连接器耐久性与铜及铜合金带组织相关性研究
国家标准《端子连接器用铜及铜合金带》(送审稿)编制说明
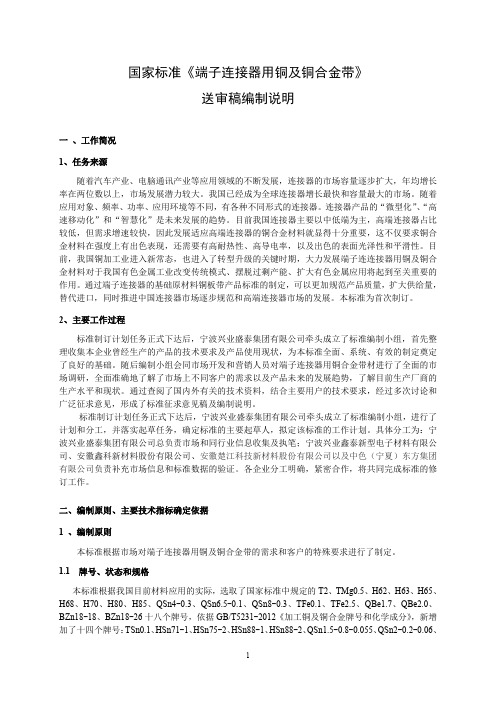
国家标准《端子连接器用铜及铜合金带》送审稿编制说明一、工作简况1、任务来源随着汽车产业、电脑通讯产业等应用领域的不断发展,连接器的市场容量逐步扩大,年均增长率在两位数以上,市场发展潜力较大。
我国已经成为全球连接器增长最快和容量最大的市场。
随着应用对象、频率、功率、应用环境等不同,有各种不同形式的连接器。
连接器产品的“微型化”、“高速移动化”和“智慧化”是未来发展的趋势。
目前我国连接器主要以中低端为主,高端连接器占比较低,但需求增速较快,因此发展适应高端连接器的铜合金材料就显得十分重要,这不仅要求铜合金材料在强度上有出色表现,还需要有高耐热性、高导电率,以及出色的表面光泽性和平滑性。
目前,我国铜加工业进入新常态,也进入了转型升级的关键时期,大力发展端子连连接器用铜及铜合金材料对于我国有色金属工业改变传统模式、摆脱过剩产能、扩大有色金属应用将起到至关重要的作用。
通过端子连接器的基础原材料铜板带产品标准的制定,可以更加规范产品质量,扩大供给量,替代进口,同时推进中国连接器市场逐步规范和高端连接器市场的发展。
本标准为首次制订。
2、主要工作过程标准制订计划任务正式下达后,宁波兴业盛泰集团有限公司牵头成立了标准编制小组,首先整理收集本企业曾经生产的产品的技术要求及产品使用现状,为本标准全面、系统、有效的制定奠定了良好的基础。
随后编制小组会同市场开发和营销人员对端子连接器用铜合金带材进行了全面的市场调研,全面准确地了解了市场上不同客户的需求以及产品未来的发展趋势,了解目前生产厂商的生产水平和现状。
通过查阅了国内外有关的技术资料,结合主要用户的技术要求,经过多次讨论和广泛征求意见,形成了标准征求意见稿及编制说明。
标准制订计划任务正式下达后,宁波兴业盛泰集团有限公司牵头成立了标准编制小组,进行了计划和分工,并落实起草任务,确定标准的主要起草人,拟定该标准的工作计划。
具体分工为:宁波兴业盛泰集团有限公司总负责市场和同行业信息收集及执笔;宁波兴业鑫泰新型电子材料有限公司、安徽鑫科新材料股份有限公司、安徽楚江科技新材料股份有限公司以及中色(宁夏)东方集团有限公司负责补充市场信息和标准数据的验证。
铜及铜合金的性能

铜及铜合金的性能成型性对于选择合金材料重要的是在冲压成型过程中能够获得所需要的几何形状的能力。
按治具的半径弯曲90 度或是更大的角度,也同时降低厚度来帮助弯曲定位,都是连接器冲制上常用的。
当合金充分退火后,绝大多数成形是可利用的,但在此条件下,强度会降低。
固体溶液的冷轧制和散粒硬质合金增加了强度,但却消耗了成型性能。
铸造方式有效地改变了回火性能,这可能由于它造成的加工硬化而损害了成型性能,或者由于其厚度降低而导致有助于成形。
连接器技术之 4.2.5 成型性--在它们制程中的大量的冷加工所发展起来的更高强度的回火结构也可能在一个方向上比在另一个方向上表现出更好的成型性能。
当可能时,最大的成形能力出现在弯曲轴线垂直于卷曲方向。
这个方向是首选的,因为它常常比另一方向的回火能具有更好的成型性。
在这个方向上的成形称之为径向的,因为它指出了随弯曲的进行金属流动的方向。
对应到平行于轧制方向的弯曲轴线的成形则称之为纬向的。
纬向弯曲上最小的可接受半径能比经向上更大,特别对于高温回火的固溶合金和散布强化合金。
在连接器壳体部分中90 度的弯曲常常朝向窄条导向以利用纵向的成型性。
窄条能形成而不产生裂缝的冲模最小范围为由设计者和制造商所共同支持的合金窄条所定义,其中的裂缝定义为一不可接受的粗糙表面。
材料的工作性能可以从弯曲的最小弯曲半径(MBR)而得知,由窄条厚度(t)所分割。
较小的MBR/t 值表明有较好的成型性。
连接器技术之 4.2.5 成型性--图表4.5 中总结了所选择合金的相关成型性。
此图表表明了名义上可拉伸强度其其每一合金可接受的最小弯曲(MBR/t value)在其纵向上和横向上从1到1.5。
在冲压工具中的实际性能与此有些不同。
此图表中所示的强度在纵向上较高,这样与通常此方向上的成型性较好是一致的。
此图表同样表明了铜合金的一个与其独立的强度来源相关的总趋势。
此固体溶解强化合金可提供一较高的强度,从而能使规定的最小成型性比固溶合金以及散布强化合金要小,因为此成形过程与其冷工作下性能的相关性很小。
铜及铜合金的焊接

铜及铜合金的焊接铜合金的制造铜合金材料在运用于连接器的加工过程中,先是被加工成为薄片状的板材,然后切成条带形状以适应后面的冲压过程的需要。
线材同样应用于连接器中,但是在端子组件和其他类型的连接器中这样的材料应用得很少。
图4.1描述了一个典型的薄板和条带铜合金的制造流程。
此外在参考书目3中可以得到更详细的描述。
合金线材以同样的方式制造但具有几个显著的特点:热挤压,轧制,和通过冲模的拉拔以改变热轧制和冷轧制在板材中的应用,以及退火处理过程经常用于这种产品。
连接器技术之4.1.1 铜合金的制造溶炼和铸造铜合金是最先用于可回收的商业应用的金属之一,这是因为工业上能用经济的办法将铜合金中的杂质维持在一个较低的水平。
溶炼常用于电溶炉之中而少见于铜合金在真空和惰性气体下的溶炼和铸造过程中。
碳层能提供一足够的保护。
此外,利用真空或特殊的空气环境将会很大的增加合金制造的成本。
氢、氧和碳的污染影响由溶炼过程和热力学方法来平衡其溶炼层进行控制,其中氢能溶解于铜,氧能与铜和一些合金元素形成氧化物,而碳能与有碳化物组分的合金起反应。
溶炼控制包括纯电解阴极铜和有选择的兼容合金碎屑。
当一些纯组分如镍、锡、硅或起支配作用的合金如磷、铍、和铬合金组分增加时,都会引起合金成份改变。
板材锻造的制造过程是从不连续的铸造成大矩形横截面金属锭或薄铸片开始的。
前述大金属锭的典型尺寸为约150 毫米厚,300 到900 毫米宽,并且经过热轧制处理以有效的减少其厚度并消除在铸造过程中残余的铸造微片。
另一种铸造方法是薄铸片(常用于窄条状铸造材料),其典型的尺寸是约15 毫米厚,150 到450 毫米宽,这些薄铸片将直接转到冷轧过程之中。
选择条形铸造是基于经济上的考虑因素(热研磨需要较高的资金成本)以及合金的特性(一些铜合金不容易在热条件下工作)。
前述半连续且大的金属锭在铸造过程中垂直利用一个中空水冷的铜模,在开始时此铜模的下底部被封住。
溶化的金属实际上并未象图4.1中所示的直接进入溶模。
铜及铜合金的金相组织分析

铜及铜合金的金相组织分析一)结晶过程的分析结晶是以树枝状的方式生长,树枝状的结晶容易造成夹渣外,通常形成显微疏松。
取决于模壁的冷却速度外,还取决于合金成分、熔化与浇注温度等。
(二)宏观分析中常见缺陷在浇注过程中往往产生缩孔、疏松、气孔、偏析等缺陷。
浇注温度和浇注方式的影响,铸锭、紫铜中容易出现气孔和皮下气孔。
由于合金元素的熔点、比重不一,熔炼工艺不当造成铸锭的成分偏析。
铸造时热应力可产生裂纹。
浇注工艺不当(浇注温度过低),浇注时金属液的中断会造成冷隔。
(三)微观分析与铜相互作用的性质,杂质可分三类:1.溶解在固态铜中的元素(铝、铁、镍、锡、锌、银、金、呻、锑)。
2.与铜形成脆性化合物的元素(硫、氧、磷等)。
3.实际上不溶于固态铜中与铜形成易熔共晶的元素(铅、铋等)。
铋与铜形成共晶呈网状分布于铜的基体上,淡灰色。
铅含量很少时和铋一样呈网状分布于晶界,其颜色为黑色;铅含量大时在铜的晶粒间界上呈单独的黑点。
暗场观察:铅点呈黑色,孔洞为亮点。
硫与氧的观察:均与铜形成化合物(Cu2S Cu2O,又以共晶形式(Cu2S+ Cu、Cu20+ CU分布在铜的晶界上。
氯化高铁盐酸水溶液浸蚀:Cu20变暗,Cu2S不浸蚀。
偏振光观察:Cu20呈暗红色。
QJ 2337-92铍青铜的金相试验方法金相分析晶粒度检测金属显微组织分析,晶粒度分析,GB/T 6394-02金属平均晶粒度测定方法ASTM E 112-96 (2004)金属平均晶粒度测定方法YS/T 347-2004铜及铜合金平均晶粒度测定方法GB/T13298-91金属显微组织检验方法GB/T 13299-91钢的显微组织评定方法GB/T 10561-2005钢中非金属夹杂物含量的测定标准评级图显微检验法ASTM E45-05钢中非金属夹杂物含量测定方法GB/T 224-87钢的脱碳层深度测定方法ASTM E407-07金属及其合金的显微腐蚀标准方法GB/T 226-91钢的低倍组织及缺陷酸蚀检验方法GB/T 1979-2001结构钢低倍组织缺陷评级图GB/T 5168-85两相钛合金高低倍组织GB/T 9441-1988球墨铸铁金相检验ASTM A 247-06铸件中石墨微结构评定试验方法GB/T 7216-87灰铸铁金相EN ISO 945:1994石墨显微结构GB/T 13320-07钢质模锻件金相组织评级图及评定方法CB 1196-88船舶螺旋桨用铜合金相含量金相测定方法JB/T 7946.1-1999铸造铝合金金相铸造铝硅合金变质JB/T 7946.2-1999铸造铝合金金相铸造铝硅合金过烧JB/T 7946.3-1999铸造铝合金金相铸造铝氧是铜中最常见的杂质,可产生氢脆。
铜及铜合金高精度板带材生产技术和发展

铜及铜合金高精度板带材生产技术和发展摘要:铜及铜合金板带材是重要的铜加工产品,随着电子信息产业的高速发展,铜及铜合金板带材消费量呈逐年上升的趋势,是目前所有加工材中,最具活力的高技术、高附加值产品。
本文就铜及铜合金板带材生产的工艺技术作简要介绍。
关键词:铜及铜合金、板带材、高精度、生产工艺1前言铜及铜合金板带材是重要的铜加工产品,占世界铜加工总量的35%。
近十年来,世界经济蓬勃发展,特别是以中国为代表的新兴发展中国家,国民经济高速发展,带动了铜及铜合金板带材需求量。
铜及铜合金带材是铜加工材的重要品种,广泛应用于电子、电气、轻工、仪器仪表等各个领域,特别是随着电子信息产业的高速发展,铜及铜合金板带材消费量呈逐年上升的趋势,是目前所有加工材中,最具活力的高技术、高附加值产品。
产品主要用于制造电连接器用接插件、集成电路引线框架、汽车水箱散热管片、汽车端子、同轴电缆、干式变压器和电子开关领域,形成了以纯铜、黄铜、引线框架用高铜合金、锡磷青铜、锌白铜为代表的高精板带材合金系列。
2铜及铜合金高精度板带材生产2.1高精度板带材的特点所谓高精度合金是指具有均匀物理性能的合金,其化学成分准确、合金不含夹杂、组织状态均匀和高的制作精度。
其具有高质量、高精度和大卷重的特性。
随着生产技术的不断创新,设备不断更新,精密铜板带的生产技术达到很高的水平,为了提高生产效率和成材率,提高性能、公差的一致性,单位宽度重量已超过15kg/mm,卷重可达到20吨以上,轧制速度达1200m/min,厚度精度可控制在±0.003mm以内,表面质量和板形都达到很高的水平。
2.2生产工艺特点高精度、大卷重、高质量铜及铜合金板带材的生产工艺主要有两种方法:一为热轧开坯生产工艺,二为水平连铸供坯冷轧生产工艺。
前者采用大容量熔铸机组铸成大规格铸锭,经热轧开坯、双面铣削后再经冷轧、退火、精整等工序出成品;后者采用水平连铸直接从保温炉中引出厚度为15~18mm带坯,经在线或离线双面铣削后成卷,再经冷轧、退火、精整等工序出成品。
铜合金接触线的研究现状
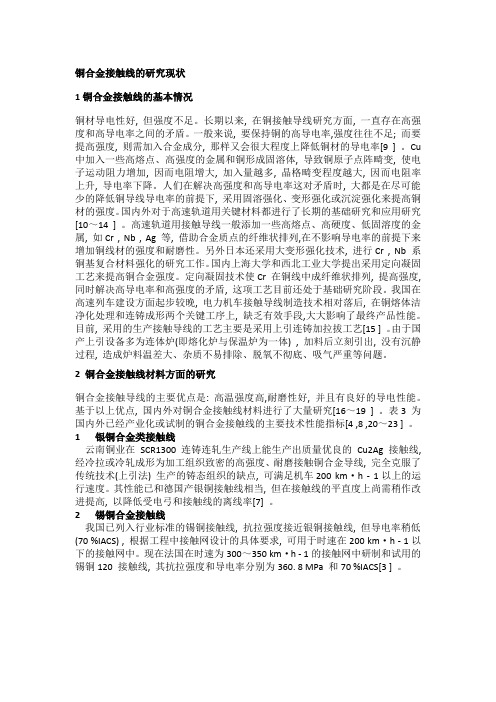
铜合金接触线的研究现状1铜合金接触线的基本情况铜材导电性好, 但强度不足。
长期以来, 在铜接触导线研究方面, 一直存在高强度和高导电率之间的矛盾。
一般来说, 要保持铜的高导电率,强度往往不足; 而要提高强度, 则需加入合金成分, 那样又会很大程度上降低铜材的导电率[9 ] 。
Cu 中加入一些高熔点、高强度的金属和铜形成固溶体, 导致铜原子点阵畸变, 使电子运动阻力增加, 因而电阻增大, 加入量越多, 晶格畸变程度越大, 因而电阻率上升, 导电率下降。
人们在解决高强度和高导电率这对矛盾时, 大都是在尽可能少的降低铜导线导电率的前提下, 采用固溶强化、变形强化或沉淀强化来提高铜材的强度。
国内外对于高速轨道用关键材料都进行了长期的基础研究和应用研究[10~14 ] 。
高速轨道用接触导线一般添加一些高熔点、高硬度、低固溶度的金属, 如Cr , Nb , Ag 等, 借助合金质点的纤维状排列,在不影响导电率的前提下来增加铜线材的强度和耐磨性。
另外日本还采用大变形强化技术, 进行Cr , Nb 系铜基复合材料强化的研究工作。
国内上海大学和西北工业大学提出采用定向凝固工艺来提高铜合金强度。
定向凝固技术使Cr 在铜线中成纤维状排列, 提高强度, 同时解决高导电率和高强度的矛盾, 这项工艺目前还处于基础研究阶段。
我国在高速列车建设方面起步较晚, 电力机车接触导线制造技术相对落后, 在铜熔体洁净化处理和连铸成形两个关键工序上, 缺乏有效手段,大大影响了最终产品性能。
目前, 采用的生产接触导线的工艺主要是采用上引连铸加拉拔工艺[15 ] 。
由于国产上引设备多为连体炉(即熔化炉与保温炉为一体) , 加料后立刻引出, 没有沉静过程, 造成炉料温差大、杂质不易排除、脱氧不彻底、吸气严重等问题。
2 铜合金接触线材料方面的研究铜合金接触导线的主要优点是: 高温强度高,耐磨性好, 并且有良好的导电性能。
基于以上优点, 国内外对铜合金接触线材料进行了大量研究[16~19 ] 。
铜及铜合金的焊接
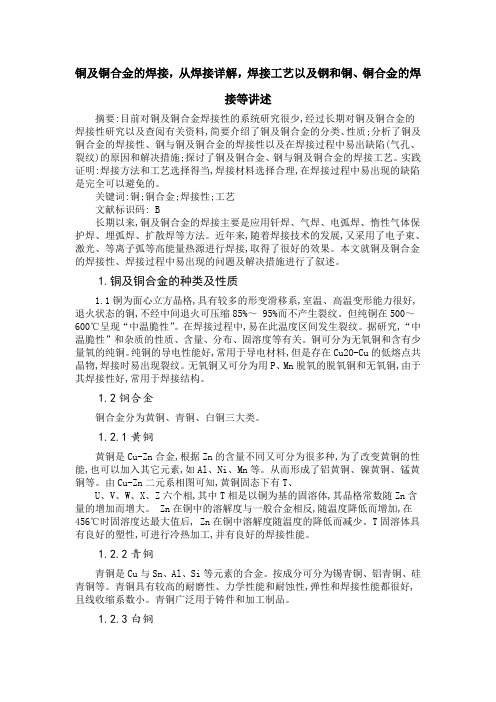
铜及铜合金的焊接,从焊接详解,焊接工艺以及钢和铜、铜合金的焊接等讲述摘要:目前对铜及铜合金焊接性的系统研究很少,经过长期对铜及铜合金的焊接性研究以及查阅有关资料,简要介绍了铜及铜合金的分类、性质;分析了铜及铜合金的焊接性、钢与铜及铜合金的焊接性以及在焊接过程中易出缺陷(气孔、裂纹)的原因和解决措施;探讨了铜及铜合金、钢与铜及铜合金的焊接工艺。
实践证明:焊接方法和工艺选择得当,焊接材料选择合理,在焊接过程中易出现的缺陷是完全可以避免的。
关键词:铜;铜合金;焊接性;工艺文献标识码: B长期以来,铜及铜合金的焊接主要是应用钎焊、气焊、电弧焊、惰性气体保护焊、埋弧焊、扩散焊等方法。
近年来,随着焊接技术的发展,又采用了电子束、激光、等离子弧等高能量热源进行焊接,取得了很好的效果。
本文就铜及铜合金的焊接性、焊接过程中易出现的问题及解决措施进行了叙述。
1.铜及铜合金的种类及性质1.1铜为面心立方晶格,具有较多的形变滑移系,室温、高温变形能力很好,退火状态的铜,不经中间退火可压缩85%~ 95%而不产生裂纹。
但纯铜在500~600℃呈现“中温脆性”。
在焊接过程中,易在此温度区间发生裂纹。
据研究,“中温脆性”和杂质的性质、含量、分布、固溶度等有关。
铜可分为无氧铜和含有少量氧的纯铜。
纯铜的导电性能好,常用于导电材料,但是存在Cu2O-Cu的低熔点共晶物,焊接时易出现裂纹。
无氧铜又可分为用P、Mn脱氧的脱氧铜和无氧铜,由于其焊接性好,常用于焊接结构。
1.2铜合金铜合金分为黄铜、青铜、白铜三大类。
1.2.1黄铜黄铜是Cu-Zn合金,根据Zn的含量不同又可分为很多种,为了改变黄铜的性能,也可以加入其它元素,如Al、Ni、Mn等。
从而形成了铝黄铜、镍黄铜、锰黄铜等。
由Cu-Zn二元系相图可知,黄铜固态下有T、U、V、W、X、Z六个相,其中T相是以铜为基的固溶体,其晶格常数随Zn含量的增加而增大。
Zn在铜中的溶解度与一般合金相反,随温度降低而增加,在456℃时固溶度达最大值后, Zn在铜中溶解度随温度的降低而减少。
高导电高耐热铜合金及铜基复合材料的研究现状与展望

高导电高耐热铜合金及铜基复合材料的研究现状与展望
王佳睿;张翔;何春年;赵乃勤
【期刊名称】《铸造技术》
【年(卷),期】2024(45)1
【摘要】高导耐热铜基材料作为现代高新技术用关键材料之一,已被广泛应用于轨道交通、电子通信和航空航天等领域。
本文从铜合金和铜基复合材料两大领域入手,介绍了常见高导耐热铜材料的设计思路、制备方法、微观组织结构、力学性能和物理性能,并对其导电机制和高温强化机理进行了归纳和阐释,最后对高导耐热铜基材料的研究现状和未来发展进行了总结与展望。
【总页数】26页(P1-26)
【作者】王佳睿;张翔;何春年;赵乃勤
【作者单位】天津大学材料科学与工程学院
【正文语种】中文
【中图分类】TG146.1
【相关文献】
1.高强高导电铜合金的研究现状及展望
2.高强度高导电性铜合金研究现状及展望
3.高强度高导电铜基复合材料制备技术回顾与展望
4.高强高导高耐热铜合金的研究进展与展望
5.高强度、高导电铜合金及铜基复合材料研究进展
因版权原因,仅展示原文概要,查看原文内容请购买。
- 1、下载文档前请自行甄别文档内容的完整性,平台不提供额外的编辑、内容补充、找答案等附加服务。
- 2、"仅部分预览"的文档,不可在线预览部分如存在完整性等问题,可反馈申请退款(可完整预览的文档不适用该条件!)。
- 3、如文档侵犯您的权益,请联系客服反馈,我们会尽快为您处理(人工客服工作时间:9:00-18:30)。
连接器耐久性与铜及铜合金带组织相关性研究张鑫【摘要】从连接器的重要基础材料之一铜及铜合金带组织性能出发,分析了该性能与连接器耐久性的相关性.铜及铜合金带的织构组织和晶粒尺寸与连接器耐久性能直接相关.【期刊名称】《汽车电器》【年(卷),期】2018(000)002【总页数】3页(P45-46,49)【关键词】连接器;耐久性;铜带;组织【作者】张鑫【作者单位】安费诺商用电子产品(成都)有限公司,四川成都 611731;陶朗分选技术(厦门)有限公司,福建厦门 361006【正文语种】中文【中图分类】U463.6耐久性是连接器可靠性的一个重要参数。
对于如何测试连接器的耐久性,国内外都制定了相应的标准,如国外的EIA-364-09C[1]和国内GB/T5095—1997(等效于IEC 512—1993)[2]。
由于耐久性测试属于破坏性试验,需要较多的时间和成本,电子元件厂或成品厂在产品的型式试验、验证阶段使用该测试方法。
为了保证连接器的耐久性,连接器行业设计者多采用最大应力方法或名义应力法设计连接器的结构。
即通过有限元等设计方法保证在使用过程中的最大应力或名义应力小于材料的屈服强度,并根据应力-寿命曲线(S-N曲线)计算连接器的耐久性[3-8]。
虽然最大应力方法或名义应力法在理论上解决了连接器的耐久性的计算问题,但在实际连接器的使用中,却常常出现连接器的耐久性与理论数据不一致的现象,给使用者带来了不必要的损失。
如何解决这个品质隐患,是连接器制造厂商及使用者需要共同面对的问题。
国内外学者从连接器设计选材参数、正向力或插拔力、电镀材料、表面粗糙度、润滑条件等方面出发,对提高连接器耐久性做了大量研究。
铜及铜合金带是连接器最重要的基础材料之一,但对铜及铜合金带的本身性能与连接器的耐久性相关性研究较少。
1 连接器端子结构连接器的端子一般具有需求量大、超薄、形状复杂、精度高等特点,通常采用连续模料带的形式在高速精密冲床上冲压制成。
端子一般由头部弯曲结构和细长悬臂结构组成[9],如图1所示。
为了提高生产效率和节省成本,经过高速冲压和电镀后,在连接器装配工序,生产者才将端子从料带上裁切下来进行组装。
图1 连接器端子图2 铜及铜合金带组织及特性经过多年的铜合金带制造的发展,连接器用铜及铜合金带主要制造方法可以简述为:半连续铸造或连续铸造、铣毛坯面、多次轧制(包括多次热处理)、精整、表面处理等生产工序[10]。
由于铜及铜合金带的轧制加工过程是沿着轧制方向的单向轧制,随着轧制变形程度的增大,铜及铜合金带的晶体逐渐形成轧制织构。
再加上轧制后热处理的不同和热处理前轧制变形程度的不同,铜及铜合金带的晶体会出现不同的再结晶织构。
织构会给铜及铜合金带不同方向的物理及力学性能带来不一致现象,即各向异性。
如在国内外研究和实践证明,铜及铜合金带材纵向弯曲方向(Good Way)和横向弯曲方向(Bad Way)的弯曲性能存在较大差异[11],一般情况下,铜及铜合金带材纵向性能好于横向性能。
铜及铜合金带的横向弯曲方向(Bad Way)和纵向弯曲方向(Good Way)定义见图2[11]。
图2 铜及铜合金带的横向、纵向弯曲方向定义图在国内标准YS/T 1041—2015《汽车端子连接器用铜及铜合金带》[12]和GB/T 26007—2010《弹性元件和接插件用铜带》[13],及其美国ASTMB888/888M-13 《电连接器或弹簧触点生产用铜合金带材的标准规范》[14]都明确定义了铜及铜合金带材的纵向、横向弯曲参数的不同。
铜及铜合金带在弯曲变形时,外侧表面发生类似拉伸试验的变形。
弯曲过程中外侧表面层拉伸不断增加,逐渐产生弹性变形、塑性变形直至开裂。
铜及铜合金带材的纵向弯曲性能优于横向弯曲性能,也表明铜及铜合金带材的纵向抗拉强度或屈服强度优于横向方向,并得到大量的试验证明[15]。
3 相关性研究3.1 横向方向的屈服强度由于国家标准GB/T 26007—2010和YS/T 1041—2015等规定的铜及铜合金带的抗拉强度、屈服强度都是纵向方向的参数。
连接器设计者在设计连接器寿命时,都以纵向方向的参数为依据。
由于成本等压力,连接器的端子普遍采用点镀金等贵金属的电镀方式,连接器端子大多数分布在横向方向(图1)。
即在连接器耐久性的设计参数与实际参数存在不一致现象。
而冲压工厂或连接器工厂收到的铜及铜合金带时,已经不易测试出横向方向的具体强度。
多数工厂使用维氏硬度来复核来料的强度性能,这种方法存在较大误差,也不能区别纵向和横向参数差异。
这是部分连接器实际机械寿命小于设计寿命的原因之一。
在铜带分条前,铜带工厂可以较方便地测试出铜及铜合金带的横向方向的抗拉强度、屈服强度、延伸率等参数。
为了保证连接器的耐久性,连接器工厂需要铜带厂提供铜及铜合金带的纵向和横向机械强度参数。
3.2 弯曲性能R/T值铜及铜合金带的弯曲性能R/T值直接影响连接器端子的成型能力。
在美国标准ASTM B820《测定铜及铜合金带材可成形性的弯曲试验的试验方法》[16]和国内YS/T 1041—2015《汽车端子连接器用铜及铜合金带》都要求纵向弯曲和横向弯曲方向取样测试。
只是美国标准要求采用了弯曲试验后使用30X放大仪器观察,试样弯曲外表面无可见裂纹的判定方法。
而国内标准要求使用肉眼观察试样弯曲外表面无可见裂纹。
理论上分析,按照国内标准检验的铜及铜合金带的弯曲性能比依照美国标准检验的铜及铜合金带差。
由此材料制造的连接器耐久性也比依照美国标准检验的铜及铜合金基材的连接器差。
为了提高连接器的耐久性,连接器工厂及铜带制造厂应使用更严格的标准检查铜及铜合金的弯曲性能R/T值。
3.3 晶粒大小与均匀性现阶段,细化晶粒(包括晶粒均匀性)是铜带厂一种常用的提高铜及铜合金带力学性能的手段。
随着超细晶和纳米晶粒的研究和实验,在一定范围内晶粒尺寸可以作为主导因素作用于铜及铜合金带的力学性能;在该范围外,作用铜及铜合金带的力学性能的主导因素将发生改变,霍尔-佩奇(Hall-Petch)公式将不再有效,即出现反霍尔-佩奇现象[17]。
在纳米晶粒研究中,晶粒尺寸分布也会很大程度上影响铜及铜合金带的力学性能,研究者发现双模晶粒分布的铜及铜合金材料具有很好的拉伸韧性,同时还保持原高于其他细晶粒材料的强度[18]。
在铜及铜合金带的大批量工业生产中,适用霍尔-佩奇(Hall-Petch)公式还占主导地位。
国内的工业化铜及铜合金带的细晶粒尺寸控制在10μm左右,个别铜带可以控制细晶粒尺寸在5μm左右。
德国、日本等国家使用累积叠轧(同步叠轧制)等技术,实现了超细晶粒铜带的工业化生产[19],其高端工业化铜及铜合金带的细晶粒尺寸已经控制在1~5μm。
在连接器实际使用过程中,晶粒尺寸小和均匀性好的铜及铜合金带具有更好的力学性能,由其制造的连接器的耐久性也更好。
4 结论1)由于铜及铜合金带制造的各向异性,轧制方向(纵向)的屈服强度好于垂直轧制方向(横向),连接器设计者在设计连接器时,应以垂直轧制方向的屈服强度为设计依据。
2)连接器用铜带制造厂应根据连接器端子的制造特点和连接器使用特点,在轧制方向(纵向)的机械性能基础上,提供并保证垂直轧制(横向)屈服强度。
3)在铜及铜合金带弯曲性能测试严苛性和适用性上,ASTM B820-14a高于我国现行标准。
使用更严苛标准测试的铜及铜合金带的产品的耐久性和机械寿命也越高。
4)在霍尔-佩奇(Hall-Petch)公式适用的范围内,拥有更小的晶粒尺寸的铜及铜合金带可以增加连接器的耐久性。
参考文献:[1] EIA-364-09C,Durability Test Procedure for Electrical Connectorsand Contacts[S]. 1999.[2] GB/T 5095,电子设备用机电元件基本试验规程及测量方法[S].1997. [3]丁元淇,康金,杜艳平,等.车用连接器端子的结构仿真分析[J].汽车电器,2016(7):51-53.[4]张忠明,服部修次,田川纪英,等.铜合金的疲劳寿命预测[J].材料热处理学报,2005,26(5):76-79.[5]林叶芳,江丙云,闫金金,等.连接器端子件的结构分析及其优化研究[J].机械设计与制造,2015(9):215-218.[6]杜永英,孔志礼,吕春梅,等.基于ANSYS某型电连接器拔插过程的可靠性分析[J].中国工程机械学报,2015,13(6):545-549.[7]陈田海.基于名义应力法的微型连接器疲劳寿命预测研究[J].机电元件,2009,29(4):20-24.[8]王帅,吴运新,滑广军,等. 一种修正金属材料S-N曲线的新方法探讨[J].热加工工艺,2011,40(8):35-37.[9]黄珍媛,郭雷,周驰,等.连接器端子悬臂变形问题的工艺预防[J].锻压技术,2008,33(6):93-96.[10]兰利亚,李耀群,杨海云,等.铜及铜合金精密带材生产技术[M].北京:冶金工业出版社,2009.[11]涂德华,张鑫.铜及铜合金带弯曲试验标准对比研究[J].四川理工学院学报(自然科学版),2016,29(5):43-46.[1 2] YS/T1041,汽车端子连接器用铜及铜合金带[S]. 2015.[1 3] GB/T26007,弹性元件和接插件用铜带[S]. 2010.[14] ASTM B888/888M-13.Standard Specification for Copper Alloy Strip for Use in Manufacture of Electrical Connectors or Spring Contacts [S]. 2013.[15]易志辉.C2680黄铜带材弯曲性能的研究[J].铜业工程,2014(34):5-10.[16] ASTM B820-14a,Standard Test Method for Bend Test for Determining the Formability of Copper and Copper Alloy Strip. [S].2014. [17]贾少伟,张郑,王文,等. 超细晶/纳米晶反Hall-Petch变形机制最新研究进展[J].材料导报, 2015(23): 114-118.[18]王玉臻,毛泽宁,赵永好.EBSD半原位研究双模晶粒分布铜的变形机理[J].材料科学与工程学报,2015,33(3):343-351.[19]王军丽,史庆南,钱天才,等.大变形异步叠轧技术制备高强高导超细晶铜材研究[J].航空材料学报,2010,30(3):14-18.。