凸点倒装焊接技术及可靠性测试
倒装焊接技术

解决途径-新型可修复底部填充材料
为了解决这一问题,目前,越来越多的 研究人员投入到新型可修复底部填充材料的 开发当中,常见的做法是,通过在用作底部 填充材料的环氧树脂中引入某些薄弱的化学 键,使其固化后仍可以再加热或加入化学试 剂后分解,使电子元器件能够返工和循环使 用。
修复过程
修复过程包括以下六步: 1.通过加热或化学处理方法迅速降低底部填充 剂的粘结强度; 2.用芯片拾取装置取下坏芯片; 3.用高速刷净设备去除树脂残留物; 4.对基板进行检测; 5.更换新的芯片; 6.重新进行底部填充。
底部填充的作用
由于有机基板和芯片的热膨胀系数无法 保证完全匹配,导致回流焊和温度循环时在 焊球处产生很大的应力,严重时甚至可能会 引起裂损现象,因此,倒装芯片一般采用底 部填充技术来避免这一问题。
底部填充同时带来的问题
由于当前的技术无法保证所供应的芯 片一定完好,使得一些有缺陷的芯片在倒 装后的测试中才被发现,这时就需要进行 返工修复替换。
倒装焊接技术
演讲人:
倒装芯片的优点
1.消除了对引线键合连接的 要求,缩短了互连距离; 2.提高了输入/输出(I/O)密 度; 3.在电路板上占用空间小; 4.符合当前微电子封装高密 度和小型化的趋势。
倒装芯片主要工艺步骤
• 第一步: 凸点底部金属化 • 第二步:芯片凸点制作 • 第三步:将已经凸点的晶片组装到基板上 • 第四步: 使用非导电填料填充芯片底部孔隙
可修复底部填充技术的技术参数
1.工业应用及固化性能
可修复底部填充技术的技术参数2 Nhomakorabea可靠性可修复底部填充技术的技术参数
3.移除性 芯片的移除是修复环节中极为重要的一步, 通常使用球栅阵列封装(BGA)型的修复设备。 修复时间与温度应保持恒定,且芯片移除过 程不会对基板造成损害。理想的移除温度与 移除过程所需要的时间分别为210 ℃、1 min。
金凸点超声热压倒装焊工艺参数优化研究
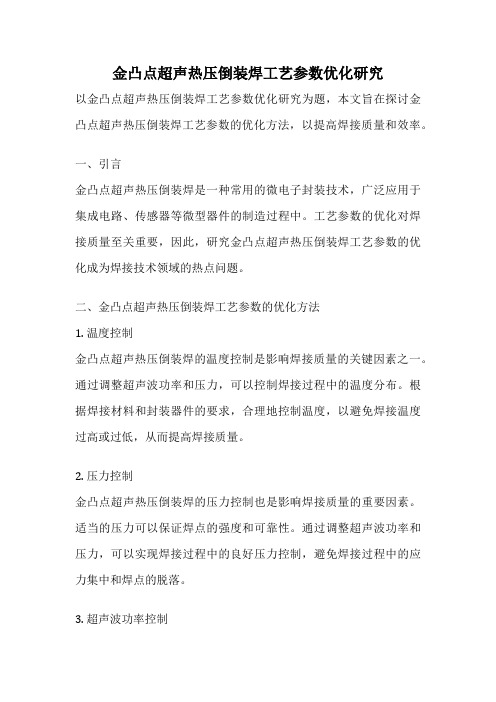
金凸点超声热压倒装焊工艺参数优化研究以金凸点超声热压倒装焊工艺参数优化研究为题,本文旨在探讨金凸点超声热压倒装焊工艺参数的优化方法,以提高焊接质量和效率。
一、引言金凸点超声热压倒装焊是一种常用的微电子封装技术,广泛应用于集成电路、传感器等微型器件的制造过程中。
工艺参数的优化对焊接质量至关重要,因此,研究金凸点超声热压倒装焊工艺参数的优化成为焊接技术领域的热点问题。
二、金凸点超声热压倒装焊工艺参数的优化方法1. 温度控制金凸点超声热压倒装焊的温度控制是影响焊接质量的关键因素之一。
通过调整超声波功率和压力,可以控制焊接过程中的温度分布。
根据焊接材料和封装器件的要求,合理地控制温度,以避免焊接温度过高或过低,从而提高焊接质量。
2. 压力控制金凸点超声热压倒装焊的压力控制也是影响焊接质量的重要因素。
适当的压力可以保证焊点的强度和可靠性。
通过调整超声波功率和压力,可以实现焊接过程中的良好压力控制,避免焊接过程中的应力集中和焊点的脱落。
3. 超声波功率控制超声波功率的控制对金凸点超声热压倒装焊的焊接质量有着重要影响。
合理地控制超声波功率可以实现焊接过程中的材料熔化和焊接点的形成,从而提高焊接强度和可靠性。
通过实验和优化方法,可以确定最佳的超声波功率控制参数。
4. 金凸点设计金凸点的设计对金凸点超声热压倒装焊的焊接质量有着重要影响。
合理地设计金凸点的形状和尺寸可以实现焊接过程中的良好热传导和焊接点的形成,从而提高焊接质量。
通过优化设计,可以得到最佳的金凸点形状和尺寸参数。
5. 焊接时间控制焊接时间的控制也是金凸点超声热压倒装焊的关键因素之一。
合理地控制焊接时间可以实现焊接过程中的材料熔化和焊接点的形成,从而提高焊接强度和可靠性。
通过实验和优化方法,可以确定最佳的焊接时间控制参数。
三、结论金凸点超声热压倒装焊工艺参数的优化对焊接质量和效率的提高具有重要意义。
通过合理地控制温度、压力、超声波功率、金凸点设计和焊接时间等工艺参数,可以实现焊接过程中的优化控制,提高焊接质量和效率。
工艺流程中的凸点检测
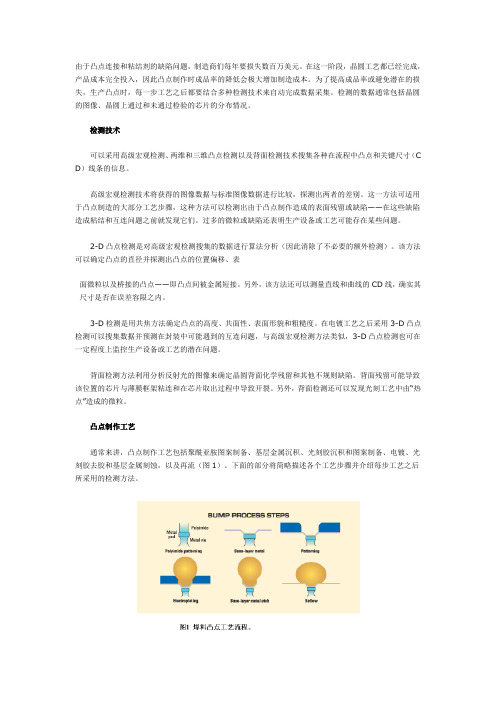
由于凸点连接和粘结剂的缺陷问题,制造商们每年要损失数百万美元。
在这一阶段,晶圆工艺都已经完成,产品成本完全投入,因此凸点制作时成品率的降低会极大增加制造成本。
为了提高成品率或避免潜在的损失,生产凸点时,每一步工艺之后都要结合多种检测技术来自动完成数据采集。
检测的数据通常包括晶圆的图像、晶圆上通过和未通过检验的芯片的分布情况。
检测技术可以采用高级宏观检测、两维和三维凸点检测以及背面检测技术搜集各种在流程中凸点和关键尺寸(C D)线条的信息。
高级宏观检测技术将获得的图像数据与标准图像数据进行比较,探测出两者的差别。
这一方法可适用于凸点制造的大部分工艺步骤,这种方法可以检测出由于凸点制作造成的表面残留或缺陷——在这些缺陷造成粘结和互连问题之前就发现它们。
过多的微粒或缺陷还表明生产设备或工艺可能存在某些问题。
2-D凸点检测是对高级宏观检测搜集的数据进行算法分析(因此消除了不必要的额外检测)。
该方法可以确定凸点的直径并探测出凸点的位置偏移、表面微粒以及桥接的凸点——即凸点间被金属短接。
另外,该方法还可以测量直线和曲线的CD线,确实其尺寸是否在误差容限之内。
3-D检测是用共焦方法确定凸点的高度、共面性、表面形貌和粗糙度。
在电镀工艺之后采用3-D凸点检测可以搜集数据并预测在封装中可能遇到的互连问题,与高级宏观检测方法类似,3-D凸点检测也可在一定程度上监控生产设备或工艺的潜在问题。
背面检测方法利用分析反射光的图像来确定晶圆背面化学残留和其他不规则缺陷。
背面残留可能导致该位置的芯片与薄膜框架粘连和在芯片取出过程中导致开裂。
另外,背面检测还可以发现光刻工艺中由“热点”造成的微粒。
凸点制作工艺通常来讲,凸点制作工艺包括聚酰亚胺图案制备、基层金属沉积、光刻胶沉积和图案制备、电镀、光刻胶去胶和基层金属刻蚀,以及再流(图1)。
下面的部分将简略描述各个工艺步骤并介绍每步工艺之后所采用的检测方法。
聚酰亚胺图案制备——通过聚酰亚胺图形化,也就是通常的光刻和显影工艺,在晶圆的表面沉积一层透明的聚酰亚胺层。
金凸点超声热压倒装焊工艺参数优化研究
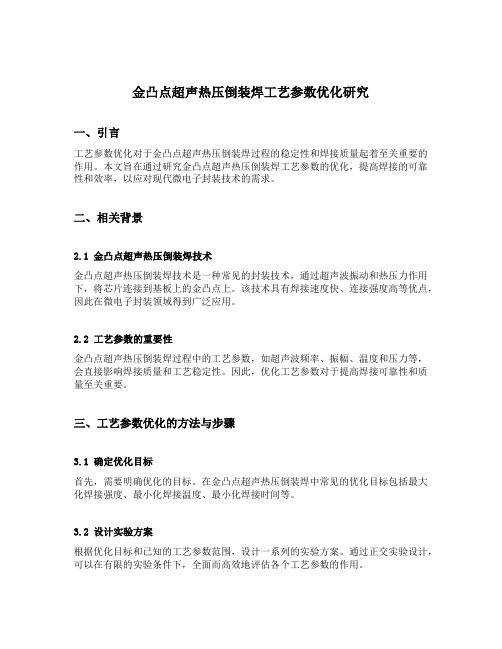
金凸点超声热压倒装焊工艺参数优化研究一、引言工艺参数优化对于金凸点超声热压倒装焊过程的稳定性和焊接质量起着至关重要的作用。
本文旨在通过研究金凸点超声热压倒装焊工艺参数的优化,提高焊接的可靠性和效率,以应对现代微电子封装技术的需求。
二、相关背景2.1 金凸点超声热压倒装焊技术金凸点超声热压倒装焊技术是一种常见的封装技术,通过超声波振动和热压力作用下,将芯片连接到基板上的金凸点上。
该技术具有焊接速度快、连接强度高等优点,因此在微电子封装领域得到广泛应用。
2.2 工艺参数的重要性金凸点超声热压倒装焊过程中的工艺参数,如超声波频率、振幅、温度和压力等,会直接影响焊接质量和工艺稳定性。
因此,优化工艺参数对于提高焊接可靠性和质量至关重要。
三、工艺参数优化的方法与步骤3.1 确定优化目标首先,需要明确优化的目标。
在金凸点超声热压倒装焊中常见的优化目标包括最大化焊接强度、最小化焊接温度、最小化焊接时间等。
3.2 设计实验方案根据优化目标和已知的工艺参数范围,设计一系列的实验方案。
通过正交实验设计,可以在有限的实验条件下,全面而高效地评估各个工艺参数的作用。
3.3 进行实验并收集数据按照设计的实验方案,进行实际的焊接实验,并记录实验过程中的各个工艺参数值以及相应的焊接质量数据。
3.4 数据分析与建模将实验收集的数据进行统计分析,通过适当的建模方法,建立工艺参数与焊接质量之间的关联模型。
常用的建模方法包括回归分析、神经网络等。
3.5 优化工艺参数根据建立的关联模型,使用优化算法寻找最优的工艺参数组合。
常见的优化算法包括遗传算法、模拟退火算法等。
3.6 验证与调整选取几个最有希望的优化结果,进行金凸点超声热压倒装焊实验,并验证焊接质量是否得到了显著的提高。
根据实验结果,调整优化的工艺参数,并进行再次验证。
四、实验结果与讨论4.1 实验结果概述根据上述优化方法,我们进行了一系列金凸点超声热压倒装焊的实验。
通过收集实验数据并进行分析,得到了优化后的工艺参数组合。
凸点实现的倒装焊推进微电子封装技术的发展
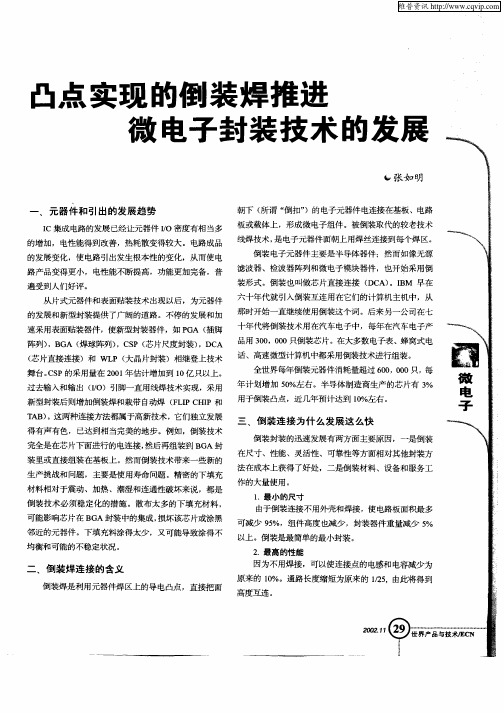
芯片到基板的整个表面 。下填充保护 凸点不受潮湿或其 它环境的影响,并为组件提供 附加的机械强度。然而它 的最主要 目的是为芯片和基板间任何热膨胀差异提供补
偿 。下填充在机械 上是将芯片与基板 “ 锁在一起 ”的 ,
所 以热膨胀差不损坏 凸点的电连接 。下填充可 以沿着每 块芯片边缘用针管涂布,下填充料因毛细管作用而汲入 芯片下的空间,加热固化后变成永久连接 。
维普资讯
组件类 型
长× 宽
面积 ( m) a r 2
表 2 线焊和倒装封装的典型信号线参数
组件类 型 参数 R() Q C (F p) L (i nl )
i
Pm 最 Br G 大 A2 小 32 5P 5
最大
0 . 2 7
.
1 8
1 . 9
17 .
l 、. 6 . 5
81 .
11 . 01 .
维普资讯
凸点 实现 的倒 装焊 推进
维普资讯
焊料凸点工艺首先要求在芯片焊 区上,用溅射、电
镀或其它方法制作凸点底层金属化 ( B ,以便 替代 U M)
绝缘的氧化铝层,并规定和限制焊料浸润面积。采用蒸
发 、电镀、网印焊膏或针管涂敷方法在 U M 上面淀积 B 焊料。 在焊料 凸点制好后 , 晶片就锯成带凸点的芯 片。 大
08 . 3
1. 0 6 0 . 9
2 . 2
l. 2 9 0 . 8
49 . 8
陶{倒装 莞
最 , J 、
电镀焊球凸点倒装焊技术
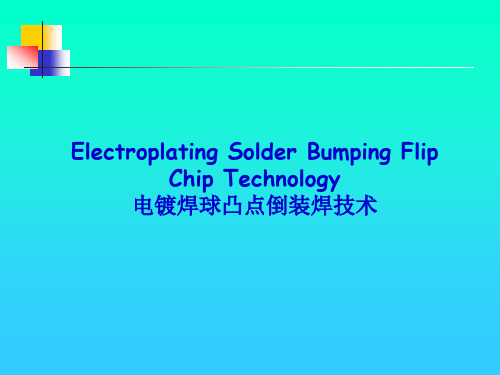
Process Specification工艺参数
➢ Photoresist Thickness 光刻胶厚度: 40~100 m ➢ Bump Material凸点材料: 63Sn/37Pb ➢ Bump height 凸点高度: 75~140 m ➢ UBM layer凸点下金属层: Ti/W-Cu, Cr-Cu ➢ Min. effective pitch of bump 最小有效凸点间距 : 125 m
2. Sputter Under Bump Metal金属层溅射
Mushrooming
Electroplated solder bump
Thick photoresist film
Chip
3. Coat with PR 覆盖光胶
PR opening
Chip
4. Pattern for bump 凸点光刻
丝网印刷凸点倒装焊技术
Electroless UBM and Stencil Printing化学镀UBM
和丝网印刷工艺
The most potential low cost flip chip bumping method. 最具前景的低成本倒装焊凸点制备方法
Using electroless Ni/Au as UBM system 用化学镀镍/金作为凸点下金属层 maskless process 无掩膜工艺 Compatible with SMT process 与表面贴装工艺兼容 Flexible for different solder alloys适用于不同焊料合金
Electroplating Solder Bumping Flip Chip Technology
电镀焊球凸点倒装焊技术
采用热压焊工艺实现金凸点芯片的倒装焊接

关 键词 : 装 焊 ; 压焊 ; 凸点 芯片 ; 倒 热 金 薄膜基板 中图分类 号 : N 0 T 6 文献标识 码 : A 文章编 号 : 0 — 4 4 20 ) 1— 0 8— 3 1 1 3 7 ( 0 8 O 0 2 0 0
As e b y o i i l m p ih s m l fFl Ch p Go d Bu p sW t
到焊 接 的 目的 。热压焊 工艺 已在液 晶显示 ( C 的 L D)
的关键 技 术之一 。多功 能和小 型化将 直接转 化 为高 密度 芯片互 连工艺 , 要 载 带 自动焊 ( A ) 需 T B 和倒 装
玻璃 板上芯 片 ( O 和光 电器 件 中 的铟 凸 点 芯 片 C G) 焊接 中成功 应用 。而金 凸点芯 片 的倒 装焊 接常规 使 用热 超声焊接 工 艺完成 。本文 所述 内容是 在借鉴 国 外先进 工艺 的基础 上 , 展 的 金 凸点 芯 片 的热 压 倒 开
Do u n d A c me tCo e:
Aril D:0 1—3 7 2 0 O t eI 1 0 c 4 4( 0 8) 1—0 2 0 8—0 3
近年来 , 电子 工业 产品 向小型化 、 高密 度和 多功
能 性方 向发展 , 电子 组装 和 封 装技 术 是 实 现此 目的
不平 整 , 热加 压也可 使上下 金属 相互 镶嵌 , 而达 加 从
维普资讯
电 子 工 艺 技 术
Elcr nisPr c s c noo e to c o e sTe h l  ̄,
第2 第1 9卷 期 20 0 8年 1 月
采 用 热 压 焊 工 艺 实 现 金 凸 点 芯 片 的 倒 装 焊 接
采用热压焊工艺实现金凸点芯片的倒装焊接_张彩云
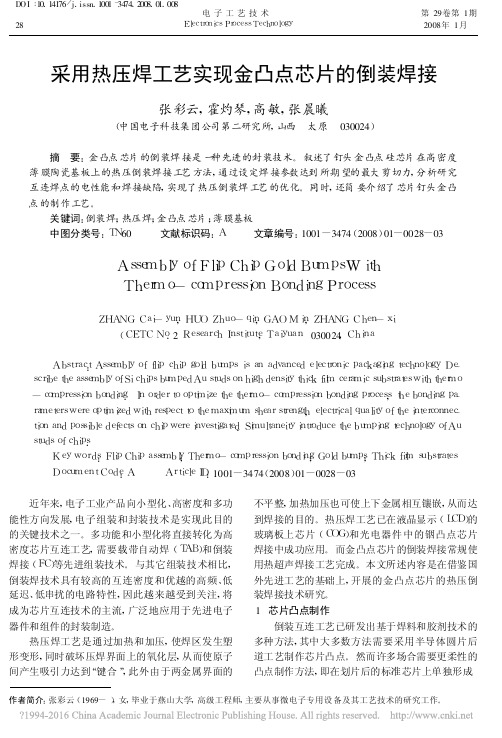
采用热压焊工艺实现金凸点芯片的倒装焊接张彩云,霍灼琴,高敏,张晨曦(中国电子科技集团公司第二研究所,山西 太原 030024)摘 要:金凸点芯片的倒装焊接是一种先进的封装技术。
叙述了钉头金凸点硅芯片在高密度薄膜陶瓷基板上的热压倒装焊接工艺方法,通过设定焊接参数达到所期望的最大剪切力,分析研究互连焊点的电性能和焊接缺陷,实现了热压倒装焊工艺的优化。
同时,还简要介绍了芯片钉头金凸点的制作工艺。
关键词:倒装焊;热压焊;金凸点芯片;薄膜基板中图分类号:T N 60 文献标识码:A 文章编号:1001-3474(2008)01-0028-03A s s e m b l y o f F l i pC h i pG o l dB u m p s Wi t hT h e r m o -c o m p r e s s i o nB o n d i n g P r o c e s sZ H A N G C a i -y u n ,H U O Z h u o -q i n ,G A OMi n ,Z H A N G C h e n -x i (C E T CN o .2R e s e a r c hI n s t i t u t e ,T a i y u a n 030024,C h i n aA b s t r a c t :A s s e m b l y o f f l i pc h i pg o l db u m p s i s a na d v a n c e de l e c t r o n i c p a c k a g i n g t e c h n o l o g y .D e -s c r i b e t h e a s s e m b l y o f S i c h i p s b u m p e d A u s t u d s o n h i g h d e n s i t y t h i c k f i l mc e r a m i c s u b s t r a t e s w i t h t h e r m o -c o m p r e s s i o n b o n d i n g .I n o r d e r t o o p t i m i z e t h e t h e r m o -c o m p r e s s i o n b o n d i n g p r o c e s s ,t h e b o n d i n g p a -r a m e t e r s w e r e o p t i m i z e d w i t h r e s p e c t t o t h e m a x i m u ms h e a r s t r e n g t h ,e l e c t r i c a l q u a l i t y o f t h e i n t e r c o n n e c -t i o n a n d p o s s i b l e d e f e c t s o n c h i p w e r e i n v e s t i g a t e d .S i m u l t a n e i t y i n t r o d u c e t h e b u m p i n g t e c h n o l o g y o f A us t u d s o f c h i p s .K e y w o r d s :F l i p C h i p a s s e m b l y ;T h e r m o -c o m p r e s s i o n b o n d i n g ;G o l d b u m p s ;T h i c k f i l m s u b s t r a t e s D o c u m e n t C o d e :A A r t i c l e I D :1001-3474(2008)01-0028-03 近年来,电子工业产品向小型化、高密度和多功能性方向发展,电子组装和封装技术是实现此目的的关键技术之一。
- 1、下载文档前请自行甄别文档内容的完整性,平台不提供额外的编辑、内容补充、找答案等附加服务。
- 2、"仅部分预览"的文档,不可在线预览部分如存在完整性等问题,可反馈申请退款(可完整预览的文档不适用该条件!)。
- 3、如文档侵犯您的权益,请联系客服反馈,我们会尽快为您处理(人工客服工作时间:9:00-18:30)。
凸点芯片倒装焊接技术及可靠性测试目录一、倒装焊工艺的选择随着轻量化、薄型化、小型化、I/O 端数的增加以及功能多样化的发展,传统的封装技术已不能满足高密度的要求。
倒装互连技术的发展为高密度封装带来了希望。
倒装技术与传统引线键合互连技术相比具有明显的优势,主要表现在以下几个方面:(1)尺寸小、薄,重量更轻;(2)密度更高,使用倒装焊技术能增加单位面积内的I/O 数量;(3)性能提高,短的互连减小了电感、电阻以及电容,信号完整性、频率特性更好;(4)散热能力提高,倒装芯片没有塑封体,芯片背面可用散热片等进行有效的冷却,使电路的可靠性得到提高;倒装焊技术中关键工艺有四个,它们分别是UBM 制备、凸点制备、倒装焊和底部填充技术,它们直接决定着倒装产品质量的好坏。
UBM的制备多层金属膜UBM(Under Bump Metallurgy)是在芯片上的Al 焊盘与凸焊点之间的一层金属化层,目的是使芯片与基板互连工艺更容易实现、互连可靠性更高。
UBM必须与Al 焊盘及凸焊点间形成良好的欧姆接触、必须能够保证凸点或焊接材料不直接与Al 焊盘接触,以使连接材料有良好的黏附性能和机械性能,并确保优良的电性能和导热性能。
UBM通常由黏附层、扩散阻挡层和浸润层等多层金属膜组成。
UBM 在进行焊料回流或焊点退火等高温处理时,能够保证凸焊点材料不会穿透UBM而进入下面的Al 焊盘中。
铝焊盘上蒸发/溅射多层金属,粘附层Cr 、扩散层Cu、阻挡层Au凸点的制备倒装焊(Flip Chip)中的首个凸点制备技术是IBM公司的C4 工艺(Controlled Collaps Chips Connection)。
凸点由蒸发的薄膜金属制成。
随工艺技术和设备的发展,满足不同产品的需求,凸点制备工艺方法越来越多,当前比较常见的方法有1. 钉头法、2.蒸发/溅射法、3. 化学镀法、4.模板印刷法、5.电镀法、6.置球凸点法(SB2 - Jet)等。
1、钉头凸点法:在这几种方法中,钉头凸点方法是在焊盘上溅射/蒸镀上UBM后,使用金/铜丝球焊机在UBM上点上凸点,凸点会带有尾丝,所以在点完凸点后还需要去除尾丝。
该方法只适合引线数少、芯片焊盘间距相对较大、品种多且数量相对不多的芯片封装上,其具有工艺简便易行、方便灵活、可在单芯片上制作凸点、不合格芯片不需要制作凸点(其他方法制备凸点时,不合格芯片也是要制备凸点的),成本低廉,但是凸点高度一致性相对较差。
2、蒸发/ 溅射:该方法制备凸点由于其投资高、凸点制备速率慢等,只限于要求凸点材料纯度高、制备的凸点致密度高的,或者制备的凸点材料不能使用电镀、印刷工艺等时。
3、化学镀法:化学镀法可以包含焊盘的UBM处理,是采用化学的方法对芯片铝压焊点进行底层处理,然后再化学镀凸点。
特点是投资少,工艺步骤少,不需要溅射/ 蒸发、光刻、电镀等,成本低,但是化学镀的镀液成分复杂,较难掌握,凸点高度受限,镀层均匀性较差,适用于单芯片、凸点高度要求低的。
4、模板印刷法:现在采用的大部分模板印刷法如图所示,通过涂刷器和模板,将钎料膏涂刷在焊盘上。
目前应用比较多的情况是焊盘间距在200—400um间,对于小间距焊盘,由于模板印刷不能均匀分配钎料体积,应用受到一定限制,而本课题中凸点间距1000um是大大超过该方法的最低限制的,是可以使用该方法的。
同时,300um的球径也满足“模板涂刷最大颗粒直径应小于模板孔径最小值的1/3”这一普遍要求。
而且模板印制法工艺简单成本低,适合制作各种尺寸Pb-Sn 和无铅钎料凸点,可批量生产。
使用该方法的关键在于要制作模板及钎料球的均匀性,以及钎料涂膏印制厚度的一致性。
5、电镀法:该方法为国际上流行且工艺成熟的凸点制作法。
电镀凸点工艺所需的UBM 同样是采用蒸发/ 溅射,但相对UBM要厚许多倍的凸点制备则采用设备投入少、运行成本低的电镀工艺方法取代。
电镀工艺重复性、一致性好,可用于批量生产加工各种类型规格芯片及不同材料、不同高度的凸点。
凸点材料主要有焊料凸点、金凸点和铜凸点三种。
6、置球凸点法:又称为SB2-Jet(solder ball bumping jet),如图10所示,该系统为PacTech 公司研制的直接植球设备。
在放置焊料球用激脉冲光同时对焊球进行回流焊,一次性完成。
该过程首先将加工好的焊料球放在储存槽中,钎料球经毛细管释放喷出(该过程时间很短,不会影响球的形状)。
在喷出时,激光系统对球加热使之熔化,使钎料球润湿芯片焊盘并形成良好的接合。
此过程用惰性气体保护,不需焊剂。
该方法简单快捷、生产效率高、可灵活应用,但投资成本也较高。
7、转移法中又有焊膏/ 焊料转移和焊球直接转移。
焊膏印刷再转移法和焊料注入转移传送法已成熟,焊料印刷转移法是首先在载体上通过印刷的方法制作出焊料球,然后再转送到焊盘上去,参见图12,其中载体必须是与焊料不润湿的材料,并且要求图样与芯片焊盘高度一致。
焊球注入转移传送法,首先在载体上注入焊料,形成焊球,然后回流,然后再进行转移。
如果其中载体上有焊料坑,可以通过压力把焊料注入到坑中。
该方法设备投入少,生产效率高。
针对本课题的锡银铜无铅焊球,选用模板印刷比较合适,焊球球径可以通过模板的孔径和高度调控施加焊料的多少,在后续回流的过程中熔成相应球径。
(助焊剂?)焊接方法熔焊(哪种回流焊设备,整体加热Or局部?)、热压、热压超声适用于本课题的倒装焊接技术主要有熔焊、热压焊、热声焊4.1 熔焊焊料可以是基板焊盘上的、芯片凸点端上的或者是焊球来充当。
基板上的焊料可以刷焊膏再回流形成,也可以是电镀、溅射/ 蒸发获得;铜凸点、高温焊料凸点上的焊料通常是电镀上去的。
倒装凸点密度比较大的,则主要采用电镀、溅射/ 蒸发工艺方法制备;而密度小(如间距≥0.4mm)、数量少的,则用焊膏印刷然后再回流制备,或直接使用焊料球或焊盘浸焊剂然后回流制备,这样制造的性价比最优,必要时需要清洗掉残留的焊剂,方可确保底部填充质量。
真空再流焊。
助焊剂?4.2 热压焊接与熔焊工艺不同,热压焊接工序中,不仅要对芯片凸点加热,还要施加一定的压力。
该工艺要求芯片或者基板上的凸点为金凸点(可电镀、溅射/ 蒸发方法制备,或者采用钉头凸点方法制备),同时还要有一个可与凸点连接的表面(如电镀或溅射/ 蒸发的金层)。
热压焊接的温度一般在300℃左右,这样才能使材料充分软化,促进连接过程中的扩散作用,使连接可靠。
该方法的优点是工艺简单,工艺温度低,无需使用焊剂,可以实现细间距连接;缺点是热压压力较大,仅适用于刚性基底(如氧化铝或硅),基板必须保证高的平整度,热压头也要有高的平行对准精度。
为避免半导体材料受到不必要的损害,设备施加压力要有精确的梯度控制能力。
4.3 超声热压焊超声热压焊连接是将超声波应用在热压连接中,使焊接过程更加快速。
超声波的引入使连接材料迅速软化,易于实现塑性变形。
热超声的优点是可以降低连接温度,缩短加工处理的时间。
缺点是可能在硅片上形成小的凹坑,主要是由于超声震动过强造成的。
该方法主要适用于金凸点、镀金焊盘的组合。
热超声倒装连接的可靠性要受基板与芯片的热膨胀系数(TEC)失配的影响,同时焊点高度、最大焊点距离亦对可靠性有影响。
连接区的裂纹多是在从焊接连接时从高温冷却下来的过程中产生的。
由于金的熔点温度高,因此它对疲劳损伤的敏感程度远小于一般的焊料凸点的。
如果在热循环中应力没有超过凸点与焊盘之间的连接强度,那么可靠性不会存在太大问题。
下底料填充(填充什么、怎么填充)底部流动、底部不流动由于硅芯片、焊料凸点和基板等材料的热膨胀系数不匹配,如表3 所示,使用过程中很容易因热失配而造成连接失效。
下填充技术能够减少硅芯片和基板间热膨胀失配造成的影响,并能有效地缓冲机械冲击的损伤程度。
其中焊料凸点与焊盘的连接界面处承受着更容易失效的风险,通过下填充可以将芯片、凸点和基板紧紧地黏附在一起,达到重新分配整个芯片上的热膨胀系数失配和机械冲击产生的应力和应变力。
下填充提供了一个好的机械连接,大大提高了封装的可靠性,并且还能防止湿气和其他形式的沾污。
使用下填充能够大大提高倒装连接的寿命,与相同封装无填充的倒装比较其使用寿命可以提高5~20 倍。
下填充工艺有两种,底部流动填充和底部不流动填充。
底部流动填充工艺,是在毛细表面张力作用下,胶填充芯片和基板底部空隙之间,胶的流动能够使芯片和基板之间的气体尽量驱除出去,减少气泡的残留。
芯片与基板之间空隙足够大时,可选用底部流动填充工艺,如果芯片面积特别大或芯片与基板的空隙小可以选择底部不流动填充工艺,应根据不同的需要选择相应的填充工艺。
二、锡银铜钎料倒装再流焊温度曲线设定原理再流焊的原理:当PCB 进入升温区(干燥区)时,焊膏中的溶剂、气体蒸发掉,同时,焊膏中的助焊剂润湿焊盘、元器件端头和引脚,焊膏软化、塌落、覆盖了焊盘,将焊盘、元器件引脚与氧气隔离; PCB 进入保温区时,使PCB和元器件得到充分的预热,以防PCB 突然进入焊接高温区而损坏PCB 和元器件。
当PCB进入焊接区时,温度迅速上升使焊膏达到熔化状态,液态焊锡对PCB 的焊盘、元器件端头和引脚润湿、扩散、漫流或再流混合形成焊锡接点; PCB进入冷却区,使焊点凝固,此时完成了再流焊。
温度曲线设置及其依据温度曲线是保证焊接质量的关键,实时温度曲线和焊膏温度曲线的升温斜率和峰值温度应基本一致。
160℃前的升温速度控制在1℃/s—2℃/s。
如果升温斜率速度太快,一方面使元器件及PCB受热太快,易损坏元器件,易造成PCB变形。
另一方面,焊膏中的熔剂挥发速度太快,容易溅出金属成份,产生焊锡球;峰值温度一般设定在比焊膏金属熔点高30℃—40℃左右(比如本课题的Sn3.0Ag0.5Cu焊膏的熔点在217℃左右,峰值温度可设置为250℃),再流时间为30s—60s。
峰值温度低或再流时间短,会使焊接不充分,严重时会造成焊膏不熔。
峰值温度过高或再流时间长,造成金属粉末氧化,还会增加共界金属化合物的产生,使焊点发脆,影响焊点强度,甚至会损坏元器件和印制板。
而且设置温度曲线必需要有一定的依据:①不同金属含量的焊膏有不同的温度曲线,应按照焊膏加工厂提供的温度曲线进行设置(主要控制升温速率、峰值温度和再流时间)。
②根据PCB板的材料、厚度、是否多层板、尺寸大小。
③根据表面组装板搭载元器件的密度、元器件的大小以及有无BGA 、CSP等特殊元器件进行设置。
④要根据设备的具体情况,例如加热区长度、加热源材料、再流焊炉构造和热传导方式等因素进行设置。
⑤热风炉和红外炉有很大区别,红外炉主要是辐射传导,其优点是热效率高,温度陡度大,易控制温度曲线,双面焊时PCB上、下温度易控制。
其缺点是温度不均匀。
在同一块PCB 上由于器件的颜色和大小不同、其温度就不同。