大众汽车标准_TL 533 硬聚乙烯 材料要求
大众标准TL精编中文版
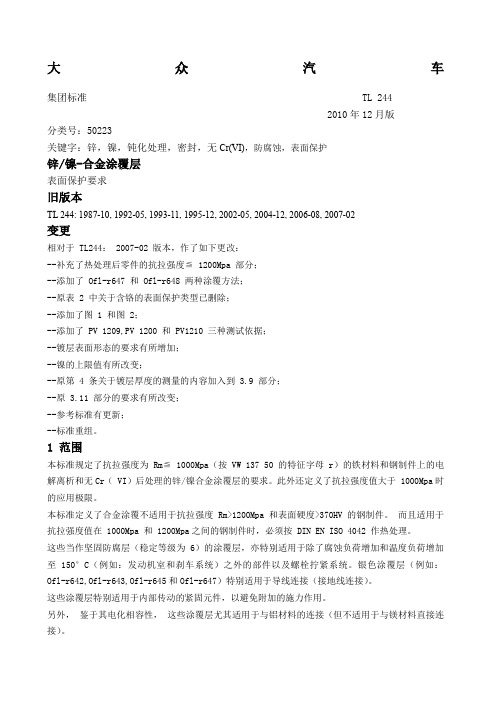
大众汽车集团标准 TL 2442010年12月版分类号:50223关键字:锌,镍,钝化处理,密封,无Cr(VI),防腐蚀,表面保护锌/镍-合金涂覆层表面保护要求旧版本TL 244: 1987-10, 1992-05, 1993-11, 1995-12, 2002-05, 2004-12, 2006-08, 2007-02变更相对于 TL244: 2007-02 版本,作了如下更改:--补充了热处理后零件的抗拉强度≦ 1200Mpa 部分;--添加了 Ofl-r647 和 Ofl-r648 两种涂覆方法;--原表 2 中关于含铬的表面保护类型已删除;--添加了图 1 和图 2;--添加了 PV 1209,PV 1200 和 PV1210 三种测试依据;--镀层表面形态的要求有所增加;--镍的上限值有所改变;--原第 4 条关于镀层厚度的测量的内容加入到 3.9 部分;--原 3.11 部分的要求有所改变;--参考标准有更新;--标准重组。
1 范围本标准规定了抗拉强度为 Rm≦ 1000Mpa(按 VW 137 50 的特征字母 r)的铁材料和钢制件上的电解离析和无Cr( VI)后处理的锌/镍合金涂覆层的要求。
此外还定义了抗拉强度值大于 1000Mpa时的应用极限。
本标准定义了合金涂覆不适用于抗拉强度 Rm>1200Mpa 和表面硬度>370HV 的钢制件。
而且适用于抗拉强度值在 1000Mpa 和 1200Mpa之间的钢制件时,必须按 DIN EN ISO 4042 作热处理。
这些当作坚固防腐层(稳定等级为 6)的涂覆层,亦特别适用于除了腐蚀负荷增加和温度负荷增加至150°C(例如:发动机室和刹车系统)之外的部件以及螺栓拧紧系统。
银色涂覆层(例如:Ofl-r642,Ofl-r643,Ofl-r645和Ofl-r647)特别适用于导线连接(接地线连接)。
这些涂覆层特别适用于内部传动的紧固元件,以避免附加的施力作用。
TL52476最新大众POM材料标准
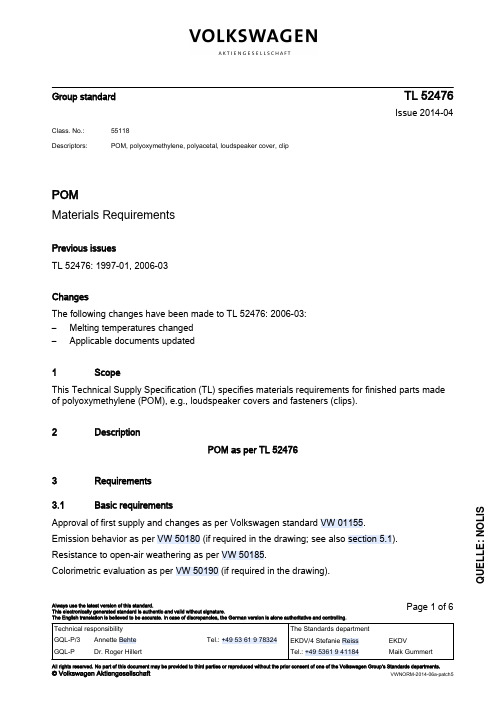
Group standardTL 52476Issue 2014-04Class. No.:55118Descriptors:POM, polyoxymethylene, polyacetal, loudspeaker cover, clipPOMMaterials RequirementsPrevious issuesTL 52476: 1997-01, 2006-03ChangesThe following changes have been made to TL 52476: 2006-03:–Melting temperatures changed –Applicable documents updated ScopeThis Technical Supply Specification (TL) specifies materials requirements for finished parts made of polyoxymethylene (POM), e.g., loudspeaker covers and fasteners (clips).DescriptionPOM as per TL 52476RequirementsBasic requirementsApproval of first supply and changes as per Volkswagen standard VW 01155.Emission behavior as per VW 50180 (if required in the drawing; see also section 5.1).Resistance to open-air weathering as per VW 50185.Colorimetric evaluation as per VW 50190 (if required in the drawing).123 3.1Always use the latest version of this standard.This electronically generated standard is authentic and valid without signature.The English translation is believed to be accurate. In case of discrepancies, the German version is alone authoritative and controlling.Page 1 of 6All rights reserved. No part of this document may be provided to third parties or reproduced without the prior consent of one of the Volkswagen Group’s Standards departments.© Volkswagen AktiengesellschaftVWNORM-2014-06a-patch5Q U E L L E : N O L I SPage 2TL 52476: 2014-04Avoidance of hazardous substances as per VW 91101.10 finished parts are required for complete testing; for fasteners (like clips), 20 finished parts are required.PropertiesThe surface and interior of the finished parts must be free of flaws and processing defects such as flow lines, cracks, air traps, or similar defects. Sink marks at the base of ribs and reinforcements are only permissible if they do not adversely affect the function, appearance, and/or assembly of the parts. The finished parts must allow for trouble-free installation.PackagingFinished parts must be packed in a way that allows air circulation. For delivery in large packaging units (cardboard boxes, pallets), the finished parts must be stacked or arranged so that air circula‐tion is possible.Marking as per VDA 260> POM <ConditioningPrior to testing, the specimens must be conditioned in the ISO 554-23/50 standard climate for at least 24 h.Evaluation of the measurement resultsThe required numerical values apply to each individual measurement.MaterialSee section 5.2.Polyoxymethylene (POM) homopolymer or, alternatively, copolymer.ColorAs per drawing and/or release.PropertySee table 1.3.1.13.1.23.2 3.33.43.53.64Page 3TL 52476: 2014-04 Table 1Page 4TL 52476: 2014-04Notes on testing Emission behaviorIf the test results do not comply with the requirements of VW 50180, the parts must be tempered until the limit values are met. The temperature must be selected such that no changes in shape,color, and to the surface occur.MaterialThe identity test is performed with infrared spectroscopy.Melting temperatureIf the differential scanning calorimetry (DSC) method is used to determine the melting temperature,the following procedure must be used:Test equipment such as the DSC 821e from Mettler Toledo can be used. A plane-parallel finished part section with a weight of approx. (5 to 10) mg is used as the specimen.Test parameters: Heat the specimen from +50 °C to +200 °C at a heating rate of 10 °C/min. After‐wards, cool it down to +50 °C at a rate of 5 °C/min and then reheat it at a rate of 10 °C/min to +200 °C. Perform the test under normal atmospheric conditions.Yield stress and yield strainTensile test as per DIN EN ISO 527-2, specimen type 5A, test speed: 50 mm/min. If no 5A speci‐men is available, it is permissible to use S3A tensile specimens (dumb-bell specimen) as per DIN 53504.Impact strengthTest equipment: 4 J pendulum impact tester.If for reasons concerning equipment and/or specimen shape and size a test as per table 1, con‐sec. no. 6 cannot be performed, the following procedure can be used as a substitute:Impact resistance test (broadside impact) as per DIN EN ISO 179-1, but with: specimen length of (50 ± 1) mm, width of (6 ± 0.2) mm, thickness matching the thickness of the finished product (up to a max. of 4 mm); distance between supports: 40 mm; test equipment: 4 J pendulum impact tester.Specimens taken from finished parts grained or painted on one side are placed on the supports of the pendulum impact tester so that the grained or painted side faces the direction of impact.Note that this procedure requires prior agreement.Notched impact strengthTest equipment: 4 J pendulum impact tester.If for reasons concerning equipment and/or specimen shape and size a test as per table 1, con‐sec. no. 7 cannot be performed, the following procedure can be used as a substitute:Impact resistance test (broadside impact) as per DIN EN ISO 179-1, but with: specimen length of (50 ± 1) mm, width of (6 ± 0.2) mm, thickness matching the thickness of the finished product (up to a max. of 4 mm); distance between supports: 40 mm; test equipment: 4 J pendulum impact tester.5 5.15.25.35.45.55.6Page 5TL 52476: 2014-04A 0.8 mm-wide U-shaped notch is made on the broad side of the specimens. The notch depth is 1/3 of the specimen thickness. The edges outlining the notch root must have a curvature radius of < 0.1 mm.Finished parts with one-sided graining must be notched on the grained side and subsequentlyplaced on the pendulum impact tester’s specimen supports in such a manner that the center of the notch is precisely within the impact plane. Care must be taken that the notch is located on the side facing away from the hammer edge. Note that this procedure requires prior agreement.Elevated-temperature behaviorHeat aging test as per DIN 53497, method B, on at least one complete finished part; aging temper‐ature of (+90 ± 1) °C; aging duration of (22 + 2) h.Low-temperature behaviorA minimum of 2 complete finished parts are aged in air at (-30 ± 1) °C; aging period (22 + 2) h.Ball drop testBall drop test as per PV 3905, but with: base plate (specimen support surface) made of steel sheet with a thickness ≥10 mm; no depression on at least three finished parts. Ball drop height:(450 ± 5) mm.LightfastnessIf the number of periods of exposure is not defined in the drawing, the following rule applies:– 3 periods of exposure for components in areas with indirect solar radiation– 5 periods of exposure for components in areas with direct solar radiation (e.g., door waist rail).–10 periods of exposure for components in areas with the highest solar radiation (e.g., rearshelf).Applicable documentsThe following documents cited in this standard are necessary to its application.Some of the cited documents are translations from the German original. The translations of Ger‐man terms in such documents may differ from those used in this standard, resulting in terminologi‐cal inconsistency.Standards whose titles are given in German may be available only in German. Editions in other languages may be available from the institution issuing the standard.PV 1303Non-Metallic Materials; Exposure Test of Passenger Compartment Com‐ponentsPV 3905Organic Materials; Ball Drop TestTL 1010Materials for Vehicle Interiors; Burning Behavior; Material Requirements VW 01155Vehicle Parts; Approval of First Supply and ChangesVW 50180Components in the Passenger Compartment; Emission Behavior VW 50185Vehicle Parts; Resistance to Open-Air Weathering5.75.85.95.106Page 6TL 52476: 2014-04VW 50190Interior Trim Components; Metrological Evaluation of Color and GlossLevel; Visual Evaluation of Chrome SurfacesVW 91101Environmental Standard for Vehicles; Vehicle Parts, Materials, Operat‐ing Fluids; Avoidance of Hazardous SubstancesDIN 53497Testing of Plastics; Hot Storage Test on Mouldings Made of Thermo‐plastic Moulding Materials without External Mechanical StressingDIN 53504Testing of rubber - determination of tensile strength at break, tensilestress at yield, elongation at break and stress values in a tensile test DIN EN 20105-A02Textiles - Tests for colour fastness - Part A02: Grey scale for assessingchange in colourDIN EN ISO 1183-1Plastics - Methods for determining the density of non-cellular plastics -Part 1: Immersion method, liquid pyknometer method and titration meth‐odDIN EN ISO 179-1Plastics - Determination of Charpy impact properties - Part 1: Non-instru‐mented impact testDIN EN ISO 306Plastics - Thermoplastic materials - Determination of Vicat softeningtemperature (VST)DIN EN ISO 3146Plastics - Determination of melting behaviour (melting temperature ormelting range) of semi-crystalline polymers by capillary tube and polariz‐ing-microscope methodsDIN EN ISO 527-2Plastics - Determination of tensile properties - Part 2: Test conditions formoulding and extrusion plasticsISO 554Standard atmospheres for conditioning and/or testing; Specifications VDA 260Components of motor vehicles - Marking of material。
VW50123大众最新标准TPE

VW50123⼤众最新标准TPEGroup standardVW 50123Issue 2015-09Class. No.:55154Descriptors:TPE, TPU, TPO, TPS, TPC, TPA, thermoplastic, elastomerThermoplastic Elastomers Quality RequirementsPrevious issuesVW 50123: 2000-10, 2005-04, 2007-10ChangesThe following changes have been made to VW 50123: 2007-10:–Standard completely revised –Applicable documents updated –Standard changed to new layout ScopeThis standard contains quality requirements for materials that are based on thermoplastic elasto‐mers (TPE) and are intended for motor vehicle components. Parts with qualities that cannot be classified on the basis of this standard require separate Technical Supply Specifications (TLs) or notes in the respective drawing.DefinitionsThermoplastic elastomers (TPE)Thermoplastic elastomers are elastomers that have a flow transition at temperatures greater than the application range.These elastomers are multi-phase materials that contain hard and soft segments as blocks in the main chain or hard segments grafted as side chains on flexible base chains. The soft segments form the movable areas necessary for the rubber elasticity. The cross-linked areas of these12 2.1Always use the latest version of this standard.This electronically generated standard is authentic and valid without signature.The English translation is believed to be accurate. In case of discrepancies, the German version is alone authoritative and controlling.Page 1 of 11All rights reserved. No part of this document may be provided to third parties or reproduced without the prior consent of one of the Volkswagen Group’s Standards departments.Volkswagen AktiengesellschaftVWNORM-2014-06a-patch5Q U E L L E : N O L I SPage 2VW 50123: 2015-09materials are relatively easy to split by means of heat and thus limit the characteristic rubber-elas‐tic application at higher temperatures. The thermoreversible cross-linking of TPEs allows for ther‐moplastic-like processing.Type groupsTypes with low hardnessHardness range ≤ 65 Shore A and hardness range > 65 Shore A.Material designations (as per DIN EN ISO 18064); Designation examples:–Urethane thermoplastic elastomer (TPU)> TPU-ARES <(aromatic hard segments/ester soft segments)> TPU-ARET <(aromatic hard segments/ether soft segments)–Ethylene propylene diene rubber(EPDM)/polypropylene (PP) thermo‐plastic elastomer (olefinic thermoplas‐tic elastomer (TPO) or thermoplasticvulcanizate (TPV))> TPO-(EPDM+PP) TPV-(EPDM+PP) <In the case of cross-linked elastomer phases –Styrenic thermoplastic elastomer(TPS)> TPS-SBS <> TPS-SEBS <Types with high hardnessHardness range of 40 to 50 Shore D.Material designations:–Copolyester thermoplastic elastomer(TPC)> TPC-EE <–Polyamide thermoplastic elastomer(TPA)> TPA-ES <DesignationRefer to DIN EN ISO 18064 for the designations of thermoplastic elastomers.Designation example for a black-dyed, lightfast TPO with a preferred hardness of 60 Shore A and a density of 1.04 g/cm 3: TPO-(EPDM+PP) as per Volkswagen standard VW 50123 – 60 Shore A, black, 1.04 g/cm 3, light‐fast Requirements Basic requirementsApproval of first supply and changes as per Volkswagen standard VW 01155Avoidance of hazardous substances as per VW 91101.2.2 2.2.12.2.234 4.1Page 3VW 50123: 2015-09In terms of the raw materials on which they are based, the materials used in components that are made of thermoplastic elastomers and that are subject to dynamic loads during driving operation must be free of recycled material. Within this context, "recycled material" refers to products from a recycling process (thermal, mechanical, and/or chemical) used to recycle material from used com‐ponents.For components subject to dynamic loads, using regrind (from the material fed directly into the components' own manufacturing process) is permissible up to a limit of 20%, provided that the re‐quired material level for the component is consistently reached so that the use of regrind does not have a significant impact on the required material properties.TPE qualities are preferably tested on components, component sections or, in exceptional cases,test plates.Samples must always be delivered with the manufacturer’s quality designation.The number of parts required for laboratory tests must be agreed upon with the appropriate Materi‐als Laboratory in each case.When manufacturing plate material, anisotropic effects (= orientation of macromolecules during production) can be expected as a result of the molding material injection process (gate marks).This will lead to differences in the mechanical characteristic values of strength and elongation de‐pending on the direction of the orientations. This must be taken into account during testing. To this end, appropriate specimens must be taken from the plate material both in the longitudinal and transverse directions and torn apart. Generally, the specimens taken transversely to the direction of orientation of the macromolecules will have lower strength and elongation values.The specimens to be used for laboratory tests as per this standard must be taken transversely to the orientation of the macromolecules.Evaluation of the measurement resultsThe required numerical values apply to each individual measurement.Color in as-received conditionAs per drawing.AppearanceNo visible flaws, inclusions, etc.Material identificationInfrared spectroscopy, pyrolysis gas chromatography mass spectrometry (Py-GC-MS)couplingPy-GC-MS as per Test Specification PV 3935.ThermogravimetrySee section 6.1.Volatile, polymer, and nonvolatile percentages must be specified.4.24.34.44.5 4.5.14.5.2Page 4VW 50123: 2015-09Differential scanning calorimetry (DSC)See section 6.2.The following must be specified: Enthalpy of fusion, melting range (T m reflects the start of melting,not the peak maximum), 1st heat-up curve, 1st crystallization curve, 2nd heat-up curve, and 2nd crystallization curve.Dimensional stability under heat as per DIN EN ISO 306, method BOnly if required in the drawing; as per the released sample.Density as per DIN EN ISO 1183-1Specified as per drawing.Hardness Shore AHardness range of 55 Shore A to 80 Shore A for TPE that are primarily exposed to daylight and weather effects (e.g., TPO, TPV).Shore DHardness range of 40 Shore D to 50 Shore D for TPE that may also come into contact with operat‐ing fluids such as oils, greases, fuels, blowby gases (limited resistance) (e.g., TPC).Low-temperature elasticity after 22 h at -40 °C GeneralrequirementsNo cracks or fractures under manual bending stress.Freeze temperature T GAs per drawing.Ozone resistance as per VW 2.8.1, installed in a manner similar to that used during op‐erationFree of cracks.Flammability as per TL 1010As per drawing.Lightfastness as per VW 2.8.1No changes compared to the as-received condition, e.g., discoloration, embrittlement, decomposi‐tion, cracks. Only required if "lightfast" is additionally specified in the drawing.4.5.3 4.5.44.5.54.6 4.6.14.6.24.7 4.7.14.7.24.84.94.10Page 5VW 50123: 2015-09Emission behavior as per VW 50180.As per drawing.PropertiesFor the Shore A hardness range, see table 1. For the Shore D hardness range, see table 2.In justified cases, deviating limits may be specified in agreement with the appropriate Volkswagen Group Materials Engineering department.Table 1 – Shore A hardness range4.11 5Page 6VW 50123: 2015-09Table 2 – Shore D hardness rangePage 7 VW 50123: 2015-09Page 8VW 50123: 2015-09Notes on testing ThermogravimetryThermogravimetric analysis as per PV 3927.Components as percentages and/or pyrolysis gas chromatography mass spectrometry as an iden‐tification check.Differential scanning calorimetry (DSC)A device such as the PerkinElmer DSC7 analyzer can be used for testing.The specimen is a plane-parallel finished part section with an approx. mass of 10 mg. The speci‐men is heated up from 50°C to 310 °C at 10 °C/min. Afterward, the specimen is cooled down to 150 °C at 5 °C/min and then heated up again to 310°C at 10 °C/min. The test is performed under normal atmospheric conditions. In order to evaluate the enthalpy of fusion of the polymer, the resi‐due determined with the thermogravimetric analysis must be subtracted from the actual original specimen weight.Heat agingAging in a forced-air oven as per DIN 53508. The aging durations and temperatures must be agreed upon. Measurements are taken after cooling down to room temperature (23 ±2) °C.6 6.16.26.3Page 9VW 50123: 2015-09Aging in operating fluids GasolineThe specimens are aged in FAM test fluid as per DIN 51604-2 (FAM 2).Composition:–84.5 volume percent FAM test fluid as per DIN 51604-1 (FAM 1)–15.0 volume percent methanol –0.5 volume percent waterOther test fluids may be used if required (deviations as per drawing).168-h aging (other aging durations as per drawing specification) at a room temperature of(23 ±2) °C; the specimens must be blotted with filter paper (black band) after aging; they are evalu‐ated 1 minute after this (in justified cases, which require agreement, the evaluation may also begin 15 minutes after removal).Diesel fuel, fatty acid methyl ester (FAME)168-h aging at room temperature (23 ±2) °C. In justified cases, other aging durations and test tem‐peratures can be agreed upon.The following test composition must be used for aging in diesel fuel:–80 volume percent Liquid F standard diesel (formerly A20 NPII made by Haltermann) as perDIN ISO 1817–20 volume percent fatty acid methyl ester (FAME) as per DIN EN 14214. Soy methyl estermust be used as the fatty acid methyl ester component.In justified cases, the use of the following test mixture is also permissible for aging in diesel fuel:–93 volume percent Liquid F standard diesel (formerly A20 NPII made by Haltermann) as perDIN ISO 1817–7 volume percent fatty acid methyl ester (FAME) as per DIN EN 14214 with rapeseed oil meth‐yl ester as the fatty acid methyl ester component Aging at an elevated temperature is performed using a reflux condenser.After the aging time ends, the specimens must be cleaned with a lint-free cloth. Specimens that have been aged at an elevated temperature can be left in the test fluid to cool down to the ambient temperature. The evaluations are carried out 1 min after the specimens are removed from the me‐dium.Engine oil, transmission fluid, and grease96-h aging duration. In justified cases, other aging times and test temperatures can be agreed upon.CoolantS 3A dumb-bell specimens as per DIN 53504 are aged in test fluid consisting of 50 parts by vol‐ume of deionized water, and50 parts by volume of coolant additive as per TL 774 at 135 °C in an autoclave. The fluid volume must be 150 to 180 times the specimen volume. After this, the speci‐mens are cooled down to (23 ±2) °C in the test fluid within 2 h and measured. Aging duration: 94 h. In justified cases, other aging durations may also be agreed upon.6.4 6.4.16.4.26.4.36.4.4Page 10VW 50123: 2015-09Brake fluidThe test specimens are aged in 75 ml of brake fluid for 70 h at 120 °C. Glass containers with an approx. volume of 250 ml and a diameter of 50 mm must be used – and tightly sealed – for this purpose. After the test is over, the elastomer parts are acclimatized in the container at (23 ±2) °C for 60 min to 90 min. The specimens are then removed from the fluid; rinsed briefly (max. 10 s) in isopropanol; and dried with a clean, fiber-free cloth. The measurements must be performed within 60 min of the specimens being rinsed in alcohol.Applicable documentsThe following documents cited in this standard are necessary to its application.Some of the cited documents are translations from the German original. The translations of Ger‐man terms in such documents may differ from those used in this standard, resulting in terminologi‐cal inconsistency.Standards whose titles are given in German may be available only in German. Editions in other languages may be available from the institution issuing the standard.PV 3307Elastomer Components; Plastic and Elastic DeformabilityPV 3927Thermogravimetric Analysis for Plastics and Elastomers; Determination:Plasticizers, Carbon BlackPV 3935Plastics and Elastomers; Pyrolytic Gas Chromatography/Mass Spec‐trometryPV 3936Polymer Materials; Testing the Resistance to Components of Blowby GasesTL 1010Materials for Vehicle Interiors; Burning Behavior; Material Requirements TL 52185Reference Engine Oil SAE 5W-30 for Testing of Compatibility with Re‐spect to Elastomer Materials; Lubricant RequirementsTL 726Transmission Oil APl GL 4 SAE 75W / SAE 80W; Lubricant Require‐mentsTL 735Multi-Purpose Grease; Lubricant RequirementsTL 745Multi-Purpose Low-Temperature Grease; Lubricant Requirements TL 766Brake Fluid; Material RequirementsTL 774Ethylene Glycol-Based Coolant Additive; Materials Requirements VW 01155Vehicle Parts; Approval of First Supply and Changes VW 2.8.1Elastomers; Materials Requirements and Testing VW 50180Components in the Vehicle Interior; Emission BehaviorVW 91101Environmental Standard for Vehicles; Vehicle Parts, Materials, Operat‐ing Fluids; Avoidance of Hazardous SubstancesDIN 51604-1FAM testing fluid for polymer materials; Composition and requirements DIN 51604-2Methanolic FAM testing fluid for polymer materials; composition and re‐quirements6.4.5 7Page 11VW 50123: 2015-09 DIN 53504Testing of rubber - determination of tensile strength at break, tensilestress at yield, elongation at break and stress values in a tensile test DIN 53508Testing of rubber - Accelerated ageingDIN 53512Testing of rubber - Determination of rebound resilience (Schob pendu‐lum)DIN EN 14214Liquid petroleum products - Fatty acid methyl esters (FAME) for use in diesel engines and heating applications - Requirements and test meth‐odsDIN EN ISO 1183-1Plastics - Methods for determining the density of non-cellular plastics -Part 1: Immersion method, liquid pyknometer method and titration meth‐odDIN EN ISO 179-1Plastics - Determination of Charpy impact properties - Part 1: Non-instru‐mented impact testDIN EN ISO 18064Thermoplastic elastomers - Nomenclature and abbreviated termsDIN EN ISO 306Plastics - Thermoplastic materials - Determination of Vicat softening temperature (VST)DIN ISO 1817Rubber, vulcanized - Determination of the effect of liquidsDIN ISO 34-1Rubber, vulcanized or thermoplastic - Determination of tear strength -Part 1: Trouser, angle and crescent test piecesDIN ISO 7619-1Rubber, vulcanized or thermoplastic - Determination of indentation hard‐ness - Part 1: Durometer method (Shore hardness)。
大众汽车标准_TL 52476_2006 英文-POM材料要求
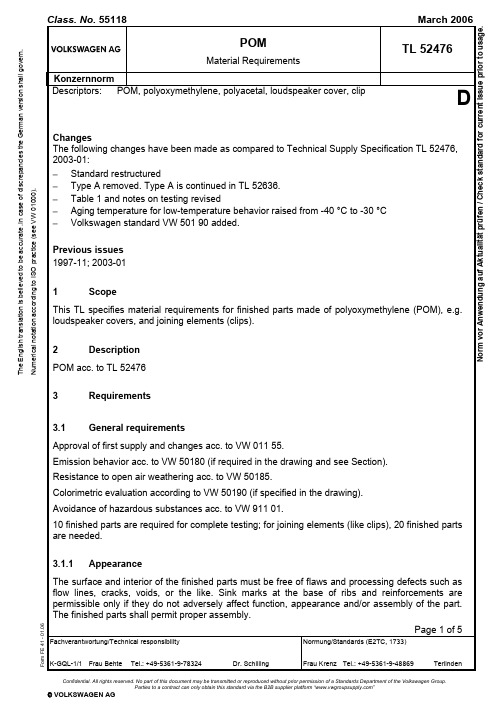
Confidential. All rights reserved. No part of this document may be transmitted or reproduced without prior permission of a Standards Department of the Volkswagen Group.Parties to a contract can only obtain this standard via the B2B supplier platform “”VOLKSWAGEN AGPage 2TL 524 76: 2006-03D3.1.2 PackagingFinished part packaging shall not be air tight to allow air circulation. In case of delivery in large packaging units (cardboard boxes, pallets), they should be stacked or arranged so that air circulation is possible.3.2 Marking according to VDA 260>POM<3.3 ConditioningPrior to testing, the specimens required for the individual tests must be conditioned for at least 48 h in the DIN 50014 – 23/50-2 standard climate.3.4 Evaluation of the measuring resultsThe required numerical values apply to each individual measurement.3.5 MaterialSee Section 5.2.Polyoxymethylene (POM) homopolymer, or copolymer alternatively.3.6 ColorAccording to drawing and/or release.4 PropertiesSee Table 1.Table 1No. Property Requirement1 Density acc. to DIN EN ISO 1183-1, buoyancy(1,42 ± 0,02) g/cm3method2 Melting temperature acc. to DIN EN ISO 3146,+166 °C to +179 °Calternatively with DSCsee Section 5.33 Dimensional stability under heat acc. to Vicat and≥ 145 °CDIN EN ISO 306, method B50≥ 60 MPa4 Yield stress acc. to DIN EN ISO 527-2see Section 5.45 Elongation acc. to DIN EN ISO 527-2≥ 6,5%see Section 5.46 Impact resistance acc. to DIN EN ISO 179-1/1eUNo fracture (kJ/m2)see Section 5.57 Notched impact strength acc. to DIN EN ISO 179-≥ 4,5 kJ/m21/1eA.see Section 5.6Page 3TL 524 76: 2006-035 Notes on testingbehavior5.1 EmissionIf the test results do not comply with the requirements of VW 50180, the parts shall be tempered until the limit values are met. The temperature shall be selected such that no changes in form, color, and surface occur.5.2 MaterialThe identity test is performed using infrared spectroscopy.temperature5.3 MeltingIf the DSC method is chosen to identify the melting temperature, the following procedure shall be applied:Test equipment such as the DSC 821e from Mettler Toledo can be used. A plane parallel finished part section of a weight of approx. 5 mg to 10 mg serves as specimen.Testing parameters: The specimen is heated from +50 °C to +200 °C at a heating rate of 10 °C/min. Afterwards, it is cooled with 5° C/min to +50° C and reheated with 10° C/min to +200° C. The test is carried out in normal atmosphere.Page 4TL 524 76: 2006-03D5.4 Yield stress and elongationTensile test according to DIN EN ISO 527-2, 5A specimen, test rate 50 mm/min. In case the 5A specimen cannot be prepared, it is permissible to use S3A tensile specimens (standard test specimens) acc. to DIN 53504.strength5.5 ImpactTest equipment: pendulum impact tester 4J.If for reasons concerning equipment and/or specimen shape and size a test according to Table 1 No. 6 cannot be performed, the following procedure may be substituted:Impact resistance test (broadside impact) according to DIN EN ISO 179-1; deviating specimen length: (50 ± 1) mm, width: (6 ± 0,2) mm, thickness according to product thickness (up to max.4 mm); mounting flange interval (support separation): 40 mm, test equipment: pendulum impact tester 4J.Specimens taken from finished parts grained or painted on one side are placed on the mounting flange of the pendulum impact tester so that the grained or painted side faces the direction of impact.Note that this procedure requires prior agreement.5.6 Notched impact strengthTest equipment: pendulum impact tester 4J.If for reasons concerning equipment and/or specimen shape and size a test according to Table 1 No. 7 cannot be performed, the following procedure may be substituted:Impact resistance test (broadside impact) according to DIN EN ISO 179-1; deviating specimen length: (50 ± 1) mm, width: (6 ± 0,2) mm, thickness according to product thickness (up to max. 4 mm); mounting flange interval (support separation): 40 mm, test equipment: pendulum impact tester 4J.The specimens are given a 0.8 mm wide U-shaped notch on the broad side. The notch depth shall be 1/3 the specimen thickness. The edges adjoining the base of the notch shall have a curvature radius of < 0,1 mm.Finished parts with one-sided graining shall be notched on the grained side and subsequently placed on the pendulum impact tester’s mounting flanges in such a manner that the center of the notch is precisely within the impact plane. Care shall be taken that the notch is located on the side away from the direction of impact. Note that this procedure requires prior agreement.behavior5.7 Elevated-temperatureAging test at elevated temperature according to DIN 53497, method B, on at least one complete finished part; aging temperature (+90 ± 1) °C; aging period (22 + 2) h.behavior5.8 Low-temperatureA minimum of two complete finished parts are aged in air at (-30 ± 1) °C; aging period (22 + 2) h.5.9 Ball drop testBall drop test acc. to PV 3905, however, base plate (specimen support) made from 10 mm thick sheet steel without recess on at least three finished parts. Ball drop height (450 ± 5) mm.Page 5TL 524 76: 2006-03D 5.10 LightfastnessIf the number of exposure periods is not defined in the drawing, the following rule applies:─ 3 periods of exposure for components in areas with indirect sun radiation.─ 5 periods of exposure for components in areas with direct sun radiation (e.g. door upper trim).─10 periods of exposure for components in areas subject to the highest sun radiation (e.g. rear shelf).standards16 ReferencedTL 1010 Materials for Vehicle Interiors; Flammability, Material RequirementsPV 1303 Non-Metallic Materials;Exposure Test of Passenger Compartment ComponentsPV 3905 Organic Materials; Ball Drop TestVW 01155 Vehicle Supply Parts; Approval of First Supply and ChangesVW 50180 Components in Passenger Compartment; Emission BehaviorVW 50185 Vehicle Components; Resistance to Open Air WeatheringVW 50190 Components of the Vehicle Interior Trim; Colorimetric EvaluationVW 91101 Environmental Standard for Vehicles; Vehicle Parts, Materials, Operating Fluids; Avoidance of Hazardous SubstancesDIN 50014 Climates and Their Technical Application; Standard AtmospheresDIN 53497 Testing of Plastics; Hot Storage Test on Mouldings Made of Thermoplastic Moulding Materials without External Mechanical StressingDIN 53504 Testing of Rubber; Determination of Tensile Strength at Break, Tensile Stress at Yield, Elongation at Break and Stress Values in a Tensile TestDIN EN ISO 179-1 Plastics; Determination of Charpy Impact Properties, Part 1: Non-Instrumented Impact TestDIN EN ISO 306 Plastics – Thermoplastic Materials – Determination of Vicat Softening Temperature (VST)DIN EN ISO 527-2 Plastics - Determination of Tensile Properties – Part 2: Test Conditions for Moulding and Extrusion PlasticsDIN EN ISO 1183-1 Plastics – Methods for Determining the Density of Non-Cellular Plastics – Part 1: Immersion Method, Liquid Pyknometer Method and Titration Method DIN EN ISO 3146 Plastics, Determination of Melting Behaviour (Melting Temperature or Melting Range) of Semi-Crystalline Polymers by Capillary Tube andPolarizing-Microscope MethodsDIN EN 20105-A02 Textiles – Tests for Colour Fastness – Part A02: Grey Scale for Assessing Change in ColourVDA 260 Motor Vehicle Components; Marking of Materials1 In this section terminological inconsistencies may occur as the original titles are used.。
大众汽车关于PA66材料成品件的质量要求 VW50133
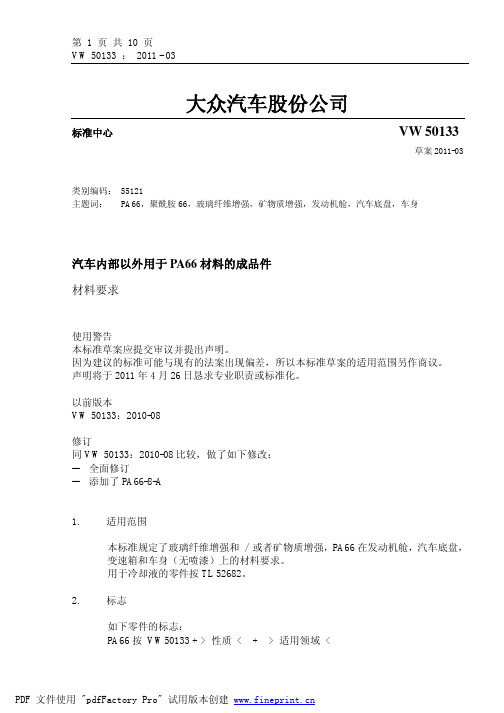
大众汽车股份公司标准中心VW 50133草案2011-03类别编码:55121主题词:PA66,聚酰胺66,玻璃纤维增强,矿物质增强,发动机舱,汽车底盘,车身汽车内部以外用于PA66材料的成品件材料要求使用警告本标准草案应提交审议并提出声明。
因为建议的标准可能与现有的法案出现偏差,所以本标准草案的适用范围另作商议。
声明将于2011年4月26日恳求专业职责或标准化。
以前版本VW 50133:2010-08修订同VW 50133:2010-08比较,做了如下修改:-- 全面修订-- 添加了PA66-8-A1.适用范围本标准规定了玻璃纤维增强和/ 或者矿物质增强,PA66在发动机舱,汽车底盘,变速箱和车身(无喷漆)上的材料要求。
用于冷却液的零件按TL 52682。
2.标志如下零件的标志:PA66按VW50133 + > 性质< + > 适用领域<如果表2至表6没有给出适用领域,只需陈述其性能例如:一个进气歧管插入件的材料是聚酰胺66,含30%的玻璃纤维:PA66按VW50133 - PA66-6-A –进气歧管3要求3.1 基本要求首次供货和更改的批准按VW 01155。
避免有害物质按VW 91101。
在从成品件上取得的样件上做试验。
为了全面彻底的检查,需要5个成品件。
如果不能在零件上面做试验,可以再数据页或者说在测试台上做试验。
3.2特性这些成品件的表面以及和功能相关的区域不得有诸如缩孔,裂纹,汇流接缝的缺陷和制造缺陷。
如果在与功能相关的区域上有缩孔或其它制造缺陷,那么供货商得有在所有负载条件下尺寸安全性的证明。
限定范围的样品与专业部门协调。
成品件必须可实现完美无缺的装配。
不允许功能性危险或安装人员被毛刺划伤的危险。
3.3制造注塑成型法3.4预处理干燥状态(预处理之前)和预处理后状态的区别。
样件在干燥状态:在试验之前直至恒重状态脱干(见7.2章节)并且在干燥的大气环境中存放不出现断裂的情况。
上汽-内外饰零件与材料要求关注点
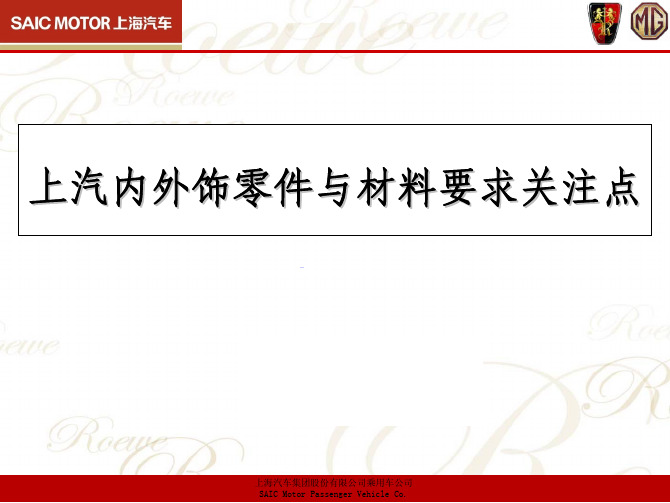
颜色要求与测定按照 SMTC 5 400 002要求
5 of
物理机械性能:
按上汽各材料性能企业标准或经批准的材料试验大纲
上海汽车集团股份有限公司乘用车公司 SAIC Motor Passenger Vehicle Co.
二,材料要求关注点
2,材料ELV要求关注点
样品要求:取自批量生产零件或与该状态一致的零件
¾ PP分子中存在叔碳原子,在光和热的作用下极易断裂降解。未加稳定 剂的PP在150℃下被加热半小时以上,或在阳光充足的地方曝晒12天 就会明显变脆。未加稳定剂的PP粉料在室内避光放置4个月也会严重 降解,散发出明显的酸味。在PP粉料造粒之前加入0.2%以上的抗氧剂 可以有效地防止PP在加工和使用过程中的降解老化。
No OK 等级C
∣ΔL*∣≤ 0.7
0.8≤∣ΔL*∣≤ 0.9
∣ΔL*∣≥ 1.0
∣Δa*∣≤ 0.3
0.4≤∣Δa*∣≤ 0.5
∣Δa*∣≥ 0.6
∣Δb*∣≤ 0.3
0.4≤∣Δb*∣≤ 0.5
∣Δb*∣≥ 0.6
2,对易起绒的织物(不具有纹理结构,如行李厢内饰、地毯)的公差 ; 3,非织物内饰件或零件具有非织物表面内饰件的样板基础公差 (黑色、棕色、米色和灰色)。
2,光照老化(内饰与外饰)
12 of
上海汽车集团股份有限公司乘用车公司
15
SAIC Motor Passenger Vehicle Co.
三,与材料有关的零件要求关注点
2,光照老化(内饰与外饰)
试验标准
PV3929
PV3930 (GB/T 16422.2)
氙灯类型
旋转式水冷氙灯
旋转式水冷氙灯
大众汽车标准_TL 52283 聚丙烯材料要求

11.1 老化时间(22+2) h
-
这些零部件,既不得有脆化现象,也不得有
老化温度(90±1)℃
肉眼可见的形态、色调和表面上的变化
至少用两个完整成品部件
11.2 老化时间(22+2) h 老化温度(110±2)℃ 至少用两个完整成品部件
这些零 部件,既 不得有 脆化现
象,也不
得有肉
眼可见
-
的形
态、色
规格 B
PP,压铸的,用 EPDM 改良的,滑石粉填充的(28%),紫外线加固的. >PP+EPDM-TD28<
规格 C
PP,压铸的,用 EPDM 改良的,滑石粉填充的(10%),紫外线加固的. >PP+EPDM-TD10<
规格 D
PP,压铸的,用 EPDM 改良的,滑石粉填充的(15%),玻璃纤维增强 的(15%),(对于可见范围内的工件主要是用紫外线加固). >PP+EPDM-(TD15+GF15)<
3.3 材料和标志按 VDA 260
规格无标记
PP,压铸的,用 EPDM (乙烯丙烯二烯单体)改良的,滑石粉填充的 (25%),紫外线加固的,高冲击韧性的 >PP+EPDM-TD25<
规格 A
PP,压铸的,用 EPDM 改良的,滑石粉填充的,有选择地用矿物粉填 充的(30%),紫外线加固的. >PP+EPDM-TD30<或>PP+EPDM-MD30<
试样的宽边上做出一个 0.8 mm,宽的 U 型缺口,其深度为 1/3 的试样厚度.受到边缘限制 的缺口,必须有一个<0.1 mm 的曲率半径.
如果成品部件的一个面上压有凸纹或上了油漆,其试样在该侧面上做出缺口时,则此 试样就该是这样放置在摆式冲击试验机支座上,使缺口的中部要准确地处于冲击平面, 而锤头要避开缺口.
VW50123-热塑性弹性体

为计算高聚物的熔融焓,应从试样重量中减去从热重分析计算得出灼烧残余物 的重量
热塑性弹性体
质量要求
表 2: Shore D 硬度范围
序号 1 1.1 1.2 1.2.1 1.2.2
1.2.2.1 1.2.2.2 1.2.2.3 1.2.2.4
1.2.2.5 1.2.2.6
1.2.2.7 1.2.2.8 1.2.2.9 2 2.1 2.2 2.3 2.4
2.5 2.6
2.7 2.8 2.9 3 3.1 3.2 3.3 3.3.1 3.3.2 3.3.3 3.3.4
对于新设计不再适用的材料标记
热塑性聚氨酯(TPE-U) >PUR< 热塑性 EPDM/PP 弹性体 (TPE-O/V) >EPDM+PP< 热塑性苯乙烯嵌段共聚物
(TPE-S) >PS/PE/PB<
对于新设计适用的材料标记
热塑性聚氨酯(TPU) >TPU-ARES< 热塑性 EPDM/PP 弹性体 (TPO) >TPO-(EPDM+PP)< 热塑性苯乙烯嵌段共聚物
热塑性弹性体热塑性弹性体热塑性弹性体热塑性弹性体质量要求vw50123shored硬度范围序号性能单位要求硬度按din5350511供货状态优先硬度值shore55312与供货状态比硬度变化121热老化后见6303122介质存放后见64条介质按图纸1221发动机油按tl52185shore1222传动器油按tl726shore1223油脂按tl735和tl745shore1224液化气汽油fam2按vw281shore0151225柴油按diniso18170151226植物油甲基酯按dinen14214shore0151227制动液按tl766shore按图纸1228冷却液按tl774shore按图纸1229图纸规定的介质shore介质存放后重量变化见64条介质按图纸21发动机油按tl5218522传动器油按tl72623油脂按tl735和tl74524液化气汽油fam2按vw28103025柴油按diniso181701526植物油甲基酯按dinen1421401527制动液按tl76628冷却液按tl77429图纸规定的介质拉伸强度按din5350431供货状态3032热老化后按633033介质存放后见64条介质按图纸331发动机油按tl5218525332传动器油按tl72625333油脂按tl735和tl74525334液化气汽油fam2按vw28120335柴油按diniso181725热塑性弹性体热塑性弹性体热塑性弹性体热塑性弹性体质量要求vw50123序号性能单位要求336植物油甲基酯按dinen1421425337制动液按tl76625338冷却液按tl77425339图纸规定的介质断裂延伸率按din5350441供货状态45042热老化后见6345043介质存放后见64条介质按图纸431发动机油按tl52185450432传动器油按tl726450433油脂按tl735和tl745450434液化气汽油fam2按vw281300435柴油按diniso1817300436植物油甲基酯按dinen14214300437制动液按tl766450438冷却液按tl774450439图纸规定的介质再撕裂力按diniso341nmm40缺口冲击强度按dineniso179123时kjm耐曲轴箱气体性能按pv3936按图纸