锌酸盐镀锌故障分析
镀锌设备故障维修方案

镀锌设备故障维修方案背景介绍镀锌是将钢铁表面镀上锌层,以起到防腐、美化和增加表面硬度的作用。
在镀锌生产过程中,设备是关键因素之一。
如果设备遇到故障或出现问题,将会严重影响生产效率和质量。
因此,制定一套科学合理的设备故障维修方案对于保障生产过程非常重要。
故障分类在镀锌生产中,设备可能遇到的故障主要可以分为以下几类:1.机械故障。
例如轴承损坏、带宽脱落等。
2.电气故障。
例如电机接线松动、电源过载等。
3.管道故障。
例如管道堵塞、漏水等。
4.其他故障。
例如变频器失控、传感器损坏、机器人误差增大等。
故障处理流程在设备出现故障时,应该采取以下流程进行处理:1.确认故障种类和具体表现。
2.停机并切断电源,防止二次损失。
3.确认故障原因,排除可能原因。
4.按照故障原因进行修理或更换部件。
5.安装好后,进行安全检查和运行测试。
6.恢复生产并记录处理过程。
设备维护为了预防设备故障的发生,设备维护也非常重要。
以下是常用的设备维护方法:1.定期检查设备,发现问题及时处理。
2.更换易损件和磨损较大的部分。
3.按时加油和润滑,保证设备正常运行。
4.监测设备的运行情况,及时调整机器参数。
5.对设备进行清洁和除尘,排除污垢和异物等。
总结针对镀锌设备故障,制定科学合理的处理方案对于保障生产效率和质量非常重要。
要根据故障种类进行分类处理,并严格按照处理流程进行,保证设备维修质量。
同时,要注重设备的维护工作,预防故障的发生。
通过科学管理和维护,保障设备的长期稳定运行。
锌酸盐镀锌工艺的故障原因与处理方法
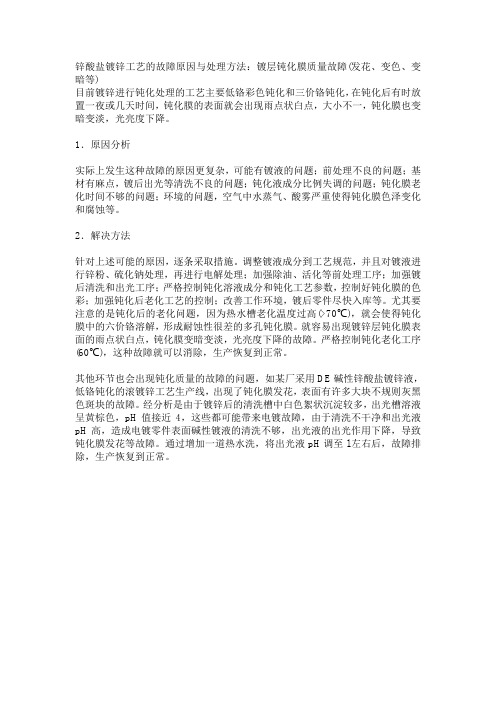
锌酸盐镀锌工艺的故障原因与处理方法:镀层钝化膜质量故障(发花、变色、变暗等)目前镀锌进行钝化处理的工艺主要低铬彩色钝化和三价铬钝化,在钝化后有时放置一夜或几天时间,钝化膜的表面就会出现雨点状白点,大小不一,钝化膜也变暗变淡,光亮度下降。
1.原因分析实际上发生这种故障的原因更复杂,可能有镀液的问题;前处理不良的问题;基材有麻点,镀后出光等清洗不良的问题;钝化液成分比例失调的问题;钝化膜老化时间不够的问题;环境的问题,空气中水蒸气、酸雾严重使得钝化膜色泽变化和腐蚀等。
2.解决方法针对上述可能的原因,逐条采取措施。
调整镀液成分到工艺规范,并且对镀液进行锌粉、硫化钠处理,再进行电解处理;加强除油、活化等前处理工序;加强镀后清洗和出光工序;严格控制钝化溶液成分和钝化工艺参数,控制好钝化膜的色彩;加强钝化后老化工艺的控制;改善工作环境,镀后零件尽快入库等。
尤其要注意的是钝化后的老化问题,因为热水槽老化温度过高(>70℃),就会使得钝化膜中的六价铬溶解,形成耐蚀性很差的多孔钝化膜。
就容易出现镀锌层钝化膜表面的雨点状白点,钝化膜变暗变淡,光亮度下降的故障。
严格控制钝化老化工序(60℃),这种故障就可以消除,生产恢复到正常。
其他环节也会出现钝化质量的故障的问题,如某厂采用DE碱性锌酸盐镀锌液,低铬钝化的滚镀锌工艺生产线,出现了钝化膜发花,表面有许多大块不规则灰黑色斑块的故障。
经分析是由于镀锌后的清洗槽中白色絮状沉淀较多,出光槽溶液呈黄棕色,pH值接近4,这些都可能带来电镀故障,由于清洗不干净和出光液pH高,造成电镀零件表面碱性镀液的清洗不够,出光液的出光作用下降,导致钝化膜发花等故障。
通过增加一道热水洗,将出光液pH调至l左右后,故障排除,生产恢复到正常。
镀锌的方法
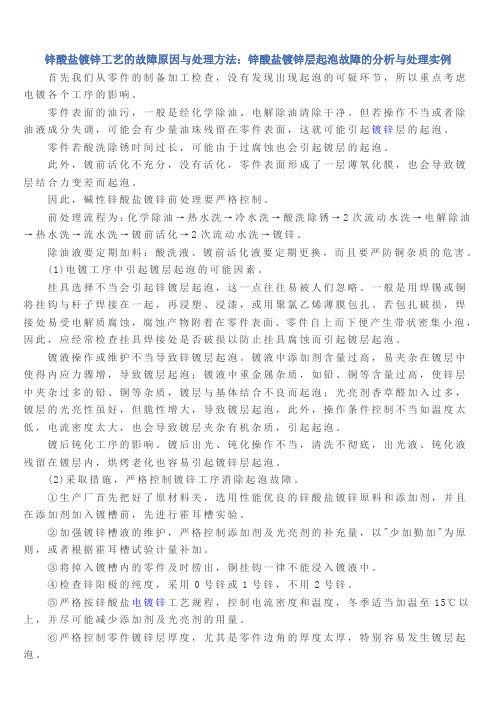
锌酸盐镀锌工艺的故障原因与处理方法:锌酸盐镀锌层起泡故障的分析与处理实例首先我们从零件的制备加工检查,没有发现出现起泡的可疑环节,所以重点考虑电镀各个工序的影响。
零件表面的油污,一般是经化学除油、电解除油清除干净。
但若操作不当或者除油液成分失调,可能会有少量油珠残留在零件表面,这就可能引起镀锌层的起泡。
零件若酸洗除锈时间过长,可能由于过腐蚀也会引起镀层的起泡。
此外,镀前活化不充分,没有活化,零件表面形成了一层薄氧化膜,也会导致镀层结合力变差而起泡。
因此,碱性锌酸盐镀锌前处理要严格控制。
前处理流程为:化学除油→热水洗→冷水洗→酸洗除锈→2次流动水洗→电解除油→热水洗→流水洗→镀前活化→2次流动水洗→镀锌。
除油液要定期加料;酸洗液、镀前活化液要定期更换,而且要严防铜杂质的危害。
(1)电镀工序中引起镀层起泡的可能因素。
挂具选择不当会引起锌镀层起泡,这一点往往易被人们忽略。
一般是用焊锡或铜将挂钩与杆子焊接在一起,再浸塑、浸漆,或用聚氯乙烯薄膜包扎。
若包扎破损,焊接处易受电解质腐蚀,腐蚀产物附着在零件表面、零件自上而下便产生带状密集小泡,因此,应经常检查挂具焊接处是否破损以防止挂具腐蚀而引起镀层起泡。
镀液操作或维护不当导致锌镀层起泡。
镀液中添加剂含量过高,易夹杂在镀层中使得内应力骤增,导致镀层起泡;镀液中重金属杂质,如铅、铜等含量过高,使锌层中夹杂过多的铅、铜等杂质,镀层与基体结合不良而起泡;光亮剂香草醛加入过多,镀层的光亮性虽好,但脆性增大,导致镀层起泡,此外,操作条件控制不当如温度太低,电流密度太大,也会导致镀层夹杂有机杂质,引起起泡。
镀后钝化工序的影响。
镀后出光、钝化操作不当,清洗不彻底,出光液、钝化液残留在镀层内,烘烤老化也容易引起镀锌层起泡。
(2)采取措施,严格控制镀锌工序消除起泡故障。
①生产厂首先把好了原材料关,选用性能优良的锌酸盐镀锌原料和添加剂,并且在添加剂加入镀槽前,先进行霍耳槽实验。
②加强镀锌槽液的维护,严格控制添加剂及光亮剂的补充量,以"少加勤加"为原则,或者根据霍耳槽试验计量补加。
用酒石酸钾钠解决锌酸盐镀锌层发花问题
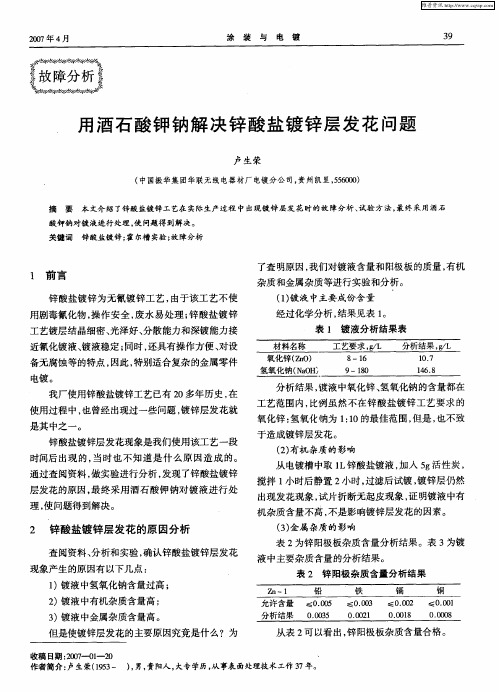
杂质和金属杂质等进行实验和分析。
() 液 中主要 成份 含 量 1镀
经过化学分析, 结果见表 1 。
表 1 镀 液分析 结果 表
材料名称
氧化锌 (n ) z0 氢氧化钠 ( a H NO
近氰化镀液、 镀液稳定 ; 同时, 还具有操作方便 、 对设 备无腐蚀等的特点 , 因此, 特别适合复杂的金属零件
半 光 亮
电 流 密度 增 大
光亮
锌分别与分析纯氢氧化钠、 工业级氢氧化钠( 工人加 料剩下的)不经过处 理按工艺参数 的 中限各配制 ,
1 L镀锌 溶液 , 加入 光亮 剂 , 霍尔槽 试验 。 做 试验条 件 : 电流 2 温度 室 温 , 间 1 钟 , A, 时 0分 结 果 如 图 1图 2 ,
酸钾钠对镀 液进行 处理 , 问题得到解决。 使 关键词 锌 酸盐镀锌 ; 尔槽 实验 ; 障分析 霍 故
了查 明原 因 , 我们 对镀液 含 量和 阳极板 的质 量 , 有机
1 前 言
锌酸盐镀锌为无氰镀锌工艺 , 由于该工艺不使 用剧毒氰化物, 操作安全 , 废水易处理 ; 锌酸盐镀锌 工艺镀层结晶细密 、 光泽好、 分散能力和深镀能力接
镀
2O O7年第 2 期
表 3 镀 液 中主要金 属 杂质含 量分析 结果
4 采取措施消 除镀锌层发花现象
通 常 , 理锌 酸盐镀 液 中的金 属杂质 , 处 采用 锌粉 或C K一78但是 , 7, 处理 时 间长 、 作 烦琐 , 别是 遇 操 特
从表 3看 出 , 杂质含 量超标 , 步判定 这是 影 铁 初 响锌 镀层 发花 的 因素 。 锌酸盐 镀锌 的 主要材 料为氧 化锌 、 氢氧 化钠 , 该
锌酸盐镀锌溶液的故障分析及处理

锌酸盐镀锌溶液的故障分析及处理吴双成【摘要】镀锌是电镀行业最基本、生产量最大的镀种.对两例锌酸盐镀锌故障进行了分析和处理,新配镀液如果所用原料纯度不高往往发生故障.向镀液中添加0.5~1g/L铝粉,可以置换出铅、镉、铁、铜、镍及铬等杂质离子,消除不良影响.铝粉可以还原Cr(Ⅵ)为Cr(Ⅲ),在强碱性镀锌溶液中Cr(Ⅲ)以亚铬酸盐的形式存在,铝粉还可以置换碱性溶液中的Cr(Ⅲ).用铝粉处理后,排除了故障.【期刊名称】《电镀与精饰》【年(卷),期】2012(034)002【总页数】5页(P31-35)【关键词】锌酸盐镀锌;故障处理;铝粉;Cr(Ⅵ)杂质;Cr(Ⅲ)杂质【作者】吴双成【作者单位】甘肃皋兰胜利机械厂, 甘肃皋兰730200【正文语种】中文【中图分类】TQ153.151936年E.Mantzell报道了锌酸盐镀锌溶液具有良好的电流效率和分散能力,但镀层是疏松的粉状物,没有使用价值。
在此后的30年中,很少有人去改进锌酸盐镀锌溶液。
Zehncleb认为三乙醇胺同其它有机配位剂相比,在中性至弱酸性时它的配位能力很弱,锌很容易沉淀出来,废水处理较为方便。
野田保夫最早在锌酸盐镀液中引入三乙醇胺,锌酸盐镀锌理论逐渐成熟完善。
传统锌酸盐镀锌添加剂缺少优良的主光亮剂,只是聚胺型载体光亮剂,仅增加了阴极极化,得到半光亮或结晶细致的无光亮镀层,现代锌酸盐镀锌添加剂已经完善,可以使镀层达到全光亮。
目前,在钢铁上镀锌是电镀行业应用量大面广的镀种,占电镀总量的60%,其中,氰化镀锌占镀锌总量的20%,碱性锌酸盐镀锌占30%,氯化物镀锌占50%,锌酸盐镀锌和氯化物镀锌是未来镀锌工艺的发展方向。
氯化钾镀锌工艺存在几大难题难以攻克:1)表面活性剂在镀层中的夹附量很大,镀锌层纯度差,氯化钾镀锌层及钝化层防蚀性能在各种镀锌工艺中最差,不适合于对防蚀性要求较高的汽车及电器产品镀锌。
2)添加剂分解产物较多,蓝白钝化易泛彩、发花或发黄;白钝化层易变灰暗,甚至长白灰、白毛;彩色钝化层色泽易变淡,彩色钝化膜附着力远不如锌酸盐镀锌。
电镀锌杂质污染故障分析及排除方法(最新版)

( 安全技术 )单位:_________________________姓名:_________________________日期:_________________________精品文档 / Word文档 / 文字可改电镀锌杂质污染故障分析及排除方法(最新版)Technical safety means that the pursuit of technology should also include ensuring that peoplemake mistakes电镀锌杂质污染故障分析及排除方法(最新版)1故障状况某电镀车间一直使用氰化电镀锌工艺,共有两槽氰化镀锌溶液约1000L。
年初,1号槽镀液逐渐泛黄,溶液粘稠、浑浊,锌沉积速度很慢,锌镀层灰暗。
用30%硝酸溶液出光后,镀件表面呈黑褐色,彩钝后表面呈雾状,且无光泽。
按电镀过程中带入铬酸,产生六价铬的污染问题处理,加入0.1g/LNa2S2O4,未见好转,又加入2g/LNa2S 和2g/L活性炭进行沉淀吸附过滤,锌镀层也未见有明显好转,而且生产故障继续恶化。
连续生产的2号镀液槽,不久又出现了同样的故障。
重新配制500L镀液,生产一段时间后镀液的颜色又逐渐变黄,锌镀层灰暗,无论是硝酸出光,还是低铬酸出光,表面均呈黑褐色,零件孔眼部位呈亮白色,钝化后严重发雾,无光泽,不足1月已经很难镀出合格产品。
操作者按1.5g/L加入Na2S也未有大起色,已无法正常生产。
2故障诊断镀液外观颜色异常,是否是操作带入铬酸所致?为此,作者做了如下工艺试验:吸取镀液5ml,用蒸馏水稀至50ml,以1∶1硫酸酸化破坏锌络合物,用20%氢氧化钠溶液调整pH值在9左右,使锌生成氢氧化锌沉淀,并过滤。
将滤液用100%硫酸调pH值至5~6后,加入二苯碳酰二胺(0.1g溶于50ml乙醇溶液加入10%硫酸200ml)铬显色剂5ml。
结果滤液无明显颜色变化,这说明没有六价铬污染。
镀锌件常见问题和解决方法
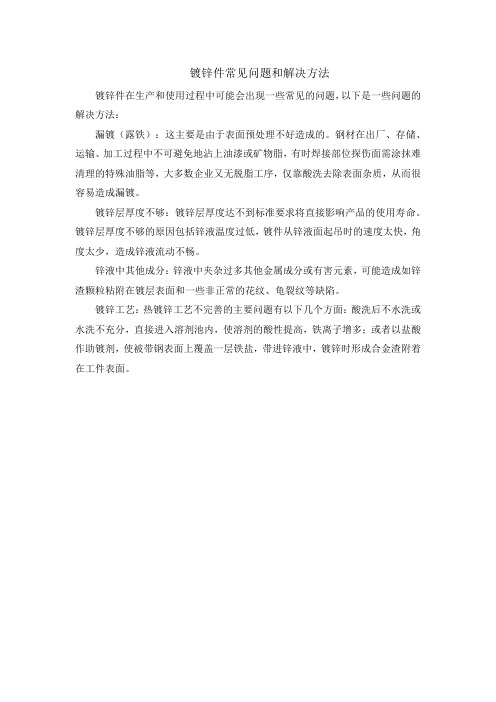
镀锌件常见问题和解决方法
镀锌件在生产和使用过程中可能会出现一些常见的问题,以下是一些问题的解决方法:
漏镀(露铁):这主要是由于表面预处理不好造成的。
钢材在出厂、存储、运输、加工过程中不可避免地沾上油漆或矿物脂,有时焊接部位探伤面需涂抹难清理的特殊油脂等,大多数企业又无脱脂工序,仅靠酸洗去除表面杂质,从而很容易造成漏镀。
镀锌层厚度不够:镀锌层厚度达不到标准要求将直接影响产品的使用寿命。
镀锌层厚度不够的原因包括锌液温度过低,镀件从锌液面起吊时的速度太快,角度太少,造成锌液流动不畅。
锌液中其他成分:锌液中夹杂过多其他金属成分或有害元素,可能造成如锌渣颗粒粘附在镀层表面和一些非正常的花纹、龟裂纹等缺陷。
镀锌工艺:热镀锌工艺不完善的主要问题有以下几个方面:酸洗后不水洗或水洗不充分,直接进入溶剂池内,使溶剂的酸性提高,铁离子增多;或者以盐酸作助镀剂,使被带钢表面上覆盖一层铁盐,带进锌液中,镀锌时形成合金渣附着在工件表面。
镀层常见故障的分析和纠正

常见故障的分析和纠正(酸锌)常见故障的分析和纠正(1)镀层起泡,结合力不好。
镀前处理不良;镀液中添加剂过多;硼酸含量过低同时阴极电流密度过大等会使镀层起泡,造成结合力不好。
镀液中添加剂含量过多,则阴极表面上吸附了较多的有机添加剂,导致阴极表面憎水,同时它还会夹附于镀层内,造成镀层与基体金属间晶格不连续而结合不牢;镀液中硼酸含量低,阴极膜中pH容易升高,同时电流密度过大,阴极膜中pH更高,容易造成金属的氢氧化物或碱式盐夹附于镀层内,影响镀层晶格的正常排列,从而造成镀层结合不牢。
硼酸含量低,电流密度大造成的结合力不好较多地出现在零件的尖端和边缘,出现这类现象时,一方面检查电流,另一方面分析硼酸含量,然后按检查和分析结果进行纠正。
在排除了硼酸含量和电流密度的影响后,再加强镀前处理或用良好的镀前处理与原来的操作进行对比,检查镀前处理是否有问题。
另外用赫尔槽试验检查添加剂的含量。
当发现添加剂含量过高,可用电解或活性炭处理降低其含量。
(2)镀层粗糙。
镀液中锌含量过高;添加剂含量偏低;温度过高或镀液中有固体微粒等都会使镀层粗糙。
镀液中锌含量和温度升高,添加剂含量降低,都是降低阴极极化,导致镀层粗糙。
假使在电镀过程中,镀液温度有升高的趋势,那么最好装置冷却设备。
假使温度略微偏高而没有冷却设备,也可加入适量的苯甲酸钠,以改善镀层的结晶组织。
添加剂含量的多少,可用前述的赫尔槽试验确定,同时还可以从一些现象进行观察,因为添加剂含量偏低时,不但镀层粗糙,同时镀层的光泽差,电流密度的范围比较狭小,低电流密度处镀层色暗,当同时出现这些现象时,再在赫尔槽试验的溶液中,加入适量的添加剂后进行试验,观察阴极样板上的镀层状况,若有好转,可向镀液中补充添加剂。
镀液中的锌含量,可按分析进行调整。
发现锌含量过高时,一方面要稀释镀液,将其浓度调节在工艺范围内,另一方面要减少阳极面积,防止锌含量继续升高。
确定镀液中是否有固体微粒,一种方法是在搅拌镀液的情况下,用500mL(或1000mL)的量杯取一杯镀液,将它放置在强烈的光线下观察;另一方法是用定量滤纸过滤少量镀液,然后观察滤纸上同体微粒的多少,从而估计镀液中固体微粒的含量,若镀液中固体杂质较多,就应过滤镀液,除去这类杂质。
- 1、下载文档前请自行甄别文档内容的完整性,平台不提供额外的编辑、内容补充、找答案等附加服务。
- 2、"仅部分预览"的文档,不可在线预览部分如存在完整性等问题,可反馈申请退款(可完整预览的文档不适用该条件!)。
- 3、如文档侵犯您的权益,请联系客服反馈,我们会尽快为您处理(人工客服工作时间:9:00-18:30)。
锌酸盐镀锌工艺的故障原因与处理方法锌酸盐镀锌层起泡故障的分析与处理(1)首先我们从零件的制备加工检查,没有发现出现起泡的可疑环节,所以重点考虑电镀各个工序的影响。
零件表面的油污,一般是经化学除油、电解除油清除干净。
但若操作不当或者除油液成分失调,可能会有少量油珠残留在零件表面,这就可能引起镀锌层的起泡。
零件若酸洗除锈时间过长,可能由于过腐蚀也会引起镀层的起泡。
此外,镀前活化不充分,没有活化,零件表面形成了一层薄氧化膜,也会导致镀层结合力变差而起泡。
因此,碱性锌酸盐镀锌前处理要严格控制。
前处理流程为:化学除油→热水洗→冷水洗→酸洗除锈→2道流动水洗→阳极电解除油→热水洗→流动水洗→镀前活化→2道流动水洗→镀锌。
除油液要定期加料;酸洗液、镀前活化液要定期更换,而且要严防铜杂质的危害。
(2)电镀工序中引起镀层起泡的可能因素。
挂具选择不当会引起锌镀层起泡,这一点往往易被人们忽略。
一般是用焊锡或铜将挂钩与杆子焊接在一起,再浸塑、浸漆,或用聚氯乙烯薄膜包扎。
若包扎破损,焊接处易受电解质腐蚀,腐蚀产物附着在零件表面、零件自上而下便产生带状密集小泡,因此,应经常检查挂具焊接处是否破损以防止挂具腐蚀而引起镀层起泡。
镀液操作或维护不当导致锌镀层起泡。
镀液中添加剂含量过高,易夹杂在镀层中使得内应力骤增,导致镀层起泡;镀液中重金属杂质,如铅、铜等含量过高,使锌层中夹杂过多的铅、铜等杂质,镀层与基体结合不良而起泡;光亮剂香草醛加入过多,镀层的光亮性虽好,但脆性增大,导致镀层起泡,此外,操作条件控制不当,如:温度太低,电流密度太大,也会导致镀层夹杂有机杂质,引起起泡。
镀后钝化工序的影响。
镀后出光、钝化操作不当,清洗不彻底,出光液、钝化液残留在镀层内,烘烤老化也容易引起镀锌层起泡。
(3)采取措施,严格控制镀锌工序消除起泡故障。
①生产厂首先把好了原材料关,选用性能优良的锌酸盐镀锌原料和添加剂,并且在添加剂加入镀槽前,先进行赫尔槽实验。
②加强镀锌槽液的维护,严格控制添加剂及光亮剂的补充量,以"少加勤加"为原则,或者根据赫尔槽试验计量补加。
③将掉入镀槽内的零件及时捞出,铜挂钩一律不能浸入镀液中。
④检查锌阳极的纯度,采用0号锌或1号锌,不用2号锌。
⑤严格按锌酸盐电镀锌工艺规程,控制电流密度和温度,冬季适当加温至15℃以上,并尽可能减少添加剂及光亮剂的用量。
⑥严格控制零件镀锌层厚度,尤其是零件边角的厚度太厚,特别容易发生镀层起泡。
⑦定期对镀液中有机物和重金属杂质进行大处理(加人lmL/L过氧化氢,搅拌30min,将镀液加温至60℃~70℃,再加入专用活性炭5g/L~l0g/L,锌粉1g/L~2g/L,充分搅拌30min~60min,静置2h,过滤,调整镀液成分,即可试镀),保证镀锌溶液处在一个好的工作状态。
⑧加强镀后处理工序,加强各道工序的漂洗,经常更换浸泡用热水,可大大减少因后处理不当而产生的起泡现象。
⑨严格控制老化温度,避免镀锌层与基体因热胀冷缩差异太大而起泡。
有些情况下,不一定是电镀工序过程出现了镀层起泡的现象,电镀生产的周围环境也可能引起电镀层的起泡。
如某厂碱性锌酸盐镀锌每年4月份~5月份总是发生镀锌层严重起泡的故障,而且开始找不出原因,只得每年停产一个多月。
后来通过观察分析发现,当镀液表面浮有一些微小的丝状物时,镀层起泡就严重,而当时的季节正是厂区周围梧桐树的开花期,其花瓣呈微小丝状的物质飘荡,或多或少落人的镀锌槽。
当采取措施阻挡了花瓣微小丝状物的影响后,这种镀锌层起泡的故障就消除了。
这说明出现电镀故障,有时候除了电镀工艺、生产之外,还要从周围的环境可能的影响考虑。
低电流密度区出现黑色或灰色镀层1.原因分析铅离子污染:当镀锌液中铅离子的含量超过15mg/L时,镀液的分散能力下降,镀层经稀硝酸出光后会出现黑色或灰色条纹。
铅离子主要是由劣质锌阳极带人的,为防止铅的污染,锌阳极需用0#锌或l#锌。
铁离子污染:镀液中铁离子含量高达50mg/L,如铁离子含量进一步提高,镀液就会出现胶体絮状物,镀层钝化后会出现紫蓝色,而且镀层容易出现气泡。
铁离子主要是由劣质氢氧化钠或工件带人。
因此,要选用白色片碱,带赤色的氢氧化钠绝对不可用,工件进入镀槽前应彻底清洗。
为调解阴、阳极面积比例,应当使用镍板或镀镍铁板作为阳极。
铜离子污染:镀液中铜离子含量高达20mg/L时,得到的镀锌层粗糙,光亮度降低,且光亮电流密度范围随铜离子含量的增加而逐渐缩小。
铜离子主要是由挂勾和洗刷导电铜杠时带入的。
2.解决方法硫化钠处理:取0.1g/L~0.5g/L化学纯硫化钠,溶于20倍以上的冷水中,在剧烈搅拌下,缓慢加入到镀液中,加完后继续搅拌20min,使之与镀液中的重金属离子充分反应,生成硫化物沉淀去除。
锌粉处理:取lg/L~3g/L锌粉,在剧烈搅拌下缓慢加入镀液中,使之与重金属离子发生置换反应,加完后继续搅拌20min,静止2h后进行过滤,静置时间不宜过长,否则失去处理意义。
低电流电解处理:取镀镍铁板数块作阴极(面积宜大些),以0.1A/dm2~0.1A/dm2的电流密度进行电解处理,处理时间视试镀后情况而定。
使用过的镀镍铁板表面的黑色镀层必须在酸中退除,然后方可作阳极使用。
该方法的优点是:操作简便,不损耗镀液。
CK-778碱性镀锌溶液净化处理:取2g/L~3g/L CK-778碱性镀锌溶液净化剂,用与锌粉同样方法进行处理,但不必过滤。
净化剂加完后在继续搅拌和静置过程中镀液中会出现漂浮物,可边搅拌边用布网捞去,处理完后最好再用低电流电解处理,并添加1/3原配方量的镀锌添加剂和光亮剂。
镀锌层出现粗糙或粗糙发暗的原因及解决方法1.原因分析按正常情况下氧化锌与氢氧化钠的比例为l:(10~12),过高或过低即会出现上述故障。
即镀锌层粗糙是氧化锌比例偏低而氢氧化钠比例偏高造成的,这种比例失调还会出现电镀沉积速度缓慢、允许电流密度上限降低、工件表面析氢加重等故障。
反过来,氧化锌比例偏高而氢氧化钠比例偏低也会造成镀锌层的粗糙与发暗,这时还会出现工件边缘部位有气泡,沉积速度缓慢,分散能力和深镀能力降低,电流升不上去,镀层结合力差等问题。
2.解决方法调整上述两种情况的故障,一般在日常维护中既要控制好氧化锌与氢氧化钠的比例,又要考虑到氧化锌与氢氧化钠的实际含量,即使氧化锌的比例偏低,也不直接添加氧化锌,而是调节锌阳极的面积,暂停使用不溶性阳极,溶液中锌含量就会很快上去。
当氧化锌含量高了,可以以镀镍铁板代替锌阳极板,添加氢氧化钠至l20g/L,这一故障即能很快获得解决。
镀层钝化膜质量故障(发花、变色、变暗等)目前镀锌进行钝化处理的工艺主要低铬彩色钝化和三价铬钝化,在钝化后有时放置一夜或几天时间,钝化膜的表面就会出现雨点状白点,大小不一,钝化膜也变暗变淡,光亮度下降。
1.原因分析实际上发生这种故障的原因更复杂,可能有镀液的问题;前处理不良的问题;基材有麻点,镀后出光等清洗不良的问题;钝化液成分比例失调的问题;钝化膜老化时间不够的问题;环境的问题,空气中水蒸气、酸雾严重使得钝化膜色泽变化和腐蚀等。
2.解决方法针对上述可能的原因,逐条采取措施。
调整镀液成分到工艺规范,并且对镀液进行锌粉、硫化钠处理,再进行电解处理;加强除油、活化等前处理工序;加强镀后清洗和出光工序;严格控制钝化溶液成分和钝化工艺参数,控制好钝化膜的色彩;加强钝化后老化工艺的控制;改善工作环境,镀后零件尽快入库等。
尤其要注意的是钝化后的老化问题,因为热水槽老化温度过高(>70℃),就会使得钝化膜中的六价铬溶解,形成耐蚀性很差的多孔钝化膜。
就容易出现镀锌层钝化膜表面的雨点状白点,钝化膜变暗变淡,光亮度下降的故障。
严格控制钝化老化工序(60℃),这种故障就可以消除,生产恢复到正常。
其他环节也会出现钝化质量的故障的问题,如某厂采用DE碱性锌酸盐镀锌液,低铬钝化的滚镀锌工艺生产线,出现了钝化膜发花,表面有许多大块不规则灰黑色斑块的故障。
经分析是由于镀锌后的清洗槽中白色絮状沉淀较多,出光槽溶液呈黄棕色,pH值接近4,这些都可能带来电镀故障,由于清洗不干净和出光液pH高,造成电镀零件表面碱性镀液的清洗不够,出光液的出光作用下降,导致钝化膜发花等故障。
通过增加一道热水洗,将出光液pH 调至l左右后,故障排除,生产恢复到正常。
锌酸盐镀锌中阳极板引起的故障实例在一个工厂的实际生产中,发现锌酸盐镀锌液中可能是镀液中杂质的影响,造成了镀锌层粗糙、灰暗、无光泽,甚至镀不上的故障。
但是在解决这个故障过程中,先是调整镀液中的氧化锌和氢氧化钠的比例,调整添加剂和光亮剂的含量,然后再电解处理几小时等措施。
但是镀锌层的质量仍然没有获得好转,在大电流密度下电镀,使得零件的边角烧焦,有镀层的部位也比较粗糙,镀液的分散能力和深镀能力极差,镀层经硝酸出光后,表面呈黑褐色。
怎么办?消除镀液中杂质最好的方法是对镀液进行去杂质处理:在镀液中加入锌粉2g/L,活性炭2g/L,经过搅拌、静置、过滤,然后进行镀液成分分析,调整成分到工艺规范范围,镀液恢复了正常,镀锌层的质量达到了要求。
但是,没过几天,没有补充其他成分,镀层又出现了上述故障,这种情况下分析杂质的来源可能是锌阳极所为,把锌阳极从镀液中取出,发现表面有异常发蓝现象,用水冲洗和用刷子刷洗后,锌阳极表面呈现出黑点,把这种黑点进行分析,发现是有机物的焦化和金属杂质,检查发现,这些物质是在浇铸锌阳极时造成的,问题找到了,更换了电镀槽内的锌阳极,彻底排除了这种电镀锌的故障。
锌阳极引起的电镀故障问题不只是一二例,某厂建成了32000L镀液的大型自动镀锌线,选用了ACF-Ⅱ碱性无氰镀锌工艺。
该工艺具有优良的分散和深镀能力,电流密度范围宽,镀层光亮度与钾盐镀锌相近,镀层与基体结合牢固,钝化膜附着力极好,彩色和深色钝化膜镀层耐腐蚀能力强等性能特点。
但是在新配镀液开始批量生产时,很快发现形状复杂的零件朝上的内腔和低电流区存在严重的镀层粗糙、发黑现象,而此现象在小试中均从未发现。
经过分析和试验,排除了这种镀锌液的成分失调、循环过滤差以及可能存在重金属杂质等情况,初步判定产生故障的根源在阳极的Zn板。
因为观察镀液中的Zn板发现,其表面有一层厚密的黑色细粉状物质,而同时悬挂的不溶性铁板则未见任何异常。
将Zn阳极板取出,进行酸洗、擦拭干净后重新放入镀槽中,继续电镀,零件内腔和低电流区的上述症状明显减轻。
但随着电镀时间的延长,Zn阳极表面的黑色细粉状物质逐渐增多,故障又重新出现,从而最终确定故障原因是,Zn板表面的黑色细粉状物质沉落于朝向上方的零件内腔和低电流区,再加上镀液的均镀能力好,零件内腔和低电流区镀层在细粉的不断沉落中快速沉积,故形成粗糙发黑的不合格镀层(零件外部和高电流区因极化较大和不易沉落黑色细粉物质,镀层属于正常沉积,所以镀层尚好)。