影响锌酸盐镀锌质量的原因浅析
锌酸盐镀锌工艺的故障原因与处理方法
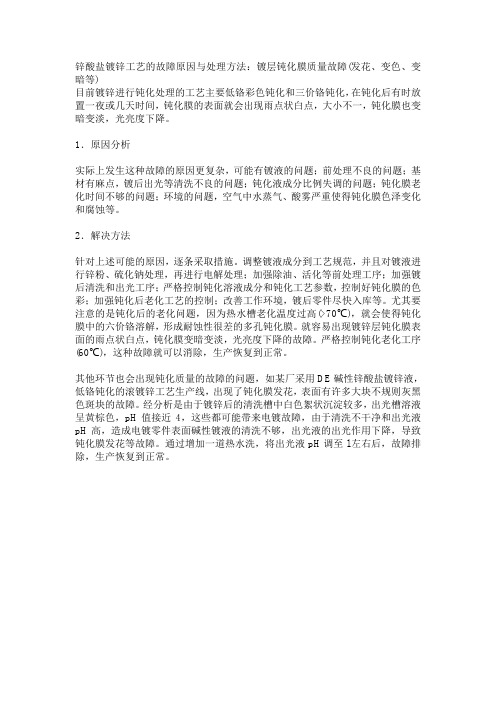
锌酸盐镀锌工艺的故障原因与处理方法:镀层钝化膜质量故障(发花、变色、变暗等)目前镀锌进行钝化处理的工艺主要低铬彩色钝化和三价铬钝化,在钝化后有时放置一夜或几天时间,钝化膜的表面就会出现雨点状白点,大小不一,钝化膜也变暗变淡,光亮度下降。
1.原因分析实际上发生这种故障的原因更复杂,可能有镀液的问题;前处理不良的问题;基材有麻点,镀后出光等清洗不良的问题;钝化液成分比例失调的问题;钝化膜老化时间不够的问题;环境的问题,空气中水蒸气、酸雾严重使得钝化膜色泽变化和腐蚀等。
2.解决方法针对上述可能的原因,逐条采取措施。
调整镀液成分到工艺规范,并且对镀液进行锌粉、硫化钠处理,再进行电解处理;加强除油、活化等前处理工序;加强镀后清洗和出光工序;严格控制钝化溶液成分和钝化工艺参数,控制好钝化膜的色彩;加强钝化后老化工艺的控制;改善工作环境,镀后零件尽快入库等。
尤其要注意的是钝化后的老化问题,因为热水槽老化温度过高(>70℃),就会使得钝化膜中的六价铬溶解,形成耐蚀性很差的多孔钝化膜。
就容易出现镀锌层钝化膜表面的雨点状白点,钝化膜变暗变淡,光亮度下降的故障。
严格控制钝化老化工序(60℃),这种故障就可以消除,生产恢复到正常。
其他环节也会出现钝化质量的故障的问题,如某厂采用DE碱性锌酸盐镀锌液,低铬钝化的滚镀锌工艺生产线,出现了钝化膜发花,表面有许多大块不规则灰黑色斑块的故障。
经分析是由于镀锌后的清洗槽中白色絮状沉淀较多,出光槽溶液呈黄棕色,pH值接近4,这些都可能带来电镀故障,由于清洗不干净和出光液pH高,造成电镀零件表面碱性镀液的清洗不够,出光液的出光作用下降,导致钝化膜发花等故障。
通过增加一道热水洗,将出光液pH调至l左右后,故障排除,生产恢复到正常。
镀锌的方法
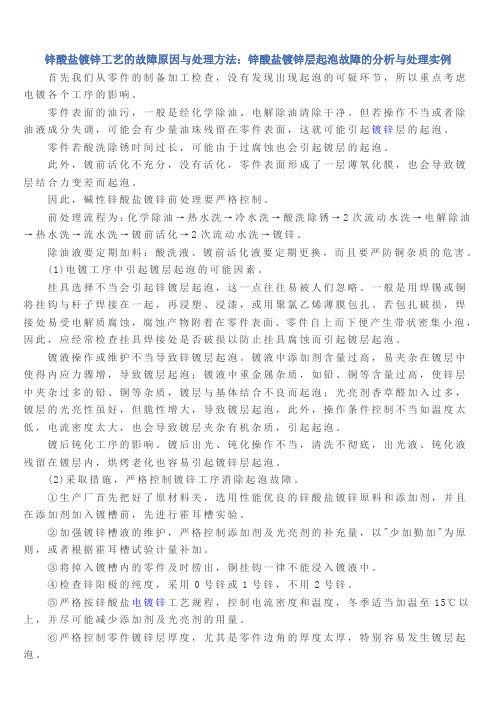
锌酸盐镀锌工艺的故障原因与处理方法:锌酸盐镀锌层起泡故障的分析与处理实例首先我们从零件的制备加工检查,没有发现出现起泡的可疑环节,所以重点考虑电镀各个工序的影响。
零件表面的油污,一般是经化学除油、电解除油清除干净。
但若操作不当或者除油液成分失调,可能会有少量油珠残留在零件表面,这就可能引起镀锌层的起泡。
零件若酸洗除锈时间过长,可能由于过腐蚀也会引起镀层的起泡。
此外,镀前活化不充分,没有活化,零件表面形成了一层薄氧化膜,也会导致镀层结合力变差而起泡。
因此,碱性锌酸盐镀锌前处理要严格控制。
前处理流程为:化学除油→热水洗→冷水洗→酸洗除锈→2次流动水洗→电解除油→热水洗→流水洗→镀前活化→2次流动水洗→镀锌。
除油液要定期加料;酸洗液、镀前活化液要定期更换,而且要严防铜杂质的危害。
(1)电镀工序中引起镀层起泡的可能因素。
挂具选择不当会引起锌镀层起泡,这一点往往易被人们忽略。
一般是用焊锡或铜将挂钩与杆子焊接在一起,再浸塑、浸漆,或用聚氯乙烯薄膜包扎。
若包扎破损,焊接处易受电解质腐蚀,腐蚀产物附着在零件表面、零件自上而下便产生带状密集小泡,因此,应经常检查挂具焊接处是否破损以防止挂具腐蚀而引起镀层起泡。
镀液操作或维护不当导致锌镀层起泡。
镀液中添加剂含量过高,易夹杂在镀层中使得内应力骤增,导致镀层起泡;镀液中重金属杂质,如铅、铜等含量过高,使锌层中夹杂过多的铅、铜等杂质,镀层与基体结合不良而起泡;光亮剂香草醛加入过多,镀层的光亮性虽好,但脆性增大,导致镀层起泡,此外,操作条件控制不当如温度太低,电流密度太大,也会导致镀层夹杂有机杂质,引起起泡。
镀后钝化工序的影响。
镀后出光、钝化操作不当,清洗不彻底,出光液、钝化液残留在镀层内,烘烤老化也容易引起镀锌层起泡。
(2)采取措施,严格控制镀锌工序消除起泡故障。
①生产厂首先把好了原材料关,选用性能优良的锌酸盐镀锌原料和添加剂,并且在添加剂加入镀槽前,先进行霍耳槽实验。
②加强镀锌槽液的维护,严格控制添加剂及光亮剂的补充量,以"少加勤加"为原则,或者根据霍耳槽试验计量补加。
常见锌镀层结合力差的六种可能原因

常见锌镀层结合力差的六种可能原因内容:引起锌酸盐镀锌层结合力差的因素很多,其中以下六种情况尤为多见。
(1)光亮剂添加过量。
锌酸盐镀锌层的光亮度稍逊于氯化钾镀锌层,有人认为可以用添加光亮剂来弥补,结果不但达不到预想目的,镀层的结合力还受到严重影响。
这一现象多发生在溶液严重老化阶段。
这时镀液中有机物质过多,属于镀层中晶格严重扭曲之故。
在这种情况必然会引起内应力增加,从而导致脆性增大,出现脱皮。
为避免这种现象的出现,首先要合理控制光亮剂的用量,并适时地用活性炭进行吸附处理。
解决方法:稀释、用活性炭处理,调整溶液成分,平时要少加、勤加。
(2)工件镀前在镀槽中停留时间太长。
有人认为锌酸盐镀锌溶液是碱性的,把经过前处理的工件挂在镀槽中,待聚够一槽后再配电施镀,结果工件发生钝化,影响到镀层的结合力。
解决方法:工件在槽内不要过长时间停留,以免引起钝化。
(3)镀层过厚。
镀层内应力和脆性增大,工件边缘部位的镀层易起泡和脱落。
解决方法:镀层厚度要控制在20μm以内。
(4)镀液表面浮有油污。
工件人槽后被镀液表面的油污和光亮剂分解物组成的污物所包围。
从而引起镀层脱皮。
解决方法:这层浮油应随时用厚层手纸吸除,工件入槽后先在镀液中抖动几下,使吸附在工件表面的油污脱离下来。
(5)工件除油不彻底。
有人认为锌酸盐镀锌溶液是碱性的,必定有除油能力,前处理可以马虎一点。
其实镀液虽是碱性的,但当有油污的工件人槽后,在其与碱性物质起作用之前,锌离子即抢先放电析出,锌层沉积在薄层油膜上,结合力显然会降低。
解决方法:加强前处理工序。
(6)工艺条件控制不当。
工艺条件偏差过大,尤其是溶液温度要求为室温。
室温通常是指18~25℃,但有人又认为既不加温又不降低即指的就是室温,冬季室内温度低于10℃时仍认为是室温,结果由于电流密度没有按温度的变化而变化而导致影响镀层的结合力。
解决方法:根据溶液温度范围的变化来调节电流密度,当溶液温度过低时需要适当加温。
镀锌工艺、原理及影响因素
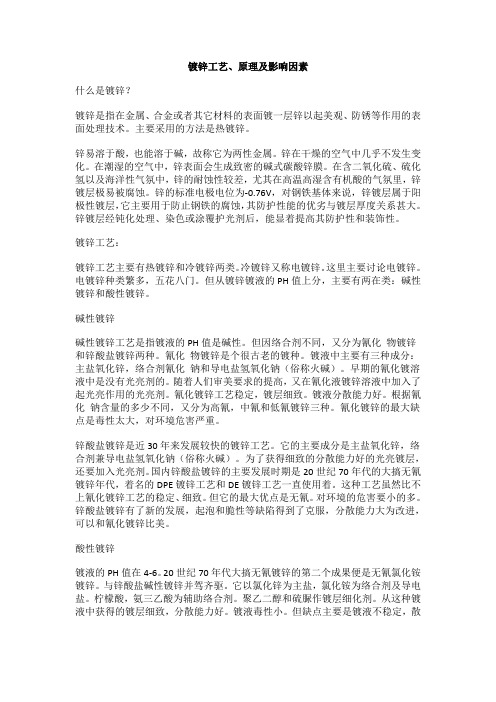
镀锌工艺、原理及影响因素什么是镀锌?镀锌是指在金属、合金或者其它材料的表面镀一层锌以起美观、防锈等作用的表面处理技术。
主要采用的方法是热镀锌。
锌易溶于酸,也能溶于碱,故称它为两性金属。
锌在干燥的空气中几乎不发生变化。
在潮湿的空气中,锌表面会生成致密的碱式碳酸锌膜。
在含二氧化硫、硫化氢以及海洋性气氛中,锌的耐蚀性较差,尤其在高温高湿含有机酸的气氛里,锌镀层极易被腐蚀。
锌的标准电极电位为-0.76V,对钢铁基体来说,锌镀层属于阳极性镀层,它主要用于防止钢铁的腐蚀,其防护性能的优劣与镀层厚度关系甚大。
锌镀层经钝化处理、染色或涂覆护光剂后,能显着提高其防护性和装饰性。
镀锌工艺:镀锌工艺主要有热镀锌和冷镀锌两类。
冷镀锌又称电镀锌。
这里主要讨论电镀锌。
电镀锌种类繁多,五花八门。
但从镀锌镀液的PH值上分,主要有两在类:碱性镀锌和酸性镀锌。
碱性镀锌碱性镀锌工艺是指镀液的PH值是碱性。
但因络合剂不同,又分为氰化物镀锌和锌酸盐镀锌两种。
氰化物镀锌是个很古老的镀种。
镀液中主要有三种成分:主盐氧化锌,络合剂氰化钠和导电盐氢氧化钠(俗称火碱)。
早期的氰化镀溶液中是没有光亮剂的。
随着人们审美要求的提高,又在氰化液镀锌溶液中加入了起光亮作用的光亮剂。
氰化镀锌工艺稳定,镀层细致。
镀液分散能力好。
根据氰化钠含量的多少不同,又分为高氰,中氰和低氰镀锌三种。
氰化镀锌的最大缺点是毒性太大,对环境危害严重。
锌酸盐镀锌是近30年来发展较快的镀锌工艺。
它的主要成分是主盐氧化锌,络合剂兼导电盐氢氧化钠(俗称火碱)。
为了获得细致的分散能力好的光亮镀层,还要加入光亮剂。
国内锌酸盐镀锌的主要发展时期是20世纪70年代的大搞无氰镀锌年代,着名的DPE镀锌工艺和DE镀锌工艺一直使用着。
这种工艺虽然比不上氰化镀锌工艺的稳定、细致。
但它的最大优点是无氰。
对环境的危害要小的多。
锌酸盐镀锌有了新的发展,起泡和脆性等缺陷得到了克服,分散能力大为改进,可以和氰化镀锌比美。
锌酸盐镀锌工艺的再研究
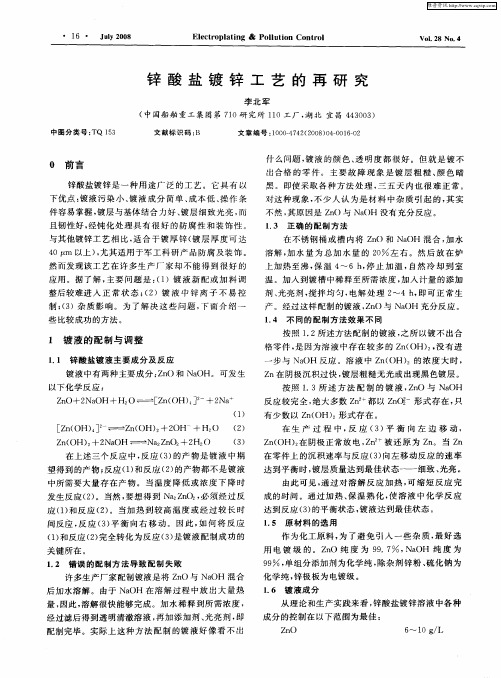
Elc r pl tng & Po l i n Co r e to a i luto ntol
Vo 2 J 1 8 N0 4
.
锌 酸 盐 镀 锌 工 艺 的 再 研 究
李 北 军
( 中国船舶 重工集 团第 7 0研 究所 10工厂 , 北 宜昌 4 30 ) 1 1 湖 40 3
Z OH ) + 2 OH n( 2 Na
Z( n OH)在 阴极正常放 电 , n 被 还原 为 Z 。当 Z Z n n 在 零件上 的沉 积速率与反应 ( ) 3 向左 移动反应 的速 率
在上述 三个反 应 中 , 反应 ( ) 3 的产 物是 镀 液 中期
望得 到的产物 ; 反应 ( ) 反应 ( ) 1和 2 的产物 都不是镀 液
应 用 。据 了 解 , 要 问 题 是 : 1 主 ( )镀 液 新 配 或 加 料 调 整后较难进 入 正 常 状 态 ;2 ( )镀 液 中 锌 离 子 不 易 控
上加热 至沸 , 温 4 , 止 加 温 , 保 ~6h 停 自然 冷却 到 室 温 。加入 到镀 槽 中稀 释至所需浓度 , 加入计 量 的添加 剂、 光亮剂 , 搅拌 均 匀 , 电解 处 理 2 , ~4h 即可 正常 生 产 。经过这样 配制 的镀液 ,n Z O与 Na OH 充分反应 。
化学纯 , 锌极 板为 电镀级 。
16 镀 液 成 分 .
许多 生产厂家配制镀 液是将 Z O与 N OH 混合 n a
后 加水溶解 。由于 N OH 在 溶解 过程 中放 出大 量热 a
量, 因此 , 溶解很快 能够 完成 。加 水稀释 到所需 浓度 ,
在不锈 钢桶 或槽 内将 Z O 和 N O 混 合 , n aH 加水
环保碱性锌酸盐镀锌浅谈

环保碱性锌酸盐镀锌浅谈(2021-12-29 22:23:49)标签:随着人们的生活水平的不断提高,环保意识也在逐渐的增强。
众所周知,电镀是一个高污染的行业,如何使电镀行业抵达清洁生产确实目的,是咱们每一个电镀技术工作者的一路的目标。
就单纯的镀锌而言,用无氰锌酸盐代替有氰镀锌,是实现环保电镀的一个很好的实例。
但在实际生产操作进程中,由于无氰电镀比有氰电镀控制起来要困难的多,而且生产本钱也比拟高,尤其是对于一些高质量要求的镀锌件来讲,氯化钾镀锌达不到要求。
所以很多的生产厂家不肯采用,继续采用老工艺有氰电镀,给推行环保型镀锌造成了必然的阻力。
但做为此刻的碱性锌酸盐镀锌体系来讲,在工艺性能方面已经完全可与之想媲美,现将本人在利用环保碱性锌酸盐镀锌的进程中产生的一些故障及排除方式做一下浅谈,希望能为推行环保型电镀生产出一份力,给咱们的子孙后代后代留一片净水。
1 工艺流程本公司所采用的碱性镀锌工艺是才用自动生产线,工艺流程为:热脱脂——清洗—清洗——喷淋清洗——酸洗——清洗——清洗——喷淋清洗——电摆脱脂——清洗——清洗——喷淋清洗——弱酸中和——喷淋清洗——碱性锌酸盐镀锌——清洗——清洗——喷淋清洗——出光——清洗——钝化——清洗——清洗——喷淋清洗——热水清洗——烘干——包装。
2 工艺条件及配方工艺配方如下:NaOH 50-80g/lZnO 8-15g/lA〔主光剂〕10—25mL/LB〔走位剂〕1—3mL/LC〔净化剂〕—1mL/L3 工艺影响因素3.1 NaOH。
氢氧化钠的含量的多少直接影响到产品质量的好坏。
尤其是对高光亮度的基体。
含量过少,阳极很容易钝化。
造成发雾现象,外表粗糟无光,分散能力变差,低区发黑。
对于镀锌后要进展机械加工的零件来讲,还容易造成脆性增大的现象。
含量太高,那么上镀速度比拟慢。
本人以为最正确的含量为130-140g/l。
3.2 ZnO。
氧化锌的含量上下因选用的光亮剂的不同而不同。
锌层外观故障分析

在我国碱性锌酸盐镀锌约占镀锌总量的50%。
在长期实践中,人们积累了许多碱性锌酸盐镀锌工艺维护管理的成功经验和排除故障的有效方法。
由于锌酸盐镀锌溶液配方和溶液成分的差异,尤其是添加剂(有进口的和国内公司生产的)的不同,可能出现的故障原因和故障特征也有所不同。
因此,需要技术人员认真分析,找出故障出现的原因,进而找出消除故障的措施。
一般而言,锌酸盐镀锌可能出现的故障现象和原因主要包括以下几种。
1 镀层起泡发脆、结合力差可能原因:①镀前处理不良;②镀液中氧化锌含量高;③镀液中氢氧化钠含量低;④阴极电流密度大;⑤镀液温度低;⑥添加剂添加过量;⑦镀液中有机杂质多等。
2 镀层结晶粗糙可能原因:①镀液中氧化锌含量高;②氢氧化钠含量低;③电流密度大;④添加剂添加过量;⑤镀液中金属杂质多等。
3 镀层沉积速率慢可能原因:①镀液中氧化锌含量低;②氢氧化钠含量高或低;③电流密度小;④镀液的温度低等。
4 镀层光亮不均匀可能原因:①电流密度小;②镀液中添加剂不足;③镀液中有机杂质多等。
5 镀层花斑发雾可能原因:①镀前处理不良;②添加剂过量;③镀液的温度高等。
6 镀层发暗或钝化无光泽可能原因:①镀液中添加剂不足;②金属杂质多等。
7 镀锌阳极出现钝化发黑可能原因:①镀液中氢氧化钠含量低;②阳极的面积小;③电流密度大等。
8 镀液的分散能力差可能原因:①添加剂不足;②氧化锌含量高;③氢氧化钠含量高;④镀液温度高等。
9 镀液的深镀(覆盖)能力差可能原因:①电流密度小;②镀液温度低;③添加剂不足,有机杂质多等。
需要说明的是,镀锌过程中出现上述故障,有可能是其中的一种或几种,分析和解决这些故障的思路和方法需要综合考虑多种因素。
另外在生产中还有一些其他的特殊的故障出现,如镀层脆性大等也需要注意。
1 工件镀锌后镀层起泡的原因是什么?工件镀锌后有的镀层当时看不出什么问题,放置几天或经过加热除氢后就发现有起泡现象。
对氰化物镀锌、碱性锌酸盐镀锌或氯化物镀锌,这种镀层起泡的相同原因都是由于:1)工件镀前处理不良;2)添加剂加入过量;3)电解液中锌离子质量浓度过高而络合剂不足。
锌酸盐镀锌液中的金属杂质及其对策
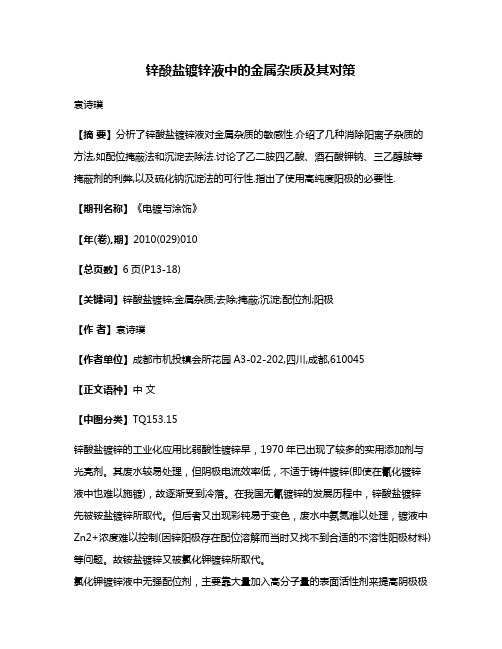
锌酸盐镀锌液中的金属杂质及其对策袁诗璞【摘要】分析了锌酸盐镀锌液对金属杂质的敏感性.介绍了几种消除阳离子杂质的方法,如配位掩蔽法和沉淀去除法.讨论了乙二胺四乙酸、酒石酸钾钠、三乙醇胺等掩蔽剂的利弊,以及硫化钠沉淀法的可行性.指出了使用高纯度阳极的必要性.【期刊名称】《电镀与涂饰》【年(卷),期】2010(029)010【总页数】6页(P13-18)【关键词】锌酸盐镀锌;金属杂质;去除;掩蔽;沉淀;配位剂;阳极【作者】袁诗璞【作者单位】成都市机投镇会所花园A3-02-202,四川,成都,610045【正文语种】中文【中图分类】TQ153.15锌酸盐镀锌的工业化应用比弱酸性镀锌早,1970年已出现了较多的实用添加剂与光亮剂。
其废水较易处理,但阴极电流效率低,不适于铸件镀锌(即使在氰化镀锌液中也难以施镀),故逐渐受到冷落。
在我国无氰镀锌的发展历程中,锌酸盐镀锌先被铵盐镀锌所取代。
但后者又出现彩钝易于变色,废水中氨氮难以处理,镀液中Zn2+浓度难以控制(因锌阳极存在配位溶解而当时又找不到合适的不溶性阳极材料)等问题。
故铵盐镀锌又被氯化钾镀锌所取代。
氯化钾镀锌液中无强配位剂,主要靠大量加入高分子量的表面活性剂来提高阴极极化值,因而镀锌层与钝化层中夹杂大量有机物,防蚀性能差,只适于要求不高的低档产品用,在汽摩、电子电器、军工产品等方面被禁止采用。
随着镀锌三价铬钝化的推广应用,锌酸盐镀锌表现出彩钝色泽相对较深、钝化层防蚀性更好的优点(某些情况下甚至优于氰化镀锌),因而从20世纪末开始,锌酸盐镀锌工艺的复苏速度不断加快。
在添加剂方面,也出现了诸如FK303、SLP323之类的集添加剂与光亮剂于一体的所谓“二合一”助剂。
然而,工业应用的结果又更加显露出锌酸盐镀锌液对杂质敏感以及杂质难以去除的问题。
若对此缺乏较深入全面的认识,锌酸盐镀锌的优点则难以充分发挥。
本文着重讨论锌酸盐镀锌液中金属杂质的问题,供使用者参考。
2. 1 敏感性在碱性条件下,绝大多数金属离子必须与配位剂形成配离子才能够稳定存在,否则会成为氢氧化物沉淀。
- 1、下载文档前请自行甄别文档内容的完整性,平台不提供额外的编辑、内容补充、找答案等附加服务。
- 2、"仅部分预览"的文档,不可在线预览部分如存在完整性等问题,可反馈申请退款(可完整预览的文档不适用该条件!)。
- 3、如文档侵犯您的权益,请联系客服反馈,我们会尽快为您处理(人工客服工作时间:9:00-18:30)。
•12 •影响锌酸盐镀锌质量的原因浅析奚兵(常州市荆川里小区12丙201,江苏 常州 213015)摘 要:分析了镀前处理、镀液成分、杂质、操作条件对锌酸盐镀锌质量的影响,并给出了相应的解决办法和措施。
介绍了各工序操作中应注意的问题及镀液维护的参数范围。
实践表明,锌酸盐镀锌工艺可以获得不亚于氰化物镀锌质量的镀层。
关键词:锌酸盐镀锌;前处理;镀液维护;镀层质量 中图分类号:TG178; TQ153.15文献标志码:B文章编号:1004 – 227X (2009) 10 – 0012 – 03Analysis on causes affecting deposit quality of zincate zinc plating // XI BingAbstract: The effects of pre-plating treatment, bath composition, impurities and operation conditions on the deposit quality of zincate zinc plating were analyzed. Some corresponding solutions and measures were suggested. The problems needing attention in process operation and the parameter range of bath maintenance were introduced. The practice shows that the quality of deposit obtained by zincate zinc plating is no worse than that by cyanide zinc plating. Keywords: zincate zinc plating; pretreatment; bath maintenance; deposit qualityAuthor’s address: Flat.201, The Third Unit, No.12 Building, Jingchuanli Residential Quarter, Changzhou 213015, China1 前言锌酸盐镀锌是在传统氰化物镀锌基础上发展起来的环保型镀锌工艺之一。
经过近40年的研究和实践,目前市售的无氰碱性镀锌添加剂和光亮剂均可获得结晶细致光亮、结合力好的镀层,不亚于氰化镀锌质量,且适应在不同的基材上电镀,达到了现代工业生产的要求。
锌酸盐镀锌由于不使用剧毒的氰化钠,金属浓度低,所以有利于清洁生产,只要调整pH ,锌就很容易变成氢氧化锌而沉淀,易于回收再利用,且成分简单,易于管理。
但是,无论有氰还是无氰电镀,在生产过程中都会出现镀层的质量问题,其原因往往是镀液中成收稿日期:2008–10–08修回日期:2009–01–20作者简介:奚兵(1935–),男,江苏苏州人,长期从事金属表面处理工作。
作者联系方式:(Tel) 0519–86972150。
分比例失调或受有害杂质干扰及前处理不良等因素所致。
本文拟就影响锌酸盐镀锌质量的原因加以分析讨论。
2 镀前处理2. 1 除油与氰化镀液相比,锌酸盐镀液的除油能力是很差的,所以,即使是碱性镀液,对除油也应该重视。
如果工件除油不良,镀层就容易起泡,影响结合力。
对于挂镀,工件最好经过电解除油或超声波除油。
如果选用化学除油,需要二次除油,第二次应在另设的除油液中进行,该除油液必须保持清洁。
对于油污较重的工件,应当先用有机溶剂清洗,然后再进行除油。
除油是否合格,最简单的方法是看从清洗水中取出的工件表面的水膜。
如果其表面水膜是连续(亲水)的,则除油合格;如果工件表面出现水珠状现象,即有不润湿的地方,则说明除油不良,必须重新除油。
2. 2 酸洗酸洗不良或不当同样会导致镀层起泡。
由于水和氧的作用,工件表面会被腐蚀,其腐蚀产物是金属氧化物(生锈),所以工件经上述工序除油后,必须进行酸洗处理,防止其影响镀层与基体的结合力。
实践表明,不同基材需采取不同的酸洗方法。
首先应了解待镀产品的材质,然后合理地选用酸洗液组分进行酸洗处理,否则可能会发生质量故障。
例如,某企业采用锌酸盐镀锌试镀一种出口产品样件,结果镀层起泡,部分呈粉状,前处理酸洗与其他工件一样为常规工艺。
后经核实,该产品的材质为硫磷钢。
由于酸洗中盐酸浓度过高,使工件基体组织中的硫、磷元素形成晶界偏析,在碱性镀锌过程中大量析氢,影响了镀层的结合。
因此,锌酸盐镀锌工艺要求:碳素钢可以用体积比1∶1的盐酸溶液酸洗;弹簧钢宜用质量分数为15%的硫酸溶液浸蚀;铸铁件应在硫酸和氢氟酸混合液中除锈;硫磷钢只能用低浓度(体积比约1∶2)盐酸水溶液处理,以防止工件基体表面的硫、磷的偏析,避免万方数据•13 •镀层起泡。
此外,钢件在酸洗过程中会产生渗氢现象。
如果渗氢严重,镀层会起泡或脱落,所以酸洗时间不能太长。
特别是高碳钢,因为其表面有碳富集区,如果碳游离析出而附着在工件表面呈挂灰状,则会严重影响镀层结合力,甚至局部镀不上锌层。
2. 3 活化工件经除油、酸洗后,其表面会生成一层氧化膜,这将影响镀层结合力。
因此,镀锌前还需用质量分数为5%的盐酸溶液进行弱腐蚀(活化),除去工件表面氧化膜,使基体表面产生微腐蚀作用,暴露出金属的结晶组织,加强机械互锁作用,以提高镀层与基体的结合力。
2. 4 预浸由于锌酸盐镀液是强碱性的,如果工件经上述工序酸洗、水洗后就进行电镀锌,此时表面呈微酸性,与碱液反应时容易使镀层发花,所以镀前必须在30%(质量分数)的氢氧化钠溶液中预浸,不用清洗直接进槽电镀。
这样既可以消除或减轻镀层发花现象,又可防止因长期带入氯离子而造成镀液的污染。
3 镀液成分3. 1 氧化锌无氰碱性镀锌液中ZnO 是主盐,其质量浓度对镀液性能影响很大。
镀液中锌的质量浓度一般维持在8 ~ 13 g/L ,较佳值为10 g/L 。
锌质量浓度高则电流效率高,但镀层光亮范围变窄,容易造成镀层起泡、结晶粗糙、疏松等质量故障;质量浓度过低时,电流密度范围缩小,沉积速度慢,镀层薄、易起泡。
因此,生产中必须严格控制氧化锌质量浓度在工艺范围内,夏季可稍高些(即工艺参数上限),冬期应该低些为宜,但不能低于8 g/L 。
3. 2 氢氧化钠锌酸盐镀液中氢氧化钠质量浓度应维持在90 ~ 150 g/L ,较佳值为110 g/L 。
NaOH 的主要作用是与锌离子形成稳定的锌酸盐,同时起到促进阳极溶解和提高镀液导电性能的作用。
因此,当NaOH 质量浓度过低时,阳极易钝化,镀液导电能力降低,阴极电流效率下降,沉积速度慢,镀层无光泽,镀液易产生白色沉淀物;NaOH 质量浓度过高时,阳极溶解快,镀液中锌离子浓度增大,镀层结晶粗糙、毛刺、发暗或呈青灰色斑点,且钝化膜不亮。
对于氢氧化钠和氧化锌在锌酸盐镀液中的比例,挂镀应保持10∶1(浓度比),滚镀应保持在12∶1。
但NaOH 质量浓度上限值为150 g/L ,如果镀层起泡,可适当提高NaOH 质量浓度。
3. 3 添加剂只用上述氧化锌和氢氧化钠形成的锌酸盐溶液电镀,得到的镀层呈粉末状,即除了金属锌外,还有其他析出物。
在其中加入适量添加剂则变成全金属锌,而且镀层结晶细致、光亮和平滑。
但是添加剂加入量过多,会造成镀层夹杂严重,使镀锌层发脆,阴极极化增大,引起初始状态渗氢过多,容易产生镀层起泡等故障。
因此,对于添加剂的维护管理十分重要。
首先是选择品牌优良的添加剂,其次是严格控制添加量。
市售无氰碱性镀锌光亮添加剂用法不同,要仔细阅读产品说明书,避免搞错。
除了配制镀液按量加入外,日常维护管理应根据生产量及槽液容量和班次而酌情补加。
如两班制,每周补加2次,每次1 ~ 2 mL/L 。
最好是按照通电电流大小和时间来计量补加,并以少加勤加的方法进行维护管理。
4 杂质积累4. 1 有机杂质无论采用什么方法补加光亮添加剂,镀液中总会存在一些无用的有机物,即杂质。
这是因为碱性镀锌添加剂是由有机胺或环氧氯丙烷在一定温度条件下反应获得的,其反应产物并不是都会在电镀过程中起到好的作用,而有相当一部分是无用,甚至有害的,这就是有机分解产物。
这种有机杂质的存在会使镀层起泡,光亮度不均匀。
因此,需对镀液进行定期净化处理,在生产正常情况下,每月1次,可用5 g/L 专用无氰活性炭吸附处理,或用常规双氧水处理后用活性炭吸附,过滤除去。
4. 2 金属杂质镀液在配制时使用了不纯的化工原料或生产过程中由外界带入的异类金属杂质(如铁、铜、铅等),会对镀层质量产生影响。
但去除杂质(包括有机杂质)的方法较简单而有效,如铁等是以氢氧化物形式悬浮在镀液中,只要经常过滤即可除去。
具体金属杂质对镀层的影响及去除方法如下:铁杂质离子质量浓度积累到5 g/L 时,低电流密度区镀层呈黑色,纯化处理也不会好转;铜杂质离子质量浓度达到3 g/L 时,镀层发白,钝化或醋酸浸渍后变黑;铅杂质离子质量浓度达万方数据•14 •到1.5 g/L 时,镀液分散能力明显下降,低电流密度区镀层也呈现黑色;如果镀液混入镍离子,则镀层孔隙增多,硬度提高。
大多数金属杂质都可以用锌粉置换使之还原后沉淀,然后用过滤的方法除去。
如每月在镀液中加入0.5 g/L 的锌粉,经充分搅拌后过滤,即可将杂质控制在允许范围内。
而对于铜离子,可用小电流密度电解法除去;如镀液中有铬杂质影响,可以用0.2 g/L 的连二亚硫酸钠(保险粉),经水溶解后搅拌下加入而将Cr(VI)还原为Cr(III)。
在电镀现场检验杂质影响的切实可行的方法是进行赫尔槽试验。
5 操作条件5. 1 温度与电流温度对电镀是非常重要的,因为它与使用的电流密度有关。
锌酸盐镀液温度达到35 °C ,尤其是超过40 °C 时,镀层发雾,光亮度下降,添加剂消耗量增大,阳极溶解快,锌离子浓度高,镀液分散能力差,镀件棱角、毛刺多且粗糙。
冬期液温低于10 °C 时,不仅电流密度范围窄,阴极电流效率低,沉积速度慢,而且镀层容易起泡。
至于电流密度,虽然工艺允许范围较宽,一般为0.5 ~ 6.0 A/dm 2,但最好控制在2 A/dm 2左右(可在约±0.5 A/dm 2范围内波动)。
欲正确测定镀件的电流密度,必须仔细测量待镀工件实际面积,这样才能获得质量好的锌镀层。
5. 2 阳极面积锌酸盐镀锌使用的阳极面积应当比氰化物镀锌的阳极面积大一些。
但由于锌酸盐镀锌液中的锌质量浓度较低(约10 g/L ),如果所用阳极与阴极(镀件)面积比为2∶1,则锌离子质量浓度会增高;如果减少阳极面积,将引起阳极钝化,影响电流正常导通,加上添加剂对阳极的影响,此时阳极更易钝化。