远安阀门控制头中文说明书
安全阀说明书
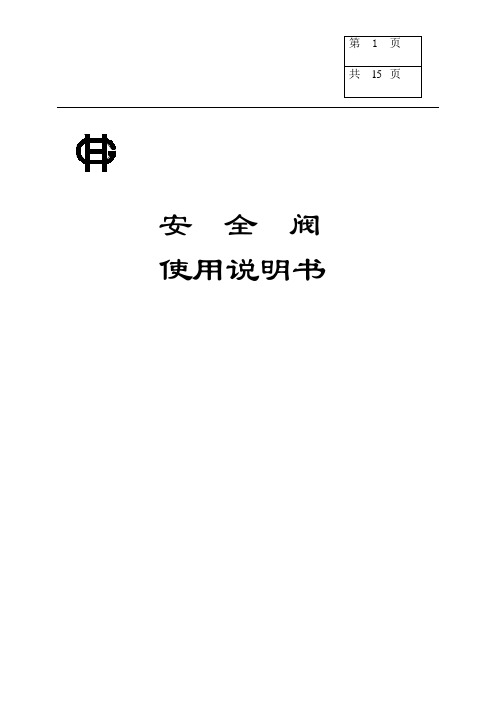
第 1 页共 15 页安全阀使用说明书目录一、用途二、主要零件的作用及结构特点三、安装1.安全阀安装2.排汽管的安装3、输水管的安装四、现场调试1.调试前准备2.新供货的阀门校验性试验3.检修后的阀门调整方法4.上、下调整环、调整套位置表示方法五、解体与装配1.局部解体2.局部解体后装配3.总解体4.总解体后装配六、研磨1.研磨工具的准备2.研磨胎具的制作3.研磨七、安全阀主要零件维护及更换标准八、订货须知一、用途安全阀用于蒸汽温度≤580℃,整定压力≤14MPa的锅炉,压力容器。
以防止蒸汽压力超过规定值,确保设备安全运行,整套阀门是按照日本冈野阀门株式会社全量型安全阀技术制造。
二、主要零件的作用及结构特点安全阀结构如图所示。
安全阀阀座设计成拉伐尔喷嘴形状,阀座内径大于等于1.15倍喉部直径,安全阀达到全开位置时,阀座口处流通面积大于1.05倍喉部面积。
根据拉伐尔喷嘴介质流动原理阀座出口介质流速达到音速,使安全阀排放系数大于0.75。
阀座突出在阀体内,避免阀体热应力对阀座密封面的影响,密封件采用了热阀瓣,并与阀瓣套筒用阀瓣螺母固定在一起,避免阀瓣套筒和阀瓣的热应力对阀瓣密封面的影响,提高了密封性。
热阀瓣用韧性好、强度高、抗冲刷、耐高温的材料制作,热阀瓣如图 -1所示,其优点是当密封面有少量蒸汽漏泄时,漏出的蒸汽降压同时降温。
热阀瓣舌头形状下部温度低于上部温度,舌头部位产生弯曲,后部就翘起,舌头部位紧接触于阀座上,增加了密封比压,提高密封能力。
当介质压力升高,介质作用力与弹簧力相平衡时,漏量无法避免。
漏量增加到一定程度时下调整环上部与热阀瓣下部形成的压力区域内的内压力将随着漏量增加而迅速增加,改变蒸汽对阀瓣的作用力,而使介质有足够的力,克服弹簧力,使阀门启跳,调整下调整环的位置高低,改变压力区域内压力,能得到满意的启跳压力,调整上调整环位置的高低,改变流体对阀瓣的反作用力,能影响阀门启跳高度和影响回座压力,当调整环得不到满意的回座压力时,可调整调整套位置,改变阀瓣背压,就可得到满意的回座压力。
Sporlan电子阀门控制板说明说明书

OPERATIONThe TCB is a microprocessor-controlled device that will supply the properstep signal to most Sporlan electric valves to position, initialize or close thevalve. The TCB can be used as an interface with an external controller; or,with the addition of a set point potentiometer and sensor, can be used as astandalone temperature control.In the interface mode, the TCB will modulate a valve in response to a signalreceived from an external source. In addition to the 0 to 10 volt DC, or 4to 20 milliamp signal commonly used on PID controllers, the TCB can beconfigured to modulate a valve in response to a TLL (5 volt) signal, or a 120volt AC pulse of three to thirty seconds duration.When used as a standalone temperature controller, the board will modulatea valve in response to a set point potentiometer and temperature sensor.The temperature sensor is a 2K, type B, NTC thermistor. This mode is usedfor the control of step motor evaporator control valves, discharge bypassvalves or any other application suitable for single point temperature control.Since superheat control requires at least two sensors, superheat controlfor electric expansion valves cannot be accomplished with the TCB intemperature control mode.The TCB is capable of powering and controlling two valves, connect inparallel. The TCB has an operational range of -40°F to 210°F.For proper operation, the signal type and valve model must be selected fromTables 1 and 2, and the TCB configured accordingly.The TCB must be installed in a dry, protected environment. The boardwill operate properly in ambient conditions of -40°F to 140°F, with 90%relative humidity, non-condensing. The board should never be mounted ina corrosive atmosphere or in a location where frost buildup is likely. TheTCB is provided with four 1/8” mounting holes as shown in Figure 2. Non-metallic standoffs are suggested but not required. Minimum clearance fromthe bottom of the TCB to a conductive substrate or mounting panel is 3/16”.WIRING and POWER SUPPLY REQUIREMENTSScrew terminals suitable for up to 14 gauge wire are provided for all inputsand outputs. An isolated secondary 24 VAC 40 VA transformer must beused to power the board and valve. The transformer must not be used tosupply power to any other device. External control signal wiring to the TCBshould be kept as short as possible to prevent electrical noise and signalattenuation. The signal is polarized and care must be taken when connectingthe wires to the (+) and (-) screw terminals. Terminals are arranged fromtop to bottom when the board is positioned with the component side up, andthe terminal strip on the left as shown in Figure 1. Input signal requirementsare shown in Table 3.T emperaTure C onTrol B oard - Installation and Servicing Instructions1” max.3/16” min.Figure 2NOTE: Only one jumper is used.NOTE: L = left, R = right, C = centerWhen board is viewed as shown in Figure 1.fdeREPLACEMENT PARTS AND PARTS KITSThere are no user serviceable parts on the TCB, however, the accessories listed in Table 3 aid in the use and testing of the TCB/electric valve system.TROUBLESHOOTINGIf a step motor is suspected to have failed, a simple resistance check may be made of the motor windings, however, actual winding failures are rare. Therefore Sporlan developed a diagnostic instrument, the SMA-12, to test our step motors. The SMA-12 is a step motor actuator that will operate all 12 volt DC bipolar step motor valves, as well as test the continuity of the valve wiring and motor. The step rate can be selected at 1, 50, 100 or 200 steps-per-second. At the one step-per-second rate the SMA-12 will test the continuity of the valve wiring and motor. The SMA-12 can also be used to manually open, position, or shut the valve should the controller fail. If contaminants are suspected, the SMA-12 can be used to drive the valve fully open to purge the foreign material.NOTE: Pin 8 causes valve to open on temperature rise above set point. Pin 9 causes valve to close on temperature rise above set point.4-20 MILLIAMP - source controller must supply 20 milliamps at 12volts DC into a 600 Ohm load.NOTE: 20 milliamps at 24 volt DC is not suitable. 0-10 VOLT - signal must be supplied with at least 20 milliampcurrent. Wiring between controller and TCB must be kept short to minimize electrical noise.TTL - logical “1” must be a DC signal greater than 4.5volts for 3 milliseconds. Logical “0” must be less than 0.5 volts DC for 3 milliseconds.AC PULSE - Must be 120 volts AC ± 20% for a period of 3 to30 seconds.INPUT SIGNAL REQUIREMENTS50000010000200003000040000-6010080604020-20-40120200180160140Temperature (Degrees Fahrenheit)O h m sFigure 3TEMPERATURE SENSOR RESISTANCEWhen a system component does fail, it is important to first determine whether the failure is the valve, the TCB, or the external controller (if used).TEST THE VALVEThe resistance of the motor winding may be tested without opening the system.1. Remove power from the external controller and/or TCB.2. Remove the valve leads from TCB.3. Measure the resistance between the black and white leads of the valve. The resistance should be 75 Ohms for brass housed valves with the valve at room temperature or about 65 Ohms if the valve is at -40ºF. The resis-tance for stainless steel housed valves should be 100 Ohms with the valve at room temperature.4. Measure the resistance between the green and red leads. This value should be within ± 5% of the resistance between the black and white leads.5. Measure the resistance from any lead to valve body. Resistance should be infinite, that is to say, open.TEST THE TCBThe flow charts that follow are designed to assist in diagnosing a possible TCB failure. All measurements should be made with a Digital Multimeter .Boards manufactured after March 1, 2000 will have a pin jumper on both P5 and P6. The boards are shipped with the jumpers on one post of P5 & P6. With the pin jumpers in this position, the valve will close when the pumpdown relay is energized. If both P5 & P6 are enabled, the valve will open when the pumpdown relay is energized.For testing purposes, make sure the pin jumpers are on both posts of pins P5 & P6.Look at the date on the serial number label in the center of the board. If the date is prior to March 1, 2000, continue with steps 9 through 13. If the date is March 1, 2000 or later, go to step 14 and continue.TROUBLE SHOOTING GUIDE – TCB Operating on External Signal (4-20 ma or 0-10 VDC)*Note: Before testing the TCB, make certain the valve is operating. See “Test the Valve” instructions.Boards manufactured after March 1, 2000 will have a pin jumper on both P5 and P6. The boards are shipped with the jumpers on one post of P5 & P6. With the pin jumpers in this position, the valve will close when the pumpdown relay is energized. If both P5 & P6 are enabled, the valve will open when the pumpdown relay is energized.For testing purposes, make sure the pin jumpers are on both posts of pins P5 & P6.Look at the date on the serial number label in the center of the board. If the date is prior to March 1, 2000, continue with steps 9 TROUBLE SHOOTING GUIDE – TCB Operating as Standalone ControllerNote: Before testing the TCB, make certain the valve is operating. See “Test the Valve” instructions.。
RPCE07三位元方向控制阀说明书
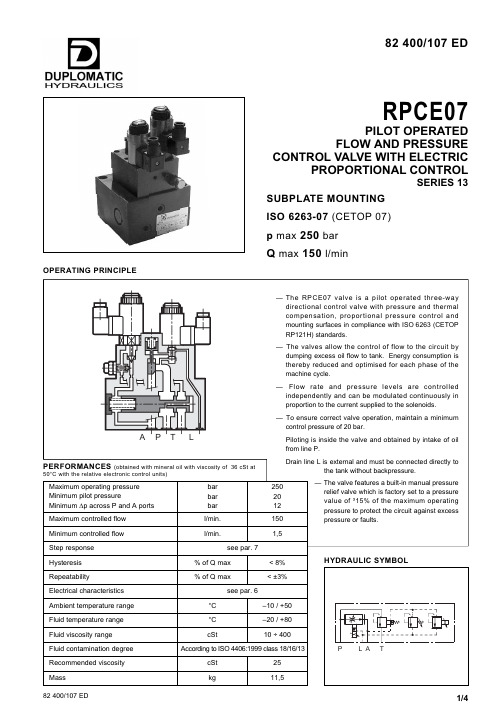
82 400/107 EDRPCE07PILOT OPERATEDFLOW AND PRESSURECONTROL VALVE WITH ELECTRICPROPORTIONAL CONTROLSERIES 13SUBPLATE MOUNTINGISO 6263-07 (CETOP 07)p max250barQ max150l/minOPERATING PRINCIPLE1 - IDENTIFICATION CODESeries No. (from 10 to 19 sizes andmounting dimensions remain unchanged)Pressure control range4= up to 140 bar 5= up to 250 barElectric proportional pressure control3-waycompensated flow control valveElectric proportional flow rate controlSize ISO 6263-07 (CETOP 07)2 - CHARACTERISTIC CURVES (measured with viscosity of 36 cSt at 50°C and UEIK-11 electronic control unit )RP C E 07-D/13Seal: omit for mineral oils V = viton for special fluids -24/Nominal solenoid voltage 24 V DC50100150200400200Q [l/min]I [mA]600800850100300500700FLOW CONTROL Q=f (I)Typical curve of flow control P →A according to current supplied to the solenoid.050100150200400250I [mA]600750100300500700p [bar]200PRESSURE CONTROL p=f (I)PRESSURE DROP ∆p=f(Q); FLOW P →TNOTE: The valve is preset at factory with a maximum current to the proportional solenoid of 750mA, to control the pressure.This setting must not exceeds the 750ma value.3 - PRESSURE COMPENSATIONThe valves are equipped with two restrictors in series. The first is an opening which can be adjusted by the proportional solenoid; the second, controlled by the pressure upstream and downstream of the first restrictor ensures constant pressure drop across the adjustable restrictor.In these conditions, the set flow rate value is maintained constant within a tolerance limit of ± 3% of the full scale flow rate for maximum pressure variation between the valve inlet and outlet chambers.4 - THERMAL COMPENSATIONA temperature-sensitive device installed on the flow control element of the valve corrects the position to maintain the set flow rate virtually unchanged, also in the case of fluid viscosity variation.Flow rate variation is therefore maintained within ± 2,5% of the set flow rate.Curve obtained with port A closed, zero current to the pressure control proportional solenoid and maximum current to the flow control proportional solenoid.Curve obtained with zero current to both the proportionalsolenoids.6 - ELECTRICAL CHARACTERISTICS7 - STEP RESPONSE (with mineral oil with viscosity of 36 cSt at 50°C inconjunction with the relative electronic control unit)8 - INSTALLATIONProportional solenoidThe proportional solenoid comprises two parts: tube and coil.The tube, screwed to the valve body, contains the armature which is designed to maintain friction to a minimum thereby reducing hysteresis.The coil is mounted on the tube secured by means of a lock nut and can be rotated through 360° depending on installation clearances.7.1 - Flow step responseStep response is the time taken for the valve to reach 90% of the set pressure value following a step change of reference signal.The table shows typical response times with an inlet flow of 100l/min and a backpressure of 50 bar on the A port.7.2 - Pressure step responseStep response is the time taken for the valve to reach 90% of the set pressure value following a step change of reference signal.The table shows typical response times with a flow of 50 l/min and the A port closed.The RPCE07 valve can be installed in any position without impairing correct operation.Ensure that there is no air in the hydraulic circuit. In particular applications, it can be necessary to vent the air entrapped in the solenoid tube, by using the apposite drain screw in the solenoid tube. Ensure that the solenoid tube is always filled with oil (see par.9). At the end of the operation, make sure of having screwed correctly the drain screw.Connect the L port on the valve directly to the tank without backpressure.5 - HYDRAULIC FLUIDSUse mineral oil-based hydraulic fluids HL or HM type, according to ISO 6743-4. For these fluids, use NBR seals.For fluids HFDR type (phosphate esters) use FPM seals (code V).For the use of other fluid types such as HFA, HFB, HFC, please consult our technical department.Using fluids at temperatures higher than 80 °C causes a faster degradation of the fluid and of the seals characteristics.The fluid must be preserved in its physical and chemical characteristics.Valves are fixed by means of screws or tie rods on a flat surface with planarity and/or roughness equal to or better than those indicated in the relative symbols. If minimum values are not observed fluid can easily leak between the valve and support surface.10 - ELECTRONIC CONTROL UNITS(valid for both flow rate and pressure controls)RPCE07SERIES 139 - OVERALL AND MOUNTING DIMENSIONSDUPLOMATIC OLEODINAMICA SpA20025 LEGNANO (MI) - P.le Bozzi, 1 / Via Edison Tel. 0331/472111-472236 - Fax 0331/548328。
MVP3300系列阀门定位器说明书
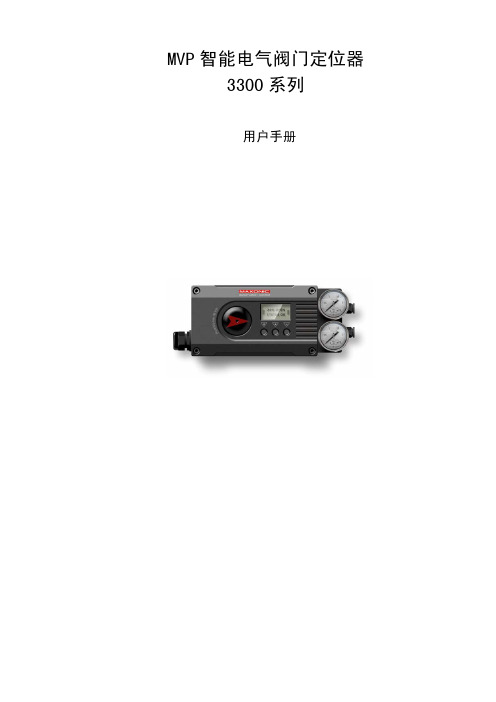
MVP智能电气阀门定位器3300系列用户手册1用户须知 (1)1.1安全指示 (1)1.2开箱清单 (1)1.3重要信息提示 (1)2概述 (1)2.1功能介绍 (2)2.2特点 (2)3技术参数 (2)4安装说明 (3)4.1外形尺寸 (3)4.2机构安装 (4)4.3气路连接 (7)4.4电气连接 (7)5调节操作 (9)5.1操作界面说明 (9)5.2用户菜单 (10)5.3初始化 (12)5.4诊断 (14)5.5报警 (14)5.6参数列表 (16)6参数解释 (17)7使用异常与维护保养 (20)7.1异常状况排除 (20)7.2维护保养 (21)8运输和贮存 (21)9订货须知 (22)9.1产品型号 (22)9.2其它可选项 (22)1用户须知1.1安全指示定位器先上电,后供气源;产品使用过程中,不要随意的触摸反馈连接装置;产品必须正确安装、正确操作和正确维护。
1.2开箱清单MVP智能阀门定位器;安装配件;用户手册;另外订制附件,详见装箱清单。
1.3重要信息提示为了您能更好地应用这份说明,以及保障你在调试,运行和维修这台仪器时的安全,请注意下列符号的用途:符号标语解说注意注意注意指潜在的危险,如不能避免,可能会损害产品本身或周围物体。
(危险物)提示提示提示是指有用的或特别的被忽视的能影响操作条件或产品功能的事物。
(不包含危险的或有害的情形)在安装和调试前请认真阅读此手册。
2概述MVP智能阀门定位器为深圳万讯自控有限公司推出的智能型两线制现场仪表。
本定位器作为气动阀门的配套控制部件,广泛运用于石油、化工、电力、冶金、轻工等领域的自动控制系统中。
MVP智能阀门定位器接受来自控制系统的4~20mA阀位设定信号,通过A/D转换得到阀位设定值;同时通过位置传感器得到实际的阀位信号;两者经过控制软件的计算处理,从而控制气动执行机构的进气与排气,驱动阀位到达设定点(如图1所示)MVP智能阀门定位器是基于微处理器技术的高性能电/气阀门定位器,能很好地克服摩擦力和阀芯上的不平衡力,提高调节阀的响应速度,使其定位迅速准确。
阀门电动装置说明书
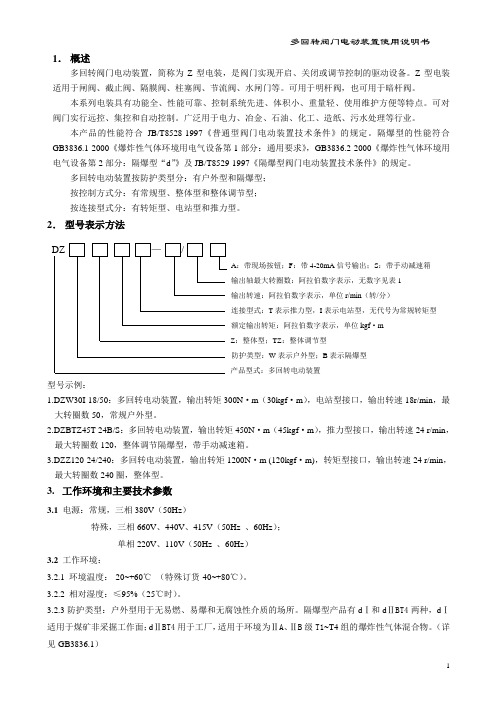
1.概述多回转阀门电动装置,简称为Z型电装,是阀门实现开启、关闭或调节控制的驱动设备。
Z型电装适用于闸阀、截止阀、隔膜阀、柱塞阀、节流阀、水闸门等。
可用于明杆阀,也可用于暗杆阀。
本系列电装具有功能全、性能可靠、控制系统先进、体积小、重量轻、使用维护方便等特点。
可对阀门实行远控、集控和自动控制。
广泛用于电力、冶金、石油、化工、造纸、污水处理等行业。
本产品的性能符合JB/T8528-1997《普通型阀门电动装置技术条件》的规定。
隔爆型的性能符合GB3836.1-2000《爆炸性气体环境用电气设备第1部分:通用要求》,GB3836.2-2000《爆炸性气体环境用电气设备第2部分:隔爆型“d”》及JB/T8529-1997《隔爆型阀门电动装置技术条件》的规定。
多回转电动装置按防护类型分:有户外型和隔爆型;按控制方式分:有常规型、整体型和整体调节型;按连接型式分:有转矩型、电站型和推力型。
2.型号表示方法A:带现场按钮;F:带4-20mA信号输出;S:带手动减速箱输出轴最大转圈数:阿拉伯数字表示,无数字见表1输出转速:阿拉伯数字表示,单位r/min(转/分)连接型式:T表示推力型,I表示电站型,无代号为常规转矩型额定输出转矩:阿拉伯数字表示,单位kgf·mZ:整体型;TZ:整体调节型防护类型:W表示户外型;B表示隔爆型产品型式:多回转电动装置型号示例:1.DZW30I-18/50:多回转电动装置,输出转矩300N·m(30kgf·m),电站型接口,输出转速18r/min,最大转圈数50,常规户外型。
2.DZBTZ45T-24B/S:多回转电动装置,输出转矩450N·m(45kgf·m),推力型接口,输出转速24 r/min,最大转圈数120,整体调节隔爆型,带手动减速箱。
3.DZZ120-24/240:多回转电动装置,输出转矩1200N·m (120kgf·m),转矩型接口,输出转速24 r/min,最大转圈数240圈,整体型。
MK系列空气阀门控制值用户操作和维护指南说明书
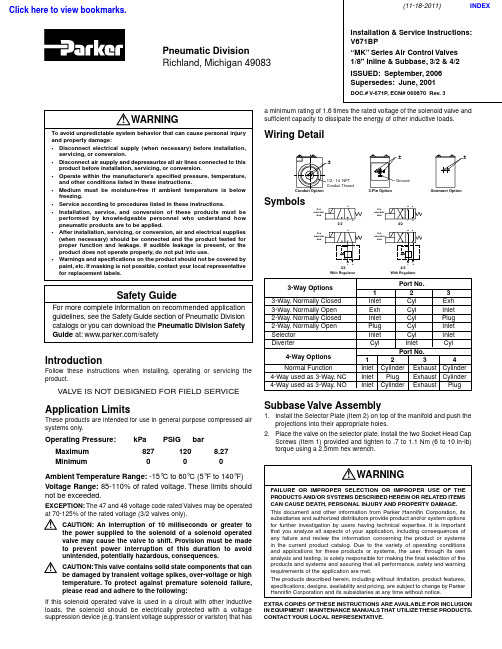
3/2With Regulator 3/24/2With Regulator4/2Installation & Service Instructions: V671BP“MK” Series Air Control Valves 1/8" Inline & Subbase, 3/2 & 4/2ISSUED: September, 2006 Supersedes: June, 2001DOC.# V-671P, ECN# 060870 Rev. 3Pneumatic DivisionRichland, Michigan 49083IntroductionFollow these instructions when installing, operating or servicing the product.VALVE IS NOT DESIGNED FOR FIELD SERVICEApplication LimitsThese products are intended for use in general purpose compressed air systems only.Operating Pressure: kPa PSIG barMaximum 827 120 8.27MinimumAmbient Temperature Range: -15°C to 60°C (5°F to 140°F)Voltage Range: 85-110% of rated voltage. These limits should not be exceeded.EXCEPTION: The 47 and 48 voltage code rated Valves may be operated at 70-125% of the rated voltage (3/2 valves only).CAUTION: An interruption of 10 milliseconds or greater to the power supplied to the solenoid of a solenoid operated valve may cause the valve to shift. Provision must be made to prevent power interruption of this duration to avoid unintended, potentially hazardous, consequences.CAUTION: This valve contains solid state components that can be damaged by transient voltage spikes, over-voltage or high temperature. To protect against premature solenoid failure, please read and adhere to the following:If this solenoid operated valve is used in a circuit with other inductive loads, the solenoid should be electrically protected with a voltage suppression device (e.g. transient voltage suppressor or varistor) that hasa minimum rating of 1.6 times the rated voltage of the solenoid valve and sufficient capacity to dissipate the energy of other inductive loads.Wiring DetailSymbols3-Way OptionsPort No.1 2 3 3-Way, Normally Closed Inlet Cyl Exh 3-Way, Normally Open Exh Cyl Inlet 2-Way, Normally Closed Inlet Cyl Plug 2-Way, Normally Open Plug Cyl Inlet Selector Inlet Cyl Inlet DiverterCyl InletCyl 4-Way OptionsPort No.1 2 3 4 Normal FunctionInlet Cylinder Exhaust Cylinder 4-Way used as 3-Way, NC Inlet Plug Exhaust Cylinder4-Way used as 3-Way, NOInlet Cylinder ExhaustPlugSubbase Valve Assembly1. Install the Selector Plate (Item 2) on top of the manifold and push theprojections into their appropriate holes.2. Place the valve on the selector plate. Install the two Socket Head CapScrews (Item 1) provided and tighten to .7 to 1.1 Nm (6 to 10 in-lb) torque using a 2.5mm hex wrench.WARNING To avoid unpredictable system behavior that can cause personal injuryand property damage:• Disconnect electrical supply (when necessary) before installation, servicing, or conversion.• Disconnect air supply and depressurize all air lines connected to this product before installation, servicing, or conversion.• Operate within the manufacturer’s specified pressure, temperature, and other conditions listed in these instructions.• Medium must be moisture-free if ambient temperature is below freezing.• Service according to procedures listed in these instructions.• Installation, service, and conversion of these products must be performed by knowledgeable personnel who understand how pneumatic products are to be applied.• After installation, servicing, or conversion, air and electrical supplies (when necessary) should be connected and the product tested for proper function and leakage. If audible leakage is present, or the product does not operate properly, do not put into use.• Warnings and specifications on the product should not be covered by paint, etc. If masking is not possible, contact your local representative for replacement labels.!WARNINGFAILURE OR IMPROPER SELECTION OR IMPROPER USE OF THEPRODUCTS AND/OR SYSTEMS DESCRIBED HEREIN OR RELATED ITEMS CAN CAUSE DEATH, PERSONAL INJURY AND PROPERTY DAMAGE.This document and other information from Parker Hannifin Corporation, its subsidiaries and authorized distributors provide product and/or system options for further investigation by users having technical expertise. It is important that you analyze all aspects of your application, including consequences of any failure and review the information concerning the product or systems in the current product catalog. Due to the variety of operating conditions and applications for these products or systems, the user, through its own analysis and testing, is solely responsible for making the final selection of the products and systems and assuring that all performance, safety and warning requirements of the application are met.The products described herein, including without limitation, product features, specifications, designs, availability and pricing, are subject to change by Parker Hannifin Corporation and its subsidiaries at any time without notice.EXTRA COPIES OF THESE INSTRUCTIONS ARE AVAILABLE FOR INCLUSION IN EQUIPMENT / MAINTENANCE MANUALS THAT UTILIZE THESE PRODUCTS. CONTACT YOUR LOCAL REPRESENTATIVE.!Safety GuideFor more complete information on recommended application guidelines, see the Safety Guide section of Pneumatic Division catalogs or you can download the Pneumatic Division Safety Guide at: /safety!!(11-18-2011)INDEXClick here to view bookmarks.3. When DIN Rail Mounting Bracket is provided: install Screws(Item 9) through the Manifold and secure the DIN Rail Connecting Bracket (Item 10) on both ends of the Manifold.4. When Regulator Kit is provided: Install the two O-rings provided(Item 3) into the slots on the Regulator Housing (Item 4). Install the Regulator Housing (Item 4) using the two Mounting Screws (Item 5) and tighten to .7 to 1.1 Nm (6 to 10 in-lb) torque using a 2.5mm hex wrench. Install the Regulator (Item 6) into the Housing (Item 4) and torque to1.7 to 2.3 Nm (15 to 20 in-lb).5. When Gauge Kit is provided: Install the appropriate Pipe Fitting(Item 8) into the Regulator Housing (Item 4) Install the Gauge (Item 7) on to the Pipe Fitting.6. T est valve for functional operation and for internal and external leakage. If leakage is audible (likely indicating improper assembly) do not operate – conduct assembly again.If in-service lubricant is used, F442 oil is recommended. F442 is specially formulated to promote maximum service life of air operated equipment. Other compatible lubricants should be of straight paraffin base mineral oil having a viscosity of 100-200 SSU @ 100°F and an Aniline Point greater than 200°F . CAUTION: Do not use synthetic, reconstituted, or oils with alcohol content or detergent additives.Subbase Kits AvailableKit No. Description PS2105P ....................................................3/2 NC Selector Plate Kit PS2106P ...................................................3/2 NO Selector Plate Kit PS2109P ...............................................Regulator Blanking Plate Kit PS2131122P ........................Regulator Kit Without Gauge, 2-60 PSI PS2131133P ......................Regulator Kit Without Gauge, 5-125 PSI PS2131155P .............................Regulator Kit With Gauge, 2-60 PSI PS2131166P ...........................Regulator Kit With Gauge, 5-125 PSI PS2188P ...................................................Valve to Subbase Bolt Kit PS2194P ..........................................3/2 Subbase Blanking Plate Kit PS219401P ......................................4/2 Subbase Blanking Plate Kit PS2195P ..............................................10-32 Extension Kit (10 / Kit)PS2196P ..................................................Swivel Adapter Kit (5 / Kit)Instructions for Converting NC to NO - 3/2 Valves OnlySelector Plates (Item 2) can be changed to convert function. Remove the Valve Body Assembly from the Base by removing the two Body / Manifold Screws (Item 1). Remove the existing Selector Plate (Item 2). Place the new Selector Plate with the appropriate function on the Subbase. The function can be read on this Selector Plate when viewed from the side opposite the Solenoid. Replace the Valve Assembly on the Selector Plate. Reinstall the two Screws (Item 1) and tighten .7 to 1.1 Nm (6 to 10 in-lb) torque. Turn on air pressure and electrical powersource. Test valve for proper functional operation and for internal and external leakage.Inline Valve on Inlet / Exhaust Manifold Assembly1. Install two of the four O-rings (Item 12) in the counterbores on top ofthe Manifold.2. Place the Valve on the Manifold. For normally closed operation(3/2 Valves), line up the Solenoid end of the Valve with the Port 1 on the Manifold. For normally open operation (3/2 valves only), line up the Solenoid end of the Valve with the Port 3 on the manifold. Install the two Socket Head Cap Screws (Item 11) provided and tighten to 1.5 to 1.9 Nm (13 to 17 in-lb) torque using a 2.5mm hex wrench. For 4/2 valves, the Solenoid end on the Valve must always line up with Port 1 of the Manifold.3. When DIN Rail Mounting Bracket is provided, install Screws (Item 14)through the Manifold and secure the DIN Rail Connecting Bracket (Item 10) on both ends of the Manifold.4. When Sandwich Regulator Kit is provided: Install the Sandwich (Item15) on top of the Manifold (Item 13). Line up Port 1 on the Manifold with the Regulator end of the Sandwich. Install the remaining two of the four O-rings provided (Item 12) into the slots on top of the Sandwich. Install the two Mounting Screws (Item 11) and tighten to 1.5 to 1.9 Nm (13 to 17 in-lb) torque using a 2.5mm hex wrench. The 3-Way valve can be oriented as described in paragraph (2) for NO or NC operation. Install the Regulator (Item 6) into the Sandwich (Item 15) and torque to1.7 to 2.3 Nm (15 to 20 in-lb).5. When Gauge is provided: Install the Gauge (Item 7) directly intothe Sandwich Regulator Housing (Item 15), or install Pipe Nipples (Item 8) (Items not shown) to Gauge port then to Gauge. Gauge diameter is larger than Regulator width, so Gauge mounting must be staggered.6. Test valve for functional operation and for internal and externalleakage. If leakage is audible (most likely indicating improper assembly) do not operate – conduct assembly again.7. When Selector Sandwich is required, install similar to Item 15. TheSelector Sandwich allows selective isolation of either the inlet or exhaust or both, when Sandwich is between valve and IEM.IEM Kits AvailableKit No. DescriptionPS2130122P .............................Regulator Kit Without Gauge, 2-60 PSI PS2130133P ...........................Regulator Kit Without Gauge, 5-125 PSI PS2130155P ..................................Regulator Kit With Gauge, 2-60 PSI PS2130166P ................................Regulator Kit With Gauge, 5-125 PSI PS2144P ..............................................................Selector Sandwich Kit PS2166P .........................3/2 or 4/2 IEM NPT Ported Blanking Plate Kit PS2169P .............................................3/2 or 4/2 IEM Blanking Plate Kit PS2184P ............................3/2 or 4/2 Valve to IEM O-Ring Kit (10 / Kit)PS2187P ..................................3/2 or 4/2 Valve to IEM Bolt Kit (10 / Kit)PS2190P ....................................Din Rail Mounting Kit, Subbase & IEM!“MK” Series Air Control Valves 1/8" Inline & Subbase , 3/2 & 4/2 V-671BPShownPneumatic DivisionRichland, Michigan 49083 269-629-5000PDNSG-1Safety Guide For Selecting And Using Pneumatic Division Products And Related AccessoriesWARNING:FAILURE OR IMPROPER SELECTION OR IMPROPER USE OF PNEUMATIC DIVISION PRODUCTS, ASSEMBLIES OR RELATED ITEMS (“PRODUCTS”) CAN CAUSE DEATH, PERSONAL INJURY, AND PROPERTY DAMAGE. POSSIBLE CONSEQUENCES OF FAILURE OR IMPROPER SELECTION OR IMPROPER USE OF THESE PRODUCTS INCLUDE BUT ARE NOT LIMITED TO:• Unintended or mistimed cycling or motion of machine members or failure to cycle • Work pieces or component parts being thrown off at high speeds.• Failure of a device to function properly for example, failure to clamp or unclamp an associated item or device.• Explosion• Suddenly moving or falling objects.• Release of toxic or otherwise injurious liquids or gasses.Before selecting or using any of these Products, it is important that you read and follow the instructions below.1. GENERAL INSTRUCTIONS1.1. Scope: This safety guide is designed to cover general guidelines on the installation, use, and maintenance of Pneumatic Division Valves, FRLs (Filters, Pressure Regulators, and Lubricators), Vacuum products and related accessory components.1.2. Fail-Safe: Valves, FRLs, Vacuum products and their related components can and do fail without warning for many reasons. Design all systems and equipment in a fail-safe mode, so that failure of associated valves, FRLs or Vacuum products will not endanger persons or property.1.3 Relevant International Standards: For a good guide to the application of a broad spectrum of pneumatic fluid power devices see: ISO 4414:1998, Pneumatic Fluid Power – General Rules Relating to Systems. See for ordering information.1.4. Distribution: Provide a copy of this safety guide to each person that is responsible for selection, installation, or use of Valves, FRLs or Vacuum products. Do not select, or use Parker valves, FRLs or vacuum products without thoroughly reading and understanding this safety guide as well as the specific Parker publications for the products considered or selected.1.5. User Responsibility: Due to the wide variety of operating conditions and applications for valves, FRLs, and vacuum products Parker and its distributors do not represent or warrant that any particular valve, FRL or vacuum product is suitable for any specific end use system. This safety guide does not analyze all technical parameters that must be considered in selecting a product. The user, through its own analysis and testing, is solely responsible for: • Making the final selection of the appropriate valve, FRL, Vacuum component, or accessory. • Assuring that all user’s performance, endurance, maintenance, safety, and warning requirements are met and that the application presents no health or safety hazards. • Complying with all existing warning labels and / or providing all appropriate health and safety warnings on the equipment on which the valves, FRLs or Vacuum products are used; and, • Assuring compliance with all applicable government and industry standards. 1.6. Safety Devices: Safety devices should not be removed, or defeated.1.7. Warning Labels: Warning labels should not be removed, painted over or otherwise obscured.1.8. Additional Questions: Call the appropriate Parker technical service department if you have any questions or require any additional information. See the Parker publication for the product being considered or used, or call 1-800-CPARKER, or go to , for telephone numbers of the appropriate technical service department.2. PRODUCT SELECTION INSTRUCTIONS2.1. Flow Rate: The flow rate requirements of a system are frequently the primary consideration when designing any pneumatic system. System components need to be able to provide adequate flow and pressure for the desired application.2.2. Pressure Rating: Never exceed the rated pressure of a product. Consult product labeling, Pneumatic Division catalogs or the instruction sheets supplied for maximum pressure ratings.2.3. Temperature Rating: Never exceed the temperature rating of a product. Excessive heat can shorten the life expectancy of a product and result in complete product failure.2.4. Environment: Many environmental conditions can affect the integrity and suitability of a product for a given application. Pneumatic Division products are designed for use in general purpose industrial applications. If these products are to be used in unusual circumstances such as direct sunlight and/or corrosive or caustic environments, such use can shorten the useful life and lead to premature failure of a product.2.5. Lubrication and Compressor Carryover: Some modern synthetic oils can and will attack nitrile seals. If there is any possibility of synthetic oils or greases migrating into the pneumatic components check for compatibility with the seal materials used. Consult the factory or product literature for materials of construction.2.6. Polycarbonate Bowls and Sight Glasses: To avoid potential polycarbonate bowl failures: • Do not locate polycarbonate bowls or sight glasses in areas where they could be subject to direct sunlight, impact blow, or temperatures outside of the rated range. • Do not expose or clean polycarbonate bowls with detergents, chlorinated hydro-carbons, keytones, esters or certain alcohols. • Do not use polycarbonate bowls or sight glasses in air systems where compressors are lubricated with fire resistant fluids such as phosphate ester and di-ester lubricants.!PDNSG-1Pneumatic Division Safety Guide ISSUED: August 1 , 2006Supersedes: June 1, 2006Pneumatic Division Safety Guide2.7. Chemical Compatibility: For more information on plastic component chemical compatibility see Pneumatic Division technical bulletinsTec-3, Tec-4, and Tec-52.8. Product Rupture: Product rupture can cause death, serious personal injury, and property damage.• Do not connect pressure regulators or other Pneumatic Division products to bottled gas cylinders.• Do not exceed the maximum primary pressure rating of any pressure regulator or any system component.• Consult product labeling or product literature for pressure rating limitations.3. PRODUCT ASSEMBLY AND INSTALLATION INSTRUCTIONS3.1. Component Inspection: Prior to assembly or installation a careful examination of the valves, FRLs or vacuum products must beperformed. All components must be checked for correct style, size, and catalog number. DO NOT use any component that displays any signs of nonconformance.3.2. Installation Instructions: Parker published Installation Instructions must be followed for installation of Parker valves, FRLs andvacuum components. These instructions are provided with every Parker valve or FRL sold, or by calling 1-800-CPARKER, or at.3.3. Air Supply: The air supply or control medium supplied to Valves, FRLs and Vacuum components must be moisture-free if ambienttemperature can drop below freezing4. VALVE AND FRL MAINTENANCE AND REPLACEMENT INSTRUCTIONS4.1. Maintenance: Even with proper selection and installation, valve, FRL and vacuum products service life may be significantly reducedwithout a continuing maintenance program. The severity of the application, risk potential from a component failure, and experience with any known failures in the application or in similar applications should determine the frequency of inspections and the servicing or replacement of Pneumatic Division products so that products are replaced before any failure occurs. A maintenance program must be established and followed by the user and, at minimum, must include instructions 4.2 through 4.10.4.2. Installation and Service Instructions: Before attempting to service or replace any worn or damaged parts consult the appropriateService Bulletin for the valve or FRL in question for the appropriate practices to service the unit in question. These Service andInstallation Instructions are provided with every Parker valve and FRL sold, or are available by calling 1-800-CPARKER, or by accessing the Parker web site at .4.3. Lockout / Tagout Procedures: Be sure to follow all required lockout and tagout procedures when servicing equipment. For moreinformation see: OSHA Standard – 29 CFR, Part 1910.147, Appendix A, The Control of Hazardous Energy – (Lockout / Tagout)4.4. Visual Inspection: Any of the following conditions requires immediate system shut down and replacement of worn or damagedcomponents:• Air leakage: Look and listen to see if there are any signs of visual damage to any of the components in the system. Leakage is an indication of worn or damaged components.• Damaged or degraded components: Look to see if there are any visible signs of wear or component degradation.• Kinked, crushed, or damaged hoses. Kinked hoses can result in restricted air flow and lead to unpredictable system behavior.• Any observed improper system or component function: Immediately shut down the system and correct malfunction.• Excessive dirt build-up: Dirt and clutter can mask potentially hazardous situations.Caution: Leak detection solutions should be rinsed off after use.4.5. Routine Maintenance Issues:• Remove excessive dirt, grime and clutter from work areas.• Make sure all required guards and shields are in place.4.6. Functional Test: Before initiating automatic operation, operate the system manually to make sure all required functions operateproperly and safely.4.7. Service or Replacement Intervals: It is the user’s responsibility to establish appropriate service intervals. Valves, FRLs and vacuumproducts contain components that age, harden, wear, and otherwise deteriorate over time. Environmental conditions can significantly accelerate this process. Valves, FRLs and vacuum components need to be serviced or replaced on routine intervals. Service intervals need to be established based on:• Previous performance experiences.• Government and / or industrial standards.• When failures could result in unacceptable down time, equipment damage or personal injury risk.4.8. Servicing or Replacing of any Worn or Damaged Parts: To avoid unpredictable system behavior that can cause death, personalinjury and property damage:• Follow all government, state and local safety and servicing practices prior to service including but not limited to all OSHA Lockout Tagout procedures (OSHA Standard – 29 CFR, Part 1910.147, Appendix A, The Control of Hazardous Energy – Lockout / Tagout).• Disconnect electrical supply (when necessary) before installation, servicing, or conversion.• Disconnect air supply and depressurize all air lines connected to system and Pneumatic Division products before installation, service, or conversion.• Installation, servicing, and / or conversion of these products must be performed by knowledgeable personnel who understand how pneumatic products are to be applied.• After installation, servicing, or conversions air and electrical supplies (when necessary) should be connected and the product tested for proper function and leakage. If audible leakage is present, or if the product does not operate properly, do not put product orsystem into use.• Warnings and specifications on the product should not be covered or painted over. If masking is not possible, contact your localrepresentative for replacement labels.4.9. Putting Serviced System Back into Operation: Follow the guidelines above and all relevant Installation and Maintenance Instructionssupplied with the valve FRL or vacuum component to insure proper function of the system.。
MA3系列水力阀门 Mill Type 圆线阀门操作指南说明书
MANUAL2Parker HannifinCylinder Division EuropeManual'Mill Type' CylindersMA3 SeriesHydraulic Cylinder Operating InstructionsFitting and commissioning is to be carried out by qualified personnel only, in accordance with the operating instructions.1. Mounting and connections1.1 Mounting of actuator depends on the options selected: – Flange – Pivot– Foot1.2 Hydraulic ports are in each end cap.1.3 Connecting the load: use the mounting thread on the piston rod.1.4 Cushion adjusting screws are fitted in the head and/ or cap, where specified.1.5 Air bleed screws are fitted in the head and/or cap, where specified.1.6 Stroke adjusters are fitted in end caps, where specified.1.7 Electrical connector for transducer, where specified.2. FunctionPressurized fluid is applied to a circular piston inside a cylinder which pushes the rod. This action moves the piston genera-ting linear motion. This linear motion and force is transmitted to the application by the rod. Where specified, the sensor provides a signal which indicates stroke position. This signal may be analogue or digital.3. General conditions of useThese general recommendations for the correct and safe use of the product must be observed at all times:– Comply with the limits specified in the catalogue. – Ensure the hydraulic fluid supplied meets the specified cleanliness level. – Ensure the correct seal class has been specified for the hydraulic fluid used. – Ensure that the actuator is suitable for the prevailing ambient conditions. – Comply with the national and local safety laws and regulations. – Remove all transport packaging. All packaging material used is recyclable. – Maintain the fluid specified for the complete service life of the product.4. InstallationMechanical– Check that the cylinder model code meets the specification required.– Handle the cylinder with care in order to prevent damage to the cylinder tube and piston rod which could reduce reliability and safe operation.– Mount the cylinder so that all control elements are always accessible.– Mount the cylinder so that there is no misalignment between the rod and its mating fitting.– Tighten screws, lock nuts and accessories to the torques specified in the maintenance manual.Hydraulic – Tube and hose fittings are to be screwed directly into the pressure ports of the cylinder end caps. – Fill the cylinder slowly in order to preventuncontrolled movements.ElectricIf a sensor is fitted, ensure that the cable is not energized when attaching the cable to the sensor connector.5. Commissioning Complete SystemSlowly fill the complete hydraulic system with oil in order to prevent any uncontrolled movements. During the filling opera-tion, the system and/or cylinder must be bled of air at suitable points.Hydraulic Cylinder – Make sure that the area traversed by the rod and attached mass is clear of personnel or any obstructing bodies. – Start a test run.– If necessary adjust the cushion screw to achieve optimal performance. The purpose of the cushion adjustment is to ensure that the cylinder achieves full stroke without striking the cap too hard.– If fitted, use the stroke adjusters to achieve the stroke required. It is recommended that hydraulic pressure should be released before makingadjustments.– CAUTION : During all adjustments ensure that theoperator is clear of the area traversed by the moving mass.6. Operation6.1 Make sure that the area traversed by the moving mass is clear of personnel or any obstructing bodies. Only handle the cylinder when all movement has ceased.6.2 Ensure that the oil and ambient temperature is within the temperature range of the cylinder fitted.6.3 Make sure that the pressure indicated on the model plate is not exceeded.7. Maintenance7.1 The cylinder must be regularly checked for leaks. If seals are leaking they must be replaced according to the maintenance bulletins (see 9)7.2 Ensure the hydraulic fluid supplied meets the specified cleanliness level. Filtration to ISO Class 17/14.7.3 Ensure that all maintenance work is in compliance with the national environmental and safety regulations.7.4 Any further instructions, see maintenance bulletin referred to in 7.1.3Parker HannifinCylinder Division EuropeManual'Mill Type' CylindersMA3 SeriesWARNING – USER RESPONSIBILITYFAILURE OR IMPROPER SELECTION OR IMPROPER USE OF THE PRODUCTS DESCRIBED HEREIN OR RELATED ITEMS CAN CAUSE DEATH, PERSONAL INJURY AND PROPERTY DAMAGE.This document and other information from Parker-Hannifin Corporation, its subsidiaries and authorized distributors provide product or system options for further investigation by users having technical expertise.The user, through its own analysis and testing, is solely responsible for making the final selection of the system and components andassuring that all performance, endurance, maintenance, safety and warning requirements of the application are met. The user must analyze all aspects of the application, follow applicable industry standards, and follow the information concerning the product in the current product catalog and in any other materials provided from Parker or its subsidiaries or authorized distributors.To the extent that Parker or its subsidiaries or authorized distributors provide component or system options based upon data or speci-fications provided by the user, the user is responsible for determining that such data and specifications are suitable and sufficient for all applications and reasonably foreseeable uses of the components or systems.Offer of SalePlease contact your Parker representation for a detailed 'Offer of Sale'.8. Disassembly and Repairs8.1 For any further instructions see maintenance bulletin referred to in 7.1.8.2 Use original Parker spare parts only. For any further advice, please contact your nearest Parker Sales office.9. Corrective Actions10. Technical DataSee catalogue: MSG1910-0262Parker Hannifin Ltd. Tachbrook Park Drive Tachbrook Park, Warwick, CV34 6TU United KingdomTel.: +44 (0) 1926 317 Manual MA3Your local authorized Parker distributor© 2020 Parker Hannifin Corporation. All rights reserved.European Product Information Centre Free phone: 00 800 27 27 5374(from AT, BE, CH, CZ, DE, DK, EE, ES, FI, FR, IE, IL, IS, IT, LU, MT, NL, NO, PL, PT, RU, SE, SK, UK, ZA)Europe, Middle East, AfricaAE – United Arab Emirates, DubaiTel: +971 4 8127100AT – Austria, St. Florian Tel: +43 (0)7224 66201 AZ – Azerbaijan, Baku Tel: +994 50 2233 458BE/NL/LU – Benelux, Hendrik Ido Ambacht Tel: +31 (0)541 585 000BY – Belarus, Minsk Tel: +48 (0)22 573 24 00CH – Switzerland, Etoy Tel: +41 (0)21 821 87 00 CZ – Czech Republic, PragueTel: +420 284 083 111DE – Germany, Kaarst Tel: +49 (0)2131 4016 0DK – Denmark, Ballerup Tel: +45 43 56 04 00ES – Spain, Madrid Tel: +34 902 330 001FI – Finland, Vantaa Tel: +358 (0)20 753 2500FR – France, Contamine s/Arve Tel: +33 (0)4 50 25 80 25GR – GreeceTel: +30 69 44 52 78 25HU – Hungary, Budaörs Tel: +36 23 885 470IE – Ireland, Dublin Tel: +353 (0)1 466 6370IL – IsraelTel: +39 02 45 19 21IT – Italy, Corsico (MI) Tel: +39 02 45 19 21KZ – Kazakhstan, Almaty Tel: +7 7273 561 000NO – Norway, Asker Tel: +47 66 75 34 00PL – Poland, Warsaw Tel: +48 (0)22 573 24 00PT – PortugalTel: +351 22 999 7360RO – Romania, Bucharest Tel: +40 21 252 1382RU – Russia, Moscow Tel: +7 495 645-2156SE – Sweden, Borås Tel: +46 (0)8 59 79 50 00SL – Slovenia, Novo Mesto Tel: +386 7 337 6650TR – Turkey, Istanbul Tel: +90 216 4997081UK – United Kingdom, Warwick Tel: +44 (0)1926 317 878ZA – South Africa, Kempton Park Tel: +27 (0)11 961 0700North AmericaCA – Canada, Milton, Ontario Tel: +1 905 693 3000US – USA, Cleveland Tel: +1 216 896 3000Asia PacificAU – Australia, Castle Hill Tel: +61 (0)2-9634 7777CN – China, Shanghai Tel: +86 21 2899 5000HK – Hong Kong Tel: +852 2428 8008IN – India, MumbaiTel: +91 22 6513 7081-85JP – Japan, Tokyo Tel: +81 (0)3 6408 3901KR – South Korea, Seoul Tel: +82 2 559 0400MY – Malaysia, Shah Alam Tel: +60 3 7849 0800NZ – New Zealand, Mt Wellington Tel: +64 9 574 1744SG – Singapore Tel: +65 6887 6300TH – Thailand, Bangkok Tel: +662 186 7000TW – Taiwan, Taipei Tel: +886 2 2298 8987Parker WorldwideSouth AmericaAR – Argentina, Buenos Aires Tel: +54 3327 44 4129BR – Brazil, Sao Jose dos Campos Tel: +55 080 0727 5374CL – Chile, Santiago Tel: +56 22 303 9640MX – Mexico, TolucaTel: +52 72 2275 4200。
多功能阀中文操作手册
普罗名特® 多功能阀操 作 手 册P r o M i n e n t®目录1结构设计 (1)2功能描述 (1)3使用范围 (2)4安装 (3)5操作 (3)6技术参数和订货号 (4)1结构设计多功能阀通过弹簧负载的隔膜实现其每个功能。
阀的卸压机构具有保持压力恒定以及卸压的功能。
2功能描述功能- 敞口计量时,产生一个稳定的背压。
顺时针方向旋转黑色星状旋钮(1)可取消此项功能。
- 防止投加点产生负压时从药桶中抽出药液。
顺时针方向旋转黑色星状旋钮(1)可取消此项功能。
注意背压阀不能用作完全密封截止阀。
1 2如果不向投加点输送计量介质或泵的待机时间长,则必须在泵的吸入端另外安装截止阀。
- 启动泵时克服压力辅助引液,而不必松开排液管线。
旋动红色星状按钮(2)实现此项功能。
注意— 由于阀工作时,系统的药液可能通过旁路管线流出,故必须在投加点安装单向止回阀。
- 当相关系统处于待机状态(例如维修)时,用于给计量管线卸压。
- 用作溢流阀,防止由计量泵产生的不允许的超压。
通过旁路管线溢流,自动执行溢流功能。
3 使用范围指定用途用于在关闭截止阀时,防止因计量泵产生的不容许的超压。
必须连接旁路管线。
非指定用途不能用于防止除计量泵以外的其它原因产生的不容许的超压。
此阀不能用作截止阀。
如果压力系统没有安装注射阀,不能使用此阀。
如系统没有安装旁路溢流管线,不能使用此阀。
4安装安全注意事项投加点必须安装单向止回阀,因为阀工作时系统中的计量介质通过旁路可能会产生回流。
机械/液压安装多功能阀直接旋到泵的压力连接端上,阀可以360°任意转动。
使用连接用具或GF螺纹配件,将计量管线或软管固定在泵的出口端上。
出厂前,EPDM材质的O型圈已安装在泵出口的凹槽内。
对于不适用EPDM材质的情况,建议安装Viton B型的O型圈,该O型圈(棕色)同阀一起供货。
使用卡环和管接螺母紧固旁路管线,并引回药桶。
因为阀在接近于开启压力时会出现少量的溢流,故必须始终接通旁路管线。
(完整版)03KMX15R控制阀说明书0001
表 10
编 号
பைடு நூலகம்零件名称
数 量
备注
编 号
零件名称
数 量
备注
101
阀体
1
201
旋入套
1
力矩74N? m
161
O形圈
1
P22A
301
堵头
1
力矩34~39N? m
162
O形圈
3
P16
511
阀芯
1
163
O形圈
2
P7
512
弹簧
1
164
O形圈
1
P11
541
阀套
1
171
内六角螺钉
4
M6-50
(10)液压回路
图13
备注
编号
零件名称
数 量
备注
303
阀杆
1
353
堵头
1
力矩59~69N? m
表
表8
编号
零件名称
数 量
备注
编号
零件名称
数 量
备注
611
阀芯
1
632
套
1
621
弹簧
1
638
过滤件
1
631
弹簧座
1
表9
编号
零件名称
数 量
备注
编号
零件名称
数 量
备注
391
阀杆
1
340
弹簧
1
317
内阀芯3
1
352
堵头
1
力矩49~59N? m
流经U型通道,再到斗杆阀杆(302)。于是,液压油沿着斗杆阀杆(302)的外圈流向接口Ba1,然 后再供给斗杆油缸小腔(有杆腔R)。
智能阀门定位器YT 3400系列使用说明书
智能阀门定位器YT-3400系列使 用 说 明 书YTC V.1.04- 目 录(硬件)-说明书概要3安全注意事项和产品保证内容及保证期限3危险区域使用时注意事项3产品简介4主要特征和功能4铭牌内容和说明5型号标记方法6主要参数7内部结构8安装9注意事项9 YT-3400L 外形尺寸图9 YT-3400R 外形尺寸图10排水接头的位置调整10 YT-3400L的安装11 YT-3400L的安装例图 11利用支架安装YT-3400L11 YT-3400R的安装15 YT-3400R的安装例图15利用支架安装YT-3400R15气管连接18注意事项18使用的空压条件18接管的条件19执行机构和YT-3400气管的连接19单作用执行机构和气管的连接19双作用执行机构和气管的连接19电源连接20注意事项20电流输入信号端子的连接21反馈信号端子的连接21限位开关端子的连接22接地端子的连接22自动/手动开关23流量调节旋钮的使用方法23- 目 录 (软件)-自动设定和基本操作方法24按钮说明24正常运行模式(RUN模式)的说明25自动设定 (AUTO CAL)25自动设定1 (AUTO 1) 26自动设定2 (AUTO 2)26自动设定3 (AUTO 3) 26自动设定HF(AUTO HF)26 BIAS设定26 V_0设定26手动模式(MANUAL)27参数模式 (PARAM)27参数种类27死区(dEAdZONE)设定28 P 值设定(KP)28I 值设定(KI)29D 值设定(KD)29P_ 值设定(KP_)30 I_ 值设定(KI_)30 D_ 值设定(KD_)30 HF启动(HF Off / On)30手动设定模式 (HAND CAL)31手动设定模式的种类31阀门的零点和量程的设定31阀位输出信号的零点和量程设定32按行程百分比降低阀门量程(PE TRIM)33设定反馈信号的正/反输出信号(TR_NORM/REV)33 HART通讯的正/反输出设定(HT NORM / REVS)33阀门模式(VALVE)34动作方式的变更 (ACT)34流量特性的变更 (CHAR)34用户自定义流量特性的设定 (USER SET)35正作用阀门紧密关闭功能的设定 (TSHUT OP)35反作用阀门紧密关闭功能的设定 (TSHUT CL)36分程控制 (SPLIT)36用户自定义零点信号大小设定(CTS ZERO)37用户自定义量程信号设定(CTS END)37角度补偿模式(ITP OFF / ON)37查看模式(VIEW)38错误警告代码39主程序软件导航图40智 能 阀 门 定 位 器 YT-3400系列说明书概要感谢选用我公司产品。