某小型铸造车间除尘系统设计(1)
车间除尘系统设计
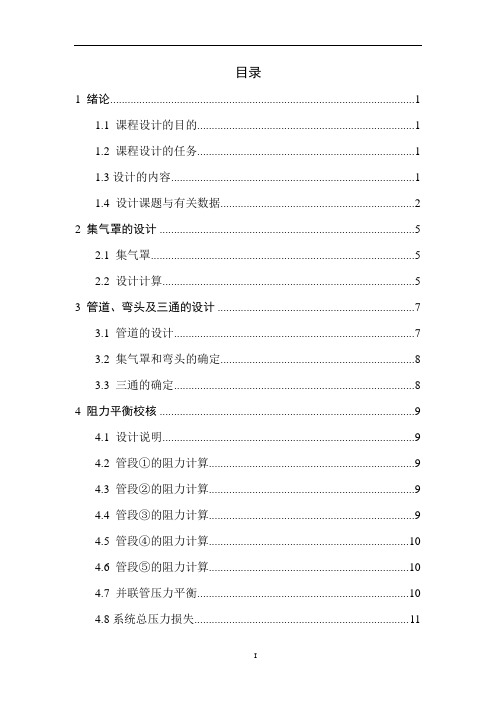
目录1 绪论 (1)1.1 课程设计的目的 (1)1.2 课程设计的任务 (1)1.3设计的内容 (1)1.4 设计课题与有关数据 (2)2 集气罩的设计 (5)2.1 集气罩 (5)2.2 设计计算 (5)3 管道、弯头及三通的设计 (7)3.1 管道的设计 (7)3.2 集气罩和弯头的确定 (8)3.3 三通的确定 (8)4 阻力平衡校核 (9)4.1 设计说明 (9)4.2 管段①的阻力计算 (9)4.3 管段②的阻力计算 (9)4.4 管段③的阻力计算 (9)4.5 管段④的阻力计算 (10)4.6 管段⑤的阻力计算 (10)4.7 并联管压力平衡 (10)4.8系统总压力损失 (11)5 风机、电机选择及计算 (12)6 厂房设计 (14)7 设计小结 (15)参考文献 (16)附录 (17)图1 车间除尘系统平面布置图 (17)图2 立面布置图 (17)图3 轴测图 (17)1 绪论1.1 课程设计的目的课程设计的目的在于进一步巩固和加深课程理论知识,并能结合实践,学以致用。
本设计为车间除尘系统的设计,能使学生得到一次综合训练,特别是:1、工程设计的基本方法、步骤,技术资料的查找与应用;2、基本计算方法和绘图能力的训练;3、综合运用本课程及其有关课程的理论知识解决工程中的实际问题;4、熟悉、贯彻国家环境保护法规及其它有关政策。
1.2 课程设计的任务学生在有限的时间内,必须在老师的指导下独立、全面地完成此规定的设计。
其内容包括:1、设计说明书和计算书各一份;2、平面布置图一份;3、立面布置图一份;4、轴侧图一份。
1.3设计的内容1、罩的设计控制点速度Vx的确定;集气罩排风量、尺寸的确定。
2、道的初步设计管内流速的确定;管道直径的确定;弯头设计;直管长的确定;三通的设计计算。
3、损平衡计算分段计算;压力校核。
4、压损计算5、风机、校核6、机选择、校核7、有关说明1.4 设计课题与有关数据1、设计题目:车间除尘系统设计;2、课题已知条件;a 车间面积与两台产生污染设备的位置,见附图。
车间除尘系统设计
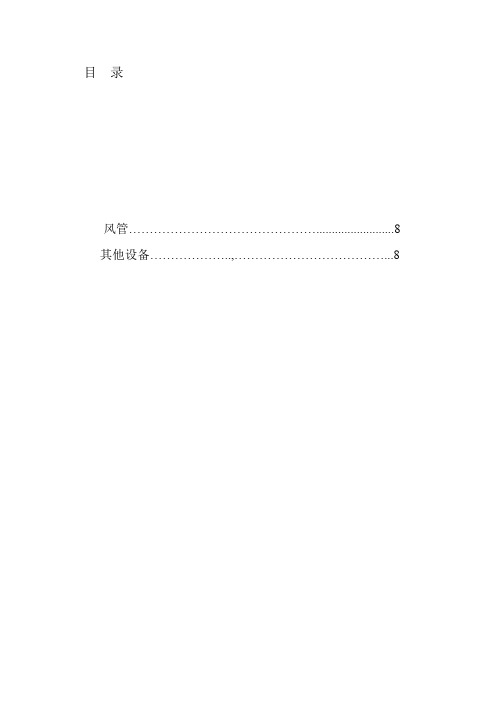
目录风管 (8)其他设备...................., (8)某车间除尘系统设计第1章课程设计任务书一、目的:课程设计的目的在于进一步巩固和加深课程理论知识,并能结合实践,学以致用。
本设计为车间除尘系统的设计,使学生得到一次综合训练。
特别是:1.工程设计的基本方法、步骤,技术资料的查找与运用;2.基本计算方法和绘图能力的训练;3.综合运用本课程及其有关的理论知识,解决工程中的实际问题;4.熟悉、贯彻国家环境保护法及其有关政策。
二、任务与要求学生在限定时间内,必须在老师指导下独立、全面地完成此规定的设计。
其内容包括:1.设计说明书一份,设计计算书一份2.平面布置图一份3.立面布置图一份4.轴侧图一份三、设计内容1.集气罩的设计控制点控制速度V的确定集气罩排风量、尺寸的确定2.管道的初步设计管内流速确定管道直径确定弯头设计直管长确定三通设计计算3.压损平衡计算分段计算压力校核4.总压损计算5.选风机、校核6.电机选择、校核7.车间大门设计四、设计课题与有关数据1.设计题:某车间除尘系统设计说明:本设计为新建项目进行设计。
项目设计完成后的验收标准有:《大气污染物综合排放标准》GB16297-96表2中二级标准;《工业企业设计卫生标准》TJ36-79车间空气中有害物质的最高容许浓度标准;2.课题已知条件a.车间面积与两台产生污染设备的位置见附图一b.产生污染源设备的情况污染源:两个污染源水平放置,立方体 L × W × H 1200×600×1000(mm)操作条件:20℃污染源产生粉尘情况:污染源产生轻矿物粉尘,以轻微速度发散到尚属平静的空气中。
c.在该污染设备的顶部设计二个伞形集气罩,罩口边须距污染面积H=600mm,才操作正常。
d.管道和集气罩均用钢板制作钢管相对粗糙度 K=排气筒口离地面高12me.所用除尘器:LD14型布袋除尘器布,该布袋除尘器阻力为980Pa,长,宽,除尘器进口高度,出口高度。
铸造车间烟气净化系统设计
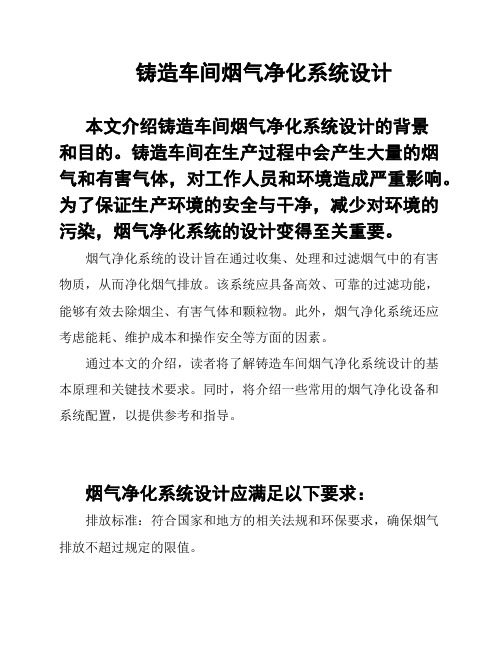
铸造车间烟气净化系统设计本文介绍铸造车间烟气净化系统设计的背景和目的。
铸造车间在生产过程中会产生大量的烟气和有害气体,对工作人员和环境造成严重影响。
为了保证生产环境的安全与干净,减少对环境的污染,烟气净化系统的设计变得至关重要。
烟气净化系统的设计旨在通过收集、处理和过滤烟气中的有害物质,从而净化烟气排放。
该系统应具备高效、可靠的过滤功能,能够有效去除烟尘、有害气体和颗粒物。
此外,烟气净化系统还应考虑能耗、维护成本和操作安全等方面的因素。
通过本文的介绍,读者将了解铸造车间烟气净化系统设计的基本原理和关键技术要求。
同时,将介绍一些常用的烟气净化设备和系统配置,以提供参考和指导。
烟气净化系统设计应满足以下要求:排放标准:符合国家和地方的相关法规和环保要求,确保烟气排放不超过规定的限值。
处理效率:能有效地去除烟气中的有害物质,达到设定的处理效率要求。
设备可靠性:确保净化设备的稳定性和可靠性,长时间运行不间断。
经济性:设计方案要考虑到投资成本、运行成本和维护成本,尽量降低整体成本。
工艺适应性:考虑到铸造车间的工艺特点和生产需求,确保净化系统能适应不同工艺条件下的烟气处理。
安全性:设计考虑到设备操作和维护的安全性,确保运行人员和维修人员的人身安全。
本文将提出一个或多个铸造车间烟气净化系统设计方案,并针对每个方案进行详细说明和分析,包括净化设备的选择、排放管道布局等。
方案一说明方案一是基于目前市场上广泛应用的湿式烟气净化技术。
该方案主要包括以下几个步骤:采集烟气:通过管道将铸造车间的烟气引入净化系统。
前处理:在进入净化设备之前,通过预处理步骤去除大颗粒物质和一些可燃杂质。
净化设备选择:选择适合铸造车间烟气净化的湿式净化设备。
根据实际情况,可以选择湿式电除尘器或湿式床塔等设备。
净化效率测试:对所选择的净化设备进行净化效率测试,确保系统的稳定性和有效性。
排放管道布局:设计合理的排放管道布局,确保排放的烟气符合环保标准。
铸造车间除尘系统设计及除尘设备选择

关风器(如第134页图2)是含尘空气进入除尘 器装置之前的最初环节,此时含尘气体中的悬浮介 质浓度较小,设备灰斗中的待处理尘粒量不大,且灰 斗下方的圆面直径设计约为100 mm,可以选择容量 较小的关风器类型,确定型号为TGFY. 4(5),叶轮 尺寸为200 mmX 150 mm,容量为4(5)L,配用动力 为 0. 37 kW,外型尺寸为 293 mm X 246 mm X 352 mm,质量约为32 kgo 2. 3风机设计
根据铸造车间的实际情况,分析出本次“新建铸 造车间配套除尘系统”的设计目的如下。
1) 净化空气中分散介质(粉尘颗粒)。在铸造 车间中,催化反应的原料气中会产生固体微粒,这些 微粒会影响催化剂的使用,因此需要原料气进入反 应器之前去除分散介质。
2) 回收分散介质。在铸造车间的生产线中,反 应器设备送出的气体中一般含有大量的催化剂悬浮 颗粒,为了维护车间内工作环境,必须借助除尘系统 回收分散物质,同时将车间中其他工艺环节送出的 气体回收,统一回收处理分散介质⑶O
・134・
山西化工
sxhgbjb@ 126. com
第41卷
准粉尘扩散方向。技术人员可以计算全密封吸尘罩 抽风量为L = 250 S,其中L表示抽风量,单位为
m3/h;S表示吸尘罩容积,单位为n?。之后,分别调 整罩内的扬尘强度,控制罩体漏风情况。
图2关风器 方,处于正压段位置或者压入段位置,此时进入通风机 的气体没有经过除尘,容易损伤通风机中的叶轮或者 机壳,且这一系统主要适用于含尘质量浓度V3 g/m3 的气体。 综合以上设备情况,本次选择除尘设备为属于负 压除尘系统结构的旋风除尘器,这一除尘器设备具有 制作简单、易于维护的优势,能够满空气中粒 子的去除,除尘率达到85%,能够适用于高温烟气环 境,充分满足本次铸造车间内的空气除尘要求。
铸造车间负压除尘系统的设计

1 序言1.1铸造车间的污染及其除尘状况的概述1.1.1研究目的和意义铸造是现代机械制造工业的基础工艺之一,因此铸造机械业的发展标志着一个国家的生产实力。
我国目前已经成为世界铸造机械大国之一,在铸造机械制造行业近年来取得了很大的成绩。
我国是铸造大国,在十五期间,随着国民经济的高速发展.我国铸件年产量一直居世界铸件生产大国榜首。
从数量上来看.整个形势是喜人的.但铸造生产的粗放特征没有得到根本改变。
据报道,冲天炉配备有效环保设施的不到总数的5%.采用手工造型为主的铸造厂占90%~95%:现场环境恶劣、作业条件差、技术落后、粗放式生产的铸造企业占90%以上。
我国铸造业环境问题尤其表现在对自然资源的超量消耗上.有“资源漏斗”的说法。
可以看出,铸造产业的除尘是非常有必要的。
一个合理的除尘系统,能让除尘的效率大大提高,不仅能让铸造车间环境大大改善,对车间以外的环境也能起到保护作用。
除尘技术的好坏也能体现一国铸造技术的好坏。
1.1.2中国铸造业现状及铸造车间污染情况近年来.我国铸造业获得了飞跃式的发展,从2000年至2003年.中国铸件产量跃居世界首位。
从2003年至今,中国铸件产量依旧保持持续增长。
并且。
整个世界都在从中国寻求更多的铸件毛坯及含有铸件的终端制品。
这种趋势在近期内有可能将继续保持并保证中国铸造业的持续繁荣。
但在铸造业繁荣的背后。
也存在着形势严峻的一面。
有资料表明。
我国铸造生产中。
材料和能源的投人之比可占到产值的55%到70%。
能源环境的制约以及国际铸造科技竞争加剧和知识产权的保护强化.已成为我国铸造业发展的瓶颈.发展节约环保型、科技创新型铸造之路刻不容缓。
我国铸造生产中。
材料和能源的投人占产值的55%~70%。
我国每产1 t铸件。
约散发50 kg粉尘.熔炼和浇注工序排放废渣300 kg、废气1 000 m3造型和清理工序排废砂1.3~1.5 t。
每年排污物总量:废渣300万t、废砂近1 650万t、废气110亿m314若从2004年开始按照平均发展速度向前发展,可以预测至2020年各年的铸件产量。
铸造车间通风除尘设计说明

某车间除尘系统设计
目录第1章课程设计任务书.................................................. - 3 -第2章局部排风除尘系统的组成.................................... - 6 -2.1 集气罩 ................................................... 错误!未定义书签。
2.2 除尘设备 ............................................... 错误!未定义书签。
2.3 风机 ....................................................... 错误!未定义书签。
2.4风管 (8)2.5其他设备...................., (8)第3章除尘系统设计计算................................................ - 8 -3.1 集气罩的设计计算.......................................................... - 8 -3.1.1集气罩的集气原理 ............................... 错误!未定义书签。
3.1.2 集气罩的设计 ................................................................. - 8 -3.1.3 集气罩设计小结 ........................................................... - 10 -3.2管道的设计 ..................................................................... - 10 -3.2.1管道设计的原则 ............................................................ - 11 -3.2.2管道分段计算 ................................................................ - 11 -3.2.3并联管路压力平衡计算 ....................... 错误!未定义书签。
电炉 冲天炉铸造车间除尘设计方案
国内已有少数单位采用湿式或干式除尘装置治理化铁炉的烟尘污染,但效果不甚理想。
湿式除尘存在二次污染问题,而干式除尘则由于降温手段不可靠,多数仍处于停止运行状态。
因此,认真分析化铁炉烟气特点,有针对性地选择简易可靠的除尘方式是摆在我们通风除尘工作者面前的重要课题。
我公司承担了上海某机修总厂铸造车间通风除尘设计任务。
该工程建筑面积为6543m2,车间下分八个生产工部和一个炉料堆场。
3t/h 化铁炉系统单独作为一个除尘系统进行干式除尘设计,设计工程竣工投产以来系统调试运行正常,实测总除尘效率为99.4%。
1、化铁炉烟气特点(1)烟气温度高,波动范围大。
化铁炉正常工作时烟气温度一般为200℃~500℃之间。
但目前我国化铁炉多为人工控制上料,一旦上料不及时,烟气温度可达到600℃以上。
停炉前,瞬时温度可达900℃~1200℃,高温限制了治理手段的发挥。
因此,不论使用何种除尘方式,都要有一定的温度控制手段。
(2)烟气含尘大,粒级分布广,有一定数量大于1mm的尘粒,必须采用多级高效除尘方式。
对该厂化铁炉烟气含尘量测定为7g/Nm3~15g/Nm3。
(3)有一定的CO,一般含量为5%~21%必须注意防爆和逸出烟气危及生产岗位工人。
2、降温方案由于化铁炉正常烟气温度一般在200℃~500℃,进入布袋除尘器时会烧环布袋,因此保证布袋除尘器工作温度小于120℃,必须对烟气进行冷却。
以下是几种降温措施的比较。
(1)掺入自然风冷却。
这种方法简单可靠,但要将高温烟气冷却到120℃,掺入的自然风量太大,故这种冷却只能作为冷却设备的辅助措施。
(2)直接喷雾冷却。
这种方法热交换率高,较为经济。
但雾滴不完全蒸发时水滴会粘附管道,布袋除尘器会产生堵塞、结露和腐蚀。
(3)水冷套管冷却。
这种方法是利用辐射,但传热效率低,需要面积大,宜作为一种辅助设施。
(4)热交换冷却器冷却。
这种方法是利用辐射、对流的方式进行热交换,冷却介质有空气和水两种。
电炉铸造车间除尘系统方案设计
- 110 -生 态 与 环 境 工 程0 引言随着大家对于生活、工作的环境洁净要求日益提高,原工业厂房的生产生产方式进行污染物防控已成为关注重点。
工业灰尘是污染环境的重要污染物,是急需进行改造优化建设的核心内容。
积极有效的防尘系统建设可以有效地保护工人在此环境作业的安全性[1]。
在此以某电炉铸造车间的除尘系统方案为研究对象,就工厂除尘建设展开分析。
1 除尘系统方案1.1 项目背景该文以某铸造车间电炉除尘项目为研究对象展开。
在原先的铸造车间中,电炉的除尘作业主要是通过布袋除尘系统来加以除尘的,但在具体应用中,该类除尘系统仍然存在着诸多的问题难以解决。
1.2 问题分析此项目原配有一套处理风量为70 000 m 3/h 的布袋除尘系统,但原除尘系统在使用时,主要问题有6个。
1)在加料过程中产生的烟气无法捕集。
熔炼过程中需要加盖才能保证熔炼过程的烟气捕集。
2) 扒渣过程中产生的大量烟气无法捕集。
3)出铁水过程产生的大量烟气无法捕集。
4)2台熔化炉(8T)保温过程产生的烟气捕集效果差。
5)炉前球化过程中产生的烟气无法捕集。
6)兑铁水过程中产生的烟气无法捕集,此次系统升级主要是要解决这些问题。
1.3 设计思路该次设计是针对原除尘系统烟气捕集不好的环节进行低阻优化设计,主要采用集脉冲喷清灰吹布袋除尘器,可以有效地降低系统阻力损耗以及功流比,防止磨损及粉尘的沉积等。
在整个系统的设计中,通过特殊规格的移动的吸尘罩设置,可有效对电炉的球化、扒渣、保温和兑铁水等流程所产生的烟气进行有效收集,然后进入对应的除尘器,净化后的气体由除尘器排风口排出,最终排入大气[2]。
2 除尘系统改进方案此次电炉除尘系统改造主要包括4个方面。
1)拆除原来的布袋除尘系统,通过对该区域除尘需求分析计算,将利用现有的除尘区域新建一套布袋除尘系统,具体设计风量为20×104 m 3/h,过滤面积为3 400 m 2。
2)根据现在的设备布置方位,并结合改进生产工艺的情况,新建1套半密闭移动式捕集罩,2台熔化炉和2台保温炉共用。
铸造车间通风除尘课程设计计算书
铸 造 车 间 除 尘 系 统 计 算 书姓名:冯 震 学 号:0805791106 班 级:建 环 083 指导老师:程 向 东目录一、工程设计概况 (3)二、除尘系统的划分与管道设计的水力计算 (3)三、除尘设备与除尘风机的选择 (10)四、水力平衡计算 (12)五、方案的建议 (13)一、工程设计概况该工程为某铸造车间的除尘系统设计,厂房建筑面积为4606㎡,内空间高度为9m ,工作区域分为清理工部与砂处理工部。
其中清理工部布有4台橡胶履带抛丸清理机,每台排风量为5500m ³/h 。
砂处理工部布有3台鳄式破碎机,每台排风量为6000m ³/h ,一台金属履带抛丸清理机,排风量为8000m ³/h ,一台球铁破碎机,排风量为8500m ³/h 。
系统总的排风量为56500m ³/h 。
铸造车间清理工部、砂工部在生产状态下如果不进行控制,粉尘浓度可超过国家标准40~489倍,工人无法在此条件下生产。
国家卫生标准规定,含有10%以上2i O S 的粉尘为2mg /m ³,含有l0% 的2i O S 粉尘为l0mg /m ³。
二、除尘系统的划分与管道设计的水力计算A.除尘系统的划分该车间的清理工部与砂处理工部跨度不大,工作班次一致,要求的除尘设备在砂处理工部的区域内,考虑经济情况及以上因素,两个区域共一个系统。
整个系统除尘风机设定为一台,另选一台旋风除尘器和一台袋式除尘器。
B.管道设计的水力计算风速:由于车间空气中含有沙尘及型砂,故水平管道风速选定为17.5m/s ,垂直风管风速为16m/s 。
系统管路的布置见下图。
管段1:Q=5500m ³/h L=13.5m V=17.5m/s沿程阻力计算:管径333.0360045.011=⎪⎪⎭⎫⎝⎛=V Q D π 取管径为330mm ,则实际s V /m 8.161=查线算图得比摩阻101=R Pa/m 沿程阻力R=a 1355.1310P =⨯局部阻力计算:1中090弯头两个17.0=ζT 字型合流三通一个:5.0480340231=⎪⎭⎫ ⎝⎛=F F 5.0480340232=⎪⎭⎫⎝⎛=F F5.011000550032==Q Q 5.031=Q Q查表85.013=ζ 局部阻力()a 5.20128.162.185.017.02222P V H =⨯⨯+⨯=∑=ρζ管段1的总压损为1P =135+201.5=336.5Pa管段2:管段2的Q.V .D 同管段1,L=7.5m 沿程阻力R=a 75105.7P =⨯ 局部阻力:090弯头一个,T 字型合流三通一个93.076.017.0=+=∑ζ 局部阻力H=157.4Pa管段2的总压损为2P =157.4+75=232.4Pa 管段3:Q=11000m ³/h L=6m V=17.5m/s经计算2D 取480,则实际3V =16.8m/s 查线算图得比摩阻m P R /a 6.53= 沿程阻力R=a 6.336.56P =⨯局部阻力计算:管段3中T 字型合流三通一个68.0580480253=⎪⎭⎫⎝⎛=F F34.0580340254=⎪⎭⎫⎝⎛=F F 33.016500550054==Q Q 67.053=Q Q 查表49.035=ζ 局部阻力为H=90Pa管段3的总压损为3P =33.6+90=123.6Pa 管段4:管段4的沿程阻力同管段2 R=75Pa局部阻力:090弯头一个,T 字型合流三通一个1.193.017.0=+=∑ζ 局部阻力H=186.3Pa管段4的总压损为=4P 186.3+75=261.3Pa 管段5:Q=16500m ³/h V=18m/s L=6m/s 经计算5D =580mm 则实际流速5V =17.4m/s 查线算图得5R =4.5Pa/m 沿程阻力:R=65.4⨯=27Pa局部阻力计算:管段5中T 字型合流三通一个77.0660580275=⎪⎭⎫⎝⎛=F F25.0660330276=⎪⎭⎫⎝⎛=F F 75.0220001650075==Q Q 25.022*********==Q Q 查表24.057=ζ 局部阻力为H=43.6管段5的总压损为P=27+43.6=70.6Pa 管段6:管段6的沿程阻力同管段2 R=75Pa局部阻力:090弯头一个,T 字型合流三通一个62.045.017.0=+=∑ζ 局部阻力H=105Pa管段6的总压损为P=75+105=180Pa 管段7:Q=22000m ³/h L=14.7m V=17.5m/s 经计算mm 6607=D 则实际流速7V =17.8 查线算图得7R =4Pa/m 沿程阻力R=4⨯14.7=56.8Pa局部阻力计算:管段7中T 字型合流三通一个44.010006602177=⎪⎭⎫⎝⎛=F F69.0100082021716=⎪⎭⎫⎝⎛=F F 39.05650022000177==Q Q 61.056500345001716==Q Q 查表05.1717=ζ 局部阻力H=193管段7的总压损为P=56.8+193=249.8Pa 管段8:Q=8500m ³/h L=8.4m V=17.5m/s 经计算=8D 410mm 则实际流速为=8V 17.9m/s 查线算图得=8R 8.2Pa/m 沿程阻力为R=8.4⨯8.2=68.9Pa局部阻力:090弯头两个17.0=ζ T 字型合流三通一个58.05404102108=⎪⎭⎫ ⎝⎛=F F 4.05403402109=⎪⎭⎫⎝⎛=F F 59.0145008500108==Q Q 4.0145006000109==Q Q 查表=810ζ0.67 局部阻力H=()a 1949.176.067.017.02222P V =⨯⨯+⨯=∑ρζ管段8的总压损为P=68.9+194=262.9Pa经计算9D =340mm 则实际流速为18.4m/s 查线算图得9R =12.5Pa/m 沿程阻力R=3.415.123.3=⨯Pa局部阻力:管段9中090弯头一个,T 字型合流三通一个72.055.017.0=+=∑ζ局部阻力为H=146.2Pa管段9的总压损为P=41.3+146.2=187.5Pa 管段10:Q=14500m ³/h L=2m V=17.5m/s 经计算10D =540mm 则实际流速为17.6m/s 查线算图得10R =4.8Pa/m 沿程阻力R=28.4⨯=9.6Pa局部阻力:T 字型合流三通一个7.064054021210=⎪⎭⎫ ⎝⎛=F F 28.064034021211=⎪⎭⎫⎝⎛=F F71.020500145001210==Q Q 3.02050060001211==Q Q 查得ζ=0.5 局部阻力H=92.9Pa管段10的总压损为P=9.6+92.9=102.5Pa 管段11:管段11的沿程阻力同管9 R=41.3Pa局部阻力:管段11中090弯头一个,T 字型合流三通一个ζ∑=0.17+0.34=0.51局部阻力H=103.5管段11的总压损为P=41.3+103.5=144.8Pa经计算12D =640mm 则实际流速为17.7m/s 查线算图得12R =4.7Pa/m 沿程阻力R=27.4⨯=9.4Pa局部阻力:T 字型合流三通一个8.072064021412=⎪⎭⎫ ⎝⎛=F F 22.072034021413=⎪⎭⎫⎝⎛=F F77.026500205001412==Q Q 23.02650060001413==Q Q 查得ζ=0.27 局部阻力H=50.8Pa管段12的总压损为P=9.4+50.8=60.2Pa 管段13:沿程阻力同管段11 R=41.3Pa局部阻力:管段13中090弯头一个,T 字型合流三通一个ζ∑=0.17+0.15=0.32局部阻力H=65Pa管段13的总压损为P=41.3+65=106.3Pa 管段14:Q=26500m ³/h L=5.1m V=17.5m/s 经计算14D =720mm 则实际流速为18.1m/s 查线算图得14R =4.5Pa/m 沿程阻力R=1.55.4⨯=23Pa局部阻力:T 字型合流三通一个77.082072021614=⎪⎭⎫ ⎝⎛=F F 24.082040021615=⎪⎭⎫ ⎝⎛=F F77.034500265001614==Q Q 3.02650080001615==Q Q 查得ζ=0.27 局部阻力H=53.1Pa管段14的总压损为P=23+53.1=76.1Pa管段15:Q=8000m³/h L=6m V=17.5m/s经计算D=400mm 则实际流速为17.7m/s15查线算图得R=8.6Pa/m15沿程阻力R=66.8⨯=51.6Pa局部阻力:管段15中090弯头一个,T字型合流三通一个∑=0.17+0.67=0.84ζ局部阻力H=157.8Pa管段15的总压损为P=51.6+157.8=209.4Pa管段16:Q=34500m³/h L=6.2m V=17.5m/s经计算D=820mm 则实际流速为18.2m/s16查线算图得R=3.8Pa/m16沿程阻力R=2.68.3⨯=23.6Pa局部阻力:T字型合流三通一个ζ=1.1局部阻力H=218.6Pa管段16的总压损为P=23.6+218.6=242.2Pa管段17、18、19的计算方法同以上步骤,在此不一一祥列,经计算管段17的总压损为231Pa 管段18的总压损为64.9Pa 管段19的总压损为33Pa三、除尘设备与除尘风机的选择A.除尘设备的选择由于厂房的除尘量较大,故选用一台旋风式除尘器作为初级过滤见下表选择XTD--20的旋风除尘器,阻力为800Pa 再选用一台袋式除尘器作为二级除尘,见下图根据风量,选取DMC--420型号的除尘器,阻力为1000Pa B.除尘风机的选择通过以上计算,得出最不利环路1-3-5-7-17-18-19的总阻力为P=336.5+123.6+70.6+249.8+231+800+64.9+1000+33=2909.4Pa 总考虑富裕值,取P=2909.4 1.15=3345.8Pa总总风量为56500m³/h 如下图风机参数故选用型号为10D 转速为1450r/m 功率为55kw四、水力平衡计算A.先计算清理工部和砂处理工部的两支管清理工部的总阻力为Q P =5.7808.2496.706.1235.3367531=+++=+++P P P P 砂处理工部的总阻力为9.7432.2421.762.605.1029.262161412108=++++=++++=P P P P P P S 则5.7809.7435.780-=-S QS P P P =0.047=4.7%<15% 表明此两支路阻力平衡。
- 1、下载文档前请自行甄别文档内容的完整性,平台不提供额外的编辑、内容补充、找答案等附加服务。
- 2、"仅部分预览"的文档,不可在线预览部分如存在完整性等问题,可反馈申请退款(可完整预览的文档不适用该条件!)。
- 3、如文档侵犯您的权益,请联系客服反馈,我们会尽快为您处理(人工客服工作时间:9:00-18:30)。
1台
14 000
2台
14 000
烘干区 总风量 8 000
4台
4 000
1台
2 000
1台
2 000
1台
4 000
混砂区 总风量 8 000
1台
3 000
1台
2 500
1台
2 500
2台
4 000
清理区 总风量 9 000
2
8 000
1
1 000
持续时间/ min
40 (冶炼) 40 (冶炼) 烘干时间 烘干时间 烘干时间 烘干时间
2. 3 烘干工段
树脂型芯烘干后产生的废气中的有害物主要为有机化合 物 ,有恶臭气味 。各型芯烘干炉炉顶均配有一个排气孔 ,烘干 后的恶臭气体由排气孔排至处理系统 。考虑到炉内抽风会导 致炉内炉外气流对流加速 ,影响炉内烘干过程 ,甚至导致型芯 烘干不均匀 ,且治理对象炉体都有不同程度的漏气现象 ,选择 用半密闭法将烘干炉围封 ,风量定为 1 000 m3/ h。烘干炉排出 的气体温度大约为 120 - 170 ℃,自然抬升作用明显 ,同时为避 免对流带来的不利影响 ,控制风速不宜过高 ,本例选取 0. 3 m/ s。
表 1 风量分配
尘源
1. 5 t 电炉 0. 5 t 电炉
12 kW 烘干炉 15 kW 烘干炉 30 kW 烘干炉 81 kW 烘干炉
S225 型混砂机 110 kg 混砂机 60 kg 混砂机
耐火搅拌机
人工清理 颚式破碎机
数量 风量/ (m3·h - 1)
熔炼区 总风量 14 000
海 :同济大学出版社 ,2007. 844 - 846.
[2 ]谭天佑 ,梁凤珍. 工业通风除尘技术. 北京 :中国建筑工业出版社 ,
1984. 100 - 101.
作者简介 陈丽娟 ,女 ,1981 年生 ,硕士 ,主要从事钢铁行业大气污
染物治理工作 。
(收稿日期 :2009 - 01 - 08)
靠 。通过几十年的发展 ,袋式除尘技术已经能完全满足烟气
除尘稳定可靠运行的需要 。本次设计选用长袋低压脉冲袋
式除尘器 ,处理风量 24 200 m3/ h ,过滤风速 1. 15 m/ min ,脉冲
喷吹压力 0. 2 MPa ,排放质量浓度 ≤50 mg/ m3 。滤袋尺寸
130 mm ×6 000 mm ,滤料采用防油防水涤纶针刺毡 。配套风
砂较重 ,不易捕集 ;另一方面在于考虑操作人员因素 ,风速不
宜太高 ,以免操作人员感觉不适 。建议工作台可以在地坑上
设置格栅 ,地坑侧设置吸尘罩。这样在进行清理时较大的砂块
可以直接下落到地坑中 ,而其他的砂粒则通过吸尘罩排出。
参考文献
[1 ]许居 ,陆哲明 ,邝子强. 机械工业采暖通风与空调设计手册. 上
除尘系统 。
2 除尘罩的设计
集气吸尘罩是除尘系统中的重要组成部分 。设计合理 的吸尘罩能有效地捕集到污染气体 ,同时又能减小系统风 量 ,减少工程成本及除尘设备能耗 。
由于在本系统中涉及到多个工段 ,每个工段的生产设 备 、操作方式 、产生的污染物性质都不同 ,因此要综合考虑以 上各因素来设计除尘罩 。
5 结论
由于工作场地限制 ,采用折叠式收尘罩与低压长袋脉冲 袋式除尘器技术 ,来治理电弧炉粉尘取得成功 ,系统运行可 靠 ,治理效果良好 ,而且投资小 ,也未影响到原来的生产工艺 , 各项指标均达到了设计要求 。
参考文献 [1 ]国家环保局. 钢铁工业废气治理. 北京 :中国环境科学出版社 ,1992. [2 ]张殿印 ,王纯. 除尘器手册. 北京 :化学工业出版社 ,2005. [3 ]郝吉明 ,马广大. 大气污染控制工程. 第 2 版. 北京 :高等教育出版
所需电动机的功率 N 根据相关公式[3] 计算 , 经计算得 N = 34. 9 kW。
根据上述计算结果选用的离心风机为 4 - 72 - №8C , 风 量为 32 400 m3/ h ,全风压为 2 579 Pa , 配用电机 Y255M - 28 型 , 转数 1 800 r/ min ,电机功率 45 kW。
2. 1 熔炼工段
1 变径管 ;2 挡板 ;3 除尘器本体 ;4 灰斗
图 3 惯性除尘器结构示意
引风机风量的确定根据相关公式[3] 计算并考虑系统漏 风因素 ,经计算风量约为 31 000 m3/ h。
引风机风压 Δp0 的确定根据相关公式[3]计算 ,经计算得 风压 Δp0 = 2 496. 8 Pa 。
系统投入使用后 ,厂房内的环境得到了极大改善 。但烘
干炉的半密闭罩仅能控制炉门密闭时的恶臭气体 ,当打开炉
门时 ,部分炉内气体溢出 。建议可在炉门上方设一顶吸罩 ,
罩口为扁长形 ,以免影响炉前操作 ,罩口风速适当取大 。同
时采取措施保持罩口风速的均匀 。
人工清理工段 ,除尘效果不是十分明显 。一方面在于落
Design of Cleaning System in a Small - size Foundry CHEN Li - juan ZHAO Li - dong
( Sinosteel Tiancheng Environmental Protection Science & Technology Co. , Ltd. Wuhan 430079) Abstract Based on the characteristics of foundry pollution , such as the diversity of producing equipment and the pollutants , and no firm processing system , this paper introduces the design of the cleaning system , including the design of cleaning hood ,pipe system , equipment se2 lection , and so on. Finally some improvements are given. Keywords foundry dust cleaning system cleaning hood pipe
机 9 - 26 - 11 - №12. 5D - 3 型 , 全 压 4 109 Pa , 电 机 型 号
Y280S - 6 ,功率 45 kW。
由于厂区地处北方 ,冬季最低日平均温度达到 - 25. 2
℃。为保证喷吹压缩空气的洁净 ,在设置空压系统时 ,同时
配备了空气冷干机及过滤器等 。
5 改进意见
电炉不同时工作 ,烘干区或者 4 台 12 kW 砂芯烘干炉 、 15 kW 与 30 kW 砂芯烘干炉三者一同工作 ,或者 4 台 12 kW 砂芯烘干炉与 81 kW 砂芯烘干炉二者一同工作 。
基于以上因素 ,设计时将熔炼区管道作为第 1 级主管 道 ,而其他 3 个除尘区管道并列作为第 2 级主管道 ,在各支 路管道上设置风量调节阀 。
2. 4 清理工段
清理区主要污染物为铸件上清理下来的落砂 。污染物 密度较大 ,上升和扩散速度较小 ,同时鉴于是手工清理 ,因此 采用了工作台上侧吸罩的形式 。操作人员离罩口距离约为 200 mm ,控制风速约为 1 m/ s ,罩口尺寸及风量选取可根据方 形罩口速度分布图来设计[2] 。
3 工艺管道的设计
2. 2 混砂工段
混砂机混制的是树脂型 (芯) 砂 ,产生的有害物主要有粉 尘(少量) 、CO、NH3 、HCN 气体 。在此采用了半密闭罩将贮砂 罐下料口及混砂机围封起来的方式 ,在一面开口留出工人操 作及观察空间 。排风口风速控制在 2 m/ s 左右 ,既保证罩内 一定负压又避免抽走物料 。
4 烟气净化系统运行效果
该工程自 2006 年末竣工以来 ,系统运行良好 ,原来“红
烟”滚滚的场景已不存在 ,车间工作环境得到较大的改善 。经 当地环保部门监测 ,烟气排放粉尘质量浓度为 10 - 25 mg/ m3 , 岗位粉尘质量浓度为 5 - 10 mg/ m3 ,均达到国家排放标准 ,整 个系统的除尘效率在 99 %以上 ,各项指标均符合设计要求 。 同时原来粉尘污染源经治理收集后变废为宝 ,取得一定经济 效益 ,达到了生产 、经济 、环境和谐统一 。
每周 1 - 3 次 , 每次 30 min 不定 8. 30 - 9. 00
由于设备开启的不确定性 ,会造成汇合后管内风量上
下波动较大 ,故应根据最经常使用设备来确定管径 ,以使管
内风速在适合范围 (14 - 22 m/ s) 之内 。现场运行情况来看 ,
效果不错 。
4 设备选型
袋式除尘器效率高 ,阻力小 ,维护简单 ,设备运行稳定可
2009 年第 June 2009
35
卷第
6
期
I ndu str ial S工afe业ty安an全d 与Env环iro保nmental
Protection
·11 ·
某小型铸造车间除尘系统设计
陈丽娟 赵立冬
(中钢集团天澄环保科技股份有限公司 武汉 430079)
摘 要 针对小型铸造车间中污染源的产生设备多种 、污染物性质多样以及整个车间中工艺操作无固定工作制等特 点 ,介绍了除尘系统的设计 ,包括各生产设备上除尘罩 、工艺管道及设备选型等 ,最后提出了可进一步改进的意见 。 关键词 铸造车间 除尘系统 除尘罩 管道
此次设计包括除尘点共 20 个 。由于铸造工艺流程的不 确定性 ,故在除尘设计时将厂区除尘点划分为 4 个主要区 域 :熔炼区 、烘干区 、混砂区及清理区 ,如图 1 所示 。
图 1 除尘系统
根据车间人员反映 ,车间内最主要的产尘点为熔炼区 , 产尘量大 ,持续时间长 。而其他 3 个区产尘小 ,时间短 ,且设 备开启台数 、何台开启依据当日生产计划确定 ,无操作规律 。 鉴于此 ,整个系统的风量可考虑为熔炼区与其他 3 个区中最 大区风量之和 。这样既可保证各点的除尘效果 ,可以节约成 本 。风量分配见表 1 。