塑胶产品涂装常见问题及解决办法
塑胶产品着色时一般出现的问题及处理方法

塑胶产品着色时一般出现的问题及处理方法
1.产品表面起粒:主要原因:
①料筒及模头有杂质;
②温度不正确;
③原料在料筒内加热停留时间太长;
④色母或色粉的分散性未处理好;
⑤过滤网已穿孔。
处理方法:把塑机温度调至低于正常温度10 -20℃,开动塑机,用原色塑料树脂以最慢速度重新进行清理工作,必要时把模头拆开清理,并调整好温度,及时更换过滤网。
改用分散良好的色母或色粉重新调试。
2.扩散不均匀:主要原因:
①混料不均匀;
②温度不适当;
③色母和原料相溶性差;
④塑机本身塑化效果差;
⑤色母投放比例太小。
处理方法:充分搅拌、温度调整适当、更换色母或原材料、更换其他机台生产、调整色母投放比例。
3.经常断料主要原因:
①温度不正确;
②原料亲和性差;
③色母分散太差;
④色母投放比例太高。
处理方法:把温度调较准确、更换所用原料、更换分散优良的色母、降低色母使用比例。
4.颜色有变化:主要原因:
①使用的原材料底色不一致;
②塑机未清洁干净;
③所用的色母或色粉耐温程度低,温度过高时消色;
④下料门未清洁干净;
⑤加工工艺改变;
⑥色母或色粉本身有色差;
⑦水口料搭配不当;
⑧混料机未清洁干净或混料时间未控制好
处理方法:使用与打板时颜色一致的原料及调整好水口料的搭配比例;把塑机、下料门及混料机彻底清洁干净;改用耐温适当、颜色一致的色母或色粉;使用稳定的加工工艺。
浅谈塑料件涂装与漆膜常见弊病处理

浅谈塑料件涂装与漆膜常见弊病处理随着生产制造技术的不断发展,塑料件越来越广泛地应用于各个领域。
为了满足消费者对产品色彩的需求,以及延长产品使用寿命,制造商们越来越注重塑料件的涂装和漆膜处理。
但是,塑料件涂装和漆膜存在常见的弊病,如果不及时处理,会严重影响产品的使用寿命和外观质量。
本文将从常见的塑料件涂装和漆膜弊病入手,介绍处理方法和预防措施。
一、常见弊病1.涂层起泡涂层起泡是由于表面存在油脂、水汽、灰尘等杂质,或涂装环境湿度过大,涂装前表面处理不彻底等原因造成。
涂层起泡严重影响外观质量,同时容易使涂层破裂、脱落。
2.熔融爆裂塑料件涂装时,由于过高的烤漆温度或烘烤时间过长,容易导致熔融爆裂。
熔融爆裂会造成漆膜厚薄不一,表面质量不良,且会导致产品变形、缩水等问题。
3.漆膜脱落漆膜脱落是由于涂装前表面处理不彻底,或使用低质量的涂料和油漆导致的。
漆膜脱落会造成外观质量不良,同时降低产品的保护性能。
4.色差问题色差问题是由于批次、环境、产品材质等原因造成。
色差严重影响产品的美观度,同时也会对消费者的体验产生不良影响。
二、处理方法1.涂层起泡涂层起泡时,应尽快将起泡处涂层抹平,避免涂层分裂。
如果局部分裂,应使用专业液体修补材料粘合分裂处。
避免涂装环境湿度过大,同时在涂装前应彻底清洁表面。
2.熔融爆裂熔融爆裂时,应尽快将产品取下,让其自然冷却,避免继续加热会导致更大的熔融爆裂。
同时应检查烤漆温度和烤漆时间是否合适,排除设备故障,及时调整涂装参数。
3.漆膜脱落漆膜脱落时,需要重新涂装。
在涂装前应彻底清洗表面,确保完全去除油脂和灰尘。
选择质量可靠的涂料和油漆,同时控制好涂料的厚度和均匀度。
4.色差问题色差问题时,需要通过设备调整和涂料配料解决。
同时在使用工具和设备时应尽量保持稳定,尽量避免因操作失误或设备故障造成的色差。
三、预防措施1.加强表面处理对于压铸、注塑或挤出件等塑料产品,在经过模具成形或切割后,表面会产生一定程度的氧化,油脂,灰尘等杂质,这些杂质直接影响后续涂装的质量。
涂膜常见弊端的原因及处理方法

塑料涂装中涂膜常见弊病及解决办法在涂装中遇到一些涂膜弊病和涂装缺陷等可能是不少施工单位和施工人员遇到过的了。
不同材质不同物体的涂装中都有可能出现这种现象。
这个时候我们就要掌握足够多的涂膜弊病的处理方法,针对具体的情况制定相应的解决方案加以修复。
塑料涂装中涂膜是有很多缺陷的,不过针对这个方面的缺陷我们都有相应的对策。
涂料能均匀稳定地涂覆于塑胶件表面的最主要条件,为涂料的表面张力必须小于被涂覆物的表面张力。
以下是常见的几种问题及其解决方法。
1. 一、橘纹现象橘皮现象是涂装设备涂漆过程中常见又较难克服的流平性问题,影响因素众多,大大地影响到涂膜的平整性。
原因及对策如下:1、在喷涂过程中,由于溶剂挥发太快,湿膜黏度急剧增加,使流平变得困难而产生橘皮。
措施是根据环境季节温度变化来选择合适的稀释剂,例如聚氨酯涂料的稀释剂有冬用和夏用之分。
?2、涂料黏度过大。
涂料粘度大时,涂料雾化性和湿膜流平性都差。
因按照施工规范进行兑稀并采用带恒温装置的喷涂设备。
3、环境温度偏高,或闪干时间不足就进行烘烤。
?4、喷涂室内空气流速太快,使湿膜溶剂快速挥发而难以流平。
(2)塑料工件温度太高,使溶剂瞬间挥发,湿膜来不及流平。
?5、喷涂时出漆量太小或喷涂距离太远,表面沉积涂膜太薄,涂装设备流平变得困难。
?6、喷枪雾化不良,漆雾颗粒过大也产生橘纹。
降低出漆量并提高压缩空气输出量,改善雾化性能。
?7、喷涂距离太近。
喷距太近虽然涂膜厚有利于流平,但压缩空气的冲击力使厚涂膜产生更大的橘纹,反而使流平性变差。
二、颗粒现象涂膜表面常见的缺陷是颗粒,严重影响外观。
对于少数微细颗粒,采用1 500目以上水砂纸打磨修饰,颗粒过大时或而积大时用800目水砂纸打磨重新喷涂。
由干塑料涂膜要求外观是非常严格的,因此颗粒现象是塑料涂料涂装过程中返修率高的主要原因,涂膜颗粒关键是要做好预防措施。
三、底漆与清漆层间附着力问题 ?如果第一道底漆的表面张力低干第二道罩光清漆的情况下,那么两层涂层间的附着力不佳,所以塑胶底漆在生产过程中的表面张力不应太低,能与底材咬合最佳为止,并使面漆对底漆的润湿性良好,两层涂膜要有一定厚度的界而层才能有稳定的附着力。
塑胶件常见不良状况及形成原因、改善对策
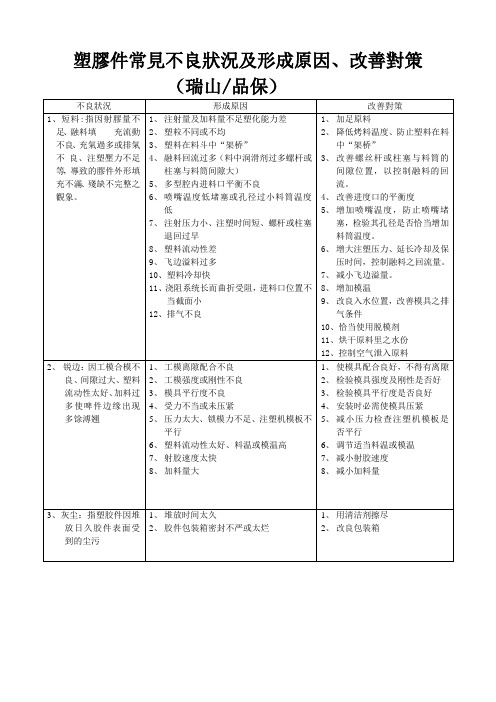
3、模温或啤塑温度低
1、烘干原料里水分
2、烤虑原料
3、增加模温及啤塑温度
10、顶白:指因部分顶针伸展太快或顶力太大,造成胶件表面呈圆形或半圆形白条称为“顶白”。
1、顶针伸展太快
2、顶力太大
3、脱模剂未使用或使用不当
1、调节顶针伸展速度
2、减小压力
3、适当使用脱模剂
11、缩水:指胶件冷却后变形一般因冷却不够或循环水温不符所致
1、压力(射胶枪)
2、增加料温及模温
3、增大压力及加快射胶速度
4、改良模具之冷却系统
5、改良水口位置及尺寸
6、供料要足
7、抛光模具改良光洁度
8、使用适当脱模剂
16、气泡:由于融料里泄入空气而导致的爆花现象多为局部起层或甩层
1、原料里含水分溶剂或挥发物
2、料温太高,加热时间太长塑料降分解
3、压力小
4、柱塞或螺丝杆退回过早
1、用布将防锈油,脱模剂擦干净
2、用抹面水擦干净胶件表面之油污
5、毛边:指因披锋后未除尽的毛刺
1、披锋太大批除不善
2、操作员操作不合理
1、调校披锋
2、指导操作员用正确的方法批除披锋
6、混色:包括黑点、白点、杂点、银纹、流纹、异色斑等
1、塑胶原料里含水分高、有低挥发物
2、料温及模温高
3、压力太大
4、模具表面有水分润滑油或脱模剂选用不相融料
5、多型腔内进料口平衡不良
6、喷嘴温度低堵塞或孔径过小料筒温度低
7、注射压力小、注塑时间短、螺杆或柱塞退回过早
8、塑料流动性差
9、飞边溢料过多
10、塑料冷却快
11、浇阻系统长而曲折受阻,进料口位置不当截面小
12、排气不良
涂装常见的质量问题

涂装常见的质量问题涂装作为一种常见的表面处理工艺,在各个行业中广泛应用。
然而,在涂装过程中常常会出现一些质量问题,影响涂装效果和产品质量。
本文将就涂装常见的质量问题进行分析和解决方法的探讨,以帮助读者更好地理解和解决涂装过程中可能遇到的问题。
1. 颜色不均匀颜色不均匀是涂装过程中最常见的质量问题之一。
它可能表现为颜色深浅不一、有色差或颜色分布不均匀等情况。
造成颜色不均匀的原因有很多,下面列举了几个常见的原因及解决方法:原因:•涂料本身的质量问题:涂料中颜料分散不均匀或颜料含量不足,导致涂料颜色不均匀。
•涂料施工不当:涂料喷涂厚度不均匀、涂料干燥时间不足等。
•基材表面处理不当:基材表面存在污垢、油脂或氧化物等,影响涂料的附着力和均匀性。
解决方法:•选择质量可靠的涂料供应商,确保涂料质量稳定。
•严格按照涂料供应商的要求进行涂料施工,控制涂料的喷涂厚度和干燥时间。
•在涂装前,对基材进行彻底的清洁和表面处理,确保基材表面的光洁度和附着力。
2. 涂层起皮或剥落涂层起皮或剥落是涂装过程中另一个常见的质量问题。
它可能表现为涂层与基材分离、涂层脱落或涂层表面出现裂纹等情况。
下面列举了几个常见的原因及解决方法:原因:•基材表面处理不当:基材表面存在油脂、污垢或氧化物等,影响涂料与基材的附着力。
•涂料不匹配:涂料与基材不相容,或者涂料之间的附着力不足。
•涂料施工不当:涂料喷涂厚度过大或者涂料干燥时间不足。
解决方法:•在涂装前,对基材进行彻底的清洁和表面处理,确保基材表面的光洁度和附着力。
•选择与基材相匹配的涂料,确保涂料与基材之间的附着力。
•严格按照涂料供应商的要求进行涂料施工,控制涂料的喷涂厚度和干燥时间。
3. 涂装气泡或麻点涂装过程中出现气泡或麻点是另一个常见的质量问题。
气泡可能表现为涂层表面出现小气泡或大气泡,麻点可能表现为涂层表面出现小颗粒或凹陷。
下面列举了几个常见的原因及解决方法:原因:•涂料中含有挥发性物质:涂料中含有挥发性物质,如溶剂或水分,造成涂装过程中产生气泡。
塑胶常见不良及解决方法

塑胶常见不良及解决方法塑胶是一种常见的材料,广泛应用于各种行业和领域。
然而,由于塑胶的特性以及制造过程中的一些问题,常常会出现一些不良现象。
本文将重点介绍一些常见的塑胶不良及其解决方法。
1.氣泡:塑膠制品中常見的一種不良現象是氣泡,這會在成品表面或内部形成小气囊。
气泡的形成是由于塑胶熔融时含有的空气或挥发物没有充分释放出来。
解决方法包括降低加工温度、增加熔体压力、增加注射速度和使用抗气泡添加剂等。
2.热胀冷缩:塑胶制品在温度变化下会发生热胀冷缩,导致尺寸变化。
这可能会导致配件无法正常连接或安装。
为了解决这个问题,可以采用材料改性或加工工艺改进,如增加冷却时间、降低注射温度等。
3.白化:白化是指塑胶制品表面或内部出现白色斑点或条纹。
这种现象通常是由于塑胶在注射过程中发生气泡聚集或制品未达到均匀熔融所致。
解决方法包括优化注射工艺、增加熔体压力、使用抗白化添加剂等。
4.热裂纹:热裂纹是指在塑胶产品成型过程中出现的裂纹现象。
这通常是由于塑胶在成型过程中存在过大的应力集中,导致塑胶产生裂纹。
解决方法包括改变模具设计、增加冷却时间、预混塑胶料等。
5.变色:变色是指塑胶制品在使用或储存过程中出现颜色变化。
这可能是由于塑胶材料受到光、热、氧化等外界因素的影响所致。
解决方法包括选择适当的防褪色添加剂、合理储存塑胶制品等。
6.毛刺:毛刺是指塑胶制品表面出现不平整、刺状的小颗粒。
这通常是由于模具表面不平整或注射工艺不当所导致的。
解决方法包括优化模具设计、控制注射压力、调整注射速度等。
7.缩水:缩水是指塑胶制品在冷却过程中发生体积收缩。
这可能导致尺寸偏离设计要求。
解决方法包括优化塑胶成型工艺、增加冷却时间和选择合适的材料等。
8.潜伏期延长:有些塑胶在使用一段时间后会发生不良现象,如变形、断裂等。
这可能是由于塑胶受到环境因素、应力或热老化的影响导致的。
解决方法包括选择合适的材料、控制加工温度、降低应力等。
总结起来,塑胶制品的不良现象可能是由于材料、工艺或环境等多种因素造成的。
塑胶件常见缺陷产生的原因及解决方法

塑胶件常见缺陷产生的原因及解决方法1.原材料质量问题:塑胶件常见的原材料问题包括原材料中含有杂质、原料失效、原料配比不正确等。
这些问题会导致塑胶件的质量下降和性能降低。
解决方法是对原材料进行严格的检验和筛选,确保原材料的纯度和质量。
2.模具设计问题:模具设计不合理可能导致塑胶件的缺陷,例如模具壁厚不均匀、模腔表面粗糙等。
解决方法是对模具进行合理设计,确保模具的结构和尺寸满足产品要求,并提高模具的制造工艺和加工精度。
3.注塑工艺问题:注塑过程中的工艺参数设置不当会导致塑胶件出现缺陷,例如温度不稳定、压力不均匀、注射速度过快等。
解决方法是优化注塑工艺参数,确保温度、压力、速度等参数的稳定和均匀。
4.模具磨损和损坏:长时间使用会导致模具磨损和损坏,影响塑胶件的质量和外观。
解决方法是加强模具的保养和维护,定期进行模具清洁和润滑,并进行必要的修复和更换。
5.后道工艺问题:塑胶件的后道加工也可能引发缺陷,例如焊接不牢固、喷涂不均匀等。
解决方法是加强后道工艺的控制,提高工艺的稳定性和一致性。
综上所述,要解决塑胶件常见缺陷的问题,需要从原材料选择、模具设计、注塑工艺、模具维护和后道工艺等方面入手,通过优化和控制各个环节,提高产品的质量和性能。
同时,还需要建立健全的质量管理体系,对生产过程进行全面监控和检测,及时发现和解决问题。
最后,还应该加强员工的培训和技能提升,提高操作技术和质量意识,提高产品的一致性和稳定性。
只有通过不断改进和严格控制,才能有效降低塑胶件的缺陷率,提高产品的质量和市场竞争力。
塑胶常见不良解决方法
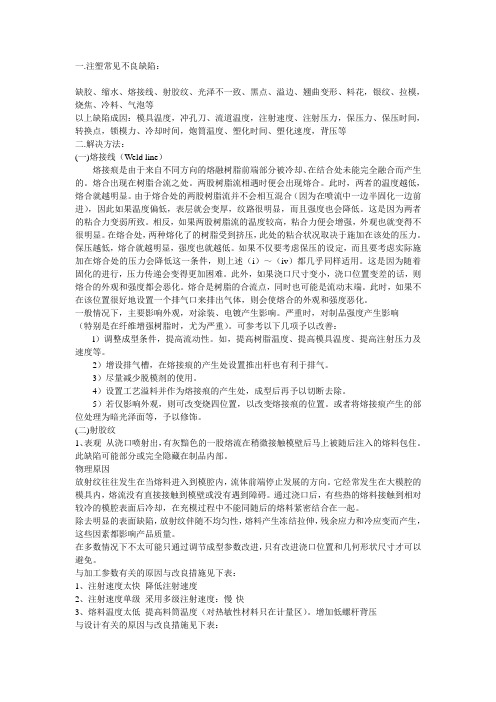
一.注塑常见不良缺陷:缺胶、缩水、熔接线、射胶纹、光泽不一致、黑点、溢边、翘曲变形、料花,银纹、拉模,烧焦、冷料、气泡等以上缺陷成因:模具温度,冲孔刀、流道温度,注射速度、注射压力,保压力、保压时间,转换点,锁模力、冷却时间,炮筒温度、塑化时间、塑化速度,背压等二.解决方法:(一)熔接线(Weld line)熔接痕是由于来自不同方向的熔融树脂前端部分被冷却、在结合处未能完全融合而产生的。
熔合出现在树脂合流之处。
两股树脂流相遇时便会出现熔合。
此时,两者的温度越低,熔合就越明显。
由于熔合处的两股树脂流并不会相互混合(因为在喷流中一边半固化一边前进),因此如果温度偏低,表层就会变厚,纹路很明显,而且强度也会降低。
这是因为两者的粘合力变弱所致。
相反,如果两股树脂流的温度较高,粘合力便会增强,外观也就变得不很明显。
在熔合处,两种熔化了的树脂受到挤压,此处的粘合状况取决于施加在该处的压力。
保压越低,熔合就越明显,强度也就越低。
如果不仅要考虑保压的设定,而且要考虑实际施加在熔合处的压力会降低这一条件,则上述(i)~(iv)都几乎同样适用。
这是因为随着固化的进行,压力传递会变得更加困难。
此外,如果浇口尺寸变小,浇口位置变差的话,则熔合的外观和强度都会恶化。
熔合是树脂的合流点,同时也可能是流动末端。
此时,如果不在该位置很好地设置一个排气口来排出气体,则会使熔合的外观和强度恶化。
一般情况下,主要影响外观,对涂装、电镀产生影响。
严重时,对制品强度产生影响(特别是在纤维增强树脂时,尤为严重)。
可参考以下几项予以改善:l)调整成型条件,提高流动性。
如,提高树脂温度、提高模具温度、提高注射压力及速度等。
2)增设排气槽,在熔接痕的产生处设置推出杆也有利于排气。
3)尽量减少脱模剂的使用。
4)设置工艺溢料并作为熔接痕的产生处,成型后再予以切断去除。
5)若仅影响外观,则可改变烧四位置,以改变熔接痕的位置。
或者将熔接痕产生的部位处理为暗光泽面等,予以修饰。
- 1、下载文档前请自行甄别文档内容的完整性,平台不提供额外的编辑、内容补充、找答案等附加服务。
- 2、"仅部分预览"的文档,不可在线预览部分如存在完整性等问题,可反馈申请退款(可完整预览的文档不适用该条件!)。
- 3、如文档侵犯您的权益,请联系客服反馈,我们会尽快为您处理(人工客服工作时间:9:00-18:30)。
一、前述;本人通过多年从事涂装行业工作及在通顺公司对汽车内外饰件塑料涂装产品的了解,深刻体会到,作为一名合格的技术管理工作人员,首先必须了解和掌握所喷涂塑料产品的原料材质以及其性能;再合理的使用涂料,安排生产喷涂工艺,现以书面形式整理成文,欢迎涂装行业同仁看过后多提宝贵意见,(本人邮箱:*********************)常见的塑料类型有:ABS(丙烯氰、丁二烯、苯乙烯)PVC(聚氰乙烯)PE(聚乙烯)PP(聚丙烯)PS(聚苯乙烯)PMMA(聚甲甲基丙烯酸甲酯)PC(聚碳酸酯)POM(聚甲醛)PA(尼龙)等塑胶原材料在塑料涂料施工过程中或施工成膜后会因各方面原因产生多种缺陷,本文涉及最主要的几种缺陷,并尽可能地讨论其产生原因及消除或尽量减少其发生的对策。
塑料涂料的许多缺陷是与表面张力现象相关的,表面张力产生的原因是:液体表面分子上力分布不对称,界面上液体的力与液体内的力不同,表面的分子具有很高的自由能,相当于每单位面积上移去表面层分子所需的能量。
在固体也存在相似表面取向效应,它有表面自由能,表面力作用来减少液体和固体的表面自由能,表面张力作用使液体缩成球,因为球的表面积/ 体积比率是最小的。
如果两个不同表面张力液体相互接触,低表面张力的流去覆盖住较高表面张力的液体,因为这样总表面自由能更低。
这种流动是表面张力差推动的,有些人称为表面张力梯度推动的流动。
涂料能均匀稳定地涂覆于塑胶件表面的最主要条件,为涂料的表面张力必须小于被涂覆物的表面张力。
以下是常见的几种问题及其解决方法。
二、涂装常见的问题及其解决方法2.1缩孔现象当表面张力较高的涂料涂覆于表面自由能较低的底材上,也就是涂料表面张力与底材表面张力相差太大时,容易造成涂料对底材的润湿性不良,接触角变大,使涂料有保持滴状倾向而裸露出被涂面,特别是罩光清漆和颜料份较少的色漆,比较容易出现这种缺陷,而且不容易修补。
缩孔是由低表面张力的小颗粒或小液滴杂物产生的,它们可能存在于塑胶底材上、涂料中或飞落在刚刚涂覆好的湿膜上。
某些低表面张力物质溶解在湿膜中产生一个局部的表面张力差,Marangoni 效应将这低表面张力部分的湿膜从颗粒流开,试图覆盖周围高表面张力的湿膜。
随着流动的发生,溶剂的挥发,表面张力差增大,流动继续,溶剂的挥发增大了黏度,阻碍了流动而最终形成凹下的缩孔。
常见解决方法使用助剂降低涂料表面张力以减少缩孔增加流平。
它可将表面张力降低到大多数会引起缩孔杂物的表面张力以下。
2.2 橘纹现象橘皮现象是涂漆过程中常见又较难克服的流平性问题,影响因素众多,大大地影响到涂膜的平整性。
原因及对策如下:(1) 在喷涂过程中,由于溶剂挥发太快,湿膜黏度急剧增加,使流平变得困难而产生橘皮。
措施是根据环境季节温度变化来选择合适的稀释剂,例如聚氨酯涂料的稀释剂有冬用和夏用之分。
(2) 塑料工件温度太高,使溶剂瞬间挥发,湿膜来不及流平。
(3) 喷涂时出漆量太小或喷涂距离太远,表面沉积涂膜太薄,流平变得困难。
(4) 喷枪雾化不良,漆雾颗粒过大也产生橘纹。
降低出漆量并提高压缩空气输出量,改善雾化性能。
(5) 喷涂距离太近。
喷距太近虽然涂膜厚有利于流平,但压缩空气的冲击力使厚涂膜产生更大的橘纹,反而使流平性变差。
(6) 涂料黏度过大。
涂料粘度大时,涂料雾化性和湿膜流平性都差。
因按照施工规范进行兑稀并采用带恒温装置的喷涂设备。
(7) 环境温度偏高,或闪干时间不足就进行烘烤。
(8) 喷涂室内空气流速太快,使湿膜溶剂快速挥发而难以流平。
(9) 底材粗糙易造成短波橘纹,要提高喷涂清洁度,减少表面颗粒,减少打磨以避免涂膜表面被破坏而产生橘皮。
(10) 飞散漆雾在已喷涂膜表面的沉积也是造成橘纹的一个因素。
另外,尽可能地提高罩光清漆的厚度并延长闪干流平时间,可以大幅度地减少橘纹,尤其是垂直面的橘纹。
2.3 咬底现象咬底是涂膜喷涂时,涂料中的有机溶剂对底层产生严重的溶胀起皱而脱离的现象。
咬底分为涂膜与底材和涂膜之间咬底两种。
底材塑件在注塑时压力不足导致塑件局部密度不一致,存在一定的内应力,而涂料中有机溶剂的极性和溶解力较强时,涂料中的强溶剂会咬进塑件内,出现咬底现象,此时的施工应在不影响涂料溶解性的情况下尽量减弱稀释剂的极性和溶解力,在涂膜咬底的部位用细砂纸打磨一遍后再喷上一道涂料也可以消除咬底现象,在涂装过程中先将底材易咬底的部位薄薄喷涂,最后将此处和另外部位一同涂覆成均匀涂膜,也可以一定程度的减弱咬底现象。
2.4 颗粒现象涂膜表面常见的缺陷是颗粒,严重影响外观。
对于少数微细颗粒,采用1500 目以上水砂纸打磨修饰,颗粒过大时或面积大时用800 目水砂纸打磨重新喷涂。
由于塑料涂膜要求外观是非常严格的,因此颗粒现象是塑料涂料涂装过程中返修率高的主要原因,涂膜颗粒关键是要做好预防措施。
2.5 底漆与清漆层间附着力问题如果第一道底漆的表面张力低于第二道罩光清漆的情况下,那么两层涂层间的附着力不佳,所以塑胶底漆在生产过程中的表面张力不应太低,能与底材咬合最佳为止,并使面漆对底漆的润湿性良好,两层涂膜要有一定厚度的界面层才能有稳定的附着力。
2.6 针孔现象针孔是指涂膜表面被针尖刺过似的小孔,类似皮革毛孔,孔径大约0.1mm 。
喷涂罩光清漆时针孔现象尤为突出:(1) 清漆精致不良,内部存在杂质。
(2) 涂料挥发过快,且用量较多,加入挥发性慢的强溶剂如CAC 、环己酮等可减少针孔现象。
(3) 涂料表面张力过大,粘度高,流动性差,气泡释放困难,加入适量流平剂以降低涂料表面张力减少针孔现象。
(4) 被涂覆塑料件未冷却,闪干时间过短,使湿膜中溶剂急剧蒸出。
(5) 涂膜喷涂太厚且表干过快。
(6) 作业环境太高,或喷涂时有水分带入涂料中。
(7) 闪干不充分,烘烤升温过快,故成膜后自然静置一段时间再进入带有温度梯度的烘道进行烘烤。
(8) 涂料长时间搅拌,形成无数细微空气泡。
(9) 颜料分散不良。
2.7 气泡和气孔问题气孔是涂膜干燥过程中滞留于涂膜的气泡强行突破涂膜逸出时留下的泡孔。
未破而使涂层隆起的称为气泡。
气泡可以是涂料搅拌时形成的空气泡,或者是干燥时溶剂急剧挥发形成的溶剂气泡,在涂料的制作过程中许多种助剂可以用来破裂气泡。
大多数应用气泡表面上表面张力差驱动的流动行为。
假使气泡表面上有一小点的表面张力低下来,则这小点上的液体就流向邻近较高表面张力处,试图将它覆盖住。
气泡壁本来是薄的,物质外流,则壁更薄更弱,所以这小点就会破裂, 例如,聚二甲基硅氧烷可有效地破裂多种泡沫,因为它们的表面张力比几乎任何气泡的表面张力低。
2.8 发花现象发花是色漆表面色调不一致,出现斑点和条纹等产生颜色杂乱的外观缺陷。
涂料中至少含有两种颜料发花现象才会明显。
在涂膜干燥过程中,由于表面张力差驱动的对流所造成的颜料分离效应。
在干燥过程中对流是由于溶剂从湿膜中快速逸出造成明显的湍动,涂料从湿膜底处流上来,然后又流下去。
在流下去之前,溶剂挥发,浓度增大,温度降低,表面张力增大,这样形成的表面张力差驱动对流继续进行,这流动图像近似圆形,当它们扩展时遇到相临的流动图像就压缩了。
如果是十分规则,那么形成的是六角形的贝纳德漩涡。
随着溶剂继续挥发,黏度增高,带着颜料颗粒一起流动变的困难了。
颗粒最小的,密度最低的流动保持的长些; 颗粒最大的,密度最高的反之,这些颜料的分离产生了发花。
2.9 浮色现象浮色是指表面颜色一致的,但与应有的不一样。
使涂膜表面与内部的色调不一致。
例如一个均一的灰漆,但比应有的深些。
浮色最困扰的是随施工条件的不同而程度不一,使同一材料用同一涂料而有不同的颜色。
浮色是由于一种或多种颜料在表面上富集而造成的。
是由于颜料的密度和大小不同,或颜料絮凝了,从而在湿膜中沉降速度不同而导致分层。
湿膜厚、基料黏度低和溶剂挥发速度慢,任何一条都会使湿膜在低黏度保持更久,而使颜料沉降更多的更加使浮色加剧。
纠正方法是避免絮凝忽然低密度细颜料, 用挥发更快的溶剂和黏度更高的基料。
湿涂膜干燥时溶剂不均及匀蒸发使表面产生表面张力差而引起对流现象,这是产生浮色的驱动力。
2.10 露底现象原因与措施:(1) 选用涂料遮盖力差。
色漆颜料份低,铝粉漆铝粉的含量低是导致露底的原因。
(2) 涂料使用前,沉降的颜料未被搅起或搅拌不充分,造成遮盖力下降。
(3) 涂料稀释过程中未按照施工工艺说明进行兑稀,兑的太稀或喷涂的湿膜太薄。
(4) 喷涂膜厚不均匀,未按照正常喷涂手法进行喷涂。
(5) 底面漆色调反差太大,对于金属闪光漆,由于底色漆喷涂很薄,中涂颜色最好与面漆相近。
2.11 发白现象涂膜干后返白失光或产生无光斑点的现象称为发白。
主要是由于施工环境湿度太大(相对湿度>80% )和溶剂挥发太快而使涂膜表面温度急剧下降,致使水汽凝集在涂膜上,从而使树脂或纤维素酯沉淀出来造成发白现象,一般快干挥发型涂料(热塑性丙烯酸等)中,由于含有大量低沸点溶剂和稀释剂,所以容易产生发白现象。
若加入防潮剂和适量高沸点慢挥发强溶剂以调整溶剂配方,或改善施工环境,除去压缩空气中的水分,定期排放空气压缩机和油水分离机的油水等均可防止发白现象。
被涂覆物表面温度太低,将塑料工件加热到高于环境温度10 ℃也可以减弱发白现象。
2.12 铝粉漆色调不均匀铝粉闪光漆是具有奇特装饰效果的高装饰性涂料,对施工工艺要求非常高,施工不当容易出现色调不均匀、闪光效果差等缺陷。
其原因主要为:(1)金属闪光涂料中铝粉含量太低,遮盖力较差,涂料的定膜能力差; 涂膜的表干时间太长。
可在铝粉涂料中加入铝粉定位剂或醋酸纤维素酯解决铝粉在涂膜中的定位问题。
(2) 底色漆喷的太薄或者漏喷、现露底色。
(3) 底色喷的太厚,且涂膜薄厚不均匀。
(4) “湿碰湿”工艺的间隔时间太短,应待底漆喷涂后静置些时间再喷涂面漆。
(5) 喷涂时空气压力太低,涂料雾化不良或空气压力太高,使片状铝粉变形。
而且喷涂时操作人员走枪方式不对或喷涂不均匀也会造成此问题。
闪光铝粉漆应该采用较低施工固体分和施工黏度喷涂,使用专用喷枪均匀喷薄,以约8 μ m 干膜厚度喷涂二道,并经充分闪干后再喷涂清漆。
2.13 附着力问题(剥落现象)这是由于涂膜附着力或层间结合力很差,造成局部甚至是全部涂膜剥落的现象。
造成剥落的原因为:(1) 喷涂前底材处理不当,表面残留油污、水或脱膜剂,或有色金属未进行适宜的表面处理。
(2) 底材表面太光滑。
(3) 底涂层放置太久,重涂间隔周期太长或涂层烘烤过度,影响自身附着力和层间结合力。
(4) 旧涂膜表面未打磨直接再涂漆。
(5) 底、面涂料不配套,造成层间结合力差。
(6) 底漆涂层含有硅油类助剂、表面张力过于低,影响重涂涂膜的浸湿结合。
2.19 起痱子现象当喷涂产品经过烘烤,表面呈有密密麻麻痱子现象(特别在阳光下目视,较为明显)。