总布置中后轮跳动校核
传动轴跳动校核规范03.108.ok

上海同*同*科技有限公司企业标准TJI/YJY·03·108-2005传动轴跳动校核规范2005-08-10 发布2005-08-16 实施上海同*同*科技有限公司发布TJI/YJY·03·108-2005前言为使总布置在进行传动轴跳动校核时,做到校核内容全面、正确,格式规范、统一,便于管理和检查评审,特制定本标准。
本标准中的各项要求,既是工程技术人员在进行传动轴跳动校核时,应该达到技术要求;又是检查评审传动轴跳动校核报告的依据。
本标准于2005年8月16日实施。
本标准的附录A为规范性附录。
本标准由上海同*同*科技有限公司提出。
本标准由上海同*同*科技有限公司质量与项目管理中心负责归口管理。
本标准主要起草人:李**TJI/YJY·03·108-2005传动轴跳动校核规范1范围本标准规定了传动轴跳动校核报告的格式及内容。
本标准适用于传动轴新产品开发设计及改型设计。
2规范性引用文件QC/T 3-92 汽车产品图样及设计完整性3术语和定义无4要求4.1 传动轴跳动校核报告格式见规范性附录A4. 2传动轴跳动校核报告应包括封面、目录、正文、参考文献四个部分4. 3传动轴跳动校核报告应包含的校核内容4.3.1上下跳动极限4.3.2上下跳动极限位置夹角附录 A (规范性附录)目录一、校核目的 (3)二、概述 (3)三、校核 (3)1、等速传动校核 (3)2、传动轴上下跳动的极限位置及工作夹角校核 (4)四、总结 (7)参考文献 (8)一校核目的1.传动轴上下跳动的极限位置及最大摆角;2.设计工况下,万向节传动的夹角是否满足等速传动;3.传动轴花键连接处的伸缩量,检查传动轴花键是否可能脱开或顶死;二概述XS6450车用传动轴属于十字轴万向节式传动轴,具体结构为后驱、两段式、3万向节的十字轴式传动轴(如图1所示)。
结构设计时需保证万向节叉在同一平面内,万向节两两互成90º,同时满足转角关系式:cosα1* cosα2=cosα3 (1)其中tanαi=√(tanαz)2+ (tanαf)2 (2)其中:αi:某万向节计算夹角;αz:αi对应主视图万向节夹角;αf:αi对应俯视图万向节夹角;图1三校核1等速传动校核根据数模和公式(2)由表1得出设计工况下各实际万向节夹角αi。
后轮偏摆分析
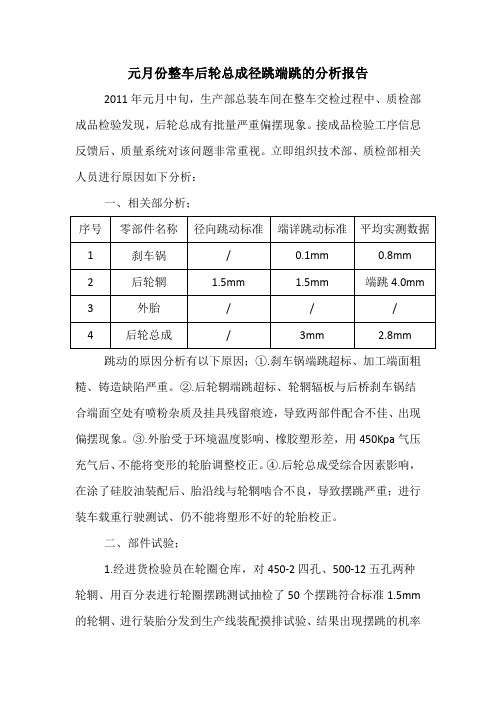
元月份整车后轮总成径跳端跳的分析报告2011年元月中旬,生产部总装车间在整车交检过程中、质检部成品检验发现,后轮总成有批量严重偏摆现象。
接成品检验工序信息反馈后、质量系统对该问题非常重视。
立即组织技术部、质检部相关人员进行原因如下分析:一、相关部分析;跳动的原因分析有以下原因;①.刹车锅端跳超标、加工端面粗糙、铸造缺陷严重。
②.后轮辋端跳超标、轮辋辐板与后桥刹车锅结合端面空处有喷粉杂质及挂具残留痕迹,导致两部件配合不佳、出现偏摆现象。
③.外胎受于环境温度影响、橡胶塑形差,用450Kpa气压充气后、不能将变形的轮胎调整校正。
④.后轮总成受综合因素影响,在涂了硅胶油装配后、胎沿线与轮辋啮合不良,导致摆跳严重;进行装车载重行驶测试、仍不能将塑形不好的轮胎校正。
二、部件试验;1.经进货检验员在轮圈仓库,对450-2四孔、500-12五孔两种轮辋、用百分表进行轮圈摆跳测试抽检了50个摆跳符合标准1.5mm 的轮辋、进行装胎分发到生产线装配摸排试验、结果出现摆跳的机率明显下降。
2.对重庆九龙、山东东岳、江苏正新三厂家的轮胎各抽取了50个,分别进行装配装车检验测试、都有摆动跳动现象,但重庆九龙轮胎端向跳动现象的比例据首位(占25%)、东岳轮胎径向跳动比例居次位(占20%),正新轮胎跳动现象占据末位(占10%)。
三、零部件控制方案及整改建议;1.加大对零部件的抽查检验力度、严格控制轮辋、后桥配件(刹车锅)以及轮胎产品质量;2.在产品装配时、环境如低于零摄氏度时,一定要关注轮胎的变形及橡胶塑形的状况。
另及时反馈此信息至供应部、有供应部协调轮胎厂家解决次质量问题。
3.严格控制后桥刹车锅径跳、端跳、端面的加工精度以及其它相关技术要求,有效控制该配件的使用性能。
4.严格管控装配过程、关注装配后的轮胎总成使用状况、强调成品检验工序严把关、严控控制、杜绝该现象重复出现。
另:对此次问题进行分析的相关数据见附页。
质量检验部2011-2-11。
整车设计的运动校核

固定节角度 35.5° 38.5° 40.2° 38° 38.6° 35.7° 38° 40.4°
移动节角度 11.75° 13.12° 10.96° 10.1° 13.6° 12.17° 10.45° 11.35°
(4)后桥中间传动轴
校核要求:
满载布置角度不大于6° 上跳,下跳角度不大于15°
中间传动轴的角度校核
挠性万向节布置角度不能大于5度的要求。
后传动轴跳动示意图
上跳极限
下跳极限 下跳极限
满载时后传动轴位置:
1.181°
1.441°
后传动轴上跳极限
后传动轴下跳极限
后传动轴校核输出
后传动轴十字万 向节夹角(分动 器端) 汽车静止满载 行驶中极 上极限 限夹角 下极限 1.181º 1.596º 6.16º 后传动轴十字万 向节夹角(后桥 端) 1.441º 1.545º 2.076º 15º 十字万向节夹 角α 不大于
转向拉杆与横向稳定杆最小间距28.5mm
与横向稳定杆间最小间隙(mm) 转向拉杆状态 左转 右转 企业标准推荐 值(mm)
跳动上极限
28
33
≥10
跳动下极限
12
51
≥10
转向拉杆与摆臂最小间距 108 mm
与摆臂间最小间隙(mm) 转向拉杆状态 左转 跳动上极限 跳动下极限 108 56 右转 77 86
6)发动机运转时对部件动态间隙
1)车轮跳动与轮罩的间隙校核
输入条件: 前轮: 独立悬挂上跳至缓冲块压缩2/3 左右转向轮按规定转至最大角度 后轮:独立悬挂上跳至缓冲块压缩2/3 非独立悬挂上跳至缓冲块压缩1/2 输出要求: 最小间隙大于15 mm,满足安装防滑链(驱动 轮)
董伟佳-轮跳仿真校核及轮罩校核

车辆类型 普通轿车
城市型SUV 越野型SUV及
皮卡
工况
工况一 工况二 工况三 工况四 工况一 工况二 工况三 工况四 工况一 工况二 工况三
车轮行程(每10%一个跨度)
80%—100%上跳 70%上跳
60%上跳—60%下跳 70%下跳—100下跳
90%—100%上跳 80%上跳
70%上跳—70%下跳 80%下跳—100下跳
a、在车轮中心向前30°和向后50°的两个辐射平面所形成的区域内(见图5-2-1),护轮板 的宽度q必须足以遮盖整个轮胎的宽度。如属双胎,则应遮盖两个轮胎的安装总宽度。
第10页/共27页
b、护轮板的后缘应位于车轮中心 上方150mm的水平面以下。而且护轮 板的边缘与这个平面的交点(图中 的A点)必须位于轮胎纵向中心平面 的外侧。如属双胎,则必须位于外 侧轮胎的纵向中心平面的外侧。
间隙变化曲线生成过程
某工况下前轮胎与转向拉杆的间隙变化图
第9页/共27页
➢ 护轮板设计技术要求 1 汽车必须装有护轮板。 2 护轮板应该能够保护其他道路使用者尽可能地不受到汽车车轮甩出的石子、泥沙、冰雪及水 等的袭击;并减小其他道路使用者由于接触运动的车轮而产生的危险。 3 护轮板必须安装牢靠。若护轮板由几部分组成,则装配后各独立零部件之间不允许有空隙。 4 在水平路面上,当汽车处于整备状态,车轮在直线行驶位置时,护轮板应满足下列要求:
度测量位置相对应),图纸最大行程如图1所示;减震器数模最大行程如图2所示。
图1、图纸最大行程
图2、数模最大行程
校核各位置轮胎包络与周边件间隙 输出校核报告
第5页/共27页
五、校核步骤
依据GB 7063-2011 《汽车护轮板》要求:汽车制造厂应把汽车设计成至少一种型 式的防滑链适用于该车驱动轮的一种形式的车轮和轮胎。根据3C 认证的需要, 企业 应申报一种轮胎与防滑链的组合, 所以在包络校核的过程中把防滑链的空间安装尺寸 考虑在内,国内常规雪链是全包型的, 厚度大约12mm。经验要求车轮包络与周边最小 间隙不小于10 mm,因此设计时在考虑防滑链的前提下车轮包络间隙最少为22 mm。基 于以往设计经验,表1中内容为前轮包络设计要求。
工程车制动时后轮跳动解决方案

工程车制动时后轮跳动解决方案摘要:通过对工程车空车制动时后轮跳动的原因分析,从理论及实践上找出此类问题产生的根本原因,让设计工程师工作中遇到类似问题时能迅速找到根本问题所在并解决。
关键词:工程车后轮跳动同步附着系数变形1 引言工程车在空车制动过程中经常会出现后轮跳动,引起驾驶室震动造成平顺性很差,而载货物后又没有后轮轮跳动情况,一些主机厂设计师通过很多方法如调整制动蹄片间隙,换制动阀等方法均不能解决问题而束手无策,下面通过笔者工作中一个车型出现同样问题后的解决过程,理论及实践相结合为该问题提出解决方案。
2 3052PER14100Q33-1是福田公司长沙汽车厂生产的工程车车型,轴距3300mm,前桥为1050桥,制动器φ310×80,后桥1080桥,后制动器改为φ320×95,悬架是前1061后140(表1)3 现象20km/h以上各速度紧急制动时驾驶室跳动。
4 初期已采取的措施及效果①将前桥制动间隙调大至无刹车,不能解决;②考虑到可能是前板簧刚度大,制动时引起的振动频率高,将前悬架板簧改复合刚度(空载时刚度减小,满载时满足刚度要求),没有解决问题;③考虑到可能是后桥质量问题,换了后桥及贮能气室后仍不能解决;④将后桥制动间隙调大,至无刹车,才不跳动;另行车制动时从侧面观测,驾驶室跳动系后轮跳动致。
5 原因初步分析在制动过程中,制动强度等于整车的同步附着系数时,路面的附着效率最高,前后轮同时抱死,此时整车的制动减速度最大。
由于许多因素影响,如:前后轴载荷的变化、路面状况的变化等因素影响,整车不可能达到理想状态。
该车在空载状态下制动时,后轮有连续跳动现象,初步分析有以下几方面影响(见图1)。
6 进一步分析6.1 后板簧(主片)刚度不足板簧主片刚度不足,整车制动时,板簧易产生S变形,易造成整车振动,可根据实际情况,把主簧第二片前吊耳处增加一卷耳(见图2), 这样相应增加了后板簧主片的刚度。
工程车制动时后轮跳动解决方案

Sci ce en an d Tethn o i nova i Her l ol gy n t on ad
工 程 车 制 动 时 后 轮 跳 动 解 决 方 案
程小建 符青 萍 ( 北汽 福 田长 沙汽 车厂技术 中心 湖南长 沙
工 程技术
4 1 9 1 ) 02
④将 后 桥 制 动 间 隙 调 大 , 无 刹车 , 至 才
后 轮跳动 , 引起 驾 驶 室 震 动 造 成 平 顺 性 很 不 跳 动 ; 差 , 载 货 物 后 叉 没 有后 轮 轮 跳 动 情 况 , 而 一 另行 车 制 动 时 从 侧 面 观 测 , 驶 室 跳 驾
F 制 动 时 , 面 产 生 的 制 动 力 一 地 R一 车 轮 的 滚 动 半 径 后 车 轮 滚 动半 径R增 大 , 相 同 制 动 力 在 的情况下, 簧受力矩增大, 板 产生 变 形 量 越
在 空 载 状 态 下 , 车 的 同 步 附 着 系 数 整
如 太 小 几乎 接 近 干 o, 轮 抱死 的 滞 后 时 间 前
能解决 ;
② 考 虑 到 可 能 是 前 板 簧 刚 度 大 , 动 但 经试 验 实 际 效 果 不 明 显 ; 以 可 以 考 虑 较 长 , 载 状 态 , 车 的 同 步 附 着 系 数 增 制 所 满 整
时 引起 的 振 动 频 率 高 , 前 悬 架 板 簧 改 复 将
要 求 ) 没有 解 决 问题 ; , ③考虑到 可能是 后桥 质量问题 , 了 换
将板 簧 剐 度 整 体 进 行 加 强 ( 满 足 前后 悬 加 , 步 附着 系数 增 加 , 轮 制 动 的 滞后 时 在 同 前
明 显 。 因整 车 配 置 所 需 , 5 - 很 多 方 法 如调 整 制 动 动 系后 轮 跳 动致 。 蹄 片 间 隙 , 制 动 阀等 方 法 均 不 能 解 决 问 换 题 而 束 手 无 策 , 面 通 过 笔 者 工 作 中 一 个 5原因初步分析 下 车 型 出 现 同 样 问题 后 的 解 决 过 程 , 论 及 理 实践相 结合为该问题提出解决方案 。
车轮跳动与轮罩设计校核

1货车后轮跳动量 . 根据悬架 的刚度和挠度的相关计算 ,货车后悬架 动挠度 为3 . r ,即后轮从设计状态 ( 79 m a 满载 )向上 的
置关系图。轮胎与轮 罩之问的最 小距离为1. m 。 9 7m
根据转 向器 的相关结构参数 ,货车 的内外轮转 向
角分 别 为3 。 7 。 7 、2。
在计算前轮上跳量时 ,由数模得 出前悬架限位块 在满载状态与纵 梁的距离 ,橡 胶 限位块按 照压缩 1 2 /
计 算 ,根 据 以上 数 据 ,得 出 货 车 前 轮 上跳 最 大行 程 为
2 0第 期 总 9 ) 0 年 3 (第 1 1 期
中目 观代欺甫 备 装
车轮跳动与轮罩设计校核
马红荣
威海职 业学院
摘
山东威 海
24 0 629
要 :本 文 通 过 介 绍 某 型 货 车 前 、 后 轮 跳 动 与轮 罩 设 计 的 校 核 , 总 结 了 车 轮 跳 动 与 轮 罩 设 计 校 核 项 目。
最 大跳 动 量 为 3 .r ,从 设 计状 态 到下 极 限的跳 动 量 79 m a 为 5. m 。 6 5m 2 货 车 后轮 跳 动 包络 图 . 货 车后 轮 跳 动包 络 体 ( 图4 示 ) 。 如 所 ‘ 根 据 以 上数 据 ,在 三 维 软 件 中 作 出的 包络 体 就是
一
图1 货车前轮 胎 包络 图 3 前 轮包 络 与 轮 罩 上部 的间 隙校 核 . 根 据轮 胎 包 络 图 ,就 可 以进 行轮 罩 的相关 设 计 。 图2 货 车 轮 胎 在 极 限位 置 时 与 轮 罩 等 的空 间位 是
汽车总布置设计指南(轮胎布置校核)

版本:01
6、轮胎型号及尺寸的确认 6.1、确定车型所选用的轮胎型号 6.2、进行轮胎运动校核时,所选用的轮胎数模必须是厂家提供的该型号轮胎的 标准尺寸数模。 6.3、若某个车型配置有多个可选轮胎型号,需对每个轮胎的断面宽度和外直径 进行对比分析,选择最大尺寸的轮胎进行轮胎包络校核。 7、校核中对防滑链的要求 7.1、驱动轮必须配备防滑链,非驱动轮可不配备防滑链 7.2、防滑链的厚度H按12mm计算,若车型明确选定了某厂家提供的防滑链,则按 该厂家提供的尺寸进行校核。 8、轮胎运动范围 8.1、转向轮:转向轮运动时,配备防滑链与不配备防滑链的运动条件设置不同, 需分别进行校核。
图1
图2
第 1页 共4页
版本:01
3.10、径向间隙:胎冠与周边零部件间隙。 3.11、侧面间隙:胎肩及胎侧与周边零部件间隙。 3,12、面接触:面接触指可能存在的干涉是周边零部件的面型结构(如轮罩表面、 纵梁侧面等)与轮胎产生干涉,这种干涉不会对轮胎造成致命损坏,不会对行驶 安全性造成严重影响。 3.13、边接触:边接触指可能存在的干涉是周边零部件的边型结构(如纵梁翻边、 侧围翻边等)与轮胎产生干涉,这种干涉会导致轮胎被划破、割裂或刺穿等,会 对轮胎造成致命损坏,会对行驶安全性造成严重影响。 3.14、标准尺寸数模:与GB/T2978中提及的新胎尺寸一致的轮胎数模。 4、轮胎与周边零部件的关系:车辆行驶过程中,轮胎存在前后旋转、转向及遇 到路面不平而产生的跳动等多种运动状态,轮胎在运动过程中,周边存在两种状 态零部件,在校核时需要区别对待。 4.1、轮胎运动时,随轮胎一起运动的零部件:这些零部件通常是随着轮胎一起 运动的零部件,包括摆臂、减振器、转向横拉杆等。由于这些件无法通过运动包络 校核间隙关系,因此需要动态地分析与车轮的间隙。 4.2、轮胎运动时,不随轮胎一起运动的零部件:这些零部件通常不随轮胎运动 而运动,主要是车身件或安装固定在车身上的零部件,包括副车架、纵梁、保 险杠、轮罩装饰件等。这些件与轮胎的运动间隙关系可以通过测量与轮胎运动包 络的间隙获得。 5、校核过程
- 1、下载文档前请自行甄别文档内容的完整性,平台不提供额外的编辑、内容补充、找答案等附加服务。
- 2、"仅部分预览"的文档,不可在线预览部分如存在完整性等问题,可反馈申请退款(可完整预览的文档不适用该条件!)。
- 3、如文档侵犯您的权益,请联系客服反馈,我们会尽快为您处理(人工客服工作时间:9:00-18:30)。
浅谈总布置中后轮跳动空间的校核
北汽福田技术研究院汽车二所张所滨
主题词:后轮跳动空间校核
一、概述
在卡车类产品的开发过程中,卡车货箱的高度直接影响使用的方便性及车辆的侧向稳定性。
在进行总布置设计时,当后悬架的高度初步确定,车架纵梁断面已定的情况下,应确定出车箱高度,这是确定整车尺寸参数的重要内容之一。
如果一辆卡车采用的是平底货箱,车轮跳动位置的高低直接决定其货箱的高度,因此后轮跳动空间的校核,是卡车类车辆总布置设计中尤为重要的一个环节。
下面介绍两种校核卡车后轮跳动空间的方法。
二、货箱上校核部位的选取
1.对于车轮较宽、轮胎处于货箱底板边纵梁正下方的卡车,一般选取货箱底架边纵梁进行校核;
2.对于车轮处在边纵梁内,但在后轮正上方有底架横梁的卡车,一般选取货箱底架横梁进行校核,
3.对于车轮外宽较窄,且在车轮正上方没有货箱横梁的卡车,一般选取货箱底板的瓦棱板下表面进行校核。
对于采用平底货箱的卡车而言,由于可以不再考虑货箱横梁的底面,而改用货箱底板的瓦棱板下表面作为校核表面,这时可为车轮上跳提供最大的空间,即允许将车箱高度适当降低,节省高度,增加货物装卸的方便性和行驶的稳定性,因而这是我们目前用得最多的情况。
三、后轮跳动空间的校核
在后轮跳动的整个过程中,最危险的工作状况是车轮上跳至铁碰铁状态后再侧倾,即所谓的斜跳状态。
下面通过两种
方法,对斜跳状态进行
校核。
1.按侧倾
6°校核(见图1)
①.在主视图上画
出板簧设计状态(压
平)时的车架纵梁断
面、缓冲块、缓冲块内
部骨架、后桥、板簧总
成、车轮这些底盘件的
初始位置。
②.按初步给出的
高度画出货箱底板及
底架边纵梁的位置。
③.连接左右板簧
主片中心A、B两点,与汽车中心线交于C点,则C点为汽车的侧倾中心。
④.过右侧缓冲块骨架中点D,向左作一下倾6°的斜线
⑤.过C点作6°斜线的垂线,与之交于E点
⑥.重绘一后桥(带车轮),作出其桥上平面中点E’点
⑦.将新桥旋转6°,使其与斜线平行。
⑧.使E’与E点重合,将新桥移至校核图上,此即为后桥斜跳的位置。
⑨.标出各种间隙值。
2.按一侧铁碰铁,另一侧下沉25m m进行校核(见图2)
①、②、③同前,
④.延长左侧缓冲块中心线,与桥上平面线交于F点,继续向下延长至点G,使FG=25mm,在右侧缓冲块骨架
下表面中点取一
点D,连接DG
得一斜线;
⑤.过C点
作DG的垂线,
与之交于E点;
⑥.重绘一
后桥(带车轮),
作出其桥上平面
中点E’点;
⑦.测出DG
的角度,并将新
桥旋至相同的角
度。
⑧、⑨同前。
3.两种方法的特点及注意事项
1.两种方法的侧倾程度不同,前者偏小,仅为6°,后者偏大,约为7-10°。
2.两种方法中,均有一侧悬架处于铁碰铁状态,属实际中很少出现的情况,将此工作状态确定为校核状态,具有较高的安全保证。
3.方法一应用于板簧较硬的车型,如卡车;方法二应用于板簧较软的车型,如轿车等乘用车。
4.两种方法的许用间隙取值不同,如方法一中,车轮与货箱底板的间隙可取为10-15mm;方法二中,此间隙则可减小至0甚至负间隙,在吉普车上曾取为-50 mm。
4.结束语
以上分别从校核的用途、相关参照物的选取、跳动位置的确定及其特点,对卡车总布置中后轮跳动空间的校核进行了说明。
其中一些经验数据的确定,因车型而异。
这方面还有待于我们在不断的实践中不断积累和完善。
■
作者简介:
张所滨同志1987年毕业于辽宁工学院汽车专业。
曾在丹东汽车制造厂从事大客车设计工作,1996年,设计完成的DD6991型客车获辽宁省科技进步奖,1998年晋升为高级工程师。
1999年初进入福田技术研究院,主要从事轻卡、客车和重型卡车的车型设计工作。