模具设计常识-2
模具设计知识点总结
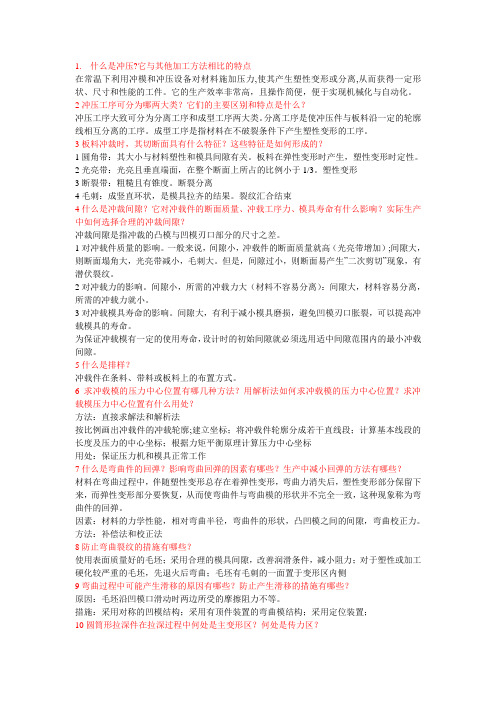
1.什么是冲压?它与其他加工方法相比的特点在常温下利用冲模和冲压设备对材料施加压力,使其产生塑性变形或分离,从而获得一定形状、尺寸和性能的工件。
它的生产效率非常高,且操作简便,便于实现机械化与自动化。
2冲压工序可分为哪两大类?它们的主要区别和特点是什么?冲压工序大致可分为分离工序和成型工序两大类。
分离工序是使冲压件与板料沿一定的轮廓线相互分离的工序。
成型工序是指材料在不破裂条件下产生塑性变形的工序。
3板料冲裁时,其切断面具有什么特征?这些特征是如何形成的?1圆角带:其大小与材料塑性和模具间隙有关。
板料在弹性变形时产生,塑性变形时定性。
2光亮带:光亮且垂直端面,在整个断面上所占的比例小于1/3。
塑性变形3断裂带:粗糙且有锥度。
断裂分离4毛刺:成竖直环状,是模具拉齐的结果。
裂纹汇合结束4什么是冲裁间隙?它对冲载件的断面质量、冲载工序力、模具寿命有什么影响?实际生产中如何选择合理的冲裁间隙?冲裁间隙是指冲裁的凸模与凹模刃口部分的尺寸之差。
1对冲载件质量的影响。
一般来说,间隙小,冲载件的断面质量就高(光亮带增加);间隙大,则断面塌角大,光亮带减小,毛刺大。
但是,间隙过小,则断面易产生”二次剪切”现象,有潜伏裂纹。
2对冲载力的影响。
间隙小,所需的冲载力大(材料不容易分离):间隙大,材料容易分离,所需的冲载力就小。
3对冲载模具寿命的影响。
间隙大,有利于减小模具磨损,避免凹模刃口胀裂,可以提高冲载模具的寿命。
为保证冲载模有一定的使用寿命,设计时的初始间隙就必须选用适中间隙范围内的最小冲载间隙。
5什么是排样?冲载件在条料、带料或板料上的布置方式。
6求冲载模的压力中心位置有哪几种方法?用解析法如何求冲载模的压力中心位置?求冲载模压力中心位置有什么用处?方法:直接求解法和解析法按比例画出冲载件的冲载轮廓;建立坐标;将冲载件轮廓分成若干直线段;计算基本线段的长度及压力的中心坐标;根据力矩平衡原理计算压力中心坐标用处:保证压力机和模具正常工作7什么是弯曲件的回弹?影响弯曲回弹的因素有哪些?生产中减小回弹的方法有哪些?材料在弯曲过程中,伴随塑性变形总存在着弹性变形,弯曲力消失后,塑性变形部分保留下来,而弹性变形部分要恢复,从而使弯曲件与弯曲模的形状并不完全一致,这种现象称为弯曲件的回弹。
模具常识

模具常识产品设计常识[转]1.胶厚(胶位):塑胶产品的胶厚(整体外壳)通常在0.80-3.00左右,太厚容易缩水和产生汽泡,太薄难走满胶,大型的产品胶厚取厚一点,小的产品取薄一点,一般产品取1.0-2.0为多。
而且胶位要尽可能的均匀,在不得已的情况下,局部地方可适当的厚一点或薄一点,但需渐变不可突变,要以不缩水和能走满胶为原则,一般塑料胶厚小于0.3时就很难走胶,但软胶类和橡胶在0.2-0.3的胶厚时也能走满胶。
2.加强筋(骨位):塑胶产品大部分都有加强筋,因加强筋在不增加产品整体胶厚的情况下可以大大增加其整体强度,对大型和受力的产品尤其有用,同时还能防止产品变形。
加强筋的厚度通常取整体胶厚的0.5-0.7倍,如大于0.7倍则容易缩水。
加强筋的高度较大时则要做0.5-1的斜度(因其出模阻力大),高度较矮时可不做斜度。
3.脱模斜度:塑料产品都要做脱模斜度,但高度较浅的(如一块平板)和有特殊要求的除外(但当侧壁较大而又没出模斜度时需做行位)。
出模斜度通常为1-5度,常取2度左右,具体要根据产品大小、高度、形状而定,以能顺利脱模和不影响使用功能为原则。
产品的前模斜度通常要比后模的斜度大0.5度为宜,以便产品开模事时能留在后模。
通常枕位、插穿、碰穿等地方均需做斜度,其上下断差(即大端尺寸与小端尺寸之差)单边要大于0.1以上。
4.圆角(R角):塑胶产品除特殊要求指定要锐边的地方外,在棱边处通常都要做圆角,以便减小应力集中、利于塑胶的流动和容易脱模。
最小R通常大于0.3,因太小的R模具上很难做到。
5.孔:从利于模具加工方面的角度考虑,孔最好做成形状规则简单的圆孔,尽可能不要做成复杂的异型孔,孔径不宜太小,孔深与孔径比不宜太大,因细而长的模具型心容易断、变形。
孔与产品外边缘的距离最好要大于1.5倍孔径,孔与孔之间的距离最好要大于2倍的孔径,以便产品有必要的强度。
与模具开模方向平行的孔在模具上通常上是用型心(可镶、可延伸留)或碰穿、插穿成型,与模具开模方向不平行的孔通常要做行位或斜顶,在不影响产品使用和装配的前提下,产品侧壁的孔在可能的情况下也应尽量做成能用碰穿、插穿成型的孔。
模具设计基础知识
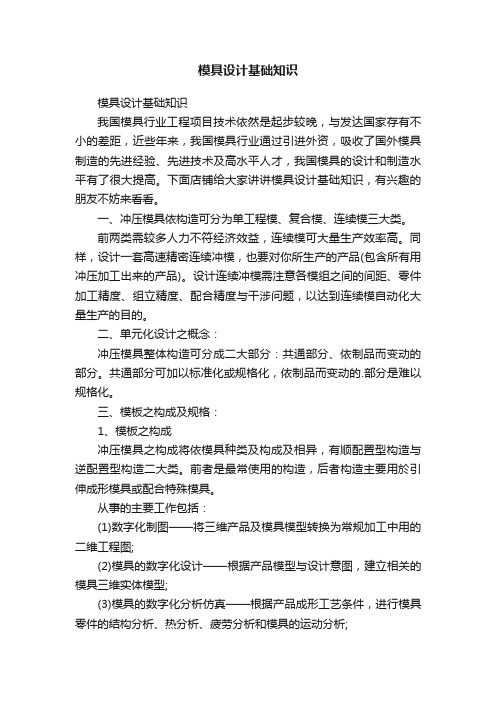
模具设计基础知识模具设计基础知识我国模具行业工程项目技术依然是起步较晚,与发达国家存有不小的差距,近些年来,我国模具行业通过引进外资,吸收了国外模具制造的先进经验、先进技术及高水平人才,我国模具的设计和制造水平有了很大提高。
下面店铺给大家讲讲模具设计基础知识,有兴趣的朋友不妨来看看。
一、冲压模具依构造可分为单工程模、复合模、连续模三大类。
前两类需较多人力不符经济效益,连续模可大量生产效率高。
同样,设计一套高速精密连续冲模,也要对你所生产的产品(包含所有用冲压加工出来的产品)。
设计连续冲模需注意各模组之间的间距、零件加工精度、组立精度、配合精度与干涉问题,以达到连续模自动化大量生产的目的。
二、单元化设计之概念:冲压模具整体构造可分成二大部分:共通部分、依制品而变动的部分。
共通部分可加以标准化或规格化,依制品而变动的.部分是难以规格化。
三、模板之构成及规格:1、模板之构成冲压模具之构成将依模具种类及构成及相异,有顺配置型构造与逆配置型构造二大类。
前者是最常使用的构造,后者构造主要用於引伸成形模具或配合特殊模具。
从事的主要工作包括:(1)数字化制图——将三维产品及模具模型转换为常规加工中用的二维工程图;(2)模具的数字化设计——根据产品模型与设计意图,建立相关的模具三维实体模型;(3)模具的数字化分析仿真——根据产品成形工艺条件,进行模具零件的结构分析、热分析、疲劳分析和模具的运动分析;(4)产品成形过程模拟——注塑成形、冲压成形;(5)定制适合本公司模具设计标准件及标准设计过程;(6)模具生产管理。
2、模具之规格(1)模具尺寸与锁紧螺丝模板之尺寸应大於工作区域,并选择标准模板尺寸。
模板锁紧螺丝之位置配置与模具种类及模板尺寸有关。
其中单工程模具最常使用锁紧螺丝配置於四边角,最标准形式工作区域可广大使用。
长形之模具及连续模具最常使用锁紧螺丝配置於四边角及中间位置。
(2)模板之厚度模板之厚度选择与模具之构造、冲压加工种类、冲压加工加工力、冲压加工精度等有绝对关系。
模具设计基础知识(新手必看)
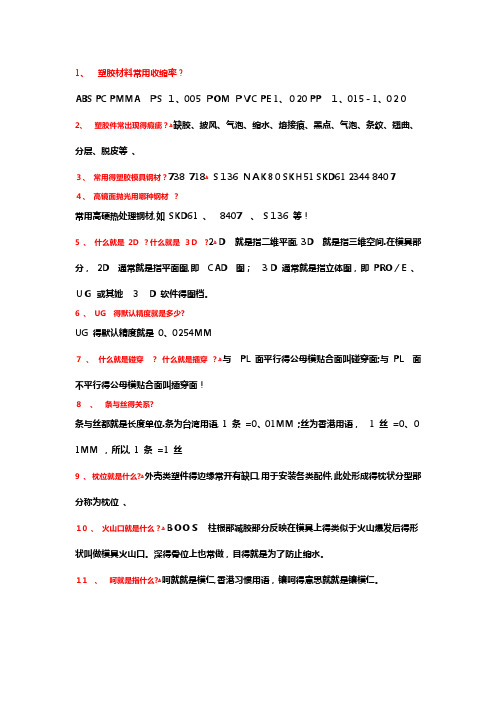
1、 塑胶材料常用收缩率?ABS PC PMMA PS 1、005 PO M PVC PE 1、020 PP 1、015-1、0202、 塑胶件常出现得瘕疵?ﻫ缺胶、披风、气泡、缩水、熔接痕、黑点、气泡、条纹、翘曲、分层、脱皮等 、3、 常用得塑胶模具钢材?ﻫ718 738 S 136 NAK 80 SK H51 SKD61 2344 8407 4、 高镜面抛光用哪种钢材 ?常用高硬热处理钢材,如 SKD61 、 8407 、 S 136 等!5 、 什么就是 2D ?什么就是 3D ?ﻫ2D 就是指二维平面, 3D 就是指三维空间.在模具部分, 2D 通常就是指平面图,即 CAD 图; 3 D 通常就是指立体图,即 PRO /E 、 UG 或其她 3 D 软件得图档。
6 、 UG 得默认精度就是多少?UG 得默认精度就是 0、0254M M7 、 什么就是碰穿 ? 什么就是插穿 ?ﻫ与 PL 面平行得公母模贴合面叫碰穿面;与 PL 面不平行得公母模贴合面叫插穿面!8 、 条与丝得关系?条与丝都就是长度单位.条为台湾用语, 1 条 =0、01M M ;丝为香港用语, 1 丝 =0、01MM ,所以, 1 条 =1 丝9 、 枕位就是什么?ﻫ外壳类塑件得边缘常开有缺口,用于安装各类配件,此处形成得枕状分型部分称为枕位 、10 、 火山口就是什么?ﻫBO OS 柱根部减胶部分反映在模具上得类似于火山爆发后得形状叫做模具火山口。
深得骨位上也常做,目得就是为了防止缩水。
11 、 呵就是指什么?ﻫ呵就就是模仁,香港习惯用语,镶呵得意思就就是镶模仁。
12 、什么就是虎口?虎口,又称管位,即用来限位得部分。
常用在模仁得四个角上,起前后模仁一个精定位得作用,常用CNC 或模床加工。
13 、什么叫排位?模具上得产品布局称为排位。
往往由进胶式样与模具结构及产品本身来决定得。
14、什么叫胶位?模具上产品得空穴称为胶位。
模具设计需要掌握知识

模具设计需要掌握知识引导语:模具设计是指从事企业模具的数字化设计,包括型腔模与冷冲模,在传统模具设计的基础上,充分应用数字化设计工具,提高模具设计质量,缩短模具设计周期的人员。
下面店铺为大家讲讲模具设计需要掌握知识有哪些。
一、模具设计需要掌握知识如下:1、压注模设计知识点:①压注模的结构及分类:掌握压注模的类型、压注模的结构、压注模的特点;②压注模与压力机的关系:掌握普通液压机上的压注模、专用液压机上的压注模;③压注模结构设计:掌握压注模零部件设计、压注模浇注系统与排溢系统设计。
2、压注模设计看图或作图技能:①根据压注模装配图,能分析模具结构组成。
②根据压注模装配图,能分析模具在压力机上的方位及与压力机的关系。
③根据压注模装配图,能分析模具结构特点。
④根据压注模装配图,能分析模具各零件的名称、作用。
3、挤出模设计知识点:①挤出模的分类及结构组成:掌握挤出成型机头的分类、挤出模的结构组成;②挤出模设计要点:掌握挤出成型机头的作用、挤出成型机头设计原则、挤出成型机头与挤出机的关系;③管材挤出模:掌握管材挤出成型机头的结构、管材挤出机头的零件设计、管材的定径和冷却;④异型材挤出模:掌握异型材分类及异型材挤出成型机头的结构形式、异型材挤出成型机头的设计要点、异型材的定型模;⑤挤出模设计实例:了解挤出模设计要求、设计步骤。
4、挤出模设计看图或作图技能:①根据挤出模装配图,能分析模具结构组成;② 根据挤出模装配图,能分析模具在挤出机上的方位及与挤出机的关系;③ 根据挤出模装配图,能分析模具结构特点;④ 根据挤出模装配图,能分析模具各零件的名称、作用。
二、设计步骤:1、对所设计模具之产品进行可行性分析,以电脑机箱为例,首先将各组件产品图纸利用设计软件进行组立分析,即我们工作中所说的套图,确保在模具设计之前各产品图纸的正确性,另一方面可以熟悉各组件在整个机箱中的重要性,以确定重点尺寸,这样在模具设计中很有好处的,具体的套图方法这里就不做详细的介绍了。
模具设计知识总结(2)
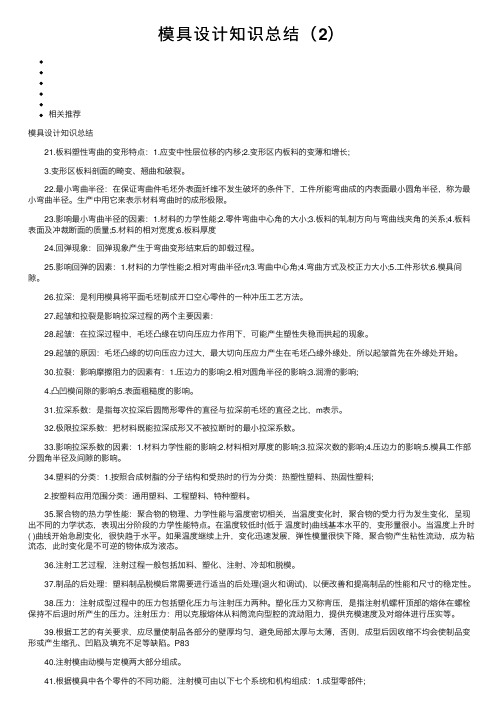
模具设计知识总结(2)相关推荐模具设计知识总结 21.板料塑性弯曲的变形特点:1.应变中性层位移的内移;2.变形区内板料的变薄和增长; 3.变形区板料剖⾯的畸变、翘曲和破裂。
22.最⼩弯曲半径:在保证弯曲件⽑坯外表⾯纤维不发⽣破坏的条件下,⼯件所能弯曲成的内表⾯最⼩圆⾓半径,称为最⼩弯曲半径。
⽣产中⽤它来表⽰材料弯曲时的成形极限。
23.影响最⼩弯曲半径的因素:1.材料的⼒学性能;2.零件弯曲中⼼⾓的⼤⼩;3.板料的轧制⽅向与弯曲线夹⾓的关系;4.板料表⾯及冲裁断⾯的质量;5.材料的相对宽度;6.板料厚度 24.回弹现象:回弹现象产⽣于弯曲变形结束后的卸载过程。
25.影响回弹的因素:1.材料的⼒学性能;2.相对弯曲半径r/t;3.弯曲中⼼⾓;4.弯曲⽅式及校正⼒⼤⼩;5.⼯件形状;6.模具间隙。
26.拉深:是利⽤模具将平⾯⽑坯制成开⼝空⼼零件的⼀种冲压⼯艺⽅法。
27.起皱和拉裂是影响拉深过程的两个主要因素: 28.起皱:在拉深过程中,⽑坯凸缘在切向压应⼒作⽤下,可能产⽣塑性失稳⽽拱起的现象。
29.起皱的原因:⽑坯凸缘的切向压应⼒过⼤,最⼤切向压应⼒产⽣在⽑坯凸缘外缘处,所以起皱⾸先在外缘处开始。
30.拉裂:影响摩擦阻⼒的因素有:1.压边⼒的影响;2.相对圆⾓半径的影响;3.润滑的影响;4.凸凹模间隙的影响;5.表⾯粗糙度的影响。
31.拉深系数:是指每次拉深后圆筒形零件的直径与拉深前⽑坯的直径之⽐,m表⽰。
32.极限拉深系数:把材料既能拉深成形⼜不被拉断时的最⼩拉深系数。
33.影响拉深系数的因素:1.材料⼒学性能的影响;2.材料相对厚度的影响;3.拉深次数的影响;4.压边⼒的影响;5.模具⼯作部分圆⾓半径及间隙的影响。
34.塑料的分类:1.按照合成树脂的分⼦结构和受热时的⾏为分类:热塑性塑料、热固性塑料; 2.按塑料应⽤范围分类:通⽤塑料、⼯程塑料、特种塑料。
35.聚合物的热⼒学性能:聚合物的物理、⼒学性能与温度密切相关,当温度变化时,聚合物的受⼒⾏为发⽣变化,呈现出不同的⼒学状态,表现出分阶段的⼒学性能特点。
模具设计基础知识
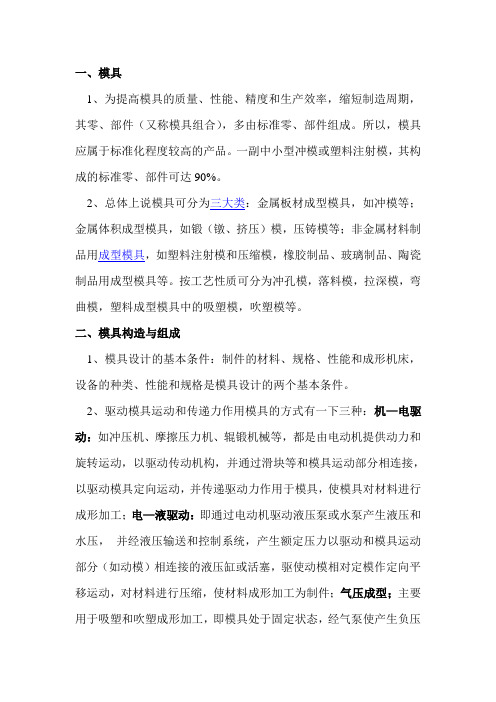
一、模具1、为提高模具的质量、性能、精度和生产效率,缩短制造周期,其零、部件(又称模具组合),多由标准零、部件组成。
所以,模具应属于标准化程度较高的产品。
一副中小型冲模或塑料注射模,其构成的标准零、部件可达90%。
2、总体上说模具可分为三大类:金属板材成型模具,如冲模等;金属体积成型模具,如锻(镦、挤压)模,压铸模等;非金属材料制品用成型模具,如塑料注射模和压缩模,橡胶制品、玻璃制品、陶瓷制品用成型模具等。
按工艺性质可分为冲孔模,落料模,拉深模,弯曲模,塑料成型模具中的吸塑模,吹塑模等。
二、模具构造与组成1、模具设计的基本条件:制件的材料、规格、性能和成形机床,设备的种类、性能和规格是模具设计的两个基本条件。
2、驱动模具运动和传递力作用模具的方式有一下三种:机—电驱动:如冲压机、摩擦压力机、辊锻机械等,都是由电动机提供动力和旋转运动,以驱动传动机构,并通过滑块等和模具运动部分相连接,以驱动模具定向运动,并传递驱动力作用于模具,使模具对材料进行成形加工;电—液驱动:即通过电动机驱动液压泵或水泵产生液压和水压,并经液压输送和控制系统,产生额定压力以驱动和模具运动部分(如动模)相连接的液压缸或活塞,驱使动模相对定模作定向平移运动,对材料进行压缩,使材料成形加工为制件;气压成型;主要用于吸塑和吹塑成形加工,即模具处于固定状态,经气泵使产生负压将塑料板材吸贴于模具型面,形成制件,吹塑则是经气泵产生气压,吹人热熔态塑件或热熔态玻璃制件毛坯空腔,使其扩展、变形,并贴附在模具型腔表面上,形成制件。
3、模具设计:过定位导向,保证模具运动精度,是模具结构设计的一个重要原则和要素。
额定力(公称力):驱动模具运动的基本条件,为作用于模具运动部分上的驱动力。
这些驱动力是制件成形加工的主要成形条件,是模具结构设计的主要依据。
4、模具型面:模具型面主要指模具构成中的工作零件(凸模、凹模)上,与制件形体相吻合、相似或相同的型面。
模具设计基础知识概括

微观不平度十点高度的数值由以下算式获得。
式中,第i个最大的轮廓高, 为第i个最大的轮廓谷深。
表面粗糙度既要满足零件的功能要求,又要考虑工艺经济 性。因此,在满足零件表面功能要求的前提下,尽量选用 数值大的粗糙度。
表面粗糙度符号、代号一般注在可见轮廓线、尺寸界线、引 出线或它们的延长线上。符号的尖端必须从材料外指向表面 表面粗糙度代号中数定及符号的方向必须按图2-16a)、图216b)标注,带有横线的表面粗糙度符号应按图2-16c)标注。
在同一图样上,每一表 面一般只标注一次符号、 代号,并尽可能靠近有 关的尺寸线,见图2-16a)。 当地位狭小或不便标注 时,符号代号可以引出 标注,如图2-16d)。
冲模零件表面粗糙度的选定
压铸模零件的表面粗糙度选定
拔模斜度如图2-17所示,有增加铸件壁厚、增减铸件壁厚 和减少铸件壁厚三种形式。未注拔模斜度大小根据模样的 拔模高度、材料类型、斜度位置等有关。
在同一模具上成型两种大小不同的塑胶制品,为了保证 在注塑时,塑胶能同时充满模具上大小不同的型腔,这 时单使用修正浇口大小,不一定能达到充填平衡效果, 必须对分流道进行修正才能达到预期效果。
在设计浇注系统时,首先是选择浇口的位置,浇口位置选 择的适当与否,将直接关系到制品的成型质量及注射过程 是否能顺利进行。
浇口位置的选择应遵循以下原则。 1)设计浇注系统时,流道应尽量减少弯折。
- 1、下载文档前请自行甄别文档内容的完整性,平台不提供额外的编辑、内容补充、找答案等附加服务。
- 2、"仅部分预览"的文档,不可在线预览部分如存在完整性等问题,可反馈申请退款(可完整预览的文档不适用该条件!)。
- 3、如文档侵犯您的权益,请联系客服反馈,我们会尽快为您处理(人工客服工作时间:9:00-18:30)。
§8-4 注塑模具结构设计常识
5.冷却系统
⑵冷却水道设计实例
密封圈规格 ØD 13.0 16.0 19.0 2.5 Ød ØD1 8.0 11.0 14.0
密封槽尺寸要求 H W
1.8
3.2
16.0
19.0 25.0 3.5
9.0
12.0 18.0 2.7 4.7
减少温差
§8-4 注塑模具结构设计常识
①主流道---由浇口套(唧嘴)组成, 一般分二板模唧嘴和三板模唧嘴。
§8-4 注塑模具结构设计常识
3.浇注系统
⑵常用流道结构:
②分流道---常用的截面形式有圆形和梯形。 圆形截面D一般在φ3~8之间选取,超过 φ8对改善流动情况影响很小。 梯形截面d一般在4~10之间选取。 一般来说为减少分流道压力损失 和保压要求: a. 在流道分支时,截面面积要 适当减小,否则不应有很大 的突变; b. 流道中的最小横断面面积大于 浇口处的最小截面面积。 c. 三板模的分流道结构和尺寸 特别要注意上面两点。
2.成型零件
⑴成型零件构成 通常由前后模仁(肉)、镶件(针) 、滑块(行 位) 、斜顶等构成,在工作中说的 “分模” 就是设计这些零件。源自§8-4 注塑模具结构设计常识
2.成型零件
⑵ 胶件排位 按胶件分有:一模出一种多件和一模出多种胶件两种类型; 按浇道分有:平衡式、非平衡式、两种混合式三种类型。 排位原则
§8-4 注塑模具结构设计常识
2.成型零件
⑷分模面与自锁
分模面常见问题及解决
§8-4 注塑模具结构设计常识
2.成型零件
⑷分模面与自锁
分模面常见问题及解决
§8-4 注塑模具结构设计常识
2.成型零件
⑸行位和斜顶
常见行位和斜顶结构及问题解决
§8-4 注塑模具结构设计常识
2.成型零件
⑸行位和斜顶
常见行位和斜顶结构及问题解决
注:模仁尺寸也要与模架尺寸匹配,必要时需进行 强度校核,深型腔还需进行刚度校核。大型模 具需根据成本校核来决定是否设计镶嵌式模仁。
§8-4 注塑模具结构设计常识
2.成型零件
⑶模仁的强度
②模仁强度校核: ●充填时所需最小锁模力Fmin: Fmin = S1x p (T)
式中:S1----胶件+流道投影面积 in² p-----塑胶材料充模压力系数 T/ in² ,
回针接触前模板或 低于0.1mm
顶针和扁顶针
§8-4 注塑模具结构设计常识
6.顶出系统
斜面上加R槽
配合段长10-15mm 间隙单边0.02mm
端面齐平
顶针装配尺寸
与避免前模碰面
顶针固定方式
垫块
e≤0.1
顶针高出
小司筒针 固定方式
大司筒针 固定方式
§8-4 注塑模具结构设计常识
6.顶出系统
型芯 推板 边钉 推板 回针
推板与型芯的配合
复位杆 挡销 摆块 压块
推板顶出
导向块 闭模状态 开模状态
先复位机构
§8-4 注塑模具结构设计常识
7.模架选用
⑴根据模仁的长L和宽W,按经验数值选取模架的长和宽尺寸。
§8-4 注塑模具结构设计常识
7.模架选用
⑴根据模仁的长L和宽W,按经验数值选取模架的长和宽尺寸。
大水口模架选用表
Fmax = S2 x [] (T)
式中: S2----模仁承压面面积 in² ,[] =3.5T/ in² ,钢材许用应力 T/ in² ,
●选择注塑机: a) 必要条件: Fmin/0.8< F注塑机 <0.75 Fmax b) F注塑机----注塑机额定锁模力,在满足必要条件下按机型靠近并尽量取小 值。 ●强度校核:模肉实际承受的最大应力 = F 注塑机 / S2 满足 1.5≤≤3.5 则安全合理, 否则修正S2。
§8-4 注塑模具结构设计常识
2.成型零件
⑸行位和斜顶
常见行位和斜顶结构及问题解决
§8-4 注塑模具结构设计常识
2.成型零件
⑸行位和斜顶
常见行位和斜顶结构及问题解决
§8-4 注塑模具结构设计常识
2.成型零件
⑸行位和斜顶
常见行位和斜顶结构及问题解决
§8-4 注塑模具结构设计常识
3.浇注系统
⑴浇注系统(流道)组成:一般冷流道包括主流道、分流道、冷料井和浇口组成。 ⑵常用流道结构:
§8-4 注塑模具结构设计常识
7.模架选用
⑴根据模仁的长L和 宽W,按经验数值 选取模架的长和宽 尺寸。
细水口模架选用表
§8-4 注塑模具结构设计常识
7.模架选用
⑵根据模仁镶进模架的深度h,按经验数公式选取模架的厚度尺寸H。
§8-4 注塑模具结构设计常识
2.成型零件
⑷分模面与自锁
分模面选择原则 ①胶件外观质量:分模线应尽可能不影响外观,而且分模面处所产生的披峰应 易于加工。胶件上披峰方向不影响使用。 ②留模方式:为便于胶件脱模,应使胶件在开模时留在后模,应保证胶件不粘 定模,碰穿孔尽量碰前模,易于脱模。 ③模具加工:分模面应使模具分割成便于加工的部件,以减少机械加工的困难。 ④胶件同轴度要求:应使有同轴度要求的部分全部留在模具同一侧(最好后 模)内成型,防止合模时前后模错位。 ⑤排气的影响:分模面的选择应有利于排气,一般分模面应与熔体流动的末端 重合;能合理安排浇注系统,特别是浇口位置。 ⑥模具的分模面一般取前模模肉的最高位,这样可以节省模肉的材料; ⑦分模面选择应尽量避免形成侧孔、侧凹,若需要行位成形,力求行位结构简 单,尽量避免前模行位.。 ⑧满足模具的锁紧要求,将胶件投影面积大的方向,放在前、后模的合模方向 上。另外,分模面是斜面或曲面时,应加斜面锁紧块。
第八章
模具设计常识
§8-4 注塑模具结构设计常识
1.注塑模的基本结构 ⑴根据其运动的特点可分为:前模部分和后模部分; ⑵根据组成的结构可分为:成型零件、浇注系统 、排气系统、冷却系统、顶
出系统、模架(胚)、辅助机构等。
§8-4 注塑模具结构设计常识
1.注塑模的基本结构
§8-4 注塑模具结构设计常识
a. 首先应考虑胶件的用量及尺寸大小和精度要求,确定一模是否出多件; b. 优先采用中心对称或轴对称的平衡式布置,当必须采用非平衡式时,应考虑模具 的压力平衡,流动平衡性(考虑流动性及胶件尺寸精度); c.便于模具的加工,如:共同枕位;共同镶件等(从模具成本考虑); d.考虑胶件入水的要求,避免胶件变形等; e.考虑胶料的流动比,保证能充满模腔; f. 一模出多种胶件时,要考虑材料和颜色要一致,产量需求不太大,各胶件尺寸 大小不能相差太悬殊(一般体积不超过2:1)。 g. 模仁满足封胶 要求和强度要求,满足行位、斜顶、冷却水和螺丝等空间要 求。模具整体长宽比要协调,同时也要考虑注塑机的安装要求。
3.浇注系统
⑵常用流道结构:
④浇口实例
浇口与胶料的关系
ABS/HIPS/PA:充填特性好,流动性较好,适 合各种浇口;镜片类最好用护耳浇口。 POM/PE/PP: 剪敏性塑料,熔料温度窄,收 缩率大,可采用侧浇口或潜伏点浇口,入水直 径大于1.0mm,不宜采用直接浇口和弧形浇口。 PC/PMMA:流动性不好,冷却快,浇注系统 以短而粗为原则,浇口取大些,适合侧浇口, 扇形浇口。 PVC/TPU: 熔料温度窄,易烧料且流动性较 差,宜采用侧浇口,不宜太小,不适合搭底。
§8-4 注塑模具结构设计常识
3.浇注系统
⑵常用流道结构:
③冷料井---冷料井是为除去因喷嘴与低温模具接触而在料流前锋产生的冷料进入 型腔而设置。它一般设置在主流道的末端和分流道的末端。其长度为(1 ~ 1.5)倍 的流道直径。
§8-4 注塑模具结构设计常识
3.浇注系统
⑵常用流道结构:
④浇口
§8-4 注塑模具结构设计常识
排气槽深度h(mm) 0.03~0.04 0.02 0.05~0.07 0.04 0.03~0.04 0.02 0.04
§8-4 注塑模具结构设计常识
4.排气系统
⑵常用的排气设计方法
§8-4 注塑模具结构设计常识
5.冷却系统
⑴冷却水道设计要求
①冷却水道的孔壁至型腔表面的距离应尽可能相等,一般取8~20mm;冷却水道数 量尽可能多,而且要便于加工。一般水道直径选用6.0,8.0,10.0,两平行 水道间距取40~60mm。 ②所有成型零部件均要求通冷却水道,除非无位置。热量聚集的部位强化冷却,如 电池兜、喇叭位、厚胶位、浇口处等。A板、B板、水口板、浇口套部分则视情况 决定。 ③降低入水口与出水口的温差。入水,出水温差会影响模具冷却的均匀性,故设计 时应标明入水,出水方向,模具制作时要求在模坯上标明。运水流程不应过长, 防止造成出入水温差过大。 ④尽量减少冷却水道中“死水”(不参与流动的介质)的存在。冷却水道应避免设在可 预 见的胶件熔接痕(夹水纹)处。 ⑤保证水孔周边的最小钢位厚度,要求当水道长度小于150mm时,钢位厚大于 3mm;当水道长度大于150mm时,钢位厚大于5mm。 ⑥冷却水道连接时要由“O”型胶密封,密封应可靠无漏水。 ⑦对冷却水道布置有困难的部位应采取其它冷却方式,如铍铜、热管等。 ⑧合理确定冷却水进出接头位置,避免影响模具安装、固定。
§8-4 注塑模具结构设计常识
2.成型零件
⑵ 胶件排位
多种混合式 平衡式 混合式
非平衡式(不好) 平衡式(好)
§8-4 注塑模具结构设计常识
2.成型零件
⑶模仁的强度
①模仁尺寸的经验值 ●浅型腔(一般h/l<0.2且 h<50mm),模仁四边枕 位m一般取 : m=20~40mm (投影面积大取大值) ●深型腔(一般h/l>0.2, 且h>50mm),模仁四边 枕位m一般取: m=h (圆形模仁可取小些)
塑胶材料充模压力系数值: 塑胶材料 p T/in² 塑胶材料 ABS 2.0 ~ 3.0(2.0) PP HIPS 1.0 ~ 2.0(1.7) PC PMMA 2.0 ~ 4.0(3.0) PA6(PA66) SAN 2.5 ~ 3.0(2.5) PA11(PA12) POM 3.0 ~ 5.0(4.0) PVC GPPS 3.0 ~ 4.0(3.0) PE