车架的改造与副车架的设计
车架的改造与副车架的设计

车架的改装主车架是汽车底盘上各总成及专用工作装置安装的基础,改装时受到的影响最大,因此,要特别引起注意。
主车架是受载荷很大的部件,除承受整车静载荷外,还要受到车辆行驶时的动载荷,为了保持主车架的强度和刚度,原则上不允许在主车架纵梁上钻孔和焊接,应尽量使用车架上原有的孔。
如果安装专用设备或其它附件,不得不在车架上钻孔或焊接时.应避免在高应力区钻孔或焊接。
主车架纵梁的高应力区在轴距之间纵梁的下冀面和后悬的上冀面处。
因为这些部位纵梁应力较大,钻孔容易产生应力集中。
对于主车架纵梁高应力区以外的其余地方需要钻孔或焊接时,应注意以下事项:1)尽量减小孔径,增加孔间距离,对钻孔的位置和孔径规范,应满足图和表的要求。
主车架钻孔的孔径和孔间距2)在纵梁翼面高应力区外的其它部位钻孔,只能在中心处钻一个孔,如图所示。
3)在纵梁的边、角区域亦禁止钻孔或焊接,所示的区域即为不允许钻孔和焊接加的部位。
因为在这些部位进行钻孔或焊接,极易引起车架早期开裂。
主车架纵梁禁止钻孔区主车架纵梁禁止焊接区4)严禁将车架纵梁或横梁的男面加工成缺口形状。
本课题中由于主车架与副车架之间的连接选用止推连接板形式,故主车架不用考虑钻孔,只需考虑焊接的位置得当。
主车架的加长设计因专用汽车法布置的需要,对主车架有时要进行加长。
例如厢式零担货物运输车和轻泡货物运输车,若用普通汽车底盘改装.则需要将轴距加大,改装长货厢来提高运输效率,此时要将车架在其中部断开后再加长。
也有将车架后悬部分加长的改装设计。
车架加长部分应尽量采用与原车架纵梁尺寸规格一样、性能相同的材料。
车架的加长部分与车架的连接一般采用焊接。
首先在纵梁腹板处,按与纵梁轴线成夹角45。
或90。
的方向把纵梁断开,然后把切口断面加工成坡口形状,如图3-4所示。
最后将加部分与车架纵梁对接起来。
为了获得v型焊缝对接接头的最佳强度,防止焊缝起点出现焊接缺陷,应朱用引弧焊法或退弧焊法。
焊接时应根据纵梁的材料选择合适的焊条型号、直径及焊接规范。
副车架设计说明书

摘要本文是对侧倾式自卸汽车副车架总成设计的简要说明。
本文首先对自卸车的设计特点以及国内外发展现状做了相关的概述,简要介绍了自卸汽车的历史跟发展前景。
文中通过对所给参数进行分析论证,对副车架纵梁的尺寸参数、材料选择,横梁的参数设计、材料选择,纵梁与横梁之间连接结构,举升机构在副车架上的安装方式进行了设计。
在设计副车架总成纵梁的的过程中,充分考虑了自卸汽车的经济性跟使用功能。
在其他部件的设计过程中,充分考虑了它们之间的相互配合,使它们能够协调工作。
所设计的副车架总成能够满足预期期望。
提供车厢、举升机构的安装位置,改善自卸汽车主车架的应力分布情况。
关键字:自卸汽车副车架总成,纵梁,横梁,连接结构安装位置,举升机构安装位置,设计ABSTRACTThat design specification is a simple explanation for the design of a subframe for a roll-type dump truck.In that design specification,a simple but clear view about the roll-type dump truck was given to help people understand the history of the roll-type dump truck better. To achieve that target,in this design specification,the deputy frame rails,the subframe beams,the connection of the deputy frame rails and the subframe beams,the installation location of lifting mechanism must be well designed.This subframe can achieve the expectation of the roll-type dump truck as required.And that subframe also provide some place to install the lifting mechanism and the compartment.As people expect,it also can make the roll-type dump truck have a better work situation. When design the subframe beams,the economic effect and the function was considered.And so on the others.Key words: subframe for a roll-type dump truck,deputy frame rails,subframe beams,location of connection,location of lifting mechanism,design目录第一章绪论 (1)1.1 课题的研究背景、意义 (1)1.1.1、课题的研究背景 (1)1.1.2、课题的研究意义 (1)第二章副车架总体方案设计 (4)2.1副车架截面形状及尺寸的设计 (6)2.2副车架前端形状的设计 (7)2.3举升机构位置的设计 (8)2.4连接结构安装位置的选择 (9)2.5铰支座位置的设计 (11)2.6副车架在二类底盘上的布置 (11)第三章副车架及相关零部件结构设计 (13)3.1纵梁的设计 (13)3.1.1纵梁结构、材料设计 (13)3.1.1纵梁强度校核 (13)3.2横梁的设计 (19)3.3连接结构的设计 (20)3.3.1副车架纵梁与横梁的连接方式的选择 (20)3.3.2铆缝的强度计算 (21)3.3.2焊接强度的计算 (22)3.4铰支座的设计 (23)3.4.1车厢与副车架连接铰支座的设计 (23)3.4.2举升机构与副车架连接铰支座的设计 (24)第四章结论 (25)致谢 (28)参考文献 (29)附录 (30)第一章绪论1.1 课题的研究背景、意义1.1.1、课题的研究背景自卸汽车是利用汽车本身的发动机动力驱动液压举升机构,使车厢倾斜一定角度进行卸货,并依靠车厢自重自动落下复位的专用汽车。
一种后副车架、后悬架总成及车辆的制作方法
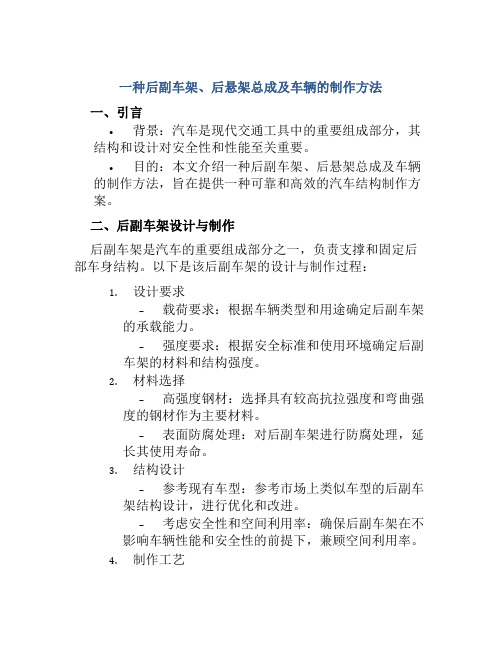
一种后副车架、后悬架总成及车辆的制作方法一、引言•背景:汽车是现代交通工具中的重要组成部分,其结构和设计对安全性和性能至关重要。
•目的:本文介绍一种后副车架、后悬架总成及车辆的制作方法,旨在提供一种可靠和高效的汽车结构制作方案。
二、后副车架设计与制作后副车架是汽车的重要组成部分之一,负责支撑和固定后部车身结构。
以下是该后副车架的设计与制作过程:1.设计要求–载荷要求:根据车辆类型和用途确定后副车架的承载能力。
–强度要求:根据安全标准和使用环境确定后副车架的材料和结构强度。
2.材料选择–高强度钢材:选择具有较高抗拉强度和弯曲强度的钢材作为主要材料。
–表面防腐处理:对后副车架进行防腐处理,延长其使用寿命。
3.结构设计–参考现有车型:参考市场上类似车型的后副车架结构设计,进行优化和改进。
–考虑安全性和空间利用率:确保后副车架在不影响车辆性能和安全性的前提下,兼顾空间利用率。
4.制作工艺–切割和弯曲:使用合适的机械设备将钢材切割成所需形状,并根据设计要求进行弯曲。
–焊接:采用高效且耐久的焊接方法将各部件焊接在一起,确保结构牢固。
三、后悬架总成设计与制作后悬架总成是支撑车辆后部车轮,并提供平稳悬挂和减震功能的重要组成部分。
以下是该后悬架总成的设计与制作过程:1.设计要求–载荷要求:根据车辆类型和用途确定后悬架总成的承载能力。
–减震要求:保证车辆在行驶过程中具备良好的减震效果,提高乘坐舒适性。
–空间利用与节约成本:确保后悬架总成结构紧凑,提高空间利用率,并减少材料和成本。
2.材料选择–弹簧:选择具有良好弹性和耐久性能的弹簧材料。
–减震器:选择高效的减震器,以提供优秀的减震效果。
3.结构设计–参考现有设计:参考市场上类似车型的后悬架总成设计,进行优化和改进。
–考虑安全性和稳定性:确保后悬架总成在高速行驶和恶劣路况下具备良好的稳定性和安全性。
4.制作工艺–弹簧制作:根据设计要求,选择适当的工艺制作弹簧。
–减震器安装:采用合适的安装方法将减震器固定在后悬架总成上,确保安全稳定。
浅谈底盘车架的改装

浅谈底盘车架的改装摘要:本文阐述专用汽车改装设计时主车架和副车架的改装设计要求。
关键词:主车架;副车架目前我国对于常规的厢式车、罐式车、自卸车等通常是采用二类汽车底盘改装设汁,这是目前专用汽车设计中选用底盘型式最多的一种。
所谓二类汽车底盘,是指在基本型整车的基础上去掉货箱。
改装设计总布置时,在没有货箱的汽车底盘上,加装所需的工作装置或特种车身。
工作装置或特种车身和底盘之间由车架进行连接固定。
1主车架的改装主车架是汽车底盘上各总成及专用工作装置安装的基础,改装时受到的影响最大,因此要特别引起注意。
1.1主车架的钻孔和焊接主车架是受载荷很大的部件,除承受整车静载荷外,还要受到车辆行驶时的动载荷,为了保持主车架的强度和刚度,原则上不允许在主车架纵梁上钻孔和焊接,应尽量使用车架上原有的孔。
如果安装专用设备或其它附件,不得不在车架上钻孔或焊接时,应避免在高应力区钻孔或焊接。
主车架纵梁的高应力区位于轴距之间纵梁的下冀面和后悬的上冀面处。
因为这些部位纵梁应力较大,钻孔容易产生应力集中。
对于主车架纵梁高应力区以外的其余地方需要钻孔或焊接时,应注意以下事项:(1)尽量减小孔径,增加孔间距离。
(2)在纵梁的边、角区域禁止钻孔或焊接。
(3)严禁将车架纵梁或横梁的截面加工成缺口形状。
1.2主车架的加长设计因专用汽车布置的需要,对主车架有时需要进行加长。
例如厢式货物运输车和轻泡货物运输车,若用普通汽车底盘改装.则需要将轴距加大,改装长货厢来提高运输效率,此时要将车架在其中部断开后再加长。
也有将车架后悬部分加长的改装设计。
车架加长部分应尽量采用与原车架纵梁尺寸规格一样、性能相同的材料。
车架的加长部分与车架的连接一般采用焊接。
首先在纵梁腹板处,按与纵梁轴线成夹角45°或90°的方向把纵梁断开,然后把切口断面加工成坡口形状,最后将加长部分与车架纵梁对接起来。
1.3主车架加强板的设计(1)主车架纵梁加强板的条件主车架改装时,为了减少车架纵梁的局部应力,或者为了使车架加长后仍能满足强度和刚度的要求,对装载质量增加;轴距和总长发生变化,使车架采用中部拼接或尾部加长时;为了使车架高应力区(危险断面)满足强度和刚度的要求,同时又使车架在某一区间的截面尺寸变化不致太大,这些情况,常常在车架纵梁上采用加强板。
前副车架设计

前副车架设计1. 引言在汽车工程中,副车架是指承载车身和连接前后悬挂系统的结构组成部分。
其中前副车架作为汽车前部的主要支撑和连接部件,承担着重要的作用。
本文将对前副车架的设计进行详细介绍,包括设计要点、材料选择、结构设计等。
2. 设计要点前副车架设计的目标是实现良好的刚度和强度,同时尽可能减轻重量,以提高汽车的操控性和燃油经济性。
下面是前副车架设计的几个重要要点:1.刚度和强度:前副车架需要具有足够的刚度和强度,以承受前部悬挂系统产生的力和扭矩。
这一点可以通过合理的结构设计和材料选择来实现。
2.重量优化:前副车架的重量对整车的性能有直接影响。
因此,在设计过程中应尽可能采用轻量化的设计方案,包括减少材料使用量、优化结构布局等。
3.安全性:前副车架需要具有良好的安全性能,能够在碰撞事故中吸收和转移能量,保护车辆乘员的生命安全。
3. 材料选择前副车架一般采用高强度钢材作为主要材料,具有良好的强度和刚度特性。
同时,为了实现重量优化,也可以考虑使用铝合金等轻质材料。
具体材料选择应根据车辆的使用环境、预算等因素进行综合考虑。
4. 结构设计前副车架的结构设计是保证刚度、强度和重量优化的关键。
下面是一些常见的结构设计方法:•框架结构:框架结构是一种常见的前副车架设计方案,可以提供较高的刚度和强度。
在设计过程中,可以通过优化框架横截面形状和尺寸,以及增加加强筋等方式来提高结构性能。
•悬挂连接:前副车架需要与前悬挂系统进行连接,以承受悬挂系统产生的力和扭矩。
悬挂连接部分的设计应保证连接强度和刚度,并考虑减少疲劳损伤。
•碰撞安全设计:前副车架在碰撞事故中起到保护车辆乘员的作用。
为了提高碰撞安全性能,可以在前副车架的设计中考虑使用可控变形结构、吸能材料等。
5. 进一步研究和发展方向随着汽车技术的不断发展,前副车架的设计也在不断创新和优化。
以下是一些可能的进一步研究和发展方向:•复合材料应用:复合材料具有高强度、轻量化和抗腐蚀等优点,可以考虑将其应用于前副车架的设计中,以进一步减轻重量。
副车架设计规范-----------新能源汽车

为便于简化后期焊接工艺,外部安装套管类零部件设计过程中,一定要保证在上下颠倒焊接时可互换通用,一般需注意上下表面公差要求相同、两端倒角相同等,且凸出高度推荐大于6mm,套管与钣金件留有(0-0.5)mm间隙。
图1-15 某车型外部安装套管
4.12副车架平台化设计
副车架设计之初就应考虑需搭载此副车架的所有车型的平台化设计,前副车架主要考虑不同动力总成、两四驱、左右舵等因素影响,如某车型共搭载4款动力总成,在此基础上需同步开发两四驱、左右舵车型,在副车架设计过程中,需考虑满足所有动力总成的最大包络要求、右舵转向器、四驱分动器等零部件的安装要求。
4.3 副车架与车身安装点、定位点设计
副车架与车身安装点一般为4个或者6个,且左右两侧相互对称,,4个安装点设计位置一般位于副车架的4个边角处, 如图1-3、1-4、1-5所示,6个安装点设计方式相对4个安装点方案一般在下摆臂安装点之间采用焊接支架的形式增加2个对称的安装点,如图1、2所示,安装点设计完成后需进行装配可行性、可维修性校核,特别是位于下摆臂之间的副车架安装点,摆臂设计过程中应对其安装点进行避让,且此安装点装配可行性校核时需将下摆臂跳动到下极限状态进行校核,如图1-1所示。
动力学性能分析部
NC阶段
5
前后悬架系统疲劳分析
可靠性工程研究院
NC阶段
6
前后悬架系统焊点及焊缝疲劳分析
可靠性工程研究院
NC阶段
6.2 副车架CAE分析所需输入
1、副车架设计数模及悬架系统数据;
2、各钣金件材质明细清单;
3、悬架系统运动硬点列表;
4、悬架系统所有弹性元件(包括副车架衬套等)刚度曲线;
5、最新副车架数据相对上版数据具体变更点。
副车架设计说明书

摘要本文是对侧倾式自卸汽车副车架总成设计的简要说明。
本文首先对自卸车的设计特点以及国内外发展现状做了相关的概述,简要介绍了自卸汽车的历史跟发展前景。
文中通过对所给参数进行分析论证,对副车架纵梁的尺寸参数、材料选择,横梁的参数设计、材料选择,纵梁与横梁之间连接结构,举升机构在副车架上的安装方式进行了设计。
在设计副车架总成纵梁的的过程中,充分考虑了自卸汽车的经济性跟使用功能。
在其他部件的设计过程中,充分考虑了它们之间的相互配合,使它们能够协调工作。
所设计的副车架总成能够满足预期期望。
提供车厢、举升机构的安装位置,改善自卸汽车主车架的应力分布情况。
关键字:自卸汽车副车架总成,纵梁,横梁,连接结构安装位置,举升机构安装位置,设计ABSTRACTThat design specification is a simple explanation for the design of a subframe for a roll-type dump truck.In that design specification,a simple but clear view about the roll-type dump truck was given to help people understand the history of the roll-type dump truck better. To achieve that target,in this design specification,the deputy frame rails,the subframe beams,the connection of the deputy frame rails and the subframe beams,the installation location of lifting mechanism must be well designed.This subframe can achieve the expectation of the roll-type dump truck as that subframe also provide some place to install the lifting mechanism and the people expect,it also can make the roll-type dump truck have a better work situation. When design the subframe beams,the economic effect and the function was so on the others.Key words: subframe for a roll-type dump truck,deputy frame rails,subframe beams,location of connection,location of lifting mechanism,design目录第一章绪论.................................................. 错误!未定义书签。
对轿车副车架设计与优化的研究洪磊

对轿车副车架设计与优化的研究洪磊发布时间:2023-05-31T11:36:09.668Z 来源:《中国电业与能源》2023年6期作者:洪磊[导读] 目前,轿车副车架设计质量提升,受到行业内关注。
本文将针对轿车载荷情况和典型工况设计情况,对轿车副车架设计开展优化,设计优化中应用三维CAD软件,提高设计质量。
最终完成构件的强度计算,借此分析优化设计后的轿车副车架优势。
研究发现,通过优化设计后的副车架可通过减小板材厚度的方式,实现车架减重的效果,进而提升轿车的整体性能。
本文关于轿车副车架性能优化的研究,可供其他同行工作参考。
宁波汇众汽车车桥制造有限公司 315033摘要:目前,轿车副车架设计质量提升,受到行业内关注。
本文将针对轿车载荷情况和典型工况设计情况,对轿车副车架设计开展优化,设计优化中应用三维CAD软件,提高设计质量。
最终完成构件的强度计算,借此分析优化设计后的轿车副车架优势。
研究发现,通过优化设计后的副车架可通过减小板材厚度的方式,实现车架减重的效果,进而提升轿车的整体性能。
本文关于轿车副车架性能优化的研究,可供其他同行工作参考。
关键词:副车架;优化设计;轿车引言:研究发现,汽车底盘性能很难兼顾舒适性、操控性,两者是相互矛盾的。
针对悬挂系统的设计,设计者会选用一些复杂结构来尽量保障操控性和底盘舒适性的平衡,而轿车副车架发挥的就是这方面的作用。
简单地说,副车架的作用显著,可看作前后车桥的骨架,属于轿车的重要构成。
传统副车架设计中应用的是承载式车身,这种方式会影响操作性能,随着副车架设计的完善,悬挂系统结构发生了改变,由散件变成了总成,操作中稍作调校便可实现良好匹配的效果。
基于这种结构的副车架设计,除了方便和优越性要得到保障以外,还要兼顾舒适性和悬挂刚度等具体需求。
1副车架的作用原理对于副车架来说,在设计中需满足性能需求,副车架的突出作用是控制路面震动的传入,借此增加行车的舒适性。
同时,借助副车架的设计,还可以强化悬挂系统连接刚度,从而提升安全性。
- 1、下载文档前请自行甄别文档内容的完整性,平台不提供额外的编辑、内容补充、找答案等附加服务。
- 2、"仅部分预览"的文档,不可在线预览部分如存在完整性等问题,可反馈申请退款(可完整预览的文档不适用该条件!)。
- 3、如文档侵犯您的权益,请联系客服反馈,我们会尽快为您处理(人工客服工作时间:9:00-18:30)。
车架的改装主车架是汽车底盘上各总成及专用工作装置安装的基础,改装时受到的影响最大,因此,要特别引起注意。
主车架是受载荷很大的部件,除承受整车静载荷外,还要受到车辆行驶时的动载荷,为了保持主车架的强度和刚度,原则上不允许在主车架纵梁上钻孔和焊接,应尽量使用车架上原有的孔。
如果安装专用设备或其它附件,不得不在车架上钻孔或焊接时.应避免在高应力区钻孔或焊接。
主车架纵梁的高应力区在轴距之间纵梁的下冀面和后悬的上冀面处。
因为这些部位纵梁应力较大,钻孔容易产生应力集中。
对于主车架纵梁高应力区以外的其余地方需要钻孔或焊接时,应注意以下事项:1)尽量减小孔径,增加孔间距离,对钻孔的位置和孔径规范,应满足图和表的要求。
主车架钻孔的孔径和孔间距2)在纵梁翼面高应力区外的其它部位钻孔,只能在中心处钻一个孔,如图所示。
3)在纵梁的边、角区域亦禁止钻孔或焊接,所示的区域即为不允许钻孔和焊接加的部位。
因为在这些部位进行钻孔或焊接,极易引起车架早期开裂。
主车架纵梁禁止钻孔区主车架纵梁禁止焊接区4)严禁将车架纵梁或横梁的男面加工成缺口形状。
本课题中由于主车架与副车架之间的连接选用止推连接板形式,故主车架不用考虑钻孔,只需考虑焊接的位置得当。
主车架的加长设计因专用汽车法布置的需要,对主车架有时要进行加长。
例如厢式零担货物运输车和轻泡货物运输车,若用普通汽车底盘改装.则需要将轴距加大,改装长货厢来提高运输效率,此时要将车架在其中部断开后再加长。
也有将车架后悬部分加长的改装设计。
车架加长部分应尽量采用与原车架纵梁尺寸规格一样、性能相同的材料。
车架的加长部分与车架的连接一般采用焊接。
首先在纵梁腹板处,按与纵梁轴线成夹角45。
或90。
的方向把纵梁断开,然后把切口断面加工成坡口形状,如图3-4所示。
最后将加部分与车架纵梁对接起来。
为了获得v型焊缝对接接头的最佳强度,防止焊缝起点出现焊接缺陷,应朱用引弧焊法或退弧焊法。
焊接时应根据纵梁的材料选择合适的焊条型号、直径及焊接规范。
可采用手工电孤焊或气体保护焊,并选用磁性焊条,保证在高载荷、变形和振动的情况下的焊接强度。
纵梁的坡口形状主车架加强板的设计1)设主车架纵梁加强板的条件主车架改装时,为了减少车架纵梁的局部应力。
或者为了使车架加长后仍能满足强度和刚度的要求,对装载质量增加;轴距和总长发生变化,使车架采用中部拼接或尾部加长时;为了使车架高应力区(危险断面)满足强度和刚度的要求,同时又使车架在某一区间的截面尺寸变化不致太大,这些情况,常常在车架纵梁上采用加强板。
2)加强板的形状加强板的截面形状推荐选用L型,其厚度应不小于车架厚度的40%。
L型加强板的冀面应贴合在车架纵梁翼面受拉伸的一边。
加强板的端头形状应逐步过渡,如切成小于45°的斜角,或在端头中部开光滑槽加强板的布置加强板布置的合理,可以有效地减少车架的应力。
若布置不合理,则可能使车架产生应力集中。
为了避免应力集中,加强板的端头位置不应在刚度变化部位和集中载荷作用的地方。
例如,应使加强板的端头和副车架的端头充分重叠一部分或使二者相互离开足够的距离,如图所示。
3)加强板的控制加强板和主车架的固定最好采用铆接。
加强板末端和铆钉孔之间的最小距离为25mm,铆钉的间距为70~150 mm。
当铆接有困难时,可在加强板上加工孔塞焊于纵梁胶板上,塞焊孔直径为20~30 mm,塞焊孔与加强板端部的最小距离为25mm,孔间距为100~170 mm。
加强板的湍头形状1-主车架纵梁;2-加强板加强板的合理布置1-加强板;2-主车架纵梁;3-副车架副车架的设计在专用汽车设计时,为了改善主车架的承载情况,避免集中载荷,同时也为了不破坏主车架的结构,一般多采用副车架(副梁)过渡。
本车在工作中受较大的弯曲应力。
因此,本车副车架纵梁采用两根抗弯性能较好的平直槽行梁,材料为16MnReL。
在增加副车架的同时,为了避免由于副车架刚度的急剧变化而引起主车架上的应力集中,所以对副车架的形状、安装位置及与主车架的连接方式都有一定的要求。
副车架的截面形状及尺寸专用汽车副车架的截面形状一般和主车架纵梁的截面形状相同,多采用如图3-7所示的槽形结构,其截面形状尺寸取决于专用汽车的种类及其承受载荷的大小。
对于随车起重运输车的副车架来说,在安装起重装置的范围内,应按如图所示的方式用一块腹板将副车架截面封闭起来,以提高副车架的抗扭和抗弯能力。
副车架的截面形状加强后的副车架截面形状1-副车架;2-腹板加强腹板的位置参照国内外总质量相近车型的副车架纵梁端面尺寸,确定副车架纵梁端面尺寸为100、80、6mm。
加强板的布置车架中部(液压举升机构位置)所受弯曲、扭曲最大,因此在这一区域应加加强板,考虑到零件的工艺性,由于下翼板所受弯曲应力较大,因此,加强板紧贴下翼板,为了避免下翼板由于钻孔而导致抗弯强度下降,除与后加强板重叠部位,该加强板主要与腹板连接。
在纵梁上加上加强板,加强板端头区域车架容易产生集中应力。
为了降低应力集中,加强板端头形状有三种设计方式,见图加强板的三种设计方式本副车架为了批量生产时工艺简单,采用了上图角型的端头形状。
副车架的前端形状及安装位置1)在保证使用可靠的前提下,为了提高挠曲性,减小副车架刚度,应尽量减少副车架的横梁,以减少对纵梁的扭转约束。
2)副车架油缸支承横梁与翻转轴横梁形成框架。
油缸支承横梁应尽量靠近后悬架前支承处的横梁,最好能位于后框架之内。
因为这段主车架变形小,所以副车架对其扭转约束力也相应减弱,同时保证了举升机构的几何特性。
3)在副车架结构要求刚性较高时,可在主、副车架中间增加一层橡胶垫,当主车架变形时以弹性橡胶的变形来减弱副车架对主车架的约束4)副车架与主车架连接如图所示。
副车架与主车架的连接A-A处是截面突变点,在受冲击载荷时,此处出现应力集中,严重时造成主车架断裂。
这就要求副车架的前端结构要设计成渐变截面,以减缓应力集中副车架的前端结构副车架前端形状常有三种形状对于这三种不同形状的副车架前端,在其与主车架纵梁相接触的翼面上部加工有局部斜面,其斜而尺寸如图3-13(c)所示:01h mm =;015~20l mm =。
副车架的三种前端形状(a )U 形;(b )角形;(c )L 形如果加工上述形状困难时,可以采用如图3-14所示的副车架前端简易形状,此时斜面尺寸较大。
对于钢质副车架:05~7h mm =;0200~300l mm =对于硬本质副车架;05~10h mm =;0l H =副车架在汽车底盘上布置时,其前端应尽可能地往驾驶室后围靠近。
为某散装水泥运输车的罐体、副车架相对于汽车底盘的安装位置。
在满足轴荷分配的前提下,其中A 不宜过大,留足空压机的位置即可;B 为副车架的前增离主车架拱形横粱的距离,一般在100 mm 之内;C 为固定副车架的前面第一个U 型螟栓距拱形横梁的距离,一般控制在500~800 mm 的范围内。
副车架前端简易形状(a )刚质副车架 ;(b )硬木质副车架 副车架的安装位置纵梁与横梁的连接设计横梁与纵梁的连接方式主要有三种横梁与纵梁的连接1-纵梁;2-连接板;3横梁横梁与纵梁上下翼板连接,该种连接方式优点是利于提高纵梁的抗扭刚度。
缺点是当车架产生较大扭转变形时,纵梁上下翼面应力将大幅度增加,易引起纵梁上下翼面的早期损坏。
由于车架前后两端扭转变形较小,因此本车架前后两端采用了该种连接方式,为了提高纵梁的扭转刚度采用了纵向连接尺寸较大的连接板。
横梁仅固定在腹板上横梁仅固定在腹板上,这种连接形式连接刚度较差,允许截面产生自由跷曲,可以在车架下翼面变形较大区域采用,以避免纵梁上下翼面早期损坏。
横梁同时与纵梁的腹板及上或下翼板相连,此种连接方式兼有以上两种方式连接的特点,但作用在纵梁上的力直接传递到横梁上,对横梁的强度要求较高。
由于该车平衡悬架的推力杆与平衡悬架支架上的两根横梁连接,因此,这两根横梁与纵梁共同承受平衡悬架传递过来的垂直力(反)和纵向力(牵引力、制动力)。
综合以上考虑,本副车架的纵梁与横梁的连接采用第3种方式,即横梁同时与纵梁的腹板及上或下翼板相连,同时为了降低成本和适于批量生产,本车架纵梁和横梁的连接方式采用铆接。
副车架与主车架的连接设计副车架与主车架的连接常采用如下几种形式。
1)止推连接板是斯泰尔重型专用汽车所采用的止推连接板的结构形状及其安装方式。
连接板上端通过焊接与副车架固定,而下端则利用螺栓与主车架纵梁腹板相连接。
止推板的优点在于可以承受较大的水平载荷,防止副车架与主车架纵梁产生相对水平位移。
相邻两个推止推连接板之间的距离在500~1000 mm范围内。
2)连接支架连接支架由相互独立的上、下托架组成,上、下托架均通过螺栓分别与副车架和主车架纵梁的腹板相固定,然后再用螺栓将上、下托架相连接,见图3-18所示。
由于上、下托架之间留有间隙,因此连接支架所能承受的水平载荷较小,所以连接支架应和止推连接板配合使用。
一般布置是在后悬架前支座前用连接支架连接,在后悬架前支座后用止推连接板连接。
3)U型夹紧螺栓当选用其它连接装置有困难时,可采用U型夹紧螺栓。
但在车架受扭转载荷最大的范围内不允许采用U型螺栓。
当采用U型螺栓固定时,为防止主车架纵梁翼面变形,应在其内侧衬以木块,坦在消声器附近,必须使用角铁等作内衬。
止推连接板的结构1-副车架;2-止推连接板;3-主车架纵梁连接支架1-上托架;2-下托架;3螺栓综合考虑三种连接方式的特点,以及装配工艺性,本文设计的EQ3090主副车架之间采用止推连接板式。