深孔加工工艺探讨
船舶机械零件的深孔工艺及其改进方法

船舶机械零件的深孔工艺及其改进方法船舶机械零件的深孔工艺是船舶制造中的重要工艺之一。
深孔加工是指孔径大于3倍长度的孔。
深孔工艺在船舶制造中应用广泛,深孔零件主要包括船用柴油机气缸体、船用主轴承壳、船用齿轮箱壳体等。
深孔工艺的加工难度大,加工精度要求高,所以深孔加工一直以来都备受制造技术工作者的重视。
本文将围绕船舶机械零件的深孔工艺及其改进方法进行深入探讨。
一、船舶机械零件深孔工艺深孔加工主要包括钻削、铰削、镗削、磨削、滚压等几种方法。
由于船舶机械零件的深孔工艺要求精度高,加工难度大,所以一般采用数控加工中心、车床等设备进行深孔加工。
深孔加工时,要根据零件的材料、尺寸以及加工要求,选择合适的切削用量、切削速度等参数,进行合理而有效的深孔工艺。
由于船舶机械零件的深孔零部件一般精度要求高,所以在深孔工艺中也需要运用一些特殊的工艺技术,如采用自动进刀、退刀系统,选择适当的润滑冷却剂等。
在实际船舶机械零件的深孔工艺中,存在一些问题,主要包括以下几个方面:1. 加工难度大:深孔加工一般要求切削刀具要足够刚性,并且要有很好的冷却润滑条件,而且还要有适当的进刀、退刀系统。
这些条件对加工设备和技术都提出了较高的要求。
2. 长时间加工:由于深孔工艺的特殊性,一般需要较长时间才能完成一件零件的深孔加工,所以一般都采用自动化生产线,以提高加工效率。
3. 加工精度要求高:船舶机械零件的深孔工艺一般都要求加工精度很高,所以加工过程中不能出现偏差、振动等情况。
4. 钻屑排除难度大:由于深孔加工的特殊性,加工过程中会形成大量的钻削屑,其排除是一个难点。
以上几点问题,制约着船舶机械零件的深孔工艺的进一步提高。
为了解决船舶机械零件深孔工艺的上述问题,提高深孔加工的效率和质量,可以运用以下一些改进方法:1. 刀具改进:针对船舶机械零件的深孔工艺要求,钻削刀具可以选择加工性好、刚性高的刀具,如合金钢、硬质合金等。
2. 流体力学辅助:可以采用流体力学辅助削削技术,通过外加压力,改善切屑的排除,并降低刀具的运动阻力。
浅析机械加工过程中的深孔加工方法

浅析机械加工过程中的深孔加工方法摘要:现阶段我国科学技术发展水平的提升,对机械加工制造产生了积极影响,逐渐扩大了其产业规模。
实践中为了使机械加工效果更加显著,增加深孔加工中的技术含量,则需要考虑与之相关的加工技术使用,落实好具体的研究工作,确保深孔加工状况良好性,为机械加工行业的可持续发展提供专业支持。
基于此,本文将对机械加工作用下的深孔加工技术进行系统阐述。
关键词:机械加工;深孔加工;技术1、深孔处理技术的技术特征1.1深孔加工技术很困难首先,大多数深孔加工是在半封闭或完全封闭的环境中进行的,因此无法直接观察到诸如加工,切削和切削之类的操作人员。
因为孔的半径与深度之间的比率较大,所以它会排干金属屑并使孔难以堵塞。
毕竟,如果钻头太长,则会出现严重降低钻头刚性的问题。
由于孔偏移或抖动等问题,难以有效地保证深孔加工的精度,并且由于孔加工的散热问题,在封闭环境下,由于孔的温度升高,钻头可能会磨损。
1.2锻炼方法本身很特殊在深孔加工的整个过程中,可以通过多种方式来操作工件和刀具,其中工件旋转并且刀具同时进给。
固定工件并同时进给刀具。
选择多种运动方法,例如定向进给,是使用深孔加工技术的主要挑战之一。
1.3深孔加工中的排屑问题深孔加工中的排屑问题是要重点解决的问题之一,排屑方法主要分为两种。
首先是外部排屑。
将冷却液倒入岩心钻杆中以清除切屑。
切割区域已清洁。
第二个是去除内部切屑,将其倒入钻杆的孔和外壁中以从切削区域去除切屑。
在实际的加工过程中,内部排屑处理方法通常是优选的,因为该方法不会引起孔壁的二次摩擦,并且钻杆的高刚度不会影响孔的表面质量。
2、深孔加工中冷却润滑液的作用深孔加工中,冷却润滑液不仅要快速去除钻孔过程中产生的热量并润滑刀具和工件,减小两者间的摩擦,更主要的是要用具有一定压力和流速的冷却液来冲走切屑,以达到排屑的目的。
切屑容易堵塞排屑通道,影响刀具正常使用。
如果堵在钻头排屑孔位置,还会挤压刀片,造成崩刃影响切削加工。
深孔加工技术分析

OCCUPATION2011 7182深孔加工技术分析文/马永波本文分析了车工单件小批量日常生产中偶尔会遇到的精度要求较高的深孔、细长孔的加工技术难点,并设计了行之有效的简易浮动铰刀,对小型加工企业和个体加工户有较重要的推广意义。
一、深孔、细长孔加工方法:打中心孔—钻孔—扩孔—铰孔 深孔是指孔深与直径之比L/d ≥5的孔。
一些中小型加工企业及个体加工户一般不具备专用的设备和特制辅助工装,因此只能采用简易的工装对深细长孔进行加工。
应采取多次扩孔加充分浇注冷却液的方法减少粗加工留下的加工误差,以提高后续加工精度。
二、钻头的刃磨要求齿轮定位套的加工由于尺寸精度要求较高,所以钻头的刃磨非常重要,因此要作特殊处理,即改进钻头的几何参数。
一是在两主切削刃上修磨出第二锋角,一般不超过75°,并在外缘刀尖角处研磨出两边R 0.2~0.5mm的圆弧过度刃,粗糙度达Ra0.4μm以下,且两个过度刃相互对称,高度一致,以增大刀尖外缘处的强度和耐磨度,改善散热条件,减小孔壁的残留面积高度。
二是将前端棱边磨窄,只保留0.1~0.2mm的宽度,修磨长度为4~5mm,以减小棱边与孔壁的摩擦。
三是修磨副切削刃、前刀面和后刀面,要求用320#以上油石研磨,最好400#以上,研磨各部位粗糙度达到Ra0.4~Ra0.2μm。
三、铰孔及注意事项 1.浮动铰刀的设计 当孔的尺寸精度、形状精度要求比较高,表面粗糙度要求又比较小时,往往还要再安排一次手铰加工。
如定位孔的圆柱度要求很高,为避免常规机用铰孔容易铰出椭圆孔的现象,可预先设计具有自动定心功能的浮动铰刀。
选用12H7的直柄机用铰刀,为让铰刀起到浮动的作用,再设计一辅助夹具,辅助夹具的安装孔要比铰刀的夹持柄部大2~3mm,然后将铰刀套在辅助夹具的安装孔上,用4~5mm钻头将安装孔连铰刀柄一起钻出一个定位孔,然后用圆柱销将铰刀安装的辅助夹具上即可得到简易的浮动铰刀。
为提高的铰刀铰削时的刚性和夹紧力,浮动铰刀的辅助装置最好采用莫氏5号的钻夹头装夹。
铝合金深孔加工的加工技术研究
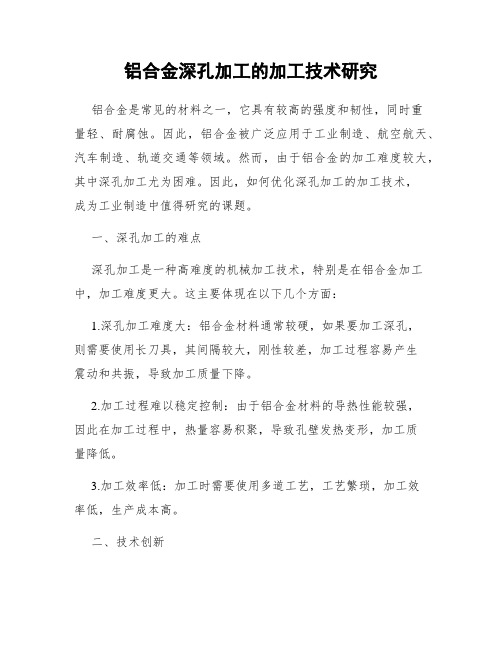
铝合金深孔加工的加工技术研究铝合金是常见的材料之一,它具有较高的强度和韧性,同时重量轻、耐腐蚀。
因此,铝合金被广泛应用于工业制造、航空航天、汽车制造、轨道交通等领域。
然而,由于铝合金的加工难度较大,其中深孔加工尤为困难。
因此,如何优化深孔加工的加工技术,成为工业制造中值得研究的课题。
一、深孔加工的难点深孔加工是一种高难度的机械加工技术,特别是在铝合金加工中,加工难度更大。
这主要体现在以下几个方面:1.深孔加工难度大:铝合金材料通常较硬,如果要加工深孔,则需要使用长刀具,其间隔较大,刚性较差,加工过程容易产生震动和共振,导致加工质量下降。
2.加工过程难以稳定控制:由于铝合金材料的导热性能较强,因此在加工过程中,热量容易积聚,导致孔壁发热变形,加工质量降低。
3.加工效率低:加工时需要使用多道工艺,工艺繁琐,加工效率低,生产成本高。
二、技术创新针对铝合金深孔加工的难点,需要技术创新,以提高加工效率和加工质量。
1.刀具研发:针对铝合金材料的硬度和韧性,研发出具有适当刚性和稳定性的合金刀具,提高了加工效率和加工质量。
2.冷却液研发:针对铝合金材料导热性能强的特点,开发出高效的冷却液,显著提高了加工的稳定性。
同时,冷却液可以降低加工温度,减少材料变形,提高了加工精度。
3.数控技术应用:数控技术可以实现自动化加工,减少了工艺繁琐的环节,也降低了人工干预的机会,提高了加工效率和加工质量。
4.高速切削技术:高速切削技术可以减少加工过程中的震动和共振,提高了加工精度和表面质量。
三、工艺控制对于铝合金深孔加工,需要严格控制加工过程中的各项参数,以确保加工质量。
1.深孔加工过程中需要保证机床稳定性,采用重负载的机床和刚性较强的刀具。
2.精确控制加工速度,以保证切削力和热量的控制。
3.精确控制加工深度,以避免切削过深带来的损伤和热量过多的问题。
4.合理选择冷却液,确保其能够有效地冷却刀具并降低材料的加工温度。
四、结论总之,铝合金深孔加工是一项高难度的机械加工技术,需要技术创新和工艺控制。
基于机械加工的深孔加工技术探析
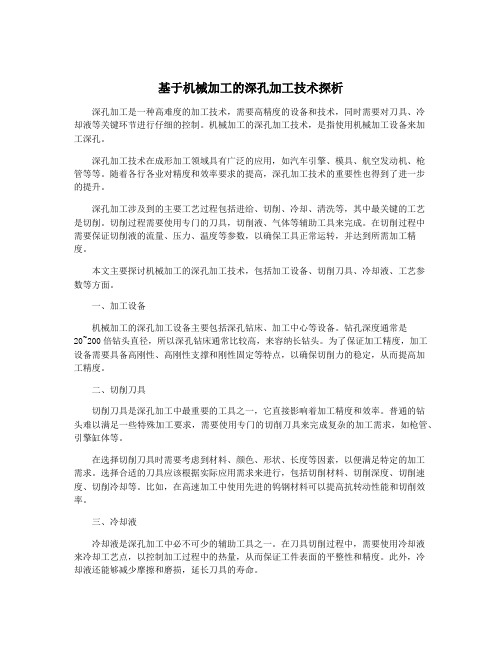
基于机械加工的深孔加工技术探析深孔加工是一种高难度的加工技术,需要高精度的设备和技术,同时需要对刀具、冷却液等关键环节进行仔细的控制。
机械加工的深孔加工技术,是指使用机械加工设备来加工深孔。
深孔加工技术在成形加工领域具有广泛的应用,如汽车引擎、模具、航空发动机、枪管等等。
随着各行各业对精度和效率要求的提高,深孔加工技术的重要性也得到了进一步的提升。
深孔加工涉及到的主要工艺过程包括进给、切削、冷却、清洗等,其中最关键的工艺是切削。
切削过程需要使用专门的刀具,切削液、气体等辅助工具来完成。
在切削过程中需要保证切削液的流量、压力、温度等参数,以确保工具正常运转,并达到所需加工精度。
本文主要探讨机械加工的深孔加工技术,包括加工设备、切削刀具、冷却液、工艺参数等方面。
一、加工设备机械加工的深孔加工设备主要包括深孔钻床、加工中心等设备。
钻孔深度通常是20~200倍钻头直径,所以深孔钻床通常比较高,来容纳长钻头。
为了保证加工精度,加工设备需要具备高刚性、高刚性支撑和刚性固定等特点,以确保切削力的稳定,从而提高加工精度。
二、切削刀具切削刀具是深孔加工中最重要的工具之一,它直接影响着加工精度和效率。
普通的钻头难以满足一些特殊加工要求,需要使用专门的切削刀具来完成复杂的加工需求,如枪管、引擎缸体等。
在选择切削刀具时需要考虑到材料、颜色、形状、长度等因素,以便满足特定的加工需求。
选择合适的刀具应该根据实际应用需求来进行,包括切削材料、切削深度、切削速度、切削冷却等。
比如,在高速加工中使用先进的钨钢材料可以提高抗转动性能和切削效率。
三、冷却液冷却液是深孔加工中必不可少的辅助工具之一。
在刀具切削过程中,需要使用冷却液来冷却工艺点,以控制加工过程中的热量,从而保证工件表面的平整性和精度。
此外,冷却液还能够减少摩擦和磨损,延长刀具的寿命。
在选择冷却液时需要考虑到加工材料、刀具材料、加工深度等因素。
一般来说,深孔加工需要使用专门的冷却液,可以根据加工工艺的不同而调整冷却液的化學成分和流量,以达到最佳的效果。
机械加工深孔加工技术研究论文

机械加工深孔加工技术研究论文机械加工深孔加工技术研究论文一、研究背景深孔加工是目前机械加工领域的一个热门技术,适用于制作特制的精密孔和精密轴。
特别是在一些外国企业的高精密加工领域和国防军工等领域,深孔加工都被广泛应用。
深孔加工在航天、军工、锅炉和化工等高端制造领域有着重要的地位。
然而,由于深孔加工的特殊性,其难度和风险相对较高。
长时间的孔加工过程和复杂的孔形结构都会给孔加工带来较大的不确定性和变异性等风险。
因此,在深孔加工领域,深入研究其加工技术和优化方法,提高深孔加工的加工质量和效率,对于提升我国制造业的技术水平和产品质量有着重要的意义。
二、研究内容和方法本论文通过对深孔加工的研究和实际应用,系统地分析了深孔加工技术的相关原理、特点和应用方法。
并在此基础上,提出了一种优化深孔加工的方法。
该方法主要涉及到以下几个方面:1. 工艺参数优化,在保证加工质量、安全性和效率的基础上,寻求合适的加工参数组合。
这里所指的工艺参数包括加工切削速度、进给速度、切削深度和加工精度等。
2. 加工设备优化,根据加工孔的形状和材料特性,合理选择深孔加工机床和刀具。
对于不同的孔型,采用不同类型的刀具和工艺流程,以保证加工的效率和质量。
3. 加工过程监控,在加工过程中通过监控切削力、温度和位移等参数,实时反馈并控制加工过程。
通过数据分析和处理,优化加工过程控制,提高加工质量。
4. 刀具润滑改进,在切削过程中应选用合适的刀具润滑方式,以降低切削力和工具磨损程度,提高加工效率和质量。
本论文的实验内容主要包括了深孔加工试样制作、加工参数优化和加工质量评估等。
通过分析加工过程中的各项参数,对加工效率和质量进行了比较和分析。
三、研究结论通过本研究的实验和分析,可以得出以下结论:1. 在深孔加工中,加工参数的选择和优化是关键。
不同的参数组合会直接影响加工效率和加工质量。
因此,应选用适合的参数组合以保证加工效果。
2. 加工设备对于深孔加工的影响较大。
某管型零件深孔加工工艺分析
关键词:拉刀;管型零件;工装;紫铜;深孔引言某管型零件外形为Φ22mm×275mm圆管,其内孔直径为Φ17.9mm±0.05mm、要求加工后内壁光洁度1.6,零件材料为紫铜。
由于紫铜材料塑性较好、强度较低,加工时极易变形,且圆孔长度大,光洁度和尺寸要求较为严格,因此Φ17.9mm圆孔加工为加工流程中最困难的环节。
在进行加工前,首先对比各种深孔加工方式。
主流的深孔加工方式有拉削、镗孔、慢走丝等。
镗孔的加工效率较高且成本低,但由于此零件长径比较高,镗刀刀杆在加工时可能出现弯曲,影响加工精度;慢走丝的精度较高,可满足加工要求,但成本高且加工效率较低。
在对比各种深孔加工方法的基础上,考虑到拉削加工方式具有加工精度高、表面光洁度易保证、生产率高、适于大批量生产等优点,且圆孔拉刀结构较为简单,易于生产,因此尝试使用拉削方式加工内孔。
1拉刀的工艺参数选择根据实际情况,由于零件内孔较小,拉刀直径受到限制,考虑到如果仅采用一把拉刀进行拉削,切削力在拉刀危险截面形成的应力将会超过拉刀危险截面许用应力,遂决定采用多把直径依次增大的圆孔拉刀从小到大依次拉削圆孔至尺寸要求的方案,即先使用线切割粗加工圆孔至Φ17.8mm,再使用多把圆孔拉刀依次拉削圆孔至尺寸Φ17.9mm。
1.1拉刀材料的选择刀具材料主要按被加工材料性质以及切削参数确定,所加工材料为紫铜,属于很容易切削的材料;拉削的切削速度、切削深度都比较低,故决定选取相对容易加工的淬火T8工具钢作为刀具材料。
1.2拉刀齿升量选择齿升量的大小会影响加工表面质量、拉削力、拉刀耐用度、拉削效率。
根据实际情况,由于被加工内孔长度较长、切屑无法在加工时排出,且被加工材料刚度较差,不能承受较大的拉削力,故不宜选择较大的齿升量,根据实验,选取单边齿升量为0.005mm。
1.3拉刀的结构设计已确定切削余量为0.1mm,单边齿升量0.005mm,故需要至少10个切削齿才能完成切削。
浅谈深孔加工技术
技术与应用A PPLICATION157OCCUPATION2014 11摘 要:本文探讨了深孔加工的特点、关键技术、加工类型、刀具及结构等问题。
关键词:深孔加工 加工特点 关键技术 加工方法浅谈深孔加工技术文/杨营营所谓深孔,是指孔深与孔径之比大于5的孔。
深孔又分为一般深孔(L /d >5~20)、中等深孔(L /d >20~30)、超深孔(L /d >30~100)三类。
不同类型的深孔,其加工方法也不相同。
一、深孔加工的特点和关键技术1.深孔件加工的特点一是深孔加工时,孔轴线容易歪斜,钻削中钻头容易引偏。
二是刀杆受内孔限制,一般细而长,刚性差,强度低,车削时容易产生振动和“让刀”现象,使零件易产生波纹、锥度等缺陷。
三是钻孔或扩孔时切屑不易排出,冷却润滑液输入困难。
四是加工时难以观察孔的加工情况,加工质量不易控制。
2.深孔加工的关键技术深孔加工的关键技术是深孔刀具几何形状的确定和切削时的冷却、排屑问题。
在加工中可采用以下措施来保证加工质量:一是粗精加工分阶段进行,二是合理选择加工刀具,三是采用导向和辅助支承,四是配置冷却液输入装置。
二、深孔加工类型一是按其所用刀具分类,可分为实心钻孔法、镗孔法、套料钻孔法。
二是按运动形式分类,可分为工件旋转,刀具做进给运动;工件不动,刀具旋转又做进给运动;工件旋转,刀具也做反向旋转又做进给运动;工件做旋转运动与进给运动,刀具不动,这种形式采用不多。
三是按排屑方法分类,可分为外排屑、内排屑。
三、深孔加工刀具及其结构1.扁钻该刀具结构简单,容易制造,在钻削加工时冷却液由钻杆内部注入孔中,切屑从零件孔内排出,适用于精度和表面粗糙度要求不高的较短深孔。
图1 简易扁钻1-钻头 2-钻杆 3、4-紧固螺钉2.单刃外排屑小深孔钻该深孔钻由切削部分和钻杆焊接而成,切削部分用W 18Cr 4V 制造或硬质合金刀头镶制;钻杆为35#~45#钢无缝钢管,上压120°V 形槽用以排屑,中空可通过切削液,从自切削部分腰圆孔处进入切屑区域。
机械加工中深孔加工技术的研究
机械加工中深孔加工技术的研究摘要:在机械工程行业壮大发展的背景下,机械化工艺水平,深加工技术在现实生产活动中得到了广泛应用,该项技术虽然能创造出较好的效益,但是客观上讲技术应用中还滞留着一些问题。
本文简单分析了深孔加工技术应用的重点与难点,包括技术操作难度较高、钻孔操作有应局限性、碎屑外排环节有问题等,简单分析以上状况的成因,以促进深加工技术有效应用为目标,总结技术要点及应用策略,希望能给同行实践过程带来些许帮助。
关键词:机械化加工;深加工;难点分析;技术应用引言机械加工制造是我国的传统行业之一,其直接关系着国民经济的整体发展水平。
机械化加工生产中可供选择的技术方法有很多,深加工就是其一,其在促进我国机械加工水平全面提升方面表现出良好效能。
深孔通常是孔长度和直径比大于5~10的孔。
通常而言,在机械化加工生产中,深孔的实际加工数量在总量内占比约50%。
综合以上数据,能够认识到做好深孔加工工作的必要性。
为了能全面提升深孔加工效率与质量,应积极研发适宜且高效化的深孔加工技术,并结合实际情况持续完善技术应用过程,彰显新技术的优势,促进我国机械行业获得更大的发展进步。
1深孔加工技术的重点和难点1.1技术应用难度较高主要体现在如下几个方面[1]:一是基本上是孔径小,孔深大的条件下进行生产,受限于设备或刀具因素的制约,加工时出口位置容易产生偏差。
二是由于孔深大,切削过程中切屑不能及时有效地排出孔,以致加工时容易发生金属屑堵塞造成孔壁局部的不良状况,甚至刀具断裂的情况。
三是配备的钻头及定位夹具均会对深孔加工技术应用效果产生较大的影响。
长时间进行深孔加工作业会导致定位导向件发生不同程度的磨损问题,以致深孔半径、深度等指标和设计要求之间出现很大的出入,不仅影响加工的精准度,还弱化深孔加工技术的价值。
四是造成钻头及加工夹具发生磨损情况的因素不唯一,而加工部位的冷却效果差、温度较高等被认定是引起磨损问题的两大主因。
1.2深孔钻加工有一定局限性钻孔作业过程中,加工零件的材质可切削性,被加工的孔深与孔径比例也局限于加工条件,钻孔的刀具刚性和排屑效果也会限制深孔的加工质量。
浅谈普通车床上深孔加工技术
主 切削 刃 上修 磨 出第二 锋 角 , 般 不超过 7 。 , 在 外缘 刀尖 角处 一 5 并 研 磨 出两边 R .~O 02 . 圆弧过 度 刃 , 糙度 达 R0 5的 粗 ,. 4以下 , 两个 且 过 度 刃相 互 对 称 , 度一 致 , 高 以增 大 刀尖 外 缘 处 的 强度 和 耐 磨度 , 改 善散 热 条件 , 少孑 壁 的残 留 面积 高度 。二是 将 前端 棱边 磨 窄 , 减 L
Jun I i t 堡 sT a ha。
浅谈普通 车床 上深 孔加工技术
徐 灵 敏
( 广东省中 山市 中等 专业学校 , 东 中山 5 80 ) 广 2 4 3
摘
要: 通过 对钻头刃 磨的特殊 处理 : 两主 切削刃 上修磨 出第 二锋角 , 端棱边磨 窄, 在 前 修磨副切 削刃和采用 浮动铰刀 的工装夹具 , 选择合
排 屑不 易 , 常会 产 生 直 径变 大 , 经 出现 锥 形 等现 象 , 从而 达 不 到 加
对 图 1 轮定 位 套 的加 工 , 齿 由于 尺 寸精 度 要求 较 高 , 以钻头 所
的刃磨 非 常重 要 , 尤其 是 最后 一 次扩 孔 钻头 的 刃磨 , 头 磨得 好不 钻
工质 量 的要 求 。因此 , 没有 深 孔加 工 的 专用 设 备下 , 普通 设 备 在 用
功 能 的浮 动铰 刀 , 图 3 示 。 用 1/ 如 所 选 2/ - 7的直 柄机 用 铰刀 , 让 为 铰 刀起 到 浮动 的作 用 , 设 计一 辅助 夹 具 , 再 辅助 夹 具 的安装 孔 要 比
4# 5 图号 O l 检验
- 1、下载文档前请自行甄别文档内容的完整性,平台不提供额外的编辑、内容补充、找答案等附加服务。
- 2、"仅部分预览"的文档,不可在线预览部分如存在完整性等问题,可反馈申请退款(可完整预览的文档不适用该条件!)。
- 3、如文档侵犯您的权益,请联系客服反馈,我们会尽快为您处理(人工客服工作时间:9:00-18:30)。
深孔加工工艺探讨
摘要:深孔加工一直是孔系加工中的难点。
深孔加工不仅加工量大,加工效率较低,且对加工设备、加工刀具耐用性及加工工艺提出了更严格的要求。
随着现代科学技术的发展,新型产品的不断更新换代,对产品深孔加工质量提出了更高的要求。
因此,研究深孔加工已经成为机械加工行业的必要。
关键词:深孔加工加工设备刀具耐用性加工工艺加工质量
中图分类号:p624.4
1. 深孔定义
一般机械加工方面将孔深l与孔径d之比:l/d>5的孔称为深孔。
原因为:一般实料孔采用麻花钻加工,麻花钻直径d、螺旋角β和螺旋槽导程p成以下关系:p/πd=tan(β)(1.1)
在实际生产中,为了保证麻花钻在钻削过程中的排屑质量,麻花钻一次钻到底即不退刀的情况下,钻孔深度l 5的孔称为深孔。
深孔加工分为:一般深孔加工、精密深孔加工和电深孔加工,这里主要介绍一般深孔加工。
一般深孔加工按照加工方式包括以下几种:
实心钻孔法即原毛坯无孔,采用钻削加工出孔;
镗孔法即已有底孔,为满足孔的精度及表面粗糙度采用镗削加工孔;
套料钻孔法即用空心钻头钻孔,加工完成后毛坯中心残存一根芯棒的方法。
现在产品多为焊接件、锻打件等,原毛坯大部分为无底孔结构,故实心钻孔法是现在深孔加工最常用的加工方法。
下面将重点介绍实心钻孔法。
2.加工设备的选择
其中适合深孔加工的设备主要包含以下几种设备:镗床、钻床、专用钻孔机、铣床、加工中心等。
根据加工工件的结构特点、现有加工设备性能、工装等进行加工设备的选择。
由于镗床、钻床、专用钻孔机等设备在加工孔前,需要借助划线或其它加工方式确定孔在整个工件中位置后,方可加工。
从而导致工件加工时工序较为分散,需要多次装夹产生大量的辅助加工时间,故在加工设备及条件允许的情况下不提倡使用镗床、钻床、专用钻孔机加工孔。
相对以上三种设备,铣床及加工中心在加工孔时,只需要在编制加工程序时确认加工孔位置坐标即可,从而实现了工序集中原则,避免多次装夹造成的装夹误差,不仅缩短了加工辅助时间且提高了加工精度。
3.加工刀具及冷却方式
一般底孔采用钻头加工,钻头的选用直接影响着孔的加工情况。
深孔加工一般处在封闭中加工,我们无法观察到加工状态,无法预测刀具状态,因此刀具的选择至关重要。
其中高速钢麻花钻头是孔加工常用的刀具,但该刀具存在刃磨现象,且横向前角是很大的负前角γ=-54°~-60°,在加工时产生很大的轴向力占45%~55%。
由于横刃长,切削时定心不好,加工时钻头易出现偏斜现象。
目前,随着机械加工刀具的不断更新,一种深孔钻钻头应运而生,深孔钻钻头前角较大,加工时产生的轴向力较小,定心作用较好,且刀片采用硬质合金材质,有效地避免了因材质不均匀或硬点造成刀具偏斜现象,故建议在加工深孔时选用深孔钻钻头。
深孔加工时,刀具在切削的过程产生大量的切削热,若不能及时有效地进行散热,易引起以下问题:
(1).工件易发生热变形;
(2).刀具的耐用度降低,刀具使用寿命较短;
(3).铁屑在高温下,排屑不畅,易造成铁屑缠绕在刀具上,形成积屑瘤,造成孔内壁划伤;
(4).加工过程中产生噪音及振动。
因此切削液的选用至关重要。
切削液的选取主要取决于工件材料的性质、加工方法、加工精度、切削液的类型及切削条件等。
加工过程中切削液的压力和流量充足时,才能将切削液输送到切削区域。
为了更好地保证切削过程刀具得到充分的冷却,推崇在选择深孔钻钻头时,应选择带内冷却液输入的钻头,如walter titex x treme。
4.数控加工深孔指令
在数控加工过程中,钻孔的加工指令包括g81、g82、g83等,下面将介绍深孔钻削指令g83:
深孔加工循环(g83)
数控程序格式:g83x_y_z_r_q_f_k_;
钻削采用深孔加工指令g83,使加工过程中刀具得到充分的冷却空间,加工时每次进给加工量较小,减少刀具在钻孔时产生的变形,有效地避免了因排屑不畅造成的刀具损伤。
5.加工参数的选择
加工参数包括切削速度、进给及切削量。
加工之前根据所选刀具结合工件材质,查找金属切削手册,选择合适的加工参数。
切削速度:用v表示,计算公式 v=nπd/(1000×60)(m/s)(1.4)式中d—工件上加工孔直径(mm),n—工件转速(r/min);
②进给:用f表示,单位(mm/r)。
工件每转一周,刀具沿进给运动方向移动的距离。
③切削量:用ap表示,单位:mm;通过切削刃基点并垂直于工作平面的方向上测量的吃刀量。
根据此定义,如纵向车外圆时,其背吃刀量可按下式计算:a p = (d w —d m )/2 (1.5 )式中:d w ——工件待加工表面直径(mm ); dm ——工件已加工表面直径( mm )。
但钻孔时,切削量为钻头直径d,即a p =d(mm)。
6.结束语
经过多年对深孔加工工艺的探究,本文所简单介绍的深孔加工工艺适合钢件材质的精度要求在it7~it12的孔径在¢14mm~¢30mm 深孔加工。
参考文献
[1]孟孝农,机械加工工艺手册,北京:机械工业出版社,1987
[2]朱祖良,孔加工刀具,北京:国防工业出版社,1990
[3]王世清,深孔加工技术,西安:西北工业大学出版社,2003
[4]上海市金属切削技术协会,金属切削手册,上海:上海科学技术出版社,2000。