冷弯成型工艺理论基础
钢结构的冷弯加工技术
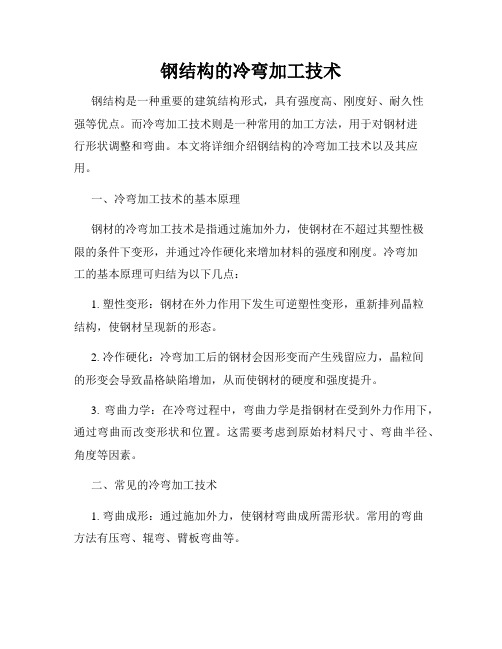
钢结构的冷弯加工技术钢结构是一种重要的建筑结构形式,具有强度高、刚度好、耐久性强等优点。
而冷弯加工技术则是一种常用的加工方法,用于对钢材进行形状调整和弯曲。
本文将详细介绍钢结构的冷弯加工技术以及其应用。
一、冷弯加工技术的基本原理钢材的冷弯加工技术是指通过施加外力,使钢材在不超过其塑性极限的条件下变形,并通过冷作硬化来增加材料的强度和刚度。
冷弯加工的基本原理可归结为以下几点:1. 塑性变形:钢材在外力作用下发生可逆塑性变形,重新排列晶粒结构,使钢材呈现新的形态。
2. 冷作硬化:冷弯加工后的钢材会因形变而产生残留应力,晶粒间的形变会导致晶格缺陷增加,从而使钢材的硬度和强度提升。
3. 弯曲力学:在冷弯过程中,弯曲力学是指钢材在受到外力作用下,通过弯曲而改变形状和位置。
这需要考虑到原始材料尺寸、弯曲半径、角度等因素。
二、常见的冷弯加工技术1. 弯曲成形:通过施加外力,使钢材弯曲成所需形状。
常用的弯曲方法有压弯、辊弯、臂板弯曲等。
2. 管道弯曲:将钢管按照所需半径和角度进行冷弯,用于制作管道弯头、转角、支架等。
常用的管道弯曲方法有冷弯弧线法、内贴模法、液压推弯法等。
3. 拼接:将两根或多根钢材通过冷弯工艺进行拼接,形成连接点。
常用的拼接方式有角焊缝拼接、法兰拼接、螺栓连接等。
三、冷弯加工技术的应用领域钢结构的冷弯加工技术广泛应用于多个领域,包括建筑、桥梁、造船、风电等。
以下是一些具体的应用示例:1. 建筑领域:冷弯加工技术可用于制作建筑中的承重构件、梯形梁、楼梯扶手等。
2. 桥梁领域:通过冷弯加工,可以制作桥梁的钢箱梁、钢板梁等结构件,提高桥梁的强度和刚度。
3. 造船领域:冷弯加工技术被广泛应用于船体结构、船舶内饰等方面,提供船舶的稳定性和安全性。
4. 风电领域:冷弯加工技术可用于制作风力发电塔架、叶片支撑等,提高风力发电设备的稳定性和寿命。
四、冷弯加工技术的发展趋势随着科技进步和工艺的不断改进,冷弯加工技术也在不断发展演进。
钢筋工作中的冷弯加工工艺与连接技术要点

钢筋工作中的冷弯加工工艺与连接技术要点钢筋在建筑、桥梁等工程中起着重要的作用,而冷弯加工工艺和连接技术则是钢筋处理中不可或缺的环节。
本文将就钢筋冷弯加工工艺与连接技术进行十二个方面的讨论,以帮助读者更好地理解和运用这些技术。
一、冷弯加工工艺的背景和概述冷弯加工是指对钢筋在常温下进行弯曲、塑性变形的加工工艺。
它的物理原理是利用材料的可塑性来达到所需形状和结构的目的。
冷弯加工工艺可以提高钢筋的使用性能和适应性。
二、冷弯加工工艺的分类与应用冷弯加工工艺可以分为手工弯曲和机械弯曲两种。
手工弯曲适用于简单的冷弯构件制作,而机械弯曲则适用于大批量、高精度的构件制作。
冷弯加工广泛应用于建筑、桥梁、道路、铁路等工程领域。
三、冷弯加工工艺的材料选择和准备工作在进行冷弯加工之前,需要选择合适的材料,并做好准备工作。
通常选用低碳钢作为冷弯加工的材料,因其可塑性好、弯曲性能稳定。
准备工作包括钢筋切断、修整、清洁等。
四、冷弯加工工艺的基本原则和操作要点冷弯加工需遵循一些基本原则和操作要点。
首先,根据设计要求选择适宜的加工方法。
其次,根据弯曲半径和角度调整加工设备。
最后,在进行冷弯加工时要注意保护设备和工人的安全。
五、冷弯加工工艺中的常见问题和解决方法在冷弯加工过程中,常会遇到一些问题,如变形过大、裂纹产生等。
针对这些问题,需要采取相应的解决方法,如调整加工参数、增加预弯等。
六、冷弯加工工艺中的关键技术和机械设备冷弯加工中的关键技术包括弯曲半径的选择、角度控制和模具设计等。
而机械设备则包括弯曲机、型式机等。
这些技术和设备的选择和应用直接影响着冷弯加工的效果和效率。
七、冷弯加工工艺中的质量检测和评价方法为确保冷弯加工质量,需要进行质量检测和评价。
常见的方法包括外观检查、尺寸检测、力学性能测试等。
通过这些方法,可以评估冷弯加工构件的质量和可靠性。
八、连接技术的重要性和应用范围钢筋的连接是保证结构强度和稳定性的关键环节。
连接技术的应用范围广泛,包括焊接、机械连接、粘结等。
冷弯成型成型道次计算公式

冷弯成型成型道次计算公式
冷弯成型是一种常用的金属加工方法,用于将金属板材弯曲成所需的形状。
在进行冷弯成型过程中,成型道次的计算是非常重要的,它决定了成品的形状和尺寸。
成型道次是指在进行冷弯成型过程中,金属板材通过多少次弯曲才能达到所需的形状。
成型道次的计算可以通过以下公式进行:
成型道次 = (内弯半径/板材厚度) + 1
其中,内弯半径是指在成型过程中所需的最小弯曲半径,板材厚度是指金属板材的实际厚度。
这个公式的推导基于冷弯成型过程中的一些基本原理。
首先,我们知道在进行冷弯成型时,金属板材会发生弯曲变形,而弯曲的程度取决于内弯半径和板材厚度。
内弯半径越小,板材的弯曲程度越大。
为了避免过度弯曲导致板材破裂,通常会选择一个合适的内弯半径。
在成型道次的计算中,我们将内弯半径与板材厚度进行比较,如果内弯半径小于板材厚度,那么至少需要一次弯曲才能达到所需的形状;如果内弯半径等于板材厚度,那么需要两次弯曲才能达到形状;以此类推,如果内弯半径大于板材厚度,需要的弯曲次数就会更多。
通过成型道次的计算公式,我们可以根据实际需求来确定冷弯成型的工艺参数,例如内弯半径和板材厚度。
这样可以确保在进行冷弯成型过程中,金属板材能够得到准确的弯曲,并达到所需的形状和尺寸。
需要注意的是,成型道次的计算公式是一个基本的参考值,实际的成型道次可能还会受到其他因素的影响,例如金属板材的强度和硬度等。
因此,在实际应用中,需要结合实际情况进行合理的调整和优化。
冷弯成型理论研究进展
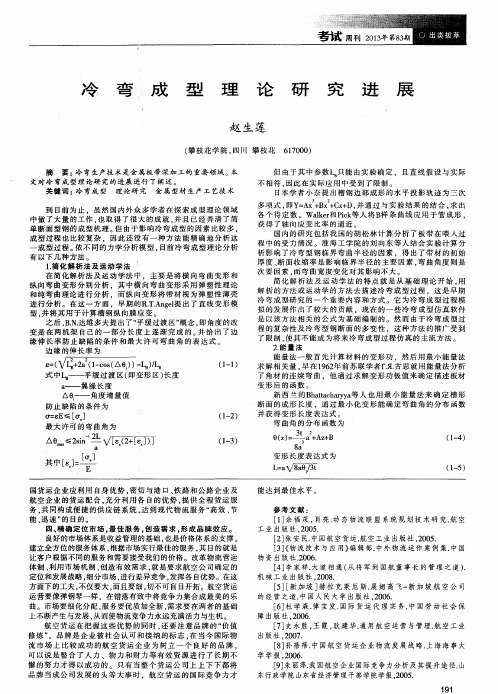
8 = ( Vg + 2  ̄ ‘ ( 1 - c o s ( a o ) ) 一 ) / L B
式 中L ——平缓过渡区( 即变 形 区 ) 长度
( 1 - 1 )
a 一 翼 缘 长 度 a0 : — — 角 度 增 量 值 防止 缺 陷 的条 件 为 8 E ≤[ O " s ] 最 大 许 可 的弯 曲角 为
L = a V  ̄O J 3 t
能达到最佳水平。
国货 运 企 业 应 利 用 自身 优 势 。 密切与港 口、 铁 路 和 公 路 企 业 及 航 空 企 业 的货 运 配 合 , 充 分 利 用 各 自 的优 势 , 提 供 全 程 货 运 服 务, 共同构成便捷 的供 应链 系统 , 达 到现代 物流服务“ 高效 、 节
.
墨
究 进 展
冷
弯
成
型
理
论
研
赵 生 莲
( 攀枝花学院 , 四J I I攀 枝 花 摘 要: 冷 弯 生 产技 术 是 金 属板 带深 加 工 的 重要 领 域 。 本 文 对 冷 弯 成 型 理论 研 究 的进 展 进 行 了 阐述 。 关键 词 :冷 弯成 型 理 论 研 究 金 属 型 材 生 产 工 艺技 术 到 目前 为 止 ,虽 然 国 内 外众 多 学 者 在 探 索 成 型 理 论 领域 中做 了 大 量 的 工作 , 也 取 得 了很 大 的 成 就 , 并 且 已经 弄 清 了 简 单 断 面 型 钢 的成 型机 理 。 但 由 于影 响冷 弯成 型 的 因素 比较 多 , 成 型 过程 也 比较 复 杂 ,因 此 还 没 有 一 种 方 法 能 精 确 地分 析 这 成 型过 程 。 依 不 同 的 力 学分 析模 型 , 目前 冷 弯 成 型 理 论 分 析 有 以下 几 种方 法 。 1 . 简 化 解 析 法 及 运 动 学 法 在 简 化 解 析 法 及 运 动 学 法 中 ,主 要 是 将 横 向弯 曲变 形 和 纵 向 弯 曲变 形 分 别 分 析 ,其 中横 向 弯 曲变 形 采 用 弹 塑性 理论 和纯 弯 曲理 论 进 行 分 析 .而 纵 向 变 形 将 带 材 视 为 弹 塑 性 薄壳 进 行 分 析 。在 这一 方 面 ,早 期 的 R . T . A n g e l 提 出 了直 线 变 形 模 型。 并 将 其 用 于 计 算 槽 钢 纵 向膜 应变 。 之后 . B . N . 达维 多 夫 提 出 了“ 平 缓 过渡 区” 概念 . 即角 度 的 改 变 是 在 两 机 架 自己 的 一 部 分 长度 上 逐 渐 完 成 的 。 并 给 出 了 边 缘 伸 长 率 防止 缺 陷 的 条 件 和 最 大 许 可 弯 曲角 的 表 达 式 。 边 缘 的伸 长 率 为
冷作工工艺第七章 弯形与压延
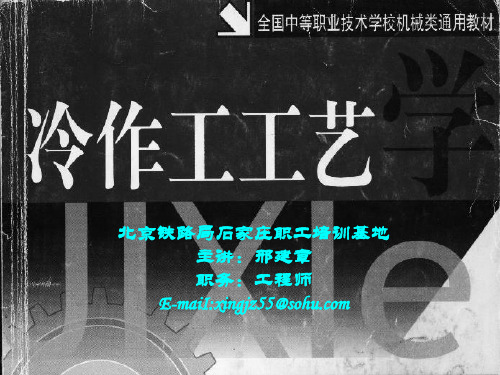
7
§7—2 压弯 一、压弯力的特点及压弯力的计算
压弯
1.压弯的特点 在压力机床上使用压弯模进/22
b)接触弯形
c)校正弯形
8
图7—5 材料压弯时的三种变形方式
2.压弯力计算 为使材料能够在足够的压力下成形,必须计算其压弯力, 作为选择压力机床工作压力的重要依据。在生产中常用经验公 式计算压弯力,见表7—2 表7-3
表中 F——压弯力,N; b——弯形件的宽度,mm; t ——弯形件的厚度,mm; r凸——凸模圆角半径,mm; L——凹模槽口两支点间距离,mm σb——材料的抗拉强度,MPa; c——系数,取c = 1~1.3; K——系数,取K:0.3~0.6; A——校正部分投影面积,mm2; q——单位面积上的校正力,N/mm2(MPa),见表7—3。
●最小弯曲率半径:材料不被破坏弯度最小的叫做
2018/9/22
最小弯曲率半径。
5
4.横截面变形
图7—3 材料纤维方向与弯曲线的关系 弯制扁钢圈时出现内侧变厚、外侧 变薄(见图7--4a);弯管时则出现椭圆截 面(见图7--4b)等。在这些情况下,就需 采用一些特殊的工艺措施来限制横截面 的变形,以保证弯形件的质量。
2018/9/22
10
二、压弯模
冷作工所用的压弯模,多数采用焊接制成,并且尽量少用 或不用切削加工零件。这样,制作方便,可以缩短模具制造周 期,还可以多利用生产边角料,降低生产加工成本。
a)、b)整体铸造后加工
c)、d)型钢焊制
图7--- 6压弯模具结构形式
2018/9/22 11
当采用接触弯形或校正弯形时,制作压弯模应考 虑以下几个方面。 1.压弯模具工作部分尺寸确定
2018/9/22 3
冷弯成型工艺理论基础
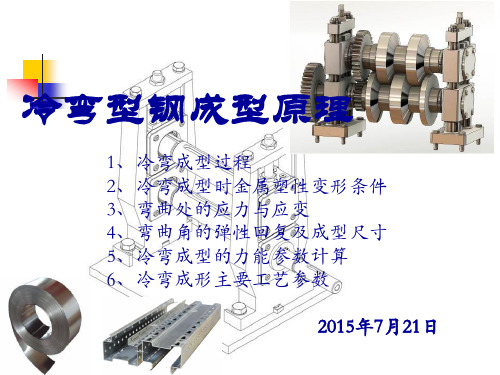
用弹复区的长度L0和成型过渡区长度L来限定两道成型辊
的间距,有利于避免边缘的塑性拉伸。
弯曲半径
1、冷弯成型过程
辊弯成型过程中,还有一个重要条件,即最小弯曲半径
的选择必须合理。
图示成型处的弯曲半径为R,带材厚度为S,图上的影线部分 代表变形沿厚度的分布状态。
。
第二次压弯φ2角,如果φ1≈φ2, 则两者的拉伸与减薄大致相等。
当一次压弯成型时,凹辊对工件 两侧压力所产生的拉力及应变集
中(b1点附近)现象将显著增大 ,外层纤维o1c1将有较大拉伸,它
向弦线靠近的距离,即减薄量
b1b1` 将明显大于a1a1` ,其中性 层内移量bb` 也要相应大aa` 。
边缘在折弯时的伸长量。
伸长量
在辊压成型过程中这个伸长量不 应超过该种材料的弹性极限延
b0
a’
l αi b’
L
a
伸量。
L
避免边缘的塑性拉伸。
b
图3-2 成型时边缘的伸长
1、冷弯成型过程
图为角型材成型时的边缘伸长,图中表 示第i道机架与第i-1道机架间成形过程。
在此过程中,角度变化量为αi,两机架 间成型过渡区长度为L,带材边缘在水平面 上投影长度为ab,在垂直面上投影长度为 a`b` ,这两个投影都是曲线形,为了计算 上方便,可以把它们都看成是直线。
图 两段压弯成型
1、冷弯成型过程
分步压弯——分次弯曲
第一次所用的凸辊圆角半径R1较大
,工件的弯曲处不受减薄和裂纹的
威胁。
第二次所用的圆角半径虽小,但它 与已经弯曲的工件的接触面积将明 显大于R2与平面的接触面积。 因此,两次压弯将比一次压弯的应 变集中程度小,厚度减薄量也小。
冷作工工艺学第五版电子课件第八章弯形与压延
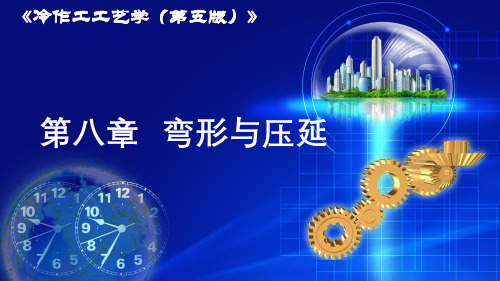
§8—1 弯形加工基础知识
4. 横截面变形
如前所述,弯形过程中,材料的横截面也要发生变化,其变化过程主要
与相对弯形半径、横截面几何特征及弯形方式等因素有关。当弯形过程中
材料横截面形状变化较大时,也会影响弯形件的质量。例如窄板弯形时出
现图a所示的畸变,弯制扁钢圈时出现内侧变厚、外侧变薄(见图a);弯
F = Aq
V 形自由弯形
经验公式
2
cbt
Rm
F=
2L
§8—2 压弯
二、压弯模
压弯模的结构形式根据弯形件的形状、精度要求及生产批量等进行选择,
最简单而且常用的是无导向装置(利用压床导向)的单工序压弯模。这种压
弯模可以整体铸造后加工制成,也可以利用型钢焊制,或由若干零件组合、
装配而成。
整体铸造后加工
弯曲成形在金属结构制造中应用很多,它可以在常温下进行,
也可以在材料加热后进行,但大多数的弯曲成形都是在常温
下进行的。
§8—1 弯形加工基础知识
一、钢材的弯曲变形过程及特点
当材料上作用有弯矩M时,就会发生弯曲变形。材料变形区内靠近曲率
中心的一侧(以下称内层)的金属,在弯矩引起的压应力作用下被压缩缩
短;远离曲率中心的一侧(以下称外层)的金属,在弯矩引起的拉应力的
采用自由弯形所需压弯力小、工作时靠调整凹模槽口的宽度和凸模的
下止点位置保证零件的形状,批量生产时弯形件质量不稳定,多用于小批
量生产大中型零件的压弯。
采用接触弯形和校正弯形时,由模具保证弯形件精度,质量较高而且
稳定。但所需压弯力较大,并且模具制造周期长,费用高。多用于大批量
生产中的中小型零件的压弯。
§8—2 压弯
冷弯成型知识7.3

冷弯成型知识1、冷弯型钢的变形特点——金属在冷态下弯曲变形,变形前后板带的厚度不变;成型后各部中性线的展开长度等于原板带宽度;成过程中不可避免的伴随着弹性变形;弯曲的各部分存在着加工硬化现象2、弯曲变形条件轧件弯曲变形时,其截面存在着中性线,中性线以上和以下部分,分别存在着压应力和拉应力。
离中性线越远,应力值越大,当其超过金属的σb值时,则该处产生更断裂。
由此可见,冷弯变形的必要条件——使弯曲截面上的最大正应力σmax满足条件:σs ≤σmax ≤σbσmax的大小取决于轧件的厚度、单道次弯曲成度。
弯曲时曲率半径越小,则弯曲程度越大;轧件越厚,在曲率半径相同的情况下,轧件上下边部产生的弯曲正应力愈大因此,为易于冷弯,应使σs降低,如采用σs较低的钢种,或冷弯成型前进行退火。
为防止弯曲时产生裂纹,必须控制各道次轧件的弯曲程度使σmax ≤σb3、中性线的求法中性线的位置取决于弯曲半径的大小和坯料厚度(如图5-8)若弯曲时轧件内侧边曲率半径为r 坯料厚度为h 则中性线曲率半径为ρ= R + xh x——经验系数(可查表)中性线曲率半径求出后,即可求出中性线长度。
L= L1 + L3 + Lρ复杂断面时可按分段叠加法计算4、孔型设计(略)5、变形区长度变形区长度——连续式辊式成型机从第一架水平辊中心至机组末架水平辊中心线的距离称为变形区长度确定变形区长度的原则——保证带钢边缘在成型过程中不产生塑性变形,以防止边缘鼓包、波浪等缺陷的产生由此确定最小变形区长度对于简单形状角钢,成型时保持带钢边缘不产生塑性变形的临界升起角α约为1°—1°25`由此可得变形区长度为因此,原则上说,弯曲角度越大,加工所需的变形区长度越大(弯曲道次越多,机架数越多),6、成型速度辊式成型机组的成型速度为0.5—250 m/min常用25--30 m/min。
- 1、下载文档前请自行甄别文档内容的完整性,平台不提供额外的编辑、内容补充、找答案等附加服务。
- 2、"仅部分预览"的文档,不可在线预览部分如存在完整性等问题,可反馈申请退款(可完整预览的文档不适用该条件!)。
- 3、如文档侵犯您的权益,请联系客服反馈,我们会尽快为您处理(人工客服工作时间:9:00-18:30)。
辊弯成型技术
板金属的成型
折弯成型
(a )依靠单个模具两步成型(b )折弯机上的分布成型
= 全部直线段长度+ 全部圆弧段长度
圆弧段长度指各圆弧的中性线长度
wi zi
B b b =+∑∑弹性范围
永久变形范围
理论上弯角成型应力-应变分布
最大应变(拉伸)
应力层
实际外层纤维
实际外层纤维中性轴-理论上中性轴-实际上
最大的应变(压缩)
实际应力分布
应力层
实际弯角应力-应变分布
屈服应变
以截面惯性主轴为坐标方位
成型无盲角,全部实弯成型;成型对称性好,型材扭转小;
成型道次少,轧辊直径小,经济性好。
盲角
盲角
☐
☐
1区:接触段;
2区:非接触变形段;3区:不变形阶段;4区:弹性回复段。
实际变形不同于理论变形
材料实验、屈服极限、抗拉极限和延伸率
通过绘制应力-应变图可以清楚地知道屈服极限、抗拉强度的大小试验过程中的应力应变图
无载荷
颈缩开始
前后
断裂
无载荷
应变应力
最大载荷
断裂
永久的弹性的
L 1应力下的总变形(应变)应力
材料3#
材料2#
材料1#应变
不同材料的应力应变图
1#为低强度高延伸率的材料2#为高强度低延伸率的材料
3#为强度更高延伸率更低的材料由应力-应变估计成型性
—应变示意图表明,材料的屈服极限和抗拉极限相差越大,材料的延伸率越高,金属的成形性越好。
能和轧制方向上的性能不同。
抗拉强度拉伸
由于轧制方向不同金属的力学性能可能发生变化轧制方向
轧制方向
由(a)和(b)可以看出,带材后续成型时,弯曲方向的选择需要考虑原始的轧制方向;(c)为弯曲线与轧制方向平行时产品的缺陷。
屈
服
点
冷压下量
铍铜1010碳钢
1350 铝
不同金属典型的冷作硬化率
应力
冷作硬化屈服点110.000psi 抗拉强度120.000psi 伸长率1%
相同钢的退火屈服点27.000psi 抗拉强度36.000psi 伸长率1%
相同材料冷作硬化和退火后应力-应变图
应力
应变
冷作硬化
屈服点110.000psi
抗拉强度120.000psi 伸长率1%相同钢的退火屈服
点27.000psi 抗拉强度36.000psi 伸长率1%上述数学估算的根据是成型边以光滑的螺旋线运动,考虑了腿高、道次数、道次间距对成型过程应变的影响。
由于实际变形区长度往往大于理论变形区长度s ,因此,实际延伸率>理论延伸率
轧辊设计的目标是以最少的成形步骤
冷弯产品的形状可以分类为:简单截面(开口),封闭截面,复杂程度中等截面,非常复杂的截面,波纹板。
断面深度越大,要求成型的道次数越多
成型道次
各种辊式弯曲截面型材的成型道次与弯角数的关系
N
形状因子法Ф=Fnt
成型道次数
对称断面的形状因子与成型道次非对称断面的形状因子与成型道次
F:边长
n:右弯角个数
t:板厚
通过边缘极限应力来计算成型道次道次数的影响因素
高强度材料和厚材料的抗皱强度较高;因此,在同样的压应力时,
与低强度或薄材料相比很少有弯皱缺陷
)材料厚度
[⎩⎨
⎧>+=时)(当
5/5.0log(5.065.05.0t r k L、t、α已知,r、k待求,插值求解
α
π
)(180
kt r +=
弯曲(展开)方法☐长度补偿的位置及比例:外侧、中间、内侧、两侧
[]⎩⎨
⎧>+=时)(当
5/5.0/log(5.065.05.0t r t r k α
π
)(180
kt r L +=
3个道次的定半径弯曲
通过定长度或者定半径法来计算成型曲线长度混合应用定长度法和定半径法成型
材料在成型过程中会产生纵向延伸
前滑
直径递增量通常在0.4~
0.6mm(约为基本直径的3/‰
左右)。
用“定长度法”弯曲比用“定半径法”弯曲的如果道次数较多,通常在
最初的道次设置前滑增量,而
在产品刚度足以避免起皱的后
道次用相同直径的轧辊。
解决回弹的有效办法是过弯
以多个直线段代替大圆弧
腹板部分通常不影响道次数。
然而,腹板段越宽,材料越薄,产生波浪的几率越大。
尽管轧辊设计得很好,也不能根除波浪。
宽波纹板的成型,通常从中心波开始。
这种情况下,除了弯曲角随道次逐渐变化,每一边有一个较宽的平直段沿同一平面横向收缩,逐渐靠近中心
顺序成型奇数波:先成型中心波,中心波成形结束后开始相邻两个波的成形。
偶数波:两侧对称成型
同时成型
21
w
1)在腹板中部增加上下轧辊进行2)在进行成型工艺设计时,优先。