ANSYS 连杆机构运动分析实例—曲柄滑块机构
曲柄滑块机构基于ANSYS的运动特性分析

ANSYS学习心得学院:班级:学号:姓名:时间:2012年7月2日——7月6日曲柄滑块机构基于ANSYS的运动特性分析摘要:随着工业的发展,不同规格的曲柄滑块机构被应用到了更多的机械设备中去,在机械制造工业以及其他工业的生产中作用越来越显著,例如在汽车、电子、农业、医疗等部门都用广泛的应用。
因而提高机械的自动化程度,降低工人的劳动强度,改善劳动条件都离不开对曲柄滑块机构的研究。
本文使用有限元法对曲柄滑块机构进行运动特性分析。
首先利用解析法对问题进行求解,但是求解过程较为复杂,计算量大,鉴于ANSYS中有一类分析类型是结构动力学分析,符合本题得要求,可以加以应用,简化计算。
本文选择三维铰链单元COMBIN7建立模型进行分析求解。
对有限元与解析解进行分析与对比,可以看出有限元解的最优解的。
关键词:有限元法,运动特性,ANSYS,瞬态动力学Crank - slider mechanism motion characteristics analysis based on ANSYS Abstract :With development of industry, more and more different specifications of the Crank - slider mechanism is applied to the mechanical equipment. It pays an increasingly significant role in the machinery manufacturing industry and other industrial production with a wide range of applications .For example,in the auto industry ,Electronics, Agriculture, Medical and other departments . Therefor, the Crank - slider mechanism increases mechanical automation ,reducing labor intensity and improving working conditions.This paper using finite element method investigate the Crank - slider mechanism analysis of movement characteristics. Firstly, by using analytical method to solve problems,but solving process is relatively complex and large amount of calculation. There is a certain type of ANSYS which is a type of structure dynamics analysis, in accordance with the required analysis which can be used. The topic choices three dimensional hinge unit COMBIN7 on the analysis solution. In the end, the analytical solution and ANSYS finite element solution is compared, we can get the optimalsolution from the finite element .Key Words :Finite element method; Movement characteristics ;ANSYS; Transientdynamic第一章 引 言1.1 本文的主要研究内容ANSYS 是大型的通用有限元软件,其功能强大,可靠性好,具有强大的结构分析能力和优化设计模块,因而被国内外大多数机械行业所采用。
ANSYS对零部件设计中的解决方案
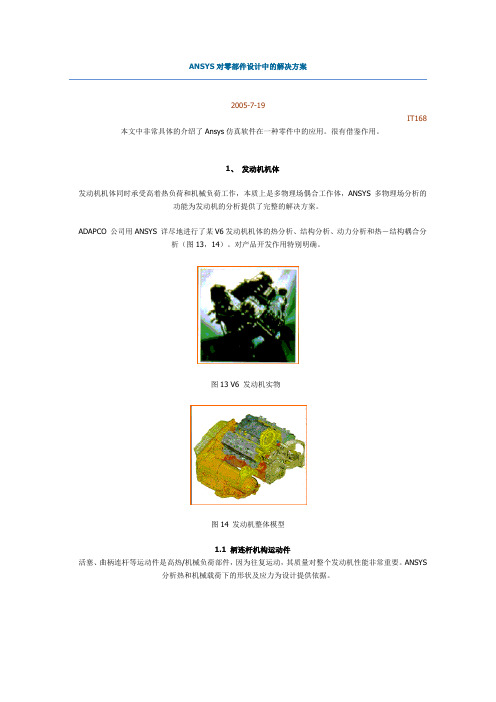
ANSYS对零部件设计中的解决方案2005-7-19IT168本文中非常具体的介绍了Ansys仿真软件在一种零件中的应用。
很有借鉴作用。
1、发动机机体发动机机体同时承受高着热负荷和机械负荷工作,本质上是多物理场偶合工作体,ANSYS 多物理场分析的功能为发动机的分析提供了完整的解决方案。
ADAPCO 公司用ANSYS 详尽地进行了某V6发动机机体的热分析、结构分析、动力分析和热-结构耦合分析(图13,14)。
对产品开发作用特别明确。
图13 V6 发动机实物图14 发动机整体模型1.1 柄连杆机构运动件活塞、曲柄连杆等运动件是高热/机械负荷部件,因为往复运动,其质量对整个发动机性能非常重要。
ANSYS分析热和机械载荷下的形状及应力为设计提供依据。
图15 曲柄连杆机构的柔体运动学、动力学分析连杆强度向来是发动机设计关键,ANSYS 柔体-柔体接触计算功能可以准确模拟连杆与大头盖、主销、曲柄销间联合工作状况。
这是ANSYS 系统分析功能和强大的接触功能体现。
ANSYS 曲轴结构分析和模态分析功能计算出曲轴扭转与弯曲模态,通过频率优化达到减震效果。
ANSYS 的疲劳计算功能,精确的计算曲轴传统疲劳强度,同时还可计算出曲轴的强度因子,从而预测疲劳裂纹的产生及疲劳寿命。
应用ANSYS 对曲轴轴颈及油膜进行流-固耦合分析评价高曲轴的耐磨性。
曲轴连杆机构运动件的重量优化设计,不仅是节省材料及发动机重量降低,运动件质量对改善发动机整体的工作状况特别有效,ANSYS 形状优化的功能可以对活塞内腔、活塞销孔、连杆形状、曲轴圆角和曲柄臂尺寸进行优化设计。
1.2 机体:缸盖、箱体、缸套机体、缸盖的热分析特别重要,热疲劳是失效和“拉缸”主要原因,为保证可*性与耐久性,应用ANSYS 分析机械和热负荷下的刚度、强度是设计师的首选。
ANSYS 可准确地计算出机体的自振频率及模态。
以控制噪声源。
此外ANSYS 可模拟机体的热冲击实验、热-结构耦合分析可计算出机械负载、热负荷双重作用下机体的变形,应力分布。
ANSYS 连杆机构运动分析实例—曲柄滑块机构

第15例 连杆机构运动分析实例—曲柄滑块机构[本例提示] 介绍了利用ANSYS 对连杆机构进行运动学分析的方法、步骤和过程,并使用解析解对有限元分析结果进行了验证。
着重介绍了曲柄滑块机构模型的创建以及约束的施加方法,介绍了三维铰链单元COMBIN7的使用方法。
15.1 概述本分析仍然属于瞬态动力学分析,分析过程与普通的瞬态动力学分析基本相同。
其关键在于三维铰链单元COMBIN7的创建,现在此简单介绍。
三维铰链COMBIN7单元属于三维单元,有5个节点,分别是活跃节点I 和J 、用以定义铰链轴的节点K 、控制节点L 和M (图15-1)。
活跃节点I 和J 应该位置重合,并且分属于LINK A 和B ,LINK A 和B 是一个单元或单元集合。
如果节点K 没有定义,则铰链轴为全球笛卡尔坐标系的z 轴。
三维铰链COMBIN7单元的进一步内容请参阅ANSYS 帮助文档。
另外,本分析必须将大变形选项打开。
15.2 问题描述及解析解图15-2所示为一曲柄滑块机构,曲柄长度R =250mm 、连杆长度L =620 mm 、偏距e =200 mm ,曲柄为原动件,转速为n 1=30 r/min ,求滑块3的位移s 3、速度v 3、加速度a 3随时间变化情况。
根据机械原理的知识[5][6],该问题的解析解十分复图 15-1 三维铰链单元COMBIN7图 15-2 曲柄滑块机构杂,使用不太方便。
本例用图解法解决问题,由于过程比较繁琐,而且只是为了验证有限元解的正确性,所以,关于滑块3的位移s 3、速度v 3、加速度a 3随时间t 变化情况的图形没有必要给出。
在这里只求解了以下数据:滑块的行程H =535.41 mm 。
机构的极位夹角为θ=19.43°,于是机构的行程速比系数242.1180180=-︒+︒=θθK 。
由于机构一个工作循环周期为2601==n T s ,所以机构工作行程经历的时间108.111=+=T K K T s ,空回行程经历的时间892.012=-=T T T s 。
基于ANSYS的曲柄滑块机构运动学分析

3 . 4 设 定非 线性 分 析 的收敛 值 在 确 定载 荷 步 时 间和 时 间步长 后 ,设定 非线
性 分析 的收敛 值 :V a l u e = l 、T o l e r = 0 . 1 。 3 . 5 施 加约 束
运 动规 律 即位移 S 3 、速度 V 3 、加速 度 a 3 、跳度 , 3 随时 间变化 情况 。
.
坐标 :C X= ( R + L ) * C OS ( F / ) ,C Y = 一 e 。 3 . 2 选择 单 元类型
三 维铰链 单 元 C OMB I N7属 于三 维单 元 ,如
图 2所 示有 5个 节 点 ,分别 是活 跃节 点 I 和J 、用 于 定义 铰链 轴 的节 点 K、控 制节 点 L和 M ,活跃
C
节 点 I和 J位 置 重合 ,并 且分 属 于 L I NK A 和
L I N KB,L I NK A和 L I NK B 是 一个 单元 集合 。如
图 1 曲柄滑块机构
果节 点 K 没有 定义 ,则铰链 轴 为全球 笛 卡 尔坐标 系的 z 轴。
2 理 论 分 析
根据 机 械原 理 的知 识 ,该 问题 的解 析解 十 分
复 杂 ,几乎 无 法使 用 。这个 问题用 传 统 的图解 法 】 可 以解 决 ,将 瞬 心法 和矢 量 方程 图解 法结 合 起 来 过程 稍简 便 一些 ,但还 是过 于繁 琐且 复杂 ( 参 见 参 考文 献【 1 】 ) , 由于 本文 是验 证有 限元 方法 的正确 性 ,所 以滑 块 3的运动 规律 这里 不给 出, 只给 出
通 过 Ma i n Me n u _ ÷ P r e p r 0 c e s s o r _ ÷ E l e me n t E 1 一
有限元案例分析(曲柄滑块机构)

University of Shanghai for Science and Technology 《有限元法》课程作业任课教师:学生姓名:学号:时间:目录一.问题描述与分析…………………………………………………………………..二. ANSYS 操作过程与方法................................................................ 1.定义工作文件名和工作标题..................................................................... 2.定义参量....................................................................................................... 3.选择单元类型.............................................................................................. 4.定义材料模型............................................................................................... 5.定义实常数................................................................................................... 6.创建节点........................................................................................................ 7.指定单元属性................................................................................................ 8.创建铰链单元................................................................................................. 9.指定单元属性.................................................................................................. 10.创建梁单元,用来模拟各个杆.............................................................. 三.有限元分析......................................................................................... 1.指定分析类型............................................................................................................. 2.打开大变形选项............................................................................................................... 3.确定载荷步时间和时间步长.......................................................................................... 4.确定数据库和结果文件中包含的内容........................................................................... 5.设定非线性分析的收敛值............................................................................................ 6.施加约束........................................................................................................................... 7.求解................................................................................................................................ 8.定义变量......................................................................................................................... 9.对变量进行数学操作.................................................................................................... 四.结果和课程总结. (3)4 4 456 678 89 91010 10 11 12 12 13 14 14 15 16一.问题描述与分析:背景:从大二以来经常有接触连杆机构,也一直很想定性的了解曲柄滑块机构中滑块的速度-时间变化曲线。
曲柄滑块机构运动分析

曲柄滑块机构运动分析一、相关参数在图1所示的曲柄滑块机构中,已知各构件的尺寸分别为mm l 1001=,mm l 3002=,s rad /101=ω,试确定连杆2和滑块3的位移、速度和加速度,并绘制出运动线图。
图1 曲柄滑块机构二、数学模型的建立1、位置分析为了对机构进行运动分析,将各构件表示为矢量,可写出各杆矢所构成的封闭矢量方程。
将各矢量分别向X 轴和Y 轴进行投影,得0sin sin cos cos 22112211=+=+θθθθl l S ll C(1) 由式(1)得2、速度分析将式(1)对时间t 求导,得速度关系C v l l l l =--=+222111222111sin sin 0cos cos θωθωθωθω(2) 将(2)式用矩阵形式来表示,如下所示⎥⎦⎤⎢⎣⎡-=⎥⎦⎤⎢⎣⎡⎥⎦⎤⎢⎣⎡-1111122222cos sin . 0 cos 1 sin θθωωθθl l v l lC(3) 3、加速度分析将(2)对时间t 求导,得加速度关系三、计算程序1、主程序%1.输入已知数据clear;l1=0.1;l2=0.3;e=0;hd=pi/180;du=180/pi;omega1=10;alpha1=0;%2.曲柄滑块机构运动计算for n1=1:721theta1(n1)=(n1-1)*hd;%调用函数slider_crank计算曲柄滑块机构位移、速度、加速度[theta2(n1),s3(n1),omega2(n1),v3(n1),alpha2(n1),a3(n1)]=slider_crank(theta1(n1),omega1,alpha1,l1,l2,e); endfigure(1);n1=0:720;subplot(2,3,1)plot(n1,theta2*du);title('连杆转角位移线图');xlabel('曲柄转角\theta_1/\circ');ylabel('连杆角位移/\circ');grid onsubplot(2,3,2)plot(n1,omega2);title('连杆角速度运动线图');xlabel('曲柄转角\theta_1/\circ');ylabel('连杆角速度/rad\cdots^{-1}');grid onsubplot(2,3,3)plot(n1,alpha2);title('连杆角加速度运动线图');xlabel('曲柄转角\theta_1/\circ');ylabel('连杆角加速度/rad\cdots^{-2}');grid onsubplot(2,3,4)plot(n1,s3);title('滑块位移线图');xlabel('曲柄转角\theta_1/\circ');ylabel('滑块位移/\m');grid onsubplot(2,3,5)plot(n1,v3);title('滑块速度运动线图');xlabel('曲柄转角\theta_1/\circ');ylabel('滑块速度/m\cdots^{-1}');grid onsubplot(2,3,6)plot(n1,a3);title('滑块加速度运动线图');xlabel('曲柄转角\theta_1/\circ');ylabel('滑块加速度/m\cdots^{-2}');grid on2、子程序function[theta2,s3,omega2,v3,alpha2,a3]=slider_crank(theta1,omega1,alpha1,l1,l2,e);%计算连杆2的角位移和滑块3的线位移s3=l1*cos(theta1)+l2*cos(theta2);theta2=asin((e-l1*sin(theta1))/l2);%计算连杆2的角速度和滑块3的线速度A=[l2*sin(theta2),1;-l2*cos(theta2),0];B=[-l1*sin(theta1);l1*cos(theta1)];omega=A\(omega1*B);omega2=omega(1);v3=omega(2);%计算连杆2的角加速度和滑块3的线加速度At=[omega2*l2*cos(theta2),0;omega2*l2*sin(theta2),0];Bt=[-omega1*l1*cos(theta1);-omega1*l1*sin(theta1)];alpha=A\(-At*omega+alpha1*B+omega1*Bt);alpha2=alpha(1);a3=alpha(2);四、程序运行结果及分析图2 运动规律曲线图从仿真曲线可以看出,当曲柄以w1=10rad/s匀速转动时,连杆的转角位移变化范围大约在-20~20度之间,在90°或270°有极值,呈反正弦变化趋势;连杆的角速度变化范围大约在-3.3~3.3rad/s,在0°或180°有极值,成反余弦变化趋势;连杆角加速度变化范围大约在-35~35rad/s2,在90°或270°有极值,呈正弦变化趋势。
基于ANSYS12.1的曲柄滑块机构动力学分析

Rii y a c 允 许 为刚体 零件定 义质 点 ,质 点 gdD n mi s
位 置可 以按地面 坐标 系位 置进行 定义 ,也可 以通过 选 择几 何体 定义 ,默认 的质 点位置 位于所 选几何 体 的 中
心。 1 4 定 义 连 接 .
D n mi 模 块 , ya c s 能够在 ANS YS软件 中直接对 刚体 进 行 动 力学分 析 , 免 了 A YS与 AD 避 NS AMS接 口的繁 琐 。它集成 于 Wo k e c r b n h环 境下 , 对所 建立 的模 型利
用 完整 的运 动副类 型 ( 固定 、 动 、 面 滑动和转 动 、 转 柱 平
1 1 定 义 工 程 数 据 .
Rii y a c 利 用完 整 的运动 副类 型 ( gdD n mi s 固定 、 转 动 、 面 滑动和转 动 、 动 、 柱 平 滑槽 、 向连接 、 万 球铰 、 面 平
运动、 自定义 等) 和弹 簧来 建立零 件之 间的连 接 ,提 供
精 确 的定 位 方 法 以保 证 零 件 间 的定 位 。 当模 型 是 从 C D 等软件 中导 入时 , A 零件 之 间的连 接或约 束并没 有 被 同时输 入 ,但 是 A YS可 以 自动探测 运动 副类 型 NS 从 而为零 件 自动 建立 连接 ,也 可以选择 手动建 立连 接 关系。 区别 于 A YS其 他处 理模 块 , ii D n mi NS R gd y a c s 分 析不 需要划 分 网格 。
1 5 建立分析 设置 .
针 对不 同 的分 析模 块 需要 定 义 不 同 的性 能 参 数 ,
曲柄导杆滑块等机构测试仿真实验报告

曲柄导杆滑块等机构测试仿真实验报告一、实验目的本次实验的目的是对曲柄导杆滑块等机构进行测试仿真,通过实验数据分析,掌握该机构的运动规律和特性,为机构设计和优化提供参考。
二、实验原理曲柄导杆滑块等机构是一种常见的机械传动装置,其主要由曲柄、连杆、导杆和滑块等部件组成。
在运动过程中,曲柄带动连杆运动,使导杆产生往复直线运动,从而驱动滑块完成工作。
三、实验器材本次实验所使用的器材包括:计算机、SolidWorks软件、Matlab软件。
四、实验步骤1.建立曲柄导杆滑块等机构三维模型利用SolidWorks软件建立曲柄导杆滑块等机构三维模型,并进行参数设置和装配。
2.进行运动分析利用SolidWorks Motion模块对该机构进行运动分析,并得出相关数据。
3.进行力学分析利用Matlab软件对该机构进行力学分析,并得出相关数据。
4.比较分析结果将两种分析方法得到的数据进行比较和分析,掌握该机构的运动规律和特性。
五、实验结果1.运动分析结果通过SolidWorks Motion模块对该机构进行运动分析,得到以下数据:曲柄转角:0~360度连杆长度:50mm导杆长度:100mm滑块位置:-50~50mm2.力学分析结果通过Matlab软件对该机构进行力学分析,得到以下数据:曲柄转角:0~360度连杆角度:0~180度导杆速度:0~10m/s滑块加速度:-10~10m/s^23.比较分析结果通过比较两种分析方法得到的数据,可以发现该机构的运动规律和特性与曲柄转角有关,当曲柄转角为180度时,导杆速度最大;当曲柄转角为90或270度时,滑块加速度最大。
此外,连杆角度与导杆速度呈正比关系。
六、实验结论通过本次实验可以得出以下结论:1.曲柄导杆滑块等机构的运动规律和特性与曲柄转角、连杆角度等参数有关。
2.该机构在不同工况下具有不同的性能表现,需要根据具体情况进行优化设计。
3.利用SolidWorks Motion模块和Matlab软件可以对该机构进行运动分析和力学分析,为机构设计和优化提供参考。
- 1、下载文档前请自行甄别文档内容的完整性,平台不提供额外的编辑、内容补充、找答案等附加服务。
- 2、"仅部分预览"的文档,不可在线预览部分如存在完整性等问题,可反馈申请退款(可完整预览的文档不适用该条件!)。
- 3、如文档侵犯您的权益,请联系客服反馈,我们会尽快为您处理(人工客服工作时间:9:00-18:30)。
第15例 连杆机构运动分析实例—曲柄滑块机构[本例提示] 介绍了利用ANSYS 对连杆机构进行运动学分析的方法、步骤和过程,并使用解析解对有限元分析结果进行了验证。
着重介绍了曲柄滑块机构模型的创建以及约束的施加方法,介绍了三维铰链单元COMBIN7的使用方法。
15.1 概述本分析仍然属于瞬态动力学分析,分析过程与普通的瞬态动力学分析基本相同。
其关键在于三维铰链单元COMBIN7的创建,现在此简单介绍。
三维铰链COMBIN7单元属于三维单元,有5个节点,分别是活跃节点I 和J 、用以定义铰链轴的节点K 、控制节点L 和M (图15-1)。
活跃节点I 和J 应该位置重合,并且分属于LINK A 和B ,LINK A 和B 是一个单元或单元集合。
如果节点K 没有定义,则铰链轴为全球笛卡尔坐标系的z 轴。
三维铰链COMBIN7单元的进一步内容请参阅ANSYS 帮助文档。
另外,本分析必须将大变形选项打开。
15.2 问题描述及解析解图15-2所示为一曲柄滑块机构,曲柄长度R =250mm 、连杆长度L =620 mm 、偏距e =200 mm ,曲柄为原动件,转速为n 1=30 r/min ,求滑块3的位移s 3、速度v 3、加速度a 3随时间变化情况。
根据机械原理的知识[5][6],该问题的解析解十分复图 15-1 三维铰链单元COMBIN7图 15-2 曲柄滑块机构杂,使用不太方便。
本例用图解法解决问题,由于过程比较繁琐,而且只是为了验证有限元解的正确性,所以,关于滑块3的位移s 3、速度v 3、加速度a 3随时间t 变化情况的图形没有必要给出。
在这里只求解了以下数据:滑块的行程H =535.41 mm 。
机构的极位夹角为θ=19.43°,于是机构的行程速比系数242.1180180=-︒+︒=θθK 。
由于机构一个工作循环周期为2601==n T s ,所以机构工作行程经历的时间108.111=+=T K K T s ,空回行程经历的时间892.012=-=T T T s 。
15.3 分析步骤15.3.1 改变工作名拾取菜单Utility Menu →File →Change Jobname 。
弹出图15-3所示的对话框,在“[/FILNAM]” 文本框中输入EXAMPLE15,单击“Ok ” 按钮。
15.3.2 定义参量拾取菜单Utility Menu →Parameters →Scalar Parameters 。
弹出图15-4所示的对话框,在“Selection ” 文本框中输入PI=3.1415926, 单击“Accept ” 按钮;再在“Selection ” 文本图 15-3 改变工作名对话框图 15-3 改变工作名对话框图 15-4 参量对话框 图 15-5 单元类型对话框框中依次输入R=0.25(曲柄长度)、L=0.62(连杆长度)、E=0.2(偏距)、OMGA1=30(曲柄转速)、T=60/OMGA1(曲柄转动一周所需时间,单位:s )、FI0=ASIN(E/(R+L))、AX=0、AY=0(铰链A 坐标)、BX=R*COS(FI0)、BY=-R*SIN(FI0) (铰链B 坐标)、CX=(R+L)*COS(FI0)、CY=-E (铰链C 坐标),同时单击“Accept ” 按钮;最后,单击图15-4所示的对话框的“Close ”按钮。
15.3.3 创建单元类型拾取菜单Main Menu →Preprocessor →Element Type →Add/Edit/Delete 。
弹出图15-5所示的对话框,单击“Add ”按钮;弹出图15-6所示的对话框,在左侧列表中选“Combination ”,在右侧列表中选“Revolute joint 7”, 单击“Apply ” 按钮;再在左侧列表中选“Structural Beam ”在右侧列表中选“3D elastic 4”, 单击“Ok ” 按钮;单击图15-5所示的对话框的“Close ”按钮。
15.3.4 定义材料特性拾取菜单Main Menu →Preprocessor →Material Props →Material Models 。
弹出的图15-7所示图15-6 单元类型库对话框图 15-7 材料模型对话框的对话框,在右侧列表中依次双击“Structural ”、“Linear ”、“Elastic ”、“Isotropic ”,弹出图15-8所示的对话框,在“EX ”文本框中输入2e11(弹性模量),在“PRXY ” 文本框中输入0.3(泊松比),单击“Ok ” 按钮;再双击右侧列表中“Structural ”下“Density ”,弹出图15-9所示的对话框,在“DENS ”文本框中输入1e-14(密度。
近似为0,即不考虑各杆的惯性力),单击“Ok ” 按钮。
然后关闭图15-7所示的对话框。
15.3.5 定义实常数拾取菜单Main Menu →Preprocessor →Real Constants →Add/Edit/Delete 。
弹出图15-10所示的对话框,单击“Add ”按钮,弹出图15-11所示的对话框,在列表中选择“Type 1 COMBIN7”,单击“Ok ” 按钮,弹出图15-12所示的对话框(注:图中对该对话框作了删节),在“K1”、“K2”、“K3”、“K4”文本框中分别输入1E9、1E3、1E3、0,单击“Ok ” 按钮;返回到图图 15-8材料特性对话框 图 15-9 定义密度对话框图 15-10 定义实常数对话 图 15-11 选择单元类型对话15-10所示的对话框, 再次单击“Add ”按钮,弹出图15-11所示的对话框,在列表中选择“Type 2 BEAM4”,单击“Ok ”按钮,弹出图15-13所示的对话框(注:图中对该对话框作了删节),在“AREA ”、“IZZ ”、“IYY ”、“TKZ ”、“TKY ”文本框中分别输入4E-4、1.3333E-8、1.3333E-8、0.02、0.02,单击“Ok ” 按钮;返回到图15-10所示的对话框,单击“Close ”按钮。
15.3.6 创建节点拾取菜单Main Menu →Preprocessor →Modeling →Create →Nodes →In Active CS 。
弹出图15-14所示的对话框,在“NODE ”文本框中输入1,在“X,Y,Z ”文本框中分别输入AX,AY ,0,单击“Apply ” 按钮;在“NODE ”文本框中输入2,在“X,Y ,Z ”文本框中分别输入BX,BY ,0,单击“Apply ” 按钮;在“NODE ”文本框中输入3,在“X,Y ,Z ”文本框中分别输入BX,BY ,0,单击“Apply ” 按钮;在“NODE ”文本框中输入4,在“X,Y ,Z ”文本框中分别输入CX,CY ,0,单击“Apply ” 按钮;在“NODE ”文本框中输入5,在“X,Y,Z ”文本框中分别输入BX,BY ,-1,单击“Ok ” 按钮。
15.3.7 指定单元属性拾取菜单Main Menu →Preprocessor →Modeling →Create →Elements →Elem Attributes 。
弹出图 15-12设置实常数对话框(1) 图 15-13 设置实常数对话框(2)图 15-14 创建节点的对话框图15-15所示的对话框,选择下拉列表框“TYPE ”为“1 COMBIN7”,选择下拉列表框“MA T ”为“1”,选择下拉列表框“REAL ”为“1”,单击“Ok ”按钮。
15.3.8 创建铰链单元拾取菜单Main Menu →Preprocessor →Modeling →Create →Elements →Auto Numbered →Thru Nodes 。
弹出拾取窗口,在拾取窗口的文本框中输入2,3,5,单击“Ok ” 按钮,于是在节点2和3处(即B 点)创建了一个铰链单元。
15.3.9 指定单元属性拾取菜单Main Menu →Preprocessor →Modeling →Create →Elements →Elem Attributes 。
弹出图15-15 单元属性对话框图 15-16 瞬态分析选项对话框图15-15所示的对话框,选择下拉列表框“TYPE”为“2 BEAM 4”,选择下拉列表框“MA T”为“1”,选择下拉列表框“REAL”为“2”,单击“Ok”按钮。
15.3.10 创建梁单元用来模拟各个杆,拾取菜单Main Menu→Preprocessor→Modeling→Create→Elements→Auto Numbered→Thru Nodes。
弹出拾取窗口,在拾取窗口的文本框中输入1,2,单击“Apply”按钮;再在拾取窗口的文本框中输入3,4,单击“Ok”按钮。
于是创建了2个梁单元,2个梁单元由B点处铰链单元连接。
15.3.11 指定分析类型拾取菜单Main Menu→Solution→Analysis Type→New Analysis 。
在弹出的“New analysis”对话框中,选择“Type of Analysis”为“Transient”,单击“Ok”按钮,在随后弹出的“Transient Analysis”对话框中,单击“Ok”按钮。
15.3.12 打开大变形选项拾取菜单Main Menu→Solution→Analysis Type→Analysis Options。
弹出图15-16所示的对话框,将“NLGEOM”打开,单击“Ok”按钮。
15.3.13 确定载荷步时间和时间步长拾取菜单Main Menu→Solution→Load Step Opts→Time/Frequenc→Time - Time Step。
弹出图15-17 确定载荷步时间和时间步长对话框图15-17所示的对话框,在 “TIME ”文本框中输入T ,在“DELTIM Time Step size ”文本框中输入T/70,选择“KBC ”为“Ramped ”,单击“Ok ” 按钮。
15.3.14 确定数据库和结果文件中包含的内容拾取菜单Main Menu →Solution →Load Step Opts →Output Ctrls →DB/Results File 。
弹出图15-18所示的对话框,选择下拉列表框“Item ”为“All Items ”,选中“Every substep ”, 单击“Ok ” 按钮。
15.3.15 设定非线性分析的收敛值拾取菜单Main Menu →Solution →Load Step Opts →Nonlinear →Convergence Crit 。