手动与自动间隙调整臂的区别及故障处理
刹车自动调整臂
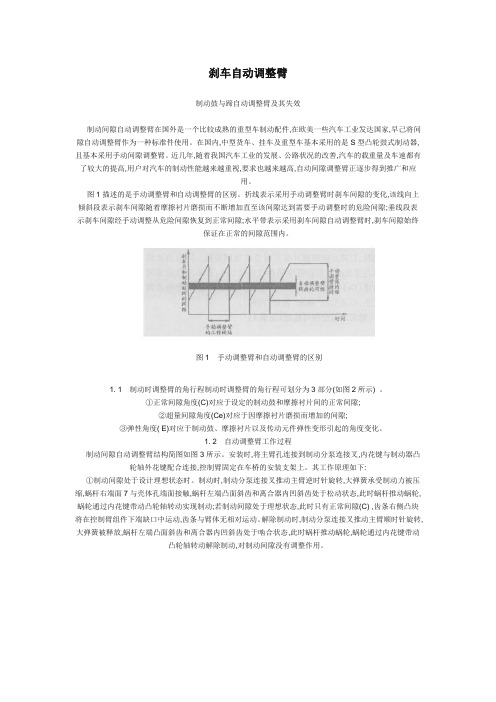
刹车自动调整臂制动鼓与蹄自动调整臂及其失效制动间隙自动调整臂在国外是一个比较成熟的重型车制动配件,在欧美一些汽车工业发达国家,早己将间隙自动调整臂作为一种标准件使用。
在国内,中型货车、挂车及重型车基本采用的是S型凸轮鼓式制动器,且基本采用手动间隙调整臂。
近几年,随着我国汽车工业的发展、公路状况的改善,汽车的载重量及车速都有了较大的提高,用户对汽车的制动性能越来越重视,要求也越来越高,自动间隙调整臂正逐步得到推广和应用。
图1描述的是手动调整臂和自动调整臂的区别。
折线表示采用手动调整臂时刹车间隙的变化,该线向上倾斜段表示刹车间隙随着摩擦衬片磨损而不断增加直至该间隙达到需要手动调整时的危险间隙;垂线段表示刹车间隙经手动调整从危险间隙恢复到正常间隙;水平带表示采用刹车间隙自动调整臂时,刹车间隙始终保证在正常的间隙范围内。
图1 手动调整臂和自动调整臂的区别1. 1制动时调整臂的角行程制动时调整臂的角行程可划分为3部分(如图2所示) 。
①正常间隙角度(C)对应于设定的制动鼓和摩擦衬片间的正常间隙;②超量间隙角度(Ce)对应于因摩擦衬片磨损而增加的间隙;③弹性角度( E)对应于制动鼓、摩擦衬片以及传动元件弹性变形引起的角度变化。
1. 2自动调整臂工作过程制动间隙自动调整臂结构简图如图3所示。
安装时,将主臂孔连接到制动分泵连接叉,内花键与制动器凸轮轴外花键配合连接,控制臂固定在车桥的安装支架上。
其工作原理如下:①制动间隙处于设计理想状态时。
制动时,制动分泵连接叉推动主臂逆时针旋转,大弹簧承受制动力被压缩,蜗杆右端面7与壳体孔端面接触,蜗杆左端凸面斜齿和离合器内凹斜齿处于松动状态,此时蜗杆推动蜗轮,蜗轮通过内花键带动凸轮轴转动实现制动;若制动间隙处于理想状态,此时只有正常间隙(C) ,齿条右侧凸块将在控制臂组件下端缺口中运动,齿条与臂体无相对运动。
解除制动时,制动分泵连接叉推动主臂顺时针旋转,大弹簧被释放,蜗杆左端凸面斜齿和离合器内凹斜齿处于啮合状态,此时蜗杆推动蜗轮,蜗轮通过内花键带动凸轮轴转动解除制动,对制动间隙没有调整作用。
东风商用车制动间隙自动调整臂结构原理

制动间隙自动调整臂结构、工作原理:制动间隙自动调整臂(以下简称自调臂)适用于鼓式制动器。
因为频繁的刹车,制动蹄片与制动鼓的间隙由于摩擦片的磨损而增大,使整车的制动性能大大降低。
手动调整臂通过人工调整制动器的间隙来保证行车的安全;在正常工作情况下的自调臂,则不再需要人工调节间隙,它利用制动和回位过程的推力和拉力使摩擦片与制动鼓之间的间隙保持到预留值,进一步提高车辆安全性。
同时,节约大量维护和保养时间,提高运营经济效益。
1、自调臂的工作原理:自动调整臂比手动调整臂增加了制动间隙的测量和制动间隙的补偿功能。
自调臂利用刹车制动和回位过程的推力与拉力,使螺纹叉c带动齿条a在自调臂转动过程中上下运动,以驱动控制元件使蜗杆b、蜗轮e相对于自调臂转动,来带动制动器凸轮轴转动,使制动间隙变小。
自调臂是通过转角来测量制动间隙,并根据其大小来实现间隙的自动调整,最终稳定在制动间隙的设定值(设定值为0.6~1.0mm)。
行车制动时,自调臂的工作可分解为三部分(见图21):正常间隙角度C (clearance),过度间隙角度Ce(excessive clearance)和弹性变形角度E(elasticity)。
图21正常间隙角度C:对应于设定的正常蹄、鼓之间的制动间隙,自调臂在该角度范围内不调整制动器的间隙。
过度间隙角度Ce:对应于因摩擦片的磨损和其它原因产生的大于正常设定值的间隙,自调臂根据该角度的大小在制动过程中进行制动间隙的自动调整,直到制动间隙为正常设定值、无超量间隙为止。
弹性变形角度E:对应于因摩擦片与制动鼓及传动元件弹性变形引起的角度变化,自调臂在该角度范围内不进行制动间隙的调整。
所以,在正常间隙角度C范围内,自调臂不参与间隙调整,只有当C+Ce>C时,自调臂才进行间隙调整,直至C+Ce=C。
并且任何一次制动过程中的弹性变形E都不参与自动调整。
2、自调臂的结构型式:目前,应用于东风公司中重型商用车的自动调整臂从结构上可以分为两种:一种为带控制臂结构(Bendix结构)的产品,另一种为不带控制臂结构(Haldex结构)的产品。
自动调整臂正确使用方法及常见问题

制动系统常见故障
制动鼓发热
原因1:制动气室推杆实际使用行程小于30㎜ 处理:1 检查调整臂预设间隙是否过小
2 检查制动器刚度是否过小,存在过调 现象
3 是否刚经历了长时间的制动过程
制动系统常见故障
制动鼓发热
原因2:新换摩擦片或制动鼓 处理:过了磨合期就会正常
原因3:制动鼓与制动器的同轴度和圆柱度 不满足要求
原因3:汽车偏载,左、右轮分配重量不等 处理:重新码放物品
制动系统常见故障
制动跑偏
原因5:一侧油封漏油,致使制动鼓与摩擦 片有油污
处理:换新摩擦片,并清洁制动鼓内表面
原因6:左右轮胎气压不一致 处理:充气使左右车轮气压相等
制动系统常见故障
制动疲软
原因1:制动气室推杆实际使用行程大于45㎜, 这里以135中心距为标准
安装过程中可能产生的错误
错误3:控制臂未推到位时,就将其固定。 分析:必须按照控制臂上箭头方向(朝制
动方向)推动控制臂,直到推不动为止, 然后才开始固定。其目的是保证调整臂正 常工作、免受破坏。
安装过程中可能产生的错误
错误4:经常用扳手拧蜗杆六方头 分析:因为调整臂为自动调整,故安装完
毕后,要求只有在安装、拆卸时,才允许转 动蜗杆六方头,否则,会严重影响产品的使 用寿命。
安装过程中可能产生的错误
错误1:先固定控制臂和定位支架,再联 接调整臂和气室推杆的U形叉。
分 析:正确安装步骤正好与之相反。 纠正方法:取出联接调整臂和推杆U形叉
的圆柱销,逆时针旋转蜗杆六方头,使 调整臂退出U形叉。再松开控制臂和定位 支架,使控制臂可上下自由转动。然后 继续上述的正确安装步骤。
安装步骤
用 SW12 扳 手 顺 时 针 旋转调整臂端部的 蜗杆六方头(注意: 不能使用电动扳手, 风动钻),使调整 臂的孔与气室推杆U 形叉的轴销孔自然 正对,然后将圆柱 销上轻松插入U形叉 孔,锁上开口销。
自动调整臂

自动调整臂1. 背景介绍自动调整臂是一种用于工业应用的机器人装置,它能够自动调整自身的姿态和位置,以适应各种工作环境和任务需求。
这种装置通常由多个关节组成,每个关节都能够运动并调整自身的角度和位置。
自动调整臂在许多领域都有广泛的应用,包括自动化生产线、仓储系统、医疗器械等等。
2. 工作原理自动调整臂的工作原理主要包括以下几个方面:2.1 传感器检测自动调整臂通常配备有多个传感器,用于感知周围的环境和目标物体的位置。
常见的传感器包括视觉传感器、力传感器、位置传感器等。
这些传感器能够实时采集环境信息,并传递给控制系统进行处理。
2.2 控制系统控制系统是自动调整臂的核心部分,它负责接收传感器采集到的数据,并根据预先设定的任务要求进行分析和决策。
控制系统能够计算出自动调整臂需要调整的姿态和位置,并输出相应的指令。
2.3 电机驱动自动调整臂中的每个关节都由电机驱动,用于实现关节的运动和调整。
电机驱动通常由控制系统发送的指令来控制,它能够通过调整关节的角度和位置,使得整个自动调整臂能够达到预定的目标姿态和位置。
2.4 反馈控制为了更加精确地控制自动调整臂的运动,通常会采用反馈控制的方法。
反馈控制通过不断检测调整臂的实际位置和姿态,并与目标位置和姿态进行比较,从而调整控制指令,使得自动调整臂能够更加准确地达到目标。
3. 应用场景自动调整臂在许多领域都有广泛的应用,以下是一些常见的应用场景:3.1 自动化生产线在自动化生产线中,自动调整臂可以用于搬运、拼装、焊接等工作。
它能够根据生产线上的物体位置和姿态进行自动调整,从而完成各种复杂的任务。
3.2 仓储系统在仓储系统中,自动调整臂可以用于货物的搬运和堆垛。
它可以根据货物的位置和重量进行自动调整,以适应不同大小和重量的货物。
3.3 医疗器械在医疗器械领域,自动调整臂可以用于手术机器人和检测设备等。
它可以根据手术区域和检测要求自动调整自身的姿态和位置,从而完成精确的手术和检测任务。
制动间隙自动调整臂的使用与维修

制动间隙自动调整臂的使用与维修制动间隙自动调整臂可以简称为“自动调整臂”,通俗易懂的可以解释为,自动调整臂可以根据当时发生的情况,自动调整刹车间隙的功能,保证刹车间隙在一个安全的范围。
本文将通过它的特点、结构、工作原理,分析阐述一下它的正确使用方法以及发生故障时的维修。
标签:自动调整臂;使用;维修根据国家规定,车辆必须使用含有刹车间隙自动调整臂功能的装置,随着车辆在行驶过程中,制动蹄片会产生摩擦,制动间隙也会越来越大,这样会导致延迟制动时间和制动的间距,造成刹车时间变长、刹车制动不及时,存在行车中的安全隐患。
1 制动间隙自动调整臂的特点(1)自动调整臂会根据车辆行驶时自动调整安全距离,可以减少人工手动的制动,在一定程度上保护了自动调整臂,减少车辆维修,减少维修车辆的开支。
(2)在车辆行驶中,自动调整臂可以保持四个车轮的平衡感、稳定感,使间距保持一致,避免了人工调整时不统一而产生车身跑偏的情况。
(3)自动调整臂的使用减少了人工调节对压缩空气的损耗,也减少了自动调整臂的使用摩擦、检查,达到延缓配件使用寿命的作用。
2 制动间隙自动调整臂的使用自动调整臂在车辆行驶过程中对超间距的行驶做出调整,可以分为三个级别。
图1中位置A为正常的间隙值。
图1中的位置B为超过间隙安全。
图1中位置C为弹性角。
自动调整臂会根据车辆行驶途中自动识别制动处在哪个位置,对于超出安全的部分进行自我调整。
(1)当自动调整臂被固定在控制环与齿条上下槽口相连接,刹车片与制动鼓之间的间隙由槽口的宽度决定。
当自动调整臂转向A的位置时,此时齿条向下活动,与控制环的槽口下端相接触,但此时的刹车片与制动鼓暂时未接触到。
自动调整臂继续向B的位置转动时,齿条与控制环的下端已接触到已无法向下活动,在控制环的反作用力下齿条驱动齿轮转向B角的的位置过量间隙时,此时刹车片与制动鼓就已接触上。
(2)当自动调整臂已超过B的位置后继续运转,调整臂壳体作用在凹轮轴和蜗轮上的两个反向力增大,使得蜗杆压缩推止弹簧移动,停止在C的位置导致蜗杆齿端与离合器的分离。
调整臂的作用
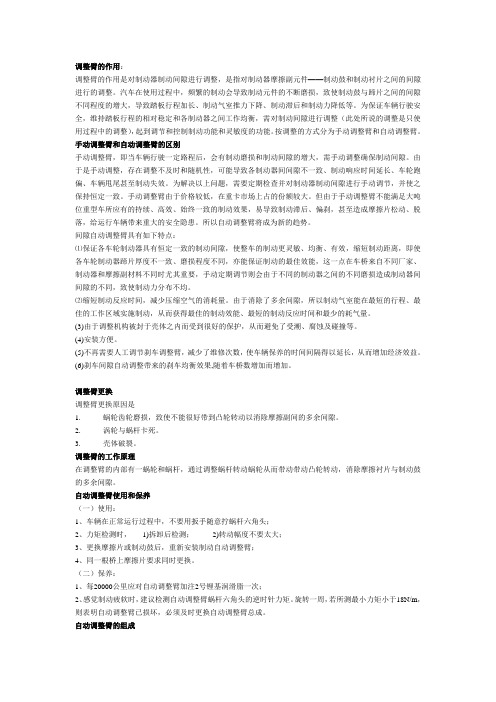
调整臂的作用:调整臂的作用是对制动器制动间隙进行调整,是指对制动器摩擦副元件——制动鼓和制动衬片之间的间隙进行的调整。
汽车在使用过程中,频繁的制动会导致制动元件的不断磨损,致使制动鼓与蹄片之间的间隙不同程度的增大,导致踏板行程加长、制动气室推力下降、制动滞后和制动力降低等。
为保证车辆行驶安全,维持踏板行程的相对稳定和各制动器之间工作均衡,需对制动间隙进行调整(此处所说的调整是只使用过程中的调整),起到调节和控制制动功能和灵敏度的功能。
按调整的方式分为手动调整臂和自动调整臂。
手动调整臂和自动调整臂的区别手动调整臂,即当车辆行驶一定路程后,会有制动磨损和制动间隙的增大,需手动调整确保制动间隙。
由于是手动调整,存在调整不及时和随机性,可能导致各制动器间间隙不一致、制动响应时间延长、车轮跑偏、车辆甩尾甚至制动失效。
为解决以上问题,需要定期检查并对制动器制动间隙进行手动调节,并使之保持恒定一致。
手动调整臂由于价格较低,在重卡市场上占的份额较大。
但由于手动调整臂不能满足大吨位重型车所应有的持续、高效、始终一致的制动效果,易导致制动滞后、偏刹,甚至造成摩擦片松动、脱落,给运行车辆带来重大的安全隐患。
所以自动调整臂将成为新的趋势。
间隙自动调整臂具有如下特点:⑴保证各车轮制动器具有恒定一致的制动间隙,使整车的制动更灵敏、均衡、有效,缩短制动距离,即使各车轮制动器蹄片厚度不一致、磨损程度不同,亦能保证制动的最佳效能,这一点在车桥来自不同厂家、制动器和摩擦副材料不同时尤其重要,手动定期调节则会由于不同的制动器之间的不同磨损造成制动器间间隙的不同,致使制动力分布不均。
⑵缩短制动反应时间,减少压缩空气的消耗量。
由于消除了多余间隙,所以制动气室能在最短的行程、最佳的工作区域实施制动,从而获得最佳的制动效能、最短的制动反应时间和最少的耗气量。
(3)由于调整机构被封于壳体之内而受到很好的保护,从而避免了受潮、腐蚀及碰撞等。
(4)安装方便。
备品业务知识---调整臂

调整臂知识手册调整臂的作用:调整臂的作用是对制动器制动间隙进行调整,是指对制动器摩擦副元件——制动鼓和制动衬片之间的间隙进行的调整。
汽车在使用过程中,频繁的制动会导致制动元件的不断磨损,致使制动鼓与蹄片之间的间隙不同程度的增大,导致踏板行程加长、制动气室推力下降、制动滞后和制动力降低等。
为保证车辆行驶安全,维持踏板行程的相对稳定和各制动器之间工作均衡,需对制动间隙进行调整(此处所说的调整是只使用过程中的调整),起到调节和控制制动功能和灵敏度的功能。
按调整的方式分为手动调整臂和自动调整臂。
手动调整臂和自动调整臂的区别手动调整臂,即当车辆行驶一定路程后,会有制动磨损和制动间隙的增大,需手动调整确保制动间隙。
由于是手动调整,存在调整不及时和随机性,可能导致各制动器间间隙不一致、制动响应时间延长、车轮跑偏、车辆甩尾甚至制动失效。
为解决以上问题,需要定期检查并对制动器制动间隙进行手动调节,并使之保持恒定一致。
手动调整臂由于价格较低,在重卡市场上占的份额较大。
但由于手动调整臂不能满足大吨位重型车所应有的持续、高效、始终一致的制动效果,易导致制动滞后、偏刹,甚至造成摩擦片松动、脱落,给运行车辆带来重大的安全隐患。
所以自动调整臂将成为新的趋势。
间隙自动调整臂具有如下特点:⑴保证各车轮制动器具有恒定一致的制动间隙,使整车的制动更灵敏、均衡、有效,缩短制动距离,即使各车轮制动器蹄片厚度不一致、磨损程度不同,亦能保证制动的最佳效能,这一点在车桥来自不同厂家、制动器和摩擦副材料不同时尤其重要,手动定期调节则会由于不同的制动器之间的不同磨损造成制动器间间隙的不同,致使制动力分布不均。
⑵缩短制动反应时间,减少压缩空气的消耗量。
由于消除了多余间隙,所以制动气室能在最短的行程、最佳的工作区域实施制动,从而获得最佳的制动效能、最短的制动反应时间和最少的耗气量。
(3)由于调整机构被封于壳体之内而受到很好的保护,从而避免了受潮、腐蚀及碰撞等。
自调臂,千万别随意调!看了原理你就懂了

自调臂,千万别随意调!看了原理你就懂了随着我国高速公路网的不断完善,长途物流运输越来越多地使用主挂车连接的运输方式,而且趋向于集成化、大吨位,这就对主挂车制动系统的匹配、协调及可靠性提出了更高要求。
本文通过梳理我国目前主挂车制动系统在使用中出现的问题,提出相应的解决方案。
主挂车制动系统存在的问题及原因目前我国主挂车运输车辆的驱动形式一般为采用6×2和6×4 2种形式。
由于6×2配置在成本上具有优势,因此近年来的新购车辆以6×2驱动形式居多。
以陕汽德龙M3000系列为例,主车6×2驱动可以准拖挂车总质量38 300 kg,6×4驱动可以准拖挂车总质量38 600 kg,所配的半挂车通常采用3轴仓栅式,是我国西部、北部地区货运市场的主流车型。
这些车辆的主车制动系统一般都配有ABS和制动间隙自动调整臂,而挂车制动系统基本都是手动调整臂,甚至部分配有ABS的挂车也使用手动调整臂。
从市场调查情况来看,在实际使用过程中普遍存在如下现象:用户擅自将主车第1轴制动管路堵死;部分用户将6×2驱动的第2轴制动管路也堵死或解除自调臂的控制臂,并将第3轴自调臂更换为手调臂;部分用户擅自在主车ABS系统中接入一个开关,重载时关闭车辆的ABS功能。
笔者认为,导致以上问题的主要原因包括以下几点。
主车第2轴控制臂解除第一,在挂车用手调臂、主车用自调臂的情况下,主车制动反应灵敏,特别在下长坡制动时挂车对主车容易产生冲击。
为避免这种情况,驾驶员希望挂车制动要先于主车,因此不希望主车制动快速有效响应。
第二,新车买回后用户自己加装气压式轮鼓喷水装置,用于制动时给轮鼓降温。
为了避免频繁制动时出现整车气压供应不足,用户会将主车1轴、部分6×2车型的2轴制动管路堵死,以降低制动用气量。
此外,当主车ABS功能被关闭时,第1、第2轴的转向轮还不会出现制动抱死现象。
第三,由于1、2轴不参与制动,主车的制动力全部由第3轴承担,容易导致制动发热,加快摩擦片磨损,但由于易损件不在三包范围内,车主为降低使用成本、延长摩擦片使用寿命,将第3轴自调臂更换成手调臂。
- 1、下载文档前请自行甄别文档内容的完整性,平台不提供额外的编辑、内容补充、找答案等附加服务。
- 2、"仅部分预览"的文档,不可在线预览部分如存在完整性等问题,可反馈申请退款(可完整预览的文档不适用该条件!)。
- 3、如文档侵犯您的权益,请联系客服反馈,我们会尽快为您处理(人工客服工作时间:9:00-18:30)。
手动与自动间隙调整臂的区别及故障处理
马国兴
【摘要】文章对手动间隙调整臂与自动间隙调整臂结构及原理进行分析,同时对安装及调试方法进行对比,对常见的故障原因及排除方法进行了列举,从而为制动间隙调整臂的调整维修提供了依据.
【期刊名称】《汽车实用技术》
【年(卷),期】2018(000)014
【总页数】3页(P230-232)
【关键词】手动间隙调整臂;自动间隙调整臂;故障处理
【作者】马国兴
【作者单位】陕西重型汽车有限公司,陕西西安 710200
【正文语种】中文
【中图分类】U461.3
前言
制动间隙调整臂是汽车气压制动系统中的一个重要总成。
卡车在行驶过程中,频繁的制动会导致制动蹄片和制动鼓不断磨损,致使它们两者之间的间隙逐渐变大;最终导致制动气室推杆行程变长,推力下降,引起制动滞后和制动力降低。
为了保障行车安全,必须保证制动蹄片和制动鼓之间有合适的配合间隙,调整臂就是用来起到调节和控制两者间隙的装置。
无论手动还是自动,他们的最终目的都是
一样,只不过自动的调整臂不用人为去干预调整,控制间隙更精确而已。
1 结构对比
1.1 手调臂
主要组成有锁止机构、蜗轮蜗杆传动机构、壳体等。
1.2 自调臂
主要组成有齿轮齿条传动机构(或齿轮+斜齿轮)、蜗轮蜗杆传动机构、单向离合器、壳体等。
图1
2 原理对比
2.1 手调臂工作原理
通过调整蜗杆轴4,驱动涡轮2,带动制动凸轮轴转过一定角度。
也就是说,在调整臂体与气室推杆相对位置不变的情况下,改变制动凸轮轴的初始位置,从而改变制动间隙。
如图2。
2.2 自调臂工作原理
通过对制动时调整臂转过的角度与所受的反作力大小变化的感知,正确识别:正常间隙角“A”、超量间隙角“B”和弹性角“C”,而仅对过量间隙进行调节。
如图3:
图2
图3
3 安装方法对比
3.1 手调臂安装
调整制动蹄片与制动鼓间隙,将调整臂螺钉顺时针拧到底,直至车轮锁死,然后将螺钉往后退,前轴听到三次响声,驱动桥听到四次响声。
图4
3.2 自调臂安装
把调整臂安装在凸轮轴上。
注意壳体上的箭头方向应与制动方向一致,也就是制动气室推杆向外推动调整臂方向。
用SW12扳手顺时针旋转调整臂端部的蜗杆六方头(注意:不能使用电动扳手,
风动钻),使调整臂柄孔与气室推杆U形叉孔自然正对,然后将圆柱销上轻松插
入U形叉孔,锁上开口销。
用隔圈、螺栓或垫片、卡簧将调整臂固定在凸轮轴上,此时应确保调整臂的轴向间隙A=0.50-2.00mm。
图5
将控制臂向制动方向推动(控制臂上有箭头示意推动方向)直到推不动为止。
此时,控制臂上指针应指向开口或控制臂上的刻线与控制臂盖上的对齐。
其操作目的是使自动调整臂正常工作、免受破坏。
安装调整臂支架,随后将控制臂紧固在定位支架上。
图6
用扳手顺时针转动调整臂蜗杆六角头直至摩擦片与制动鼓接触,然后再逆时针方向转动蜗杆六角头3/4圈(反向转动时会听到咔咔声)。
注意:不能使用电动扳手、风动钻!
施加若干次制动,刹车间隙自动调整至正常范围,调整功能可通过蜗杆六角头在刹车即将结束时顺时针方向自动旋转观察到,至此安装过程结束。
图7
4 常见失效模式及失效判定
4.1 常见失效模式
自调臂失效模式中,自调失效引起的制动失效发生频次最高。
也就是说目前单向离合器的寿命满足不了要求。
每刹车一次,单向离合器分离打滑一次,使离合弹簧表
面粗糙度减少,摩擦力就会相应减少,按照这个趋势发展,单向离合器结合正向旋转的摩擦力会越来越小,最终导致正向打滑状态,就会出现离合器自调失效。
压力越大、接触面越粗糙,滑动摩擦力越大。
频繁的刹车会引起摩擦系数改变,还有自调臂本身的密封不良,导致灰尘跑进去,也会增大离合弹簧表面磨损的快慢,最终影响摩擦系数,导致摩擦力减少,减少寿命。
其它失效模式:
(1)蜗杆锥齿磨损,通过检测蜗杆反向力矩值可判断。
(2)L型控制臂上的连接套脱落或磨损,目测可发现。
使用隆中专利扁形销可极大减少该问题的发生。
(3)调整臂回位慢,引起制动发热、疲软等。
(4)安装不当,控制臂铆接位打滑、控制臂断裂。
(5)安装不当,引进的制动间隙小,导致制动鼓发热。
(6)安装不当,气室行程不足引起制动疲软。
4.2 失效判定
外观判定:
(1)检查壳体以及控制臂等部位,对于出现裂纹或者断裂的产品判定失效。
(2)加强圈、连接套出现严重磨损的产品判定失效。
(3)连接环与控制臂能够相对转动,则判定产品已失效,通常称为控制臂打滑。
(4)将控制臂先按顺时针方向转动,直至转不动为止,然后按逆时针方向旋转,此时蜗杆六角头不能随之转动,则判定产品已失效。
参数判定:
(1)逆时针转动调整臂蜗杆六角头,力矩小于18N·m的调整臂判定为失效。
(2)逆时针转动调整臂蜗杆六角头,声音不连续、不清脆,而是“噗、噗”…的声音则判定失效。
5 常见故障处理
表1?
6 结论
在汽车行驶过程中,由于调整臂的频繁使用,磨损或损毁不可避免,技术状态容易变差或者出现故障。
因此学会正确的判断和排除调整臂的常见故障能够很大程度地提高调整臂的使用寿命。
参考文献
【相关文献】
[1] 胡丽君,吴涛,俞碧君.刹车间隙自动调整臂工作原理及设计重点.中国机械.
[2] 桑楠.S形凸轮制动间隙自动调整臂工作原理及运动仿真.武汉理工大学.
[3] 段敏,赵安成,田万禄.汽车制动器间隙自动调整装置. 辽宁工业大学学报(自然科学版).
[4] 卢春雷.刹车(制动)间隙自动调整臂(二):两种不同类型的刹车(制动)间隙自动调整臂.汽车与配件.
[5] 陈黎,夏小均,刘生刚.汽车制动器制动间隙自调模式分析.机械工程师.。