多连杆后悬副车架结构及衬套优化设计
多连杆后悬架课程设计
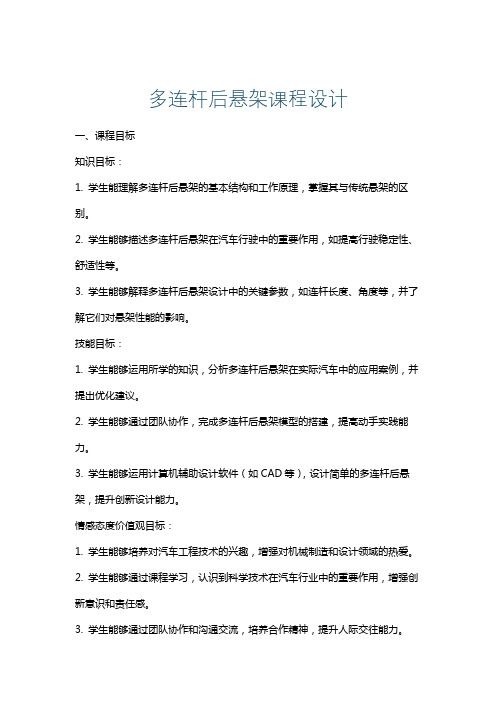
多连杆后悬架课程设计一、课程目标知识目标:1. 学生能理解多连杆后悬架的基本结构和工作原理,掌握其与传统悬架的区别。
2. 学生能够描述多连杆后悬架在汽车行驶中的重要作用,如提高行驶稳定性、舒适性等。
3. 学生能够解释多连杆后悬架设计中的关键参数,如连杆长度、角度等,并了解它们对悬架性能的影响。
技能目标:1. 学生能够运用所学的知识,分析多连杆后悬架在实际汽车中的应用案例,并提出优化建议。
2. 学生能够通过团队协作,完成多连杆后悬架模型的搭建,提高动手实践能力。
3. 学生能够运用计算机辅助设计软件(如CAD等),设计简单的多连杆后悬架,提升创新设计能力。
情感态度价值观目标:1. 学生能够培养对汽车工程技术的兴趣,增强对机械制造和设计领域的热爱。
2. 学生能够通过课程学习,认识到科学技术在汽车行业中的重要作用,增强创新意识和责任感。
3. 学生能够通过团队协作和沟通交流,培养合作精神,提升人际交往能力。
课程性质:本课程为高二年级汽车工程兴趣小组的专题课程,结合学生特点和教学要求,注重理论知识与实践操作的相结合,提高学生的综合运用能力。
学生特点:高二学生对汽车结构有一定的基础认识,对汽车工程技术感兴趣,具备一定的动手实践能力。
教学要求:教师应注重启发式教学,引导学生主动探究,提高学生的创新设计和实践操作能力。
同时,关注学生的情感态度价值观培养,使学生在掌握知识技能的同时,形成良好的合作精神和社会责任感。
通过分解课程目标为具体学习成果,便于后续教学设计和评估。
二、教学内容本课程教学内容围绕多连杆后悬架的设计与应用,结合课本第四章“汽车悬架系统”相关内容展开。
1. 多连杆后悬架基本概念:- 悬架系统的作用与分类- 多连杆后悬架的结构特点- 多连杆后悬架与传统悬架的性能对比2. 多连杆后悬架工作原理与性能分析:- 悬架运动学分析- 悬架动力学分析- 多连杆后悬架关键参数对性能的影响3. 多连杆后悬架设计与应用:- 设计原则与要求- 常见多连杆后悬架结构类型- 多连杆后悬架在汽车中的应用案例4. 实践操作与设计:- 多连杆后悬架模型搭建- 计算机辅助设计(CAD)软件在悬架设计中的应用- 创新设计实践教学大纲安排:第一课时:多连杆后悬架基本概念第二课时:多连杆后悬架工作原理与性能分析第三课时:多连杆后悬架设计与应用第四课时:实践操作与设计(分组进行多连杆后悬架模型搭建和创新设计)教学内容进度:第一周:基本概念学习第二周:工作原理与性能分析第三周:设计与应用第四周:实践操作与设计教学内容与课本紧密关联,旨在确保学生掌握多连杆后悬架相关知识,同时注重实践操作和创新设计能力的培养。
探讨汽车副车架强度模态分析及结构优化

探讨汽车副车架强度模态分析及结构优化摘要:随着社会上经济的发展汽车成为人们出行的必备交通工具,而汽车也在社会上变得越来越普及。
现在就以轿车的副车架为研究的对象,在很多的软件当中建立起来的模型模拟,然后对这些结构进行新型的分析,在进行分析的过程中采取的方法主要就是对强度和自由度进行的分析,在进行分析之后,得出的结果也说明了,汽车的副车架本身的强度是符合要求的,并且汽车的副车架跟发动机之间是有一定的联系,针对这样的问题也有相应的解决方法进行解决。
关键词:汽车的副车架的结构;强度化分析;拓扑结构优化前言:随着人们经济水平的提高,人们对于吃、穿、住、用、行等方面的要求也在不断的提高,随着科技的发展和技术水平的进步,大多数人对汽车的品牌、汽车的舒适度和安全性能还有一系列有关车方面的要求也变得越来越高,而在这其中汽车舒适度和安全性能这两个方面是相互影响、相互制约的,汽车的副车架是现在大部分汽车底盘的最主要的承载件,使用的越来越普及,因为它在使用的过程中比较的频繁,所以应该具有较好的强度和动态特性。
目前,世界上的很多人认为,在使用频率作为优化目标进行优化的过程中进行了很多方面的研究,而且在研究的过程中取得了很多的成果。
在相关的书籍中曾经有过记载,在选择使用轻型车车架的频率来当作拓扑结构优化的主要目标,在这当中进行多部拓扑结构进行优化以此来得到副车架横梁的最佳的拓扑结构。
还有在相关的书籍中记载里,在对汽车的副车架进行频率的拓扑结构的优化时,根据所得到的密度的图纸进行相关数据方面的分析,他的分析出来的计算的结果和实验的数值的数据一致,使得本来应该拥有的频率得到应有的优化,这样也就让更多的人们对汽车的副车架有了更多的了解。
一、汽车的副车架在有限模型方面的建立汽车的副车架在制作的过程中采用的原材料的形成过程是非常复杂的,在汽车的副车架和车架之间,应用四个轴向竖直的橡胶衬套相互连接在一起,纵臂上下摆臂,以及其他的后悬架零部件安装在汽车的副车架上。
S3拖曳臂多连杆后独立悬架装配工艺、工装分析

拖曳臂多连杆后独立悬架装配工艺、工装分析陈信敏(一汽海马汽车有限公司海口 570216)摘要:本文描述了S3车型拖曳臂多连杆后独立悬架后桥的装配工艺以及总装车间AGV小车后桥工装的设计、调试、整改过程,通过四轮工装的设计、调试、整改、验证,最终解决了S3车型拖曳臂多连杆后独立悬架后桥总成装配困难问题。
关键词:工艺工装多连杆后独立悬架一、S3后悬架介绍:S3车型属于前置前驱,城市SUV车型,后悬架采用拖曳臂多连杆独立式,弹簧与减震器分开布置,其优点相比双连杆麦弗逊式的量产车而言,拖曳臂的承重能力大,能够满足SUV越野车需要的承载力及抗冲击载荷;多连杆可以使得车轮在跳动过程中保证更加精准的定位,有效的保证了轮胎的抓地力和良好的接地性能,减少了轮胎的磨损,S3后轮上跳行程可以达到130mm而下跳行程可以达到90mm;弹簧与减震器分开布置,有效的避免了麦弗逊式悬架对减震器侧向冲击大的缺点,延长了减震器的使用寿命。
二、 S3后悬架总成特点:S3后悬架总成由后横梁、左右上下横拉杆总成、后轴总成、后悬螺旋弹簧、减震器、调节套筒、偏心螺母、缓冲垫组成,见图示。
此悬挂总成的特点是占有空间大,后轴总成质量重、结构不规则,弹簧与减震器分开布置,后轴总成前端与车身连接由调节套筒与偏心螺母组成,配合精度要求高。
因此,S3后悬架总成的装配工艺以及AGV小车的工装设计难度较大。
三、 装配工艺的研究在样车试制阶段,我们重点研究装配工艺问题,经过22台样车的试制研究,后悬挂总成的装配工艺主要有两种方案:第一种方案:分装后悬挂横梁、横向拉杆、后轴总成→固定后悬挂横梁、安装调节套筒、凸轮螺母→下降AGV小车安装后悬弹簧→压缩弹簧连接后减震器与后轴总成后端。
如下图:第二种方案:分装后悬挂横梁、横向拉杆、后轴总成、压缩后悬弹簧→固定后悬挂横梁、安装调节套筒、凸轮螺母、装配后减震器与后轴总成后端。
如下图:第一种装配工艺的优点是,工装相对比较简单,缺点是弹簧的装配、压缩难度大,利用后桥AGV工装压缩弹簧有可能会顶翻车身;第二种装配工艺的优点是,弹簧是在分装时进行压缩的,相对比较容易,缺点是工装比较复杂且对于总装车身吊架的一致性要求较高。
中级轿车多连杆后悬架设计-王昱昕-20070306
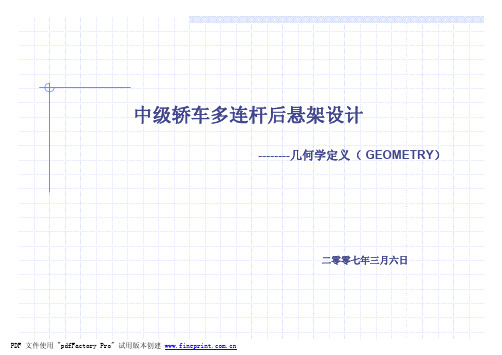
中级轿车多连杆后悬架设计--------几何学定义(GEOMETRY)二零零七年三月六日序言本文档主要从整车总布置角度出发,在总体概念设计阶段进行悬架的选型、硬点、几何定义设计,从而确定悬架各相关部件的详细结构设计边界和输入信息。
拖曳臂(TRAILING ARM)后悬架优点:•沿Y和Z方向的尺寸较小,因此对于后部车厢布置非常有利,能有较好的空间利用率(尤其是轮罩之间的宽度较大)和容易布置备胎和油箱。
•悬架和车身容易装配•悬架结构简单: 零部件少、容易分装•由于没有衬套,滞后性较小•容易保护后驱Compatibility with traction缺点:•在沿着车身与拖曳臂的旋转轴,拖曳臂的长度和宽度有比较大的杠杆比,因此当存在侧向载荷时,有不利的前束。
•在车身的横向翻转时有不利的车轮外倾角(如果有一个比较合适的悬转轴,有可能纠正外倾角,但这样会影响轮罩之间的宽度。
)•不好的调整潜能: 所有的几何特征和相应变形参数都是相关联的。
•由于缺少衬套,不能进行有效的衰减震动。
扭曲梁(TWIST AXLE)后悬架优点:•悬架和车身容易装配•悬架结构简单: 零部件少、容易分装•垂直尺寸较小•水平方向尺寸较小,有利于布置备胎和油箱•在车轮上下跳动不同时,可以进行自动调整车轮外倾角•当车身有横向倾斜时,可以进行前束自动调整•有好的操纵性能,尤其是在光滑路面•当存在障碍物时,有增大轮距的能力•如果设计要求拉焊,有比较大的抗误操作强度缺点:•对横向和纵向的梁的拉焊工艺有比较严格的质量要求•不利于进行驱动•对车辆动态最小化比较敏感–轴上的满载变化Skoda Fabia多连杆悬架具有下列优点:具有良好的操纵稳定性和平顺性,这一良好的潜在性能是由下列主要的几何特性所决定:当存在横向载荷时将自动纠正(Toe-in recovery )当存在纵向载荷时将自动纠正(Toe-in recovery )•在车轮跳动行程中外倾角自动纠正(Camber recovery )当障碍物时,轮当•与后轮驱动有很好的兼容性当后轮驱动时,有好的转向矩控制多连杆通常有下列缺点•有较多的零部件,加工制造复杂•调教实验比较复杂,而且与其他车型共用平台适应性研究比较复杂•对悬架几何参数和弹性元件特性有较高的敏感性•承载能力和悬架重量比值不合理(需要副车架)•误操纵容易损坏•悬架整体尺寸较大,降低后部车厢的空间利用率,影响后底板布置•在欧美市场工业制造有较高的成本Only one archetype is adopted by all makers: a longitudinal arm guided by transverse links.多连杆(MULTILINK )后悬架THREE-LINK: AUDI A3–NEW GOLF前束将自动纠正(Toe-in recovery )大多数多连杆独立后悬架都只是某种传统悬架的变体,最大的改进应该就在于toe control arm。
对轿车副车架设计与优化的研究洪磊

对轿车副车架设计与优化的研究洪磊发布时间:2023-05-31T11:36:09.668Z 来源:《中国电业与能源》2023年6期作者:洪磊[导读] 目前,轿车副车架设计质量提升,受到行业内关注。
本文将针对轿车载荷情况和典型工况设计情况,对轿车副车架设计开展优化,设计优化中应用三维CAD软件,提高设计质量。
最终完成构件的强度计算,借此分析优化设计后的轿车副车架优势。
研究发现,通过优化设计后的副车架可通过减小板材厚度的方式,实现车架减重的效果,进而提升轿车的整体性能。
本文关于轿车副车架性能优化的研究,可供其他同行工作参考。
宁波汇众汽车车桥制造有限公司 315033摘要:目前,轿车副车架设计质量提升,受到行业内关注。
本文将针对轿车载荷情况和典型工况设计情况,对轿车副车架设计开展优化,设计优化中应用三维CAD软件,提高设计质量。
最终完成构件的强度计算,借此分析优化设计后的轿车副车架优势。
研究发现,通过优化设计后的副车架可通过减小板材厚度的方式,实现车架减重的效果,进而提升轿车的整体性能。
本文关于轿车副车架性能优化的研究,可供其他同行工作参考。
关键词:副车架;优化设计;轿车引言:研究发现,汽车底盘性能很难兼顾舒适性、操控性,两者是相互矛盾的。
针对悬挂系统的设计,设计者会选用一些复杂结构来尽量保障操控性和底盘舒适性的平衡,而轿车副车架发挥的就是这方面的作用。
简单地说,副车架的作用显著,可看作前后车桥的骨架,属于轿车的重要构成。
传统副车架设计中应用的是承载式车身,这种方式会影响操作性能,随着副车架设计的完善,悬挂系统结构发生了改变,由散件变成了总成,操作中稍作调校便可实现良好匹配的效果。
基于这种结构的副车架设计,除了方便和优越性要得到保障以外,还要兼顾舒适性和悬挂刚度等具体需求。
1副车架的作用原理对于副车架来说,在设计中需满足性能需求,副车架的突出作用是控制路面震动的传入,借此增加行车的舒适性。
同时,借助副车架的设计,还可以强化悬挂系统连接刚度,从而提升安全性。
基于福特C1平台的E型多连杆悬架结构分析
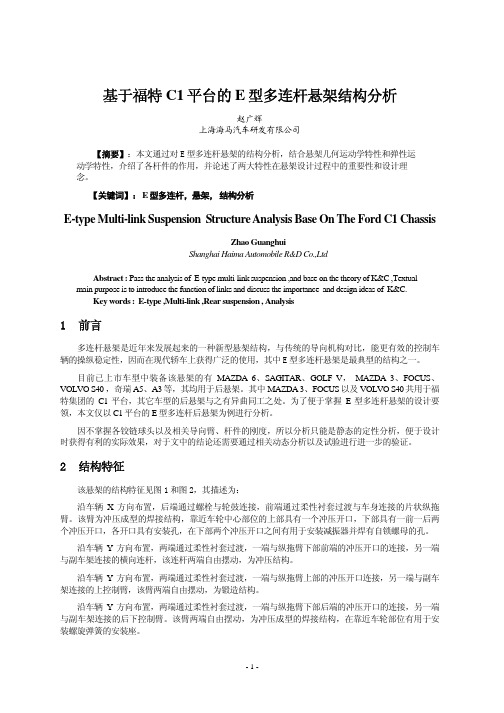
基于福特C1平台的E型多连杆悬架结构分析赵广辉上海海马汽车研发有限公司【摘要】:本文通过对E型多连杆悬架的结构分析,结合悬架几何运动学特性和弹性运动学特性,介绍了各杆件的作用,并论述了两大特性在悬架设计过程中的重要性和设计理念。
【关键词】: E型多连杆,悬架,结构分析E-type Multi-link Suspension Structure Analysis Base On The Ford C1 ChassisZhao GuanghuiShanghai Haima Automobile R&D Co.,LtdAbstract : Pass the analysis of E-type multi-link suspension ,and base on the theory of K&C ,Textual main purpose is to introduce the function of links and discuss the importance and design ideas of K&C.Key words : E-type ,Multi-link ,Rear suspension , Analysis1前言多连杆悬架是近年来发展起来的一种新型悬架结构,与传统的导向机构对比,能更有效的控制车辆的操纵稳定性,因而在现代轿车上获得广泛的使用,其中E型多连杆悬架是最典型的结构之一。
目前已上市车型中装备该悬架的有MAZDA 6、SAGITAR、GOLF V, MAZDA 3、FOCUS、VOLVO S40 ,奇瑞A5、A3等,其均用于后悬架。
其中MAZDA 3、FOCUS以及VOLVO S40共用于福特集团的C1平台,其它车型的后悬架与之有异曲同工之处。
为了便于掌握E型多连杆悬架的设计要领,本文仅以C1平台的E型多连杆后悬架为例进行分析。
因不掌握各铰链球头以及相关导向臂、杆件的刚度,所以分析只能是静态的定性分析,便于设计时获得有利的实际效果,对于文中的结论还需要通过相关动态分析以及试验进行进一步的验证。
006-基于MSC.ADAMS的多连杆式后悬架的优化分析
effects on kinematic performance of vehicle suspension. Based on the theory of multi-body dynamics , a multi-body dynamics model of a Multi-link suspension is built by using ADAMS/Car.And applying the ADAMS/Insight,the kinematics analysis of the suspension is carried out. Through the parameter optimization design using ADAMS/Insight, the optimized parameters for suspension structure is obtained. Then the kinematic performance of the vehicle suspension has been largely improved.
图 7 悬架刚度变化曲线
5、结论
1 )将 ADAMS / Car 和 ADAMS / Insight 综合使用可以快速高效地对悬架 进行运动学分析和优化设计,以改善汽车的操纵稳定性、行驶安全性和乘坐 舒适性。 2 )运用 ADAMS/Insight 模块,通过对模型的硬点坐标进行多次调整, 仿真同一悬架系统的不同动态特性, 可以对模型的某项或是多项性能指标进 行参数优化。 3 )通过悬架系统运动学仿真,可以分析各参数对悬架系统动态性能的 影响,验证并预测评估汽车动态性能,并可对影响汽车动态性能的不合理的 结构参数进行优化,改善悬架系统性能,从而可以达到减少重复试制物理样 机,缩短开发周期, 提高设计质量,降低实际 情况, 考虑各个橡胶衬套的弹性作用对车轮 定位参数与车轮跳动量之间关系的影响,上下横臂、连杆及纵摆臂与车身之 间连接都采用弹性元件 Bushing 连接。 在 ADAMS/Car 中建立的某 A 级车的多 连杆式悬架如图 1 所示。
多连杆后悬架K&C性能的一种优化分析方法-刘红领
经验作为支撑;其二,影响K&C性能的因素比较多,而且很多K&C性能指标之间又相互制约, 依赖工程师的手工调整,很难使所有的性能指标达到一个比较理想的平衡状态,而且花费的 时间比较长。采用专业化的工具,建立自动化的仿真流程,减少人为因素的限制,是解决上 述问题的一个重要途径。通过第三方优化工具Optimus,集成动力学仿真软件ADAMS/Car,可 以搭建出自动化的优化流程;然后采用适当的优化算法来寻找悬架硬点位置和衬套刚度参数 的最佳匹配,并统筹兼顾各个K&C性能指标的要求,就可以在比较短的时间内将整车操控性能 调整到一个比较理想的状态。 奇瑞某车型 K&C 试验结果显示,在侧向受载、制动等工况下,后悬架某些性能指标与竞 争车相比存在一定的差距,影响了整车的操控性,因此,需要对这些性能指标进行优化改进。 为了在最短的时间内实现性能的显著提升,减少调校的时间,保证研发进度,本文采用上面 介绍的方法,开展下列的工作:首先进行 K&C 仿真分析与试验的对比,验证了仿真模型与实 际样车的一致性;然后通过田口法对悬架硬点坐标以及衬套刚度进行筛选,挑选出敏感参数 作为优化分析的设计变量;接着运用适当的优化算法对 K&C 性能进行优化分析,结合调校样 件的实际状况,给出适当的解决方案,并在样车上实施;最后进行 K&C 试验验证,与优化前 相比相关性能指标显著提高,证明了该方法的可行性。
[4] [3]
随着数值计算技术的发展,在过去的几十年中,优化算法从传统算法发展到了智能算法, 比如模拟退火算法、神经网络算法、遗传算法等,这些算法在解决某些优化问题的时候非常 有帮助。本文的优化分析采用的自适应进化算法同遗传算法类似,但有一个很大的差别。传 统的遗传算法首先需要对种群的个体进行编码,然后对编码后的问题进行迭代进化,而自适 应进化算法直接在真实向量的基础上,模仿生物的杂交、突变与选择,从而实现迭代进化。 该算法是基于具有 个设计的随机种群的一种多重组合方法,选择一组具有较好适应度的μ 个父代 x p ,通过交叉、变异产生 个后代。 按照式(1)对每个设计进行独立变异:
基于多目标约束的多连杆悬架优化设计
第27卷第2期2019年6月山东交通学院学报JOURNALOFSHANDONGJTAOTONGUNTVERSTTYVol.27No.2Jun.2019DOT10.3969/j.issn.1672-0032.2019.02.002基于多目标约束的多连杆悬架优化设计张鹏,王洪新,曹昌勇(皖西学院机械与车辆工程学院,安徽六安237012)摘要:多连杆悬架的运动学特性与柔性特性(kinematic&compliance,K&C)是整车操控平顺性的重要组成部分,以正在对标开发的多连杆悬架为例,分析悬架硬点坐标与衬套刚度对车辆K&C主要特性参数的影响程度,并以车轮前束角、车轮外倾角、车辆纵向位移和侧向位移等K&C的主要特性参数满足设计要求为约束条件,通过调整悬架硬点坐标和衬套刚度,实现多连杆悬架的优化#研究表明:优化后的悬架双轮平行跳动时车轮前束角变化、车辆侧倾时前束角变化、悬架侧倾中心高度和纵向力与侧向力作用下的轮心位移变化都能够满足设计要求#关键词:多连杆悬架;多目标约束;悬架硬点;衬套刚度;K&C特性参数;优化中图分类号:U463.33文献标志码:A文章编号:1672-0032(2019)02-0009-08引用格式:张鹏,王洪新,曹昌5.基于多目标约束的多连杆悬架优化设计[J].山东交通学院学报,2019,27(2):9-16.ZHANG Peng,WANG Honyxin,CAO Changyong.Optimized design of multi-link suspension based on multi-objective restrictions[J].Journal of Shandong Jiaotong University,2019,27(2):9-16.0引言随着汽车操纵稳定性和舒适性要求的不断提高,多连杆悬架作为车辆的后悬架被广泛采用。
FSAE电动赛车多连杆式后悬架结构设计与分析中期报告
1)本毕业设计对FSAE赛车后悬架的结构及特点进行比较,综合比对选取适合的后悬架类型;根据赛车参数,进行了大量的计算,根据数据确立了后悬架的尺寸,材料,以及悬架部件的选取,
2)然后利用proe建立FSAE赛车后悬架的三维机构仿真模型;将三维模型导入有限元软件ANSYS中,进行静力学计算.
中期报告
系名
专业
学生姓名
班级
学号
论文(设计)题目:
FSAE电动赛车多连杆式后悬架结构设计与分析
本人在该论文(Βιβλιοθήκη 计)中具体应完成的工作:1.根据赛车参数,进行了大量的计算,根据数据确立了后悬架的尺寸,材料
后利用proe建立FSAE赛车后悬架的三维机构仿真模型;将三维模型导入有限元软件ANSYS中,进行静力学计算。
然后对推杆划分网格,考虑推杆座,球饺接座,安装衬套和推杆的连接因此使用自动网格工具和设置网格大小。
再次对推杆进行约束。在施加约束时,由于没有找好约束点,ansys分析后的结果与现实中的位移不符,且应力也不相同,因此在施加约束这一过程中,存在问题,正在不断实验中。
中期报告
3.指导教师对该学生前期研究工作的评价(是否同意继续研究工作)
3)对后悬架下控制臂的加速工况,转弯工况的应变和应力进行分析,并进行模态分析,判断下控制臂的结构和材料是否满足设计要求。
中期报告
2.目前存在的问题,下一步的主要研究任务,具体设想与安排(要详细内容)
控制臂主要由四部分组成,推杆座,球饺接座,安装衬套和推杆。对推杆进行有限元分析时,首先定义推杆的料厚5mm.材料弹性模量 MPa。泊松比 。密度; 。
指导教师亲笔签字:
年月日
- 1、下载文档前请自行甄别文档内容的完整性,平台不提供额外的编辑、内容补充、找答案等附加服务。
- 2、"仅部分预览"的文档,不可在线预览部分如存在完整性等问题,可反馈申请退款(可完整预览的文档不适用该条件!)。
- 3、如文档侵犯您的权益,请联系客服反馈,我们会尽快为您处理(人工客服工作时间:9:00-18:30)。
・18・
万方数据
构造了L:,。(3 4425824622)矩阵作为试验设计矩阵。 部分设计矩阵如表3所示。
表3试验设计矩阵
序号 前安装点衬套 Y、Y方向刚度
1 2 128 256
表4部分样本试验设计结果
序号
重量/kg
l 12.199 2 20.3lO
1阶模态/Hz
127.35l
图2参数化几何模型
P3X方向低频动刚度 一0 3
图3所示为设计参数对于某输出指标的贡献
2试验设计及数据挖掘
2.1试验设计样本计算 采用Adams和Radioss软件将256个样本进 行DOE计算,获得各样本的性能指标结果,表4所 示为部分样本的DOE计算结果。
上海汽车2014.07
率结果。从中可以看出,后横梁的位置对于该指 标的贡献率超过50%,是该指标的主要影响因素, 更改后横梁位置是提高该指标水平最有效的途 径,中间两个横梁总体的累积贡献率超过90%,其 它设计变量对于该指标的影响很小,这对后期设 计优化重点具有极其重要的参考价值。
37 09 17
静刚度/
(kN/mm)
弹簧控制臂A连接点y,J+向 弹簧控制臂A连接点Z方向
72 1l
图1
初始后悬架几何模型
动刚度/ (kN/mm)
车身前连接点X方向低频 车身前连接点Ⅳ方向高频
5
1
64.3
刚度包括副车架与各控制臂以及横向稳定杆相连 的8个点的x、)’、。3个方向的静刚度;动刚度包括 副车架与各控制臂、横向稳定杆以及与车身连接 共12个点的3个方向低频及中频动刚度;模态包 括副车架前6阶自由模态;p/f包括4个车轮激励 下的车内声压响应曲线中20~50 Hz的3个峰值; K/C指标包括同向侧向力作用下的轮心侧向位移
1 2
后横梁上表面焊缝位置
12 13
尺寸 尺寸
后横梁截面高度 前横梁截面宽度
35 50
70 70
90 lOO
14 16
位置 位置
前横梁垂向位置
侧边粱下表面位置
472 一5
475 0
546 5
23
厚度
厚度
1号板厚度
1.8;2 0;2.2;2
4;
2.5;2.6;2.8;3.0 1.8;2 0;2 2;2 4;
・19・
万方数据
分析发现,该模型能够满足后续进行优化设计的
』再瞵梁位置_●■———一50 J・i横梁截嘶高度_15
48%
20%
精度要求。
表6
指标
前横粱z乃川位置高度-1
}
r
3 71% 37%
近似模型最大与最小误差对比
+Y方向
8.89 6.86 29.04
}ju墩粱截丽高t_《{:_12
2I;板厚度ll
3
后悬近似模型及误差分析
后悬设计工况中包括各种复杂的线性和非线
性计算指标,需要采用一种合理的算法来搭建近 似模型以保证优化设计具有高精度。通过研究分 析,采用基于方差最小的无偏估计法建立克里格 近似模型。表6列出了采用Cross—validation方法 对于所有114个输出指标中误差最小和最大两个 指标的误差对比结果。综合所有输出指标的误差 求。
图3
设计变量对于某指标的贡献率结果
图4所示为设计变量相对该指标的主效应结 果。从主效应图中可以看出,该指标随贡献量最 大的变量即后横梁位置变化呈现下降趋势,而且 有较为明显的2阶非线性关系。在后横梁位置变 化区间中段位置该指标的变化最为明显,在两端 区域,该指标随后横梁的位置变化不显著。
52 103
多连杆后悬副车架结构及衬套优化设计米
姜 欣唐晓峰俞斌张猛
(泛亚汽车技术中心有限公司,上海201201)
【摘要】
结合某车型开发工作,针对该车型所采用的新型四连杆后悬架系统,采用先进的多学科优化技
术对后桥结构及衬套刚度进行全面优化设计,并对遗传算法、模拟退火及混合多梯度探测等多目标优化算法在 该系统中的应用进行了详细的对比论证。
收稿日期:2014—01一叭 +为上海市汽车工程学会201 3年优秀论文。
上海汽车2014.07
・17・
万方数据
型相关数据得到了所有设计变量的量化区间,部 分设计变量如表2所示:
表1
重量/kg
初始模型性能计算结果
17.6
模态/Hz
.r阶
、+1阶
195.46 301 58
弹簧控制臂A连接点.、方向
7
【Abstract】Combined
nique.We
get
an
with the development process of
rear
a
vehicle,the real-cradle
structure
and
bushing stiffness in the new 4-1ink
suspension is optimized by the advanced optimization tech—
上海汽车2014.07
优化设计
有了高精度的近似模型,便可以在近似模型
上进行多目标优化设计来达到各设计指标的要
・20・
万方数据
表7不同优化算法优化结果对比
算法
NSGA II ASA HMGE
重量/kg
17.5l 16.40 16.40
DPDSl 6.84 6.52 6.52
DPDs2 6.60 6.24 6.24
后桥几何模型。对于四连杆后悬架,采用了常用 的井字梁副车架结构形式。初始数模如图1所 不。 1.1优化设计工况定义 与后悬架相关的车辆指标包括重量、空间、结 构耐久、车辆动力学、NVH以及安全性几个方面。 从该车型的实际开发角度考虑,在前期设计阶段 与后副车架结构及衬套相关的工况要求有:副车 架重量、结构静刚度、模态、动刚度、整车声压频率 响应函数(p/f)以及部分后悬K/C指标。其中静
197
209
2 730
3 510
5 070
2 730
某点X方向静刚度/(kN/mm)
5.943
9.405
后横梁底部
焊缝位置
0.25
0 50
0.75
O.25
悬架跳动外倾角变化K/C
28.741
28.741
后横梁z 方向位置
O O
45.O
O.0
15.O
2.2试验设计数据挖掘 数据挖掘可以清晰呈现复杂系统的整体结 构,通过数据挖掘可以获得所有设计参数和输出 指标之间的关系,评估各设计变量对于输出指标
义
在悬架硬点及布置策略确定之后,建立初始
高,应用优化设计进行产品开发成为业界公认的 最科学有效的开发方法,全球各汽车公司也越来 越广泛地应用优化设计进行车辆的早期设计开 发。底盘系统作为国内各大整车厂以及研发机构 的开发重点和难点,如何用优化设计的方法完成 新车型悬架等关键系统的早期开发,是亟待解决 的问题之一。本文所完成的主要工作是在某车型 的多连杆后悬架开发过程中,根据硬点及总布置 要求,通过科学的试验设计、近似模型以及多目标 优化开发过程进行优化设计,开发满足前期车辆 动力学、结构、NVH、重量等多学科要求的最优化 后副车架结构以及悬架各级衬套刚度,为后续整
表5部分指标的相关性分析
P,I P,Y
项目
重量
l阶 模态
2阶 模态 方向 方向
P.J方 P.Y方
吖方
P31方
向高频 向低频 向高频 向低频
静刚度 静刚度 动刚度 动刚度 动刚度 动刚度 重量 I阶模态 2阶模态 PIX方向静刚度 P3X方向静刚度 P。J方向高频动刚度 P.Y方向低频动刚度 P、I方向高频动刚度
155
206 257
样本编号
78E+00 O%
^j墩梁宽度
20%40% 60%, 8【)% 100%
图5某输出指标的近似模型误差分析结果
图4设计变量对于某指标的主效应分析结果
通过Isight软件将近似模型封装成可预测数 学模型,便可在设计区间内任意调整设计变量取 值并立即得到精确的输出指标。这极大提高了设 计方案选择和评估的效率。图6所示为Isjght集 成环境下的可预测数学模型: 4
multi—objective
optimi・
this system’S application.
【关键词】
多连杆悬架后副车架汽车优化设计
doi:10.3969/j.issn.1007-4554.2014.07.05 车开发提供坚实可靠的架构基础。 0
引言
1 随着优化设计技术及计算机水平的不断提
后悬优化设计参数及优化工况定
24
2号板厚度
2.5;2.6;2.8;3.0
31 36
衬套刚度 前安装点Y、l,方向刚度 衬套刚度 A衬套Y方向刚度
2 730 168
3 900 240
5 070 312
1.4构造试验设计矩阵 为了满足55个不同水平的设计变量以及最 小化DOE矩阵样本的要求,同时又要保证后期近 似模型的精度,通过对不同试验设计算法的深入 研究和软件的自主开发,本文应用了复杂正交试 验软件“OATS”进行详细计算与分析,针对该问题
DPDS3 6.09 7.54 7.54
DPDs4 5.23 4.98 4.98
从表7可以看出,通过模拟退火和HMGE算 法获得的优化结果完全一致,重量可达16.4
图6输出指标预测模型
kg,
相对于初始设计方案减轻9.3%,而利用第2代遗 传算法获得的优化结果重量为17.5l kg,相比原 始设计方案几乎未减重。优化后的p/f曲线如图 8所示,其中虚线为初始设计方案,细实线为ASA 算法优化结果,粗实线和加深实线分别为HMGE