QSY1592-2013油气管道管体修复技术规范(最终) (1)
油管加工修复汇报隆基
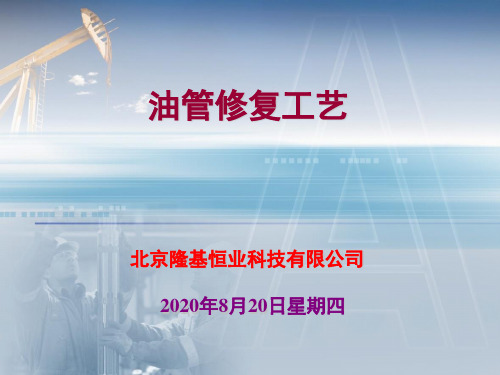
报废油管 成品油管
35
避免经 常震动
避免与其他 油管混合
每类产品设置单 独标识牌
BGT1类油套管储存期间, 必须要注意以下几点
避免潮湿环境储存
避免储 存变形
避免磕伤 、碰伤
成品储存
不能直接堆放在地面、铁轨、钢板或混凝土地板上,底层离地面或地板 应至少保持2英尺的距离。
每一层下面应至少放3排支撑物,避免油管中间下陷,引起水在油套管内 积存。油套堆放高度不应超过10英尺。
注:拧扣结束后选择相应壁厚通径规对管 体拧接钳牙夹持部位(接箍端至管体1米 处)进行通径检验,检查有无夹扁现象。 通径不过的油管需锯头重新加工。
28
为保证螺纹加工质量,对加 工的BGT特扣进行第三方气 密封检测,采用干燥氮气, 99MPa情况下,保压15分 钟无泄漏。确保上井使用的 油管无质量事故碱、清洗工序
使用高压清洗机对BGT1油管进行内、外壁进行除油清洗中,清洗压力调整 到4MPa。要求达到油管内壁无油污、清洁干净。对内壁稠油的油管进热洁 炉热洁。保证油管内壁无油污。
11
内外壁除锈工序
在内壁除锈中,要求除锈杆从公端进入管体内壁进行除锈,同时为了保证 母端护丝不易脱落,必须调整通径杆旋转电机以反转方式进行内壁除锈 (逆时针旋转)。要求除完锈的油管见管体本色,管体表面无氧化锈皮。
三
成品入库及储存
四 各工序执行标准
3
一 油管修复操作规范
4
油管修复操作规范
BGT1油管钢级分选 全长通径检验 BGT1油管切头 BGT1油管收口 BGT1螺纹加工 BGT1螺纹检验 抛丸喷砂
通径不过报废 螺纹损伤
接箍拧接 管端通径检验 钳牙印打磨 测长、清吹 护丝、喷漆、喷标 成品检验入库
2013年石化标准

SH/T3020-2013石油化工仪表供气设计规范SH/T3031-2013石油化工逆流式机械通风冷却塔结构设计规范SH/T3060-2013石油化工企业供电系统设计规范SH/T3071-2013石油化工电气设备抗震鉴定标准SH/T3117-2013石油化工设计热力工质消耗量计算方法SH/T3122-2013炼油装置工艺管道流程设计规范SH/T3130-2013石油化工建筑抗震鉴定标准SH/T3401-2013石油化工钢制管法兰用非金属平垫片SH/T3402-2013石油化工钢制管法兰用聚四氟乙烯包覆垫片SH/T3403-2013石油化工钢制管法兰用金属环垫SH/T3404-2013石油化工钢制管法兰用紧固件SH/T3406-2013石油化工钢制管法兰SH/T3407-2013石油化工钢制管法兰用缠绕式垫片SH/T3517-2013石油化工钢制管道工程施工技术规程SH3518-2013石油化工阀门检验与管理规程SH/T3521-2013石油化工仪表工程施工技术规程SH/T3551-2013石油化工仪表工程施工质量验收规范SH3009-2013石油化工可燃性气体排放系统设计规范SH/T3010-2013石油化工设备和管道绝热工程设计规范SH/T3021-2013石油化工仪表及管道隔离和吹洗设计规范SH/T3092-2013石油化工分散控制系统设计规范SH/T3104-2013石油化工仪表安装设计规范SH/T3126-2013石油化工仪表及管道伴热和绝热设计规范SH/T3132-2013石油化工钢筋混凝土水池结构设计规范SH3137-2013石油化工钢结构防火保护技术规范SH/T3141-2013石油化工用往复泵工程技术规范SH/T3151-2013石油化工转子泵工程技术规范SH/T3175-2013固体工业硫磺储存输送设计规范SH/T3519-2013乙烯装置离心压缩机机组施工及验收规范SH/T3533-2013石油化工给水排水管道工程施工及验收规范SH/T3553-2013石油化工汽轮机施工及验收规范SH/T3554-2013石油化工钢制管道焊接热处理规范SH/T3613-2013石油化工非金属管道工程施工技术规程SH/T3017-2013石油化工生产建筑设计规范SH3076-2013石油化工建筑物结构设计规范SH3094-2013 石油化工厂区雨水明沟设计规范SH3173-2013石油化工污水再生利用设计规范SH/T3174-2013石油化工在线分析仪系统设计规范SH3552-2013石油化工电气工程施工质量验收规范SH3612-2013石油化工电气工程施工技术规程SH/T3080-2013石油化工横流式机械通风冷却塔结构设计规范SH/T3100-2013石油化工工程测量规范。
汽水管道检修规程
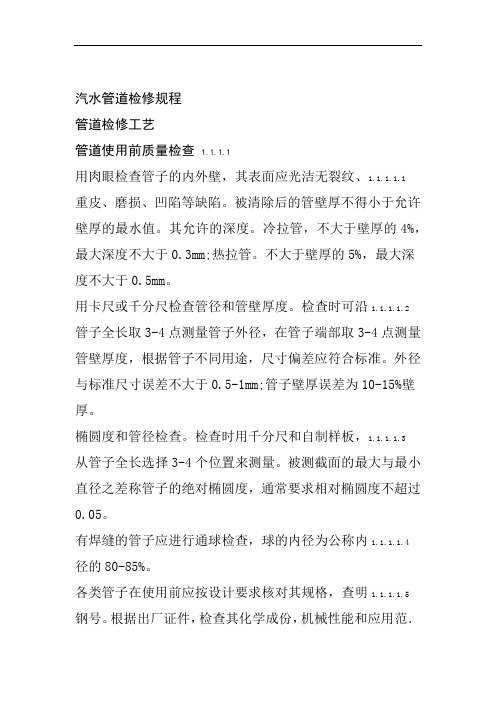
汽水管道检修规程管道检修工艺管道使用前质量检查 1.1.1.1用肉眼检查管子的内外壁,其表面应光洁无裂纹、1.1.1.1.1重皮、磨损、凹陷等缺陷。
被清除后的管壁厚不得小于允许壁厚的最水值。
其允许的深度。
冷拉管,不大于壁厚的4%,最大深度不大于0.3mm;热拉管。
不大于壁厚的5%,最大深度不大于0.5mm。
用卡尺或千分尺检查管径和管壁厚度。
检查时可沿1.1.1.1.2 管子全长取3-4点测量管子外径,在管子端部取3-4点测量管壁厚度,根据管子不同用途,尺寸偏差应符合标准。
外径与标准尺寸误差不大于0.5-1mm;管子壁厚误差为10-15%壁厚。
椭圆度和管径检查。
检查时用千分尺和自制样板,1.1.1.1.3从管子全长选择3-4个位置来测量。
被测截面的最大与最小直径之差称管子的绝对椭圆度,通常要求相对椭圆度不超过0.05。
有焊缝的管子应进行通球检查,球的内径为公称内1.1.1.1.4 径的80-85%。
各类管子在使用前应按设计要求核对其规格,查明1.1.1.1.5 钢号。
根据出厂证件,检查其化学成份,机械性能和应用范.围。
对合金钢要进行光谱分析,检查化学成份是否与钢号相符合。
对于要求严格的部件,对管材还应作压偏试验和水压试验。
管道焊接 1.1.1.2管子接口距离弯管弯曲起点不得小于管子外径,且1.1.1.2.1 不小于100mm。
管子接口不应布置在支吊架上,至少应离开支吊架1.1.1.2.2 边缘50mm。
管子两个接口间距不得小于管子外径,且不小于1.1.1.2.3150mm。
对需焊后热处理的焊口,距支吊架边缘不得小于焊缝宽度的5倍,且应不小于100mm。
管子接口应避开,疏放水及仪表管等的开孔位置,1.1.1.2.4一般距开孔边缘不得小于50mm,且不得小于孔径。
管道在穿过隔墙、楼板时,位于墙、楼板内的管段1.1.1.2.5 不得有接口。
高压管子焊缝不允许布置在管子弯曲部分。
1.1.1.2.6对接焊缝中心线距管子弯曲起点或汽包联箱的外壁1.1.1.2.7 以及支吊架边缘,至少距离70mm。
城镇燃气管道非开挖修复更新工程

城镇燃气管道非开挖修复更新工程1范围本规程规定了城镇燃气管道非开挖修复更新工程的设计、插入法、工厂预制成型折叠管内衬法、现场成型折叠管内衬法、缩径内衬法、静压裂管法、翻转内衬法、试验与验收、修复更新后的管道接支管和抢修。
本规程适用于采用插入法、折叠管内衬法、缩径内衬法、静压裂管法和翻转内衬法对在役燃气管道进行沿线修复更新的工程。
本规程不适用于新建埋地城镇燃气管道的非开挖施工、在役管道的局部修补和架空燃气管道的修复更新工程。
2规范性引用文件下列文件对于本文件的应用是必不可少的。
凡是注日期的引用文件,仅注日期的版本适用于本文件。
凡是不注日期的引用文件,其最新版本(包括所有的修改单)适用于本文件。
GB/T 3512《硫化橡胶或热塑性橡胶热空气加速老化和耐热试验》GB/T 3923.1《纺织品织物拉伸性能第1部分:断裂强力和断裂伸长率的测定(条样法)》GB/T 8806《塑料管道系统塑料部件尺寸的测定》GB/T 11547《塑料耐液体化学试剂性能的测定》GB/T 15558.1-2015《燃气用埋地聚乙烯(PE)管道系统第1部分:管材》GB/T 15558.2《燃气用埋地聚乙烯(PE)管道系统第2部分:管件》GB/T 23658《弹性体密封圈输送气体燃料和烃类液体的管道和配件用密封圈的材料要求》GB 50028《城镇燃气设计规范》CJJ 33《城镇燃气输配工程施工及验收规范》CJJ 51《城镇燃气设施运行、维护和抢修安全技术规程》CJJ 63《聚乙烯燃气管道工程技术标准》CJ/T 358《非开挖工程用聚乙烯管》HG/T 20606《钢制管法兰用非金属平垫片(PN系列)》3术语和定义下列术语和定义适用于本文件。
3.1管道非开挖修复更新trenchless rehabilitation and renewal of pipeline采用非开挖施工技术在在役管道原位对管道进行沿线缺陷修复,或者原位更新在役管道以改善其性台P 能匕。
油气输送管道凹坑修复判定准则
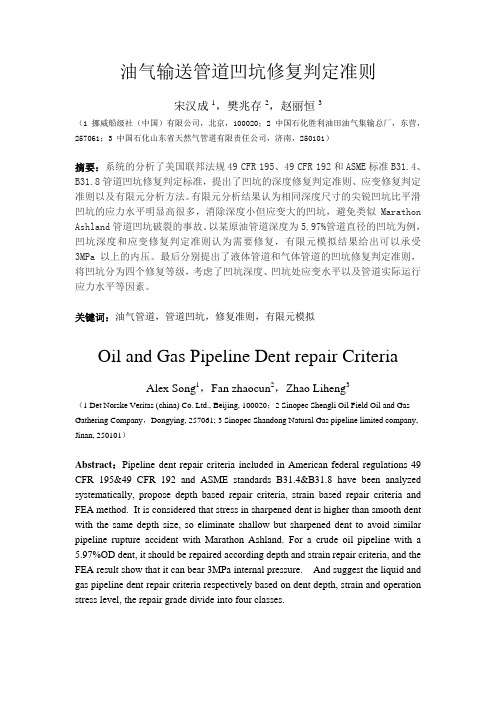
3 分别为公式(1)-(3)。
1 t
1 1 1 2 R0 R1 1 t 2 2 R2
(1) (2)
3 2 L
其中, t 为管道壁厚,mm; d 为凹坑深度,%OD; L 为凹坑长度,mm。 则凹坑处管道内表面应变 i 和外表面应变为公式(4)-(5)。
油气输送管道凹坑修复判定准则
宋汉成 1,樊兆存 2,赵丽恒 3
(1 挪威船级社(中国)有限公司,北京,100020;2 中国石化胜利油田油气集输总厂,东营, 257061;3 中国石化山东省天然气管道有限责任公司,济南,250101)
摘要:系统的分析了美国联邦法规 49 CFR 195、49 CFR 192 和 ASME 标准 B31.4、 B31.8 管道凹坑修复判定标准,提出了凹坑的深度修复判定准则、应变修复判定 准则以及有限元分析方法。 有限元分析结果认为相同深度尺寸的尖锐凹坑比平滑 凹坑的应力水平明显高很多,消除深度小但应变大的凹坑,避免类似 Marathon Ashland 管道凹坑破裂的事故。 以某原油管道深度为 5.97%管道直径的凹坑为例, 凹坑深度和应变修复判定准则认为需要修复,有限元模拟结果给出可以承受 3MPa 以上的内压。最后分别提出了液体管道和气体管道的凹坑修复判定准则, 将凹坑分为四个修复等级,考虑了凹坑深度、凹坑处应变水平以及管道实际运行 应力水平等因素。 关键词:油气管道,管道凹坑,修复准则,有限元模拟
[4]
图 4 49 CFR 192 凹坑修复判定准则 Figure 4 49 CFR 192 Dent Repair Criteria
图 5 ASME B31.8-2010 凹坑修复判定准则 Figure 5 ASME B31.8-2010 Dent Repair Criteria
油气田埋地管道软管内衬修复技术

5.4 江苏油田污水集输管线软管内衬工程 规格:D273*8,780m,架空敷设,53个弯头 特点:管径大,弯头多
3、技术优选
(1)风送挤涂 埋地管道经清洗合格后将防腐修复材料注入到管道中,采用
风送挤涂工艺推动挤涂球将涂层均匀涂敷到管道内壁,形成连 续的内防腐层。
其优点是施工管径小(DN50)、挤涂长度长(2km)、耐腐 蚀性强。涂层连续、补口点少、可抢维修。
3.3 抗渗透性
(4)穿插工艺 4.1 简介
软管穿插工艺是将HPCH管经过缩径变形(压U)后拉进到待防腐修 复管道内,通过打压复到原始状况,与金属管道紧密贴合,起到隔 离腐蚀介质、防止管道腐蚀、增强管道耐压能力的作用。
4.2 工艺特点 (1)软管本体承压,可对腐蚀穿孔、壁厚减薄管道进行补强, 提高管道耐压等级,也可以抵御外腐蚀穿孔; (2)耐腐蚀性能强,延长管道使用寿命; (3)一次性施工长度2km,能通过6D弯头1-2个。 (4)软管压扁后缠绕,每卷2km左右,运输方便; (5)施工快捷,对于施工环境温度要求不苛刻;施工面积小, 只需要两端开挖,对环境影响较少。
(2)软管翻转(CIPP) Ø 编织软管 Ø 缝制软管
3、技术优选
(3)塑料管穿插 将HDPE塑料管通过变形后穿插到集输管道内,再通过打压使
塑料管复原紧贴在管道内壁形成一管中管的结构。 其优势是耐腐蚀性能强、清洗要求低,其不足是耐温性能差,
不耐芳烃类溶胀,穿插施工时不能过弯头。
3、技术优选
(3)塑料管穿插 Ø 等径压缩 Ø 压U
3、技术优选 (4)技术比选
Ø 风送挤涂:施工长度,过弯头,抗渗性;不耐压。 Ø 塑料管穿插:耐腐蚀性好,抗外压;耐温性低,不能过弯头。 Ø 软管翻转:耐压,抗外压,抗渗;施工距离短。 Ø 软管穿插:本体承压,过弯头;不抗外压。
关于建设部发布2013年新规范的公告
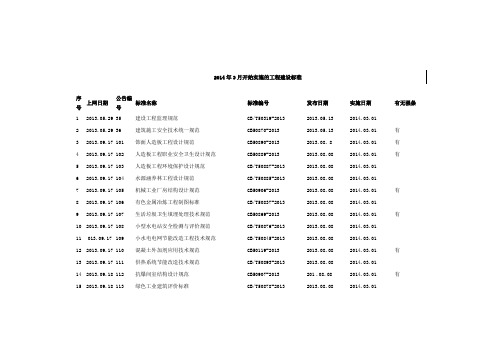
2014年3月开始实施的工程建设标准序号上网日期公告编号标准名称标准编号发布日期实施日期有无强条1 2013.05.29 35 建设工程监理规范GB/T50319-2013 2013.05.13 2014.03.012 2013.05.29 36 建筑施工安全技术统一规范GB50870-2013 2013.05.13 2014.03.01 有3 2013.09.17 101 饰面人造板工程设计规范GB50890-2013 2013.08.8 2014.03.01 有4 2013.09.17 102 人造板工程职业安全卫生设计规范GB50889-2013 2013.08.08 2014.03.01 有5 2013.09.17 103 人造板工程环境保护设计规范GB/T50887-2013 2013.08.08 2014.03.016 2013.09.17 104 水源涵养林工程设计规范GB/T50885-2013 2013.08.08 2014.03.017 2013.09.17 105 机械工业厂房结构设计规范GB50906-2013 2013.08.08 2014.03.01 有8 2013.09.17 106 有色金属冶炼工程制图标准GB/T50837-2013 2013.08.08 2014.03.019 2013.09.17 107 生活垃圾卫生填埋处理技术规范GB50869-2013 2013.08.08 2014.03.01 有10 2013.09.17 108 小型水电站安全检测与评价规范GB/T50876-2013 2013.08.08 2014.03.0111 013.09.17 109 小水电电网节能改造工程技术规范GB/T50845-2013 2013.08.08 2014.03.0112 2013.09.17 110 混凝土外加剂应用技术规范GB50119-2013 2013.08.08 2014.03.01 有13 2013.09.17 111 供热系统节能改造技术规范GB/T50893-2013 2013.08.08 2014.03.0114 2013.09.18 112 抗爆间室结构设计规范GB50907-2013 201.08.08 2014.03.01 有15 2013.09.18 113 绿色工业建筑评价标准GB/T50878-2013 2013.08.08 2014.03.0116 2013.09.18 114 建筑模数协调标准GB/T50002-2013 2013.08.08 2014.03.0117 2013.09.18 115 非织造布设备工程安装与质量验收规范GB/T50904-2013 2013.08.08 2014.03.0118 2013.09.18 116 机械工业工程节设计规范GB50910-2013 2013.08.08 2014.03.01 有19 2013.09.18 117 煤炭工业半地下储仓建筑结构设计规范GB50874-2013 2013.08.08 2014.03.01 有20 2013.09.18 118 组合钢模板技术规范GB/T50214-2013 2013.08.08 2014.03.0121 2013.09.18 119 地铁设计规范GB50157-2013 2013.08.08 2014.03.01 有22 213.09.18 120 核电厂工程气象技术规范GB/T50674-2013 2013.08.08 2014.03.0123 2013.09.18 121 室内混响时间测量规范GB/T50076-2013 2013.08.08 2014.03.0124 2013.09.18 122 火炸药工程设计能耗指标标准GB50767-2013 2013.08.08 2014.03.01 有25 2013.10.11 157 生活垃圾土土工试验技术规程CJJ/T204-2013 2013.9.25 2014.03.0126 2013.10.11 158 城市轨道交通结构安全保护技术规范CJJ/T202-2013 2013.09.25 2014.03.0127 2013.10.11 159 城市居住区热环境设计标准JGJ286-2013 2013.09.25 2014.03.01 有28 2013.10.11 160 城市轨道交通接触轨供电系统技术规范CJJ/T198-2013 2013.09.25 2014.03.0129 2013.10.11 161 直线电轨道交通施工及验收规范CJJ201-2013 2013.09.25 2014.03.01 有30 2013.10.11 162 建设领域信息技术应用基本术语标准JGJ/T313-2013 2013.09.25 2014.03.0131 2013.10.11 176 城市市政综合监管信息系统模式验收CJ/T423-2013 2013.10.09 2014.03.0132 2013.11.11 189 无负压静音管中泵给水设备CJ/T440-2013 2013.10.30 214.03.0133 2013.11.11 190 户用生活污水处理装置CJ/T441-2013 2013.10.30 2014.03.0134 2013.11.11 191 硬泡聚氨酯板薄抹灰外墙外保温系统材料JG/T420-2013 2013.10.30 2014.03.0135 2013.12.23 226 城市公共汽、电车候车亭CJ/T107-2013 2013.12.03 2014.03.0136 2013.12.23 227 建筑排水低噪声硬聚氯乙烯(PVC-U)管材CJ/T442-2013 2013.12.03 2014.03.0137 2013.12.23 228 建筑施工用木工字梁JG/T425-2013 2013.12.03 2014.03.0138 2013.12.31 246 遮阳用膜结构织物JG/T423-2013 2013.12.17 2014.03.0139 2013.12.31 247 建筑遮阳用织物通用技术要求JG/T424-2013 2013.12.17 2014.03.0140 2013.1231 248 抹灰砂浆增塑剂JG/T426-2013 2013.12.17 2014.03.0141 2014.01.23 274 钢框组合竹胶合板模板JG/T428-2014 2014.01.07 2014.03.0142 2014.01.23 275 建筑反射隔热涂料JG/T235-2014 2014.01.07 2014.03.0143 2014.01.23 276 外墙外保温系统耐候性试验方法JG/T429-2014 2014.01.07 2014.03.01 4 2014.01.23 277 住宅卫浴五金配件通用技术要求JG/T427-2014 2014.01.07 2014.03.01 45 2014.01.23 278 免漆饰面门JG/T419-2014 2014.01.07 2014.03.01关于建设部发布2013年新规范的公告现批准《住房保障基础信息数据标准》为行业标准,编号为CJJ/T197-2012,自2013年3月1日起实施。
油气田地面建设工程常用标准规范

《建设工程监理规范》GB/T50319-2013《建设工程项目管理规范》GB/T50326-2006《建筑工程质量验收统一标准》GB/T50300-2013(系列)《石油天然气建设工程施工质量验收规范通则》SY4200-2007(系列)《建设工程文件归档整理规范》GB/T50328-2001现行国家、行业施工验收规范(包括但不限于)GB50254-2014《电气装置安装工程低压电器施工及验收规范》GB50168-2016《电气装置安装工程电缆线路施工及验收规范》GB50169-2016《电气装置安装工程接地装置施工及验收规范》GB50171-2012《电气装置安装工程盘、柜及二次回路接线施工及验收规范》GB50257-2014《电气装置安装工程爆炸和火灾危险环境电气装置施工及验收规范》GB50303-2015《建筑电气工程施工质量验收规范》GB50150-2016《电气装置安装工程电气设备交接试验标准》GB50350-2015《油气集输设计规范》GB/T8163-2013《输送流体用无缝钢管》GB50540-2009《石油天然气站内工艺管道工程施工规范》SY4200-2007《石油天然气工程施工质量验收规范》SY4201-2016《石油天然气工程施工质量验收规范设备安装工程》SY4203-2016《石油天然气工程施工质量验收规范站内工艺管道工程》SY4204-2016《石油天然气工程施工质量验收规范油气田集输管道工程》SY/T4102-2013《阀门的检查与安装规范》SY4103-2006《钢制管道焊接及验收》GB/T12459-2017《钢制对焊管件》SY6444-2010《石油工程建设施工安全规定》SY/T6524-2010《石油工业作业场所劳动防护用具配备要求》GB 50300-2013《建筑工程施工质量验收统一标准》SY/T5257-2012《油气输运用钢制弯管》SY/T0422-2010《油气田技术管道施工技术规范》SY4207-2007《石油天然气建设工程施工质量验收规范管道穿跨越工程》SY4205-2016《石油天然气建设工程施工质量验收规范自动化仪表工程》SY4206-2016《石油天然气建设工程施工质量验收规范电气工程》SY/T0414-2017《钢质管道聚乙烯胶粘带防腐层技术标准》SY6444-2010《石油工程建设施工安全规定》SY/T 6609-2004《环境、健康和安全(EHS)管理体系模式》SY/T6276-2014《石油天然气工业健康、安全与环境管理体系》SY/T0021-2016《油气田和管道工程建设设计规范》SY4025-1993《石油建设工程质量检验评定标准建筑工程》SY6444-2010《石油工程建设施工安全规定》SY/T0043-2006《油气田地面管线和设备涂色规范》GB50242-2016《建筑给水排水及采暖工程施工质量验收规范》SY/T0452-2012《石油天然气金属管道焊接工艺评定》SY/T0315—2013《钢制管道单层熔结环氧粉末外涂层技术规范》GB/T8923—2011《涂装前钢材表面锈蚀等级和除锈等级》SY/T4024—2016《石油建设工程质量检验评定标准通则》SY/T6276-2014《石油天然气工业健康、安全与环境管理体系》SY 1241-2009《动火作业安全管理规范》。
- 1、下载文档前请自行甄别文档内容的完整性,平台不提供额外的编辑、内容补充、找答案等附加服务。
- 2、"仅部分预览"的文档,不可在线预览部分如存在完整性等问题,可反馈申请退款(可完整预览的文档不适用该条件!)。
- 3、如文档侵犯您的权益,请联系客服反馈,我们会尽快为您处理(人工客服工作时间:9:00-18:30)。
永久 修复a 永久 修复 永久 修复a
否l
永久 修复c 永久 修复e
否l
永久 修复
否l
永久 修复 永久修 复b 永久 修复e
临时 修复 否l 否l 否l 否l 否l
永久 修复 永久 修复 永久 修复
否l
否l
永久 修复
2
Q/SY 1592—2013
表1(续)
缺陷类型
打磨 堆焊 补板
A型 套筒
B型 套筒
II
前言
Q/SY 1592—2013
本标准按照GB/T 1.1-2009给出的规则起草。 本标准由中国石油天然气集团公司标准化委员会天然气与管道专业标准化委员会提出并归口。 本标准起草单位:西部管道分公司、天然气与管道分公司、管道分公司、北京天然气管道有限公司、 西气东输管道分公司、天津大学。 本标准主要起草人:郭臣、杨永和、徐震、付立武、蒋金生、胡江锋、项卫东、高强、周永涛、陈 旭、高丽兰、孙震东、代鹏飞、马剑。
5.1 管体缺陷修复原则 .............................................................. 4 5.2 管体泄漏 ...................................................................... 4 5.3 管体外腐蚀 .................................................................... 4 5.4 管体内部缺陷或腐蚀 ............................................................ 5 5.5 管体凿槽或其它金属损失 ........................................................ 5 5.6 管体电弧烧伤、夹渣 ............................................................ 5 5.7 管体凹坑 ...................................................................... 5 5.8 管体硬点 ...................................................................... 6 5.9 管体裂纹 ...................................................................... 6 5.10 管体焊缝缺陷 ................................................................. 6 5.11 管体环焊缝缺陷 ................................................................ 6 5.12 管体皱弯、弯曲缺陷 ............................................................ 7 5.13 管体砂眼、氢致裂纹缺陷 ........................................................ 7 5.14 管体打孔盗油(气)泄漏 ........................................................ 7 6 管体修复作业流程 .................................................................. 7 6.1 作业流程图..........。............................................................7 6.2 管体缺陷评价......................................................................7 6.3 修复方案制定......................................................................8
否l
否l
集中的凹坑
修复i
永久
否l
否l
否l
否l
修复
硬点
否
否
否
永久 永久
否l
裂
<0.4t
修复d 修复e
纹 0.4t≤裂纹
永久
否l
否l
深度<0.8t
修复e
永久
永久
永久
永久
否l
修复e
修复b
修复e
修复e
Q/SY
中国石油天然气集团公司企业标准
Q/SY 1592—2013
油气管道管体修复技术规范
Repair technical specification for oil & gas pipeline
2013 - 10 - 1 发布 中国石油天然气集团公司
2013 - 10 -1 实施 发布
Q/SY 1592—2013
1
Q/SY 1592—2013
3.6 套筒修复 full encirclement steel sleeve repair
利用两个由钢板制成的半圆柱外壳覆盖在管道缺陷外,通过焊接连接在一起,套筒与管壁紧密结合, 协同变形,提高缺陷管体的承压能力。 3.7
复合材料修复 nonmetallic composite repair 利用复合材料修复层的高强度和高模量,通过涂敷在缺陷部位的高强度填料,以及管体上和纤维材 料层间的强力胶,将作用管道损伤部位的应力均匀地传递到复合材料修复层上。
目次
前言 ................................................................................ II 1 范围 .............................................................................. 1 2 规范性引用文件 .................................................................... 1 3 术语和定义 ........................................................................ 1 4 修复技术选择 ...................................................................... 2 5 管体缺陷修复 ...................................................................... 4
械夹具及换管修复技术,具体介绍参见附录A。对于管体打孔盗油(气)泄漏,常采用管帽或补板修复,
具体介绍参见附录B。
油气管体不同缺陷类型宜选用的修复技术如表1所示。
缺陷类型
打磨
表1 油气管体不同缺陷类型与修复技术对应表
堆焊
补板
A型 套筒
B型 环氧钢 套筒 套筒
复合 材料
机械 夹具
换管 修复
泄漏或缺陷深
度>0.8t
I
Q/SY 1592—2013
油气管道管体修复技术规范
1 范围
本标准规定了油气管道管体修复技术的技术特点、修复要点及施工流程。 本标准适用于油气长输管道管体缺陷、打孔盗油(气)点等的修复工作。
2 规范性引用文件
下列文件对于本文件的应用是必不可少的。凡是注日期的引用文件,仅所注日期的版本适用于本文 件。凡是不注日期的引用文件,其最新版本(包括所有的修改单)适用于本文件。
腐蚀深度
<0.8t
外
腐 点蚀深度
蚀
≥0.8t
焊缝损伤
或腐蚀
内部缺陷或腐蚀
管体凿槽或其它 金属损失
否l 否l 否l 否l 否l 永久 修复d
否l 永久 修复 否l
否l
否l 永久 修复e
永久 修复 永久 修复 永久 修复
否l
否l
永久 修复e
否l
永久 修复 否l
否l
永久 修复c 永久 修复e
永久 修复 永久 修复 永久 修复 永久 修复b 永久 修复 永久 修复f
I
Q/SY 1592—2013 6.4 修复材料准备......................................................................8 6.5 现场开挖..........................................................................8 6.6 旧防腐层清除及基材表面处理........................................................8 6.7 缺陷定位..........................................................................8 6.8 缺陷修复..........................................................................8 6.9 现场检测..........................................................................9 6.10 修复层防腐及回填.................................................................9 6.11 后期工作.........................................................................9 附录 A(资料性附录) 修复技术 ....................................................... 10 附录 B(资料性附录) 管道打孔盗油(气)修复 ......................................... 27 附录 C(规范附录) 管道维修的 HSE 管理规定 ........................................... 31 附录 D(资料性附录) 管体缺陷与修复记录表 ........................................... 33 附录 E(资料性附录) 复合材料修复管道缺陷后的性能测试 ............................... 35 参考文献 ............................................................................ 38