钻头的选型
钻孔钻头的规格和标号

钻孔钻头的规格和标号主要有以下几种:1. M3钻头:全长65mm,柄径6.4mm,刃长35mm,小径3.4mm,大径6.4mm。
2. M4钻头:全长75mm,柄径8.4mm,刃长42mm,小径4.5mm,大径8.4mm。
3. M5钻头:全长85mm,柄径10.4mm,刃长50mm,小径5.5mm,大径10.4mm。
4. M6钻头:全长90mm,柄径12.0mm,刃长53mm,小径6.6mm,大径12.5mm。
除此之外,还有一些直柄沉头钻头规格和常用钻头规格等其他规格和标号。
直柄沉头钻头规格通常为12mm×1mm、14mm×1.25mm、16mm×1.5mm等,具体规格要根据工作需要来选择。
常用钻头规格尺寸有:直杆钻头、锥形钻头、长钻头、镀钛钻头和T型钻头等。
1. 直杆钻头:常用尺寸有0.3mm、0.5mm、0.8mm、1.0mm、1.2mm、1.5mm、1.8mm、2.0mm、2.5mm、3.0mm、4.0mm等。
2. 锥形钻头:常用尺寸有3.0mm、4.0mm、5.0mm、6.0mm、8.0mm、10.0mm等。
3. 长钻头:常用尺寸有1.0mm、1.2mm、1.5mm、2.0mm、2.5mm、3.0mm、4.0mm、5.0mm、6.0mm等。
4. 镀钛钻头:常用尺寸有1.0mm、1.5mm、2.0mm、2.5mm、3.0mm、3.5mm、4.0mm、4.5mm、5.0mm等。
5. T型钻头:常用尺寸有0.25mm、0.5mm、0.8mm、1.0mm、1.2mm、1.5mm、1.8mm、2.0mm、2.5mm、3.0mm等。
钻头选型方法综述
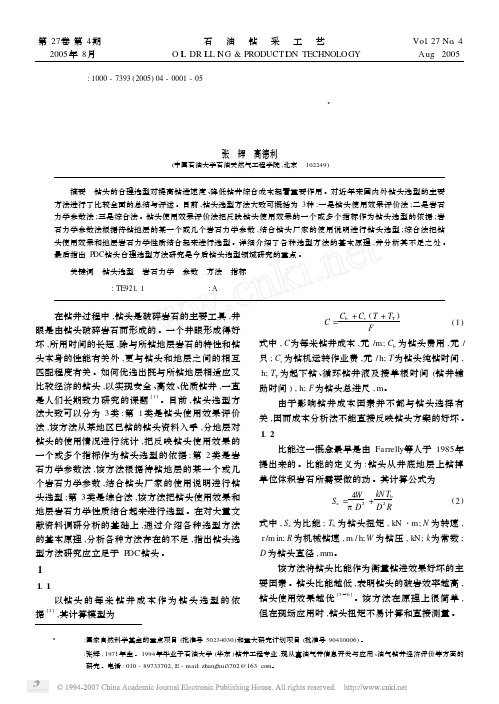
1. 3 经济效益指数法 根据钻头进尺 、机械钻速 、钻头成本 3个因素的
综合指标来评价钻头的使用效果 ,其评价结果与每 米钻井成本法总体上是一致的 。钻头经济效益指数 计算模型为 [ 7 ]
Eb
=α FR
Cb
(3)
式中 , Eb 为钻头经济效益指数 , m ·m / (元 ·h) ;α
为系数 。 Eb 越大 ,钻头使用效果越优 。
神经网络模型决定地层 、钻头性能和作业参数之间
陈德光 、唐念登 ( 1995, 2000 年 )等利用灰类白
的复杂关系 。该方法输入参数为 :钻头尺寸 、钻头总 化权函数聚类法 ,将岩石按硬度 、可钻性 、抗压强度
张 辉等 :钻头选型方法综述
3
等参数进行聚类 , 为钻头选型提供可靠的依 据 。 [ 15~16 ]
1. 4 灰类白化权函数聚类法
王越之 (1991年 )将钻头进尺 、纯钻时间 、机械
钻速和钻头成本作为钻头使用效果的评价指标 ,应 用灰类白化权函数法 ,根据聚类值的大小对钻头的 优劣进行评价 [ 8 ] 。 1. 5 综合指数法 (主分量分析法 )
于润桥 (1993年 )选择机械钻速 、牙齿磨损量 、 轴承磨损量 、钻头进尺 、钻头工作时间 、钻压 、转速 、 泵压 、泵排量及井深 10项指标 ,应用主成分分析法 , 综合钻头的使用效果和使用条件 ,提出了评选钻头 的“综合指数法 ”[ 9 ] 。应用华北油田 132 口井实钻 资料 ,给出了综合指数的表达式为
料计算综合指数 ,进行定量选型 [ 30 ] 。阎铁等 ( 2002 年 )提出利用自适应共振神经网络进行钻头优 选 [ 31 ] 。该神经网络共选用 12个神经元 ,包括地区 、 井深 、可钻性系数 、研磨性系数 、机械钻速 、钻头进 尺 、钻压 、转速 、井底水功率 、井底压差 、钻头牙齿磨 损和钻头轴承磨损 ;输出层为钻头型号 。神经网络 方法在实际应用中较复杂 ,有些输入参数不易求取 ,
牙轮钻头选型原则

牙轮钻头选型原则(1)软地层应选择有移轴、超顶、复锥3种结构的牙轮钻头,齿应是高、宽、稀、齿尖角大的铣齿或镶齿。
随着岩石硬度增大,选择钻头的上述3种结构值应相应减小,齿也应矮、窄、密,齿尖角也要相应减小。
(2)钻研磨性地层,应该选用带保径齿的镶齿钻头。
当发现上一个钻头的外排齿磨圆而中间齿磨损较少时,则下一个钻头应该选用有保径齿的镶齿钻头。
(3)在易斜地层钻进时,应选用不移轴或移轴量小、无保径齿并且齿多而短的钻头;同时,在保证移轴小的前提下,所选钻头适应的地层应比所钻地层稍软一些,这样可以在较低的钻压下提高机械钻速。
(4)选用镶硬质合金齿钻头时要注意:所钻地层页岩占多数时,用楔形齿钻头;钻石灰岩地层时,使用抛物体形或双锥形齿钻头;当用高密度钻井液钻井时,使用楔形齿钻头;当所选地层中页岩成分增加或钻井液密度增大时,用偏移值大的钻头;钻石灰岩或砂岩地层,选用偏移值小的钻头;钻硬的研磨性石灰岩、燧石、石英石时,用无移轴的球齿轱斗。
(5)在软硬交错地层钻进时,一般应按其中较硬的岩石选择钻头类型,这样既在软地层中有较高的机械钻速,也能顺利地钻穿硬地层。
在钻进过程中钻井参数要及时调整,在软地层钻进时,可适当降低钻压并提高转速;在硬地层钻进时可适当提高钻压并降低转速。
(6)浅井段岩石一般较软,同时起下钻所需时间较短,应选用能获得较高机械钻速的钻头;深井段地层一般较硬,起下钻时间较长,应选用有较高总进尺的钻头。
(7)在小井眼(井眼直径小于177mm)钻井中常选用单牙轮钻头,单牙轮钻头比同尺寸三牙轮钻头的牙轮、牙齿、轴径、轴承大,强度高,破岩效率高。
(8)按钻头产品目录选择钻头类型。
钻头生产厂家通过大量的试验,对各型钻头的适用地层情况进行了界定,形成了钻头产品目录。
根据钻头产品目录,结合所钻地层性质选择钻头类型,基本能够做到对号入座,匹配合理。
表卜10为国产三牙轮钻头产品目录。
(9)由于即使是同一种岩性,其机械性能差别也很大,所以仅根据岩性按钻头产品目录来确定钻头类型是不够全面的,还应收集邻近井相同地层钻过的钻头资料及上一个钻头的磨损分析,结合本井的具体情况来选择。
钻头选型的原则与依据23页PPT

H
1500
三、钻头选型的依据
1.地层条件 所钻地层岩石的机械力学特性,可钻性;地层的均质性、地层的完
整性、地层造斜特性、地层温度等。 2.钻井方式
旋转钻井;动力钻具;复合钻井 3.轨迹控制
造斜、稳斜 4.井眼尺寸 5.地质设计要求
如岩屑录井、取心等。
四、钻头选型方法
1.根据地层条件、钻井方式、井眼轨迹控制要求、井眼 尺寸以及地质要求选择合适的钻头类型。
2. IADC金刚石钻头分类方法及编号
IADC制定了适于用金刚石钻头的“固定切削齿钻头分 类标准”。这个标准主要根据钻头的结构特点进行分类, 并没有像牙轮钻头那样考虑钻头适用的地层。
金刚石钻头分类号由四个字符组成,第一个字符用英 文字母表示钻头体的材料,第二至第四个字符用阿拉伯 数字分别表示钻头的布齿密度、金刚石的尺寸或切削齿 的类别、钻头的冠部轮廓形状。
好
中钻压,高转速 复合钻井
井眼尺寸 事故率
录井限制
较大井眼 高 无
无限制 低 有
无限制 低 有
无限制 低 有
二、钻头选型原则 钻头选型的原则是使钻头的每米成本最低。目标 函数:单位进尺成本。
钻头单位进尺成本:
CpmCbCr(ttt) H
式中 Cpm—单位进尺成本,元/每米 Cb—钻头成本,元; Cr —钻机作业费,元/每小时; t—钻头纯钻进时间, tt—辅助时间(起下钻及接单根时间), H—钻头进尺。
一、不同钻头类型性能的差异
1.不同类型钻头机械钻速与钻头寿命百分比的关系
机 械 钻 速
钻头寿命百分比
分析:①不同类型钻头,机械钻速的总体差异; ②不同类型钻头,机械钻速随钻头新度的变化规律。
2.钻头的使用范围对比
钻头选择的一般原则
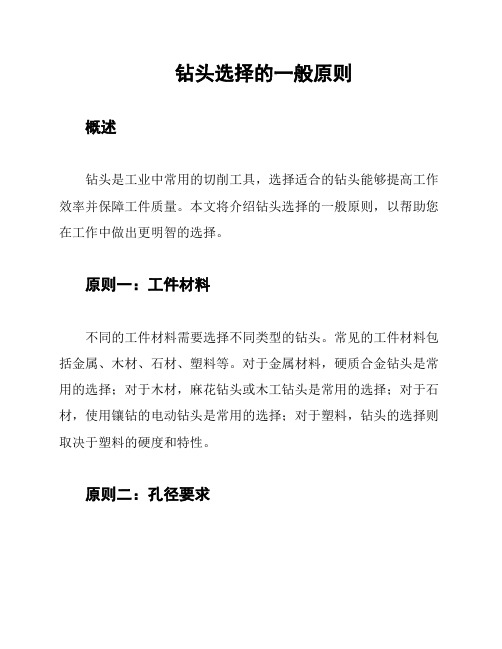
钻头选择的一般原则概述钻头是工业中常用的切削工具,选择适合的钻头能够提高工作效率并保障工件质量。
本文将介绍钻头选择的一般原则,以帮助您在工作中做出更明智的选择。
原则一:工件材料不同的工件材料需要选择不同类型的钻头。
常见的工件材料包括金属、木材、石材、塑料等。
对于金属材料,硬质合金钻头是常用的选择;对于木材,麻花钻头或木工钻头是常用的选择;对于石材,使用镶钻的电动钻头是常用的选择;对于塑料,钻头的选择则取决于塑料的硬度和特性。
原则二:孔径要求不同的工作需求需要选择不同孔径的钻头。
通常情况下,钻头尺寸与孔径直径成正比。
在选择钻头时,需要根据工作需要确定所需的孔径范围,并选择对应的钻头。
原则三:加工方式加工方式也是选择钻头的重要考虑因素。
常见的加工方式包括手持钻孔、电钻孔、立式钻削等。
对于手持钻孔,需要选择手持钻头;对于电钻孔,需要选择电动钻头;对于立式钻削,需使用立式钻头。
选择合适的钻头将有助于提高加工效率和精度。
原则四:工作环境工作环境也需要考虑,因为环境的特点将影响钻头的选择。
例如,在高温环境下,需要选择具有较高耐热性能的钻头;在潮湿环境下,需要选择具有防锈防腐蚀能力的钻头。
因此,在选择钻头时,需要充分了解工作环境的特点,并选择符合要求的钻头。
原则五:经济性考虑在选择钻头时,也需要考虑经济性。
较高质量的钻头可能价格更高,但其寿命更长,工作效率更高。
因此,根据具体需求,需要权衡价格和性能,并选择性价比较高的钻头。
总结钻头选择的一般原则包括考虑工件材料、孔径要求、加工方式、工作环境和经济性等因素。
根据这些原则选择合适的钻头能够提高工作效率、减少工作成本,并保障工件质量。
以上是钻头选择的一般原则,希望能对您在工作中做出合理选择提供帮助。
钻头选型
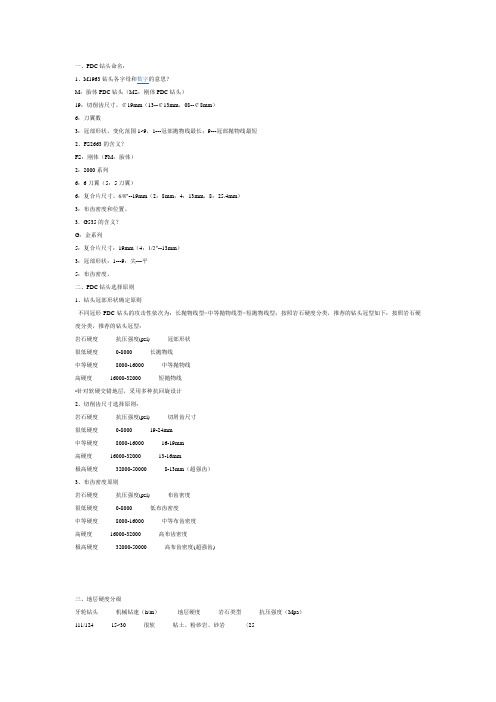
一、PDC钻头命名:1、M1963钻头各字母和数字的意思?M:胎体PDC钻头(MS:刚体PDC钻头)19:切削齿尺寸,¢19mm(13--¢13mm,08--¢8mm)6:刀翼数3:冠部形状,变化范围1~9,1---冠部抛物线最长;9---冠部抛物线最短2、FS2663的含义?FS:刚体(FM:胎体)2:2000系列6:6刀翼(5:5刀翼)6:复合片尺寸,6/8″--19mm(2:8mm;4:13mm,8:25.4mm)3:布齿密度和位置。
3.G535的含义?G:金系列5:复合片尺寸:19mm(4:1/2″--13mm)3:冠部形状:1---9:尖---平5:布齿密度。
二、PDC钻头选择原则1、钻头冠部形状确定原则不同冠形PDC钻头的攻击性依次为:长抛物线型>中等抛物线型>短抛物线型;按照岩石硬度分类,推荐的钻头冠型如下:按照岩石硬度分类,推荐的钻头冠型:岩石硬度抗压强度(psi) 冠部形状很低硬度0-8000 长抛物线中等硬度8000-16000 中等抛物线高硬度16000-32000 短抛物线•针对软硬交错地层,采用多种抗回旋设计2、切削齿尺寸选择原则:岩石硬度抗压强度(psi) 切屑齿尺寸很低硬度0-8000 19-24mm中等硬度8000-16000 16-19mm高硬度16000-32000 13-16mm极高硬度32000-50000 8-13mm(超强齿)3、布齿密度原则岩石硬度抗压强度(psi) 布齿密度很低硬度0-8000 低布齿密度中等硬度8000-16000 中等布齿密度高硬度16000-32000 高布齿密度极高硬度32000-50000 高布齿密度(超强齿)三、地层硬度分级牙轮钻头机械钻速(h/m)地层硬度岩石类型抗压强度(Mpa)111/124 15~30 很软粘土、粉砂岩、砂岩〈25116/137、437 9~15 软粘土岩、泥灰岩、砂岩25~50126/139517/537 4.5~9 中软粘土岩、褐煤、砂岩、粉砂岩,凝灰岩50~75211/217517/537 2.5~6 中等泥岩、灰岩、硬石膏砂岩(钙质)75~100211/236537/617 1.5~2.5 中硬灰岩、硬石膏砂岩(钙质)100~200311/347627/637 1~1.5 硬泥岩(钙质)、砂岩(质)粉砂岩100~200637、737、837 1 极硬石英石、火成岩〉200岩石的可钻性在岩土钻掘工程设计与实践中,人们常常希望能事先知道所施工岩石的破碎难易程度,以便正确选择合理的钻(掘)进方法、钻(钎)头的结构及工艺规程参数,制定出切合实际的岩土钻掘工程生产定额。
Part II--钻头选型解析

9.钻头期望值
➢ 钻头使用目的; ➢ 机械钻速; ➢ 钻头进尺.
10.经济评价
Cb + Cr (Tb + Tc + Tt) Cf=
H ➢ Cf-----每米钻井成本; ➢ Cb----钻头价格; ➢ Cr----钻机日作业费; ➢ Tb----纯钻进时间; ➢ Tc----辅助时间; ➢ Tt-----起下钻时间; ➢ H------钻头进尺.
200
400
600
800
TRQ (kn.m )--S91JT5737 0 5 10 15 20
200
400
600
800
FR (l/min)--S91JT5737 320 340 360 380 400 00000 200
400
600
800
1000
1000
1000
1200
1200
1200
1400
1400
泥 面:35.00m
20"隔水导管入泥45m 9-5/8"套管前置浆返至13-3/8"套 管 鞋 上 下 至 少 各 100m 17-1/2"井眼:205.00m 13-3/8"套管:200.00m
水泥返高1100m
12-1/4"井眼@1752米 9-5/8"套管@1750米
8-1/2"井眼1750-2205米 8-1/2"分支井眼100-150米
1. 地层岩性--地层变性
地层较深的泥岩地层,在大钻压下, 机械钻速低于1.5米/小时,如果静液 柱压力>6500 psi 时,将产生塑性, 岩屑又长又细. 即: 井眼垂深(英尺)X泥浆密度(磅/ 加仑)X0.052 >=6500 psi
钻头怎么选 钻头选型方法【老师傅干货】

钻头怎么选_钻头选型方法【老师傅干货】内容来源网络,由“深圳机械展(11万㎡,1100多家展商,超10万观众)”收集整理!更多cnc加工中心、车铣磨钻床、线切割、数控刀具工具、自动化、数字无人工厂、精密测量、3D打印、激光切割、钣金冲压折弯、精密零件加工等展示,就在深圳机械展.钻头是机械加工中应用广泛的五金件,它用以在实体材料上钻削出通孔或盲孔,并能对已有的孔扩孔的刀具。
但不同的作业环境我们选取的钻头种类也不同,常用的钻头主要有麻花钻、锪钻、中心钻和深孔钻。
扩孔钻和锪钻虽不能在实体材料上钻孔,但习惯上也将它们归入钻头一类。
麻花钻是应用广的孔加工刀具。
通常直径范围为0.25~80毫米。
它主要由工作部分和柄部构成。
工作部分有两条螺旋形的沟槽,形似麻花,因而得名。
标准麻花钻的切削部分顶角为118,横刃斜角为40°~60°,后角为8°~20°。
麻花钻的柄部形式有直柄和锥柄两种,加工时前者夹在钻夹头中,后者插在机床主轴或尾部的锥孔中;一般麻花钻用高速钢制造。
深孔钻通常是指加工孔深与孔径之比大于6的孔的刀具。
常用的有枪钻、BTA深孔钻、喷射钻、DF深孔钻等。
扩孔钻有3~4个刀齿,其刚性比麻花钻好,用于扩大已有的孔并提高加工精度和光洁度。
锪钻有较多的刀齿,以成形法将孔端加工成所需的外形,用于加工各种沉头螺钉的沉头孔,或削平孔的外端面。
中心钻供钻削轴类工件的中心孔用,它实质上是由螺旋角很小的麻花钻和锪钻复合而成,故又称复合中心钻。
模具制造业的钻削加工在几个关键要素上往往与常规钻削有所不同。
首先,在不规则表面上钻孔的情况很常见;其次,该行业所用的工件材料通常比常规材料更难加工。
为了成功应对这些加工特点,需要采用具有针对性的加工策略。
无论是使用可转位刀片式钻头、可换钻尖式钻头,还是整体硬质合金钻头乃至高速钢钻头,在不规则表面上钻孔或进行断续切削都有可能出现问题,这是因为加工表面越不规则,钻头挠曲变形的可能性就越大。
- 1、下载文档前请自行甄别文档内容的完整性,平台不提供额外的编辑、内容补充、找答案等附加服务。
- 2、"仅部分预览"的文档,不可在线预览部分如存在完整性等问题,可反馈申请退款(可完整预览的文档不适用该条件!)。
- 3、如文档侵犯您的权益,请联系客服反馈,我们会尽快为您处理(人工客服工作时间:9:00-18:30)。
钻头类型定性选择原则
(1)根据地层条件、钻井方式、井眼轨迹控制要求、井眼尺寸以及地质要求选择合适的钻头类型。
(2)在多种类型钻头都适宜的情况下,要选择机械钻速高、寿命长、安全性好的钻头。
(3)在软至中硬地层,PDC钻头和牙轮钻头都可选用;
如果地层均质,应尽量选用PDC钻头。
因为PDC钻头机械钻速高,安全可靠。
如果地层破碎,软硬变化频繁夹层多,应该选用牙轮钻头。
因为在这样的地层,PDC钻头易发生冲击破坏,影响钻头使用效果。
2.3牙轮钻头选型原则
牙轮钻头的设计参数(包括齿高、齿距、齿宽、移轴距、牙轮布置等等),是根据不
同地层的需要设计的,因此应根据不同的地层选用不同的钻头。
(1)地层的软硬层度和研磨性
地层的岩性和软硬不同,对钻头的要求及破碎机理也不同。
软地层应选择兼有
移轴、超顶、复锥三种结构,牙轮齿形较大、较尖,齿数较少的铣齿或镶齿钻
头,以充分发挥钻头的剪切破岩作用;随着岩石硬度增大,选择钻头的上诉三
种结构值相应减少,牙齿也要减短加密。
研磨性地层会使牙齿过快磨损,机械钻速迅速降低,钻头进尺少,特别容易磨
损钻头的保径齿、背锥以及牙掌的掌尖,使钻头直径磨小,更严重的是会使轴
承外漏、轴承密封失效,加速钻头损坏。
因此,钻研磨性地层,应该选用有保
径齿的镶齿钻头。
(2)井深
浅井段岩石一般较软,同时起下钻所需时间较短,应选用能获得较高机械钻速
的钻头。
深井段地层一般较硬,起下钻时间较长,应选用较高总进尺(钻头寿命长)的
钻头。
(3)地层的自然造斜性能
在易斜地层钻进时,地层因素是造成井斜的客观原因,而下部钻柱的弯曲以及
钻头的选型不当则是造成井斜的技术因素。
在易井斜地层钻进,应选用不移轴或移轴量小的钻头;同时,在保证移轴小的
前提下,所选的钻头适应的地层比所钻地层稍软一些,这样可以在较低的钻压
下提高机械钻速。
(4)地层的均质性
在软硬交错地层钻进时,一般应按其中较硬的岩石选择钻头,这样既在软地层
中有较高的机械钻速,也可以顺利地钻穿硬地层。
在钻进过程中钻井参数要及时调整,在软地层钻进时,可适当降低钻压并提高
钻速;在硬地层钻进时可适当提高钻压并且降低钻速。
2.4PDC钻头选型原则
根据地层强度确定PDC切削块直径(1/2’’或3/4’’)。
一般而言,对于软到中硬地层,选用直径较大的PDC复合片,采用低密度或中等密度布齿的钻头,。
对于中硬到坚硬地层,选用直径小的PDC复合片,采用中等密度或高密度布齿的钻头。
对地层研磨性不太强的地层,可以选用一般的PDC钻头钻进。
对研磨性较强的地层,宜选用耐磨性好的特殊加工的PDC钻头或天然金刚石钻头。
PDC钻头钻进井段较长,穿越的层位比较多,应按预期钻遇强度最高的地层进行选型。
PDC钻头适合软到中硬地层、均匀地层,不适合含砾石、黄铁矿、燧石、花岗岩、硬
夹层地层,对硬地层应采用低钻压、高钻速钻进。
TSP钻头适合中等至硬地层钻井。
天然金刚石钻头适合研磨性强、中到坚硬地层。
层相匹配的情况
下,PDC钻头应
该配合螺杆或涡
轮钻具使用才能
取得更为满意的机械钻速和进尺。
对于定向井而言,在研磨性较高的稳斜井段钻进时除了要保证所选的PDC切削齿具有高的耐磨性以外,还要保证所选的钻头具有良好的保径效果(一般选用相对较小的保径长度),以期得到较高的机械钻速和进尺。
在PDC钻头选型方面,应注意钻头的轮廓和布齿方式,下表是常用的PDC钻头轮廓及适用范围。
在石油勘探和钻井作业中牙轮式钻头最为普遍,应用范围也较为广泛;金刚石式钻头在特殊地质有着良好的适用性,石油钻井应该掌握的主要技术之一;而刮刀式钻头应
用范围较窄,而且已经遭淘汰,在此就不进行描述。