球墨铸铁及其球化不良缺陷浅谈球墨铸铁及其球化不良缺陷木兰县工业科技情报研究所刘淑清球墨铸铁是本世纪4O年代末发明的,从1950年前后才真正用于生产实践中。
由于球状石墨造成的应力集中小,对基体的割裂作用也较小,所以球墨铸铁的抗拉强度、塑性和韧性均高于其他铸铁。
与相应组织的钢相比,塑性低于钢,疲劳强度接近一般中碳钢,屈强比可达0 .7~0 .8,几乎是一般碳钢的2倍,而成本比钢低,因此其应用日趋广泛。
目前,球墨铸铁已广泛的用于制造一些受力复杂、强度、韧性、耐磨性要求高的零部件,如柴油机、汽车及拖拉机的曲轴、凸轮轴、中压闸门,汽车及拖拉机的某齿轮以及农机、农具等零件。
当然,球墨铸铁也不是十全十美的,它除了会产生一般的铸造缺陷外,还会产生一些特有的缺陷,如缩松、夹渣、皮下气孔、球化不良及球化衰退等。
这些缺陷影响铸件的性能,使铸件的废品率增高。
为了防止这些缺陷的发生,有必要对其进行分析,总结出形成缺陷的原因,提出防止措施,才能有效的降低缺陷的产生,从而提高铸件的力学性能和生产效益世界铸铁件的生产状况和趋势是,灰铸铁件的比例明显下降,但仍占优势。
球墨铸铁件的产量持续增长,蠕墨铸铁和特种铸铁也有了较大的发展。
我国球墨铸铁件在质量和生产稳定性方面的差距也较大。
我国球墨铸铁生产较突出的问题是材质强韧性上和缺陷多,其原因除炉料、球化处理方法和球化剂等因素外,主要是球化处理前对铁液含硫量要求过松。
因此,为使我国球墨铸铁生产能有大幅度的增长,必须大力实施能稳定提供质量可靠的优质球墨铸铁件的配套技术。
现在就球墨球铁最常见的缺陷球化不良进行论述一下。
一.球化不良的特征球化不良是指球化剂加入量不足以使铸铁石墨充分球化。
铸件中的石墨多呈团块状、开花状、枝晶状、蠕虫状、厚片状。
球化不良是稀土镁球墨铸铁经常遇到的问题之一。
其宏观特征表现为:银白色的断口上分布有黑色斑点,破断铸件在其整个断面上分布有明显可见的小黑点,越接近中心越密集。
球墨铸铁常见缺陷及防止措施

球墨铸铁常见缺陷及防止措施作者:叶得强来源:《名城绘》2019年第09期摘要:球墨铸铁具有优良的使用性能,但在生产中常出现缩孔、缩松、夹渣、球化不良及球化衰退等缺陷。
当球墨铸铁出现相应缺陷的时候,会对产品质量产生直接影响,所以必须对其做到足够重视。
为了防止这些缺陷的产生,需对其进行分析,提出防止产生缺陷的办法,降低废品率,提高工厂的经济效益当球墨铸铁出现相应缺陷的时候,会对产品质量产生直接影响,所以必须对其做到足够重视。
在文本中,分析了球墨铸铁的常见缺陷,并且提出了相关防治措施。
关键词:球墨铸铁;常见缺陷;防治措施球墨铸铁是20世纪五十年代发展起来的一种高强度铸铁材料,其综合性能接近于钢,正是基于其优异的性能,已成功地用于铸造一些受力复杂,强度、韧性、耐磨性要求较高的零件。
球墨铸铁已迅速发展为仅次于灰铸铁的、应用十分广泛的铸铁材料。
所谓“以铁代钢”,主要指球墨铸铁。
在国内生产中,较多的对双联熔炼工艺进行应用,但在实际生产中,所具有的铁液熔炼温度存在一定的不足,并因此对铁液的成本以及质量产生影响。
对于中频感应电炉熔炼方式来说,在实际应用中即能够较灵活的调整成分,具有工艺简单以及质量高的特征,在较多铸造厂当中得到了应用。
一、球墨铸铁常见缺陷及形成原因1、石墨漂浮。
通常认为,石墨漂浮的产生过程是由于碳、硅含量高,铁液冷却速度缓慢,析出多量的大径石墨,并在铸件上部偏析而集聚。
石墨漂浮的产生主要与碳当量有关。
除了碳当量过高,还与铁液中存在过多的氧化物浮渣和硫化物浮渣有关,由于它们的存在而加剧了石墨的漂浮。
2、缩孔缩松。
当球磨铸铁处于凝固状态中的时候,共晶膨胀力得到相应增大,当铸型钢度比较小,胀大铸铁外形的时候,铸件最终凝固部位所得到的液态金属补偿是无法对相关要求进行满足的,进一步导致缩孔缩松问题的出现。
同时,对于大型球墨铸铁件来说,其本种问题是比较容易出现的,主要的原因是壁厚尺寸和热节厚,在没有对浇注系统进行合理设计的条件下,型腔中的铁液温度梯度无法对相关要求进行有效满足,尚未合理设置配套补缩冒口,也就无法补缩相应热节的液体冷却。
球化不良解析与措施

2〕预防措施 ① 测球化前首温,管制1530℃↓ ② 针对低温产品,要求出铁温度低时,铁水倒入球化桶内,人 工晃动球化桶让其完全球化反应,且时间不可超过180秒。 ③ 球化剂、覆盖剂填埋松一点。
④ 确保桶内无残余铁水,及按规定进行洗锅,避免球化剂烧损。
FUJIWA MACHINERY INDUSTRY (KUNSHAN) CO., LTD.
每包压包前后均要检查球化室情况,待铁水包冷下来后 应该用棍子将球化室中的渣滓戳干净。
出水如果发现异常立即停止出水,将铁水回炉进行确认 球化。
FUJIWA MACHINERY INDUSTRY (KUNSHAN) CO., LTD.
五、操作细节问题
2、包温过高,球化剂的Mg吸收率低 1)现象
球化包内壁超过温度900℃,内壁通红!(球化包温度也 不能过低,应500℃↑,否则影响浇注温度)。
③ 加球化剂的漏斗放在球化桶上,必须确认漏斗口是否对准球化室;
④ 做一个放料盆的搁架,依照顺序放球化剂、孕育剂、覆盖剂,从料架上依次取 用球化辅料;
⑤ 倒空的球化剂、孕育剂、覆盖剂的空盆,必需放回料架;
⑥ 球化人员必需注意每桶的球化状况;
⑦ 各种料盆,使用喷上不同颜色和原料名称,搁架上贴标签,比如球化剂标识为 绿底黑字。称量球化剂的盆子刷成绿色,且摆的顺序由上而下为球化剂、覆盖 剂、孕育剂;
球墨铸铁件常见缺陷的分析与对策(1)
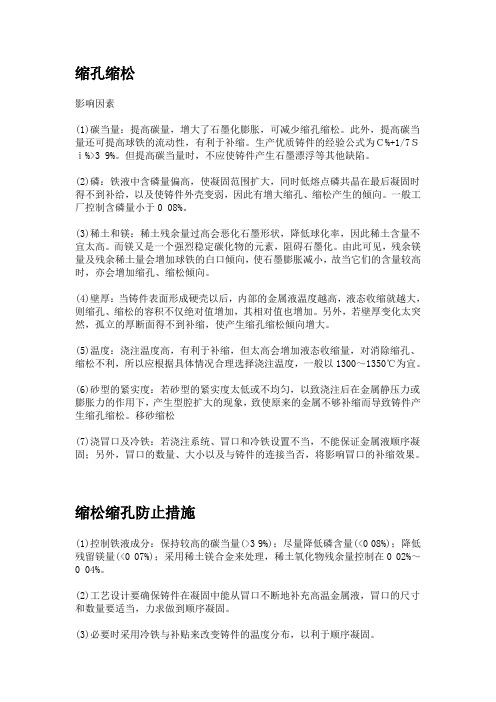
缩孔缩松影响因素(1)碳当量:提高碳量,增大了石墨化膨胀,可减少缩孔缩松。
此外,提高碳当量还可提高球铁的流动性,有利于补缩。
生产优质铸件的经验公式为C%+1/7Si%>3 9%。
但提高碳当量时,不应使铸件产生石墨漂浮等其他缺陷。
(2)磷:铁液中含磷量偏高,使凝固范围扩大,同时低熔点磷共晶在最后凝固时得不到补给,以及使铸件外壳变弱,因此有增大缩孔、缩松产生的倾向。
一般工厂控制含磷量小于0 08%。
(3)稀土和镁:稀土残余量过高会恶化石墨形状,降低球化率,因此稀土含量不宜太高。
而镁又是一个强烈稳定碳化物的元素,阻碍石墨化。
由此可见,残余镁量及残余稀土量会增加球铁的白口倾向,使石墨膨胀减小,故当它们的含量较高时,亦会增加缩孔、缩松倾向。
(4)壁厚:当铸件表面形成硬壳以后,内部的金属液温度越高,液态收缩就越大,则缩孔、缩松的容积不仅绝对值增加,其相对值也增加。
另外,若壁厚变化太突然,孤立的厚断面得不到补缩,使产生缩孔缩松倾向增大。
(5)温度:浇注温度高,有利于补缩,但太高会增加液态收缩量,对消除缩孔、缩松不利,所以应根据具体情况合理选择浇注温度,一般以1300~1350℃为宜。
(6)砂型的紧实度:若砂型的紧实度太低或不均匀,以致浇注后在金属静压力或膨胀力的作用下,产生型腔扩大的现象,致使原来的金属不够补缩而导致铸件产生缩孔缩松。
移砂缩松(7)浇冒口及冷铁:若浇注系统、冒口和冷铁设置不当,不能保证金属液顺序凝固;另外,冒口的数量、大小以及与铸件的连接当否,将影响冒口的补缩效果。
缩松缩孔防止措施(1)控制铁液成分:保持较高的碳当量(>3 9%);尽量降低磷含量(<0 08%);降低残留镁量(<0 07%);采用稀土镁合金来处理,稀土氧化物残余量控制在0 02%~0 04%。
(2)工艺设计要确保铸件在凝固中能从冒口不断地补充高温金属液,冒口的尺寸和数量要适当,力求做到顺序凝固。
(3)必要时采用冷铁与补贴来改变铸件的温度分布,以利于顺序凝固。
- 1、下载文档前请自行甄别文档内容的完整性,平台不提供额外的编辑、内容补充、找答案等附加服务。
- 2、"仅部分预览"的文档,不可在线预览部分如存在完整性等问题,可反馈申请退款(可完整预览的文档不适用该条件!)。
- 3、如文档侵犯您的权益,请联系客服反馈,我们会尽快为您处理(人工客服工作时间:9:00-18:30)。
(4)注意处理温度。出炉温度应低于1460t,以防球化剂严重烧损;要防止高温下的氧化现象,盖好筱盖球化剂的铁板(厚度应>3mm) ;铁液扒渣后应用草木灰等盖好;当铁液温度>1350℃出现球化不良及衰退时,可补加球化荆;而当<1350℃时就不能补加球化剂,也不得浇注球铁件,只能补加其它铁液浇注不重要的灰铸铁件或芯骨等。
(2)硫:当铁液中的含硫量太高时,硫与镁和稀土生成硫化物.因其密度小而上浮到铁液表面,而这些硫化物与空气中的载发生反应生成硫,硫又回到铁液,又重复上述过程,从而降低了镁与稀土含量。当铁液中的硫大于0.1%时,即使加入多量的球化剂,也不能使石墨完全球化。
(3)稀土与镁:稀土与镁含量过低时,往往产生球化不良或球化衰退现象。一般工厂要求球化剂的加人量为1.8%一2.2%0
影晌因素
(1)碳当量:铁液的碳当量大高时(尤其是硅含量也高时)将使石里球化受到影响。试验表明,对于厚壁铸件,当碳当盆超过共晶成分时就有可能产生开花状石墨。但是提高铁液的含碳量有利于镁回收率的提高。因此生产中大多采用高碳低硅的原则,通常含硅量控制在2%左右。此外,碳当量的选取还与铸件壁厚有关:当壁厚为6.5一76mm时,碳当量为4.35%--4.7%;当壁厚>76mm,碳当量为4.3%一4.35 % () .
(5)铁液出炉后应及时浇注,浦留时间不得超过20min
(6)合理设计浇冒口,采用型内和型上球化处理,加强孕育。
(1)严格控制铁液成分:选择合适的碳当量;铁液中的含硫量应小于0.08% (其中生铁含硫不得大于0.03%,焦碳含硫不得大于0.08%),可采用小苏打进行脱硫。
(2)加入足够的球化剂,一般为1.8%一2.2%;此外应注意球化剂的质量,若球化剂破碎后使用,放置时间不得超过一周。处理后的球铁铁液中稀土镁的残留量不应过低,MgM>0.02%, REA>0.02%,
(4)壁厚:铸件壁太厚也容易产生球化不良及衰退缺陷,主要是因为铁液在铸型中长时间处于液态,镁燕汽上浮,造成镁含量降低;共晶时大量石墨生成而释放出的结晶潜热使奥氏体壳重新熔化,石墨伸出壳外而崎形长大,形成非球状石墨。
(5)温度:若铁液沮度过高,铁液氧化严重,由于镁与稀土易与氧化物产生还原反应,而使得镁、稀土含量降低,同时高温也将增加镁的烧损和蒸发;铁液沮度太低,球化剂不能熔化和被铁液吸收,而上浮至铁液表面燃烧或被氧化。
(6)滞留时间:铁液中镁的含量是随孕育处理后停留时间的增加而减少,其主要原因是因硫及镁、稀土的氧化与燕发造成的。图5反映了滞留时间与残镁量的关系(1),一般情况下,滞留时间不超过20min。
(7)浇冒口:浇冒口若设计不合理,会产生浇注时间太长、铁液飞溅以及卷入空气,使镁、稀土氧化严重。
S.2防止措施ห้องสมุดไป่ตู้