基于PLC的材料分拣系统
基于PLC的材料分拣模型控制系统设计

基于PLC的材料分拣模型控制系统设计一、引言在现代工业生产中,材料分拣是一个重要且常见的环节。
材料分拣可以将不同种类、不同属性的物料进行分类和分配,以满足生产的需求。
为了提高分拣效率和准确性,需要设计一个可靠的控制系统来实现材料分拣的自动化。
二、设计目标本次设计旨在设计一个基于PLC的材料分拣模型控制系统,实现以下目标:1.实现对不同种类材料的分拣和分配;2.提高分拣的准确性和效率;3.实现故障检测和自动化维修。
三、系统方案1.硬件设计本系统的主要硬件设备包括传感器、执行器和PLC控制器。
传感器用于检测材料的属性和位置信息,例如颜色传感器、光电开关和位置传感器。
执行器用于执行分拣和分配任务,例如电磁阀和电动机。
PLC控制器作为系统的核心控制设备,负责接收传感器的信号、执行相应的控制逻辑,并控制执行器完成分拣任务。
2.软件设计本系统的软件设计主要包括PLC程序设计和人机界面设计。
PLC程序设计是系统的核心,通过Ladder图编程,实现对传感器和执行器的控制逻辑。
人机界面设计是为了方便操作员监控和控制系统的运行状态,可以使用触摸屏或者上位机软件进行设计。
3.系统工作流程本系统的工作流程如下:(1)启动系统:操作员通过操作界面启动系统,PLC控制器开始运行。
(2)材料检测:传感器对传入的材料进行检测,获取材料的属性和位置信息。
(3)控制逻辑执行:PLC根据传感器的信号执行相应的控制逻辑,控制执行器完成分拣任务。
(4)分拣完成信号:当分拣任务完成时,系统发送完成信号。
(5)系统监控:操作员通过人机界面监控系统运行状态,可以查看材料分拣结果和系统故障信息。
(6)故障检测和维修:系统可以检测到传感器故障或执行器故障,并进行自动化维修或发送故障信息。
四、总结本次设计基于PLC的材料分拣模型控制系统,实现了对不同种类材料的分拣和分配,并提高了分拣的准确性和效率。
通过软件设计和硬件设计的协调工作,实现了系统的自动化和人机交互功能。
《2024年基于PLC控制的多传感器物料自动分拣系统设计》范文
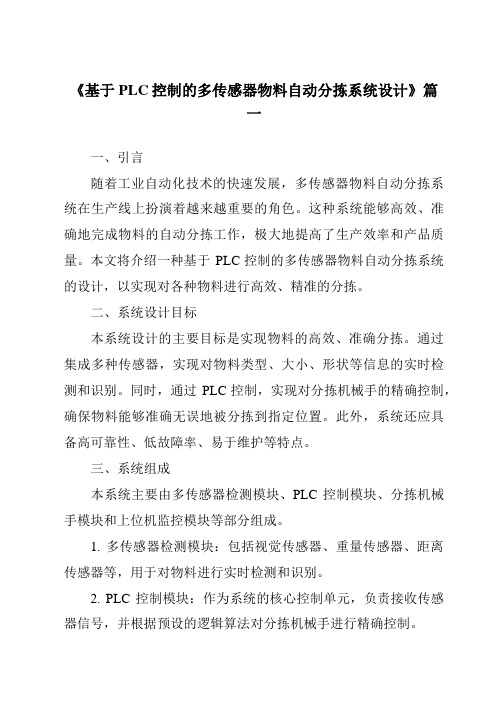
《基于PLC控制的多传感器物料自动分拣系统设计》篇一一、引言随着工业自动化技术的快速发展,多传感器物料自动分拣系统在生产线上扮演着越来越重要的角色。
这种系统能够高效、准确地完成物料的自动分拣工作,极大地提高了生产效率和产品质量。
本文将介绍一种基于PLC控制的多传感器物料自动分拣系统的设计,以实现对各种物料进行高效、精准的分拣。
二、系统设计目标本系统设计的主要目标是实现物料的高效、准确分拣。
通过集成多种传感器,实现对物料类型、大小、形状等信息的实时检测和识别。
同时,通过PLC控制,实现对分拣机械手的精确控制,确保物料能够准确无误地被分拣到指定位置。
此外,系统还应具备高可靠性、低故障率、易于维护等特点。
三、系统组成本系统主要由多传感器检测模块、PLC控制模块、分拣机械手模块和上位机监控模块等部分组成。
1. 多传感器检测模块:包括视觉传感器、重量传感器、距离传感器等,用于对物料进行实时检测和识别。
2. PLC控制模块:作为系统的核心控制单元,负责接收传感器信号,并根据预设的逻辑算法对分拣机械手进行精确控制。
3. 分拣机械手模块:包括机械手本体、驱动装置和执行机构等,根据PLC的指令进行物料分拣。
4. 上位机监控模块:用于实时监控系统的运行状态,包括传感器数据、机械手运动状态等,便于操作人员进行管理和维护。
四、系统工作原理系统工作时,多传感器检测模块首先对物料进行实时检测和识别,将检测到的信息传输给PLC控制模块。
PLC控制模块根据预设的逻辑算法对信息进行处理,并发出控制指令给分拣机械手模块。
分拣机械手模块根据指令进行物料分拣,将物料准确无误地分拣到指定位置。
同时,上位机监控模块实时监控系统的运行状态,确保系统的稳定性和可靠性。
五、系统实现1. 硬件实现:根据系统设计要求,选择合适的传感器、PLC、机械手等硬件设备,并进行合理的布局和安装。
2. 软件实现:编写PLC控制程序和上位机监控程序,实现系统的逻辑控制和监控功能。
基于某PLC的自动控制分拣系统的设计

基于某PLC的自动控制分拣系统的设计自动控制分拣系统是现代物流仓储行业非常重要的一环,它能够提高分拣的效率和准确性,降低分拣过程中的人为错误率,减少人力成本。
本文将基于PLC来设计一个自动控制分拣系统。
该系统的主要功能是将不同种类的货物根据事先设定的规则自动进行分拣,并将其送到相应的目的地或存储区域。
系统包括输入设备、PLC、执行机构和输出设备四个主要部分。
1.输入设备:将待分拣的货物信息输入到系统中。
例如,可以使用条形码扫描设备将货物的条形码信息输入到PLC。
2.PLC:作为系统的核心控制设备,负责接收输入的货物信息,并根据事先设定的规则进行分拣指令的生成。
PLC还可以接收其他传感器中的信息,如输送机上的检测装置,以确保分拣过程的准确性。
3.执行机构:根据PLC生成的指令,将货物送到相应的目的地。
执行机构可以是机械臂、输送带或滑道等。
这些设备需要与PLC进行通信,接收和执行PLC的指令。
4.输出设备:该设备用于输出分拣结果。
例如,可以使用LED显示屏或打印机来显示或打印分拣结果,以供操作员查看。
在设计该自动控制分拣系统时,首先需要进行需求分析和系统功能分析,确定具体的分拣规则和分拣目的地。
然后,根据这些规则和目的地,编写PLC的程序,实现分拣系统的自动控制。
在编写PLC程序时,需要考虑到各种情况,例如货物种类的多样性、货物尺寸的不同、运输速度的变化等。
接下来,需要选择适合的执行机构。
根据不同的需求,可以选择机械臂、输送带或滑道等设备。
这些设备需要与PLC进行连锁操作,以确保分拣的准确性和效率。
最后,在实际应用中,需要对系统进行测试和调试。
这包括验证系统是否能够按照设计的规则进行分拣,以及是否能够正常运行。
在测试和调试过程中,可能会遇到一些问题,例如分拣错误、传感器故障等,需要及时解决和修复。
总之,基于PLC的自动控制分拣系统的设计需要从需求分析、PLC编程、执行机构选择和测试调试等多个方面考虑。
基于PLC的快递分拣系统

基于PLC的快递分拣系统概述快递行业的发展使得快递分拣系统成为了必不可少的一部分。
而基于PLC(可编程逻辑控制器)的快递分拣系统因其高效、可靠、灵活等优点而得到广泛应用。
本文将介绍基于PLC 的快递分拣系统的工作原理、架构设计以及应用场景。
工作原理基于PLC的快递分拣系统主要通过PLC控制器来实现从快递包裹到分拣口的自动分拣过程。
其工作原理如下:1.快递包裹进入系统:当快递包裹进入系统时,会通过传感器检测并将包裹的信息发送给PLC控制器。
2.包裹信息解析:PLC控制器会解析包裹的信息,包括收件人地址、重量、体积等,以便进行后续的分拣操作。
3.分拣策略确定:根据包裹的信息,PLC控制器会根据预设的分拣策略来确定将包裹分配到哪个分拣口。
4.分拣执行:PLC控制器会通过控制气动装置、电机等设备,将包裹送往相应的分拣口。
5.分拣完成:当包裹成功分拣到相应的分拣口时,PLC控制器会发送信号给操作员,提示分拣完成。
架构设计基于PLC的快递分拣系统的架构设计如下:1.PLC控制器:负责整个系统的控制和协调,包括接收传感器信号、执行分拣策略、控制分拣设备等。
2.传感器:用于检测和获取包裹的相关信息,例如光电传感器、称重传感器、尺寸传感器等。
3.分拣设备:包括气动装置、电机、传送带等,用于将包裹从入口送往相应的分拣口。
4.人机界面:为操作员提供交互界面,以便查看分拣状态、设置分拣策略等。
5.数据收集与处理系统:用于收集、分析和统计快递分拣系统的工作数据,以便进行效率优化和管理决策。
应用场景基于PLC的快递分拣系统在快递行业中应用广泛,主要有以下几个应用场景:1.快递中心:大型快递中心通常需要处理大量的包裹,通过基于PLC的分拣系统可以实现自动化、高效率的分拣操作。
2.仓储物流:在仓储物流领域,基于PLC的快递分拣系统可以提升货物的分拣速度和准确率,从而提高仓库的运营效率。
3.高速分拣线:高速分拣线通常需要处理大量快递包裹的同时保证分拣精度和速度,基于PLC的快递分拣系统能够满足这种需求。
【《基于plc的自动分拣系统》4400字(论文)】
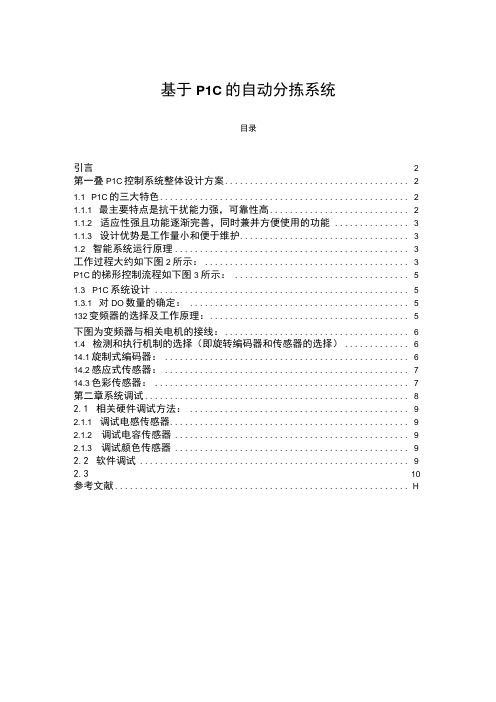
基于P1C的自动分拣系统目录引言2第一叠P1C控制系统整体设计方案 (2)1.1 P1C的三大特色 (2)1.1.1 最主要特点是抗干扰能力强,可靠性高 (2)1.1.2 适应性强且功能逐渐完善,同时兼并方便使用的功能 (3)1.1.3 设计优势是工作量小和便于维护 (3)1.2 智能系统运行原理 (3)工作过程大约如下图2所示: (3)P1C的梯形控制流程如下图3所示: (5)1.3 P1C系统设计 (5)1.3.1 对DO数量的确定: (5)132变频器的选择及工作原理: (5)下图为变频器与相关电机的接线: (6)1.4 检测和执行机制的选择(即旋转编码器和传感器的选择) (6)14.1旋制式编码器: (6)14.2感应式传感器: (7)14.3色彩传感器: (7)第二章系统调试 (8)2.1相关硬件调试方法: (9)2.1.1 调试电感传感器 (9)2.1.2 调试电容传感器 (9)2.1.3 调试颜色传感器 (9)2.2软件调试 (9)2.310参考文献........................................................... H引言在物料搬运系统中存在智能分拣系统这个分支系中,能够为后续机械化操作打下可靠的基础。
不仅在化工、电气行业得到了应用、近期在制药行业也逐渐兴起。
目前,由于目前市场上自动化分拣设备前景良好,再加上人力成本的逐年上升趋势,智能P1C更新速度愈发迅速。
众所周知,P1C以其灵活可靠、易于扩展、通用性强等特性,逐渐成为自动化生产领域的主控设备之一。
本次论文结合变频技术、遥感技术等,来进行最终的设计。
第一章P1C控制系统整体设计方案1.1P1C的三大特色1.1.1最主要特点是抗干扰能力强,可靠性高传统的继电器■接触器控制系统由于使用了大量的机械触点,使得存在良好的抗干扰能力,但由于设备之间的接线比较复杂,而且由于设备的老化,触点脱焊、抖动,在分合闸时触点会被电弧损坏,同时由于机械触点之间容易出现接触不良的状况,会使得出现故障的可能性提高,从而大大降低了系统的可靠性。
基于PLC的物流分拣系统解析
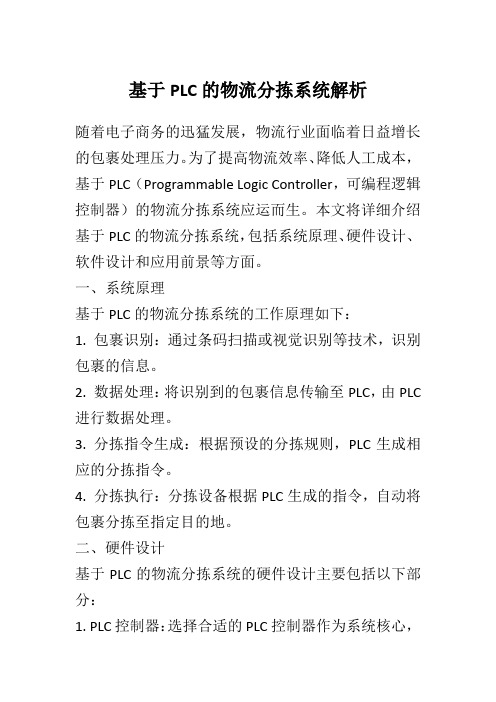
基于PLC的物流分拣系统解析随着电子商务的迅猛发展,物流行业面临着日益增长的包裹处理压力。
为了提高物流效率、降低人工成本,基于PLC(Programmable Logic Controller,可编程逻辑控制器)的物流分拣系统应运而生。
本文将详细介绍基于PLC的物流分拣系统,包括系统原理、硬件设计、软件设计和应用前景等方面。
一、系统原理基于PLC的物流分拣系统的工作原理如下:1. 包裹识别:通过条码扫描或视觉识别等技术,识别包裹的信息。
2. 数据处理:将识别到的包裹信息传输至PLC,由PLC 进行数据处理。
3. 分拣指令生成:根据预设的分拣规则,PLC生成相应的分拣指令。
4. 分拣执行:分拣设备根据PLC生成的指令,自动将包裹分拣至指定目的地。
二、硬件设计基于PLC的物流分拣系统的硬件设计主要包括以下部分:1. PLC控制器:选择合适的PLC控制器作为系统核心,负责数据处理和指令生成。
2. 传感器与执行器:设计合适的传感器和执行器电路,用于包裹识别、分拣设备控制和状态反馈等。
3. 通信模块:设计合适的通信模块,实现PLC与上位机、分拣设备等之间的数据传输。
4. 电源模块:设计合适的电源模块,为系统提供稳定的电源供应。
三、软件设计基于PLC的物流分拣系统的软件设计主要包括以下部分:1. 控制算法:设计高效的分拣控制算法,包括包裹识别、数据处理、指令生成等。
2. 用户界面:设计友好的用户界面,方便操作人员进行监控和故障排查。
3. 数据管理:设计合理的数据管理算法,确保包裹信息的安全和可靠。
四、应用前景基于PLC的物流分拣系统具有广泛的应用前景,主要包括以下几个方面:1. 电子商务:在电子商务领域,物流分拣系统可以提高包裹处理效率,降低人工成本。
2. 制造业:在制造业中,物流分拣系统可以实现对原材料、成品等物料的自动化分拣。
3. 邮政快递:在邮政快递领域,物流分拣系统可以提高邮件、包裹的处理速度和准确性。
基于PLC物料传送分拣控制系统设计
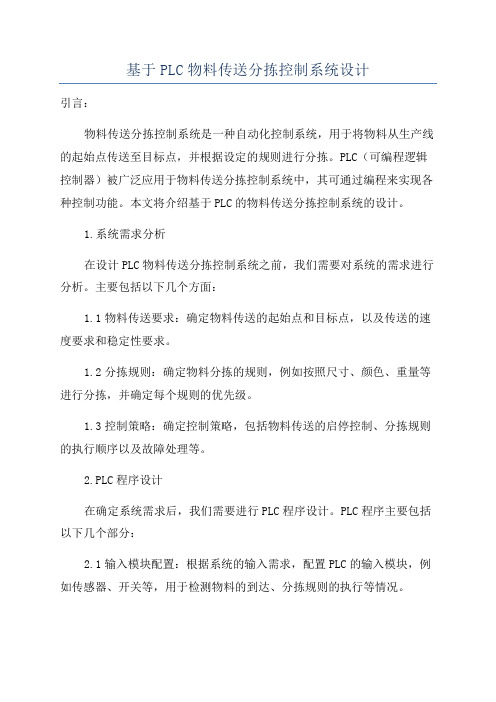
基于PLC物料传送分拣控制系统设计引言:物料传送分拣控制系统是一种自动化控制系统,用于将物料从生产线的起始点传送至目标点,并根据设定的规则进行分拣。
PLC(可编程逻辑控制器)被广泛应用于物料传送分拣控制系统中,其可通过编程来实现各种控制功能。
本文将介绍基于PLC的物料传送分拣控制系统的设计。
1.系统需求分析在设计PLC物料传送分拣控制系统之前,我们需要对系统的需求进行分析。
主要包括以下几个方面:1.1物料传送要求:确定物料传送的起始点和目标点,以及传送的速度要求和稳定性要求。
1.2分拣规则:确定物料分拣的规则,例如按照尺寸、颜色、重量等进行分拣,并确定每个规则的优先级。
1.3控制策略:确定控制策略,包括物料传送的启停控制、分拣规则的执行顺序以及故障处理等。
2.PLC程序设计在确定系统需求后,我们需要进行PLC程序设计。
PLC程序主要包括以下几个部分:2.1输入模块配置:根据系统的输入需求,配置PLC的输入模块,例如传感器、开关等,用于检测物料的到达、分拣规则的执行等情况。
2.2输出模块配置:根据系统的输出需求,配置PLC的输出模块,例如电机、气缸等,用于控制物料的传送和分拣。
2.3逻辑控制程序编写:根据系统需求和控制策略,编写逻辑控制程序。
程序主要包括启停控制、分拣规则的执行和故障处理等。
2.4HMI界面设计:为了方便系统操作和监视,可以设计人机界面(HMI),用于显示系统运行状态、设置参数等。
3.系统组态与调试在PLC程序设计完成后,需要进行系统组态与调试。
主要包括以下几个步骤:3.1确定输入输出映射关系:将PLC的输入输出模块与实际硬件设备进行映射,确保PLC能够正确读取传感器的信号和控制执行器的动作。
3.2参数设置与校准:根据实际情况,设置系统参数,例如物料传送速度、传感器的灵敏度等。
并进行校准,确保系统运行的准确性和稳定性。
3.3系统调试:进行系统的调试,测试物料传送、分拣和故障处理等功能的正确性和可靠性。
基于PLC的物料自动分拣系统设计毕业设计

基于PLC的物料自动分拣系统设计毕业设计摘要:随着物流业的发展,自动分拣系统在物料仓储和配送方面起着重要的作用。
本文设计了一种基于可编程逻辑控制器(PLC)的物料自动分拣系统。
该系统通过搬运装置和传感器进行物料的识别和分拣,并利用PLC来控制整个分拣过程。
通过使用PLC,可以实现自动化、高效和准确的物料分拣。
本文还对系统的硬件和软件实现进行了详细的介绍,并进行了系统的测试和评估。
实验结果表明,该系统具有较高的可靠性和分拣准确性。
1.引言物流行业是现代经济的重要组成部分,随着电子商务和电子零售的兴起,物流需求也日益增长。
物料的快速、准确和高效分拣对于满足市场需求至关重要。
然而,传统的人工分拣工具费时费力,人工成本高。
因此,自动分拣系统具有重要意义。
2.系统设计2.1系统架构本系统采用基于PLC的物料自动分拣系统。
系统架构包括四个主要模块:传感器模块、搬运装置模块、PLC模块和控制台模块。
2.2传感器模块传感器模块用于对物料进行识别和检测。
常用的传感器包括光电传感器、摄像头和压力传感器。
这些传感器通过检测物料的形状、颜色、大小等特征,将物料识别为不同的类别。
2.3搬运装置模块搬运装置模块用于将被识别的物料从输入端搬运到输出端。
该模块可以使用输送带、机械臂等搬运设备。
2.4PLC模块PLC模块用于控制整个物料分拣系统的运行。
它可以接收传感器模块发出的信号,根据程序逻辑进行判断和控制,并输出控制信号给搬运装置模块。
2.5控制台模块3.硬件和软件实现硬件方面,本系统采用了PLC、光电传感器、输送带和工作台等设备。
软件方面,使用PLC编程软件进行程序的编写和调试。
4.系统测试和评估通过对系统的功能和性能进行测试和评估,可以评估系统的稳定性、准确性和效率。
在测试中,我们使用了一定数量的不同类别的物料进行分拣。
实验结果表明,系统能够准确识别和分拣物料,并且具有高效率和稳定性。
5.结论基于PLC的物料自动分拣系统是一种自动化、高效和准确的物料分拣解决方案。
- 1、下载文档前请自行甄别文档内容的完整性,平台不提供额外的编辑、内容补充、找答案等附加服务。
- 2、"仅部分预览"的文档,不可在线预览部分如存在完整性等问题,可反馈申请退款(可完整预览的文档不适用该条件!)。
- 3、如文档侵犯您的权益,请联系客服反馈,我们会尽快为您处理(人工客服工作时间:9:00-18:30)。
基于P L C的材料分拣系统文件编码(008-TTIG-UTITD-GKBTT-PUUTI-WYTUI-8256)引言随着社会的不断发展,市场的竞争也越来越激烈,因此各个生产企业都迫切地需要改进生产技术,提高生产效率。
在需要进行材料分拣的企业,以往都采用人工分拣的方法,分拣效率极为低下,致使生产成本高,企业竞争力差。
近年来,随着科学技术的不断发展,出现了一些自动控制分拣系统装置,它可以大幅度的提高分拣效率,因此越来越多的企业采用了自动控制分拣系统装置。
关于自动控制分拣系统装置现在市场上已经大量出现了,并且也应用到生产实际中了。
由于PLC具有体积小、易安装、维修性好等特点,所以设计本课题是用PLC来控制分拣系统装置的。
可编程序控制器(PLC)现在已经综合了计算机技术、自动控制技术和网络通信技术,其功能越来越强大。
本课题采用PLC控制分拣系统装置,可以同时实现三种物料的快速分拣,分别是铁质物料、铝质物料和颜色物料等。
并且可以与上位机相接,实现实时监控。
它不但可以快速分拣效率,节省大量的人力资源,而且可靠性高,稳定性强,可长时间进行分拣,正是需要进行材料分拣的企业所迫切希望的分拣系统装置。
第1章绪论该课题是基于PLC的材料分拣系统设计,它包括可编程序控制部分、传感器检测部分、电动机控制部分以及空气压缩机部分。
对于本课题来讲,它就是自动化技术、传感器检测技术以及电气拖动技术的融合,在国民经济发展中起着推动作用。
近年来,分拣领域已经并正在发生着日新月异的变化,各种先进技术已经被应用到各个工程实际中,并且已经取得了很大的成就。
随着社会的不断发展,市场的竞争也越来越激烈,因此各个生产企业都迫切地希望改进生产技术,提高生产效率,同样在需要进行材料分拣的企业,以往一直采用人工分拣的方法,致使生产效率低,生产成本高,企业的竞争能力差,材料分拣系统装置已成为他们的必然选择。
虽然材料分拣系统装置现在已经开始在工程实际应用中开始发挥作用,但是随着科学技术的不断发展,分拣系统也在不断的完善中。
分拣系统装置有几种系统控制方式。
分别是继电器控制系统、计算机控制系统以及PLC等。
几十年来继电器控制系统一直为工业发展起到了巨大的作用,而且目前仍然在工业中大量应用,然而其控制性能与自身的功能已无法满足与适应工业控制要求和发展。
计算机控制系统有着十分强大的计算与数据处理能力,但在别的方面却没有PLC功能强大。
因此在这个设计中选择PLC来控制分拣系统装置。
此设计正是基于采用PLC来实现关于材料分拣控制系统的设计。
材料分拣控制系统组成主要有传感器、断电延时器、进料槽、传送带、分拣推手等组成。
当第一个光电传感器检测到进料槽有物体时,上料传感器输出信号给PLC,PLC控制输送带继续运转,同时控制上料气动阀进行上料,每次上料时间间隔可以根据实际情况进行调整。
第一个物料传感器为电感传感器,当检测出物料为铁质物料时,反馈信号送PLC,由PLC控制气动阀动作选出该物料;第二个物料传感器为电容传感器,当检测出物料为铝质物料时,反馈信号送PLC,PLC控制气动阀动作选出该物料;第三个物料传感器为颜色传感器,当检测出物料的颜色为待检测颜色时,PLC控制气动阀动作选出该物料;最后还有一个备用的传感器,是用来检测并推下漏拣的物料。
本课题由于采用PLC作为控制系统,它存在输入输出响应的滞后现象。
滞后现象是指PLC外部输入信号发生变化的时刻起至它控制的有关外部输出信号发生变化的时刻之间的间隔。
虽然它有一定的延迟但并不影响分拣系统装置的工作,因为PLC的延迟时间只有几十毫秒,对于本分拣系统装置起不到什么影响,完全可以忽略。
本设计主要研究的是使分拣系统装置能进行三种物料的分拣并能与上位机相连进行实时监控。
可编程序控制器(PLC)现在已经综合了计算机技术、自动控制技术和网络通信技术,其功能越来越强大。
该篇设计有着广阔的应用前景,它节省大量的劳动力,从而可以大大提高生产率,促进社会工业的发展。
第2章方案比较与选择由于本设计是基于PLC的材料分拣系统设计,所以从材料分拣系统装置的控制系统方面进行方案的比较与选择。
一共有三种方案:分别是PLC 、继电器控制系统与计算机控制系统。
下面是关于三种方案的比较与选择。
一、几十年来,继电器控制系统为工业控制的发展起到了巨大的作用,而且目前仍然在工业领域中大量的应用,然而其控制性能与自身的功能已无法满足与适应工业控制的要求和发展,与PLC相比较,存在着质的差别。
下面是关于它们的各个方面的比较:(1)控制功能的实现:继电器控制系统通过对继电器进行硬接线完成相应的控制功能,PLC对进行编程实现所需控制要求。
(2)对生产工艺变化的适应性:继电器控制系统需要重新设计与接线,适应性差,PLC只需对程序进行修改,适应性强。
(3)可靠性:继电器控制系统元器件多,触点多,容易出现故障,PLC采用大规模集成电路,绝大部分是软继电器,可靠性高。
(4)控制的实时性:继电器控制系统机械动作时间常数大,实时性差,PLC 微处理器控制,实时性非常好。
(5)占用空间与安装:继电器控制系统控制体积巨大、笨重,安装施工工作量大,PLC体积小,重量轻,安装工作量小。
(6)使用寿命:继电器控制系统易损,寿命短,PLC寿命长。
(7)价格:继电器控制系统较低,PLC较高。
(8)维护:继电器控制系统维护复杂、工作量大,PLC维护工作量小。
二、通用计算机具有十分强大的计算与数据处理能力,同时数据处理速度已达到极高的水平,但是应用通用计算机进行工业控制,在很多方面没有PLC功能强大。
下面是关于它们的比较:(1)工作方式:通用计算机采用中断方式,PLC采取扫描方式。
(2)通用计算机使用汇编语言、高级语言,PLC采用助记符语句表、梯形图等。
(3)工作环境:通用计算机要求较高,PLC可在较差的环境工作。
(4)对使用者的要求:通用计算机需要专门的学习培训才行,PLC语言易学,稍加培训即可使用。
(5)可靠性:通用计算机商业级要求,PLC工业级,且有多种特殊设计,包括监视记时器功能。
(6)系统软件:通用计算机系统软件功能强大,但占用存储空间过大,PLC 系统软件功能专用,占用存储空间小。
(7)价格:通用计算机价格高,PLC价格较低。
以上各种情况综合分析,决定采用PLC控制系统来控制材料分拣系统装置。
和其它两种控制系统相比PLC控制系统主要优点是可靠性、易操作性(操作方便、编程方便、维修方便)、灵活性(编程的灵活性、扩展的灵活性、操作的灵活性)、机电一体化等。
另外PLC的功能有:(1)关于逻辑和顺序控制:主要完成开关逻辑运算和进行逻辑控制,从而可以实现各种简单或复杂的控制要求。
(2)定时控制:PLC具有很强的定时、记数功能,而且是间隔可以由用户自己设定。
(3)数据处理:新型PLC都具有数据处理能力,它能进行算术运算,数据传送。
(4)通信:PLC作为下位机,与上位机或同级的可编程序控制器进行通信,完成数据的处理和信息的交换。
第3章基于PLC的材料分拣系统的硬件设计部分材料分拣系统流程图及PLC选型一、材料分拣系统流程图材料分拣系统流程图如下图所示,它是利用各种传感器对待测物料进行检测并分类。
根据选用的传感器类型不同,可分辨出铁、铝及非金属,并能分辨出某种颜色。
当待测物体经下料装置传入传送带后,依次接受各种传感器的检测。
如果被某种传感器测中,通过相应的气动装置将其推入料箱,否则继续前行。
料槽有料时,上料传感器输出信号给PLC ,PLC 控制输送带继续运转,同时控制上料气动阀进行上料,每次上料时间间隔可以进行调整。
物料传感器1为电感传感器,当检测出物料为铁质物料时,反馈信号送PLC ,由PLC 控制气动阀1动作选出该物料。
物料传感器2为电容传感器,当检测出物料为铝质物料时,反馈信号送PLC ,PLC 控制气动阀2动作选出该物料;物料传感器3为颜色传感器,当检测出物料的颜色为待检测颜色时,PLC 控制气动阀3动作选出该物料。
当系统设定为分拣某种颜色的金属或非金属物料时,由程序记忆各传感器的状态,完成分拣任务。
二、PLC 的选型1、控制要求及I/O 接口本设计要求实现三种物料的分拣,分别是铁质、铝质和带颜色的物料。
根据要求选用了四个种类的五个传感器来检测物料。
它们分别是电感传感器、电容传感器、颜色传感器以及光电传感器。
电感传感器专门检测铁质物料,电容传感器检测铝质物料,颜色传感器检测颜色物料。
光电传感器一共有两个,一个用于进料槽检测有无物品,另一个作为备用传感器负责把前面三个传感器漏拣的物料分拣下来。
另外还用了异步电动机来带动传送带,它可以满足快速启动及制动的控制要求。
空气压缩机通过电磁阀来控制推手把物料分拣下去。
如图3-2所示。
5510个信号。
输出包括控制电动机运动的接触器,以及5个控制气缸动作的电磁阀。
共需要I/O接点21个,其中有15个输入点和6个输出点。
如下表所表示。
表3-1 输入信号和输出信号输入信号:推气缸1动作限位SFW1 X004推气缸2动作限位SFW2 X012推气缸3动作限位SFW3 X020推气缸4动作限位SFW4 X023推气缸5动作限位SFW5 X001电感传感器SA X003电容传感器SB X011颜色传感器SC X014备用传感器SD X022光电传感器SN X000推气缸1动作限位SBW1 X010推气缸2动作限位SBW2 X013推气缸3动作限位SBW3 X021推气缸4动作限位SBW4 X024推气缸5动作限位SBW5 X002输出信号:推气缸1电磁阀YV1 Y003推气缸2电磁阀YV2 Y005推气缸3电磁阀YV3 Y007推气缸4电磁阀YV4 Y009推气缸5电磁阀YV5 Y011电动机 YV6 Y002根据要求选用选用三菱FX2N系列PLC。
主要是因为FX2N有以下的优点。
FX2N是FX系列中功能最强、速度最快的微型可编程序控制器。
FXZN系列PLC是超小型机,I/O点数最大可扩展到256点。
它有内置8K步的RAM,使用存储卡盒后,最大容量可扩大到16K步。
编程指令丰富,有27条基本指令、2条步进指令和128种功能指令。
PLC运行时,对一条基本指令的处理时间只要。
它不仅能完成逻辑控制,顺序控制、模拟量控制、位置控制、高速计数等功能。
还能做数据检索、数据排列、三角函数运算、平方根以及浮点数运算、脉冲输出(20kHz/DC5V,10kHz/DC12~14V)、脉宽调制、PID运算等更为复杂的数据处理。
所以FX2N系列PLC具有容量大、运行速度快、指令功能完善等特点。
在FX2N系列PLC基本单元上,可连接扩展单元、扩展模块以及各种功能的特殊单元、特殊模块,还可在基本单元左侧接口上,连接一台功能扩展板,完成FX2N系列PLC与各种外部设备的通信,实现模拟量设定功能。