常温单轴拉伸实验、压缩实验、扭转实验
常温单轴拉伸实验、压缩实验、扭转实验
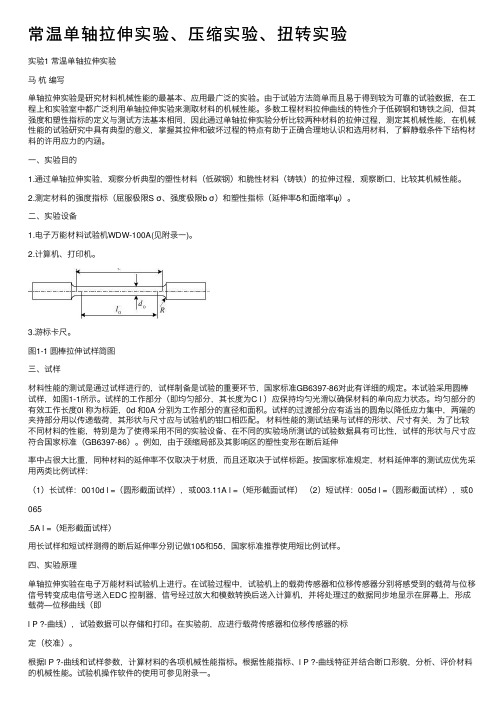
常温单轴拉伸实验、压缩实验、扭转实验实验1 常温单轴拉伸实验马杭编写单轴拉伸实验是研究材料机械性能的最基本、应⽤最⼴泛的实验。
由于试验⽅法简单⽽且易于得到较为可靠的试验数据,在⼯程上和实验室中都⼴泛利⽤单轴拉伸实验来测取材料的机械性能。
多数⼯程材料拉伸曲线的特性介于低碳钢和铸铁之间,但其强度和塑性指标的定义与测试⽅法基本相同,因此通过单轴拉伸实验分析⽐较两种材料的拉伸过程,测定其机械性能,在机械性能的试验研究中具有典型的意义,掌握其拉伸和破坏过程的特点有助于正确合理地认识和选⽤材料,了解静载条件下结构材料的许⽤应⼒的内涵。
⼀、实验⽬的1.通过单轴拉伸实验,观察分析典型的塑性材料(低碳钢)和脆性材料(铸铁)的拉伸过程,观察断⼝,⽐较其机械性能。
2.测定材料的强度指标(屈服极限S σ、强度极限b σ)和塑性指标(延伸率δ和⾯缩率ψ)。
⼆、实验设备1.电⼦万能材料试验机WDW-100A(见附录⼀)。
2.计算机、打印机。
3.游标卡尺。
图1-1 圆棒拉伸试样简图三、试样材料性能的测试是通过试样进⾏的,试样制备是试验的重要环节,国家标准GB6397-86对此有详细的规定。
本试验采⽤圆棒试样,如图1-1所⽰。
试样的⼯作部分(即均匀部分,其长度为C l )应保持均匀光滑以确保材料的单向应⼒状态。
均匀部分的有效⼯作长度0l 称为标距,0d 和0A 分别为⼯作部分的直径和⾯积。
试样的过渡部分应有适当的圆⾓以降低应⼒集中,两端的夹持部分⽤以传递载荷,其形状与尺⼨应与试验机的钳⼝相匹配。
材料性能的测试结果与试样的形状、尺⼨有关,为了⽐较不同材料的性能,特别是为了使得采⽤不同的实验设备、在不同的实验场所测试的试验数据具有可⽐性,试样的形状与尺⼨应符合国家标准(GB6397-86)。
例如,由于颈缩局部及其影响区的塑性变形在断后延伸率中占很⼤⽐重,同种材料的延伸率不仅取决于材质,⽽且还取决于试样标距。
按国家标准规定,材料延伸率的测试应优先采⽤两类⽐例试样:(1)长试样:0010d l =(圆形截⾯试样),或003.11A l =(矩形截⾯试样)(2)短试样:005d l =(圆形截⾯试样),或0065.5A l =(矩形截⾯试样)⽤长试样和短试样测得的断后延伸率分别记做10δ和5δ,国家标准推荐使⽤短⽐例试样。
单轴拉伸实验报告
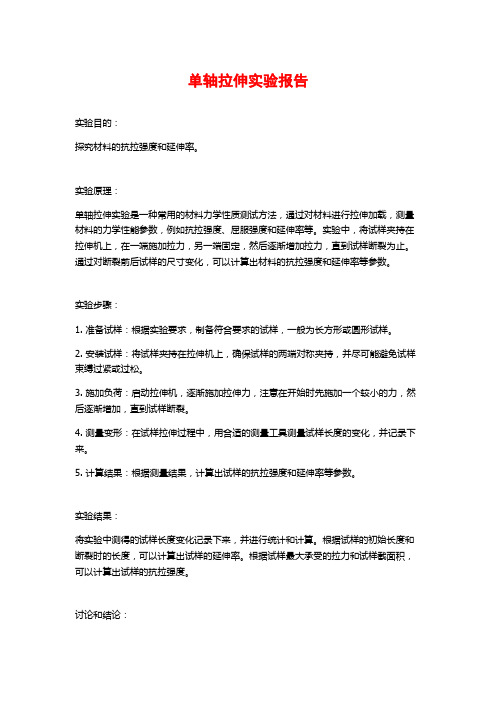
单轴拉伸实验报告实验目的:探究材料的抗拉强度和延伸率。
实验原理:单轴拉伸实验是一种常用的材料力学性质测试方法,通过对材料进行拉伸加载,测量材料的力学性能参数,例如抗拉强度、屈服强度和延伸率等。
实验中,将试样夹持在拉伸机上,在一端施加拉力,另一端固定,然后逐渐增加拉力,直到试样断裂为止。
通过对断裂前后试样的尺寸变化,可以计算出材料的抗拉强度和延伸率等参数。
实验步骤:1. 准备试样:根据实验要求,制备符合要求的试样,一般为长方形或圆形试样。
2. 安装试样:将试样夹持在拉伸机上,确保试样的两端对称夹持,并尽可能避免试样束缚过紧或过松。
3. 施加负荷:启动拉伸机,逐渐施加拉伸力,注意在开始时先施加一个较小的力,然后逐渐增加,直到试样断裂。
4. 测量变形:在试样拉伸过程中,用合适的测量工具测量试样长度的变化,并记录下来。
5. 计算结果:根据测量结果,计算出试样的抗拉强度和延伸率等参数。
实验结果:将实验中测得的试样长度变化记录下来,并进行统计和计算。
根据试样的初始长度和断裂时的长度,可以计算出试样的延伸率。
根据试样最大承受的拉力和试样截面积,可以计算出试样的抗拉强度。
讨论和结论:根据实验结果,可以分析材料的力学性能,例如材料的延伸性、强度等。
通过比较不同材料的实验结果,可以评估材料的质量和适用性,为相关工程应用提供依据。
安全注意事项:1. 实验过程中应注意操作规程,确保实验过程的安全。
2. 实验时应注意加强照明,以避免因疏忽而引起的意外事故。
3. 对于可能具有挥发性、腐蚀性或有毒性的材料,应采取相应的安全防护措施,如佩戴防护手套、眼镜等。
实验设备和试剂:1. 拉伸机:用于施加拉力和测量力学参数。
2. 试样:用于实验的材料样品。
3. 尺规:用于测量试样长度的变化。
实验结果记录表:试样编号初始长度(mm)断裂时长度(mm)抗拉强度(MPa)延伸率(%)12345备注:每个试样的实验结果都应进行独立记录和计算,并统计出平均值和标准偏差等参数。
拉伸和压缩实验.
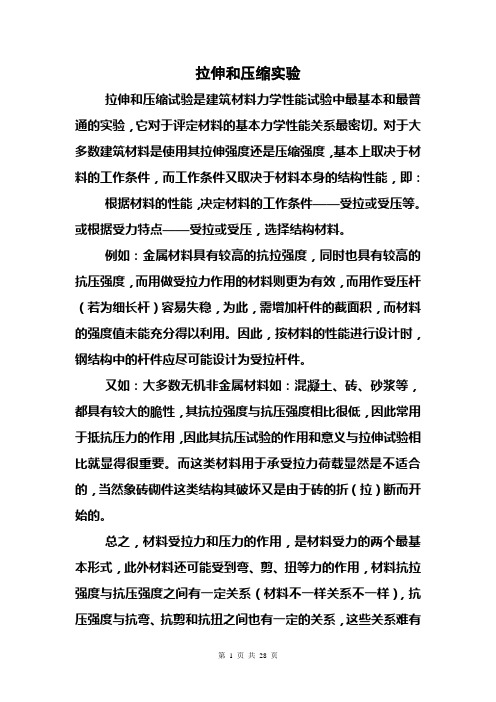
拉伸和压缩实验拉伸和压缩试验是建筑材料力学性能试验中最基本和最普通的实验,它对于评定材料的基本力学性能关系最密切。
对于大多数建筑材料是使用其拉伸强度还是压缩强度,基本上取决于材料的工作条件,而工作条件又取决于材料本身的结构性能,即:根据材料的性能,决定材料的工作条件——受拉或受压等。
或根据受力特点——受拉或受压,选择结构材料。
例如:金属材料具有较高的抗拉强度,同时也具有较高的抗压强度,而用做受拉力作用的材料则更为有效,而用作受压杆(若为细长杆)容易失稳,为此,需增加杆件的截面积,而材料的强度值未能充分得以利用。
因此,按材料的性能进行设计时,钢结构中的杆件应尽可能设计为受拉杆件。
又如:大多数无机非金属材料如:混凝土、砖、砂浆等,都具有较大的脆性,其抗拉强度与抗压强度相比很低,因此常用于抵抗压力的作用,因此其抗压试验的作用和意义与拉伸试验相比就显得很重要。
而这类材料用于承受拉力荷载显然是不适合的,当然象砖砌件这类结构其破坏又是由于砖的折(拉)断而开始的。
总之,材料受拉力和压力的作用,是材料受力的两个最基本形式,此外材料还可能受到弯、剪、扭等力的作用,材料抗拉强度与抗压强度之间有一定关系(材料不一样关系不一样),抗压强度与抗弯、抗剪和抗扭之间也有一定的关系,这些关系难有准确的表达式,而拉、压强度是材料使用得最为广泛的两个强度值。
(建筑结构中,柱墙主要承受压力,梁、板主要承受弯曲应力,屋架中的拉杆承受拉力)第一节拉伸实验一、对试件的要求(对试件总的要求是,对试验结果影响大的应消除)1、试件形式,有园柱形,如钢,平板形,如钢板等,8字形,如砂浆等,受拉截面一般为园形、正方形或长方形。
为了使断裂面发生在试件中长度的中部试件总是制成在长度中间的横截面小于两端的横截面,在这个断面上的应力不受夹具装置的影响。
2、试件的端部形状,应适合于试验材料本身的性能和试验机夹具装置。
可做成平滑的、阶梯形、螺纹形或锥形等。
端部的直径或宽度与中间偏袄截面直径或宽度之比与材料性能有关,如钢材为1.5:1,材料1.7—3.75:1,对脆性材料端部的制作特别重要,由于受夹具作用应力的影响,避免在端部破坏,应做得大一些。
拉伸 压缩 弯曲试验

拉伸压缩弯曲试验1. 简介拉伸、压缩和弯曲试验是材料力学中常用的实验方法,用于评估材料在不同加载条件下的性能和行为。
这些试验可以帮助工程师和科学家了解材料的强度、刚度和可靠性,并为设计和制造过程提供重要的参考数据。
本文将对拉伸、压缩和弯曲试验进行详细介绍,包括实验原理、设备及操作步骤,并探讨其在不同领域中的应用。
2. 拉伸试验2.1 实验原理拉伸试验是一种将材料加载到其断裂点之前的最大应力状态的实验。
通过施加均匀的拉力来延长材料,测量应力和应变之间的关系。
根据胡克定律,应力与应变成正比,即:σ=F Aε=ΔL L0其中,σ是应力(单位:Pa),F是施加到材料上的拉力(单位:N),A是横截面积(单位:m^2),ε是应变,ΔL是材料长度的变化量,L0是原始长度。
2.2 实验设备拉伸试验通常需要使用万能试验机。
该设备包括一个夹具,用于夹住材料样本,并施加拉力。
在实验过程中,通过加载单轴力来拉伸样本,同时测量应力和应变。
2.3 操作步骤以下是拉伸试验的一般操作步骤:1.准备样本:根据实验需求,制备符合标准尺寸要求的样本。
2.安装样本:将样本夹入夹具中,确保夹紧并正确对齐。
3.设置试验参数:根据材料类型和预期结果,设置加载速率、加载范围等参数。
4.开始试验:启动万能试验机,并开始施加拉力。
5.记录数据:随着加载的进行,记录应力和应变的数据,并绘制应力-应变曲线。
6.分析结果:根据实验数据分析材料的强度、刚度等性能指标。
3. 压缩试验3.1 实验原理压缩试验是一种将材料加载到其断裂点之前的最大压缩状态的实验。
通过施加均匀的压力来压缩材料,测量应力和应变之间的关系。
与拉伸试验类似,根据胡克定律,应力与应变成正比。
3.2 实验设备压缩试验通常需要使用万能试验机或压缩试验机。
该设备包括一个夹具,用于夹住材料样本,并施加压力。
在实验过程中,通过加载单轴力来压缩样本,同时测量应力和应变。
3.3 操作步骤以下是压缩试验的一般操作步骤:1.准备样本:根据实验需求,制备符合标准尺寸要求的样本。
实验一 拉伸与压缩实验

实验一 拉伸与压缩实验拉伸实验是对试件施加轴向拉力,以测定材料在常温静荷载作用下的力学性能的实验。
它是材料力学最基本、最重要的实验之一。
拉伸实验简单、直观、技术成熟、数据可比性强,它是最常用的实验手段。
由此测定的材料力学性能指标,成为考核材料的强度、塑性和变形能力的最基本的依据,被广泛、直接地用于工程设计、产品检验、工艺评定等方面。
而有些材料的受压力学性能和受拉力学性能不同,所以,要对其施加轴向压力,以考核其受压性能,这就是压缩实验。
一、实验目的1.通过对低碳钢和铸铁这两种不同性能的典型材料的拉伸、压缩破坏过程的观察和对实验数据、断口特征的分析,了解它们的力学性能特点。
2.了解电子万能试验机的构造、原理和操作。
3.测定典型材料的强度指标及塑性指标,低碳钢拉伸时的屈服极限S σ,(或下屈服极限SL σ),强度极限b σ,延伸率δ,截面收缩率ψ,压缩时的压缩屈服极限SC σ,铸铁拉伸、压缩时的强度极限b σ、bC σ。
二.实验设备及试件1. 电子万能试验机:试验机结构与原理――材料力学基本实验设备是静态万能材料试验机, 能进行轴向拉伸、轴向压缩和三点弯曲等基本实验。
试验机主要由机械加载、控制系统、测量系统等部分组成。
当前试验机主要的机型是电子万能试验机,其加载是由伺服电机带动丝杠转动而使活动横梁上下移动而实现的。
在活动横梁和上横梁(或工作台上)安装一对拉伸夹具或压缩弯曲的附件,就组成了加载空间。
伺服控制系统则控制伺服电机在给定速度下匀速转动,实现不同速度下横梁移动或对被测试件加载。
活动横梁的移动速度范围是0.05~500毫米/每分钟。
图1-1 万能材料试验机结构图图1—2 拉伸圆试件 测量系统包括负荷测量、试件变形测量和横梁位移测量。
负荷和变形测量都是利用电测传感技术,通过传感器将机械信号转变为电信号。
负荷传感器安装在活动横梁上,通过万向联轴节和夹具与试件联在一起,测量变形的传感器一般称作引伸计安装在试件上。
材料拉伸和压缩试验报告

材料的拉伸压缩实验【实验目的】1.研究低碳钢、铸铁的应力——应变曲线拉伸图。
2.确定低碳钢在拉伸时的机械性能(比例极限R、下屈服强度R eL、强度极p限R m、延伸率A、断面收缩率Z等等)。
3. 确定铸铁在拉伸时的力学机械性能。
4.研究和比较塑性材料与脆性材料在室温下单向压缩时的力学性能。
【实验设备】1.微机控制电子万能试验机;2.游标卡尺。
3、记号笔4、低碳钢、铸铁试件【实验原理】1、拉伸实验低碳钢试件拉伸过程中,通过力传感器和位移传感器进行数据采集,A/D转换和处理,并输入计算机,得到F-∆l曲线,即低碳钢拉伸曲线,见图1。
对于低碳钢材料,由图1曲线中发现OA直线,说明F正比于∆l,此阶段称为弹性阶段。
屈服阶段(B-C)常呈锯齿形,表示载荷基本不变,变形增加很快,材料失去抵抗变形能力,这时产生两个屈服点。
其中,B'点为上屈服点,它受变形大小和试件等因素影响;B点为下屈服点。
下屈服点比较稳定,所以工程上均以下屈服点对应的载荷作为屈服载荷。
测定屈服载荷Fs时,必须缓慢而均匀地加载,并应用σs=F s/ A0(A0为试件变形前的横截面积)计算屈服极限。
图1低碳钢拉伸曲线屈服阶段终了后,要使试件继续变形,就必须增加载荷,材料进入强化阶段。
当载荷达到强度载荷F b后,在试件的某一局部发生显著变形,载荷逐渐减小,直至试件断裂。
应用公式σb =F b /A 0计算强度极限(A 0为试件变形前的横截面积)。
根据拉伸前后试件的标距长度和横截面面积,计算出低碳钢的延伸率δ和端面收缩率ψ,即%100001⨯-=l l l δ,%100010⨯-=A A A ψ 式中,l 0、l 1为试件拉伸前后的标距长度,A 1为颈缩处的横截面积。
2、压缩实验铸铁试件压缩过程中,通过力传感器和位移传感器进行数据采集,A/D 转换和处理,并输入计算机,得到F-∆l 曲线,即铸铁压缩曲线,见图2。
对铸铁材料,当承受压缩载荷达到最大载荷F b 时,突然发生破裂。
拉伸和压缩实验.
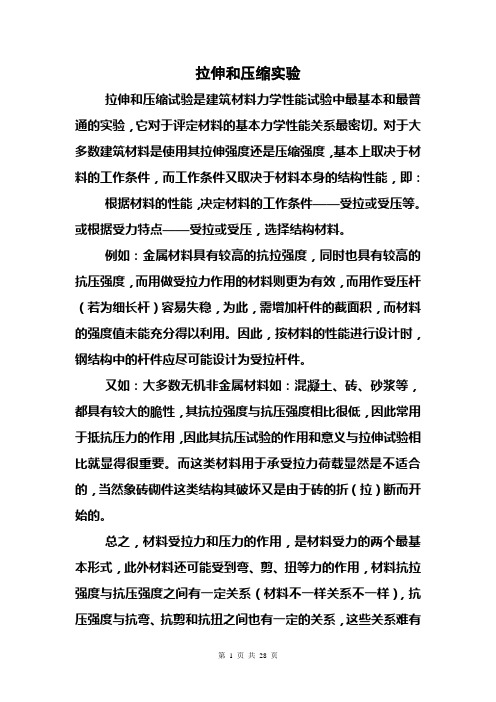
拉伸和压缩实验拉伸和压缩试验是建筑材料力学性能试验中最基本和最普通的实验,它对于评定材料的基本力学性能关系最密切。
对于大多数建筑材料是使用其拉伸强度还是压缩强度,基本上取决于材料的工作条件,而工作条件又取决于材料本身的结构性能,即:根据材料的性能,决定材料的工作条件——受拉或受压等。
或根据受力特点——受拉或受压,选择结构材料。
例如:金属材料具有较高的抗拉强度,同时也具有较高的抗压强度,而用做受拉力作用的材料则更为有效,而用作受压杆(若为细长杆)容易失稳,为此,需增加杆件的截面积,而材料的强度值未能充分得以利用。
因此,按材料的性能进行设计时,钢结构中的杆件应尽可能设计为受拉杆件。
又如:大多数无机非金属材料如:混凝土、砖、砂浆等,都具有较大的脆性,其抗拉强度与抗压强度相比很低,因此常用于抵抗压力的作用,因此其抗压试验的作用和意义与拉伸试验相比就显得很重要。
而这类材料用于承受拉力荷载显然是不适合的,当然象砖砌件这类结构其破坏又是由于砖的折(拉)断而开始的。
总之,材料受拉力和压力的作用,是材料受力的两个最基本形式,此外材料还可能受到弯、剪、扭等力的作用,材料抗拉强度与抗压强度之间有一定关系(材料不一样关系不一样),抗压强度与抗弯、抗剪和抗扭之间也有一定的关系,这些关系难有准确的表达式,而拉、压强度是材料使用得最为广泛的两个强度值。
(建筑结构中,柱墙主要承受压力,梁、板主要承受弯曲应力,屋架中的拉杆承受拉力)第一节拉伸实验一、对试件的要求(对试件总的要求是,对试验结果影响大的应消除)1、试件形式,有园柱形,如钢,平板形,如钢板等,8字形,如砂浆等,受拉截面一般为园形、正方形或长方形。
为了使断裂面发生在试件中长度的中部试件总是制成在长度中间的横截面小于两端的横截面,在这个断面上的应力不受夹具装置的影响。
2、试件的端部形状,应适合于试验材料本身的性能和试验机夹具装置。
可做成平滑的、阶梯形、螺纹形或锥形等。
端部的直径或宽度与中间偏袄截面直径或宽度之比与材料性能有关,如钢材为1.5:1,材料1.7—3.75:1,对脆性材料端部的制作特别重要,由于受夹具作用应力的影响,避免在端部破坏,应做得大一些。
材料拉伸、压缩及扭转实验

目录
实验目的 实验仪器 实验原理 实验步骤 实验数据表格及数值修约 实验思考题
材料力学实验的实验内容
1、材料的基本力学性能测定 2、验证已建立的理论。 3、应力分析实验。 4、理论分析计算与实验结果相结合。 5、看得见、摸得着的材料力学概念。
材料力学实验的标准、方法和要求
1、标准:材料的强度指标虽是材料的固有属性但往 往与试 样的形状、尺寸等有关。为了使实验结果能够相互 比较,国家标准对试样的取材、尺寸、形状、加工 精度、实验手段和方法以及数据的处理都有统一的 规定。我国标准的代码是GB。
现象及其破坏特征,并对试样断口进行分析。 (P 155)
二、实验仪器
1、万能材料实验机 2、扭转实验机 3、游标卡尺(单位mm,精度0.02)
三、实验原理
1、拉伸时低碳钢的下屈服强度σs ,抗拉强度σb的测 定(p144,2)
2、拉伸时低碳钢的断后伸长率δ和断面收缩率ψ的 测定(p145)
3、拉伸时铸铁抗拉强度σb的测定(p146) 4、压缩时,低碳钢的下屈服强度与铸铁的抗压强度
学号排好后交给实验老师。
一、实验目的
1. 了解一种万能力学试验机的构造和工作原理,掌握其操作规程和使 用注意事项;(P 141)
2. 测定低碳钢拉伸时的屈服极限σs 、强度极限σb、断后伸长率δ和断面 收缩率ψ ; (P 141)
3. 测定铸铁拉伸时的强度极限σb ; (P 142) 4. 测定低碳钢的压缩屈服极限σs 和铸铁的强度极限σb ; (P 150) 5. 测定铸铁材料的抗扭强度极限τb ; (P 155) 6. 测定低碳钢材料的扭转屈服极限τs 和抗扭强度极限τb ; (P 155) 7. 观察比较铸铁和低碳钢两种材料在拉伸、压缩、扭转变形过程中的
- 1、下载文档前请自行甄别文档内容的完整性,平台不提供额外的编辑、内容补充、找答案等附加服务。
- 2、"仅部分预览"的文档,不可在线预览部分如存在完整性等问题,可反馈申请退款(可完整预览的文档不适用该条件!)。
- 3、如文档侵犯您的权益,请联系客服反馈,我们会尽快为您处理(人工客服工作时间:9:00-18:30)。
实验1 常温单轴拉伸实验马 杭 编写单轴拉伸实验是研究材料机械性能的最基本、应用最广泛的实验。
由于试验方法简单而且易于得到较为可靠的试验数据,在工程上和实验室中都广泛利用单轴拉伸实验来测取材料的机械性能。
多数工程材料拉伸曲线的特性介于低碳钢和铸铁之间,但其强度和塑性指标的定义与测试方法基本相同,因此通过单轴拉伸实验分析比较两种材料的拉伸过程,测定其机械性能,在机械性能的试验研究中具有典型的意义,掌握其拉伸和破坏过程的特点有助于正确合理地认识和选用材料,了解静载条件下结构材料的许用应力的内涵。
一、实验目的1.通过单轴拉伸实验,观察分析典型的塑性材料(低碳钢)和脆性材料(铸铁)的拉伸过程,观察断口,比较其机械性能。
2.测定材料的强度指标(屈服极限S σ、强度极限b σ)和塑性指标(延伸率δ和面缩率ψ)。
二、实验设备1.电子万能材料试验机WDW-100A(见附录一)。
2.计算机、打印机。
3.游标卡尺。
图1-1 圆棒拉伸试样简图三、试样材料性能的测试是通过试样进行的,试样制备是试验的重要环节,国家标准GB6397-86对此有详细的规定。
本试验采用圆棒试样,如图1-1所示。
试样的工作部分(即均匀部分,其长度为C l )应保持均匀光滑以确保材料的单向应力状态。
均匀部分的有效工作长度0l 称为标距,0d 和0A 分别为工作部分的直径和面积。
试样的过渡部分应有适当的圆角以降低应力集中,两端的夹持部分用以传递载荷,其形状与尺寸应与试验机的钳口相匹配。
材料性能的测试结果与试样的形状、尺寸有关,为了比较不同材料的性能,特别是为了使得采用不同的实验设备、在不同的实验场所测试的试验数据具有可比性,试样的形状与尺寸应符合国家标准(GB6397-86)。
例如,由于颈缩局部及其影响区的塑性变形在断后延伸率中占很大比重,同种材料的延伸率不仅取决于材质,而且还取决于试样标距。
按国家标准规定,材料延伸率的测试应优先采用两类比例试样:(1)长试样:0010d l =(圆形截面试样),或003.11A l =(矩形截面试样) (2)短试样:005d l =(圆形截面试样),或0065.5A l =(矩形截面试样)用长试样和短试样测得的断后延伸率分别记做10δ和5δ,国家标准推荐使用短比例试样。
四、实验原理单轴拉伸实验在电子万能材料试验机上进行。
在试验过程中,试验机上的载荷传感器和位移传感器分别将感受到的载荷与位移信号转变成电信号送入EDC 控制器,信号经过放大和模数转换后送入计算机,并将处理过的数据同步地显示在屏幕上,形成载荷—位移曲线(即l P ∆-曲线),试验数据可以存储和打印。
在实验前,应进行载荷传感器和位移传感器的标定(校准)。
根据l P ∆-曲线和试样参数,计算材料的各项机械性能指标。
根据性能指标、l P ∆-曲线特征并结合断口形貌,分析、评价材料的机械性能。
试验机操作软件的使用可参见附录一。
五、试验步骤1.原始尺寸测量:(1)确定标距0l 。
(2)测量直径0d :在标距中央及两条标距线附近各取一截面进行测量,每截面沿互相垂直方向各测一次取平均值,0d 采用三个截面中的平均值的最小值。
2.初始条件设定:如图1-2,(1)首先进行载荷与位移清零,用鼠标点击载荷与位移(绿色)显示区右上方的0.0按纽,使两者的显示值均为零。
(2)点击左上方“曲线参数”,根据材料的强度与塑性,选择合适的显示量程。
图二右下方为载荷—位移曲线的显示区,其X 轴为横梁位移(mm ),Y 轴为载荷(kN )。
(3)点击左上方“试样信息”,输入试样参数。
3.试样装夹:(1)选择“手动操作”,设定较快的横梁移动速度(20mm/min 或50mm/min ),点击“上升”或“下降”使横梁移动并观察。
当横梁到达合适的位置时,点击“停止”使横梁停止移动。
(2)将试样的夹持端插入上楔形夹头并旋紧,点击“下降”使试样的另一端插入下楔形夹头,下降时注意对中以免产生碰撞,停机后旋紧下夹头。
注意,试样装夹之后不再进行载荷清零。
图1-2 拉伸试验的计算机界面4.加载试验:(1)选择“手动操作”,设定试验速度,建议低碳钢试样设为5mm/min ,铸铁试样设为1-2mm/min 。
(2)点击“上升”开始拉伸试验,注意观察试样、曲线显示区的曲线以及载荷与位移显示值的变化。
(3)低碳钢试样将依次出现变形的四个阶段。
当载荷从最大值开始下降时可以看到试样的颈缩区,如果试样表面光滑、材料杂质含量少,可以清楚地看到表面45°方向的滑移线。
试样断裂后试验机自动停止加载。
5.试验结束前的重要工作:(1)打印记录曲线,开启打印机电源后,依次点击右上角“分析”(弹出新界面)、“打印”。
点击右上角“保存”,可以将本次试验的信息以文本文件的形式保存起来,文件名的后缀为“.dat ”。
(2)取下试样,对拢已破坏的试样,测量有关数据,观察断口形貌。
六、试验结果整理1.强度指标计算:(1)屈服极限 0/A P S S =σ (MPa ) (2)强度极限 0/A P b b =σ (MPa )屈服载荷S P 取屈服平台的下限值。
b P 取l P ∆-曲线上的最大载荷(参见图三)。
脆性材料不存在屈服阶段,所以只需计算b σ。
2.塑性指标计算:(1)延伸率%10001⨯-=l l l δ(2)面缩率 %100010⨯-=A A A ψ3.绘制l P ∆-曲线:将载荷—位移记录曲线绘制在坐标纸上,标注坐标的刻度,标明变形的各个阶段,标出曲线上的特殊点(例如下屈服点,等等)。
4.画出断口形貌草图,根据试验结果,对两种材料的性能进行分析比较,完成试验报告。
七、预习与思考1.认真预习实验指导书,明确实验目的和方法,明了试验中应当注意观察的现象。
2.本试验的l P ∆-曲线上的变形量与试样上的变形量是否相同?如果要利用l P ∆-曲线来近似确定试样的断后延伸率,应怎样做?3.为什麽要采用比例试样?同一材料的10δ和5δ有何关系?八、两种典型材料的l P ∆-曲线低碳钢具有良好的塑性,从图1-3可以看出,低碳钢的l P ∆-曲线明显地分为四个阶段:(1)弹性阶段(OA ):试样的变形是弹性的,若在弹性阶段卸载,试样恢复原来的尺寸,几乎不存在残余变形。
材料在弹性范围内服从Hooke 定律,其载荷—伸长、应力—应变成正比。
(2)屈服阶段(AB ):标志着宏观塑性变形的开始,材料暂时丧失抵抗继续变形的能力。
在屈服阶段,载荷(应力)往往出现锯齿状波动,载荷开始下降所对应的应力称为上屈服点,其数值受材料状态和试验条件多种因素的影响,而屈服阶段应力的最低值—下屈服点的数值则比较稳定,所以通常用下屈服点作为材料的屈服极限S σ。
结构、零件的应力一旦超过屈服极限,就会因为变形过量而失效。
从屈服阶段开始,材料的变形包含弹性与塑性两部分。
(3)强化阶段(BC ):亦称均匀变形阶段,材料恢复了对继续变形的抵抗能力,载荷随着变形而持续上升。
如果在该阶段卸载,试验机和试样组成的系统的弹性变形随之消失,试样的塑性变形将永远保留下来,卸载路径与弹性阶段平行。
如果卸载后再次加载,加载路径近似与卸载路径重合,载荷到达原卸载点时将重新进入屈服并产生塑性变形,材料表现出强度上升、塑性下降的现象,称作形变强化(或冷作硬化、加工硬化)。
形变强化是金属材料的宝贵品质,是材料强化的重要手段。
(4)颈缩阶段(CD ):亦称局部变形阶段。
这时,材料形变强化对载荷增加的贡献已经不能抵偿试样截面积减小对载荷的削弱作用,载荷下降,塑性变形在局部进行,承载面积迅速减小,直到断裂。
断裂后试样的弹性变形消失,塑性变形则保留在断裂的试样上。
图1-3 低碳钢与铸铁的l P ∆-曲线铸铁是典型的脆性材料,拉伸过程比较简单,不存在低碳钢那样的四个阶段,可以近似认为经弹性阶段直接过渡到断裂,断裂后的延伸率极小,因此这类材料若使用不当,容易发生事故。
实验2 单轴压缩实验李享荣 编写一、实验目的1.观察并比较低碳钢和铸铁在压缩时的变形和破坏现象。
2.测定低碳钢的屈服极限Sσ和铸铁的强度极限bσ。
二、实验原理1.低碳钢:一般取圆柱形试件,尺寸为1<d h /<3,在屈服以前,其应力-应变关系基本上与拉伸时相同,随后横截面逐渐增大,试件最后压成饼形而不破裂(图2-1),故只能测出SF ,由sσ=/A F S 于是得出材料受压时的屈服极限,而得不出受压时的强度极限。
2.铸铁:铸铁压缩一般也取圆柱形试件,其尺寸与低碳钢一样,试件受力直至破坏(图2-2),破坏断面与试样轴线约成35o— 45o,测出破坏时的载荷bF ,由b σ=0/A F b 得到铸铁的强度极限bσ。
OPl低碳钢l∆PO铸铁图2-1 低碳钢压缩 图2-2 铸铁压缩图2-3 低碳钢压缩l F ∆-图 图2-4 铸铁压缩的l F ∆-图三、实验设备1.WE300型万能试验机(见附录二)。
2.游标卡尺。
四、实验方法及步骤1.校正测力盘零点(详见附录二油压式万能试验机说明),调整好记录仪。
2.用游标卡尺量取试件的横截面直径。
3.将试件放在压板的中心。
4.缓慢均匀地加载荷,注意低碳钢压缩时的屈服载荷,并记下这一载荷sF ,过屈服后一直压到试样成扁平状.铸铁一直压到破坏为止,记下破坏时的载荷bF 。
五、预习题和思考题1.本试验的目的是什么?2.压缩试件为什么做成短柱形?3.低碳钢和铸铁压缩试验时应记录哪些试验数据?实验3 扭转实验李享荣 编写一、实验目的1.测定低碳钢的扭转屈服极限和强度极限。
2.测定铸铁的扭转强度极限。
3.观察低碳钢和铸铁的断口情况,并分析其原因。
二、实验设备1.K —500型扭转机(见附录三)2.游标卡尺三、实验原理及装置1.低碳钢园截面试件扭转时,其尺寸和形式视试验机而定。
在弹性范围内,扭矩T 与扭转角ϕ为直线关系(图3-1a)。
当扭矩超过比例极限扭矩pT 时,曲线变弯并逐渐趋于水平。
在屈服阶段时,扭角增加而扭矩不增加,此时的扭矩即为屈服扭矩sT 。
屈服后,圆截面上的剪应力,由边缘向中心将逐步升值到扭转屈服极限sτ(图3-1b),即截面材料处于全屈服状态,由此,可以求得材料的剪切屈服极限为:图3-1a 低碳钢扭转时的ϕ-T 曲线 3-1b 低碳钢扭转时横截面在全屈服下的应力分布ps s W T 43=τ , 其中163d W p π=此后,扭转变形继续增加,试件扭矩又继续上升至C 点,试件被剪断,记下破坏扭矩bT ,扭转强度极限bτ为:pb b W T 43=τ铸铁受扭时,ϕ-T 曲线如图3-2所示。
从开始受扭,直到破坏,近似为一条直线,故其强度极限b τ可按线弹性应力公式计算如下:pb b W T =τ图3-2 铸铁扭转时的ϕ-T 曲线 图3-3 铸铁扭转时沿45o 斜截面的应力材料在纯剪切时,横截面上受到切应力作用,而与杆轴成45o 螺旋面上,分别受到拉应力τσ=1和压应力τσ-=3的作用(图3-3)。