传动效率实验
减速器传动效率的测定实验报告

减速器传动效率的测定实验报告实验目的:通过测定减速器传动效率,了解减速器的工作性能和性能指标。
实验原理:减速器是将动力源的转速降低并增加扭矩的装置。
减速器的传动效率是指在运行过程中,减速器所能输出的实际功率与输入的实际功率之比。
传动效率由于摩擦、传动间隙等因素的存在而不为100%,通常在80%-95%之间。
实验仪器:1. 减速器实验台2. 电机3. 力传感器4. 轴功率测量仪实验步骤:1. 将电机与减速器实验台连接,并将功率传感器固定在减速器输出端。
2. 打开电源,启动电机,使其开始运转。
3. 通过轴功率测量仪测量电机输入功率和减速器输出功率,并记录读数。
4. 根据所测得的数据,计算减速器的传动效率。
实验数据记录与计算:1. 电机输入功率:P1=XXX W;2. 减速器输出功率:P2=XXX W;3. 传动效率:η = (P2/P1) × 100%。
实验结果与分析:根据实验数据计算得到的传动效率为XXX%。
传动效率的大小可以反映减速器的传动性能和能量损失程度。
通过观察传动效率的变化,可以判断减速器的工作状态和性能。
可能的实验误差与改进方法:1. 传感器的精度误差:选择更精确的传感器进行测量。
2. 实验操作误差:在进行实验时,加强实验操作的规范性和准确性。
3. 环境因素的影响:在实验过程中,尽量控制环境因素对实验结果的影响。
结论:减速器传动效率是减速器工作性能的重要指标,可以通过实验测定来了解减速器的传动效率。
在实验中我们得到了减速器传动效率为XXX%。
通过对传动效率的观察和分析,可以判断减速器的工作状态和性能,并且对于减速器的设计和选用具有重要的指导意义。
带传动及齿轮传动效率实验
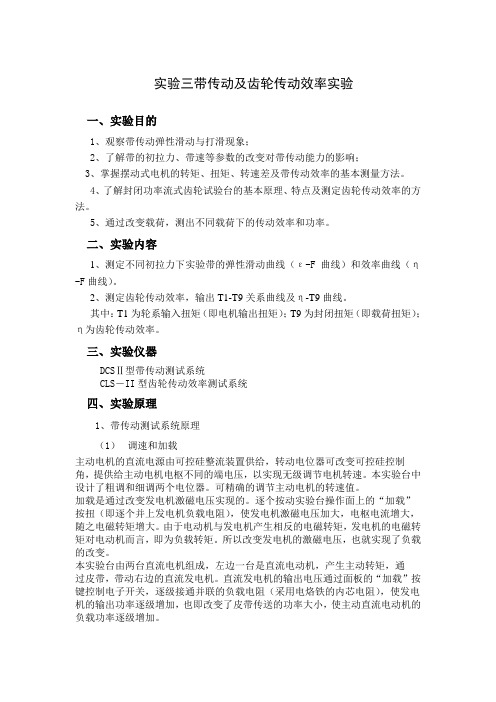
实验三带传动及齿轮传动效率实验一、实验目的1、观察带传动弹性滑动与打滑现象;2、了解带的初拉力、带速等参数的改变对带传动能力的影响;3、掌握摆动式电机的转矩、扭矩、转速差及带传动效率的基本测量方法。
4、了解封闭功率流式齿轮试验台的基本原理、特点及测定齿轮传动效率的方法。
5、通过改变载荷,测出不同载荷下的传动效率和功率。
二、实验内容1、测定不同初拉力下实验带的弹性滑动曲线(ε-F曲线)和效率曲线(η-F曲线)。
2、测定齿轮传动效率,输出T1-T9关系曲线及η-T9曲线。
其中:T1为轮系输入扭矩(即电机输出扭矩);T9为封闭扭矩(即载荷扭矩);η为齿轮传动效率。
三、实验仪器DCSⅡ型带传动测试系统CLS-II型齿轮传动效率测试系统四、实验原理1、带传动测试系统原理(1)调速和加载主动电机的直流电源由可控硅整流装置供给,转动电位器可改变可控硅控制角,提供给主动电机电枢不同的端电压,以实现无级调节电机转速。
本实验台中设计了粗调和细调两个电位器。
可精确的调节主动电机的转速值。
加载是通过改变发电机激磁电压实现的。
逐个按动实验台操作面上的“加载”按扭(即逐个并上发电机负载电阻),使发电机激磁电压加大,电枢电流增大,随之电磁转矩增大。
由于电动机与发电机产生相反的电磁转矩,发电机的电磁转矩对电动机而言,即为负载转矩。
所以改变发电机的激磁电压,也就实现了负载的改变。
本实验台由两台直流电机组成,左边一台是直流电动机,产生主动转矩,通过皮带,带动右边的直流发电机。
直流发电机的输出电压通过面板的“加载”按键控制电子开关,逐级接通并联的负载电阻(采用电烙铁的内芯电阻),使发电机的输出功率逐级增加,也即改变了皮带传送的功率大小,使主动直流电动机的负载功率逐级增加。
图1直流发电机加载示意图(2)转速测量两台电机的转速,分别由安装在实验台两电机带轮背后环形槽中的红外交电传感器上测出。
带轮上开有光栅槽,由光电传感器将其角位移信号转换为电脉冲输入单片计算机中计数,计算得到两电机的动态转速值,并由实验台上的LED 显示器显示上来也可通过微机接口送往PC机进一步处理。
5蜗杆传动效率实验
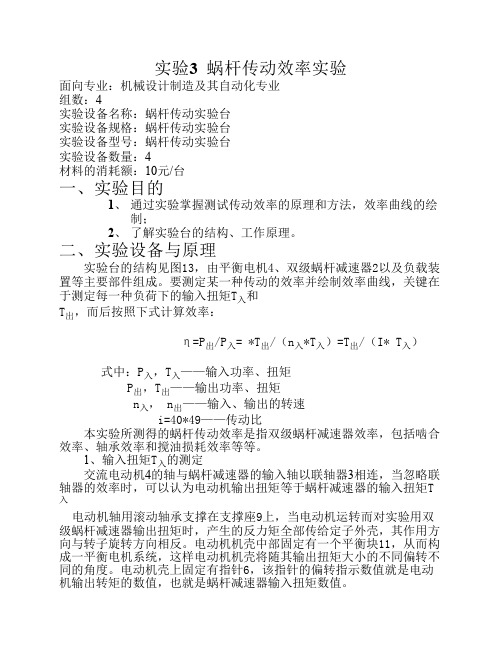
五、思考题
1、 叙述本实验输入扭矩的测定装置。 2、 请你另设计一套输出扭矩的测定方法。 3、 绘出两级蜗杆减速器的传动简图。 4、 影响蜗杆传动效率的因素有哪些?
2、输出扭矩T出的测定 蜗杆减速器2的输出端固定有一主绳轮1,上面其上绕有绳子,并经 转向后悬挂着负载架18。负载架上可加砝码,其累计总量G为负载总 重。故输出扭矩为:
T出=G*D/2=9.8*(100/1000)*G/2≈0.5G N.m 式中:D——主绳轮直径100mm
G——负载架和砝码重量(每个砝码重2.5Kg)之和算累计总 重。
本实验所测得的蜗杆传动效率是指双级蜗杆减速器效率,包括啮合 效率、轴承效率和搅油损耗效率等等。
1、输入扭矩T入的测定 交流电动机4的轴与蜗杆减速器的输入轴以联轴器3相连,当忽略联 轴器的效率时,可以认为电动机输出扭矩等于蜗杆减速器的输入扭矩T
入
电动机轴用滚动轴承支撑在支撑座9上,当电动机运转而对实验用双 级蜗杆减速器输出扭矩时,产生的反力矩全部传给定子外壳,其作用方 向与转子旋转方向相反。电动机机壳中部固定有一个平衡块11,从而构 成一平衡电机系统,这样电动机机壳将随其输出扭矩大小的不同偏转不 同的角度。电动机壳上固定有指针6,该指针的偏转指示数值就是电动 机输出转矩的数值,也就是蜗杆减速器输入扭矩数值。
二、实验设备与原理
实验台的结构见图13,由平衡电机4、双级蜗杆减速器2以及负载装 置等主要部件组成。要测定某一种传动的效率并绘制效率曲线,关键在 于测定每一种负荷下的输入扭矩T入和 T出,而后按照下式计算效率:
实验二齿轮传动效率测试实验指导书
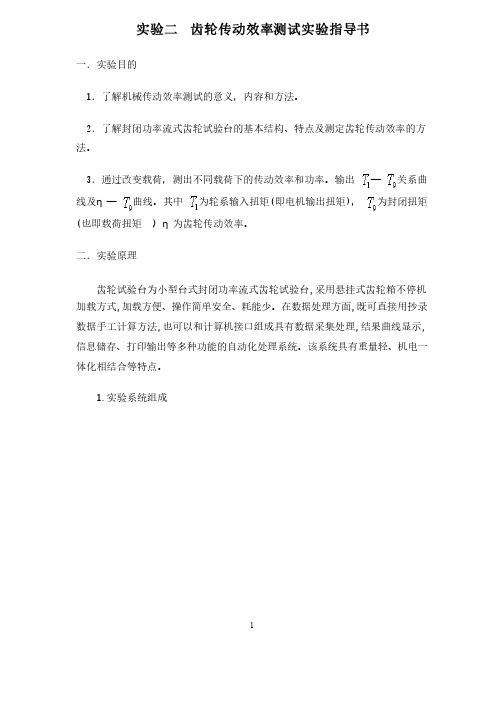
1实验二 齿轮传动效率测试实验指导书一.实验目的一.实验目的1.了解机械传动效率测试的意义,内容和方法。
.了解机械传动效率测试的意义,内容和方法。
2.了解封闭功率流式齿轮试验台的基本结构、特点及测定齿轮传动效率的方法。
法。
3.通过改变载荷,测出不同载荷下的传动效率和功率。
输出 — 关系曲线及η— 曲线。
其中 为轮系输入扭矩为轮系输入扭矩((即电机输出扭矩即电机输出扭矩)), 为封闭扭矩(也即载荷扭矩也即载荷扭矩 ) ),η为齿轮传动效率。
为齿轮传动效率。
二.实验原理二.实验原理齿轮试验台为小型台式封闭功率流式齿轮试验台齿轮试验台为小型台式封闭功率流式齿轮试验台,,采用悬挂式齿轮箱不停机加载方式加载方式,,加载方便、操作简单安全、耗能少。
在数据处理方面加载方便、操作简单安全、耗能少。
在数据处理方面,,既可直接用抄录数据手工计算方法数据手工计算方法,,也可以和计算机接口组成具有数据采集处理也可以和计算机接口组成具有数据采集处理,,结果曲线显示结果曲线显示,,信息储存、打印输出等多种功能的自动化处理系统。
该系统具有重量轻、信息储存、打印输出等多种功能的自动化处理系统。
该系统具有重量轻、机电一机电一体化相结合等特点。
体化相结合等特点。
1.1.实验系统组成实验系统组成实验系统组成图 1 实验系统框图实验系统框图实验系统框图 2.2.实验台结构实验台结构实验台结构试验台的结构示意图如图2所示,由定轴齿轮副、悬挂齿轮箱、扭力轴、双万向连轴器等组成一个封闭机械系统。
万向连轴器等组成一个封闭机械系统。
图 2齿轮实验台结构简图齿轮实验台结构简图1.1.悬挂电机悬挂电机悬挂电机 2 . 2 .转矩传感器转矩传感器 3. 3.浮动连轴器浮动连轴器 4. 4.霍耳传感器霍耳传感器 5. 5.定轴齿轮副定轴齿轮副 6.6.刚性连轴器刚性连轴器刚性连轴器 7. 7.悬挂齿轮箱悬挂齿轮箱 8. 8.砝码砝码 9. 9.悬挂齿轮副悬挂齿轮副 10. 10.扭力轴扭力轴 11. 11.万向连轴器连轴器 12. 12.永久磁钢永久磁钢电机采用外壳悬挂结构,通过浮动连轴器和齿轮相连电机采用外壳悬挂结构,通过浮动连轴器和齿轮相连,,与电机悬臂相连的转矩传感器把电机转矩信号送入实验台电测箱,在数码显示器上直接读出。
封闭功率流式齿轮传动效率测定实验

实验三 封闭功率流式齿轮传动效率测定实验一实验目的1、了解封闭功率流式齿轮试验台的基本原理、特点和测定齿轮传动效率的方法.2、测定齿轮传动功率和效率.二试验台结构及工作原理.1、试验台结构图1如图1所示,齿轮固连于刚性轴A 的两端,齿轮b 套在弹性轴B 外,齿轮C固连于弹性轴B 的左端,电机采用外壳悬挂装置,并通过齿轮、齿条机构和传感器6获得电机输出力矩, 其结构见图4.封闭力矩的施加通过手轮7和螺旋槽加载器5获取. 加载器件5的结构见图2 所示,加载时,转动手轮7,使端头螺杆7’旋转,推动加载器的螺母套5直线左移并通过推力轴承4,使加载套3同样左移, 加载套的左移,一方面使固定于其上的销轴滚轮组2沿固定于齿轮b 上的螺旋槽套1中的槽滑移,另一方面, 加载套3弹性轴端头上的键滑移,滑移结果使得弹性轴产生相对扭转变形,从而对齿轮产生了加载力.加载力的情况如图例 3所示. F=轴向力N 由加载手轮7的螺杆7’产生.R=圆周力 β=斜槽螺旋角=15;r=d/2=16mm 螺旋槽套1的半径由图知 βtg F R =则所施加的封闭力矩为).(1000mm N tg rF T B ⋅⨯=βF 值的确定,通过传感器6的位移量转换成电量确定电机的输出力矩:).(10008.91m N T L T ⨯⨯=式中L---电机外壳齿轮的节圆半径=mm, T---弹簧反力kg本装置通过应用电机转角变化的机械量转换成电量的变化,再经放大整形电路直接由数码显示、电机的输出为力矩;其结构见图4;2、封闭加载原理封闭功率流式齿轮试验台,主要是通过装置系统中的一个特殊部件来加载,用以获得为平衡此弹性件的变形而产生的内力矩封闭力矩,运转时,这内力矩相应作功而成为封闭功率,并在此封闭回路中按一定方向流动;a 与b 和c 与d 为两对具有相同速比和中心距A 的圆柱齿轮传动,并如图1所示构成了一个封闭的机械系统;系统中当螺旋槽加载器不加载时处在松开的位置,此时控制箱中的转矩显示在“0000”位置;当加载时,加载套左移,使得弹性轴产生相对扭转变形-即内力矩封闭力矩,从而对左右两对齿轮产生了加载力,各传动元件运转时相应作功,此功率在封闭系统中按一定的方向流动,并在流动过程中不断循环;在这种情况下,由于载荷已体现为系统的内力,因此电机提供的动力,主要用于克服此系统中各传动件的摩擦阻力,其能耗远远小于开式的实验装置,因而可大大减小电机容量;3.效率的测定先判明齿轮的主动、从动关系,以及功率的流动方向;根据图2的加载方向,以及齿轮的啮合情况和电机的转动方向,由图5可看出,齿轮a 为主动,a 推动b,c 推动d,其功率按a d c b →→→方向流动;而当电动机的回转方向相反时,齿轮d 为主动,c 为从动,功率流向也相反,因而,对于封闭试验台,可以根据加载力矩的方向和电动机转向来判明齿轮是主动或从动;图5中,①、②、③分别表示电动机的功率在循环过程中消耗于齿轮、轴承、联轴节等的损耗;在测定及计算效率时,常将功率转化为扭矩,并取:1电机的输出功率时P 1 ,完全消耗于克服封闭系统的摩擦损耗,即P 1=P 5; 2取两对齿轮的效率ηηηη,==--d c b a 为平均效率当齿轮a 主动时,功率由a 流向d,由于轮d 为封闭功率流的末端输出端,则 :B i P P = ---封闭功率对于齿轮:或dc Bc T T -=η对于齿轮:a d c B a c ab b a T T T T T T --===∴ηη或dc b a Ba T T --=ηη 由于封闭功率的始端与末端的功率之差即为该系统的摩擦损耗,也就是电动机的输出功率P 1,因此从平衡电机可直接测出输出扭矩T 1,则:或1T T T B Bd c b a +=--ηη 则平均效率为1T T T B Bd c b a +==--ηηη 当齿轮d 为主动时,功率流反向,变为a b c d →→→,齿轮a 为功率流的末端,b a T T =,此时,封闭功率大于传出功率,则电机供给的摩擦功率为:或)1(21η-=B T T 则BB T T T 1-=η 由效率公式看出,只要能实际测出电机的输出扭矩及施加的封闭力矩即能测定该封闭传动装置的效率;三实验步骤:1、开启电源前先用手检查齿轮传动是否轻松,力矩输出电位器是否在原始位置;2、开启电源,指示灯亮,检查数码管是否是在“0000”位置;3、顺时针缓慢调节调速旋扭,使齿轮转速达到一适当值;一般小于1000 rpm ;4、记录第一组T 1、T B 值,T 1、T B 值通过控制箱显示面板按扭得到;5、反时针转动加载手轮7一次,施加封闭力矩后,记录第二组T 1、T B 值;6、重复转动手轮,再记录第三组,第四组….第十组T 1、T B 值,施加封闭力矩m ax B T 不宜过大,以免负荷过重损坏元件,一般m ax B T =7、顺时针转动手轮卸去载荷,使转矩T B 显示码处在最小位置; 8、降低转速至齿轮停止转动,转速显示码处在“0000”值; 9、关闭电源; 10.根据1+=B BT T η即可绘制出该齿轮传动的效率曲线. 11、如果时间有余,选做下列两种情况下的一种,并绘制曲线; 1、保持一定转速n 基本一致改变T B ,可绘制效率曲线T B --η曲线;2、在一定的T B 情况下,从低速到高速约300rpm —1100rpm 改变n,可绘制n-η曲 线;四注意事项1、 由于齿轮传动敞开,务必注意安全,当心衣帽发辨轧入齿轮;2、 调节转速时,必须缓慢进行,逐渐提高转速,以免形成冲进损坏传动元件及传感器;3、试验完后,须先卸载后停止转动;。
传动效率实验
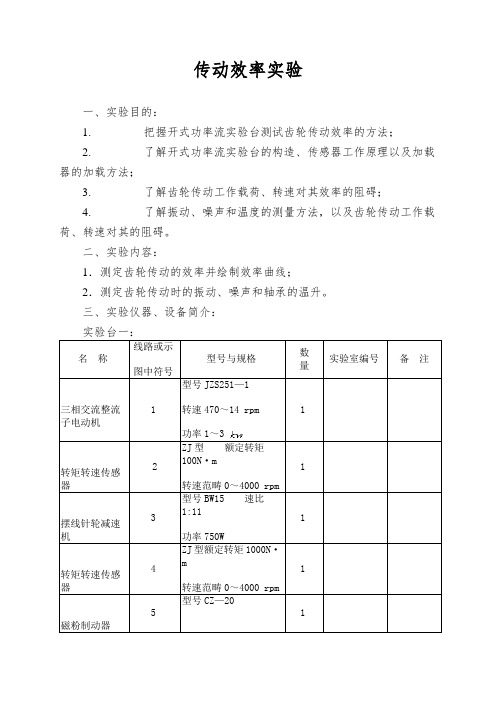
传动效率实验一、实验目的:1.把握开式功率流实验台测试齿轮传动效率的方法;2.了解开式功率流实验台的构造、传感器工作原理以及加载器的加载方法;3.了解齿轮传动工作载荷、转速对其效率的阻碍;4.了解振动、噪声和温度的测量方法,以及齿轮传动工作载荷、转速对其的阻碍。
二、实验内容:1.测定齿轮传动的效率并绘制效率曲线;2.测定齿轮传动时的振动、噪声和轴承的温升。
三、实验仪器、设备简介:实验台一:名称线路或示图中符号型号与规格数量实验室编号备注三相交流整流子电动机1型号JZS251—1转速470~14 rpm功率1~31转矩转速传感器2ZJ型额定转矩100N·m转速范畴0~4000 rpm1摆线针轮减速机3型号BW15 速比1:11功率750W1转矩转速传感器4ZJ型额定转矩1000N·m转速范畴0~4000 rpm1磁粉制动器5型号CZ—201实验台二:效率仪6 MTEM-1 1可调直流稳压、稳流电源5,型号DF1701SB/SC输出电压32V 输出电流3A1便携式红外温度计WFHX-68 1声级计HS5660A 1四、实验用详细线路图或其他示意图:图1实验台一简图图2实验台二简图图3转矩传感器工作原理图图4磁粉制动器工作原理示意图五、实验有关原理及原始运算数据,所应用的公式1.实验台的组成实验台一简图如图1 所示, 三相交流整流子电动机1 通过转矩转速传感器2与摆线针轮减速机3的输入轴相连,减速器3的输出轴再通过转矩转速传感器4与磁粉制动器5相连。
转矩转速传感器(2,4)与转矩转速测量仪5 '相配套。
实验台二由电磁调速电动机1通过转矩转速传感器2与三减速器3的输入轴相连, 减速器3的输出轴再通过转矩转速传感器4与磁粉制动器5相连。
转矩转速传感器(2,4)与效率仪6相连。
2. 实验原理交流整流子电动机(或电磁调速电动机)作为运动和动力的输入部分,其转速能够在一定范畴内调整:磁粉制动器作为加载器, 由稳流电源改变激磁电流大小,以获得不同的负载力矩:输入输出的转矩转速可由转矩转速传感器通过转矩转速仪(或效率仪)测得:如此就能够测出不同工况下齿轮箱的传动效率。
典型减速器传动效率的测定实验步骤
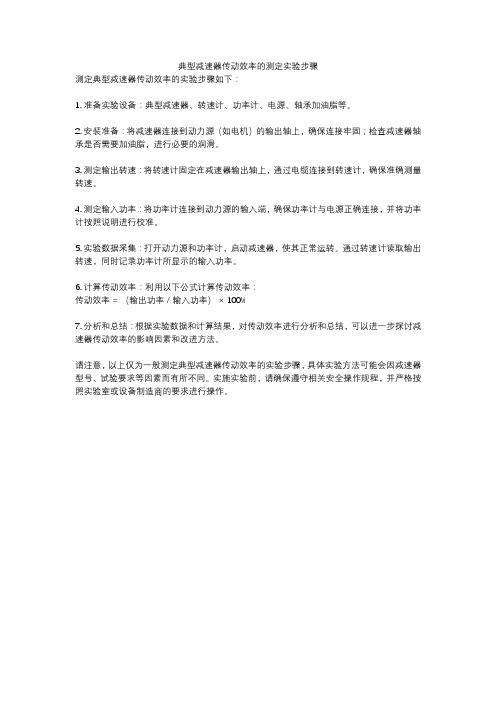
典型减速器传动效率的测定实验步骤
测定典型减速器传动效率的实验步骤如下:
1. 准备实验设备:典型减速器、转速计、功率计、电源、轴承加油脂等。
2. 安装准备:将减速器连接到动力源(如电机)的输出轴上,确保连接牢固;检查减速器轴承是否需要加油脂,进行必要的润滑。
3. 测定输出转速:将转速计固定在减速器输出轴上,通过电缆连接到转速计,确保准确测量转速。
4. 测定输入功率:将功率计连接到动力源的输入端,确保功率计与电源正确连接,并将功率计按照说明进行校准。
5. 实验数据采集:打开动力源和功率计,启动减速器,使其正常运转。
通过转速计读取输出转速,同时记录功率计所显示的输入功率。
6. 计算传动效率:利用以下公式计算传动效率:
传动效率 = (输出功率 / 输入功率)× 100%
7. 分析和总结:根据实验数据和计算结果,对传动效率进行分析和总结,可以进一步探讨减速器传动效率的影响因素和改进方法。
请注意,以上仅为一般测定典型减速器传动效率的实验步骤,具体实验方法可能会因减速器型号、试验要求等因素而有所不同。
实施实验前,请确保遵守相关安全操作规程,并严格按照实验室或设备制造商的要求进行操作。
实验五齿轮传动效率实验
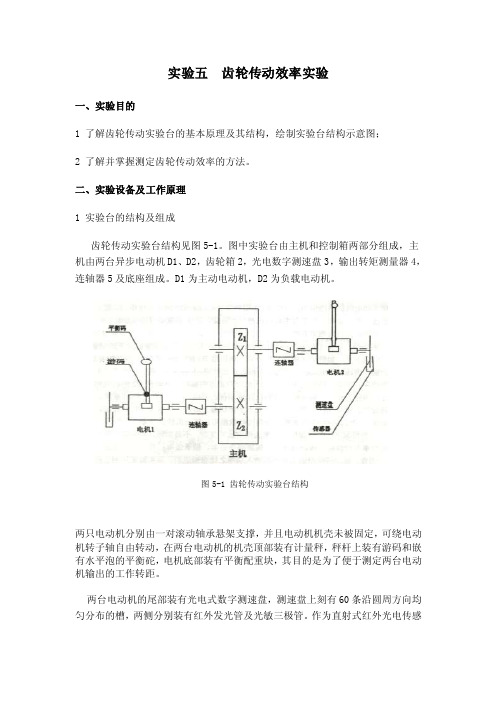
实验五齿轮传动效率实验一、实验目的1 了解齿轮传动实验台的基本原理及其结构,绘制实验台结构示意图;2 了解并掌握测定齿轮传动效率的方法。
二、实验设备及工作原理1 实验台的结构及组成齿轮传动实验台结构见图5-1。
图中实验台由主机和控制箱两部分组成,主机由两台异步电动机D1、D2,齿轮箱2,光电数字测速盘3,输出转矩测量器4,连轴器5及底座组成。
D1为主动电动机,D2为负载电动机。
图5-1 齿轮传动实验台结构两只电动机分别由一对滚动轴承悬架支撑,并且电动机机壳未被固定,可绕电动机转子轴自由转动,在两台电动机的机壳顶部装有计量秤,秤杆上装有游码和嵌有水平泡的平衡砣,电机底部装有平衡配重块,其目的是为了便于测定两台电动机输出的工作转距。
两台电动机的尾部装有光电式数字测速盘,测速盘上刻有60条沿圆周方向均匀分布的槽,两侧分别装有红外发光管及光敏三极管。
作为直射式红外光电传感器,测速盘每旋转一周,发出60个脉冲信号给计数器,计数器每一秒采样一次来读取计数,分别显示于控制箱上的转速表上,便于实验人员记录。
控制箱上(图5-2)分别装有两台电机输入电压的调压器B1、B2,以及电压表V1、V2,电流表A1、A2,转速表N1、N2、及启动、停止按钮.(注:下标为1的均为主动电机1的相关数据及控制,下标为2的均为从动电机2的相关数据及控制。
具体数据在实验时按控制箱实际标志而定。
)2 实验台基本工作原理两台同型号的异步电动机分别通过三相调压器并联接入电网,他们的电气参数一致。
实验台在设计时已令两台电动机的转向相反,齿轮箱内与主动电动机连接的主动齿轮Z1的齿数大于与从动电机连接的从动齿轮Z2的齿数。
这样当主动电动机工作在其同步转速n1时,从动电机的转速n2因为主动齿轮的齿数Z1大于从动齿轮齿数Z2,而使从动电动机D2的转数n2大于主动电动机D1的同步转数n1,由于两台异步电动机的型号是一样的,所以它们的同步转速是一样的,因此,当n2>n1时(此时n1为两台电动机的同步转速),从动电动机的实际转速n2是大于其自身的同步转数n1的,从而使从动电动机D2必然产生一个反向输入力矩,从而实现给电动机D1的加载。
- 1、下载文档前请自行甄别文档内容的完整性,平台不提供额外的编辑、内容补充、找答案等附加服务。
- 2、"仅部分预览"的文档,不可在线预览部分如存在完整性等问题,可反馈申请退款(可完整预览的文档不适用该条件!)。
- 3、如文档侵犯您的权益,请联系客服反馈,我们会尽快为您处理(人工客服工作时间:9:00-18:30)。
传动效率实验
一、实验目的:
1.把握开式功率流实验台测试齿轮传动效率的方法;
2.了解开式功率流实验台的构造、传感器工作原理以及加载器的加载方法;
3.了解齿轮传动工作载荷、转速对其效率的阻碍;
4.了解振动、噪声和温度的测量方法,以及齿轮传动工作载荷、转速对其的阻碍。
二、实验内容:
1.测定齿轮传动的效率并绘制效率曲线;
2.测定齿轮传动时的振动、噪声和轴承的温升。
三、实验仪器、设备简介:
实验台一:
名称
线路或示
图中符号型号与规格
数
量
实验室编号备注
三相交流整流子电动机1
型号JZS251—1
转速470~14 rpm
功率1~3
1
转矩转速传感器2
ZJ型额定转矩
100N·m
转速范畴0~4000 rpm
1
摆线针轮减速机3
型号BW15 速比
1:11
功率750W
1
转矩转速传感器4
ZJ型额定转矩1000N·
m
转速范畴0~4000 rpm
1
磁粉制动器5
型号CZ—20
1
实验台二:
效率仪
6 MTEM-1 1
可调直流稳压、稳流电源5,
型号DF1701SB/SC
输出电压32V 输出电
流3A
1
便携式红外温
度计
WFHX-68 1
声级计HS5660A 1
四、实验用详细线路图或其他示意图:
图1实验台一简图
图2实验台二简图
图3转矩传感器工作原理图
图4磁粉制动器工作原理示意图
五、实验有关原理及原始运算数据,所应用的公式
1.实验台的组成
实验台一简图如图1 所示, 三相交流整流子电动机1 通过转矩转速传感器2与摆线针轮减速机3的输入轴相连,减速器3的输出轴再通过转矩转速传感器4与磁粉制动器5相连。
转矩转速传感器(2,4)与转矩转速测量仪5 '相配套。
实验台二由电磁调速电动机1通过转矩转速传感器2与三减速器3的输入轴相连, 减速器3的输出轴再通过转矩转速传感器4与磁粉制动器5相连。
转矩转速传感器(2,4)与效率仪6相连。
2. 实验原理
交流整流子电动机(或电磁调速电动机)作为运动和动力的输入部分,
其转速能够在一定范畴内调整:磁粉制动器作为加载器, 由稳流电源改变激磁电流大小,以获得不同的负载力矩:输入输出的转矩转速可由转矩转速传感器通过转矩转速仪(或效率仪)测得:如此就能够测出不同工况下齿轮箱的传动效率。
ZJ 型转矩转速传感器的工作原理如图2 所示, 在弹性轴两端固定有两个外齿轮,内齿轮、磁钢固定在外壳上,磁钢上绕有信号线圈。
当内外齿轮发生相对转动时,由于磁通量持续变化,在线圈中便感应出近似正弦波的感应电动势, 两感应电动势在外加转矩为零时的初始相位差是恒定的,当加上转矩后弹性轴产生扭转变形,在弹性范畴内外加转矩与机械扭转角成正比, 这时两感应电动势的相位差要发生变化,其绝对值与外加转矩成正比。
因此,就能够利用测量相位差的方法来测量转矩。
磁粉制动器工作原理如图4所示。
1为旋转的圆柱形转子;2为定子;3为激磁线圈:4为圆柱形转子上的隔磁环:5为磁粉;6为定子冷腔。
当激磁线圈加上某一直流电压时,线圈内产生激磁电流,此电流流经线圈后形成了如图中虚线所示的闭合磁场,在磁场作用下工作间隙中的摩擦力产生制动力矩。
磁粉制动器所消耗的功率变成热能由冷却水冷却达到平稳。
3. 操作步骤
(1)按图检查电动机、ZJ转矩转速传感器、被测齿轮箱、磁粉制动器的联接,用手检查齿轮及电动机的转动是否轻巧。
(2)接上转矩转速仪( 或效率仪)、稳流电源、冷却水管,检查各仪器的接线是否完整、正确。
开启电源, 指示灯亮, 检查各仪器是否正常, 确认稳流电源的输出电流为零。
(3)接上输出端转矩转速传感器上的小电机的电源,待稳固后由转速仪(或效率仪)读出该小电机的转速, 并记录下来。
(4)确认整流子电动机的调速手轮(或电磁调速电动机的调速旋钮)
放在最低速挡, 接上电动机电源, 在空载状态下检查各部分是否运行正常。
检查转矩转速仪, 指示灯I 、II 点亮是表示仪器己接收到来自转矩转速传感器送出的两个信号:然后进行调零, 把调零开关拨到“自动”, 当转矩显示窗显示全零时, 调零即告完成。
将开关拨回“测量”时, 便可进行正常测量。
(5)旋转整流子电动机调速手轮( 或电磁调速电动机的调速旋钮), 调整电动机转速, 并调整激磁电流, 操纵磁粉制动器的负载力矩。
在各种负载力矩下, 由转矩转速仪(或效率仪) 读出转速、转矩, 并作记录:用测温仪、振动仪和声级计测量各种状态下齿轮箱的温度、振动和噪声。
(6)在负载力矩保持恒定值时, 改变电动机的转速, 由仪器读出转速、转矩, 并作记录:同时, 测量各种状态下的温度、振动及噪声。
(7)按照下列公式运算效率
其中,——齿轮箱的传动效率;、——输入输出转矩, N·m;
、——输入输出转速,rpm
六、实验方法及注意事项:
1. 开机时, 应先接通各测量仪器的电源, 检查仪器是否工作正常,各调剂旋钮是否都在零位, 然后再启动电动机。
电动机应在低速挡启动,
以免转速过快, 发生意外。
2.加载后, 应及时开通冷却水, 对加载器进行冷却。
3.关机前, 应先关冷却水, 再卸载。
然后调低电动机转速, 再关机,关仪器。
4.机周围应无较强振动的机器工作和强电磁场干扰。
5.各测量仪器上的开关和旋钮不得任意拨动, 以免损坏元件和带来测量误差甚至错误的测量。
6.对转矩转速仪, 每次关机后再开机, 都应先调零再测量。