钻头怎么选 钻头选型方法【老师傅干货】
旋挖钻头的选配与使用
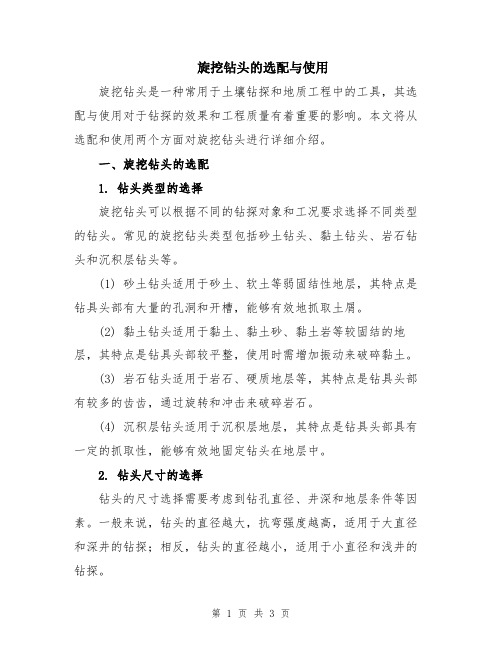
旋挖钻头的选配与使用旋挖钻头是一种常用于土壤钻探和地质工程中的工具,其选配与使用对于钻探的效果和工程质量有着重要的影响。
本文将从选配和使用两个方面对旋挖钻头进行详细介绍。
一、旋挖钻头的选配1. 钻头类型的选择旋挖钻头可以根据不同的钻探对象和工况要求选择不同类型的钻头。
常见的旋挖钻头类型包括砂土钻头、黏土钻头、岩石钻头和沉积层钻头等。
(1) 砂土钻头适用于砂土、软土等弱固结性地层,其特点是钻具头部有大量的孔洞和开槽,能够有效地抓取土屑。
(2) 黏土钻头适用于黏土、黏土砂、黏土岩等较固结的地层,其特点是钻具头部较平整,使用时需增加振动来破碎黏土。
(3) 岩石钻头适用于岩石、硬质地层等,其特点是钻具头部有较多的齿齿,通过旋转和冲击来破碎岩石。
(4) 沉积层钻头适用于沉积层地层,其特点是钻具头部具有一定的抓取性,能够有效地固定钻头在地层中。
2. 钻头尺寸的选择钻头的尺寸选择需要考虑到钻孔直径、井深和地层条件等因素。
一般来说,钻头的直径越大,抗弯强度越高,适用于大直径和深井的钻探;相反,钻头的直径越小,适用于小直径和浅井的钻探。
选择钻头尺寸时还需考虑地层条件,例如如果遇到较坚硬的岩石地层,钻头应选择直径较大、齿齿较少的钻头,以提高钻探效率和钻头寿命。
3. 钻头材质的选择钻头的材质直接影响钻具的切削性能和使用寿命。
常见的钻头材质有合金钢、硬质合金和切割器具等。
硬质合金的切削性能和耐磨性较好,适用于较坚硬的地层;合金钢具有较高的韧性和强度,适用于较软的地层和一般的土壤。
4. 钻头连接方式的选择钻具的连接方式包括直角扣、螺纹连接和销钉连接等多种形式。
选用合适的连接方式需要考虑到钻孔的直径、井深和钻机的具体情况等因素,以确保连接的可靠性和方便性。
二、旋挖钻头的使用1. 钻具存放和保养在使用旋挖钻头之前,需要将钻具存放在干燥通风的地方,防止受潮和锈蚀。
使用过程中,要做好钻具的清洁和保养工作,及时去除沉积在钻具上的泥沙和岩石屑,防止泥沙或坚硬的岩石粒子损坏钻具。
钻头选择注意事项是什么

钻头选择注意事项是什么钻头选择是钻孔工作中非常重要的一个环节,它直接关系到钻孔效率和质量。
钻头的选择要根据具体的工作要求和材料特性进行合理的选择,下面是钻头选择的注意事项:1. 材料特性:钻头的材料特性是选择钻头的重要考虑因素之一。
根据所要钻孔的材料硬度、韧性和耐磨性等特点,选择合适的钻头材料。
通常有高速钢、硬质合金、立方氮化硼等材料可供选择。
需要特别注意的是,材料的硬度越大,对钻头的要求也就越高。
2. 钻孔尺寸:钻头的选择还要根据所要钻孔的尺寸来确定。
一般来说,钻孔的直径越大,所需的钻头也就越粗且牢固。
对于小直径的孔,可以选择钻头直径与之相等的凸腹钻头。
而对于大直径孔,可以选择带内冷负压的大直径钻头。
3. 钻孔深度:钻孔深度也是选择钻头的重要考虑因素。
根据钻孔深度的不同,可以选择适合的加强型钻头。
对于浅孔,可以选择普通钻头,而对于深孔,选择中心和凸腹钻头更为适合。
此外,还应注意合理选择钻头的长度,避免钻孔过深或过浅。
4. 钻头类型:根据所要钻孔的不同,有不同类型的钻头供选择。
常见的有全螺纹钻头、内冷钻头、凸腹钻头、钻孔插入式钻头等。
根据具体需求,选择合适的钻头类型,能够提高钻孔的效率和质量。
5. 冷却方式:钻孔时,冷却液的选用也是非常重要的。
适当的冷却可以降低摩擦,延长钻头的使用寿命,并且提高钻孔质量。
根据具体需求,可以选择空气冷却、清洁液冷却或其它冷却方式。
6. 使用环境:钻孔作业时的环境因素也要考虑。
例如,如果是高温环境,要选择能够耐高温的钻头;如果是湿润环境,要选择防锈处理的钻头;如果是高压环境,要选择能够承受高压的钻头。
7. 选择品牌和质量:在选择钻头时,应该选择质量可靠的知名品牌的产品。
只有品牌产品才能保证钻头的使用寿命和稳定性。
同时,应该注意购买时的售后服务和保修条款,以保证后期的使用和维护。
8. 刀具磨损检查:在使用钻头前后,要进行刀具磨损的检查。
如果发现钻头存在磨损或者已经不锋利,应及时更换新的钻头。
钻头选择和使用

钻头选择和使用1、硬质合金钻头的选择胶结性的砂岩、黏土亚黏土、泥岩以及风化岩层、遇水膨胀或缩径地层宜选用肋骨式硬质合金钻头或刮刀式硬质合金钻头;可钻性3-5级的中、弱研磨性地层,铁质、钙质岩层、大理岩等宜用直角薄片式钻头、单双粒钻头或品字形钻头;研磨性强、非均质较破碎、稍硬岩层,如石灰岩等宜用负前角阶梯钻头;软硬不均、破碎及研磨性强的岩层,如砾石等宜用大八角钻头;砂岩、砾岩等选用针状合金钻头。
常用硬质合金取心钻头及其适用范围见表6-1。
2、金刚石钻头的选择金刚石钻进适用于中硬以上岩层。
一般聚晶金刚石、金刚石复合片、烧结体钻头适用于3~7级岩层,单晶孕镶金刚石钻头适用于5~12级完整和破碎岩层,天然表镶金刚石钻头适用于4~10级完整岩层。
不同类型金刚石钻头的选用见表6-2。
金刚石钻头主要参数及结构要素与钻头选择如下:(1)钻头唇面形状。
中硬、中等研磨性的岩层,宜选用平底形唇面或圆弧形唇面;坚硬且研磨性高的岩层,可用半圆形唇面;对复杂、破碎不易取得岩心的地层,可选用阶梯底喷式唇面;坚硬、致密易出现打滑的岩层,可选用锯齿形唇面。
金刚石取心钻头唇面形状及适用地层参见表5-29。
(2)胎体硬度。
岩石的研磨性越强或硬度越低,则钻头胎体的硬度应越髙;反之,岩石的研磨性越弱或硬度越高,则钻头胎体的硬度应越低。
不同岩层推荐胎体硬度及耐磨性参见第5章表5-35。
(3)金刚石浓度。
岩石硬度越高或研磨性越弱,则钻头金刚石浓度应越低;反之,岩石硬度越低或研磨性越强,则钻头金刚石浓度应越髙。
人造孕镰金刚石钻头在不同岩层推荐的金刚石浓度值参见表5-39。
(4)金刚石粒度。
若石的研磨性越强,硬度越高,则要求钻头的金刚石颗粒应越小,最好用孕镶钴头;岩石硬度越低,研磨性越弱,则要求钻头的金刚石夥粒应越大。
孕镶金刚石钻头推荐粒度参见表5-40,表镶金刚石钻头推荐粒度参见表5-41。
3、钻头的合理使用(1)按照相关标准严格检查钻头与扩孔器,将符合要求者按钻头与扩孔器外径先大后小的次序排队编组轮换使用,同时亦应先用内径小的,后用内径大的在轮换过程中,应保证排队的钻头、扩孔器都能正常下到孔底,以避免扫孔残留岩心。
钻头选择的一般原则
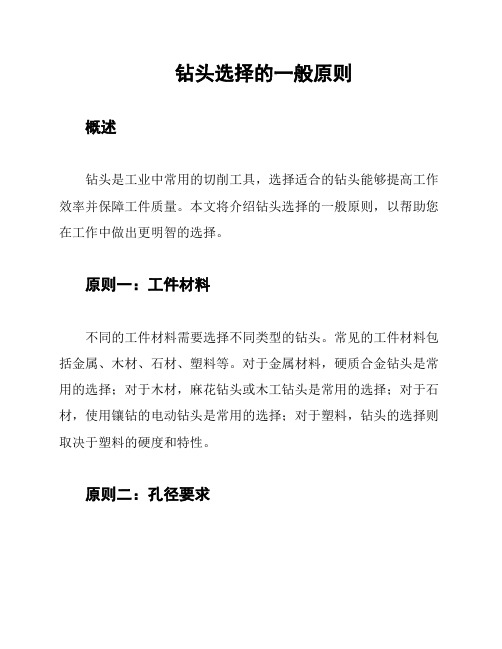
钻头选择的一般原则概述钻头是工业中常用的切削工具,选择适合的钻头能够提高工作效率并保障工件质量。
本文将介绍钻头选择的一般原则,以帮助您在工作中做出更明智的选择。
原则一:工件材料不同的工件材料需要选择不同类型的钻头。
常见的工件材料包括金属、木材、石材、塑料等。
对于金属材料,硬质合金钻头是常用的选择;对于木材,麻花钻头或木工钻头是常用的选择;对于石材,使用镶钻的电动钻头是常用的选择;对于塑料,钻头的选择则取决于塑料的硬度和特性。
原则二:孔径要求不同的工作需求需要选择不同孔径的钻头。
通常情况下,钻头尺寸与孔径直径成正比。
在选择钻头时,需要根据工作需要确定所需的孔径范围,并选择对应的钻头。
原则三:加工方式加工方式也是选择钻头的重要考虑因素。
常见的加工方式包括手持钻孔、电钻孔、立式钻削等。
对于手持钻孔,需要选择手持钻头;对于电钻孔,需要选择电动钻头;对于立式钻削,需使用立式钻头。
选择合适的钻头将有助于提高加工效率和精度。
原则四:工作环境工作环境也需要考虑,因为环境的特点将影响钻头的选择。
例如,在高温环境下,需要选择具有较高耐热性能的钻头;在潮湿环境下,需要选择具有防锈防腐蚀能力的钻头。
因此,在选择钻头时,需要充分了解工作环境的特点,并选择符合要求的钻头。
原则五:经济性考虑在选择钻头时,也需要考虑经济性。
较高质量的钻头可能价格更高,但其寿命更长,工作效率更高。
因此,根据具体需求,需要权衡价格和性能,并选择性价比较高的钻头。
总结钻头选择的一般原则包括考虑工件材料、孔径要求、加工方式、工作环境和经济性等因素。
根据这些原则选择合适的钻头能够提高工作效率、减少工作成本,并保障工件质量。
以上是钻头选择的一般原则,希望能对您在工作中做出合理选择提供帮助。
钻头选型
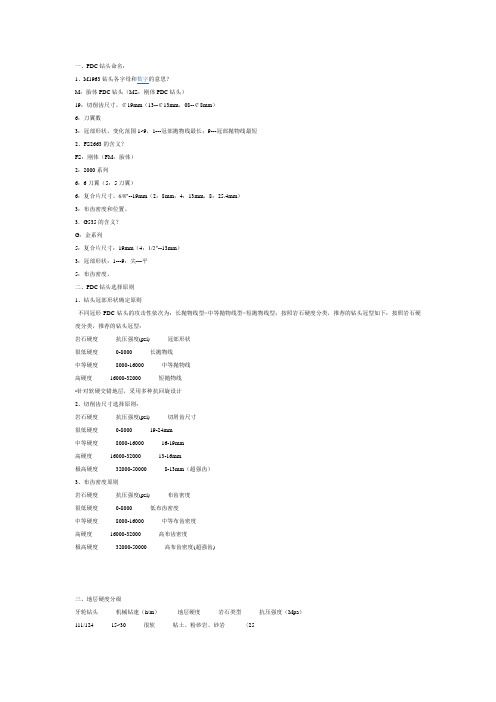
一、PDC钻头命名:1、M1963钻头各字母和数字的意思?M:胎体PDC钻头(MS:刚体PDC钻头)19:切削齿尺寸,¢19mm(13--¢13mm,08--¢8mm)6:刀翼数3:冠部形状,变化范围1~9,1---冠部抛物线最长;9---冠部抛物线最短2、FS2663的含义?FS:刚体(FM:胎体)2:2000系列6:6刀翼(5:5刀翼)6:复合片尺寸,6/8″--19mm(2:8mm;4:13mm,8:25.4mm)3:布齿密度和位置。
3.G535的含义?G:金系列5:复合片尺寸:19mm(4:1/2″--13mm)3:冠部形状:1---9:尖---平5:布齿密度。
二、PDC钻头选择原则1、钻头冠部形状确定原则不同冠形PDC钻头的攻击性依次为:长抛物线型>中等抛物线型>短抛物线型;按照岩石硬度分类,推荐的钻头冠型如下:按照岩石硬度分类,推荐的钻头冠型:岩石硬度抗压强度(psi) 冠部形状很低硬度0-8000 长抛物线中等硬度8000-16000 中等抛物线高硬度16000-32000 短抛物线•针对软硬交错地层,采用多种抗回旋设计2、切削齿尺寸选择原则:岩石硬度抗压强度(psi) 切屑齿尺寸很低硬度0-8000 19-24mm中等硬度8000-16000 16-19mm高硬度16000-32000 13-16mm极高硬度32000-50000 8-13mm(超强齿)3、布齿密度原则岩石硬度抗压强度(psi) 布齿密度很低硬度0-8000 低布齿密度中等硬度8000-16000 中等布齿密度高硬度16000-32000 高布齿密度极高硬度32000-50000 高布齿密度(超强齿)三、地层硬度分级牙轮钻头机械钻速(h/m)地层硬度岩石类型抗压强度(Mpa)111/124 15~30 很软粘土、粉砂岩、砂岩〈25116/137、437 9~15 软粘土岩、泥灰岩、砂岩25~50126/139517/537 4.5~9 中软粘土岩、褐煤、砂岩、粉砂岩,凝灰岩50~75211/217517/537 2.5~6 中等泥岩、灰岩、硬石膏砂岩(钙质)75~100211/236537/617 1.5~2.5 中硬灰岩、硬石膏砂岩(钙质)100~200311/347627/637 1~1.5 硬泥岩(钙质)、砂岩(质)粉砂岩100~200637、737、837 1 极硬石英石、火成岩〉200岩石的可钻性在岩土钻掘工程设计与实践中,人们常常希望能事先知道所施工岩石的破碎难易程度,以便正确选择合理的钻(掘)进方法、钻(钎)头的结构及工艺规程参数,制定出切合实际的岩土钻掘工程生产定额。
钻头的选用方法

2 .焊接硬质合金钻头
焊接 硬质 合金 钻 头 是 在 钻 柄 螺 旋 槽 的尖 端 ,焊 接上 一块硬 质 合 金 钻 尖 ,如 图 4所 示 。钻 尖 可 多次 重磨 ,刀具 成 本 低 于 整体 硬 质 合 金 钻 头 ,适 用 于直
性 夹套 ,故 刀柄 成 本 略 低 。侧 固刀 柄 定 位 精 度 略 低 于 圆柱 柄 ,适 用 于加工 孔 的精 度为 I9 1 。特 别 T ~ 0级
图 4 焊接 硬质合 金钻 头
心 ,中心刀 片过 中心 内刃 钻 出 1 8 锥 面 ,可 引 导 钻 2。 轴 不偏 。外 刀片 刀刃安 装 出 8 。 9 主偏角 ,形成 了 1 8 7。 顶 角 ,径 向力 极 小 ,同时 形 成 了 1 的 副偏 角 。主 副 。 刀 刃转 角处 有 圆弧 刃 相 连 有 利 于修 光 。可 转 位 刀 片 钻 头可用 的切 削参 数 为 V=10~10 / i 、厂 . 8 2 5 m r n =0 0 a
图 8 可转位刀片钻头 的钻镗功能
4 .可 转 位 刀 片 钻 头 可 转位 刀 片 钻 头 也 称 可 转 位 浅 孔 钻 、u 形 钻 , 适 合用 于 L D< / 5的 中等直 径 孔加 工 ,可 在 车床 、钻 床 上使 用 。如 图 6所 示 ,可 转 位 刀 片 交 错 分 布 在 钻
0 1 m / ,钻孔效 率较 高 。 .8 m r
称 刀头 ) 与 刀体 用 圆
柱 头 定 位 ,弹 性 加 紧
2 。 6
方 式 连 接 ,更 换 方
6 9
便 ,重 复 定 位 精 度 较 高 ,加 工 精 度 可 达 I8级 。一 支 钻 体 可 T 配用 1 mm范 围 内的不 同尺 寸 的 刀 头 ,并 能 多次 更 换 刀 头 重 复 使
钻头的主要参数
钻头的主要参数钻头的主要参数是指影响钻头性能和适用范围的关键参数,钻头的选择和使用取决于这些参数的特性。
以下是钻头的主要参数及其相关内容:1. 刀具材料:钻头的刀具材料是影响钻头性能的重要因素之一。
常见的刀具材料包括高速钢、硬质合金、陶瓷和金刚石等。
不同材料具有不同的硬度、耐磨性和热稳定性,选择合适的刀具材料可以提高钻头的寿命和效率。
2. 刀具形状:钻头的刀具形状也是影响其性能的关键参数。
常见的刀具形状包括直柄钻头、T型钻头、锥柄钻头、螺旋钻头等。
不同形状的钻头适用于不同的钻孔任务,选择合适的刀具形状可以提高钻头的钻孔精度和效率。
3. 刀具直径:钻头的直径是指钻头刀具的直径尺寸,通常以毫米或英寸为单位。
钻头的直径决定了钻孔的尺寸和精度,选择合适直径的钻头可以确保钻孔的质量和准确度。
4. 刀具长度:钻头的长度是指钻头刀具的长度尺寸,不同长度的钻头适用于不同深度的钻孔任务。
选择合适长度的钻头可以提高钻头的稳定性和钻孔的精度。
5. 刀具涂层:钻头的涂层是钻头表面的一层特殊涂层,可以提高钻头的硬度、耐磨性和热稳定性。
常见的钻头涂层包括TiN涂层、TiCN涂层、TiAlN涂层等,选择合适的涂层可以提高钻头的寿命和性能。
6. 刀具刃数:钻头的刃数是指钻头刀具的切削刃数目,刃数的多少影响钻头的切削效率和钻孔的表面质量。
通常,刃数越多的钻头切削效率越高,但钻头的切削力和振动也会增加。
7. 刀具钻头的冷却方式:钻头的冷却方式是钻头的冷却和润滑的关键参数,不同的钻头冷却方式包括内冷钻头、外冷钻头、内外冷钻头等。
选择合适的冷却方式可以降低钻头的温度和摩擦,延长钻头的寿命和提高钻头的钻孔质量。
钻头的主要参数包括刀具材料、刀具形状、刀具直径、刀具长度、刀具涂层、刀具刃数和刀具钻头的冷却方式等,选择合适的钻头参数可以提高钻头的性能和钻孔的质量,确保钻孔任务的顺利进行。
钻头选型的原则与依据
钻头选型
第一节
钻头选型的原则与依据
目的意义:
钻头类型不同,性能不同; 同一类型钻头,结构参数不同,性能不同; 同一型号钻头,厂家不同,性能不同。 选择哪一种类型的钻头,同种钻头选择哪一种型号的
钻头,同一种型号选择哪一个厂家的钻头,直接关系到钻
井速度与钻井成本。因此钻头优选对于提高钻井速度降低 钻井成本具有重要意义。
t—钻头纯钻进时间, tt—辅助时间(起下钻及接单根时间),
H—钻头进尺。
例题:
某一型号PDC成本10万元,钻头钻进1500米 后报废,此钻头纯钻时间100小时,辅助钻进时 间100小时,钻机日费2.4万元,计算该钻头的
平均机械钻速和单位进尺成本?
解:
钻头平均机械钻速:
ROP H 1500 m 15m / h T 100 h
切削齿大小和切削齿密度 水力结构特点 钻头冠部形状 英文字母表示钻头体的材料
一、不同钻头类型性能的差异
1.不同类型钻头机械钻速与钻头寿命百分比的关系
机 械 钻 速
钻头寿命百分比
分析:①不同类型钻头,机械钻速的总体差异;
②不同类型钻头,机械钻速随钻头新度的变化规律。
2.钻头的使用范围对比
单晶金刚石钻头 TSP钻头 PDC钻头 牙轮钻头 地层硬度级别 1 2 3 4 5 6 7 8 9 10 11 12
3—滚动轴承,保径;
4一滚动、密封轴承; 5一滚动、密封轴承,保径;
6—滑动、密封轴承;
7一滑动、密封轴承,保径。
第四位字码为钻头附加结构特征代号,用以表示前面
位数字无法表达的恃征,用英文字母表示,目前,IADC已
定义了11个特征,用下列字母表示: A—空气冷却; C—中心喷嘴;D—定间钻井;E—加长 喷嘴; G—附加保径/钻头体保径;J—喷嘴偏射;R—加强焊 缝:S—标准铣齿; X—楔形镶齿;R—圆锥形镶齿;Z—其
钻头基本知识和选型(技术员培训)
钻头基本知识和选型
Technology Development Centre ( EOTDC).Southwest.Drilling company of Zhongyuan Petroleum Engineering Co.Ltd Sinopec
量的问题。
使用环境因素对钻头性能的影响
影响PDC钻头机械钻速的因素: 钻头本身的因素和使用环境因素 钻头本身因素(或内因)包括:
钻头选型 PDC钻头对地层相对比较敏感,根据地层情况选择合适的钻头 型号或根据地层情况进行针对性的设计钻头,是非常重要的,也是PDC 钻头能否取得较好经济指标的前提和关键。
钻井工程数据
– 井身结构 – 井眼轨迹 – 泥浆性能 – 钻具组合 – 钻井参数
邻井钻头使用资料
岩石力学分析及应用
常用测井方式、代码和单位
测井代码 DT, DTc RHOB, DEN GR, GRc Pe CAL RES S-POR,S-PORc D-POR,D-POR N-POR ND-POR UCS-psi CCS-psi
钻头设计参数和制造工艺; 切削齿性能及质量;
使用环境因素对钻头性能的影响
使用环境因素包括:
地层岩性和压实强度; 使用的钻井参数;包括钻压、转速和排量等。
✓ PDC的刚脆性要求钻头旋转要平稳、减少振动,钻具组合时最好加上减振器, 减少振动,防止跳钻和溜钻;
✓ PDC的热敏性要求选择合适的排量,以达到清洗和冷却切屑齿。通过水力参 数计算,一般选择的排量要求钻头喷嘴的射流冲击力要达到40米/秒以上,钻 头比水马力要达到1.5马力/in2以上,以满足清洗岩屑和冷却PDC的要求,泥 浆环空最低返速达到0.6-1米/秒。
挑选钻头的5大要点
一、看地层,挑选钻斗类型。
再好的钻斗也要在适合的环境下方能发挥最佳效果,因地
制宜挑选钻斗就成功了一大半,如何因地制宜?地质报告是我们一个可靠的依据,可以让甲方提供,具体土层与钻斗的配置如下:
螺旋钻主要作用是破碎,钻进后提物量极少,不能单独使用,需配合捞砂斗使用。
二、选好型,再看料。
很多朋友买钻斗直接问价格,下次不妨问问他的料,钢板是钻斗
的主要材料,在使用过程中也是冲在一线。
闹个脾气咱就得闹心。
现在市场的斗大多是用的Q345B钢板,这种钢板就目前来说的性价比是最好的,综合性良好,特别是焊接性能和可切削性能好;还有一种耐磨钢板,这种钢板的应用不是很多,主要是成本贵很多,厚度有限,它是由低碳钢板和合金耐磨层组成,有很高的耐磨性能和较好的冲击性能。
同样的钢板厚度的大小也会影响磨损速度优力特重工
三、选齿,齿是冲锋兵,咱知道,齿的质量及齿的角度是钻进速度的保证,齿的质量影
响磨损速度,角度影响进土的速度,在选购斗的时候可跟工厂提供地形,设计人员会根据地层来设计齿角度和选用齿优力特重工
四、选方头,方头连接钻杆,带动钻斗钻进,在选购时一定要根据自己的钻杆机型来配
置,一般需要方头的尺寸大小及型号
五、私人订制,前四条都是一般钻斗要注意的,依靠地层原因很多钻斗都是需要改进或
则完善来达到预期钻进效果,这个时候,需要与钻具设计人员沟通,调整设计方案,磨刀不误砍柴工,钻具的正确选择会加快工程进度,大大节约人力成本及时间成本。
- 1、下载文档前请自行甄别文档内容的完整性,平台不提供额外的编辑、内容补充、找答案等附加服务。
- 2、"仅部分预览"的文档,不可在线预览部分如存在完整性等问题,可反馈申请退款(可完整预览的文档不适用该条件!)。
- 3、如文档侵犯您的权益,请联系客服反馈,我们会尽快为您处理(人工客服工作时间:9:00-18:30)。
钻头怎么选_钻头选型方法【老师傅干货】
内容来源网络,由“深圳机械展(11万㎡,1100多家展商,超10万观众)”收集整理!
更多cnc加工中心、车铣磨钻床、线切割、数控刀具工具、自动化、数字无人工厂、精密测量、3D打印、激光切割、钣金冲压折弯、精密零件加工等展示,就在深圳机械展.
钻头是机械加工中应用广泛的五金件,它用以在实体材料上钻削出通孔或盲孔,并能对已有的孔扩孔的刀具。
但不同的作业环境我们选取的钻头种类也不同,常用的钻头主要有麻花钻、锪钻、中心钻和深孔钻。
扩孔钻和锪钻虽不能在实体材料上钻孔,但习惯上也将它们归入钻头一类。
麻花钻是应用广的孔加工刀具。
通常直径范围为0.25~80毫米。
它主要由工作部分和柄部构成。
工作部分有两条螺旋形的沟槽,形似麻花,因而得名。
标准麻花钻的切削部分顶角为118,横刃斜角为40°~60°,后角为8°~20°。
麻花钻的柄部形式有直柄和锥柄两种,加工时前者夹在钻夹头中,后者插在机床主轴或尾部的锥孔中;一般麻花钻用高速钢制造。
深孔钻通常是指加工孔深与孔径之比大于6的孔的刀具。
常用的有枪钻、BTA深孔钻、喷射钻、DF深孔钻等。
扩孔钻有3~4个刀齿,其刚性比麻花钻好,用于扩大已有的孔并提高加工精度和光洁度。
锪钻有较多的刀齿,以成形法将孔端加工成所需的外形,用于加工各种沉头螺钉的沉头孔,或削平孔的外端面。
中心钻供钻削轴类工件的中心孔用,它实质上是由螺旋角很小的麻花钻和锪钻复合而成,故又称复合中心钻。
模具制造业的钻削加工在几个关键要素上往往与常规钻削有所不同。
首先,在不规则表面上钻孔的情况很常见;其次,该行业所用的工件材料通常比常规材料更难加工。
为了成功应对这些加工特点,需要采用具有针对性的加工策略。
无论是使用可转位刀片式钻头、可换钻尖式钻头,还是整体硬质合金钻头乃至高速钢钻头,在不规则表面上钻孔或进行断续切削都有可能出现问题,这是因为加工表面越不规则,钻头挠曲变形的可能性就越大。
不过,在考虑钻头挠曲变形之前,首先应该考虑选用哪种类型的钻头。
答案取决于技术性和经济性两方面的考虑。
对于直径在12.7mm以下、孔深在70倍孔径(70×D)以内的孔,适合用整体硬质合金钻头加工。
而在加工直径更大、孔深为5×D以内的孔时,可转位刀片式钻头往往能提供有效的解决方案。
对于孔深为(5-10)×D的孔,可换钻尖式钻头则是首选刀具。
对于所有这些加工,都推荐采用内冷却式钻头。
此外,还需要考虑加工的经济性。
不同类型钻头的每孔加工成本存在差异。
每孔加工成本会随着加工批量(钻孔数)的增加而下降。
如果每孔加工成本居高不下(处于成本曲线的峰值),则表明需要选用另一种钻头或另一组刀片。
每孔加工成本(即决策点)的权衡要素为孔的加工数量和加工质量,在某种程度上还包括机床和夹具。
当加工批量很小时,加工循环时间和每孔加工成本并不太重要,采用经济性较好的高速钢钻头可能就足够了。
而对于批量较大的加工,整体硬质合金钻头可能更具优势,因为这种钻头虽然价格比较贵,但它可以采用更高的切削速度和更大的切削参数,从而能提供更低的每孔加工成本和更高的生产能力。
不过,对于孔径大于12.7mm、孔深在5×D以内的孔加工,可转位刀片式钻头通常可以提供的加工循环时间和每孔加工成本,这是因为其刀具材料与孔壁的接触面较小,因此产生的摩擦也较小,可以采用更高的切削速度。
与高速钢钻头或整体硬质合金钻头相比,可转位刀
片式钻头还有一个优势——无需重磨和重新涂层。
不足之处是孔的加工精度(孔的位置精度和直径公差)比整体硬质合金钻头稍逊一筹,这是因为可转位钻头更容易发生挠曲变形。
为了大限度地减小钻头挠曲变形或提高孔的加工精度,可以采用各种不同的策略。
为了减小累积误差,可以采用精磨刀片,而不是用刀具的外周刃加工。
此外,还可以采用可调偏距的刀具夹头。
由于靠近中心处的刀片切削速度较低,因此其承受的切削力比靠近外缘处的刀片更大,从而会产生更大的偏斜力。
刀具设计工程师可以通过调整刀片在刀具内的分布位置,来抵消这种偏斜力。
无论采用何种类型的钻头,都可以先在不规则表面上进行预加工,然后钻削定心孔。
采用诸如此类的加工策略,可以根据用户的需求和当务之急,提高钻削加工性能。
由于模具制造业大量采用高硬度、高强度的工件材料,因此必须对刀片牌号与几何形状的组合进行评估。
由于中心刀片比外周刀片承受的切削力更大,因此通常需要采用非常强韧的刀片牌号和不容易崩刃的几何形状。
而外周刀片的切削速度更高,因此应采用耐磨性更好的硬质合金牌号,这种组合匹配可以优化加工性能。
内容来源网络,由“深圳机械展(11万㎡,1100多家展商,超10万观众)”收集整理!
更多cnc加工中心、车铣磨钻床、线切割、数控刀具工具、自动化、数字无人工厂、精密测量、3D打印、激光切割、钣金冲压折弯、精密零件加工等展示,就在深圳机械展.。