煤基费托合成油加氢裂化反应稳定控制的方法探讨
加氢裂化转化率和调节手段

加氢裂化转化率和调节手段加氢裂化是石油化工中一种重要的催化裂化工艺,可以生产出丰富的石油产品。
但是,加氢裂化转化率是影响产品质量和经济效益的一个重要指标,需要得到有效的控制。
加氢裂化转化率主要受到压力、温度、氢气流量、试剂比例等工艺参数的影响。
在确定合理的工艺参数时,需要考虑到反应的热力学和动力学条件。
通常来说,加氢裂化的反应热量较大,因此需要控制反应的温度,以避免反应失控。
同时,氢气也是加氢裂化反应中的重要参与者,需要保证氢气流量的充足,以提高反应效率。
除了工艺参数的控制之外,还可以采用催化剂的调节手段来增强加氢裂化转化率。
催化剂是加氢裂化反应中的关键因素,对反应速率和选择性都有着重要的影响。
通常来说,催化剂需要具备活性高、稳定性好、抗中毒性强等特点。
在使用催化剂时,可以采用以下几个调节手段:1. 催化剂的再生。
在催化剂的使用过程中,会受到碳积累、焦炭沉积等因素的影响,导致催化剂的活性下降。
因此,在一定周期内需要对催化剂进行再生,以恢复其活性。
2. 催化剂的表面改性。
通过物理或化学手段改变催化剂的表面结构和化学性质,可以有效提高其反应活性和选择性。
3. 催化剂的物理或化学混合。
将具有不同化学性质的催化剂物理或化学混合使用,可以将各种催化剂的优点充分发挥,提高反应效率和选择性。
4. 催化剂载体的改性。
通过改变催化剂的载体结构和性质,可以调节催化剂的酸碱性、孔径大小等特性,从而实现催化剂的选择性调节。
总之,加氢裂化转化率是影响石油加工生产的重要因素,需要通过合理的工艺参数和催化剂调节手段来实现控制。
催化裂化 加氢裂化吸收稳定系统流程及优化

催化裂化加氢裂化吸收稳定系统流程及优化1. 引言1.1 概述催化裂化和加氢裂化是石油炼制领域中常用的重要工艺,主要用于石油原料的转化和提纯。
通过催化裂化和加氢裂化技术,可以将重质石油馏分转变为更高附加值的产品,如汽油、柴油、润滑油等。
这些工艺的关键在于稳定系统流程的运行,以确保产品质量的稳定性、生产效率的提高和设备寿命的延长。
本文目的在于深入探讨催化裂化和加氢裂化吸收稳定系统流程,并提出优化方案以改善工艺效果。
首先概述了本文将要讨论的内容和结构,然后介绍了引言部分的目标。
1.2 文章结构本文主要分为五个部分进行描述。
第一部分是引言,简要介绍了本文内容和结构。
第二、三和四部分则详细讨论了催化裂化系统流程、加氢裂化系统流程以及吸收系统流程优化。
最后一部分是结论与展望,总结了已经探讨过的内容,并对未来进行展望。
1.3 目的本文的目的是深入探讨催化裂化和加氢裂化吸收稳定系统流程,并提出优化方案以改善工艺效果。
通过对系统组成、工艺概述和问题解决方案的介绍,旨在帮助工程师和研究人员更好地理解这些重要工艺,并为实践中的流程优化提供指导。
同时,本文还将对未来的研究方向进行展望,为相关领域提供新的思路和建议。
通过深入分析和讨论,我们期望能够推动催化裂化和加氢裂化技术的进一步发展和优化。
以上就是引言部分的内容,在接下来的文章中,我们将逐一探讨催化裂化系统流程、加氢裂化系统流程以及吸收系统流程优化。
这些内容将有助于读者更好地理解相关工艺,并为实践中的问题解决和优化提供参考。
最后,我们将对已经探讨过的内容进行总结,并展望未来该领域研究方向。
以下内容不属于引言部分。
2. 催化裂化系统流程:2.1 系统组成:催化裂化系统主要由反应器、催化剂输送装置、分离装置和再生装置组成。
其中,反应器是催化裂化过程中最重要的组件,它用于将原料油在催化剂的作用下发生裂解反应。
催化剂输送装置用于将新鲜催化剂及再生后的催化剂注入反应器中。
分离装置则用于将裂解产物进行分离和提纯,包括汽油分离塔、液-液萃取塔等。
加氢裂化装置优化运行生产航煤技术攻关

加氢裂化装置优化运行生产航煤技术攻关为了提高航煤的品质,同时降低其生产成本,加氢裂化装置的优化运行成为了一项具有重要意义的技术攻关。
针对这一问题,本文将从以下三个方面进行探讨:加氢裂化装置的工艺原理和流程;装置优化运行的必要性和挑战;装置优化运行中的关键技术和应用方法。
一、加氢裂化装置的工艺原理和流程加氢裂化是利用催化剂和氢气使长链烃分子在高温下断裂成短链分子的工艺。
加氢裂化装置的主要部件包括加氢反应器、分馏塔、冷却器等。
其工艺流程如下图所示:[插入图片]在这一工艺中,原料油进入加氢反应器后,在氢气的存在下,经过高温高压的加氢反应,长链烃分子被断裂成短链烃分子。
随着反应的进行,反应器中不断有新的短链分子生成,同时也有短链分子进一步加氢,生成更短的分子。
这时,分馏塔将反应产物分为轻质和重质两部分,轻质部分包含甲烷、乙烷、丙烷等气态产品,重质部分则包含乙烯、丙烯、苯等液态产品。
最后,这些产品经过冷却器冷却,通过分选装置分离出不同产品。
二、装置优化运行的必要性和挑战加氢裂化装置的优化运行主要是为了提高产品的催化裂化效率和产品品质,同时降低生产成本。
具体来说,装置优化运行的必要性体现在以下几个方面:1.提高产品的品质。
通过优化反应的温度、压力、质量比等因素,可以使产物中不同组分的含量得到有效控制,从而提高产品的品质和附加值。
2.降低生产成本。
装置优化运行可以帮助企业在提高产品品质的同时,尽可能降低生产成本,提高经济效益和市场竞争力。
3.优化反应系统的安全性。
优化加氢裂化装置的运行参数,可以有效减少一些不必要的反应失控和事故风险,保证生产过程的稳定性和安全性。
然而,装置优化运行所面临的挑战也不容忽视。
首先,加氢裂化反应机理较为复杂,其反应产物不仅涉及到烃类气体和液体,还可能出现其他非烃类物质,例如硫化物、酸性物等。
其次,不同反应物质的加工条件和要求也不尽相同,因此在不同的工作状态下对不同反应物质进行加工还需要进行针对性的优化。
费托合成油品加氢裂化异构化反应的热力学

Do I : 1 0 . 3 9 6 9 / j . i s s n . 1 0 0 5 - 9 9 5 4 . 2 0 1 4 . 0 3 . 0 0 7
应温度的选择应兼顾各种反应 的进 行 ; 烯烃 比烷 烃更 容易发 生加氢 裂化异 构化反 应 ; 所获得 的热力学 数据可 为费 托合成油品加氢裂化异构化工 艺研 究 、 反应器开 发以及新 型催化剂研制等提供理论依据 。 关键词 : 费托合成 油品 ; 加氢裂化异 构化 ; 热力学分析 ; 反应 限度
W U J i a n - mi n , S U N Qi - we n, Z H ANG Z o n g — s e n , P AN G L i - f e n g
( S t a t e K e y L a b o r a t o r y o f C o a l L i q u e f a c t i o n a n d C o a l C h e m i s t r y , S h a n g h a i Y a n k u a n g E n e r g y R & D C o . , L t d . , S h a n g h a i 2 0 1 2 0 3 ,C h i n a )
c h a n g e ,Gi b b s f r e e e n e r g y c h a n g e a n d e q u i l i b i r u m c o n s t a n t o f h y d r o c r a c k i n g a n d i s o me r i z a t i o n r e a c t i o n o f F i s c h e r —
加氢裂化转化率和调节手段

加氢裂化转化率和调节手段引言加氢裂化技术是炼油工业中常用的重要工艺之一,主要用于转化重质烃类原料(如重柴油、重油)为轻质烃类产品(如汽油、燃料油)。
而加氢裂化转化率则是评价该技术效果的重要指标之一。
在实际生产过程中,通过对加氢裂化转化率进行调节手段的应用,能够有效提高产品质量、降低生产成本、提高工艺稳定性。
本文将介绍加氢裂化转化率及其调节手段的相关内容,以期为相关从业人员提供一些思路和建议。
一、加氢裂化转化率的影响因素加氢裂化转化率是指在加氢裂化反应过程中,原料烃类被转化为轻质烃类产品的比例。
在实际生产中,影响加氢裂化转化率的因素有很多,主要包括以下几个方面:1. 催化剂的选择和活性:选择合适的催化剂对提高转化率具有重要作用。
活性高、稳定性好的催化剂能够更好地促进反应的进行,提高转化率。
2. 反应温度和压力:反应温度和压力是影响加氢裂化转化率的关键因素。
通过合理控制反应温度和压力,可以实现更高的转化率。
3. 原料烃类性质:原料烃类的性质对加氢裂化反应也有着重要影响。
原料烃类的分子结构、碳数、硫含量等都会对转化率产生影响。
5. 反应副产物的影响:在加氢裂化反应中,副产物如焦炭、硫化物等会对催化剂活性产生影响,从而影响转化率。
以上几个因素是影响加氢裂化转化率的主要因素,针对这些因素进行合理的调节手段,可以有效提高加氢裂化转化率。
二、调节手段在实际生产中,采用各种调节手段对加氢裂化转化率进行提高是一个重要的技术工作。
下面将介绍一些常用的调节手段:3. 催化剂再生和中毒物的处理:催化剂在使用过程中可能会遇到中毒等情况,通过对中毒催化剂进行再生或者处理,可以恢复催化剂的活性,从而提高转化率。
4. 反应器结构和空速的调整:通过对反应器结构和反应空速进行调整,可以实现更好的转化效果。
改变反应器的结构,优化反应空速等手段都可以提高转化率。
5. 副产物的处理:对反应过程中生成的副产物进行合理处理也是提高转化率的一种重要手段。
加氢裂化装置优化运行生产航煤技术攻关
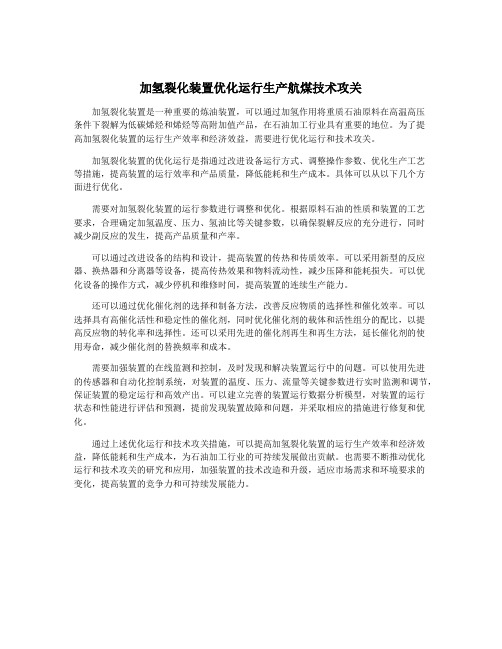
加氢裂化装置优化运行生产航煤技术攻关加氢裂化装置是一种重要的炼油装置,可以通过加氢作用将重质石油原料在高温高压条件下裂解为低碳烯烃和烯烃等高附加值产品,在石油加工行业具有重要的地位。
为了提高加氢裂化装置的运行生产效率和经济效益,需要进行优化运行和技术攻关。
加氢裂化装置的优化运行是指通过改进设备运行方式、调整操作参数、优化生产工艺等措施,提高装置的运行效率和产品质量,降低能耗和生产成本。
具体可以从以下几个方面进行优化。
需要对加氢裂化装置的运行参数进行调整和优化。
根据原料石油的性质和装置的工艺要求,合理确定加氢温度、压力、氢油比等关键参数,以确保裂解反应的充分进行,同时减少副反应的发生,提高产品质量和产率。
可以通过改进设备的结构和设计,提高装置的传热和传质效率。
可以采用新型的反应器、换热器和分离器等设备,提高传热效果和物料流动性,减少压降和能耗损失。
可以优化设备的操作方式,减少停机和维修时间,提高装置的连续生产能力。
还可以通过优化催化剂的选择和制备方法,改善反应物质的选择性和催化效率。
可以选择具有高催化活性和稳定性的催化剂,同时优化催化剂的载体和活性组分的配比,以提高反应物的转化率和选择性。
还可以采用先进的催化剂再生和再生方法,延长催化剂的使用寿命,减少催化剂的替换频率和成本。
需要加强装置的在线监测和控制,及时发现和解决装置运行中的问题。
可以使用先进的传感器和自动化控制系统,对装置的温度、压力、流量等关键参数进行实时监测和调节,保证装置的稳定运行和高效产出。
可以建立完善的装置运行数据分析模型,对装置的运行状态和性能进行评估和预测,提前发现装置故障和问题,并采取相应的措施进行修复和优化。
通过上述优化运行和技术攻关措施,可以提高加氢裂化装置的运行生产效率和经济效益,降低能耗和生产成本,为石油加工行业的可持续发展做出贡献。
也需要不断推动优化运行和技术攻关的研究和应用,加强装置的技术改造和升级,适应市场需求和环境要求的变化,提高装置的竞争力和可持续发展能力。
加氢裂化转化率和调节手段

加氢裂化转化率和调节手段加氢裂化是一种重要的石油化工过程,其主要作用是将高分子烃类化合物转化为低碳数的烃类产品,以满足石油产品市场的需要。
在加氢裂化过程中,转化率是一个非常重要的参数,它能够反映出反应器的性能和操作效果。
而为了达到更好的转化率,需要采取一些调节手段来优化加氢裂化的工艺条件。
本文将从加氢裂化转化率和调节手段两方面进行讨论。
一、加氢裂化转化率加氢裂化转化率是指在一定反应条件下,原料烃类化合物发生裂化反应后所转化成的产品的化学反应率。
在加氢裂化过程中,烃类化合物通过裂解反应,生成低碳数的烃类产品。
转化率的高低直接影响到产品的质量和产量,因此是一个重要的工艺指标。
加氢裂化转化率受多种因素影响,包括反应温度、催化剂活性、压力、空速、烃类物料性质等。
一般来说,较高的反应温度和较高的压力会促进裂化反应的进行,从而提高转化率。
过高的温度和压力可能导致催化剂的失活和设备的损坏,因此需要在安全范围内进行调控。
催化剂的选择和活性也对加氢裂化转化率产生影响。
优质的催化剂应具有良好的烃裂解活性和稳定性,能够在较高温度和压力下保持高的转化率。
对于高硫、高金属含量的原料烃类化合物,还需要选择具有较强抗毒性的催化剂,以延长其使用寿命。
二、调节手段为了优化加氢裂化的工艺条件,提高转化率,可以采取一些调节手段来进行调控。
主要的调节手段包括控制反应温度、调整压力、改良催化剂性能、优化原料烃类物料性质等。
1. 调控反应温度控制反应温度是影响加氢裂化转化率的关键因素之一。
通常情况下,提高反应温度会促进裂解反应,从而提高转化率。
过高的温度会导致催化剂的失活和设备的损坏,因此需要在安全范围内进行调控。
可以通过增加或减少热交换器的热载体流量,调节反应器的冷却方式,控制反应温度的升降,以实现对反应温度的有效调控。
2. 调整压力在加氢裂化过程中,适当的压力是保证裂化反应进行的必要条件之一。
通常情况下,提高压力可以促进裂化反应,从而提高转化率。
加氢工艺处理煤液化加氢稳定油的研究

加工工艺炼油技术与工程PETROLEUM REFINERY ENGINEERING2019年第49卷第6期加氢工艺处理煤液化加氢稳定油的研究陈光,黄新露,吴子明,李扬,范思强(中国石油化工股份有限公司大连石油化工研究院,辽宁省大连市116045)摘要:加氢精制与加氢改质都是煤液化加氢稳定油高附加值利用的有效途径。
实验结果表明,两种工艺在产物分布、化学氢耗与装置液体收率以及产品质量等方面存在明显差异。
与加氢精制工艺相比,加氢改质工艺得到的高附加值产品(重石脑油+喷气燃料)收率髙、喷气燃料与柴油产品品质更佳、重石脑油芳桂潜含量相对较低,但仍为优质的重整原料;在反应温度3609/380t、体系压力16.0MPa、体积空速0.69h"、氢油体积比800:1的反应条件下重石脑油与喷气燃料总收率为42.5%,重石脑油芳怪潜含量为76.11%,喷气燃料烟点为26mm、改质柴油十六烷值提升到49,表明加氢改质为更优的煤液化加氢稳定油处理工艺。
关键词:加氢精制加氢改质煤液化加氢稳定油处理工艺重石脑油喷气燃料煤化工过程中会产生大量的煤直接液化油,需经催化加氢环节脱除油品中的杂原子及芳桂得到煤液化加氢稳定油。
但煤液化加氢稳定油仍含有较多的硫、氮杂原子及难脱除的单环芳烧,需经进一步处理才能得到高附加值的石化产品。
加氢处理工艺包含常规的加氢精制与加氢改质等工艺方法。
加氢精制的主要化学反应包括加氢脱除硫、氮、氧等杂原子和金属杂质、烯坯和芳桂加氢饱和;加氢改质主要的化学反应包括裂解反应、环烷怪和芳桂的部分加氢开环等。
用加氢处理工艺可以降低柴油硫含量,提高十六烷值,提升柴油的流动性能尤其是低温流动性,提高油品的安定性“切。
在现有形势下研究煤液化加氢稳定油的加氢处理工艺,有利于煤化工产品比例最优化和经济效益最大化,满足国内对煤化工领域产品升级的技术要求。
1实验部分1.1装置流程采用中国石油化工股份有限公司大连(抚顺)石油化工研究院开发的加氢精制催化剂与改质催化剂体系,在200mL固定床加氢试验装置上进行加氢改质试验。
- 1、下载文档前请自行甄别文档内容的完整性,平台不提供额外的编辑、内容补充、找答案等附加服务。
- 2、"仅部分预览"的文档,不可在线预览部分如存在完整性等问题,可反馈申请退款(可完整预览的文档不适用该条件!)。
- 3、如文档侵犯您的权益,请联系客服反馈,我们会尽快为您处理(人工客服工作时间:9:00-18:30)。
煤基费托合成油加氢裂化反应稳定控制的方法探讨
摘要本文从反应温度、反应压力、氢油比、原料油性质等方向着手,分析讨论
了影响煤基费托合成油加氢裂化反应的各种因素,进而得出稳定控制反应的方法。
控制原料油的馏程和流量,根据组分变化及时调整反应温度;严格控制裂化反应
器入口和各床层的温度,升温速率不能太快,适当提高氢分压和氢油比;加强循
环氢压缩机的运行监护,保证急冷氢供应充足。
最后提出反应器超温时一些合理
的处理方法,为今后加氢裂化装置生产过程操作和超温事故的处理提供一些操作
依据。
关键词加氢裂化装置温升因素反应超温处理
国家能源集团神华宁煤煤制油分公司400万吨/年煤制油项目加氢裂化装置采
用两台反应器并联裂化尾油全循环的工艺,由反应系统、分馏系统、热工和公用
工程等部分组成。
原料为加氢精制装置减压塔底精制尾油,主要产品为混合柴油、重柴油、液化石油气、稳定石脑油,装置操作灵活。
加氢裂化反应是高温、高压、临氢的催化裂化反应,反应是放热反应,且煤
基费托合成油存在无硫、无氮、低芳香烃、正构烷烃含量高等特点,影响反应的
因素较多,且温升波动大,操作难度高。
如果操作不当,反应器极易超温,甚至
飞温,轻则烧损催化剂,重则发生泄漏、中毒及着火爆炸事故。
所以,如何稳定控
制裂化反应至关重要的,本文探讨了影响反应的因素,得到稳定控制加氢裂化反
应的方法。
1 影响加氢裂化反应的因素
1.1 反应温度
对裂化反应影响最大的因素是反应温度,也是最主要、最灵活的操作参数,
可通过控制反应温度来调整产品质量和转化率。
由于裂化反应是放热反应,提高
反应温度会抑制反应的进行。
反应温度过低会减慢反应速度,降低反应转化率。
反应温度过高会使裂化反应加剧,产品收率降低,同时易导致催化剂积炭,床层
压差增大。
另外,反应温度与空速具有关联性,在总进料量稳定的情况下,空速
相对于反应温度变化滞后。
因此,为保证反应器稳定运行,升温速率要缓慢。
1.2 反应压力
反应压力直接影响裂化反应的氢分压,是影响反应的重要控制参数。
裂化反
应是体积缩小的反应,提高反应压力有利于反应的进行。
然而,反应压力的提高,操作费用和安全风险也相应提高。
故应综合考虑产品生产方案和原料油性质,并
兼顾操作的灵活性,来确定“最经济的反应压力”,才具有较好的技术经济性。
1.3 氢油比
氢油比的大小直接关系到氢分压和油品的停留时间,并且还影响油的汽化率。
循环气量的增加可以保证系统有足够的氢分压,有利于加氢反应。
此外,过剩的
氢气可起到保护催化剂表面的作用。
在一定的范围内可防止油料在催化剂表面缩
和结焦;同时,氢油比增加可及时的将反应热从系统带出。
有利于反应床层的热
平衡,从而使反应器内温度容易控制平稳。
但过大的氢油比会使系统的压降增大,油品和催化剂接触的时间缩短,从而会使反应深度下降,循环机负荷增大,动力
消耗增大。
因此,必须根据装置运行情况设置合理的氢油比,一般最为经济合理
氢油比为化学耗氢的4-5倍。
1.4 原料油性质
不同的原料油组成,裂化反应的深度不一样,产生的热量也不一样。
加氢精
制尾油作为裂化装置的原料油,与裂化循环油共同进入裂化反应器。
精制尾油和
裂化循环油的轻重和流量对反应都有较大影响。
原料干点是加氢裂化原料一项重
要的控制指标。
干点提高,黏度增大,原料向催化剂内部扩散速度降低,降低了反应
速度,同时分布不均匀易造成催化剂表面积炭。
2 裂化反应的控制方法
本装置加氢裂化反应器有4个床层,一床层可以根据目标转化率和产品质量
通过加热炉出口温度来控制,其它三个床层可由上一床出口温度和急冷氢来控制。
由于入口温度变化后产品分布和产品质量的表现需要一定的时间,故升温或降温
需要有一定时间间隔,一般控制不超过5℃/h。
循环氢的纯度直接影响加氢裂化反应氢分压,影响循环氢纯度的因素有很多,原料油的性质、反应温度、反应压力、催化剂活性、尾氢排放量、新氢纯度等,
通常通过控制尾氢排放量来控制循环氢纯度。
尾氢排放量增大,循环氢纯度增加;尾氢排放量减少,循环氢纯度降低。
提高循环氢纯度有利于加氢裂化反应进行,
但是,为提高循环氢纯度必须大量排放尾氢,造成物耗增加,成本增大。
循环氢
纯度降低,平均分子量增大,在循氢机转速不变的情况下,循氢机负荷增大,透
平蒸汽消耗增加。
因此,要控制循环氢纯度在适当范围,本装置循环氢纯度控制
在>95%。
3 加氢裂化飞温的处理方法
加氢裂化反应一旦出现温升大幅升高,应立即确认循氢机是否正常运行。
如
循氢机正常运行,应立即开大相应床层急冷氢阀,提高急冷氢量,控制反应温升,同时防止大量热量被带到下一床层,造成下一床层飞温,只要发现及时并且处理
得当,一般可避免飞温。
如果循氢机停止运行,或者床层温升急剧上升,应立即
打开0.7MPa/min或2.1MPa/min紧急泄压阀泄压,通过紧急泄压带走大量的反应热,来降低系统温度、保护床层催化剂,防止生产事故的发生。
加氢裂化装置一般有0.7MPa/min、2.1MPa/min和现场手动泄压三种方式。
0.7MPa/min泄压系统在循环氢压缩机故障时自动启用。
也可由操纵台操作员在需要快速停车的情况下启用。
当0.7MPa/min泄压系统启用时,下列动作会自动发生:反应器进料泵停车、反应加热炉停车。
如果0.7MPa/min泄压系统手动启用,循环氢压缩机将继续运转。
在0.7MPa/min泄压开始后,观察所有的反应器温度,确认所有温度下降或不变。
如果反应器温度继续上升,立即开始2.1MPa/min泄压。
0.7MPa/min泄压系统后,只有在已建立可靠的氢气循环且所有反应器温度都低于正常操作值至少30℃,泄压阀才应关闭。
4 结论
根据以上分析,要保证加氢裂化装置安全稳定长周期运行,必须做到以下几点:①由于裂化循环油与精制尾油混合作为裂化反应进料,因此要严格监控分馏系统侧线抽出率和操作稳定性,原料的馏程和流量要控制稳定,当终馏点偏高时,要
及时提高反应温度,防止系统负荷增大。
②反应温升较温度变化滞后,反应器入口温度提高后,需要一段缓冲时间来达到新的平衡,故升温速率一定要缓慢。
③严格控制循环氢纯度,通过每8小时循环氢纯度分析结果,及时调整尾氢排放量
和新氢补充量。
④根据反应运行情况,维持稳定的氢油比,严格控制各项参数在指标范围内,密切注意原料性质及组成的变化,提前预判处理,实现装置稳定控制。
参考文献:
[1]曾榕辉祁兴维.石油炼制与化工,2002,36(6):27~31.
[2]郑世桂.炼油技术与工程,2003,33(5):11~14.。