锌酸盐镀锌工艺的故障原因与处理方法
镀锌的方法
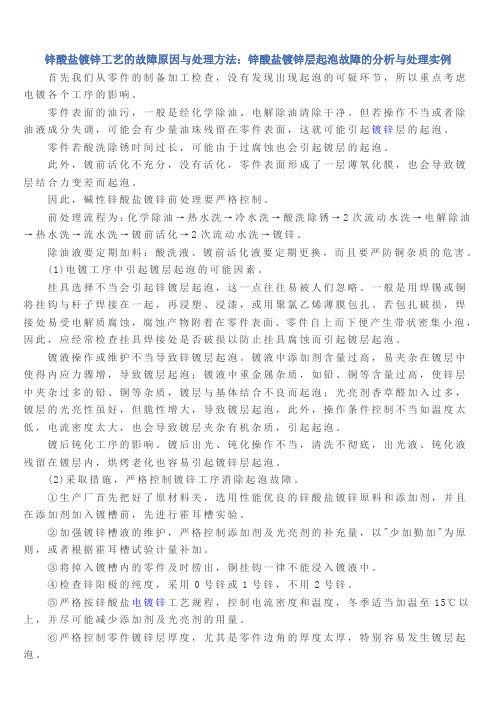
锌酸盐镀锌工艺的故障原因与处理方法:锌酸盐镀锌层起泡故障的分析与处理实例首先我们从零件的制备加工检查,没有发现出现起泡的可疑环节,所以重点考虑电镀各个工序的影响。
零件表面的油污,一般是经化学除油、电解除油清除干净。
但若操作不当或者除油液成分失调,可能会有少量油珠残留在零件表面,这就可能引起镀锌层的起泡。
零件若酸洗除锈时间过长,可能由于过腐蚀也会引起镀层的起泡。
此外,镀前活化不充分,没有活化,零件表面形成了一层薄氧化膜,也会导致镀层结合力变差而起泡。
因此,碱性锌酸盐镀锌前处理要严格控制。
前处理流程为:化学除油→热水洗→冷水洗→酸洗除锈→2次流动水洗→电解除油→热水洗→流水洗→镀前活化→2次流动水洗→镀锌。
除油液要定期加料;酸洗液、镀前活化液要定期更换,而且要严防铜杂质的危害。
(1)电镀工序中引起镀层起泡的可能因素。
挂具选择不当会引起锌镀层起泡,这一点往往易被人们忽略。
一般是用焊锡或铜将挂钩与杆子焊接在一起,再浸塑、浸漆,或用聚氯乙烯薄膜包扎。
若包扎破损,焊接处易受电解质腐蚀,腐蚀产物附着在零件表面、零件自上而下便产生带状密集小泡,因此,应经常检查挂具焊接处是否破损以防止挂具腐蚀而引起镀层起泡。
镀液操作或维护不当导致锌镀层起泡。
镀液中添加剂含量过高,易夹杂在镀层中使得内应力骤增,导致镀层起泡;镀液中重金属杂质,如铅、铜等含量过高,使锌层中夹杂过多的铅、铜等杂质,镀层与基体结合不良而起泡;光亮剂香草醛加入过多,镀层的光亮性虽好,但脆性增大,导致镀层起泡,此外,操作条件控制不当如温度太低,电流密度太大,也会导致镀层夹杂有机杂质,引起起泡。
镀后钝化工序的影响。
镀后出光、钝化操作不当,清洗不彻底,出光液、钝化液残留在镀层内,烘烤老化也容易引起镀锌层起泡。
(2)采取措施,严格控制镀锌工序消除起泡故障。
①生产厂首先把好了原材料关,选用性能优良的锌酸盐镀锌原料和添加剂,并且在添加剂加入镀槽前,先进行霍耳槽实验。
②加强镀锌槽液的维护,严格控制添加剂及光亮剂的补充量,以"少加勤加"为原则,或者根据霍耳槽试验计量补加。
用酒石酸钾钠解决锌酸盐镀锌层发花问题
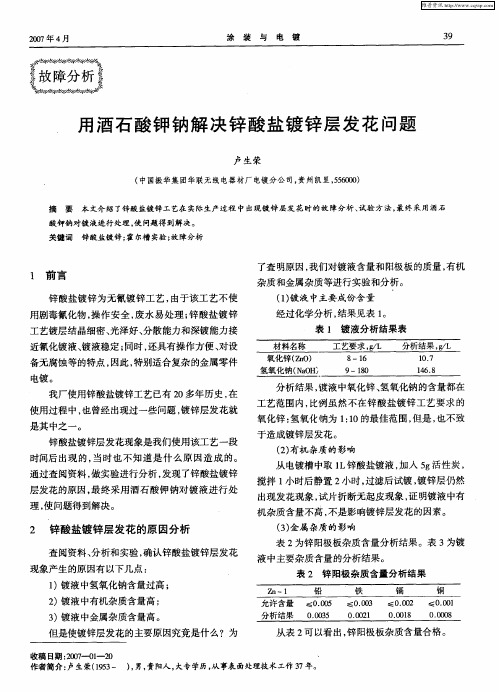
杂质和金属杂质等进行实验和分析。
() 液 中主要 成份 含 量 1镀
经过化学分析, 结果见表 1 。
表 1 镀 液分析 结果 表
材料名称
氧化锌 (n ) z0 氢氧化钠 ( a H NO
近氰化镀液、 镀液稳定 ; 同时, 还具有操作方便 、 对设 备无腐蚀等的特点 , 因此, 特别适合复杂的金属零件
半 光 亮
电 流 密度 增 大
光亮
锌分别与分析纯氢氧化钠、 工业级氢氧化钠( 工人加 料剩下的)不经过处 理按工艺参数 的 中限各配制 ,
1 L镀锌 溶液 , 加入 光亮 剂 , 霍尔槽 试验 。 做 试验条 件 : 电流 2 温度 室 温 , 间 1 钟 , A, 时 0分 结 果 如 图 1图 2 ,
酸钾钠对镀 液进行 处理 , 问题得到解决。 使 关键词 锌 酸盐镀锌 ; 尔槽 实验 ; 障分析 霍 故
了查 明原 因 , 我们 对镀液 含 量和 阳极板 的质 量 , 有机
1 前 言
锌酸盐镀锌为无氰镀锌工艺 , 由于该工艺不使 用剧毒氰化物, 操作安全 , 废水易处理 ; 锌酸盐镀锌 工艺镀层结晶细密 、 光泽好、 分散能力和深镀能力接
镀
2O O7年第 2 期
表 3 镀 液 中主要金 属 杂质含 量分析 结果
4 采取措施消 除镀锌层发花现象
通 常 , 理锌 酸盐镀 液 中的金 属杂质 , 处 采用 锌粉 或C K一78但是 , 7, 处理 时 间长 、 作 烦琐 , 别是 遇 操 特
从表 3看 出 , 杂质含 量超标 , 步判定 这是 影 铁 初 响锌 镀层 发花 的 因素 。 锌酸盐 镀锌 的 主要材 料为氧 化锌 、 氢氧 化钠 , 该
镀锌常见质量问题及其解决方法
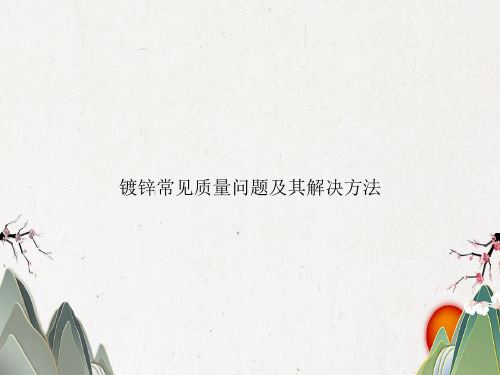
• 2、原料钢卷边部较脏(有油或其它脏物),清洗不 干净,也容易造成侧缘露钢。
• 3、a.炉区非氧化直火燃烧段(NOF段)烧嘴变形致 火焰直接烧于钢板,致带钢边部氧化。b.烧嘴火焰调 的不好直接烧于钢板,致带钢边部氧化(空燃比不正确 或烧嘴变形后致LPG、AIR混合不好)。更换或维修 好变形烧嘴,调节好火焰(空燃比)即可。炉区NOF 烧嘴空燃比范围:0.92~0.98均可,在保证质量的 情况下,空燃比应尽量按偏大控制。日本内外炉推荐 空燃比为0.965。
• 应对措施:1、减速。 2、改变张力:选择合适的张 力(有时减小、有时增大),可能原因分析:张力大 时造成轴承处卡死,张力小时摩擦系数不够。 3、更 换规格:比如生产0.28mm出现划伤时,换0.33mm可 能会正常;生产0.43mm出现划伤时,换0.28mm可 能会正常。 4、沉辊辊面摩擦系数的改变:如是否有 沟槽,辊面是否结渣等。 5、沉辊整修的影响(整修 组补充):
• 点状锌渣痕:沉辊粘渣、锌液中悬浮渣较多、面渣较 多、炉鼻处(锌液浸泡部分)粘渣等因素均可造成板 面点状锌渣痕。解决思路:1、掌握正确的刮渣方法 和捞面渣方法。2、定期清理底渣。3、清除炉鼻处粘 渣。4、有时更换沉辊即可消除点状锌渣痕,具体原 因仍有待探讨。(与沉辊沟槽有何联系?与沉辊转动 是否同步有无联系?是否锌液中悬浮渣较多?)
• 七、板面条状或线状露钢:露钢在板面纵向成 线条状,以连续性较为多见。
• 常见原因:1、炉区漏气,气流喷吹在运行中 的带钢上,形成线条状氧化。 2、带钢在出锌 池前板面被划伤(如前处理辊轮、炉底辊、热 张力辊、沉辊等),而划伤处又粘上了污染物 (如油泥、炉灰、锌灰等),造成镀不上锌。
镀锌件常见问题和解决方法
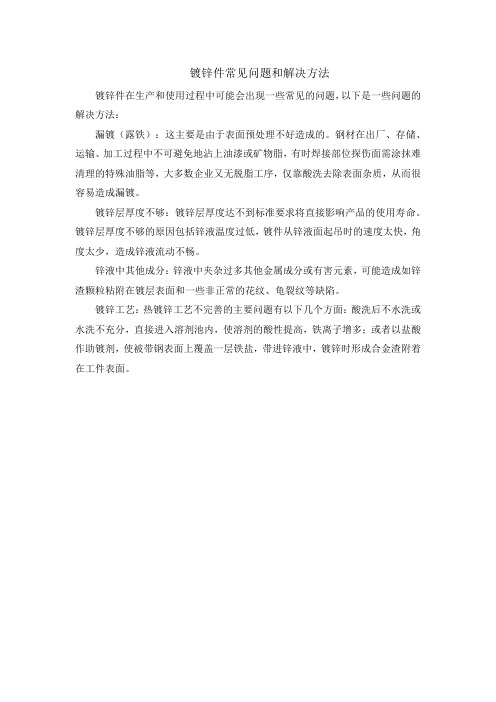
镀锌件常见问题和解决方法
镀锌件在生产和使用过程中可能会出现一些常见的问题,以下是一些问题的解决方法:
漏镀(露铁):这主要是由于表面预处理不好造成的。
钢材在出厂、存储、运输、加工过程中不可避免地沾上油漆或矿物脂,有时焊接部位探伤面需涂抹难清理的特殊油脂等,大多数企业又无脱脂工序,仅靠酸洗去除表面杂质,从而很容易造成漏镀。
镀锌层厚度不够:镀锌层厚度达不到标准要求将直接影响产品的使用寿命。
镀锌层厚度不够的原因包括锌液温度过低,镀件从锌液面起吊时的速度太快,角度太少,造成锌液流动不畅。
锌液中其他成分:锌液中夹杂过多其他金属成分或有害元素,可能造成如锌渣颗粒粘附在镀层表面和一些非正常的花纹、龟裂纹等缺陷。
镀锌工艺:热镀锌工艺不完善的主要问题有以下几个方面:酸洗后不水洗或水洗不充分,直接进入溶剂池内,使溶剂的酸性提高,铁离子增多;或者以盐酸作助镀剂,使被带钢表面上覆盖一层铁盐,带进锌液中,镀锌时形成合金渣附着在工件表面。
锌酸盐镀锌工艺的再研究
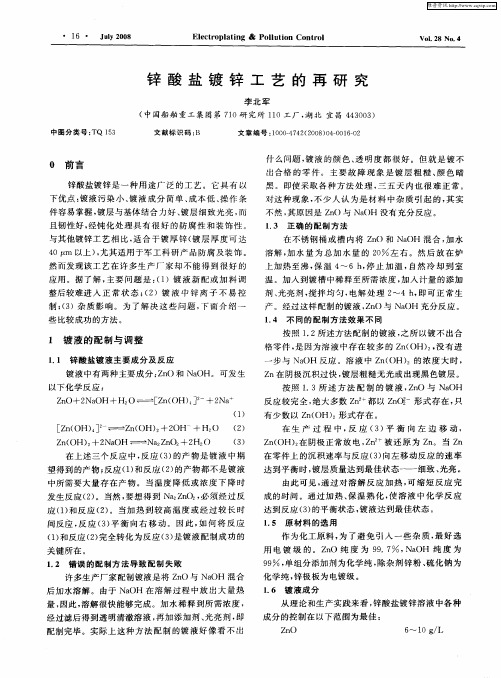
Elc r pl tng & Po l i n Co r e to a i luto ntol
Vo 2 J 1 8 N0 4
.
锌 酸 盐 镀 锌 工 艺 的 再 研 究
李 北 军
( 中国船舶 重工集 团第 7 0研 究所 10工厂 , 北 宜昌 4 30 ) 1 1 湖 40 3
Z OH ) + 2 OH n( 2 Na
Z( n OH)在 阴极正常放 电 , n 被 还原 为 Z 。当 Z Z n n 在 零件上 的沉 积速率与反应 ( ) 3 向左 移动反应 的速 率
在上述 三个反 应 中 , 反应 ( ) 3 的产 物是 镀 液 中期
望得 到的产物 ; 反应 ( ) 反应 ( ) 1和 2 的产物 都不是镀 液
应 用 。据 了 解 , 要 问 题 是 : 1 主 ( )镀 液 新 配 或 加 料 调 整后较难进 入 正 常 状 态 ;2 ( )镀 液 中 锌 离 子 不 易 控
上加热 至沸 , 温 4 , 止 加 温 , 保 ~6h 停 自然 冷却 到 室 温 。加入 到镀 槽 中稀 释至所需浓度 , 加入计 量 的添加 剂、 光亮剂 , 搅拌 均 匀 , 电解 处 理 2 , ~4h 即可 正常 生 产 。经过这样 配制 的镀液 ,n Z O与 Na OH 充分反应 。
化学纯 , 锌极 板为 电镀级 。
16 镀 液 成 分 .
许多 生产厂家配制镀 液是将 Z O与 N OH 混合 n a
后 加水溶解 。由于 N OH 在 溶解 过程 中放 出大 量热 a
量, 因此 , 溶解很快 能够 完成 。加 水稀释 到所需 浓度 ,
在不锈 钢桶 或槽 内将 Z O 和 N O 混 合 , n aH 加水
锌层外观故障分析

在我国碱性锌酸盐镀锌约占镀锌总量的50%。
在长期实践中,人们积累了许多碱性锌酸盐镀锌工艺维护管理的成功经验和排除故障的有效方法。
由于锌酸盐镀锌溶液配方和溶液成分的差异,尤其是添加剂(有进口的和国内公司生产的)的不同,可能出现的故障原因和故障特征也有所不同。
因此,需要技术人员认真分析,找出故障出现的原因,进而找出消除故障的措施。
一般而言,锌酸盐镀锌可能出现的故障现象和原因主要包括以下几种。
1 镀层起泡发脆、结合力差可能原因:①镀前处理不良;②镀液中氧化锌含量高;③镀液中氢氧化钠含量低;④阴极电流密度大;⑤镀液温度低;⑥添加剂添加过量;⑦镀液中有机杂质多等。
2 镀层结晶粗糙可能原因:①镀液中氧化锌含量高;②氢氧化钠含量低;③电流密度大;④添加剂添加过量;⑤镀液中金属杂质多等。
3 镀层沉积速率慢可能原因:①镀液中氧化锌含量低;②氢氧化钠含量高或低;③电流密度小;④镀液的温度低等。
4 镀层光亮不均匀可能原因:①电流密度小;②镀液中添加剂不足;③镀液中有机杂质多等。
5 镀层花斑发雾可能原因:①镀前处理不良;②添加剂过量;③镀液的温度高等。
6 镀层发暗或钝化无光泽可能原因:①镀液中添加剂不足;②金属杂质多等。
7 镀锌阳极出现钝化发黑可能原因:①镀液中氢氧化钠含量低;②阳极的面积小;③电流密度大等。
8 镀液的分散能力差可能原因:①添加剂不足;②氧化锌含量高;③氢氧化钠含量高;④镀液温度高等。
9 镀液的深镀(覆盖)能力差可能原因:①电流密度小;②镀液温度低;③添加剂不足,有机杂质多等。
需要说明的是,镀锌过程中出现上述故障,有可能是其中的一种或几种,分析和解决这些故障的思路和方法需要综合考虑多种因素。
另外在生产中还有一些其他的特殊的故障出现,如镀层脆性大等也需要注意。
1 工件镀锌后镀层起泡的原因是什么?工件镀锌后有的镀层当时看不出什么问题,放置几天或经过加热除氢后就发现有起泡现象。
对氰化物镀锌、碱性锌酸盐镀锌或氯化物镀锌,这种镀层起泡的相同原因都是由于:1)工件镀前处理不良;2)添加剂加入过量;3)电解液中锌离子质量浓度过高而络合剂不足。
影响锌酸盐镀锌质量的原因浅析

•12 •影响锌酸盐镀锌质量的原因浅析奚兵(常州市荆川里小区12丙201,江苏 常州 213015)摘 要:分析了镀前处理、镀液成分、杂质、操作条件对锌酸盐镀锌质量的影响,并给出了相应的解决办法和措施。
介绍了各工序操作中应注意的问题及镀液维护的参数范围。
实践表明,锌酸盐镀锌工艺可以获得不亚于氰化物镀锌质量的镀层。
关键词:锌酸盐镀锌;前处理;镀液维护;镀层质量 中图分类号:TG178; TQ153.15文献标志码:B文章编号:1004 – 227X (2009) 10 – 0012 – 03Analysis on causes affecting deposit quality of zincate zinc plating // XI BingAbstract: The effects of pre-plating treatment, bath composition, impurities and operation conditions on the deposit quality of zincate zinc plating were analyzed. Some corresponding solutions and measures were suggested. The problems needing attention in process operation and the parameter range of bath maintenance were introduced. The practice shows that the quality of deposit obtained by zincate zinc plating is no worse than that by cyanide zinc plating. Keywords: zincate zinc plating; pretreatment; bath maintenance; deposit qualityAuthor’s address: Flat.201, The Third Unit, No.12 Building, Jingchuanli Residential Quarter, Changzhou 213015, China1 前言锌酸盐镀锌是在传统氰化物镀锌基础上发展起来的环保型镀锌工艺之一。
常见锌镀层结合力差的6种原因
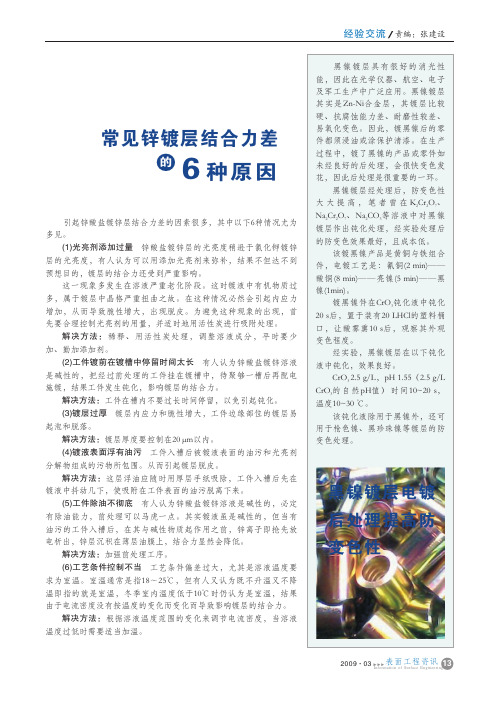
2009·03经验交流责编:张建设13Information of Surface Engineering表面工程资讯引起锌酸盐镀锌层结合力差的因素很多,其中以下6种情况尤为多见。
(1)光亮剂添加过量 锌酸盐镀锌层的光亮度稍逊于氯化钾镀锌层的光亮度,有人认为可以用添加光亮剂来弥补,结果不但达不到预想目的,镀层的结合力还受到严重影响。
这一现象多发生在溶液严重老化阶段。
这时镀液中有机物质过多,属于镀层中晶格严重扭曲之故。
在这种情况必然会引起内应力增加,从而导致脆性增大,出现脱皮。
为避免这种现象的出现,首先要合理控制光亮剂的用量,并适时地用活性炭进行吸附处理。
解决方法:稀释、用活性炭处理,调整溶液成分,平时要少加、勤加添加剂。
(2)工件镀前在镀槽中停留时间太长 有人认为锌酸盐镀锌溶液是碱性的,把经过前处理的工件挂在镀槽中,待聚够一槽后再配电施镀,结果工件发生钝化,影响镀层的结合力。
解决方法:工件在槽内不要过长时间停留,以免引起钝化。
(3)镀层过厚 镀层内应力和脆性增大,工件边缘部位的镀层易起泡和脱落。
解决方法:镀层厚度要控制在20 μm以内。
(4)镀液表面浮有油污 工件入槽后被镀液表面的油污和光亮剂分解物组成的污物所包围。
从而引起镀层脱皮。
解决方法:这层浮油应随时用厚层手纸吸除,工件入槽后先在镀液中抖动几下,使吸附在工件表面的油污脱离下来。
(5)工件除油不彻底 有人认为锌酸盐镀锌溶液是碱性的,必定有除油能力,前处理可以马虎一点。
其实镀液虽是碱性的,但当有油污的工件入槽后,在其与碱性物质起作用之前,锌离子即抢先放电析出,锌层沉积在薄层油膜上,结合力显然会降低。
解决方法:加强前处理工序。
(6)工艺条件控制不当 工艺条件偏差过大,尤其是溶液温度要求为室温。
室温通常是指18~25℃,但有人又认为既不升温又不降温即指的就是室温,冬季室内温度低于10℃时仍认为是室温,结果由于电流密度没有按温度的变化而变化而导致影响镀层的结合力。
- 1、下载文档前请自行甄别文档内容的完整性,平台不提供额外的编辑、内容补充、找答案等附加服务。
- 2、"仅部分预览"的文档,不可在线预览部分如存在完整性等问题,可反馈申请退款(可完整预览的文档不适用该条件!)。
- 3、如文档侵犯您的权益,请联系客服反馈,我们会尽快为您处理(人工客服工作时间:9:00-18:30)。
锌酸盐镀锌工艺的故障原因与处理方法:镀层钝化膜质量故障(发花、变色、变暗等)
目前镀锌进行钝化处理的工艺主要低铬彩色钝化和三价铬钝化,在钝化后有时放置一夜或几天时间,钝化膜的表面就会出现雨点状白点,大小不一,钝化膜也变暗变淡,光亮度下降。
1.原因分析
实际上发生这种故障的原因更复杂,可能有镀液的问题;前处理不良的问题;基材有麻点,镀后出光等清洗不良的问题;钝化液成分比例失调的问题;钝化膜老化时间不够的问题;环境的问题,空气中水蒸气、酸雾严重使得钝化膜色泽变化和腐蚀等。
2.解决方法
针对上述可能的原因,逐条采取措施。
调整镀液成分到工艺规范,并且对镀液进行锌粉、硫化钠处理,再进行电解处理;加强除油、活化等前处理工序;加强镀后清洗和出光工序;严格控制钝化溶液成分和钝化工艺参数,控制好钝化膜的色彩;加强钝化后老化工艺的控制;改善工作环境,镀后零件尽快入库等。
尤其要注意的是钝化后的老化问题,因为热水槽老化温度过高(>70℃),就会使得钝化膜中的六价铬溶解,形成耐蚀性很差的多孔钝化膜。
就容易出现镀锌层钝化膜表面的雨点状白点,钝化膜变暗变淡,光亮度下降的故障。
严格控制钝化老化工序(60℃),这种故障就可以消除,生产恢复到正常。
其他环节也会出现钝化质量的故障的问题,如某厂采用DE碱性锌酸盐镀锌液,低铬钝化的滚镀锌工艺生产线,出现了钝化膜发花,表面有许多大块不规则灰黑色斑块的故障。
经分析是由于镀锌后的清洗槽中白色絮状沉淀较多,出光槽溶液呈黄棕色,pH值接近4,这些都可能带来电镀故障,由于清洗不干净和出光液pH高,造成电镀零件表面碱性镀液的清洗不够,出光液的出光作用下降,导致钝化膜发花等故障。
通过增加一道热水洗,将出光液pH调至l左右后,故障排除,生产恢复到正常。