离型涂布方式
离型纸的离型力
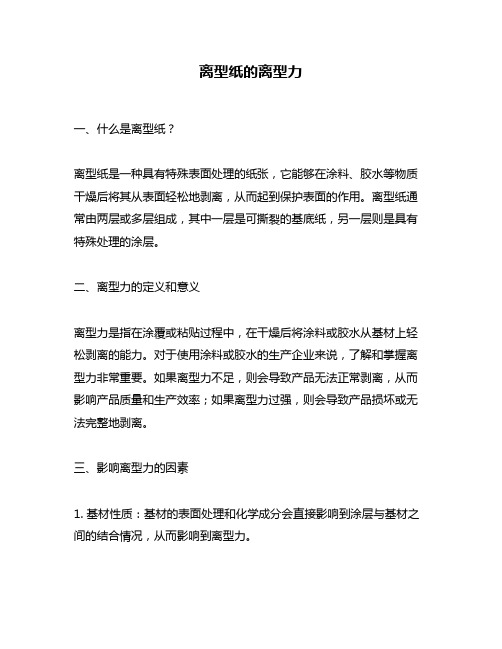
离型纸的离型力一、什么是离型纸?离型纸是一种具有特殊表面处理的纸张,它能够在涂料、胶水等物质干燥后将其从表面轻松地剥离,从而起到保护表面的作用。
离型纸通常由两层或多层组成,其中一层是可撕裂的基底纸,另一层则是具有特殊处理的涂层。
二、离型力的定义和意义离型力是指在涂覆或粘贴过程中,在干燥后将涂料或胶水从基材上轻松剥离的能力。
对于使用涂料或胶水的生产企业来说,了解和掌握离型力非常重要。
如果离型力不足,则会导致产品无法正常剥离,从而影响产品质量和生产效率;如果离型力过强,则会导致产品损坏或无法完整地剥离。
三、影响离型力的因素1. 基材性质:基材的表面处理和化学成分会直接影响到涂层与基材之间的结合情况,从而影响到离型力。
2. 涂料或胶水性质:涂料或胶水的成分、浓度、粘度等性质会影响到其与基材的结合情况和干燥时间,从而影响到离型力。
3. 涂布方式和条件:涂布方式和条件包括涂布厚度、温度、湿度等因素,它们会影响到涂料或胶水的干燥速度和结构形态,从而影响到离型力。
4. 储存环境:储存环境中的温度、湿度等因素会直接影响到离型纸的性能,从而影响到离型力。
四、提高离型力的方法1. 优化涂层配方:通过调整涂料或胶水的成分和浓度,以及优化涂布方式和条件等方法来提高离型力。
2. 选择适合的基材:选择适合自己产品的基材,并对其进行表面处理,以提高涂层与基材之间的结合情况。
3. 控制储存环境:在储存离型纸时,控制好温度、湿度等因素,避免出现过高或过低的情况。
4. 加强质量管理:加强对生产过程中各项参数和指标的检测和监控,及时发现问题并进行调整,以提高离型力。
五、离型纸的应用领域离型纸广泛应用于电子、印刷、塑料、建材等行业中。
例如,在电子行业中,离型纸主要用于保护印刷电路板;在印刷行业中,离型纸主要用于保护印刷品表面;在塑料行业中,离型纸主要用于模具表面防粘剂。
六、总结离型力是影响离型纸性能的重要因素之一。
了解和掌握离型力对于生产企业来说非常重要。
氟素离型膜生产工艺
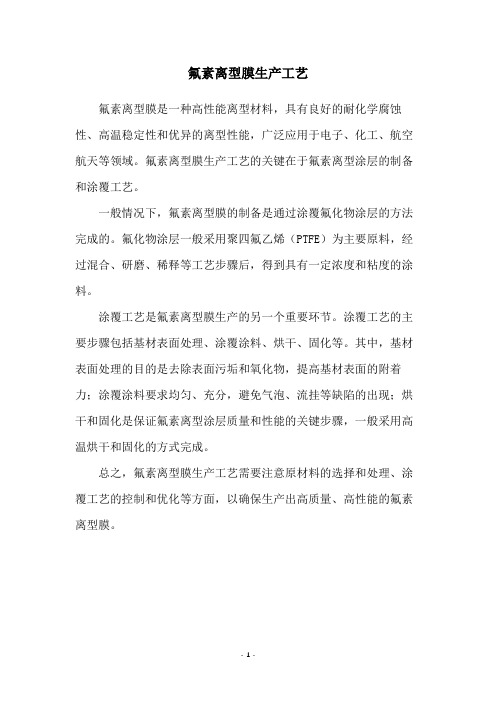
氟素离型膜生产工艺
氟素离型膜是一种高性能离型材料,具有良好的耐化学腐蚀性、高温稳定性和优异的离型性能,广泛应用于电子、化工、航空航天等领域。
氟素离型膜生产工艺的关键在于氟素离型涂层的制备和涂覆工艺。
一般情况下,氟素离型膜的制备是通过涂覆氟化物涂层的方法完成的。
氟化物涂层一般采用聚四氟乙烯(PTFE)为主要原料,经过混合、研磨、稀释等工艺步骤后,得到具有一定浓度和粘度的涂料。
涂覆工艺是氟素离型膜生产的另一个重要环节。
涂覆工艺的主要步骤包括基材表面处理、涂覆涂料、烘干、固化等。
其中,基材表面处理的目的是去除表面污垢和氧化物,提高基材表面的附着力;涂覆涂料要求均匀、充分,避免气泡、流挂等缺陷的出现;烘干和固化是保证氟素离型涂层质量和性能的关键步骤,一般采用高温烘干和固化的方式完成。
总之,氟素离型膜生产工艺需要注意原材料的选择和处理、涂覆工艺的控制和优化等方面,以确保生产出高质量、高性能的氟素离型膜。
- 1 -。
涂布产品-离型膜

1.2 离型膜分类 按硅油涂层分类:
按基材分类:
普通硅油离型膜 PE(聚乙烯)离型膜 ; BOPP(聚丙烯)离型膜 ; 氟塑离型膜 其它类:比如耐高温有机硅压敏胶。 PET(聚酯)离型膜。 按表面颜色分类: 红色离型膜、黄色离型膜、绿色离型膜、 超轻离型离型膜(<5g) 蓝色离型膜、白色离型膜等各种颜色的 轻离型离型膜(5-10g); PET离型膜。 中离型离型膜(10-50g); 按基材表面处理分类: 重离型离型膜(50g以上)。 单面离型膜、双面离型膜、无硅离型膜。
按离型力分类:
• 1.3 离型涂料构成
有机硅 树脂
主体树 脂
溶剂
甲苯、丁 酮、正己 烷、120# 溶剂油
催化剂
离型涂 料构成
剥离力 调节剂 附着力 促进剂
Pt, Sn…
特殊有机 硅树脂
根据需 要添加
1.4 离型涂料主要厂家来源
美国道康宁 日本信越 蓝星罗地亚 德国瓦克 德国德固赛 …
1、离型膜
1.1 简介 离型膜是指表面具有分离性的薄膜,离型膜与特定的材料在有限的条件 下接触后不具有粘性,或轻微的粘性。
通常情况下为了增加塑料薄膜的离型力,会将塑料薄膜做等离子处理 ,或 涂氟处理,或涂硅离型剂于薄膜材质的表层上,让它对于各种不同的压感 胶表现出极轻且稳定的离型力。根据不同所需离型膜离型力,隔离产品 胶的粘性不同,离型力相对应调整,使之在剥离时达到极轻且稳定的离 型力。
1.5 工艺流程
来料检验
配料
搅拌,过滤
上料
检验
收卷
横拉 (烘箱)
涂布
包装
出货
离型纸_精品文档
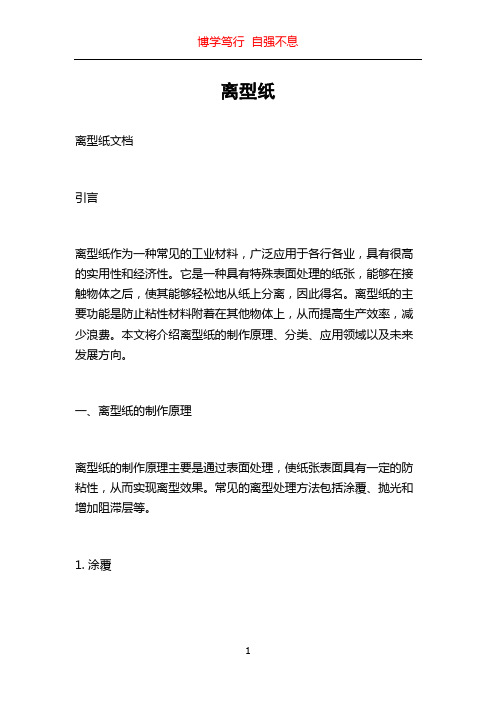
离型纸离型纸文档引言离型纸作为一种常见的工业材料,广泛应用于各行各业,具有很高的实用性和经济性。
它是一种具有特殊表面处理的纸张,能够在接触物体之后,使其能够轻松地从纸上分离,因此得名。
离型纸的主要功能是防止粘性材料附着在其他物体上,从而提高生产效率,减少浪费。
本文将介绍离型纸的制作原理、分类、应用领域以及未来发展方向。
一、离型纸的制作原理离型纸的制作原理主要是通过表面处理,使纸张表面具有一定的防粘性,从而实现离型效果。
常见的离型处理方法包括涂覆、抛光和增加阻滞层等。
1. 涂覆涂覆是一种常用的离型处理方法,通常使用聚合物涂料进行涂覆。
涂覆过程中,将聚合物涂料均匀地涂布在纸张表面,形成一层均匀的涂层。
这个涂层能够在接触物体的时候,形成一种隔离层,防止物体与纸张黏连在一起。
2. 抛光抛光是通过对纸张表面进行抛光处理,使其表面更加光滑,从而降低物体附着的可能性。
抛光处理通常使用抛光剂和抛光机械完成。
3. 增加阻滞层增加阻滞层是一种特殊的离型处理方法,通过在纸张表面加工一层阻滞层,使物体与纸张之间形成一层隔离层。
这种阻滞层可以是特殊的化学涂料或添加剂。
二、离型纸的分类离型纸可以根据其应用领域和制作材料进行分类。
根据应用领域,离型纸主要可以分为工业离型纸和食品级离型纸。
1. 工业离型纸工业离型纸主要应用于工业制造过程中,用于防止粘性材料黏附在设备、工具和模具上。
工业离型纸通常使用较粗的纸张和持久的涂层,以确保其在高温、高压和严苛的环境下具有良好的离型效果。
2. 食品级离型纸食品级离型纸主要应用于食品加工和包装行业,用于防止食物粘附在容器和包装材料上。
食品级离型纸通常采用无毒、无味的材料制作,以确保对食品的安全性。
根据制作材料,离型纸可以分为硅油离型纸、石墨离型纸和蜡离型纸等。
三、离型纸的应用领域离型纸在各行各业都有广泛的应用,下面将介绍离型纸在几个主要领域的应用情况。
1. 粘合剂制造离型纸在粘合剂制造过程中起到了重要的作用。
离型膜常用知识

涂布方式及工艺介绍 2.涂布工艺
注:烘箱温度不固定,一般依据不良配方、基材、外部环境调整,位于中间的几节烘箱温度较高。
离型膜常见异 常介绍
离型膜常见异常介绍
1.反离型异常
(1)未涂硅,目视或油 性笔涂写可区分,由涂 头异常停机、料槽缺 料、涂头未接触基材引 起 (2)脱硅,表面涂层脱 落,老化测试可发现, 由离型膜固化不良、基 材锚固性失效引起 (3)覆盖不良,不稳定 剥离力&染色实验可识 别,涂布量少、原膜厚 度不均引起 (4)硅层破坏,显微镜 大镜识别,由机械划 伤、收卷摩擦引起
(2)尺寸
A.料件形状不规格; B.最窄处近似1mm宽度或更小;
(只作为理论参考图)
剥离力
25 20
20 16
15
12
10
10
8
6
4
5
2
0
0
0
10
20
30
40
50ห้องสมุดไป่ตู้
60
尺寸
离型膜常见异常介绍
4.静电
(1)静电产生:原子由质子带正电、中子不带电、电子带负电组成,外界作用 使原子的正负电不平衡。任何两个不同材质的物体接触后再分离,即可产生静 电,静电产生的根本原因是电荷的分布不均匀而无法中和 (2)静电产生形式:接触,摩擦,剥离,诱导 (3)静电放电方式:传导,电晕,火花,中和 (4)静电影响: A.高静电会吸引空气中的灰尘与细毛,造成产品表面清洁度下降 B.当收卷静电过高,大量静电耦合在产品内部,模切使用时会出现粘附,不宜分 离,电击 C.快速收放卷的过程中,物料与辊之间会产生大量的摩擦、剥离、挤压,使物体 表面积聚不同电性的静电荷, D.速度越快,时间越长,积累的静电越大,静电值最高可达几十万伏 (5)防静电: A.收放卷及分切时使用静电消除棒静电 B.湿度增加 C.减少摩擦或接触面积
无溶剂纸张离型剂涂布技术

85 ° C 600 (350) 0.27 0.24
85 ° C 200 (550) 0.20 0.19
高速固化 通用型 低粘度,适用 于补偿网纹辊涂 布
85 ° C 200 高速固化 低剥离速度下 极低离型力,随 剥离速度增加离 型力增加
85 ° C 1100 0.29 0.26
无溶剂涂布
4
Evan WU
罗地亚有机硅(上海)有限公司
无溶剂型热固化体系:性能表现
主要性能特点(与现有溶剂型比较):
不使用溶剂,环保安全 不使用溶剂,固化速度高 不使用溶剂,成本低 分子尺寸小,高渗透性,高涂布量,对基材要求高 交联密度高,高膜硬度,低高速剥离力,低迁移性,高光泽 涂布工艺技术要求非常高 需要特殊技术以获得低温度固化
无溶剂纸张离型剂涂布技术
Evan WU
无溶剂涂布
1
Evan WU
罗地亚有机硅(上海)有限公司
内容
无溶剂热固化体系
无溶剂辐射固化体 系
Rhodia服务及 技术支持
无溶剂涂布
2
Evan WU
罗地亚有机硅(上海)有限公司
内容
无溶剂热固化体系
无溶剂涂布
3
Evan WU
罗地亚有机硅(上海)有限公司
无溶剂型热固化体系: 组成及化学
使用与目前加成型溶剂型热固化体系类似的技术:
主体带有反应活性基团的有机硅聚合物,活性基团为Vi 使用含氢硅油作为交联剂,品种及数量可调节 使用铂金络合物作为催化剂 可通过调节配方或添加剥离力调节剂调节离型效果
但存在如下区别:
• 主体分子量很小(~8,000 Vs 500,000), 分子尺寸小,粘度低(200~800cps) • 催化剂、主体都不使用溶剂 • 浴槽稳定剂一般与溶剂型体系不同
离型膜涂布工艺与关键指标介绍!

离型膜涂布工艺与关键指标介绍!离型膜涂布方式概述涂布方式大致分为:1、光辊涂布2、网纹涂布3、刮刀式涂布4、喷雾涂布和帘式涂布根据不同产品,涂料特性不同而采用不同涂布方式。
各涂布方式的特点(一)光辊涂布这种涂布采用两辊或多辊转移涂布方式,调整各辊之间的间隙和转速比列,就可以调整涂布量的大小。
整涂布头的结构比较复杂,要求上胶辊、涂布辊、牵引辊及刮刀的加工精度和装配精度要求较高,成本较高。
由于这种涂布机采用高精度光棍进行涂布上胶,涂布效果好,涂布量大小除了通过上胶辊和涂布辊之间的间隙来调整,还可以通过涂布刮刀微动调节来灵活控制,涂布精度高。
(二)网辊涂布这种涂布设备主要采用网纹(凹眼)涂布棍进行上胶,其涂不均匀性较好,而且涂布量准确,但缺点是涂布量难调节。
用网纹辊涂布时,涂不量与网纹辊的凹眼深度和胶水自身的特系(黏度、固含量)有关。
(三)刮刀式涂布刮刀式涂布往往回出现上胶不均匀,主要与刮刀的加工精度、刮刀安装方法涂布时刮到于背胶轮的角度以及涂料的黏度有很大关系。
刮刀的平整度精度要求高,就是指刮刀不翘曲变形或缺口,否则涂布量误差大。
在涂布时,刮刀与上胶轮的觫点切线间的角度一般在15o~30o之间,如果太大,其刮到几乎顶着背胶轮,背胶轮高速运转时刮刀容易引起震动,引起涂布不均匀,涂布量差异大。
另外,还会引起涂布的膜面不平整、有刮痕,同时还易引起刮刀刀刃损伤。
(四)喷雾涂布和帘式涂布喷雾涂布和帘式涂布新型涂布方式,预示着美好的发展前景。
上述的发展不可能一帆风顺,必须面临许多技术上的挑战。
高固含量刮刀涂布会产生诸如刮刀痕、刮刀压力大、刮刀上涂料析出(俗称翻料)和刮刀磨损快等运转性问题。
计量施胶压榨涂布涂布必须要面对高速、高固含量和高涂布量涂布所带来的诸多难题,包括涂布辊压区出口的雾溅、涂布面的橘皮纹纸病等。
新型涂布方式也要解决常规涂布中不曾遇到的新问题。
干燥工艺基础1、涂布和干燥的相互关系:干燥过程和涂面布过程各自独立,又相互联系:涂层的性质影响到干燥工艺的设计和操作;涂布速度,涂层的厚度决定干燥长度;干燥过程中涂层有流平过程,因此一台涂布机在设计过程中能否准确地运用最佳期的涂布、干燥工艺,平衡两者的关系,最终影响到涂布机的综合技术性能。
离型纸的选纸和生产工艺以及流程

离型纸的选纸和生产工艺以及流程离型纸对原纸即纸基层有较高的要求,不仅要求其具有较高的强度而且在耐热性松厚度水分等方面也有严格的要求。
在原纸定量方面一般选用125g/m2以上的纸张,其生产技术难点在于,对原纸松厚度和耐热性的控制。
在松厚度方面一般选用针叶木浆与阔叶木浆配比抄造的方式来控制在耐热性方面需要,在浆料中添加耐热剂来增强纸张的耐热性能。
所以一般的离型纸都会使用淋膜纸制作离型纸,因其平整度好,韧性好,符合离型纸制作的基本要求。
离型涂料层可分为两大类,即硅系离型涂料层和非硅系离型涂料层。
硅系离型材料包括硅酮树脂和改性硅酮树脂用醇酸树脂丙烯酸树脂等。
非硅系离型材料包括铬络合物甲基丙烯酸型或脂肪酸型聚丙烯树脂,聚甲基戊烯树脂和其它特殊树脂氨基醇酸树脂,环氧树脂等。
不同类型的离型涂层各自具有不同的特点,比如硅酮树脂型涂层具有优良的剥离性能和耐热性能,铬络合物型涂层耐溶剂性较差,聚丙烯型涂层具有较高的光泽度但耐热性能较差。
不同类型的离型涂层其技术工艺也有所不同,硅系离型涂料一般采用辊式或刮刀式的涂布方法,且要求所用的原纸要先进行一层底涂。
底涂的主要目的是为了提高平滑度和抗硅系涂料渗透的能力。
聚丙烯树脂和聚甲基戊烯树脂型涂层主要通过挤压涂布的方式,它所用原纸可以不进行底涂,其涂层中的其它添加成分通过挤压涂布机的进料槽进料,这些离型涂层技术工艺都涉及到涂层剥离强度的控制,这也是其技术难点所在。
因为这又涉及到剥离力控制剂的选择及其对离型涂层其他性能的影响。
离型纸的生产工流程分为四大类:第一道工序:带有印刷的离型纸,淋膜纸,硅油纸必须先印刷,才能做后道工序:淋膜和涂硅。
第二道工序:P E淋膜(涂塑),PE淋膜机又称涂塑机,将热熔的PE塑料膜均匀地涂布在纸张表面,形成淋膜纸,也称涂塑纸或塑纸。
- 1、下载文档前请自行甄别文档内容的完整性,平台不提供额外的编辑、内容补充、找答案等附加服务。
- 2、"仅部分预览"的文档,不可在线预览部分如存在完整性等问题,可反馈申请退款(可完整预览的文档不适用该条件!)。
- 3、如文档侵犯您的权益,请联系客服反馈,我们会尽快为您处理(人工客服工作时间:9:00-18:30)。
THE YASUI SEIKI "Micro Gravure™" COATING METHODYasui Seiki Co., (USA) 2333 Industrial Drive, Suite 24A3 Bloomington, IN 47404 Tel: 812-331-0700 Fax: 812-331-2800Web Site: E-mail: Coating@601 S Liberty DriveBloomington, IN 47403 TEL: 812-331-0700 FAX: 812-331-1119Table of ContentIntroduction (3)What is the Micro Gravure™ Method? (3)Micro Gravure™ vs. other methods (4)Operation of Micro Gravure™ (6)Advantages of Micro Gravure™ (8)Summary (9)Figures & TableFigure 1 (3)Figure 2 (4)Figure 3 (5)Figure 4 (5)Figure 5 (7)Table 1 (10)INTRODUCTIONMany different types of coating systems are available, and in use today. Direct or reverse gravure, reverse roll, die coaters, wire bar, knife or blade coaters and many more are known and are widely used. All these techniques and more are offered by many machine manufacturers including Yasui Seiki Company.However, many converters have reported disappointing results with techniques such as the wire bar and reverse roll. Many streaks with a wire bar and ‘orange peel’ with reverse roll, or creases caused by the backing roll of a gravure coater, troublesome changes of gravure roll and backingroll, and many other quality problems or difficulties are often reported.The Micro Gravure™ coating method wasdeveloped in response to the need for a smooth and uniform thin layer coatingtechnique offering simplicity, reliability andreproducibility of coating . The MicroGravure™ method uses a gravure roll. TheMicro Gravure™ roll surface is engraved with a patternor cells which provide a specific coating volume, just asin standard gravure. The Micro Gravure™ roll is mounted in bearings and rotates partially submerged in a coating pan. Rotation of the roll picks up the coating, which is doctored (pre-metered) by a flexible steel blade as the roll rotates toward the contact point with the web. (Fig.1)WHAT IS THE “Micro Gravure™” METHOD?Generically described, this Micro Gravure™ is a reverse, kiss gravure coating method. Standard gravure can be segregated into several types; direct and reverse are the two of greatest interest to this discussion. (Fig. 2) Typically, both of these types use a backing roll, usually rubber covered, and about the same diameter as the engraved roll. The web is trapped, or nipped, between the engraved roll and the backing roll. In addition to the obvious and frequently encountered problems of web creases or breaks, a nip point introduces a number of mechanical, hydraulic and other stresses which impact coating quality. Micro Gravure™ is a kiss coatingmethod. “Kiss” implies the absence of a backing roll, which would trap the web against the engraved roll. Since Micro Gravure™is a kiss method, and does not use a nip, a number of these potentially deleterious stresses (and safety issues) are eliminated.Micro Gravure™is a reverse process. That is to say that the rotational direction of the engraved cylinder is opposite to the travel direction of the web. The coating is thus applied to the web in a shearing manner, or the liquid coating is experiencing shear. If the web direction and the cylinder rotation are the same, the coating would be split apart; some would tend to go to the web, some would tend to stay on thecylinder. This condition is oftendescribed as “film splitting”.Depending on the strength ofthe internal forces in the coatingitself, film splitting can be verydisruptive. On the other hand, “shear”application is generally acknowledged toproduce somewhat smoother coatings than“film splitting”. Figure 2The Surface of the roll used in MicroGravure™ coating has a number of regularlyspaced "cells" which determine a finite volumeof internal capacity. The geometry, number andspacing, depth or other features of the cell can be varied to produce a range of total volume to accomplish coating weight (thickness) control. This logic is, of course, the same as in standard gravure. So, Micro Gravure™ is a kind of gravure coating method.“Micro Gravure™”vs. OTHER METHODSTherefore, what is the difference between this Micro Gravure™system and conventional ordinary direct or reverse gravure systems? There is, of course, a great difference between them.The “Micro “reference is in regard to the small physical diameter of the engraved roll. In the case of conventional gravure coating methods, standard gravure roll diameters are typically in the range of 125 to 250mm. On the other hand, Micro Gravure™ diameters are from 20mm to 50mm, determined by the coated width required. Micro Gravure™ rolls are 20mm diameter for 300mm width and increase to 50mm diameter for coating widths of 1600mm. The small diameter produces a much smaller line of contact on the web at the point the web touches Micro Gravure™ roll. This is easily visualized by two concentric circles with a pair of rays drawn from the center of each (Fig. 3). The arc on the circumference of the larger circle is obviously much greater than on the small circle. The total contact area of web andwet gravure roll has a certain criticality. In general, a largercontact area may exhibit coating problems to a much greaterdegree than a smaller contact area. The total area is a product ofdimension in the transport direction and in the cross webdirection. It is really the transport direction (the length of thecontact) that is the critical factor. For a given set of conditions, alarger diameter roll will produce a longer line of contact than asmaller diameter. When a backing roll is introduced, this region ofcontact is increased even more.In the case of standard gravure, operating in the direct mode, the amount of the coating in the cells is divided. Some is transferred to the web and some part remains in the cell after the contact point has passed. Typically, there is established a reservoir of coating at both the entry point and the departure point of the nip. Within these two beads of coating, a pattern of turbulentre-circulation will occur. The large diameter rolls used in standard gravure can produce very large turbulent beads,which in turn create aberrations in the coating. (Fig. 4)When nip roll pressure, skewness of rolls, or othermechanical factors are present, the situation is evenmore critical.In standard reverse gravure, particularly with abacking roll, much of the above holds true. In somecases a very large reservoir of coating at the web exit point can be generated. This is seriously influenced by abnormal or faulty condition of the backing roll. The absence of a backing rollwith Micro Gravure™ reduces or eliminates many of the nip induced coating defects associated with other methods. The turbulent bead problem is also minimized because of the small diameter rolls used. The volume of the bead present on the entry and exit point is very small and stable.Like any “gravure” or “engraved roll” system the Micro Gravure™ system also requires two basic processes; introduction of coating to the roll surface, and a means of evenly and accurately metering the coating on the roll surface. A common method of coating application to the roll is a “pan” in which the roll rotates partially submerged. Since the amount of coating on the roll surface is largely dependent on viscosity, some metering means must be used. A blade, or knife is used to remove excess coating solution. Without this, the cell volume could not be the major factor in determining thickness or weight of the wet coating on the substrate. However, the blade used in Micro Gravure™is quite different from blades used in most gravure processes. The major departure relates to stiffness and the angle of attack of the blade to the roll surface. Micro Gravure™ blades are quite thin and flexible in comparison to those typically used in gravure processes. The pressure of the blade against the roll is rather light. The angle of attack of a standard gravure blade is steep. The line of the blade extension typically passes close to the roll center. The thin, flexible Micro Gravure™ blade lays on the roll, nearly tangent to the surface. The comparison here is a scraping action versus smoothing or metering. Standard Doctor metering can cause considerable wearing of blade and roll surface because of this scraping action. The life of both blade and roll is extended because of the more gentle contact inherent in the Micro Gravure™ process.OPERATION of “Micro Gravure™”As already mentioned, the Micro Gravure™ roll is made with surface cells designed to produce a specific coating volume, just as in a standard gravure system. A wide range of patterns and cell volumes is available. The roll is mounted in bearings and is rotated by a small motor through a coupling. Direction of rotation is opposing that of web travel. As the roll rotates, it picks up coating in the ink pan. Continuing rotation takes the coating to the blade where a small excess amount is removed prior to the contact point with the web. The distance from coating impingement on the roll surface to web transfer point is less than a 90degree arc. The circumferential distance is about 30mm or less even for a 40mm diameter roll. (Fig.1)The ratio of the web speed to circumferential speed of the engraved roll is critical in establishing coating thickness. (Fig. 5)At a given web speed with the cylinder stationary, no coating is transferred to the web. As rotational speed is increased, coating will start. Additional rotational speed increases the coating weight until flooding, or instability, and a decrease in coating weight occurs. Coating weight plotted against speed ratio will generally show a “hump back” or bell-shaped curve. The behavior of a “typical” coating will follow the pattern: 60% - coating starts, 100 to 130% - a smooth and uniform coating, 130 to 200% - weight increase, 200% or more – weight decrease and instability. If the web speed is 30m per minute and the cylinder’s surface speed is also 30m per minute, it is 100% or 1 to 1, and if the roll speed is 60m per minute for 30m per minute web speed, then it is 200% or 2 to 1 ratio. Although the cell volume is the major control of coating weight, a “window” will exist on the linear portion of the curve, usually between 100% and 130%, which will allow coating weight or thickness control, while maintaining a uniform appearance. In a very practical way, weight changes of perhaps +/-10% or more, can be made for each cylinder pattern. This can result in economy through requiring a fewer number of rolls to obtain particular weights. From the list of rolls shown in Table 1, it can be seen that it is possible to overlap adjacent rolls via the ratio change. In this way almost continuous changes in weight can be made. For critical applications a curve should be developed for each cell pattern and rheological combination.A 1 to 1 ratio is a good starting point for examination of a new coating. Some 100% solids formulations have been seen to exhibit rather strange behavior relative to the “typical coating” with a 1 to 1 ratio, although it is really not surprising, to see a departure from a typical 30-40% solids solution chemistry. The Micro Gravure™ system can easily respond via manipulation of the ratio. On occasion, a ratio of 2 to 1 or 3 to 1 has produced good coatings with 100% solids UV or radiation curables.ADVANTAGES of “Micro Gravure™”Micro Gravure™can put down thinner coatings on thinner webs, than any other system. This is accomplished primarily because of the very small “footprint” of the web on the roll and because no backing roll is used. A nip point can cause breakage, wrinkles or folds in the web. As Table 1 shows, a 250 mesh (250 cells per linear inch) gravure roll can produce a 1 micron thick wet coated layer. If the coating’s solid content is 5%, then the applied film is 0.05 micron thick after drying.Since there is no backing roll, coating can be applied close to the film edge without concern for transfer to the backside of the film or to the backing roll. Film widths can be changed without having to change the backing roll, as would be required in standard gravure. A wide variety of thin films, papers, fabrics and foils can be easily accommodated. But, this does not mean that the Micro Gravure™ system is only suitable for thin films, i.e. 2 micron PET. This system is also used for coating on 8 mil (200 micron) thick steel foil.Wear of the doctor blade and of the engraved cylinder is minimized because of the light contact of blade and roll. The action is pre-metering rather than scraping.The cost of the small diameter rolls is relatively low, so that many can be on hand without economic penalty. Because of the small size, quick changes of rolls can be made to change coating thickness. Speed ratio manipulation, as previously discussed, makes thickness changes possible as well.Reverse or shearing application normally produces smooth coatings without the need for a post smoothing system. The small diameter also allows more volatile solvents to be used without danger of cell plugging. There is considerable flexibility in formulating for the system;experience indicates a viable range of viscosity from 1 cps to 1000 cps and in some cases even to 2000 cps.SUMMARYVery simply,regardless of whether for production use or for laboratory use a coating machine must satisfy such requirements as ‘Reliability’, ‘Reproducibility of coating’ and ‘Simplicity of operation’. The physical comparisons of Micro Gravure™ to other roll coating processes show simplicity versus complexity. Machine construction is such that vibration, drive inconsistency, tension variation or similar problems do not arise to adversely effect coating quality. Particular attention is given to component selection such as: drive couplings, motors, tension controls and the like. Structural members are selected with regard to influence on the most sensitive coating methods. Sensible design and quality assembly of top grade components assures reliability and reproducibility. Simplicity of the Micro Gravure™ system fosters simplicity of operation.In the past 20 years, over 300 Yasui production coating lines, laboratory use coaters, and over 100 Micro Gravure™production coating stations have been sold all over the world to companies, such as Eastman Kodak, DuPont, 3M, JVC, Hitachi, Toshiba, Panasonic, Mitsubishi Chemical, Teijin, SKC, and many other leading companies in various industrial fields. Virtually all of our customers who replaced or supplemented their production system or laboratory use system with Micro Gravure™coaters produced better results than with their other production systems or research coaters. Especially when a smooth, uniform and very thin layer such as several or a few microns or even a few hundred angstroms is required, this Micro Gravure™system exhibits its capability.Yasui Seiki Company does not wish to give the impression that the Micro Gravure™system can do anything and everything. Our experience indicates that in many cases improved coating quality can result from use of this technology for solvent and emulsion coatings or UV curables. We also do not imply that all other coating methods are categorically inferior to Micro Gravure™. We are certainly well aware that quality coatings are being made every day using a wide range of coating techniques….Table 1Micro Gravure™ Wet Coat weight ChartMesh Lines/inchWet CoatThickness µ*MeshLines/inchWet CoatThickness µ*25 50 - 80 85 13 - 22 30 30 - 45 90 8 - 16 36 28 - 43 95 7 - 15 38 25 - 40 100 6 - 14 45 28 - 43 110 6 - 13 50 25 - 35 120 5 - 11 55 20 - 30 150 4 - 9 60 21 - 31 180 3 - 8 65 13 - 22 200 2 - 5 70 16 - 30 230 1.5 - 3.5 75 20 - 30 250 0.8 - 2 80 12 - 20Notes: *Coat weight is controlled by speed ratio of Gravure speed ÷ web speed, in ranges shown。