7 副车架设计指导书
车架设计手册汇总
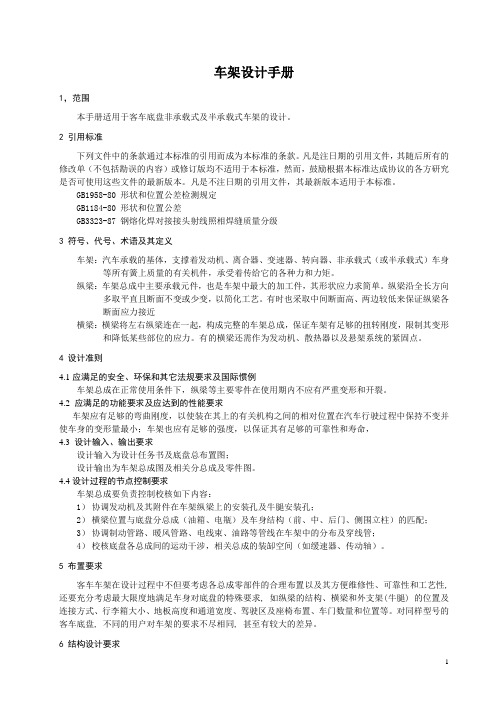
车架设计手册1,范围本手册适用于客车底盘非承载式及半承载式车架的设计。
2 引用标准下列文件中的条款通过本标准的引用而成为本标准的条款。
凡是注日期的引用文件,其随后所有的修改单(不包括勘误的内容)或修订版均不适用于本标准,然而,鼓励根据本标准达成协议的各方研究是否可使用这些文件的最新版本。
凡是不注日期的引用文件,其最新版本适用于本标准。
GB1958-80 形状和位置公差检测规定GB1184-80 形状和位置公差GB3323-87 钢熔化焊对接接头射线照相焊缝质量分级3 符号、代号、术语及其定义车架:汽车承载的基体,支撑着发动机、离合器、变速器、转向器、非承载式(或半承载式)车身等所有簧上质量的有关机件,承受着传给它的各种力和力矩。
纵梁:车架总成中主要承载元件,也是车架中最大的加工件,其形状应力求简单。
纵梁沿全长方向多取平直且断面不变或少变,以简化工艺。
有时也采取中间断面高、两边较低来保证纵梁各断面应力接近横梁:横梁将左右纵梁连在一起,构成完整的车架总成,保证车架有足够的扭转刚度,限制其变形和降低某些部位的应力。
有的横梁还需作为发动机、散热器以及悬架系统的紧固点。
4 设计准则4.1应满足的安全、环保和其它法规要求及国际惯例车架总成在正常使用条件下,纵梁等主要零件在使用期内不应有严重变形和开裂。
4.2 应满足的功能要求及应达到的性能要求车架应有足够的弯曲刚度,以使装在其上的有关机构之间的相对位置在汽车行驶过程中保持不变并使车身的变形量最小;车架也应有足够的强度,以保证其有足够的可靠性和寿命,4.3 设计输入、输出要求设计输入为设计任务书及底盘总布置图;设计输出为车架总成图及相关分总成及零件图。
4.4设计过程的节点控制要求车架总成要负责控制校核如下内容:1)协调发动机及其附件在车架纵梁上的安装孔及牛腿安装孔;2)横梁位置与底盘分总成(油箱、电瓶)及车身结构(前、中、后门、侧围立柱)的匹配;3)协调制动管路、暖风管路、电线束、油路等管线在车架中的分布及穿线管;4)校核底盘各总成间的运动干涉,相关总成的装缷空间(如缓速器、传动轴)。
车架的改造与副车架的设计

车架的改装主车架是汽车底盘上各总成及专用工作装置安装的基础,改装时受到的影响最大,因此,要特别引起注意。
主车架是受载荷很大的部件,除承受整车静载荷外,还要受到车辆行驶时的动载荷,为了保持主车架的强度和刚度,原则上不允许在主车架纵梁上钻孔和焊接,应尽量使用车架上原有的孔。
如果安装专用设备或其它附件,不得不在车架上钻孔或焊接时.应避免在高应力区钻孔或焊接。
主车架纵梁的高应力区在轴距之间纵梁的下冀面和后悬的上冀面处。
因为这些部位纵梁应力较大,钻孔容易产生应力集中。
对于主车架纵梁高应力区以外的其余地方需要钻孔或焊接时,应注意以下事项:1)尽量减小孔径,增加孔间距离,对钻孔的位置和孔径规范,应满足图和表的要求。
主车架钻孔的孔径和孔间距2)在纵梁翼面高应力区外的其它部位钻孔,只能在中心处钻一个孔,如图所示。
3)在纵梁的边、角区域亦禁止钻孔或焊接,所示的区域即为不允许钻孔和焊接加的部位。
因为在这些部位进行钻孔或焊接,极易引起车架早期开裂。
主车架纵梁禁止钻孔区主车架纵梁禁止焊接区4)严禁将车架纵梁或横梁的男面加工成缺口形状。
本课题中由于主车架与副车架之间的连接选用止推连接板形式,故主车架不用考虑钻孔,只需考虑焊接的位置得当。
主车架的加长设计因专用汽车法布置的需要,对主车架有时要进行加长。
例如厢式零担货物运输车和轻泡货物运输车,若用普通汽车底盘改装.则需要将轴距加大,改装长货厢来提高运输效率,此时要将车架在其中部断开后再加长。
也有将车架后悬部分加长的改装设计。
车架加长部分应尽量采用与原车架纵梁尺寸规格一样、性能相同的材料。
车架的加长部分与车架的连接一般采用焊接。
首先在纵梁腹板处,按与纵梁轴线成夹角45。
或90。
的方向把纵梁断开,然后把切口断面加工成坡口形状,如图3-4所示。
最后将加部分与车架纵梁对接起来。
为了获得v型焊缝对接接头的最佳强度,防止焊缝起点出现焊接缺陷,应朱用引弧焊法或退弧焊法。
焊接时应根据纵梁的材料选择合适的焊条型号、直径及焊接规范。
一种后副车架、后悬架总成及车辆的制作方法
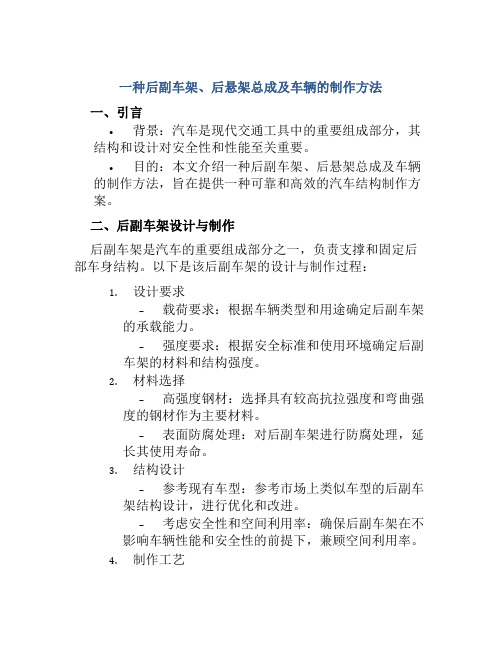
一种后副车架、后悬架总成及车辆的制作方法一、引言•背景:汽车是现代交通工具中的重要组成部分,其结构和设计对安全性和性能至关重要。
•目的:本文介绍一种后副车架、后悬架总成及车辆的制作方法,旨在提供一种可靠和高效的汽车结构制作方案。
二、后副车架设计与制作后副车架是汽车的重要组成部分之一,负责支撑和固定后部车身结构。
以下是该后副车架的设计与制作过程:1.设计要求–载荷要求:根据车辆类型和用途确定后副车架的承载能力。
–强度要求:根据安全标准和使用环境确定后副车架的材料和结构强度。
2.材料选择–高强度钢材:选择具有较高抗拉强度和弯曲强度的钢材作为主要材料。
–表面防腐处理:对后副车架进行防腐处理,延长其使用寿命。
3.结构设计–参考现有车型:参考市场上类似车型的后副车架结构设计,进行优化和改进。
–考虑安全性和空间利用率:确保后副车架在不影响车辆性能和安全性的前提下,兼顾空间利用率。
4.制作工艺–切割和弯曲:使用合适的机械设备将钢材切割成所需形状,并根据设计要求进行弯曲。
–焊接:采用高效且耐久的焊接方法将各部件焊接在一起,确保结构牢固。
三、后悬架总成设计与制作后悬架总成是支撑车辆后部车轮,并提供平稳悬挂和减震功能的重要组成部分。
以下是该后悬架总成的设计与制作过程:1.设计要求–载荷要求:根据车辆类型和用途确定后悬架总成的承载能力。
–减震要求:保证车辆在行驶过程中具备良好的减震效果,提高乘坐舒适性。
–空间利用与节约成本:确保后悬架总成结构紧凑,提高空间利用率,并减少材料和成本。
2.材料选择–弹簧:选择具有良好弹性和耐久性能的弹簧材料。
–减震器:选择高效的减震器,以提供优秀的减震效果。
3.结构设计–参考现有设计:参考市场上类似车型的后悬架总成设计,进行优化和改进。
–考虑安全性和稳定性:确保后悬架总成在高速行驶和恶劣路况下具备良好的稳定性和安全性。
4.制作工艺–弹簧制作:根据设计要求,选择适当的工艺制作弹簧。
–减震器安装:采用合适的安装方法将减震器固定在后悬架总成上,确保安全稳定。
车身前副车架安装点设计指南

车身前副车架安装点设计规范1 范围本标准规定了车身前副车架安装点设计要点及其判断标准等。
本标准适用于新开发的M1类和N1类汽车车身前副车架安装点设计。
2 规范性引用文件下列文件对于本文件的应用是必不可少的。
凡是注日期的引用文件,仅注日期的版本适用于本文件。
凡是不注日期的引用文件,其最新版本(包括所有的修改单)适用于本文件。
《GB 11566-2009 乘用车外部凸出物》《GB/T19234-2003 乘用车尺寸代码》《GB/T 709-2006 热轧钢板和钢带的尺寸、外形、重量及允许偏差》《GB/T 710-2008 优质碳素结构钢热轧薄钢板和钢带》《GB/T4780-2000 汽车车身术语》《整车车身设计公差与装配尺寸链分析》《螺栓连接的装配质量控制》3 术语和定义3.1 车身结构3.1.1车身结构是各个零件的安装载体。
3.2 副车架3.2.1副车架最早的应用原因是可以降低发动机舱传递到驾驶室的振动和噪音。
副车架与车身的连接点就如同发动机悬置一样。
通常一个副车架总成需要由四个悬置点与车身连接,这样既能保证其连接刚度,又能有很好的震动隔绝效果。
副车架能分5级减小震动的传入,对副车架来说,在性能上主要目的是减小路面震动的传入,以及提高悬挂系统的连接刚度,因此装有副车架的车驾驶起来会感觉底盘非常扎实,非常紧凑。
而副车架悬置软硬度的设定也面临着像悬挂调校一样的一个不可规避的矛盾。
所以工程师们在设计和匹配副车架时通常会针对车型的定位和用途选择合适刚度的橡胶衬垫。
由于来自发动机和悬挂的一部分震动会先到达副车架然后再传到车身,经过副车架的衰减后振动噪声会有明显改善。
副车架发展到今天,可以简化多车型的研发步骤。
这是因为悬挂、稳定杆、转向机等底盘零件都可以预先安装在一起,形成一个所谓的超级模块,然后再一起安装到车身上。
3.3前副车架安装点3.3.1前副车架安装点指安装在车身的安装孔中心线与安装面下平面交点的位置(XYZ 坐标)及装配孔公称尺寸。
副车架设计作业指导书

副车架设计作业指导书编制: 日期:审核: 日期:批准: 日期:发布日期:年 月 日 实施日期:年 月 日前 言为使本公司副车架设计规范化,参考国内外汽车副车架设计的技术要求,结合本公司已经开发车型的经验,编制本汽车副车架设计指导书。
意在对本公司设计人员在副车架设计的过程中起到一种指导设计的作用,让副车架设计的员工有所依据,在设计的过程中少走些弯路,提高汽车副车架设计的效率和精度!本作业指导书将在本公司所有车型副车架开发设计中贯彻,并在实践中进一步提高完善。
本标准于2011年XX月XX日起实施。
本指导书由上海同捷科技股份有限公司第五研发中心底盘总布置分院提出。
本指导书由上海同捷科技股份有限公司第五研发中心底盘总布置分院负责归口管理。
本标准主要起草人:马显目录一 副车架概述 (4)1.1 副车架功能概述 (4)1.2副车架主要结构形式 (6)二 副车架设计流程 (9)2.1 副车架主要设计流程 (9)2.2 副车架设计要求 (11)2.3 相关设计标准 (13)三.副车架的设计过程 (13)3.1 设计输入及标杆对比分析 (14)3.2 副车架设计构想的确定 (19)3.3副车架总成结构设计。
(21)3.4 焊接流程确定、焊接定位关系确定及焊接总成公差尺寸保证 (24)3.5 因成型分析而进行的调整 (26)3.6 因CAE分析结果而对局部结构进行的调整 (26)3.7 因工艺及零部件平台化而进行的调整 (27)3.8技术文件的编制 (28)3.9输出内容检查项目 (31)四.试制装车及生产中经常出现的问题 (31)五 参考文献 (33)一 副车架概述副车架可以看成是前后车桥的骨架,是前后车桥的组成部分。
副车架并非完整的车架,只是支承前后车桥、悬挂的支架,使车桥、悬挂通过它再与“正车架”相连,习惯上称为“副车架”。
1.1 副车架功能概述从结构上讲,传统没有副车架的承载式车身悬挂系统是直接与车身钢板相连的,如下图所示,前后车桥的悬挂摇臂机构都为散件。
副车架设计说明书

摘要本文是对侧倾式自卸汽车副车架总成设计的简要说明。
本文首先对自卸车的设计特点以及国内外发展现状做了相关的概述,简要介绍了自卸汽车的历史跟发展前景。
文中通过对所给参数进行分析论证,对副车架纵梁的尺寸参数、材料选择,横梁的参数设计、材料选择,纵梁与横梁之间连接结构,举升机构在副车架上的安装方式进行了设计。
在设计副车架总成纵梁的的过程中,充分考虑了自卸汽车的经济性跟使用功能。
在其他部件的设计过程中,充分考虑了它们之间的相互配合,使它们能够协调工作。
所设计的副车架总成能够满足预期期望。
提供车厢、举升机构的安装位置,改善自卸汽车主车架的应力分布情况。
关键字:自卸汽车副车架总成,纵梁,横梁,连接结构安装位置,举升机构安装位置,设计ABSTRACTThat design specification is a simple explanation for the design of a subframe for a roll-type dump truck.In that design specification,a simple but clear view about the roll-type dump truck was given to help people understand the history of the roll-type dump truck better. To achieve that target,in this design specification,the deputy frame rails,the subframe beams,the connection of the deputy frame rails and the subframe beams,the installation location of lifting mechanism must be well designed.This subframe can achieve the expectation of the roll-type dump truck as that subframe also provide some place to install the lifting mechanism and the people expect,it also can make the roll-type dump truck have a better work situation. When design the subframe beams,the economic effect and the function was so on the others.Key words: subframe for a roll-type dump truck,deputy frame rails,subframe beams,location of connection,location of lifting mechanism,design目录第一章绪论.................................................. 错误!未定义书签。
厢式货车副车架设计
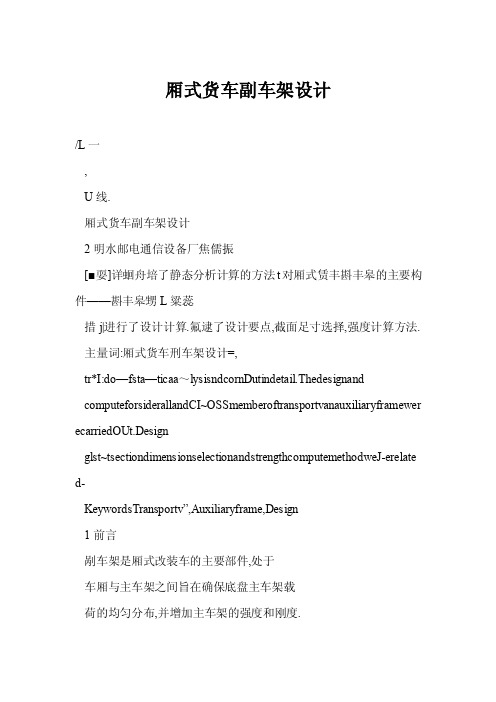
厢式货车副车架设计/L一,U线.厢式货车副车架设计2明水邮电通信设备厂焦儒振[■耍]详蛔舟培了静态分析计算的方法t对厢式赁丰斟丰皋的主要构件——斟丰皋甥L粱蕊措j|进行了设计计算.氟逮了设计要点,截面足寸选择,强度计算方法. 主量词:厢式货车刑车架设计=,tr*I:do—fsta—ticaa~lysisndcornDutindetail.Thedesignand computeforsiderallandCI~OSSmemberoftransportvanauxiliaryframewer ecarriedOUt.Designglst~tsectiondimensionselectionandstrengthcomputemethodweJ-erelate d-KeywordsTransportv”,Auxiliaryframe,Design1前言剐车架是厢式改装车的主要部件,处于车厢与主车架之间旨在确保底盘主车架载荷的均匀分布,并增加主车架的强度和刚度.探入了解酣车架的承载特性及其与主车架承蓑分配情况是副车架结构设计,设进和优化的基础.随着计算机辅助设计及有限元法的广泛应用,动态设计计算日益显得重要.但由于条件的限制,动态设计计算的准确性和可靠性尚显不足,而且大部分厢式车改装厂还难以进行动态设计计算,因此.静态计算仍然是基本的设计计算手段.本文用静态计算的方法对厢式货车副车架的主要构件——副车架纵粟(简称副纵粱)及横粱进行设计计算并予以讨论分析.2翻车集设计2.1副纵粱设计&11副纵粱设计要点a.对具有较高质心位置及载质量较大的厢式车一般采用槽形通长式副纵粱.截面如图1.b.制造材料应具有良好的焊接性和机械性能,一般要求抗拉强度a,~370N/mm.屈服极限,≥240N/ram.,延伸率以≥20.啊1剐纵粱藏面c.翼缘宽度应与主车架纵粱(简称主纵粱)翼缘宽度相同.不宜大于主纵粱翼缘宽度.d.副纵粱截面尺寸确定后,要分别对副纵粱和主纵粱进行强度计算,并根据其惯性矩,抗弯截面系数分配弯矩.2.1.2副纵粱截面尺寸选择副纵粱翼缘宽度应与主纵粱翼缘宽度相同,板材厚度}≥4ram.因此,副纵粱截面尺寸选择主要是确定鹿板高度H.鹿板高度取决于副纵粱承受弯矩的能力及结构上的需要.国外汽车生产厂家均在汽车改装指导书中提出槽形副纵粱截面的最小尺寸,供改装时选择采用,如”依维柯汽车改装指南”中给出的槽形副纵粱截面最小尺寸如表1.根据我厂多年设计生产的经验,副纵粱截面最小尺寸如表2.一2.1.3副纵粱强度计算2.1.3.1强度计算根据主,副纵粱受力特点,一般只需计算.孽墓1997?3专用池车SpecialPurposeV ehicle?15? 弯曲应力,因其剪应力较小,可略去不计.表1依雏柯改装车副纵梁截面最小尺寸酎纵粱截面车辆级别抗弯截面系数尺寸Ⅳ,mT【LH,8,”mm3~7t1600680,50,47.9~1[】{26000100,50,511~33t46000120,60,6剐纵粱截面车载质量抗弯截面系数尺寸1,mmH,B,,mm5t以下250008550,45~8t3900O120,70,58~10t56000120,70,6副纵粱采用U形夹紧螺栓与主纵粱紧密连接,因此可采用两种材料组合粱弯曲时弯矩的计算方法计算主,哥j纵粱动载荷下的摄大弯矩MM—及其弯曲应力,.M~一?M~一?=—HijMla~一Mla~,=式中:E.,E——主,副纵粱材料的弹性模量.,——主,副纵粱截面惯性矩朋.——车架动载荷下的最大弯矩——主,副纵粱抗弯截面系数一的计算方法,在”邮政车副车架设计”一文中有详细介绍(见本刊1.996年第1 期).根据上面的计算,若满足<一及<(一,.分别为主剐纵粱材料的疲劳极限),则所选副纵粱截面尺寸是合理的. 否则,应重新选取副纵梁截面尺寸,即对主,副纵梁承受弯矩进行重新分配.2.1.3.2临界弯曲应力校核当副纵粱变形时,上下翼缘分别受到压缩和拉伸作用而使翼缘断裂.因此,通过以上计算确定副纵粱截面尺寸后,应按薄板理论计算其临界弯曲应力口,并使<.否则,应重新选择副纵粱截面尺寸.E,t,0一0『=【言j式中:——泊松比,取一0.3一般来说,在选定酎纵粱材料厚度t的情况下,副纵粱翼缘的最大宽度应满足B≤16t.2.2横粱设计2.2.1横粱设计要点a制造材料要求与副纵粱制造材料要求相同.b.横粱数目及横粱截面尺寸要根据载质量及受力情况确定.c.尽可能选取同样的横粱间距.这样可使纵粱各段的扭矩相同,也有利于承受弯曲d.尽可能选取相同的横粱截面尺寸.这样可使各横粱刚性一致,协调承载.2.2Z横粱截面尺寸选择横粱截面形状有多种形式,如图2,其宽度B一般取45~50mm;高度不仅要满足强度要求,而且要考虑结构上的要求一般在80~100ram;材料厚度t在2.5~4mm.横粱的截面形状可以用板材折弯,也可使用轧镧型钢,但必须避免出现裂纹,缺口等缺陷.占一田2擅喜I截面类型2.2.3横粱强度计算横粱与剐纵粱相互垂直焊接或螺接在一16?.蕾懦|I厢成货车l9革毒设计起,形成框式结构横粱的两端与货厢骨架侧围焊接或螺接,用以承受货厢的重量.视横梁为固定于副纵粱上的悬臂粱,最大弯矩在横粱与副纵梁腹板的连接处.为了计算方便,假a.横粱等距均布在副纵粱上;b.载质量均布在每一横梁上;c.货厢质量均布在每一横粱的两端.横粱受力简化如图3.图中4,B为横粱与剐纵粱腹板的连接点.,zG1/2IIII{IIIIsIJA占r.田3横粱受力简田A处的弯矩肘为:G百I+一+式中:工——磺粱长度L——横梁悬臂长——横梁载荷中心点至的距离388’25O0.700O0105DO01820851l1775421403结束语a.由于结构的需要或为避免与其他构件发生干涉,游梁无法实现等距均布时,应计算闻距最大处的横梁强度,其承受的货厢质量及计算载荷可按每一横梁所分担的车架长度计算.b.由于普遍超载运行现象,因此,在副车架设计时应予以充分考虑.c.建议汽车底盘生产厂编制改装指导书,为汽车改装厂家提供上装指导.(收稿:1997—06—04责任编辑:张全寿)篙J庠一■l。
副车架设计规范-----------新能源汽车

副车架与车身安装点一般为4个或者6个,且左右两侧相互对称,,4个安装点设计位置一般位于副车架的4个边角处, 如图1-3、1-4、1-5所示,6个安装点设计方式相对4个安装点方案一般在下摆臂安装点之间采用焊接支架的形式增加2个对称的安装点,如图1、2所示,安装点设计完成后需进行装配可行性、可维修性校核,特别是位于下摆臂之间的副车架安装点,摆臂设计过程中应对其安装点进行避让,且此安装点装配可行性校核时需将下摆臂跳动到下极限状态进行校核,如图1-1所示。
4、副车架结构设计
4.1 副车架基本形式的选择
根据设计车型前期的悬架形式定位,选择副车架的基本形式。为降低开发成本及风险,副车架设计基本分为2种情况,情况一为完全重新设计,基本形式在标杆车基础上进行重新设计,情况二为在现有平台基础上进行改款升级,一般形式与基础车型相同。
4.2 副车架的硬点的确定
副车架硬点包括安装硬点、定位硬点、运动硬点三种。
图1-6副车架转向器安装点(左舵上,右舵下)
4.7 后悬置安装点设计
后悬置安装点需根据同平台所有动力总成后悬置点位置进行居中选定,以保证副车架后悬置安装点的平台化;后悬置安装点主要承受来自后悬置的X向力,所以在结构设计过程中需注意将其X向力均匀传递至副车架整体后横梁总成,避免应力集中风险,如图1-7所示。后悬置安装点结构形式可归纳为2类,第一种结构为在后横梁本体上焊接安装支架,如图1-7所示,第二种结构为直接安装在后横梁上下板之间,中间采用支撑板加强,如图1-8所示。
XXXXXXX有限公司
副车架设计规范
编制:
校对:ห้องสมุดไป่ตู้
审核:
批准:
2017-09-15发布 2017-09-20实施
- 1、下载文档前请自行甄别文档内容的完整性,平台不提供额外的编辑、内容补充、找答案等附加服务。
- 2、"仅部分预览"的文档,不可在线预览部分如存在完整性等问题,可反馈申请退款(可完整预览的文档不适用该条件!)。
- 3、如文档侵犯您的权益,请联系客服反馈,我们会尽快为您处理(人工客服工作时间:9:00-18:30)。
副车架设计指导书
1 副车架设计
副车架与主车架的连接一般采用刚性连接。
副车架在设计中应考虑自身结构、刚性分布等,要尽量符合主车架在承载状况下的变形规律,使副车架顺应主车架的扭曲,达到主、副车架的刚性尽量匹配合理(如图2)。
2 车架强度校核
在实际使用状况下车架受力比较复杂,在车架初始设计时,一般对车架强度校核简化为对车架纵梁进行弯曲强度校核。
2.1基本假设
车架纵梁进行弯曲强度校核时,作以下假设:纵梁是支承在悬架支座上的简支梁;所有作用力均通过车架纵梁断面的弯曲中心(即纵梁只发生纯弯曲);空车簧载质量均匀分布在汽车左、右纵梁上;满载时有效载质量e 为集中载荷,分布如图3所示:主、副车架为刚性连接,即主、副车架挠度 2.2车架受力分析及计算
车架受力分析如图3所示。
图三
图中:
G ef
,G
er 为前、后支架所
承受的有效载质量,由上装平衡条件”1计算可得:
G
ef
= )
2/2//()2/(n f e d n f G e
++++
)2/2//()2/(n f e d d e ef e er G G G G e
++++=-=; F f ,F r
为前后轴对车架的
支反力,由车架平衡条件计算可得:F f =b n f l b G a L e
s
G /)]()2/ [--++-,
F r
=[
l)]/b
-n (f G L)-(L/2[e ++G s ;
G
s
为空车簧载重质量,取
G
s
=2
m g/3z(
m 为汽车
整备质量)
2.3车架纵梁弯矩计算
由受力分析和计算结果,可计算每侧车架纵梁各段的弯矩:
21/(2)
S M G X L =- 0X a <≤
22/(2)()
S f M G X L F X a =-+- a X a c <≤+
22
3/(2)())s f ef M G X L F X a G X a c =-+---- a c X a c d +<≤++
24/(2)()()
s f ef M G X L F X a G X a c d =-+----- a c d X a b ++<≤+
25()()/(2)
er s M G X a b G X a b L =------ a c d X a b l n
++<≤++-226()/(2)()/(2)
S er M G X a b l n L G X a b l n n =----+----+
a b l n X L ++-<≤
式中:X 为截面至车架前端距离。
由此可以求得车架纵梁的最大弯矩max
M
2.4 主,副车架弯矩计算
设车架纵梁在任一截面的弯矩为M,而在截面处,主车架纵梁所受弯矩Z
M ,副车架所受
的弯矩为
f
M ,则有如下关系式;
z f M M M
+=
''//yz z z z
D dx M
E J = ''//yf z f f
D dx M
E J =
z f
y y =
式中;
z y f
y 为主副车架纵梁的挠度;
f
z E E ,为主,副车架纵梁材料的弹性模量,
f
z J J ,为主副车架纵梁的截面惯性矩;假设主副车架纵梁的材料基本相似,即z f
E E =,则可求得
主副车架的弯矩
)
()/(f z f f f z z z J J MJ M J J MJ M +=+=
2.5 强度校核
主车架纵梁强度校核
Z
Z Z Z f z z z z H J W W J J J M W M /2)/(/P max max =+==
式中;Z W 为主车架纵梁危险截面系数;Z H 为主车架纵梁高度。
主车架纵梁最大动弯曲应力
zs
f z Z d z d zd p J J M H nk p nk P <+==)(2/max
式中:
d
k 为动载荷系数;n 为疲劳系数;
zs
p 为主车架纵梁材料弯曲应力。
2.6 副车架纵梁强度校核
副车架纵梁最大东弯曲应力:
]
[)(2/max fs f z f fd P J J M H P <+=
式中:
f
H 为副车架纵梁高度;
]
[fs P 为副车架纵梁材料许用应力。
3.主要零件制造工艺 3.1 纵梁和横梁材料
纵梁采用C 型槽钢,由于纵梁受力特别复杂(主要是有弯曲应力)既要有很高
的强度,又要满足连接的加工工艺,一般采用16Mn C 型槽钢。
3.2 纵梁和横梁加工工艺
由于纵梁一般长度很长,常用滚压的方法来加工,少数也采用冲压的方法来加工。
横梁一般较短,常采用冲压来加工。
3.3 纵横梁孔的加工工艺
车架连接精度要求特别高,对孔的加工工艺要求特别高。
孔一般有下面两种加
工方法。
a.采用钣金数控加工中心(投入成本特别大)。
b.采用传统的加工方法,先钻,然后用铰刀铰孔达到一定精度要求。
3.4 纵横梁的连接
由于驱动装置和转向装置都安装在车架上,对定位要求比较高,一般连接采用铆
钉铆接,少数的采用螺栓连接。