硅集成电路工艺基础复习
硅集成电路复习提纲(最终版)

集成电路工艺基础复习绪论1、Moore law:芯片上所集成的晶体管的数目,每隔18个月翻一番。
2、特征尺寸:集成电路中半导体器件能够加工的最小尺寸。
3、提拉法(CZ法,切克劳斯基法)和区熔法制备硅片:答:区熔法制备的硅片质量更高,因为含氧量低。
目前8英寸以上的硅片,经常选择选择CZ法制备,因为晶圆直径大。
4、MOS器件中常使用什么晶面方向的硅片,双极型器件呢?答:MOS器件:<100> Si/SiO2界面态密度低;双极器件:<111>的原子密度大,生长速度快,成本低。
氧化1、sio2的特性二氧化硅对硅的粘附性好,化学性质比较稳定,绝缘性好2、sio2的结构,分为结晶形与不定形二氧化硅3、什么是桥键氧和非桥键氧连接两个Si-o四面体的氧称为桥键氧;只与一个硅连接的氧称为非桥键氧。
4、在无定形的sio2中,si、o那个运动能力强,为什么?氧的运动同硅相比更容易些;因为硅要运动就必须打破四个si-o键,但对氧来说,只需打破两个si-o键,对非桥键氧只需打破一个si-o键。
5、热氧化法生长sio2过程中,氧化生长的方向是什么?在热氧化法制备sio2的过程中,是氧或水汽等氧化剂穿过sio2层,到达si-sio2界面,与硅反应生成sio2,而不是硅向sio2外表面运动,在表面与氧化剂反应生成sio26、Sio2只与什么酸、碱发生反应?只与氢氟酸、强碱溶液发生反应7、杂质在sio2中的存在形式,分别给与描述解释,各自对sio2网络的影响能替代si-o四面体中心的硅,并能与氧形成网络的杂志,称为网络形成者;存在于sio2网络间隙中的杂志称为网络改变者。
8、水汽对sio2网络的影响水汽能以分子态形式进入sio2网络中,并能和桥键氧反应生成非桥键氢氧基,本反应减少了网络中桥键氧的数目,网络强度减弱和疏松,使杂志的扩散能力增强。
9、为什么选用sio2作为掩蔽的原因,是否可以作为任何杂质的掩蔽材料为什么?10、制备sio2有哪几种方法?热分解淀积法,溅射法,真空蒸发法,阳极氧化法,化学气相淀积法,热氧化法等。
硅集成电路工艺基础
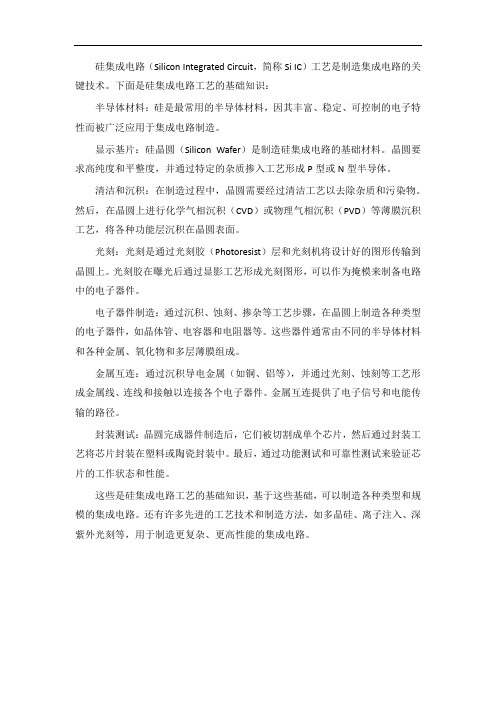
硅集成电路(Silicon Integrated Circuit,简称Si IC)工艺是制造集成电路的关键技术。
下面是硅集成电路工艺的基础知识:
半导体材料:硅是最常用的半导体材料,因其丰富、稳定、可控制的电子特性而被广泛应用于集成电路制造。
显示基片:硅晶圆(Silicon Wafer)是制造硅集成电路的基础材料。
晶圆要求高纯度和平整度,并通过特定的杂质掺入工艺形成P型或N型半导体。
清洁和沉积:在制造过程中,晶圆需要经过清洁工艺以去除杂质和污染物。
然后,在晶圆上进行化学气相沉积(CVD)或物理气相沉积(PVD)等薄膜沉积工艺,将各种功能层沉积在晶圆表面。
光刻:光刻是通过光刻胶(Photoresist)层和光刻机将设计好的图形传输到晶圆上。
光刻胶在曝光后通过显影工艺形成光刻图形,可以作为掩模来制备电路中的电子器件。
电子器件制造:通过沉积、蚀刻、掺杂等工艺步骤,在晶圆上制造各种类型的电子器件,如晶体管、电容器和电阻器等。
这些器件通常由不同的半导体材料和各种金属、氧化物和多层薄膜组成。
金属互连:通过沉积导电金属(如铜、铝等),并通过光刻、蚀刻等工艺形成金属线、连线和接触以连接各个电子器件。
金属互连提供了电子信号和电能传输的路径。
封装测试:晶圆完成器件制造后,它们被切割成单个芯片,然后通过封装工艺将芯片封装在塑料或陶瓷封装中。
最后,通过功能测试和可靠性测试来验证芯片的工作状态和性能。
这些是硅集成电路工艺的基础知识,基于这些基础,可以制造各种类型和规模的集成电路。
还有许多先进的工艺技术和制造方法,如多晶硅、离子注入、深紫外光刻等,用于制造更复杂、更高性能的集成电路。
硅集成电路工艺基础10
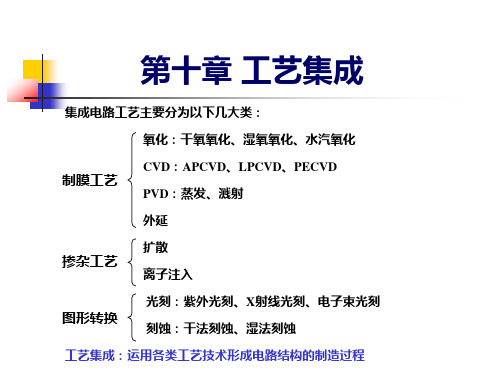
LOCOS隔离工艺的改进 --- 减小鸟嘴
在亚微米集成电路制备中,对LOCOS隔离工艺进行改进,出现了减 小鸟嘴,提高表面平坦化的隔离方法。
1. 回刻的LOCOS工艺:通过回刻除去部分场氧化层,从而使表面平坦 并恢复部分被鸟嘴占去的有源区。
2. 多晶硅缓冲层的LOCOS工艺:由于鸟嘴的形成与二氧化硅缓冲层密 切相关,减薄二氧化硅缓冲层可以减小鸟嘴的尺寸,因此在多晶硅缓冲 层的 LOCOS工艺中,利用多晶硅和二氧化硅叠层替代单一的二氧化硅 缓冲层(多晶硅50nm/SiO25~10nm),可以大大降低鸟嘴的尺寸。
源漏扩展结构(S/D extension):
随着器件特征尺寸的进一步缩小,为了获得更浅的结 深和更高的掺杂浓度以改善器件的特性、抑制短沟效应, 出现了源漏扩展结构,其中超浅的扩展区用以形成浅结, 抑制短沟效应;较深的源漏区用以形成好的欧姆接触、 降低接触电阻。
利用大角度倾斜注入反型杂质的技术:
进一步降低短沟效应、降低源漏扩展区的横扩、提高 杂质分布的梯度以降低源漏串联电阻,在源漏扩展区周 围形成反型掺杂区,其杂质分布截面类似于晕环(halo) 和袋状结构。
防止场区的寄生MOSFET开启的方法:
提高寄生MOSFET的阈值电压,使寄生场效应晶体管的阈值电压高于 集成电路的工作电压。通常场区的阈值电压要比集成电路的电源电压高 3~4V,以使相互隔离的两个MOSFET间的漏电流小于l pA。
提高场效应晶体管阈值电压的方法主要有两种:
➢ 增加场区SiO2的厚度,但是过厚的氧化层将产生过高的台阶,从而引起 台阶覆盖的问题,通常场氧化层厚度为栅氧化层厚度的7-10倍。
双掺杂多晶硅栅工艺
理想的方法是采用双掺杂多晶硅栅工艺,在同一芯片上分别使用 n+和p+多晶硅栅电极,即nMOS采用n+多晶硅栅电极,pMOS采用p+ 多晶硅栅电极。这样可以使得nMOS与pMOS在阈值电压、沟道长度、 沟道掺杂等多方面对称。
硅集成电路工艺基础复习
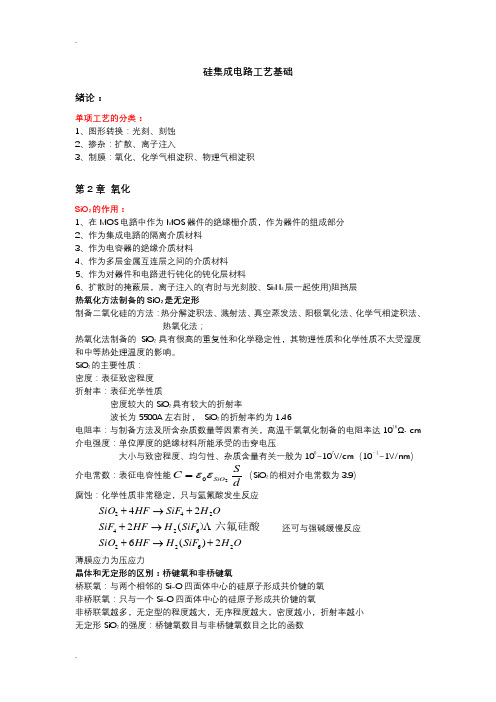
硅集成电路工艺基础绪论:单项工艺的分类:1、图形转换:光刻、刻蚀2、掺杂:扩散、离子注入3、制膜:氧化、化学气相淀积、物理气相淀积第2章 氧化SiO 2的作用:1、在MOS 电路中作为MOS 器件的绝缘栅介质,作为器件的组成部分2、作为集成电路的隔离介质材料3、作为电容器的绝缘介质材料4、作为多层金属互连层之间的介质材料5、作为对器件和电路进行钝化的钝化层材料6、扩散时的掩蔽层,离子注入的(有时与光刻胶、Si 3N 4层一起使用)阻挡层 热氧化方法制备的SiO 2是无定形制备二氧化硅的方法:热分解淀积法、溅射法、真空蒸发法、阳极氧化法、化学气相淀积法、热氧化法;热氧化法制备的SiO 2具有很高的重复性和化学稳定性,其物理性质和化学性质不太受湿度和中等热处理温度的影响。
SiO 2的主要性质: 密度:表征致密程度 折射率:表征光学性质密度较大的SiO 2具有较大的折射率波长为5500A 左右时, SiO 2的折射率约为1.46电阻率:与制备方法及所含杂质数量等因素有关,高温干氧氧化制备的电阻率达1016Ω· cm 介电强度:单位厚度的绝缘材料所能承受的击穿电压大小与致密程度、均匀性、杂质含量有关一般为106~107V/cm (10-1~1V/nm ) 介电常数:表征电容性能dSC SiO 20εε=(SiO 2的相对介电常数为3.9) 腐蚀:化学性质非常稳定,只与氢氟酸发生反应OH SiF H HF SiO SiF H HF SiF OH SiF HF SiO 26226242422)(6(224+→+→++→+六氟硅酸)还可与强碱缓慢反应 薄膜应力为压应力晶体和无定形的区别:桥键氧和非桥键氧桥联氧:与两个相邻的Si-O 四面体中心的硅原子形成共价键的氧 非桥联氧:只与一个Si-O 四面体中心的硅原子形成共价键的氧非桥联氧越多,无定型的程度越大,无序程度越大,密度越小,折射率越小 无定形SiO 2的强度:桥键氧数目与非桥键氧数目之比的函数 结晶态和无定形态区分——非桥联氧是否存在 杂质分类:网络形成者和网络改变者网络形成者:可以替代SiO 2网络中硅的杂质,即能代替Si -O 四面体中心的硅、并能与氧形成网络的杂质网络改变者:存在于SiO 2网络间隙中的杂质 SiO 2作为掩蔽层对硼、磷有效,对钠离子无效B 、P 、As 等常用杂质的扩散系数小, SiO 2对这类杂质可以起掩蔽作用 Ga 、某些碱金属(Na )的扩散系数大, SiO 2对这类杂质就起不到掩蔽作用 Si 热氧化生长SiO 2的计算:02xC x C SiO Si = 无定形SiO 2的分子密度:322/102.22cm C SiO ⨯=硅晶体的原子密度:322/100.5cm C Si ⨯=干氧、水汽和湿氧。
硅集成电路考试基础知识.doc

硅集成电路考试基础知识第一章:1。
为什么常用的半导体材料选择硅(1)硅的丰度。
低成本消费;(2)更高的熔化温度允许更宽的工艺公差。
硅1412℃锗937℃(3)较宽的工作温度。
增加了半导体的应用范围和可靠性;(4)自然形成的氧化硅,优质稳定的电绝缘材料si,金刚石110面(线)密度最大,111面(线)密度最小2。
缺陷:主要缺陷(生长过程)、有害杂质(加工过程)(1)点缺陷:自间隙原子、空位、肖特基缺陷(原始原子向表面移动)、伦克尔缺陷(原始原子进入间隙)、外来原子(替代型、间隙型)(2)线缺陷: 位错(边缘位错(位错线的垂直滑移方向)、螺旋位错(位错线的平行滑移方向)、扩展位错(T增加,位错迁移))(3)表面缺陷: 堆垛层错(与原子紧密堆积结构紊乱相关的界面缺陷)(4)整体缺陷:杂质沉淀(5)有害杂质:1)杂质条纹:电活性杂质的条纹缺陷,导致晶体电阻率的微区不均匀2)有害杂质(三级):非金属、金属和重金属非金属:氧、碳重金属:铁和铜(引入复合中心以降低载流子寿命;容易沉积金属:纳,钾(引入浅能级中心参与传导);铝的引入补偿了氮型材料的掺杂)。
基底材料要求:通过单晶生长过程中的质量控制和后续处理,提高了单晶的质量,使单晶趋于完美。
减少单晶材料中缺陷和有害杂质的后续处理方法通常采用吸杂技术。
吸收技术主要包括物理吸收、增溶吸收和化学吸收。
1)物理学:内在、背面损伤、应力、扩散2)溶解性增强:t增加,固体溶解度增加,杂质迁移率增加,并且很难沉积3)化学物质:含氮气体与硅表面金属杂质反应,产生挥发性产品缺陷要求、参数均匀性要求和晶片平整度要求4。
区域熔化法:将籽晶和多晶棒紧密粘结在一起,在将熔化区域从籽晶移动到多晶的另一端的过程中,使用分段熔化多晶棒将多晶转化为单晶。
1)水平区域熔化法(布里奇曼法)-1。
为什么常用的半导体材料选择硅(1)硅丰度。
低成本消费;(2)更高的熔化温度允许更宽的工艺公差。
硅1412℃锗937℃(3)较宽的工作温度。
硅集成电路工艺基础重点

1 SiO2的结构和性质:①分为结晶形和非结晶形(无定形),均由Si-O四面体组成:中心-硅原子,四个顶角-氧原子,形成O-Si-O 键桥,相邻四面体靠此键桥连接。
结晶形SiO2—由Si-O四面体在空间规则排列所构成。
非结晶形SiO2—依靠桥键氧把Si-O四面体无规则地连接起来,构成三维的玻璃网络体。
②热氧化制备SiO2的过程中,是氧或水汽等氧化剂穿过SiO2层,到达Si-SiO2界面,与Si反应生成SiO2,而不是Si向SiO2外表面运动、在表面与氧化剂反应生成SiO2。
2 SiO2的掩蔽作用:按杂质在网络中所处的位置可分为两类:网络形成者和网络改变者。
网络形成者(剂)--可以替代SiO2网络中硅的杂质,也就是能代替Si-O四面体中心的硅,并能与氧形成网络的杂质。
特点:离子半径与硅接近。
网络改变者(剂)--存在于SiO2网络间隙中的杂质。
一般以离子形式存在网络中。
特点:离子半径较大,以氧化物形式进入SiO2中,进入网络之后便离化,并把氧离子交给SiO2网络。
硅的热氧化的两种极限:一:当氧化剂在中的扩散系数D SiO2 很小时称为扩散控制,二当扩散系数D SiO2很大时称为反应控制。
3决定氧化常数的各种因素和影响氧化速率的因素:(1)氧化剂分压,在一定的氧化条件下,通过改变氧化剂分压课达到改变二氧化硅的生长速率的目的。
(2)氧化温度,温度对抛物型速率常数的影响是通过氧化剂在SiO2中的扩散系数产生的。
(3)硅表面晶向对氧化速率的影响。
(4)杂质对氧化速率的影响4 决定热氧化过程中的杂质在分布的因素:a杂质的分凝现象,b杂质通过二氧化硅的表面逸散,c氧化速率的快慢,d杂质在二氧化硅中的扩散速度。
5分凝系数与再分布的关系:m=杂志在硅中的平衡浓度/杂质在二氧化硅中的平衡浓度四种分凝现象:m<1,SiO2中慢扩散:B;m<1, SiO2中快扩散:H2气氛中的B;m>1, SiO2中慢扩散:P; m>1, SiO2中快扩散:Ga;6杂质扩散机构:(1)间隙式扩散——杂质在晶格间的间隙运动,(2)替位式扩散——杂质原子从一个晶格点替位位置运动到另一个替位位置。
习题 4 硅集成电路工艺基础 习题 答案

复习题2-21、试说明热氧化法的两种基本方法,并比较两种方法的主要优缺点。
干氧氧化:是通过把硅暴露在高纯度氧气的高温气氛里完成氧化层均匀生长的方法。
氧化层结构致密、均匀性和重复性好,掩蔽能力强;与光刻胶粘附性较好,不易产生浮胶现象;氧化速度慢。
水汽氧化:高温下,将硅与高纯水产生的水蒸汽反应生成SiO2的方法。
水汽氧化速度更快;且受温度的影响更小;氧化层密度比干氧氧化的小(氧化层结构疏松,质量不如干氧氧化的好);但可通过在惰性气体中加热氧化来改善;氧化层表面与光刻胶粘附性差,但可用吹干氧(或干氮)热处理来解决。
2、为什么水汽氧化生成的氧化层质量不如干氧氧化层?工艺中采用什么办法来改善其氧化层质量?原因:(1)由于水汽的进入,是网络中大量的桥键氧变为非桥键氧的羟基,使氧化层结构变疏松,密度降低,质量不如干氧氧化的好。
----可通过在惰性气体中加热氧化来改善。
(2)氢留在氧化层中,会产生陷阱或形成潜在的电荷态,造成结构的弱化和疏松。
(3)氧化层表面产生了极性的硅烷醇,它极易吸附水,从而使氧化层表面与光刻胶的粘附性变差。
----可用吹干氧(或干氮)热处理来解决。
3、什么是掺氯氧化?试说明氧化工艺中掺氯的主要优点。
掺氯氧化:在用于热氧化的干氧中填加少量卤素的一种新的热氧化技术,其将氯结合到氧化层中并集中分布在Si-SiO2界面附近,称之为掺氯氧化。
主要优点:可固定(称为钝化或俘获)可动离子,尤其是钠离子(Na+),即氯有不断清洁含有这些杂质的环境的功效;可中和界面处的电荷堆积,降低了膜层中固定电荷和界面态密度;提高氧化速率提高10%~15%;增加了氧化层下面硅中少数载流子的寿命;减少了SiO2中的缺陷,提高了氧化层的抗击穿能力;减少了硅中的氧化诱生堆垛层错。
4、试说明什么是迪尔-格罗夫模型?试给出迪尔-格罗夫模型的示意图,并说明其物理含义。
Deal-Grove 氧化模型(线性-抛物线模型linear-parabolic model),是可以用固体理论解释的一维平面生长氧化硅的模型,是用来预测氧化层厚度的热动力学模型。
硅集成电路工艺基础7-文档资料

上节课内容小结
铝的化学气相沉积
优点:①CVD铝对接触孔有很好的填充性; ②较低的电阻率(与钨相比); ③一次完成填充和互连。
MOCVD Al:沉积温度低200度 Al的有机化合物有毒、易燃、接触水会爆炸,必须密封保存,合理操作。 化学性质活泼,必须低温保存,进入反应室前,采取措施以保持稳定性 CVD铝抗电迁移能力差:CVD铝铜合金
上节课内容小结
TiN的化学气相沉积
在ULSI互连系统中,使用铝合金、铜、钨等金属作为互连线或者填充接 触孔和通孔,在这层金属下面要先淀积一层TiN薄膜。其作用是: ➢对于铝合金层,它作为扩散阻挡层防止在金属互连层之间形成接触点; ➢对于钨或铜的覆盖层,它既作为扩散阻挡层又作为附着层,称为衬垫。
CVD的TiN薄膜保形性好,可以形成理想的填充 LPCVD:沉积温度高,600度以上,超过了Al能承受的范围,只能用于接 触孔的淀积。 MOCVD:淀积温度低, 400度以下,在接触孔和通孔中都能使用。
上节课内容小结
硅化钨的化学气相沉积
ploycide(多晶硅/难熔金属硅化物)多层栅结构 WF6 (气) 2SiH4 (气) WSi (固) 6HF (气) H2 (气)
采用DCS和WF6反应生成WSix薄膜的台阶覆盖好一些,且碎裂剥 落也不太严重,因而用DCS取代了SiH4进行CVD硅化钨。 WF6 (气) 3.5SiH2Cl2 (气) WSi2 (固)1.5SiCl4 (气) 6HF (气) HCl (气)
➢在TEOS/O3淀积SiO2层; ➢再用PECVD方法淀积一层SiO2作为保护层,避免氧化层中含有的Si-OH键吸收水
汽。
上节课内容小结
CVD掺杂二氧化硅 1. 磷硅玻璃
PSG在高温下可以流动,从而可以形成更为平坦的表面,使随后淀积的 薄膜有更好的台阶覆盖。 回流平坦化温度1000-1100 ℃ 。 磷最好限制在6-8wt%。
- 1、下载文档前请自行甄别文档内容的完整性,平台不提供额外的编辑、内容补充、找答案等附加服务。
- 2、"仅部分预览"的文档,不可在线预览部分如存在完整性等问题,可反馈申请退款(可完整预览的文档不适用该条件!)。
- 3、如文档侵犯您的权益,请联系客服反馈,我们会尽快为您处理(人工客服工作时间:9:00-18:30)。
硅 集 成 电 路 工 艺 基绪论:单项工艺的分类: 1、 图形转换:光刻、刻蚀 2、 掺杂:扩散、离子注入3、 制膜:氧化、化学气相淀积、物理气相淀积第2章氧化SiO 2的作用:1、 在MOS 电路中作为 MOS 器件的绝缘栅介质,作为器件的组成部分2、 作为集成电路的隔离介质材料3、 作为电容器的绝缘介质材料4、 作为多层金属互连层之间的介质材料5、 作为对器件和电路进行钝化的钝化层材料6、 扩散时的掩蔽层,离子注入的 (有时与光刻胶、Si 3N 4层一起使用#阻挡层 热氧化方法制备的 SiO 2是无定形制备二氧化硅的方法:热分解淀积法、溅射法、真空蒸发法、阳极氧化法、化学气相淀积法、热氧化法;热氧化法制备的 SiO 2具有很高的重复性和化学稳定性,其物理性质和化学性质不太受湿度和中 等热处理温度的影响。
SiO 2的主要性质: 密度:表征致密程度 折射率:表征光学性质密度较大的SiO 2具有较大的折射率 、 波长为5500A 左右时,SiO 2的折射率约为1.46电阻率:与制备方法及所含杂质数量等因素有关,高温干氧氧化制备的电阻率达 1016 Q介电强度:单位厚度的绝缘材料所能承受的击穿电压大小与致密程度、均匀性、杂质含量有关一般为106〜10?V/cm (10 1〜1V/nm )S介电常数:表征电容性能C 二;SQ — ( SiO 2的相对介电常数为 3.9)2d腐蚀:化学性质非常稳定,只与氢氟酸发生反应SiO 2 4HF > SiF 4 2出0SiF 4 2HF > H 2(SiF 6)… 六氟硅酸 还可与强碱缓慢反应SiO 2 6HF > 出儕6)2出。
薄膜应力为压应力晶体和无定形的区别:桥键氧和非桥键氧 桥联氧:与两个相邻的Si-O 四面体中心的硅原子形成共价键的氧非桥联氧:只与一个 Si-O 四面体中心的硅原子形成共价键的氧非桥联氧越多,无定型的程度越大,无序程度越大,密度越小,折射率越小 无定形SiO 2的强度:桥键氧数目与非桥键氧数目之比的函数 结晶态和无定形态区分一一非桥联氧是否存在cm杂质分类:网络形成者和网络改变者网络形成者:可以替代SiO2网络中硅的杂质,即能代替Si— O四面体中心的硅、并能与氧形成网络的杂质网络改变者:存在于 SiO2网络间隙中的杂质SiO2作为掩蔽层对硼、磷有效,对钠离子无效B、P、As等常用杂质的扩散系数小,SiO2对这类杂质可以起掩蔽作用Ga、某些碱金属(Na)的扩散系数大,SiO2对这类杂质就起不到掩蔽作用Si热氧化生长SiO2的计算:C si X二C SQ2X O无定形SiO2的分子密度:C SiO =2.2 1022/cm3硅晶体的原子密度:C Si=5.0 1022 /cm3干氧、水汽和湿氧。
实际生产采用干氧-湿氧-干氧的方式1、干氧氧化①氧化剂:干燥氧气②反应温度:900〜1200 °C干氧氧化制备的 SiO2的特点:①结构致密、干燥、均匀性和重复性好②与光刻胶粘附性好,掩蔽能力强。
③生长速度非常慢干氧氧化的应用:MOS晶体管的栅氧化层2、水汽氧化反应条件:①氧化剂:高纯水产生的蒸汽②反应温度:高温水汽氧化制备的 SiO2的特点:①SiO2生长速率快②结构粗糙3、湿氧氧化反应条件:氧化剂:高纯水(95 C左右)+氧气特点:①生长速率较高②SiO2结构略粗糙4、三种氧化法比较干氧氧化:结构致密但氧化速率极低湿氧氧化:氧化速率高但结构略粗糙,制备厚二氧化硅薄膜水汽氧化:结构粗糙不可取热氧化的过程(D-G模型)①氧化剂从气体内部以扩散形式穿过附面层运动到气体一SiO2界面,其流密度用F1表示。
流密度定义为单位时间通过单位面积的粒子数。
②氧化剂以扩散方式穿过SiO2层(忽略漂移的影响),到达SiO2 — Si界面,其流密度用 F2表示。
L那心T,(.硅7-!潼玄农财谱豪寒馆■鑒轉AT■-硅表面附近的杂质浓度比体内还要低。
Ga 镓就属于这种类型的杂质。
Si-SiO 2界面存在四种电荷 Si- SiO 2界面电荷类型: 可动离子电荷 界面陷阱电荷 氧化层固定电荷 氧化层陷阱电荷 第3章扩散 扩散机构:间隙式和替位式 1、间隙式扩散:①定义:间隙式杂质从一个间隙位置到另一个间隙位置的运动③ 氧化剂在Si 表面与Si 反应生成SiO 2,其流密度用F 3表示。
④ 反应的副产物离开界面。
D-G 模型适用氧化层厚度:30nm 热氧化存在两种极限情况 当氧化剂在SiO2中的扩散系数 D SiO 很小时D SQ 2定:k s x 0,则G —• 0, C 。
一; C °在这种 极限情况下,SiO 2的生长速率主要由氧化剂在 SiO 2中的扩散速度所决定,故称这种极限情况为扩散控制。
当氧化剂在SiO 2中的扩散系数 D SQ 很大,则C ^C ^C / 1 k s /h 。
在这种极限情况下,SiO 2生长速率由Si 表面的化学反应速度控制,故称这种极限情况为反应控制 决定氧化速率常数的因素:氧化剂分压、氧化温度 1、氧化剂分压P g 通过C ”对B 产生影响,B 与P g 成正比关系 2、氧化温度温度对抛物型速率常数B 的影响是通过影响 D SiO 产生的,B 三2D SiOC / N 1温度对线性速率常数 B / A 的影响是通过影响 k s 产生的 分凝系数,图2.21分凝系数:掺有杂质的硅在热氧化过程中,在Si — SiO 2界面上的平衡杂质浓度之比(a)当m ::: 1,在SiO 2中是慢扩散的杂质,也就是说在分凝过程中杂质通过 SiO 2表面损失的很少,硼就属于这类。
再分布之后靠近界面处的 SiO 2中的杂质浓度比硅中高,硅表面附近的浓度下降。
(b)当m ::: 1,在SiO 2中是快扩散的杂质。
因为大量的杂质通过SiO 2表面跑到气体中去,杂质损失非常厉害,使 SiO 2中杂质浓度比较低,硅表面的杂质浓度几乎降到零。
H 2气氛中的B 就属于这种情况。
(c) 当m 1,在SiO 2中是慢扩散的杂质,再分布之后硅表面的浓度升高 质。
(d) 当m 1,在SiO 2中是快扩散的杂质,分凝过程中杂质通过P 磷就属于这种杂SiO 2表面损失的厉害,最终使cjij-i咖!② 杂质:Na 、K 、Fe 、Cu 、Au 等元素 ③ 间隙杂质在间隙位置上的势能相对极小, 相邻两间隙位置之间, 对间隙杂质来说是势能极大位置。
势垒高度:W i =0.6~1.2eV④ 主要与晶格结构与晶向有关,原子密度越大,间隙越小,⑤运动条件:E W i 跳跃率:R =v 0e "i/kT2、替位式扩散:① 定义:替位式杂质从一个替位位置到另一个替位位置的运动 (a) 直接交换 (b) 空位交换(主要) ② 杂质:III 、丫族元素③ 对替位杂质来说,在晶格位置上势能相对最低,而间隙处是势能最高位置。
势垒高度:W s④ 运动条件:E W s ,平衡时单位体积的空位数为n = Ne _Wv/kT , 每个格点上岀现空位的几率为n / N = e 现/kT ,扩散方式:恒定表面源和有限表面源(定义和杂质分布形式) 1、恒定表面源扩散① 定义:在整个扩散过程中,硅片表面的杂质浓度始终不变的扩散② 边界条件和初始条件: ③ 恒定表面源扩散的杂质分布: ④ 杂质分布形式特点:在表面浓度C s 一定的情况下,扩散时间越长,杂质扩散的就越深,扩到硅内的杂质数量也就越多。
Qt = C(x,t)dx =2C s Dt、&扩到硅内的杂质数量可用高为C s ,底为2、Dt 的三角形近似;表面浓度C s 由杂质在扩散温度下的固溶度所决定。
而在900 ~1200 C 内,固溶度变化不大,可见很难通过改变温度来控制 C s2、有限表面源扩散① 定义:扩散之前在硅片表面淀积一层杂质, 在整个扩散过程中这层杂质作为扩散的杂质源, 不再有新源补充W i 就越大有耿涵旷恆的枭质井帀形兀②初始条件和边界条件:③杂质分布形式特点:当扩散温度相同时,扩散时间越长,杂质扩散的就越深,表面浓度就越低。
当扩散时间相同时,扩散温度越高,杂质扩散的就越深,表面浓度下降的也就越多 扩散过程中杂质量不变实际生产中采用两步扩散(每一步的扩散方式及作用) 两步扩散:① 预扩散:在低温下采用恒定表面源扩散方式,控制扩散杂质的数量 ② 主扩散将由预扩散引入的杂质作为扩散源, 在较高温度下进行扩散。
控制表面浓度和扩散深度③ 分布形式:影响杂质分布的因素:横向扩散 第4章离子注入 离子注入:最主要的掺杂工艺①离子注入是一种将带电的且具有能量的粒子注入衬底硅的过程,注入能量介于1KeV 到1MeV 之间,注入深度平均可达 10nm ~10」m 。
离子剂量变动范围,从用于阈值电压调整的1012/cm 2到形成绝缘埋层的1018/cm 2。
相对于扩散,它能更准确地控制杂质掺杂、可重复性LSS 理论:注入离子在靶内的分布理论LSS 理论认为,注入离子在靶内的能量损失分为两个彼此独立的过程:核碰撞(核阻止)和电子 碰撞(电子阻止)不同能区的能量损失形式 低能区:以核碰撞为主 中能区:核碰撞、电子碰撞持平 高能区:以电子碰撞为主 注入离子在无定形靶中的分布计算相同质量且相同初时能量的离子在靶中有一定的空间分布,投影射程的统计涨落称为投影偏差''R p ,沿着入射轴垂直方向上的统计涨落,称为横向偏差纵向分布:一级近似下用高斯函数表示:横向分布:高斯分布;横向渗透远小于热扩散 沟道效应及避免的方法 ① 定义:当离子注入的方向与靶晶体的某个晶向平行时,一些离子将沿沟道运动。
沟道离子唯一的能量损失机制是电子阻止,因此注入离子的能量损失率就很低,故注入深度较大。
和较低的工艺温度。
离子注入已成为 VLSI 需要6~12个或更多的离子注入步骤。
②应用:隔离工序中防止寄生沟道用的沟道截断调整阈值电压用的沟道掺杂CMOS 阱的形成 浅结的制备离子注入的特点 优点:注入的离子纯度高 可以精确控制掺杂原子数目 温度低:小于400 C 掺杂深度可控非平衡过程,杂质含量不受固溶度限制 低温注入,避免高温扩散所引起的热缺陷 横向扩散效应比热扩散小得多离子通过硅表面的薄膜注入止污染 可以对化合物半导体进行掺杂 缺点: 产生的晶格损伤不易消[除 …一 很难进行很深或很浅的'结的注入 高剂量注入时产率低 设备价格昂贵(约 200万美金)制程上最主要的掺杂技术。
一般 CMOS 制程,大约R_。
② 避免方法:a. 倾斜样品表面,晶体的主轴方向偏离注入方向,典型值为 7°。
b. 先重轰击晶格表面,形成无定型层在无定形靶运动的离子由于碰撞方向不断改变,因而也会有部分离子进入沟道,但在沟道 运动过程中又有可能脱离沟道,故对注入离子峰值附近的分布并不会产生实质性的影响 c. 表面长二氧化硅薄层 注入离子造成的损伤 ① 级联碰撞 ② 简单晶格损伤孤立的点缺陷或缺陷群(注入离子每次传递给硅原子的能量约等于移位阈能) 局部的非晶区域(单位体积的移位原子数目接近半导体的原子密度) ③ 非晶层注入离子引起损伤的积累 热退火① 定义:又叫热处理,集成电路工艺中所有的在氮气等不活泼气氛中进行的热处理过程都可以称 为退火 ② 作用激活杂质:使不在晶格位置上的离子运动到晶格位置,以便具有电活性, 杂质的作用 消除损伤 ③ 退火方式: 炉退火快速退火:脉冲激光法、扫描电子束、连续波激光、非相干宽带频光源 墨加热器、红外设备等) ④ 快速热退火 a. 传统热退火的缺点不能完全消除缺陷,产生二次缺陷 高剂量注入时的电激活率不够高 高温长时间热退火会导致明显的杂质再分布 b. 快速退火技术在氮气或惰性气体的气氛下,极短的时间内,把晶片温度提高到 C.快速热退火作用:消除由注入所产生的晶格损伤 恢复材料少子寿命和载流子迁移率 杂质激活 第5章物理气相淀积 两种基本方法① 物理气相淀积定义:利用某种物理过程,例如蒸发或者溅射现象实现物质的转移, 子由源转移到衬底表面上,并淀积成薄膜。