深孔加工难题例解
数控机床孔加工常见问题解决方案

数控机床孔加工常见问题解决方案数控机床在工业生产中扮演着重要的角色,它的高精度和高效率使其成为现代制造业不可或缺的工具。
然而,数控机床在孔加工过程中,常常会遇到一些问题。
本文将针对数控机床孔加工中常见的问题进行解决方案的讨论,以帮助工程师和操作人员提高加工效率。
1. 孔径误差过大孔径误差过大是数控机床孔加工中常见的问题之一。
造成孔径误差的原因可能有多种,例如机床参数设置错误、刀具磨损、夹具不稳定等。
解决方案:1.1 检查并优化机床参数设置,确保正确设置进给速度和转速等相关参数。
1.2 定期检查和更换刀具,保持刀具的锋利度,避免磨损引起的误差。
1.3 确保夹具的稳定性,避免夹具松动引起孔径误差。
2. 表面质量不佳表面质量不佳是另一个常见的孔加工问题,特别是在高速切削和深孔加工中。
表面质量不佳可能导致工件精度降低、表面粗糙度增加等问题。
解决方案:2.1 优化切削参数,确保适当的进给速度和切削速度。
2.2 使用合适的刀具和切削液,选择适当的刀具材料和涂层技术,以及使用切削液来降低摩擦和热量。
2.3 定期清洁和维护切削工具,包括清理切片和刀尖,并确保它们保持锋利。
3. 孔面度问题在孔加工过程中,孔面度问题是常见的挑战之一。
孔面度问题包括圆度误差、垂直度误差等。
解决方案:3.1 使用高精度的加工工具和设备,例如精密刀具、夹具等。
3.2 检查和校准机床的几何精度,确保机床的精度和稳定性。
3.3 在加工过程中使用合适的切削液和冷却系统,避免因热变形导致的孔面度问题。
4. 加工效率低加工效率低是数控机床孔加工中常见的问题之一。
低效率可能导致生产周期延长、成本增加等问题。
解决方案:4.1 优化切削参数,例如有效减少孔深和切削时间,提高进给速度和切削速度等。
4.2 使用高效的刀具和切削液,选择合适的刀具和涂层技术,以及使用切削液来降低摩擦和热量。
4.3 自动化和智能化,利用数控机床的自动化功能和智能化控制系统,提高加工效率和生产能力。
深孔(通孔)的加工
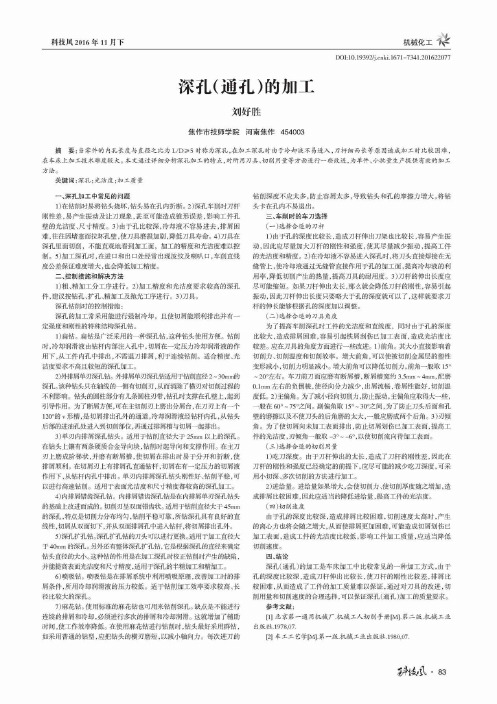
不利影响。钻头的圆柱部分有几条圆柱刃带,钻孔时支撑在孔壁上,起到 引导作用。为了断屑方便,可在主切削刃上磨出分屑台,在刀刃上有一个
度 低 。2)主 偏 角 。为 了 减 小 径 向 切 削 力 ,防 止 振 动 ,主 偏 角 应 取 得 大 一 些 , 一 般 在 60。~ 75。之间 。副 偏 角 取 15。~ 30。之 间 ,为了防止刀头后面和孔
深孔里 面 切 削 ,不能直观地看到加工面,加工的精度和光洁度难以控 动 ,因此应尽量加大刀杆的刚性和强度,使 其 尽 量 减 少 振 动 ,提高工件
制 。5)加 工 深 孔 时 ,在进口和出口处经常出现波纹及喇叭口,车削直线 的光洁度和精度。2)在冷却液不容易进入深孔时,将刀头直接焊接在无
度 公 差 保 证 难 度 增 大 ,也 会 降 低 加 工 精 度 。 二、 控制措施和解决方法
科 技 风 2016年 1 1 月下
机械化工 D O I :10.19392/ki.1671 -7341.201622077
深孔(通孔)的加工
刘好胜
焦 作 市 技 师 学 院 河 南 焦 作 454003
摘 要 :当零件的内孔长度与直径之比为L /D 彡5 时称为深孔,在加工深孔时由于冷却液不易进入,刀杆细而长等原因造成加工时比较困难, 在 车 床 上 加 工 技 术 难 度 较 大 。本 文 通 过 详 细 分 析 深 孔 加 工 的 特 点 ,对 所 用 刀 具 、切 削 用 量 等 方 面 进 行 一 些 改 进 ,为 单 件 、小 批 量 生 产 提 供 有 效 的 加 工 方法。
1)
关于深孔缺陷的原因与防治措施

加工工艺问题
总结词
钻头设计不合理、钻头刃磨质量差、设备精度问题。
详细描述
钻头设计不合理,如钻头顶角过小、切削刃不锋利等,都会影响深孔加工的质量。钻头刃磨质量差会导致钻头磨损不均匀、切削刃崩裂等问题,进而产生深孔缺陷。设备精度问题,如主轴精度差、导轨不直等,也会导致深孔加工过程中的误差和缺陷。
首先,本文主要针对刀具几何参数、切削速度和进给速度等主要影响因素进行了研究,但实际上深孔缺陷的发生还可能受到其他因素的影响,如工件材料性质、冷却液种类等
研究不足与展望
THANKS
感谢观看
案例二:某铸造企业的深孔缺陷问题
总结词
汽车零部件制造企业的深孔缺陷问题通常源于高强度钢板的焊接工艺和后处理流程。
详细描述
该企业在生产一种汽车底盘零件时,发现部分产品存在焊接气孔和夹杂物等深孔缺陷。经过深入调查,发现是由于焊接工艺参数设置不当,导致气体在焊接过程中无法完全排出;同时,后处理流程中的杂质也容易进入焊接区域。针对这些问题,企业调整了焊接工艺参数,优化了后处理流程,从而有效地减少了深孔缺陷的产生。
04
典型案例分析
总结词
机械加工企业的深孔缺陷问题主要源于工件材料、刀具、加工参数以及工艺流程等环节的不合理选择或设计。
要点一
要点二
详细描述
该企业在对一种新型高强度材料进行钻孔加工时,发现孔洞表面粗糙度超标,且存在明显的划痕和挤压痕迹。经过深入调查和分析,发现是由于刀具选择不当,无法适应这种新型材料的硬度要求,加之加工参数设置不合理,导致刀具磨损严重,从而产生了深孔缺陷问题。
案例一:某机械加工企业的深孔缺陷问题
总结词
铸造企业的深孔缺陷问题通常源于模具设计、铸造工艺以及熔炼过程的不完善。
深孔加工中常见的10种问题及解决措施

深孔加工中常见的10种问题及解决措施一、什么是深孔在机械制造业中,一般将孔深超过孔径5倍的圆柱孔称为深孔。
深孔按孔深与孔径之比(L/D)的大小通常可分为一般深孔、中等深孔及特殊深孔三种。
(ps:L/D的比值越大加工起来就越困难。
)1、L/D>5,属于一般深孔,常在钻床或车床上用接长麻花钻加工。
2、L/D=20--30,属于中等深孔,常在车床上加工。
3、L/D=30--100,属于特殊深孔,必须使用深孔钻在深孔钻床或专用设备上加工。
深孔钻按排屑方式分为外排屑和内排屑两种:外排屑有枪钻、整体合金深孔钻(可分为有冷却孔和无冷却孔两种);内排屑又分为BTA 深孔钻、喷吸钻和DF 系统深孔钻三种。
二、加工中常见问题及解决办法1、孔径缩小产生原因:铰刀外径尺寸设计值偏小;切削速度过低;进给量过大;铰刀主偏角过小;切削液选择不合适;刃磨时铰刀磨损部分未磨掉,弹性恢复使孔径缩小;铰钢件时,余量太大或铰刀不锋利,易产生弹性恢复,使孔径缩小以及内孔不圆,孔径不合格。
解决措施:更换铰刀外径尺寸;适当提高切削速度;适当降低进给量;适当增大主偏角;选择润滑性能好的油性切削液;定期互换铰刀,正确刃磨铰刀切削部分;设计铰刀尺寸时,应考虑上述因素,或根据实际情况取值;作试验性切削,取合适余量,将铰刀磨锋利。
2、孔径增大产生原因:铰刀外径尺寸设计值偏大或铰切削刃口有毛刺;切削速度过高;进给量不当或加工余量过大;铰刀主偏角过大铰刀弯曲;铰切削刃口上粘附着切屑瘤;刃磨时铰切削刃口摆差超差;切削液选择不合适;安装铰刀时锥柄表面油污未擦干净或锥面有磕碰伤;锥柄的扁尾偏位装入机床主轴后锥柄圆锥干涉;主轴弯曲或主轴轴承过松或损坏;铰刀浮动不灵活;与工件不同轴以及手铰孔时两手用力不均匀,使铰刀左右晃动。
解决措施:根据具体情况适当减小铰刀外径;降低切削速度适当调整进给量或减少加工余量;适当减小主偏角校直或报废弯曲的不能用的铰刀;用油石仔细修整到合格;控制摆差在允许的范围内;选择冷却性能较好的切削液;安装铰刀前必须将铰刀锥柄及机床主轴锥孔内部油污擦净,锥面有磕碰处用油石修光;修磨铰刀扁尾调整或更换主轴轴承;重新调整浮动卡头,并调整同轴度;注意正确操作。
加工深孔不震刀的方法

加工深孔不震刀的方法
这就好比在走钢丝的时候不能晃悠,一旦震刀,那可就糟糕透啦!
首先说说步骤。
得选好合适的刀具,就像战士上战场要挑趁手的兵器一样。
刀具的材质、角度都得讲究。
然后调整好切削参数,速度不能太快也不能太慢,这就跟开车似的,太快了容易失控,太慢了又没效率。
接着要保证工件的夹紧牢固,可不能松松垮垮的,不然就像在摇晃的船上干活,能不出问题吗?
注意事项也不少呢!刀具要定期检查和更换,要是磨损了还硬着头皮用,那肯定不行。
切削液也得选对,它就像是给机器喝的饮料,得合适才行。
还有啊,操作的时候一定要小心,可不能马虎大意。
安全性和稳定性那是必须要考虑的。
不震刀才能保证操作的安全呀,要是刀震得厉害,说不定啥时候就飞出去了,那多吓人!稳定性好的话,加工出来的孔质量才高,不会出现偏差。
应用场景可多啦!机械加工、模具制造都能用到。
它的优势也很明显,能提高加工效率,减少废品率,让你的工作事半功倍。
咱再来看看实际案例。
有一次,一个工厂在加工深孔的时候总是震刀,
废品率特别高。
后来他们按照我说的方法调整了刀具和切削参数,嘿,问题就解决了。
加工出来的孔又光滑又标准,老板高兴得不得了。
所以啊,加工深孔不震刀的方法真的很重要。
只要掌握了正确的方法,就能让你的工作顺顺利利,再也不用为震刀而烦恼啦!。
采用深孔加工技术解决机床主轴深孔加工难题
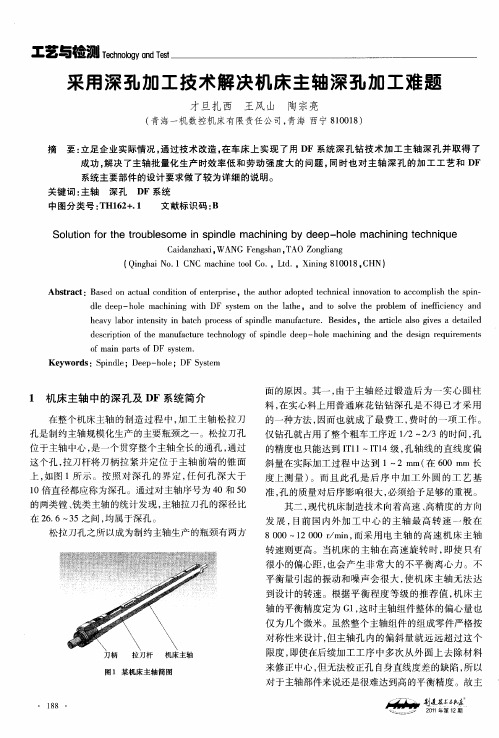
1 机床主轴 中的深孔及 D F系统简 介
在 整个机 床 主轴 的制 造 过 程 中 , 工 主轴 松 拉 刀 加
孔 是制 约主轴 规模 化生 产 的主要瓶 颈之一 。松 拉刀 孔
面 的原 因。其一 , 由于 主轴 经 过 锻 造后 为 一 实 心 圆 柱 料, 在实心 料上 用普 通麻 花 钻 钻 深 孔是 不 得 已才 采 用 的一 种方 法 , 因而也 就 成 了最 费工 , 费时 的一 项 工作 。 仅钻 孔就 占用 了整个 粗车 工序 近 12~ / / 2 3的 时间 , 孔 的精 度也 只能 达到 I1 ~I1 , 轴 线 的 直线 度 偏 T 1 T 4级 孔
工艺与检测 ThI de enga I C0yn s l T 0
采 用 深 孔 加 工技 术 解 决 机 床 主 轴深 孔 加 工 难 题
才旦扎西 王风 山 陶宗亮
( 青海 一机 数 控机床 有 限责任公 司, 青海 西 宁 80 1 ) 10 8
摘 要: 立足企 业 实际情 况 。 过技 术改造 , 车床 上 实现 了用 D 系统 深 孔钻 技 术 加 工主 轴 深 孔并 取得 了 通 在 F 成功 , 决 了主轴 批量化 生产 时效 率低 和 劳 动 强 度大 的 问题 , 解 同时也 对 主 轴 深 孔 的加 工 工 艺和 D F 系统 主要部 件 的设 计 要求做 了较 为详 细的说 明 。 关键 词 : 主轴 深 子 D L F系统 文献标 识码 : B 中图分 类号 : H1 2 . T 6+1
he v a o n e st n b th p o e s o p n l n f cu e Be i e ,t e atce a s i e e ald a y l b r it n i i a c r c s fs i d e ma u a t r . y sd s h ril lo gv s a d tie d s rp in o h n fc u e tc oo y o p n l e — oe ma h n n n h sg e u r me t e c i t ft e ma u a t r e hn l g fs i d e de p—h l c i i g a d t e de in r q ie n s o o i a t fDF s se fman p rs o y tm. Ke wor y ds:S i d e;De p—h l pn l e oe;DF S se y t m
基于机械加工的深孔加工技术探析
基于机械加工的深孔加工技术探析一、引言深孔加工是一种特殊的加工方式,其对工件质量和加工精度要求非常高。
针对深孔加工技术,传统的机械加工方法在加工效率和加工质量方面都存在一定的局限性。
如何基于机械加工技术进行深孔加工是一个重要的课题。
本文将探索基于机械加工的深孔加工技术,分析其优势和不足,并对未来的发展方向进行展望。
二、传统机械加工中的深孔加工技术1. 深孔加工的难点及其解决方法深孔加工过程中的难点主要包括切削阻力大、刀具寿命短、加工精度难以控制等问题。
针对这些难点,传统的机械加工技术采用了一系列工艺改进和刀具优化措施,如采用特殊的刀具材料、提高刀具的刚性和韧性、优化刀具结构等方法。
这些改进措施在一定程度上提高了深孔加工的加工效率和加工质量,但仍然存在一定的局限性。
2. 传统机械加工的优势和不足传统机械加工方法在深孔加工中有其独特的优势,如设备成本低、加工精度高、加工表面质量好等。
但传统机械加工方法在面对深孔加工时,由于工件材料和加工尺寸的限制,存在加工效率低、加工精度难以控制等问题。
1. 刀具技术的发展随着刀具制造技术的不断进步,新型刀具材料和刀具涂层技术的应用,保障了刀具的寿命和性能。
新一代的刀具结构设计也在提高切削效率的降低了切削温度和切削力,有利于深孔加工过程中的稳定加工。
2. 设备技术的改进基于机械加工的深孔加工技术中,设备的改进也是一个重要的方向。
随着数控技术的发展,深孔加工设备的自动化程度不断提高,加工精度和稳定性得到了显著提升。
一些新型的深孔加工设备在结构上也有所突破,如多轴切削、自动化刀具更换等技术的应用,进一步提高了深孔加工设备的灵活性和效率。
3. 加工工艺的优化在基于机械加工的深孔加工技术中,加工工艺的优化也是一个重要的方向。
通过优化切削参数、采用新型的切削液和切削方式等措施,可以提高深孔加工的效率和精度。
基于数字化加工的优化方法也在不断发展,通过建立数学模型和仿真分析,提高深孔加工的过程控制和优化效果。
曲轴油孔加工过程中的问题及解决措施
曲轴油孔加工过程中的问题及解决措施一、深孔钻概念在机械制造业中,一般将孔深超过孔径10倍的圆柱孔称为深孔。
深孔按扎深与孔径之比(L/D)的大小通常可分为一般深孔、中等深孔及特殊深孔3种。
1 L/D=10~20,属于一般深孔。
常在钻床或车床上用接长麻花钻孔加工。
2 L/D=20~30,属于中等深孔。
常在车床上加工。
3 L/D=30~100,属于特殊孔深。
必须使用深孔钻在深孔钻床或专用设备上加工。
二、深孔加工难点1.不能直接观察到切削情况。
仅凭声音、看切削、观察机床负荷、油压等参数来判断排屑与钻头磨损情况。
2. 切削热不易传出。
3.排屑较困难,如遇切削阻塞则会引起钻头损坏。
4.因钻杆长、刚性差、易振动,会导致孔轴线偏斜,影响到加工精度及生产效率。
三、深孔加工类型(曲轴油孔工艺案例)深孔钻的类型、使用范围及工作原理,深孔钻按排屑方式分为外派屑和内排屑2种,外排屑有枪钻、整体合金孔钻(可分为有冷却和无冷却孔2种):内排屑又分为BTA深孔钻、喷吸钻和DF系统深孔钻3种。
(下面我们来介绍下曲轴油孔工艺)01、曲轴油孔工艺图纸第一步:选择平底钻在曲轴的连杆或主轴曲面上铣出小平面(为后序引导钻提供基础平面)。
第二步:选择引导钻在连杆或主轴上钻入1.5D-2D的孔深(为后序深孔钻提供良好的导向和预钻准备)。
第三步:选择深孔钻头在已有的孔径上钻通该孔径。
第四步:(主轴/连杆颈)孔口倒角,去除孔口毛刺。
PS:曲轴油孔工艺一般分为两种类型,1、交叉孔:连杆油孔和主轴油孔相互交叉。
(加工有难度)2、直通孔:连杆有油孔,主轴无油孔。
上面描述的油孔工艺是很多工厂采用的普遍方式,也有的工厂把第一步和第二步合并了,用平底钻当做引导钻的方式进行预定心(这里不建议工厂采用这种形式),貌似加工的效率提高了,其实后面的刀具维护成本会增加,请注意。
(有需要油孔加工程序的可以联系小编我,提供程序供您研究)02、曲轴油孔加工注意问题一般平底钻和引导孔的长短很接近,在更换刀具的时候请操作者要看清楚,否则容易发生撞刀事件。
某管型零件深孔加工工艺分析
关键词:拉刀;管型零件;工装;紫铜;深孔引言某管型零件外形为Φ22mm×275mm圆管,其内孔直径为Φ17.9mm±0.05mm、要求加工后内壁光洁度1.6,零件材料为紫铜。
由于紫铜材料塑性较好、强度较低,加工时极易变形,且圆孔长度大,光洁度和尺寸要求较为严格,因此Φ17.9mm圆孔加工为加工流程中最困难的环节。
在进行加工前,首先对比各种深孔加工方式。
主流的深孔加工方式有拉削、镗孔、慢走丝等。
镗孔的加工效率较高且成本低,但由于此零件长径比较高,镗刀刀杆在加工时可能出现弯曲,影响加工精度;慢走丝的精度较高,可满足加工要求,但成本高且加工效率较低。
在对比各种深孔加工方法的基础上,考虑到拉削加工方式具有加工精度高、表面光洁度易保证、生产率高、适于大批量生产等优点,且圆孔拉刀结构较为简单,易于生产,因此尝试使用拉削方式加工内孔。
1拉刀的工艺参数选择根据实际情况,由于零件内孔较小,拉刀直径受到限制,考虑到如果仅采用一把拉刀进行拉削,切削力在拉刀危险截面形成的应力将会超过拉刀危险截面许用应力,遂决定采用多把直径依次增大的圆孔拉刀从小到大依次拉削圆孔至尺寸要求的方案,即先使用线切割粗加工圆孔至Φ17.8mm,再使用多把圆孔拉刀依次拉削圆孔至尺寸Φ17.9mm。
1.1拉刀材料的选择刀具材料主要按被加工材料性质以及切削参数确定,所加工材料为紫铜,属于很容易切削的材料;拉削的切削速度、切削深度都比较低,故决定选取相对容易加工的淬火T8工具钢作为刀具材料。
1.2拉刀齿升量选择齿升量的大小会影响加工表面质量、拉削力、拉刀耐用度、拉削效率。
根据实际情况,由于被加工内孔长度较长、切屑无法在加工时排出,且被加工材料刚度较差,不能承受较大的拉削力,故不宜选择较大的齿升量,根据实验,选取单边齿升量为0.005mm。
1.3拉刀的结构设计已确定切削余量为0.1mm,单边齿升量0.005mm,故需要至少10个切削齿才能完成切削。
深孔加工常见问题解决方法
深孔加工常见问题解决方法【德州三嘉机器】在深孔加工过程中,经常出现被加工件尺寸精度、表面质量以及刀具的寿命等问题,如何减少甚至避免这些问题的产生,是我们目前亟待解决的问题。
德州三嘉机器制造有限公司拥有先进的深孔加工技术,拥有一支精益求精、不懈创新的科研团队。
下面德州三嘉为我们介绍一下深孔加工常见问题解决办法~#详情查看#【德州三嘉机器:深孔加工】难切削材料的深孔加工、深孔钻削孔轴线偏斜和深孔加工表面出现螺旋沟都是深孔加工中难以解决的问题,直接影响深孔加工质量和加工效率。
因此,研究难切削材料的深孔加工技术、控制深孔钻削孔轴线偏斜技术和抑制深孔加工表面出现螺旋沟技术,成为深孔加工中最为关注的问题。
【深孔加工常见问题解决方法】1、难切削材料的深孔加工难加工材料一般是指不锈钢类、钛合金类、高温合金类材料,这些材料的共同点是韧性强,断屑困难,导热性差,容易产生加工硬化,应采取相应工艺措施:1.1、选择合适的刀具材料,因为加工材料中有的元素与刀具材料有一定的亲和力,会产生严重的粘刀现象,刀具磨损严重。
1.2、选择合适的切削用量:一般选用V≤20m/min,f=0.01-0.07mm/r。
1.3、选择合适的刀具角度:选择大前角,使切削轻快省力。
1.4、选择合适的排屑方式:由于难加工材料不容易断屑,如果采取低转速,较深断屑台的方式都不能很好断屑的话,最好采用不断屑的相反措施,即减小进给量,适当提高转速,切出薄薄的切屑,使切屑绵长不断并顺利排出,切削十分平稳。
2、深孔钻削孔轴线偏斜深孔钻削孔轴线偏斜问题是目前存在的一个技术难题。
当钻孔长径比大于50时,孔轴线的偏斜一般无法预测和控制。
孔轴线偏斜到一定程度后,就开始急剧变化,此时,孔轴线大大超差,钻头甚至从工件中间穿出,造成工件报废,钻头损坏,损失较大。
针对以上问题可采取以下措施:1、选择最佳切削方式,尽量选择工件旋转+刀具旋转,条件允许的情况下,工件应旋转。
2、合理选择刀具几何参数。
- 1、下载文档前请自行甄别文档内容的完整性,平台不提供额外的编辑、内容补充、找答案等附加服务。
- 2、"仅部分预览"的文档,不可在线预览部分如存在完整性等问题,可反馈申请退款(可完整预览的文档不适用该条件!)。
- 3、如文档侵犯您的权益,请联系客服反馈,我们会尽快为您处理(人工客服工作时间:9:00-18:30)。
深孔加工难题例解Exa mp les of So lving D ifficut P roble m s in L ong Ho le M ach in ing西安石油学院深孔加工技术研究所(710065) 彭海 刘战锋 刘雁蜀【摘要】介绍了超小直径的深孔加工、异形零件的深孔加工、薄壁精密零件的深孔加工、两端孔径小中间孔径大的深孔加工方法,并例举5个加工实例,阐明零件的深孔加工工艺及该深孔与其他加工面之间的主要加工难点、解决办法及加工注意事项等。
关键词 深孔加工 加工实例 工艺措施Keywords l ong ho le m ach in ing ,p ractical exa mp les of m ach in ing ,techno l ogicalm easures小直径深孔的加工 本文所指的小直径深孔是53~56mm ,长径比(Ld )为80~300的深孔,加工这类深孔,一般可采用枪钻或深孔麻花钻。
由于56mm 以下小孔的枪钻制造,目前在国内还是个难题,而进口枪钻价格高,因此受到一定的限制。
在对一般加工精度的这类深孔,采用深孔麻花钻加工,也能满足孔加工尺寸精度和孔表面质量要求时,由于其不需要专用的深孔加工机床、油路系统及其附加装置,应用仍很广泛。
我们就曾采用大螺旋角、厚钻芯的蜗杆形深孔麻花钻(刃形都修磨成XXZ 21刃形[1]或群钻刃形)加工此类小直径深孔,注重钻头的刃磨和操作规则,均取得了较好的效果。
如图1所示的零件,为一支撑板,上有53mm 的相交孔,若用枪钻钻孔,除钻头价较高外,在厚度只有8mm 的钢板端面上进行高压密封也十分困难,且装夹工件、定位夹紧、油路系统及密封装置都十分复杂。
而用53mm 蜗杆形的深孔麻花钻加工,相对而言则较为简便。
图1 支撑板零件图在加工中,采用回转式的专用夹具,以工作面C ,B 定位,首先钻削孔1,2,3,4,随后,将工件随夹具体回转90°,用表找正A 面,保证A 面与B 面平行,夹持后,钻削孔5,6;最后将工件和夹具体回转180°,找正A 面,夹持后钻削孔7,8。
在钻削这些孔时,每个孔必须钻直,否则两孔就很难垂直相交,并容易断钻;同时也难保证与大孔5154.5+0.20mm 间的1.25mm 最小壁厚。
因此,必须对钻头修磨横刃,使横刃长度b 7≈0.2mm ;除此之外,在加工中,应及时修磨刃口,保持钻刃的锋利性,并保证缓慢匀速进给。
在整个钻削过程中必须稳定可靠,对修磨钻头的刃形、提钻排屑的次数、每次钻削的深度及切削用量等都必须严格的按规程操作,否则废品率将相当高。
图2 驱动体套中有平行深孔的零件图图2所示为驱动体套零件,材质为35C r M o 钢,在壁厚为15mm 的孔壁上分别钻削56×1880mm 和56×1835mm 两个小孔,并要求此两小孔与584+0.054mm 大孔的平行度为50.3mm ,以便保证壁厚能承受70M Pa 的工作压力。
为满足平行度要求,采取的主要工艺步骤是:1)按5130×2130mm 尺寸下料;2)钻562mm 通孔;3)将工件按L 1=1400mm ,L 2=730mm 截成2段;4)以内孔为基准,2段按同一尺寸车削外圆(留半精车余量);5)对较长的L 1段,采用深孔麻花钻在其两端对钻56mm 小孔,保证560-0.1mm 检验棒能顺利通过对穿钻通的56mm 小孔;对较短的L 2段,钻56mm 盲孔,保证孔深;6)对2段加工焊接坡·81·《新技术新工艺》·机械加工与自动化 2001年 第6期口,保证对中同轴;7)焊接,并钻通56mm 接缝;8)热处理并按外圆校直;9)以56mm 两小孔为基准(找正),半精车外圆,保证56mm 两小孔与外圆母线的平行度;10)以外圆为基准半精镗、精镗、精珩内孔达到尺寸精度;11)以内孔为基准精车成外圆。
异形零件的深孔加工 如图3所示的驱动体零件,对U 形斜槽(斜度为4°)的加工,若用铣削,不仅需要设计制造专用铣刀,且加工质量难以保证。
针对该零件的特殊性,我们采用了以下主要工艺措施:1)将下料尺寸加大加长到5100×887mm ;2)将调质处理后的工件,半精车成597±0.1×880±0.5mm ,并距右端420mm 处铣15mm ×15mm 找正基图3 驱动体套中有U 形斜槽的零件图准缺口,保证缺口底面与工件轴心线平行;3)在卧铣床上,找正工件母线,并找正基准15mm ×15mm 的缺口底面与铣床工作台面垂直,在工件右端上铣4°斜面(作为钻、镗孔时的密封面);4)为保证右端底面在工件总长截短(830mm )后仍有2mm 的壁厚,采取在工件右端距轴线下端22±0.02mm 处打顶尖孔,左端距轴线39.5mm 处打顶尖孔,两顶尖孔轴线应在同一截面内,这样,工件两端形成4°斜孔的顶尖孔基准;并车出两端定位外圆。
在深孔钻床上找正工件后钻镗、珩磨540+0.146+0.1斜孔;5)配右端斜孔堵头,两端校正后打584-0.036-0.071mm 外圆柱面的顶尖孔,并精车、精磨584mm 外圆。
经过上述加工后,就保证了斜孔540+0.146+0.1的精度要求。
其他加工工艺略。
薄壁超细长钛合金零件的加工 图4所示的零件材料为TC 10,是钛合金材料中最难切削的一种,由于弹性模量E ≈10000N mm 2,加工变形很大。
工件壁厚又仅为5mm ,长径比L d =170(使用单位加长了工艺夹头,工件实际加工长度L =3400mm ),工件刚度极差。
该零件加工要求又非常高,在全长范围内,任何一个截面内的尺寸及壁厚超差,都按废品处理。
制定加工工艺时,内孔是外圆加工的基准,外圆要根据内孔的直线度及壁厚校直、找正后进行车削。
因此,深孔钻削质量的高低,直接影响外圆的车削质量,是保证外圆精度的关键。
对此,针对钛合金材料的特性,设计了专用的错齿内排屑深孔钻头,它在钻削时能完全分屑,钻刃刃形能保证径向力压向两导图4 钛合金零件图向块,使自身导向平稳可靠,且直线度较好。
并在整个加工过程中采取了有效的监测措施,以保证钻削过程排屑顺畅,随时进行纠偏处理,保证了钻孔平直。
孔钻完后先进行粗珩,待精车完外圆后再精珩内孔。
为保证车削质量及较高的车削效率,还采用了刚性好的跟刀架、中心架及宽刃弹簧车刀。
孔径两端小中间大的深孔加工 图5所示的工件,孔径两端小,中间大。
加工这种零件需设计专用的镗刀。
要求镗刀应满足:1)镗刀由小孔进入适当位置后,镗刀块能强迫伸出、夹紧。
当到达一定位置后,镗刀块又能松开,缩回刀体以便镗刀能从小孔中退出;2)要求镗刀在孔中能自身导向,以增强镗刀的刚性;3)镗刀体应有一定的容屑、排屑的空间,并通过一定压力的切削液强迫切屑沿一定方向排出。
图5 缸套零件图图5所示零件是在高转速下工作的(10000~20000r m in ),故要求尺寸精度和相互位置精度都较高,特别是壁厚差需要严加控制。
由于工件刚度很差,加工难度非常大,因此,制定该零件加工工艺时采取以下措施:1)钻孔、粗镗、半精镗内孔;2)以内孔为基准,半精车两端外圆,以保证两端外圆与内孔的同轴度;3)内、外圆互为基准,经几次反复的粗加工及半精加工后,再用珩磨的方法精磨“大肚子孔”;4)精车外圆,在此,以内孔及壁厚尺寸来决定外圆尺 (转下页)·91·《新技术新工艺》·机械加工与自动化 2001年 第6期迭片式装置的工作原理和应用效果Functi onal P rinci p le and A pp licati on Purpo se to C ircularity L a m inated Equi pm en t武汉理工大学信息工程学院(430070) 李彬 张兴中【摘要】介绍火力发电厂水处理设备——双流弱酸离子交换器的内部结构特点及迭片式装置专利产品如何代替传统的包网工艺,同时阐述在诸多的装置中,迭片式结构的先进性,以及采用迭片式装置时应注意的几个问题。
关键词 双流弱酸 迭片 装置 树脂Keywords double 2fl ow w eak acid ,la m inated ,equi pm en t ,resin 双流弱酸离子交换器是工业水处理离子交换设备,它的优点是工作交换容量高,设备出力大,与双流机械过滤器、双流混床等设备相比较,在同直径设备水处理出力条件下,可节约投资,减少占地面积,降低运行费用。
图1是双流弱酸离子交换器工作原图1 双流弱酸离子 交换器工作原理图理示意图。
工作时,水由上下封头同时进入内部,经穹形多孔板的筛分及砂垫层的配水作用,在上下树脂层中进行交换,处理后由中部送出。
树脂失效后,先反洗上部床层,再反洗整个树脂层,再生液自上而下通过全部树脂层,最后对整个床内树脂进行置换和正洗。
由图1所示工作原理可知:在离子交换器正常工作时,为保证交换后的软化水进入锅炉,而要求树脂不与软化水一起流失,要使用中排水装置;另一方面,使用中交换剂(树脂)频繁失效、再生,再生的废液经排液装置流出,而交换剂不可以流失,这就需要由再生装置来完成。
中排水装置和再生装置均可统称为排(进)液装置。
迭片式排(进)液装置是一种先进的排除液体,阻止固体流失的装置,因此,中排水装置和再生装置都可采用迭片式排(进)液装置,它有足够的强度,简单的结构,优良的抗酸碱腐蚀性。
迭片式装置的应用 双流弱酸离子交换器的排(进)液装置,是按大阻力配水系统设计的,通过提高小孔流速使集水均匀。
它具有两种作用:一是将经上、下树脂层交换之后的优质水汇集送出;二是兼作上层树脂进水松动反洗。
出水母管上置于水平母管上,支管为鱼刺型,由法兰连接于系统(见图2),其材质按用户要求,有1C r 18N i 9T i (美国称321),0C r 17N i 12M o 2(美国称316),00C r 17N i 14M o 2(美国称316L )等。
传统水处理设备中的排(进)液装置,一律采用包网方法,其包网金属骨架与迭片装置金属骨架一样,而骨架上的包网材质有塑料网与金属网。
按系统阻力力计算出支管直径及其上的孔数,钻孔后在每根支管上先套16目塑料窗纱,经100℃水或蒸汽热缩在金属骨架上,其外再套60目涤纶布后,按一定(接上页) 寸,即保证壁厚的办法车削外圆。
值得注意的是由于该零件壁厚只有4mm ,外径又比较大,为增大阻尼,减小车削振动,我们向内孔灌入2 3~3 4容积的砂粒,这样就有效地保证了车削的正常进行;5)在各工序之间对零件进行了多次时效处理,以减小工件的变形量。