球铁及其球化不良问题探讨分析
球墨铸铁常见缺陷的分析与对策
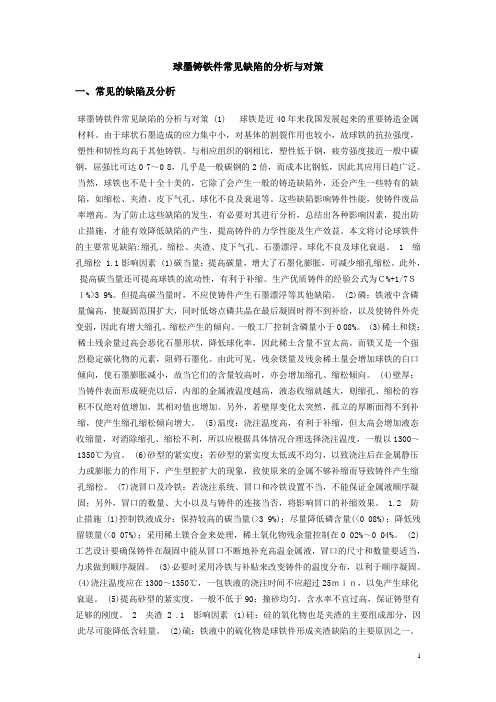
球墨铸铁件常见缺陷的分析与对策一、常见的缺陷及分析球墨铸铁件常见缺陷的分析与对策 (1) 球铁是近40年来我国发展起来的重要铸造金属材料。
由于球状石墨造成的应力集中小,对基体的割裂作用也较小,故球铁的抗拉强度,塑性和韧性均高于其他铸铁。
与相应组织的钢相比,塑性低于钢,疲劳强度接近一般中碳钢,屈强比可达0 7~0 8,几乎是一般碳钢的2倍,而成本比钢低,因此其应用日趋广泛。
当然,球铁也不是十全十美的,它除了会产生一般的铸造缺陷外,还会产生一些特有的缺陷,如缩松、夹渣、皮下气孔、球化不良及衰退等。
这些缺陷影响铸件性能,使铸件废品率增高。
为了防止这些缺陷的发生,有必要对其进行分析,总结出各种影响因素,提出防止措施,才能有效降低缺陷的产生,提高铸件的力学性能及生产效益。
本文将讨论球铁件的主要常见缺陷:缩孔、缩松、夹渣、皮下气孔、石墨漂浮、球化不良及球化衰退。
1 缩孔缩松 1.1影响因素 (1)碳当量:提高碳量,增大了石墨化膨胀,可减少缩孔缩松。
此外,提高碳当量还可提高球铁的流动性,有利于补缩。
生产优质铸件的经验公式为C%+1/7Si%>3 9%。
但提高碳当量时,不应使铸件产生石墨漂浮等其他缺陷。
(2)磷:铁液中含磷量偏高,使凝固范围扩大,同时低熔点磷共晶在最后凝固时得不到补给,以及使铸件外壳变弱,因此有增大缩孔、缩松产生的倾向。
一般工厂控制含磷量小于0 08%。
(3)稀土和镁:稀土残余量过高会恶化石墨形状,降低球化率,因此稀土含量不宜太高。
而镁又是一个强烈稳定碳化物的元素,阻碍石墨化。
由此可见,残余镁量及残余稀土量会增加球铁的白口倾向,使石墨膨胀减小,故当它们的含量较高时,亦会增加缩孔、缩松倾向。
(4)壁厚:当铸件表面形成硬壳以后,内部的金属液温度越高,液态收缩就越大,则缩孔、缩松的容积不仅绝对值增加,其相对值也增加。
另外,若壁厚变化太突然,孤立的厚断面得不到补缩,使产生缩孔缩松倾向增大。
实战专家总结球化不良缺陷的13条原因,预防措施该如何做?
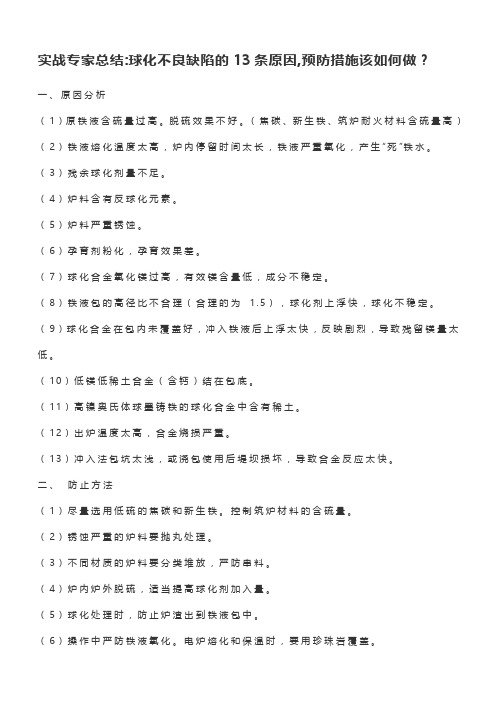
实战专家总结:球化不良缺陷的13条原因,预防措施该如何做?一、原因分析(1)原铁液含硫量过高。
脱硫效果不好。
(焦碳、新生铁、筑炉耐火材料含硫量高)(2)铁液熔化温度太高,炉内停留时间太长,铁液严重氧化,产生“死”铁水。
(3)残余球化剂量不足。
(4)炉料含有反球化元素。
(5)炉料严重锈蚀。
(6)孕育剂粉化,孕育效果差。
(7)球化合金氧化镁过高,有效镁含量低,成分不稳定。
(8)铁液包的高径比不合理(合理的为 1.5),球化剂上浮快,球化不稳定。
(9)球化合金在包内未覆盖好,冲入铁液后上浮太快,反映剧烈,导致残留镁量太低。
(10)低镁低稀土合金(含钙)结在包底。
(11)高镍奥氏体球墨铸铁的球化合金中含有稀土。
(12)出炉温度太高,合金烧损严重。
(13)冲入法包坑太浅,或浇包使用后堤坝损坏,导致合金反应太快。
二、防止方法(1)尽量选用低硫的焦碳和新生铁。
控制筑炉材料的含硫量。
(2)锈蚀严重的炉料要抛丸处理。
(3)不同材质的炉料要分类堆放,严防串料。
(4)炉内炉外脱硫,适当提高球化剂加入量。
(5)球化处理时,防止炉渣出到铁液包中。
(6)操作中严防铁液氧化。
电炉熔化和保温时,要用珍珠岩覆盖。
(7)在保证球化的前提下,尽量降低出炉温度。
(8)注意球化处理操作,调整铁液包的高径比,球化剂和硅铁上面要覆盖铁销或珍珠岩,防止铁液与球化剂作用过分激烈或“结死”包底。
(9)镁球化处理中,加入少量稀土,可中和反球化元素的干扰。
(10)包坑与堤坝按要求,损坏后要及时修复。
(11)使用配比合适、成分稳定的中间合金采用随流孕育和二次孕育。
(12)交界铁液要分离干净。
(13)厚大件球化处理时可冲入一些钼、铜、锑、铋等合金元素。
也可采用重稀土合金球化剂。
(14)使用低镁、低稀土合金,使球化处理反应平缓;减少镁的烧损。
(15)高镍奥氏体球墨铸铁处理用不含稀土的镍镁或硅镁合金。
(16)采用喂丝处理铁水包的出铁量要适当,或适当加高铁水包,留下喂丝时铁液反应空间。
球化过程及主要缺陷分析 文档
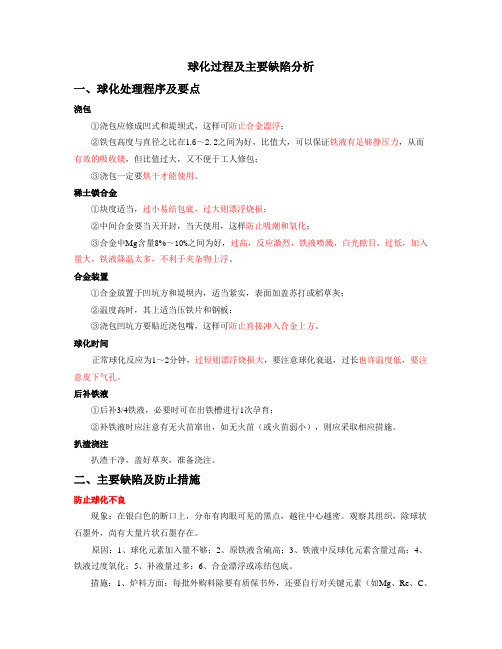
球化过程及主要缺陷分析一、球化处理程序及要点浇包①浇包应修成凹式和堤坝式,这样可防止合金漂浮;②铁包高度与直径之比在1.6~2.2之间为好,比值大,可以保证铁液有足够静压力,从而有效的吸收镁,但比值过大,又不便于工人修包;③浇包一定要烘干才能使用。
稀土镁合金①块度适当,过小易结包底,过大则漂浮烧损;②中间合金要当天开封,当天使用,这样防止吸潮和氧化;③合金中Mg含量8%~10%之间为好,过高,反应激烈,铁液喷溅,白光眩目。
过低,加入量大,铁液降温太多,不利于夹杂物上浮。
合金装置①合金放置于凹坑方和堤坝内,适当紧实,表面加盖苏打或稻草灰;②温度高时,其上适当压铁片和钢板;③浇包凹坑方要贴近浇包嘴,这样可防止直接冲入合金上方。
球化时间正常球化反应为1~2分钟,过短则漂浮烧损大,要注意球化衰退,过长也许温度低,要注意皮下气孔。
后补铁液①后补3/4铁液,必要时可在出铁槽进行1次孕育;②补铁液时应注意有无火苗窜出,如无火苗(或火苗弱小),则应采取相应措施。
扒渣浇注扒渣干净,盖好草灰,准备浇注。
二、主要缺陷及防止措施防止球化不良现象:在银白色的断口上,分布有肉眼可见的黑点,越往中心越密。
观察其组织,除球状石墨外,尚有大量片状石墨存在。
原因:1、球化元素加入量不够;2、原铁液含硫高;3、铁液中反球化元素含量过高;4、铁液过度氧化;5、补液量过多;6、合金漂浮或冻结包底。
措施:1、炉料方面:每批外购料除要有质保书外,还要自行对关键元素(如Mg、Re、C、S、As等)进行检测。
自制合金也要随机抽样化验,并要做到当天熔制当天破碎和使用。
2、熔炼方面:严格按照操作指导书的要求配制铁水,各元素的最终成分应该在一定的变化范围内。
3、处理方面:球化剂不可压得过紧和过松,并且放入包内时间越短越好。
一定要做到定量出液,特别要防止包内进渣,处理后要及时搅拌,扒净浮渣,盖好草灰。
防止皮下气孔现象:经常在铸件上表面的表层内,一般位于表面下0.5m m~3mm处,形成分散细小的圆形或椭圆形光滑孔洞,直径多在1~3mm左右。
球铁常见缺陷及特征
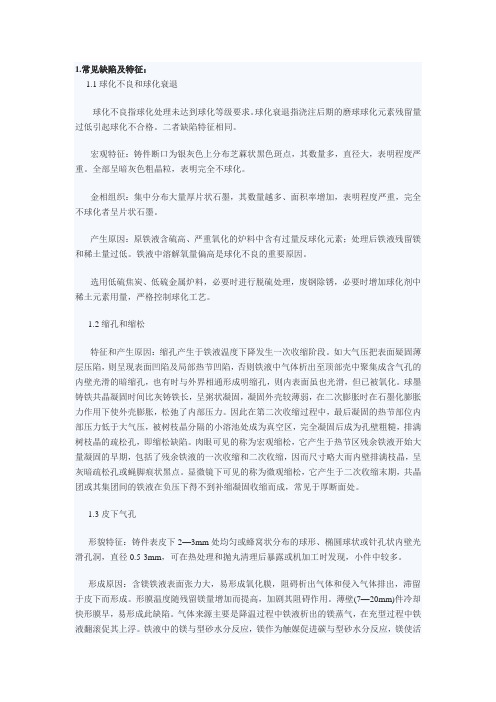
1.常见缺陷及特征:1.1球化不良和球化衰退球化不良指球化处理未达到球化等级要求。
球化衰退指浇注后期的磨球球化元素残留量过低引起球化不合格。
二者缺陷特征相同。
宏观特征:铸件断口为银灰色上分布芝蔴状黑色斑点,其数量多,直径大,表明程度严重。
全部呈暗灰色粗晶粒,表明完全不球化。
金相组织:集中分布大量厚片状石墨,其数量越多、面积率增加,表明程度严重,完全不球化者呈片状石墨。
产生原因:原铁液含硫高、严重氧化的炉料中含有过量反球化元素;处理后铁液残留镁和稀土量过低。
铁液中溶解氧量偏高是球化不良的重要原因。
选用低硫焦炭、低硫金属炉料,必要时进行脱硫处理,废钢除锈,必要时增加球化剂中稀土元素用量,严格控制球化工艺。
1.2缩孔和缩松特征和产生原因:缩孔产生于铁液温度下降发生一次收缩阶段。
如大气压把表面疑固薄层压陷,则呈现表面凹陷及局部热节凹陷,否则铁液中气体析出至顶部壳中聚集成含气孔的内壁光滑的暗缩孔,也有时与外界相通形成明缩孔,则内表面虽也光滑,但已被氧化。
球墨铸铁共晶凝固时间比灰铸铁长,呈粥状凝固,凝固外壳较薄弱,在二次膨胀时在石墨化膨胀力作用下使外壳膨胀,松弛了内部压力。
因此在第二次收缩过程中,最后凝固的热节部位内部压力低于大气压,被树枝晶分隔的小溶池处成为真空区,完全凝固后成为孔壁粗糙,排满树枝晶的疏松孔,即缩松缺陷。
肉眼可见的称为宏观缩松,它产生于热节区残余铁液开始大量凝固的早期,包括了残余铁液的一次收缩和二次收缩,因而尺寸略大而内壁排满枝晶,呈灰暗疏松孔或蝇脚痕状黑点。
显微镜下可见的称为微观缩松,它产生于二次收缩末期,共晶团或其集团间的铁液在负压下得不到补缩凝固收缩而成,常见于厚断面处。
1.3皮下气孔形貌特征:铸件表皮下2—3mm处均匀或蜂窝状分布的球形、椭圆球状或针孔状内壁光滑孔洞,直径0.5-3mm,可在热处理和抛丸清理后暴露或机加工时发现,小件中较多。
形成原因:含镁铁液表面张力大,易形成氧化膜,阻碍析出气体和侵入气体排出,滞留于皮下而形成。
球化剂对球铁影响

球化剂对球铁影响以球化剂对球铁的影响为标题,我们将从以下几个方面进行探讨和分析。
1. 球化剂的作用原理球化剂是一种在铁熔液中加入的特殊化合物,它能够改变铁的微观组织结构,使之由板条状铁素体转变为球状铁素体。
球状铁素体具有较好的塑性和韧性,因此球化剂的添加可以显著提高球铁的力学性能。
2. 球化剂的种类和选择目前常用的球化剂包括稀土系球化剂、硅铁球化剂等。
不同的球化剂对球铁的影响略有差异,因此在实际应用中需要根据具体要求选择合适的球化剂。
3. 球化剂对球铁的影响(1)改善铁的铸造性能:球化剂的添加可以改善铁的流动性和润湿性,减少铁水在浇注过程中的气孔和缺陷,提高铁件的表面质量和尺寸精度。
(2)提高球铁的力学性能:球化剂能够促使铁素体形成球状结构,使球铁具有较高的塑性和韧性,降低其脆性,提高抗拉强度和抗冲击性能。
(3)改善球铁的热处理性能:球化剂的添加可以使球铁具有较好的热处理响应性,有利于后续的热处理工艺,如淬火、回火等,进一步提高球铁的力学性能。
(4)调节球铁的组织和相态:球化剂的添加可以调节球铁的组织和相态,优化其性能和结构。
例如,适量的球化剂添加可以使球铁中的珠光体含量增加,提高其硬度和磨削性能。
4. 球化剂的使用注意事项在使用球化剂时,需要注意以下几个方面:(1)球化剂的添加量应适中,过多或过少都会影响球铁的性能。
因此,需要进行试验和优化,确定最佳的添加量。
(2)球化剂的加入时间和方式应掌握好,一般在铁液准备和调温阶段加入,确保球化剂充分分散和溶解。
(3)球化剂的质量要求高,应选择优质的球化剂供应商,并进行必要的质量检验和控制。
(4)球化剂的存储和保管要注意防潮、防火等安全措施,避免对环境和人体造成伤害。
球化剂对球铁具有显著的影响,可以改善球铁的铸造性能和力学性能,提高其综合性能和应用价值。
在实际生产中,需要根据具体情况选择合适的球化剂,并注意使用和管理要点,以确保球铁的质量和稳定性。
影响球化处理若干因素及应对措施

影响球化处理的若干因素及对策方法。
球墨铸铁定义:球墨铸铁是指铁液在凝固过程中碳以球形石墨析出的铸铁。
影响球化不良、球化衰退的因素有:一.操作原因:1.球化剂未扒平捣实,未按压包要求操作。
对策:将球化剂倒入包坑内,用铁棍扒平捣实,倒入孕育剂后再次扒平捣实,(覆盖1-1.5kg除渣剂)用硅钢片10-15kg覆盖。
2.球化剂未按额定要求称量准确。
对策:保证基本加入量,其重量为20kg/包,并准确称量。
3.出铁时浇包未注意压包方向,铁液直接冲在球化剂上。
对策:必须保证埋包方向靠电炉。
4.出铁速度太慢。
对策:出铁时,前期尽可能快,后期速度开始放缓,以保证铁液的飞溅和铁重的准确性。
5.出铁包残留铁液未倾倒干净。
对策:必须保证每次压包时无铁液残留在包内。
6.出铁量过多。
对策:允许上下波动范围在±50kg,超过该范围必须采取浇注一半后回炉或直接回炉。
7.未及时更换出铁包。
8.对策:要求每炉次更换一次出铁包。
9.未掌握好生产节拍,压球化剂过早或停留时间过长。
对策:需时刻观察造型节拍,不能压包停留时间过长或出铁后等浇注。
10.浇注包内残留铁液过多。
对策:原则上不允许有铁液残留在浇注包内,鉴于各产品重量差异,允许包内残余铁液<30kg。
11.出铁包内渣过多未及时清理。
对策:要求每更换一次球化包就要对包进行一次除渣处理。
12.炉前出铁温度过高。
对策:1)、产品要求浇注温度在1410-1430℃时需增加覆盖用硅钢片18-20kg 或加盖一块钢板。
2)、在压包未知的情况下,如出炉温度过高,反应过快,应减少出铁量或直接回炉处理。
3)、炉前已测得出炉温度过高时应采取打开炉盖,降温到要求温度(依据各产品浇注温度)才可出炉。
二.球化包、浇注原因:1.出铁包、浇包未烘透烘干。
对策:应按照筑包烘包要求进行操作,初次使用的浇包应烫包后才可使用,发现球化时有大量浓烟,浇注包外有大量水蒸汽冒出时,应回炉处理。
2.球化包堤坝太矮或包坑太小。
【坛友分享】球铁件七种常见缺陷原因分析

【坛友分享】球铁件七种常见缺陷原因分析热加工行业论坛热加工行业论坛昨天1、石墨球异化石墨球异化出现不规则石墨,如团块状、蝌蚪状、蠕虫状、角状或其他非圆球状。
这是由于球状石墨沿辐射方向生长时,局部晶体生长模式和生长速率偏离正常生长规律所致。
铸件中残余球化元素量超出应有范围时,如残余镁太高,超过了保持石墨球化所需的最低量时,也会影响石墨结晶条件,就容易产生蝌蚪壮石墨。
而残余稀土较多时,高碳当量铁水易产生碎块石墨,碎块石墨的集中区域一般称做“灰斑”。
而蠕虫状石墨的出现则是由于球化元素残余量不足或者含有超限的钛和铝。
2、石墨漂浮过共晶成分的厚壁球铁件中,在浇注位置顶部,常常出现一个石墨密集区域,即“始末漂浮”现象,这是由于石墨与铁水密度不同,过共晶铁水直接析出的石墨受到浮力作用向上所致。
石墨漂浮程度与碳当量、球化元素的种类及残留量、铸件凝固时间、浇注温度等因素有关系。
镁能使球铁的共晶含碳量提高,碳当量相同的铁水,提高其残余镁量就能减少石墨漂浮,残留稀土量过高,有助于爆裂状石墨的升成。
3、反白口一般铸铁件的白口组织容易出现在冷却较快的表层、尖角、披缝等处,反白口缺陷则相反,碳化物相出现在铸件中等断面心部、热节等部位。
球化元素残余量过多时,有促进反白口缺陷产生的作用,稀土元素强于镁,它们一般都能增加球铁组织形成时的过冷度。
4、皮下针孔皮下针孔内主要含有氢,也有少量一氧化碳和氮。
残余镁量过高时,也同时加强了从湿型中吸收氢的倾向,因而产生皮下针孔的几率增加。
另外,球化铁水停留时间长也能增加针孔的数量。
5、缩孔缩松缩孔常出现在铸件最后凝固部位(热节处、冒口颈与铸件连接处、内角或内浇口与铸件连接处),是隐蔽于铸件内部或与外表连通的孔洞。
缩松,宏观的出现在热节处,细微的收缩孔洞,大多是孔洞内部互相连通。
与球化元素有关的是,要控制残余镁和稀土不能过高,这对减少宏观和微观缩松都有明显效果,缩松倾向几乎与球化元素成正比。
6、黑渣它一般发生在铸件的上部(浇注位置),主要分为块状、绳索状和细碎黑渣。
球墨铸铁件表面球化衰退的研究

球墨铸铁件表面球化衰退的研究
球墨铸铁(Ductile iron)是一种具有高强度和高韧性的铸铁材料,它通过球墨化处理(Spheroidization process)使铸铁组织中的石墨以球状形态存在,从而提高了材料的塑性和耐磨性。
球化衰退是指球墨铸铁在使用过程中,球状石墨的形态发生退化,变得不规则、片状或断裂,从而影响了材料的性能。
球墨铸铁的球化衰退通常与以下几个方面有关:
1. 材料成分和熔炼工艺:球墨铸铁的化学成分和熔炼工艺对材料的球化效果有重要影响。
合理选择合金元素含量和添加剂,严格控制合金熔炼温度和时间,以及采取适当的球化剂,可以提高球状石墨的稳定性和一致性。
2. 球化处理工艺:球化处理是通过在铸件冷却过程中添加球化剂,使石墨球化的过程。
球化处理的温度、时间和冷却速率等参数对球状石墨形态的稳定性具有重要影响。
不适当的球化处理工艺可能导致球墨铸铁球状石墨的退化。
3. 热处理和应力状况:球墨铸铁在使用过程中,可能会受到热处理或应力的影响,从而导致球状石墨的退化。
高温时的相变、残余应力
和机械载荷等都可能对球状石墨产生负面影响,导致其断裂或退化。
为了研究球墨铸铁件表面球化衰退,通常需要对材料的成分、熔炼工艺、球化处理工艺以及应力状况等进行综合分析和实验研究。
通过优化材料配方、改进熔炼和球化处理工艺,以及合理设计和控制热处理条件,可以有效减少球墨铸铁件表面球化衰退现象的发生,提高材料的性能和使用寿命。
- 1、下载文档前请自行甄别文档内容的完整性,平台不提供额外的编辑、内容补充、找答案等附加服务。
- 2、"仅部分预览"的文档,不可在线预览部分如存在完整性等问题,可反馈申请退款(可完整预览的文档不适用该条件!)。
- 3、如文档侵犯您的权益,请联系客服反馈,我们会尽快为您处理(人工客服工作时间:9:00-18:30)。
球铁及其球化不良问题探讨分析岗铁的应用使人类文明进入了铁器时代。
球墨铸铁的诞生,是继人类发明炼钢技术之后,在黑色金属应用技术方面又一次大的技术创新,是20世纪材料科学最重大的技术进展之一。
我国古代工匠早在2000年前就已制造出具有球状石墨的铸铁,分析表明上述铸铁件不含镁或稀土元素,是采用高纯木炭生铁熔剂,在金属型中浇注,经热处理后制成。
但由于这种工艺难于大量生产,因而这种古代球铁的独特技艺没有流传至今。
现代球墨铸铁采用向铁液中添加球化剂的方法使其在铸态下析出球状石墨,使得球墨铸铁真正登上了工业应用的舞台。
世界铸铁件的生产状况和趋势是,灰铸铁件的比例明显下降,但仍占优势。
球墨铸铁件的产量持续增长,蠕墨铸铁和特种铸铁也有了较大的发展。
我国球墨铸铁件在质量和生产稳定性方面的差距也较大。
我国球墨铸铁生产较突出的问题是材质强韧性上、缺陷多,其原因除炉料、球化处理方法和球化剂等因素外,主要是球化处理前对铁液含硫量要求过松。
因此,为使我国球墨铸铁生产能有大幅度的增长,必须大力实施能稳定提供质量可靠的优质球墨铸铁件的配套技术。
现在就球铁常见的缺陷球化不良结合我们单位的实际系统地进行论述一下。
球化剂的合理选用和稀土(RE)元素的加入是实现高强度薄壁球墨铸铁铸造的关键。
⑴该技术的核心是在铸造(熔炼)工艺中要保证RE/S=2~2.5。
球化剂要选用Fe-Si-Mg-RE-Ca 系材料,其中稀土元素(Ce、La、Pr)的加入并使之与硫保持一定比例是球化技术的关键。
试验证实,当RE/S<2时,出现球化不良;RE/S>2.5、Mg/S>5时,易出现白口,同时严格控Wp<0.04%、WBi=0.003%~0.007%。
灰铸铁铸件所产生的各种铸造缺陷(如缩孔、气孔、渣孔、夹砂、冷隔、浇不足等)都会在生产稀土镁球墨铸铁时产生。
球墨铸铁常见缺陷有球化不良(球铁处理不成)、球化衰退、缩松、皮下气孔等缺陷。
球化不良是稀土镁球墨铸铁经常遇到的问题之一。
球化不良是指球化剂加入量不足以使铸铁石墨充分球化。
铸件中的石墨多呈团块状、开花状、枝晶状、蠕虫状、厚片状。
球化不良其宏观观特征为⑵:银白色的断口上分布有黑色斑点,破断铸件在其整个断面上分布有明显可见的小黑点,愈往中心愈密。
球化不良的程度越严重,黑斑直径越大数量越多,甚至全部断口为黑灰色,类似灰铸铁的断口。
金相微观分析能发现有集中分布的厚片状石墨或晶间石墨以及少量球状、团状石墨,严重时还出现片状石墨。
球化不良使力学性能急剧下降,不能达到牌号所规定的性能指标。
球化不良主要是因为镁和稀土元素的残留量不足造成的。
产生的原因主要有:(1)使用高硫的焦炭和新生铁,根据我厂生产的经验,当原铁水含硫量达0.1%以上时,经常造成球化不良;(2)与灰铸铁交界铁水没有分离干净,由于炉料计算误差,灰铸铁铁水过多,交界铁水没有分离干净。
结果高硫、低碳的灰铸铁铁水混入球墨铸铁中,而造成球化不良。
生产中经常遇到与灰铸铁交界的第一包球墨铸铁球化不良;(3)铁水氧化,最后一包球墨铸铁是打炉铁水,操作不当往往造成铁水氧化,镁石强烈脱氧剂,结果一部分镁耗费在脱氧上,起球化作用的镁量不足而造成球化不良。
(4)使用镁烧损严重的稀土镁合金;(5)铁水温度过高或过低,铁水温度过高,中间合金与铁水作用激烈,镁烧损严重;铁水温度过低,中间合金容易“结死”在包底不起作用,(6)前炉储存铁水不足,球化处理时将炉渣也出到铁水包中。
由于稀土镁中间合金与铁水作用,产生强烈的翻滚,使炉渣卷入铁水与球化剂作用。
因为渣中硫高,氧化物多,就消耗了部分镁和稀土,这也造成球化不良的原因之一。
针对上述原因,根据导致残留量不足,应采取不同的措施来防止球化不良的产生:(1)如果球化剂中球化元素含量不足,加入量不够,则应根据生产条件,选用合适的球化剂和确定加入量,要严格掌握铁水量,防止失控造成出铁量过大失球化剂量相对减少;(2)处理前铁水温度过高或过低;过高球化剂作用激烈,球化元素烧损严重;过低,则球化剂易在包底冻结。
应根据出铁温度掌握好球化剂和覆盖物的紧实程度,球化剂放在包中装的太松,反应过于激烈,如出铁温度过低,则应及时捅开包底的“结壳”,使球化剂顺利反应;(3)严格控制铁水的含硫量和含氧量。
选用低硫焦炭和生铁。
掌握好合理的供风制度,防止铁水过度氧化,在和其他牌号的铁水同炉熔化时,要注意分离交界铁水,防止混入高硫铁水;(4)出铁时要防止酸性炉渣流入铁水包,特别是当采取炉外去硫操作时,要及时扒渣,以免“回硫”,消耗过多的球化元素,造成球化失败。
(5)生铁中有时会含有一些妨碍球化的元素,数量虽不多,危害却很大,因此球化处理不顺利时,可更换一下生铁。
讨论分析结论:针对我国目前球墨铸铁在钢铁行业中的重要地位,以及其将来的发展和壮大,我们必须加大对球墨铸铁的研究和应用,以便为我们的经济发展打下良好的基础。
同时减少球墨铸铁铸件的缺陷是首要问题,球化不良是其中的一项重要问题,对以上的讨论和分析,我们在生产中要注意球化剂的使用和球化剂在球化过程中必须注意的问题。
孕育剂改善球墨铸铁的石墨化通常球铁生产中氧与硫成核的可能性取决于铁水的纯度和添加物,其保持时间和温度以及铁水的处理方法和添加物。
此前使用的孕育剂是添加了Ca、Ba、Sn、Zn等金属的硅铁。
添加这些元素的目的是使之与铸铁中氧和硫相结合以生成石墨核。
但是与处理生成的有效的核数相比,铁水中的氧化硫数量相对较少,因此,用金属孕育剂的方法受到了限制。
为使其增加有效性而使用了加入Ce、Ca、S、O等元素的新的孕育剂(详见下表)Si Ca Ce Al S O规定成份 70-75 0.75-1.25 1.5-2 0.75-1.25 <1 <1有代表性加成份 73 1 1.75 1 Tnace tnace用这种孕育剂不产生白口,为使阻碍球状化的有害元素无害化可调整Ca、Ce的量。
另外,此孕育剂中含有少量的S、O在其溶入铁水过程中与Ce、Ca反应。
此项孕育剂首要目的是:在铁水中引入金属元素同时也引入S、O等非金属元素。
S可使石墨有效的生成,O在孕育过程起着非常重要作用。
Ca在孕育时是第一反应元素同时在共晶时对石墨的核生成起着重要作用。
Ce对S和O亲和力非常强,可以缓和其害处,Ce的化合物也起核生成的作用。
由于增加这些元素使核数比通常的要增加,有助于石墨化,冷铁的减少白口并减少收缩。
结果可制成有较高韧性和冲击性能的铁素体系铸铁。
特别是这种孕育剂对低S铁水,使用精包处理的铁水和用喂係法的铁水都有效果。
这种新的孕育剂在二次孕育前的铁水和Mg处理后的铁水,经过长时间保持后,也同样可以陆续生成核。
制成铁素体、基体球铁时,强的生核作用和增加石墨数是必要条件。
石墨数增加及其均一分布,有助于珠光体助长元素的偏析和缩孔的减少,和铁素体的生成。
使用这种孕育剂而得到改善的事例。
例1.用加有Zn、Mn、Ca的孕育剂进行随流孕育,在薄壁铸件中苦于碳化物的生成和缩孔,改成这种孕育剂后,没有白口,壁厚部位也无有缩孔。
石墨粒数在壁厚2-3mm部位,原来为3N一粒/mm2,改变了孕剂后达到602粒,孕育剂的用量也减少25%。
例2.用加有Sn的孕育剂,在壁厚5mm处石墨粒数只有312,而用这种孕育剂后在壁厚40mm 处也可增加到340,并因此而减少了缩孔缺陷,同时减少了孕育剂的用量。
例3.壁厚的铸件中由于石墨漂浮、偏析、缩孔、低球化率而受到困扰,原来用含Ba孕育剂,石墨数只有187个,后用这种孕育剂增加到357。
而且缩孔减少,球化率提高10%,抗拉强度和冲击值提高了,加工时刀具的寿命也提高了50%。
含硫、氧的球墨铸铁孕育剂常规的球墨铸铁生产中,铁中能否有硫化物和氧化物作为石墨结晶的核心,取决于原铁水的纯度和添加剂、保持时间和温度以及冶金处理工艺和添加剂。
生产中通用的孕育剂是硅铁,其中还含有钙、钡、锶、锰和锆等金属元素。
加入上述有反应能力的元素,目的是使其与铁中的硫和氧结合,为石墨提供有效的非均质结晶核心。
但是,铁水中能起作用的硫和氧是有限的,孕育剂中的添加元素的作用,因而也是有限的。
处理后可能形成的有效晶核的数量将制约孕育的效果。
为了增强孕育效果,推出了一种新型孕育剂,其中含有铈(Ce)、钙(Ca)、硫(S)和氧(O),见表I。
已经证实,采用这种孕育剂,能使球墨铸铁的显微组织,更为均匀,缩孔倾向较小,从而有较好的加工性能。
表1 新型孕育剂的化学成分(%)Si Ca Ce Al S O规格要求 70-76 0.75-1.25 1.5-2.0 0.75-1.25 ≤1.0≤1.0典型实例 73 1 1.75 1 微量微量1.Ca- Ce -S –O的配合作用孕育剂中的Ca和Ce,其含量已经调定到能使铸铁的白口倾向最小,并能中和阻碍形成球状石墨的微量元素的作用。
孕育剂中含有少量的S和O,加入铁水后,可以和Ca和Ce反应。
新型孕育剂的主要作用是:在加入金属元素的同时,引进一定浓度的非金属元素(S和O)。
孕育剂中反应能力强的Ca和Ce与硫、氧作用后,就会产生较多的石墨晶核。
硫有利于形成石墨晶核,氧则对孕育过程有重要的作用。
通过瞬时孕育处理,石墨生核过程中,将同时受益于钙、铈、硫、氧的协同作用。
孕育处理时,钙是首要反应元素,对共晶石墨生核有决定性的作用。
均衡含量的铈,可以中和有害元素的作用,产生稳定的金属间化合物,且对硫和氧有强亲和力,从而生成高度稳定的氧化物、硫化物和硫氧化物。
在整个凝固区间内,此类含铈的化合物都有助于改善生核条件,有益于孕育处理过程。
在球化剂、孕育剂和原铁水之间反应并产生晶核的同时,上述晶核也一并起作用。
孕育剂成分的拟定,是要使球墨铸铁在减轻白口倾向和缩孔倾向的同时,还能强化石墨的生核条件。
这种孕育的理念是新的,体现在加入硅铁的同时还加入非金属粉末,以使其有特殊的性能。
制造对韧性和冲击性能要求较高的铁素体球墨铸铁时,适于采用此种新型孕育剂。
对于含硫量低的球墨铸铁,在转包中用镁处理的球墨铸铁或用喂线法处理的球墨铸铁,这种孕育剂特别有效。
2.石墨球数增多用含钙、铈、硫、氧的新型孕育剂,能使球墨铸铁中的石墨球数增多,并可改善各种性能,如:◆因避免了形成硬质碳化物,加工性能改善;◆促进石墨和铁素体形成;◆减轻合金元素和微量元素的偏析;◆减少凝固过程中的收缩;◆提高韧性;◆形成复杂的铸件,不同部位的组织和性能比较均一。
大家都知道,瞬时孕育前保持了较长时间的原铁水或加镁处理过的铁水,其生核能力会大为减弱。
此种情况下,采用新型孕育剂能有效地提供新的晶核。
生产铸态铁素体球墨铸铁件时,强生核作用和石墨球数增多是使铁素体含量最多的前提条件。
采用新型孕育剂,可使石墨球的尺寸有大、小二种,呈双峰分布,这有助于减少收缩,并可在富含珠光体促进元素的偏析区沉积碳,以产生较多的铁素体。