酸轧机组设备工艺操作规程(DOC 44页)
轧机工艺技术操作规程
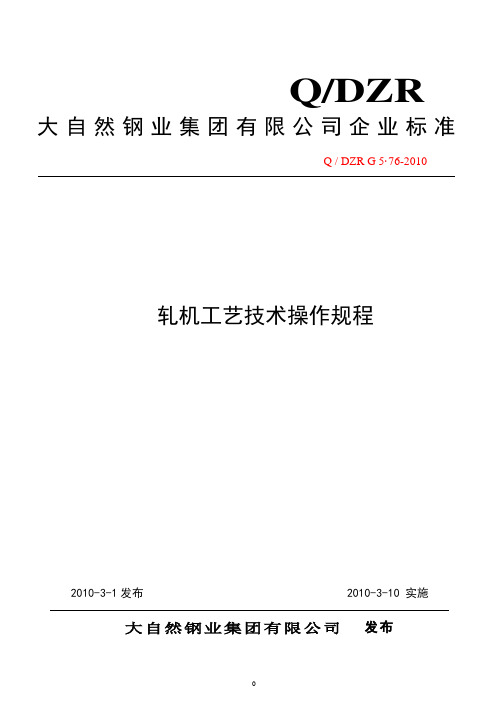
Q/DZR 大自然钢业集团有限公司企业标准轧机工艺技术操作规程2010-3-1发布2010-3-10 实施大自然钢业集团有限公司发布大自然钢业集团有限公司管理体系程序文件Q / DZR G 5·76-2010轧机工艺技术操作规程1.开卷岗位操作规程1.1上卷前的准备(手动状态)上卷小车降至下限上卷小车退到受料台正下方开卷机卷筒缩径对中泵站运转正常卷筒位于对中中位开头压辊抬到上限开头机引料辊在上限开头机导板刮板缩回开头刮板摆下至下限带卷位于鞍座1.2上卷升起小车,慢速托起带卷离开鞍座小车拖动带卷前进至卷筒前停小车下降,目测使带卷中轴线与卷筒中轴线对正开进小车,将带材套在卷筒上,目测带宽中心线与卷筒中心对正开卷压辊压在带卷上,拆除捆带,小车下降至下限卷筒胀径,撑紧带材,1.3开头1.3.1开头机状态矫直辊抬起,夹送辊抬起切头剪处于最大开口度1.3.2开头点动开卷机将带头转到带卷上方抬起并伸出刮板,对准带头前点开卷机,将带头向前沿导板送到夹送辊处,停压下送料辊将带头压住,抬起开卷机压辊缩回刮板,摆下,自动对中投入并点动夹送辊,将带头送至矫直辊处,可根据需要切除带头压下矫直辊,矫直带头,使带头上翘,以便于穿带抬起矫直辊,将带头送到引导板处停,切断所有动作等待穿带1.4穿带和第一道次轧制启动自对中,点动开卷机和夹送辊联合送料,将带头送到入口导向辊配合入口工、出口工继续送料,直到将带头送入左卷钳口打活套约1.5米,待左卷缠绕1~2圈带钢为止,穿带完毕向主控发出信号,准备进行第一道次轧制,通知入口工打联动,轧机启动后视来料情况通知主控工升降速在接近尾部时,通知主控降速,剩余2~3圈时降到穿带速度,切断自对中升起伸缩刮板带尾脱离卷筒,到矫直辊处,压下矫直辊矫平带尾甩尾完毕停车,恢复穿带前状态,准备下一卷轧制注意事项送料时抬起开卷压辊,以免料拱起,顶坏对中光头。
所有液压马达不用时打中位,以免损坏2.入口岗位操作规程2.1穿带前的准备(手动状态)(1)右卷压辊在抬起状态(2)右入口导板在下限(3)摆动压辊位于中间位(4)卷推板在缩回状态(5)对中侧导板打开状态(6)机前压板在下降位(7)测厚仪离线,关闭(8)真空除油装置在线,压辊抬起(9)右卷活动支撑打开,卷筒缩径,钳口位于左上方(10)小车位于下限,并退至鞍座下方2.2穿带放下右卷压辊至水平抬起入口导板至上限当开卷工将带头送到偏导辊时,引料辊前摆,压住带钢点动引料辊与开卷工联合送料用对中侧导板夹正带钢当料头送到左钳口时,停止送料抬起引料辊,用对中侧导板将带钢夹正通知主控工具备压下条件,可以压下,降下入口导板至右卷钳口位轧辊压住带钢后,压力超过200吨,打开侧导板,按下开卷联动按钮,准备第一道次轧制2.3第一道次轧制及甩尾当主控压下带钢后,压下真空抽吸装置压辊打开机前乳化液轧机启动后,调整偏摆,控制带钢跑偏待稳定轧制升速后,抬起入口真空抽吸压辊,注意随时调整双摆当轧制接近尾部,降速时,压下真空抽吸压辊等带材离开卷卷筒后,调整双摆,进行甩尾轧制带尾至偏导辊时,停车,关闭乳化液,通知主控将轧辊抬起关闭测厚仪,准备第二道次的穿带,取消开卷联动2.4第二道次的穿带及入口轧制操作a.穿带前状态(手动状态)真空除油压辊抬起左卷压辊抬起至上限测厚仪离线,关闭b.第二道次的穿带第一道停车,降下压上后,取消开卷联动,用对中侧导板夹正带钢,等待出口工回送带头向卷筒方向压摆动引料导辊,引导带头将带头送入钳口,卷筒涨径,扣合活动支撑摆下入口导板通知出口打活套0.7米,左点卷筒将带钢在卷筒上缠绕至少半圈通知出口停止送料,拉缠1圈半通知主控压下,之后打开侧对中导板,并按下左卷联动按钮打开机后测厚仪准备轧制c.偶道次轧制主控工启动轧机后,调整双摆,压正带钢,使带钢顺利走出机架压下真空除油压辊,启动抽吸装置通知主控工缓慢升速,并随时调整双摆、工作辊和中间辊弯辊,使板型调整至最佳,向主控工发出升速信号随时注意板型的调整,直到本道次轧制结束关闭机后乳化液、机前抽吸装置打开机前乳化液,准备下一道次轧制,待轧机升速后,抬起机前抽吸装置压辊,启动机后抽吸装置2.5卸卷停车后,取消左卷联动,关闭乳化液测厚仪,及真空抽吸装置,抬起真空除油压辊压下开卷机压辊压住带钢入口导板抬至合适位,护住小车行走前限位等出口工剪断带钢后,左点卷取机,拉出带头并置于卷筒左下方,如有可能尽力使钳口向上打开活动支撑,开进卸卷小车,至前限位卷筒缩径,升起卸卷小车托起带卷抬起开头机压辊,降下入口导板至下限推动左卷推板,同时小车慢速后退,将带卷退出卷筒,并缩回推板,小车行走停小车上升,将带卷托至上限小车继续下降至下限,同时小车开进至第一个鞍座下方停,卸卷完毕小车后退至鞍座位置,小车下降,将带卷放于鞍座2.6换辊操作2.6.1 工作辊中间辊换辊2.6.1.1轧机停车关闭乳液,2.6.1.2打到停止状态换辊状态(主控)2.6.1.3压上油缸降到最低位(主控)2.6.1.4提升压下螺杆及上支撑辊平衡装置到最高位2.6.1.5提升工作辊轨道及上中间辊轨道到最高位2.6.1.6置上下中间辊横移缸到中间位置(各移动125mm)2.6.1.7上下接轴扁孔处于垂直位置(主控)2.6.1.8接轴抱紧装置夹紧(更换工作辊)2.6.1.9卸掉所要更换辊的油雾快速接头2.6.1.10打开所要换下辊的锁板或夹钳2.6.1.11降下活动盖板2.6.1.12换辊车大车锁紧缸退回2.6.1.13空换辊箱对准轧机并开进,在接轨位置锁定大车2.6.1.14牵引车向前开到抽辊位置,各夹钳夹紧相应的辊头2.6.1.15开动牵引车抽出旧辊2.6.1.16牵引车夹钳脱开,后退到极限2.6.1.17横移车横移,新辊对准轧机窗口2.6.1.18牵引车前行新辊推入机内2.6.1.19所上新辊的锁板或定位夹钳2.6.1.20打开接轴夹紧装置2.6.1.121牵引车后退到极限2.6.1.22大车锁紧缸退回,换辊大车退到后极限位置锁定2.6.1.23根据轧制规格进行中间辊横移2.6.1.24降下上工作辊中间辊轨道2.6.1.25升起活动盖板2.6.1.26插上油雾润滑快速接头2.6.1.27轧制线标高调整(主控)2.6.1.27.1输入上工作辊、中间辊、支撑辊直径2.6.1.27.2压到设定位置自动停,完成标高调整2.6.1.28升起压上油缸,辊系压靠零位,准备轧制2.6.2支撑辊换辊2.6.2.1换辊前的准备2.6.2.1.1工作辊中间辊全部抽出。
酸轧轧机工艺讲解讲诉
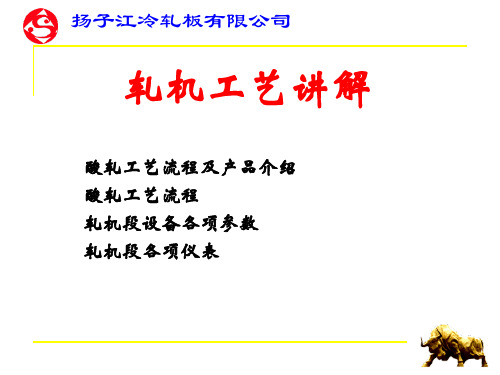
功能:卷取带钢,使带钢成卷。 参数:卷取张力:max.115 kN
卷筒:Φ508/Φ610×1450 mm
扬子江冷轧板有限公司
轧2、机轧段辊设数备据参数
轧机
单位
轧辊
辊身直径最大/最小 mm
辊身长度 辊颈直径 轧辊近似重量
两条机组设计年产量200万吨,单卷重量6-28 吨。机组主要 工艺参数:
入口段速度:最大500m/min 酸洗段速度:最大200m/min 圆盘剪速度:最大250m/min 轧机段速度:最大1700m/min 产品规格:厚度:0.18-2.0(mm); 宽度:750-1300(mm)
扬子江冷轧板有限公司
酸轧车间工艺流程
主要设备组成有:开卷机、激光焊机、入口活套、破鳞拉矫机、 酸洗槽、漂洗槽、出口活套、圆盘剪、联机活套、五机架连轧 机、飞剪、卷取机及焊缝检测仪、张力辊、纠偏辊、测厚仪、 板型仪等。
扬子江冷轧板有限公司
轧机段主要设备介绍
五机架连轧机
卷取机
功能:改变带钢规格和改善板型。 参数:工作辊:450/390×1420mm
扬子江冷轧板有限公司
轧机工艺讲解
酸轧工艺流程及产品介绍 酸轧工艺流程 轧机段设备各项参数 轧机段各项仪表
扬子江冷轧板有限公司
酸轧工艺流程及产品介绍
酸轧机组,采取酸洗-冷轧联合工艺,设备大量采取国内外 合作方式制造,技术先进、成熟,装备水平达世界一流。主要技 术有:激光焊接技术、喷射紊流式酸洗技术、五机架六辊轧制技 术以及全线自动带钢跟踪控制技术,能实现板厚、板形全自动控 制,可为后续工序提供尺寸精确板型好、表面光洁性能高的冷轧 原料。
酸轧轧机卸卷手动操作流程
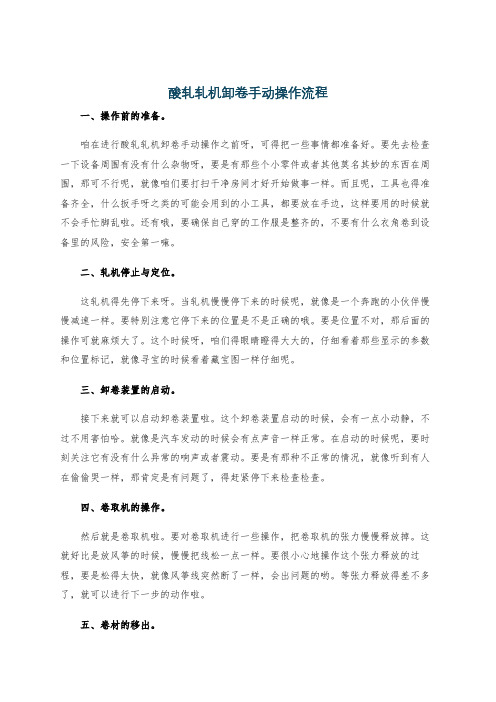
酸轧轧机卸卷手动操作流程一、操作前的准备。
咱在进行酸轧轧机卸卷手动操作之前呀,可得把一些事情都准备好。
要先去检查一下设备周围有没有什么杂物呀,要是有那些个小零件或者其他莫名其妙的东西在周围,那可不行呢,就像咱们要打扫干净房间才好开始做事一样。
而且呢,工具也得准备齐全,什么扳手呀之类的可能会用到的小工具,都要放在手边,这样要用的时候就不会手忙脚乱啦。
还有哦,要确保自己穿的工作服是整齐的,不要有什么衣角卷到设备里的风险,安全第一嘛。
二、轧机停止与定位。
这轧机得先停下来呀。
当轧机慢慢停下来的时候呢,就像是一个奔跑的小伙伴慢慢减速一样。
要特别注意它停下来的位置是不是正确的哦。
要是位置不对,那后面的操作可就麻烦大了。
这个时候呀,咱们得眼睛瞪得大大的,仔细看着那些显示的参数和位置标记,就像寻宝的时候看着藏宝图一样仔细呢。
三、卸卷装置的启动。
接下来就可以启动卸卷装置啦。
这个卸卷装置启动的时候,会有一点小动静,不过不用害怕哈。
就像是汽车发动的时候会有点声音一样正常。
在启动的时候呢,要时刻关注它有没有什么异常的响声或者震动。
要是有那种不正常的情况,就像听到有人在偷偷哭一样,那肯定是有问题了,得赶紧停下来检查检查。
四、卷取机的操作。
然后就是卷取机啦。
要对卷取机进行一些操作,把卷取机的张力慢慢释放掉。
这就好比是放风筝的时候,慢慢把线松一点一样。
要很小心地操作这个张力释放的过程,要是松得太快,就像风筝线突然断了一样,会出问题的哟。
等张力释放得差不多了,就可以进行下一步的动作啦。
五、卷材的移出。
现在呢,就可以把卷材移出啦。
这个过程要稳稳当当的哦。
就像是抱着一个珍贵的宝贝一样,小心翼翼的。
要注意卷材移动的方向是不是正确的,可不能让它走偏了。
如果走偏了,就像走路走错了方向,会很麻烦的呢。
在移出的过程中,还要看看有没有什么东西会阻碍卷材的移动,要是有就像路上有石头挡住一样,要把它清除掉。
六、操作后的检查。
等卷材成功移出之后呀,可还没结束呢。
轧机设备操作规程
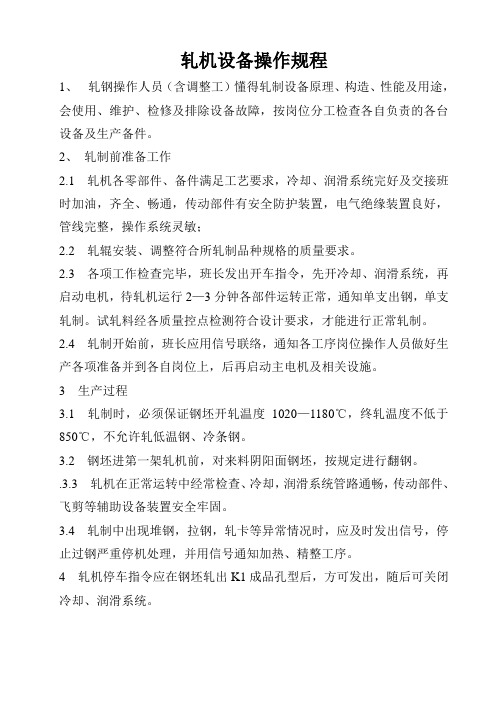
1、轧钢操作人员(含调整工)懂得轧制设备原理、构造、性能及用途,会使用、维护、检修及排除设备故障,按岗位分工检查各自负责的各台设备及生产备件。
2、轧制前准备工作2.1 轧机各零部件、备件满足工艺要求,冷却、润滑系统完好及交接班时加油,齐全、畅通,传动部件有安全防护装置,电气绝缘装置良好,管线完整,操作系统灵敏;2.2 轧辊安装、调整符合所轧制品种规格的质量要求。
2.3 各项工作检查完毕,班长发出开车指令,先开冷却、润滑系统,再启动电机,待轧机运行2—3分钟各部件运转正常,通知单支出钢,单支轧制。
试轧料经各质量控点检测符合设计要求,才能进行正常轧制。
2.4 轧制开始前,班长应用信号联络,通知各工序岗位操作人员做好生产各项准备并到各自岗位上,后再启动主电机及相关设施。
3 生产过程3.1 轧制时,必须保证钢坯开轧温度1020—1180℃,终轧温度不低于850℃,不允许轧低温钢、冷条钢。
3.2 钢坯进第一架轧机前,对来料阴阳面钢坯,按规定进行翻钢。
.3.3 轧机在正常运转中经常检查、冷却,润滑系统管路通畅,传动部件、飞剪等辅助设备装置安全牢固。
3.4 轧制中出现堆钢,拉钢,轧卡等异常情况时,应及时发出信号,停止过钢严重停机处理,并用信号通知加热、精整工序。
4 轧机停车指令应在钢坯轧出K1成品孔型后,方可发出,随后可关闭冷却、润滑系统。
1、精整设备操作人员,懂得设备原理、构造、性能及用途、会使用、维护、检修及排除设备故障。
2、启动精整设备前,必须认真检查各零部件齐全完好,定倍尺装置调整到位,锯片质量和安全装置齐全可靠。
3、冷床/散泠滚道各气缸管路无漏气,电气管线完整,操作系统灵敏,符合正常生产要求。
4、冷床/散泠滚道同步运转良好,发现异常情况及时排除。
5、精整设备运转过程中,经常检查过润滑点的润滑情况及管路无泄漏。
6、当出现成品冲冷床跑槽或吐丝机卡钢时,应立即停止过钢处理、操作控制台及时发出信号通知停止轧制。
酸轧机组设备工艺操作规程.

1、酸洗轧机联合机组概述1.1 酸轧联机的原料条件1.1.1 原料材质原料钢种:热轧低碳钢、超低碳钢(IF钢)及高强度钢等。
产品品种:CQ、DQ、DDQ、EDDQ、S-EDDQ及HSS。
强度级别::max.270 N/mm2软钢:σsσ:max.390 N/mm2b:max.590 N/mm2高强钢:σs:max.800 N/mm2σb1.1.2 机组入出口钢卷数据1.2 机组具有的带钢变规格的能力1.2.1 带钢宽度变化范围:从窄料向宽料变化时,最大范围 100mm ;从宽料向窄料变化时,最大范围 150mm 。
O 5表面质量等级的带钢,宽度必须从宽向窄变化;O 3表面质量等级的带钢,宽度可以从宽向窄、也可以从窄向宽变化。
1.2.2 入口带钢厚度变化的范围:相对值(d2-d1)/d1*100%≤25% (d2数大,d1数小);绝对值 d2-d1≤0.8 mm(其中d为带钢厚度)。
1.2.3 出口带钢厚度变化的范围:相对值(d2-d1)/d1*100%≤30% (d2数大,d1数小);绝对值 d2-d1≤0.5mm(其中d为带钢厚度)。
1.2.4 带钢屈服强度变化的范围:从硬钢到软钢为30%,即(y2-y1)/y1*100% ≤30%从软钢到硬钢为45%,即(y2-y1)/y1*100% ≤45%(其中y为带钢的屈服强度,y2数大,y1数小)2 酸洗部分技术操作规程2.1酸洗基本工艺参数:入口最大速度: 700m/min酸洗段最大速度: 270m/min出口最大速度: 320m/min穿带最大速度: 60m/min甩尾最大速度: 120 m/min酸洗段加速度、减速度:入口: 0.78m/s2酸洗工艺段: 0.30m/s2出口: 0.44m/s2焊机型号:米巴赫HSL21型激光焊机酸洗段最大加热能力: 670t/h酸洗槽总长度: 3×35+2.5=107.5m酸洗时间(酸洗速度270m/min) 105/270×60=23s活套的储存量:入口活套: 668m出口1#活套: 290m出口2#活套: 448m2.2 酸洗各岗位技术操作规程2.2.1 酸轧原料库:2.2.1.1 酸轧原料库用途:有效储存热轧钢卷;自然冷却热轧钢卷;处理不合格钢卷2.2.1.2 主要技术要求堆放形式:按卷位堆放两层上料温度:≤80℃2.2.1.3 原料技术条件:二冷轧厂原料是热轧厂供给的热轧齐边带钢钢卷,按原料验收标准收料 (验收过程中不能直接检查的项目如宽度、厚度、板形和凸度表面质量等应在生产过程中检查),发现问题再进行判定,退料或处理掉不合格部分。
酸轧工艺流程及流程说明

酸轧工艺流程及流程说明酸轧工艺流程1#张力辊 2#张力辊 1#纠偏辊入口活套(2#、3#纠偏辊) 3#张力辊破鳞拉矫机 4#张力辊酸洗槽 4#纠偏辊漂洗槽烘干机 5#张力辊5#纠偏辊酸洗出口活套 6#纠偏辊月牙剪 7#纠偏辊切边剪(碎边剪)6#张力辊去毛刺辊 8#纠偏辊联机活套(9#纠偏辊) 10#纠偏辊 7#张力辊 11#纠偏辊 8#张力辊入口液压剪三辊稳定辊 1#---5#轧机板形仪出口夹送辊转鼓式飞剪卡罗塞尔卷取机出口步进梁打捆称重标识步进梁双切剪矫直机激光焊机开卷机轧后库成品卷酸轧工艺说明钢卷运输在酸洗入口段,钢卷的运输由步进梁、托辊站、钢卷旋转装置、No.1/ No.2 上卷小车等组成。
平行于酸轧机组中心线。
No.1/ No.2 上卷小车分别垂直于酸轧机组中心线。
用车间行车将原料库内存放的热轧钢卷吊放到步进梁运输机上,钢卷经过测量宽度、对中、拆除捆带、旋转等操作后,由步进梁将钢卷运到入口 No.1 固定鞍座上,入口往返小车根据生产情况可以将钢卷从入口 No.1 固定鞍座送到No.2 固定鞍座上。
上卷小车根据开卷状况进行接卷。
然后钢卷由上卷小车输送到等待位置。
在等待位置,上卷小车调整钢卷中心与开卷机芯轴中心重合后,再将钢卷运到开卷机卷筒上。
钢卷带头由夹送穿带装置送到夹送矫直机矫平后,带头送至入口分切剪进行切头,当前一个钢卷还在生产时,带头将自动停留在No.2 转向夹送辊前的等待位置。
入口段在上一个钢卷的带尾快要甩尾之前,开卷机上的自动停车装置将及时对入口段进行减速,当达到甩尾速度时,处理器的矫直辊压下,同时焊机后 No.1 张力辊的压辊也压下。
一旦带尾离开开卷机,其卷筒立即收缩,同时夹送辊和矫直机抬起。
然后,如前所述,可以进行下一个钢卷相同的穿带程序。
被矫直的带尾送进入口分切剪,切去不合格部分。
通过分切剪前的对中装置,可以进行直角剪切。
矫直辊压下深度根据来料钢种和规格自动设定,并可人工干预。
41酸连轧机组操作规程
中冶恒通冷轧技术有限公司酸连轧机组操作规程ZY/MCC14-41-A发布时间:二OO七年十月一日酸连轧生产线操作规程一、开卷操作规程1、按生产计划认真核对钢卷钢种、板宽、板厚、卷重、卷号等参数,核对无误后方可上料。
2、钢卷内圈严重变形的,严重拆边或有其他不宜在酸洗机组上矫直等缺陷的料卷不得使用,待处理后方可上料。
3、天车将轧卷吊放在鞍座上(注意上卷料头方向)人工剪去捆带,上料小车从鞍座上取走钢卷,并经1#(或2#)冷金属检测器测宽后,在经卷径测量装置(1#或2#)测钢卷外径之后,送到开卷机卷筒的轧制线对中位置。
4、人工操作纵卷筒胀开.压辊压下小车下降并退回。
二、焊机操作规程1、首次焊接先检查空气压缩机的压力是否满足,冷却水的流量是否满足,冷却水的温度是否满足(大于35度不能焊接)。
2、启动液压泵,选定远程/就地开关,启动循环泵一分钟后高压泵指示按钮开始闪烁,允许高压泵启动。
3、选择手动模式移动可移动框架,入、出口夹钳、传动小车、对中单元以及修磨月牙剪等设备,仔细观察运转情况,如果发现问题应检查相应的电气和机械液压设备。
4、①选择半自动模式,选择相应的步骤程序(修磨、月牙剪、对中单元、剪切对中、中性层调整、出口电极移动等)按初始化按钮焊接程序自动中单元是否打开,入、出口活套辊是否在低位,可移动小车是否在初始位置,月牙剪、修磨单元、冲孔单元是否满足条件,移动框架夹钳中性层条件是否被初始化,如果条件具备,程序循环按钮闪烁进行下一步操作。
②定缝刀下降相应单元空气吹扫,等待焊接工艺参数的输入,按下PD1确认按钮,如果条件满足程序循环按钮闪烁等待命令。
③按下一步出口活套起套,点动主线相应按钮,带钢撞贴定缝刀,2#、3#对中单元动作,调整3#对中单元使钢带头部贴紧定缝刀。
④按下一步程序出口夹钳夹紧带钢,对中打开空气吹扫单元吹扫。
⑤按下一步入口单元动作,和出口单元类似活套辊起套,对中单元动作,夹钳夹紧带钢。
⑥按下一步可移动框架后移,定缝刀上升回到初始位置,可移动框架按照程序靠近出口带钢,调整固定单元移动使带钢对齐,执行下一步开始焊接。
冷轧酸轧机组工艺流程与冷轧产品综述
冷轧酸轧机组工艺流程与冷轧产品综述一、引言冷轧是金属材料加工工艺中的一种重要环节,通过在室温下将金属材料压制成所需厚度和宽度的产品。
冷轧工艺主要应用于钢材、不锈钢、铝等材料的加工中。
冷轧酸轧机组是冷轧生产线的关键设备,通过机械压力和酸洗工艺,将热轧卷材经过一系列处理步骤,获得平整度高、厚度均匀、表面光洁的冷轧产品。
本文将对冷轧酸轧机组的工艺流程进行详细介绍,并对常见的冷轧产品进行综述,以期帮助读者了解和掌握这一领域的基础知识。
二、冷轧酸轧机组工艺流程2.1 准备工作在冷轧酸轧机组开始工作之前,需要进行一系列准备工作,包括设备检查、原材料准备和设备调试等。
设备检查主要是确保机械设备的正常运行、安全性和稳定性。
原材料准备包括提前准备好待加工的热轧板卷或钢坯等。
设备调试是为了保证机械设备在工作状态下的正常运行。
2.2 酸洗准备酸洗是冷轧酸轧机组的关键工艺之一,目的是去除热轧板卷表面的氧化皮和锈蚀物,以提高产品的表面质量和性能。
酸洗准备包括酸洗槽的清洁和酸液的配制。
酸洗槽的清洁是为了去除上一批产品加工残留物,以避免对下一批产品的影响。
酸液的配制需要根据不同材料和工艺要求来确定酸浴的成分和浓度。
2.3 酸洗工艺酸洗工艺包括浸酸、洗涤、中和和淋水等步骤。
首先,将待处理的热轧板卷或钢坯浸入酸槽中,使其表面与酸液充分接触,以去除氧化皮和锈蚀物。
然后,将酸洗后的产品进行洗涤,以去除酸液残留。
接着,使用碱液中和酸洗过程中产生的酸性物质,以保证产品表面的中性。
最后,使用水进行淋水处理,以确保产品表面无任何残留物。
2.4 冷轧工艺经过酸洗后的产品进入冷轧机组进行冷轧加工。
冷轧工艺通过机械力的作用,使得产品的厚度和宽度发生变化,同时提高其平整度和尺寸精度。
冷轧机组通常包括多辊机、矫直机和切割机等设备。
在冷轧过程中,需对轧辊进行定期润滑和更换,以保证机组的连续稳定运行。
2.5 表面处理经过冷轧加工的产品表面通常需要进行进一步的处理,以改善其表面质量和耐腐蚀性能。
轧机技术操作规程
轧机技术操作规程(旧油田管修复专用)(一)原料准备:旧油管除垢、矫直、清理完成后,运送到上料存放架上备用。
(二)通水:开启循环水泵,检查所有水路有无堵塞、滴漏现象,发现问题及时处理。
(三)送电:合上总电源,观察各仪表指示应正常。
(四)轧制:1、跑车后退到最后位置,此时水箱内的污水泵应自动启动,将石墨水喷到芯头上。
启动液压站电机,打开升压电磁阀,液压缸开始动作。
2、上料:将除垢并清理完内壁的旧油管由上料存放架滚到上料输送架上,点动跑车,将芯头深入钢管内,然后启动上料架电机,使跑车芯杆与旧油管同时前进,待到管前端到达输送辊后,停止前进。
3、轧制:(1)启动输送电机、主电机,将调速表调到合适位置。
(2)启动中频电源,将电压表调到合适位置。
(3)降下上输送辊,待到钢管开始旋转时再轻点一至两下“输送辊降”按钮,不可使输送辊压得太紧。
(4)钢管进入感应圈后,要注意观察加热温度,温度过高或过低时应通过调整中频电源或调整输送电机转速,使加热温度适合轧制。
钢管到达轧辊之前,开动跑车将芯头送到最前端。
(5)钢管进入轧辊并与轧辊充分接触后,立即按“输送辊升”升起上输送辊,使之离开钢管,由轧辊带动钢管继续前行。
钢管前端到达轧辊轧制工作面后,转动控制液压缸电磁阀开关,使其由升压转到泄压位置,使跑车随着液压缸的泄压后退而缓慢前行。
注意要调节好液压缸的前进与后退速度,使之与钢管轧制时间相吻合。
(6)当钢管经过轧辊轧制后前端离开轧辊时,要注意导向角钢的位置,切不可使钢管顶到导向角钢,或角钢偏离钢管,应使钢管刚好沿角钢底面及侧面旋转前进。
(7)钢管到达中料架处,应注意调整中料架高度。
(8)轧制过程中应注意钢管加热温度,如果发现因钢管偏沟偏壁原因而烧裂的现象,应立即停机,将钢管退出轧机,作报废处理。
(9)轧制完成,钢管尾部离开轧辊后,立即将液压缸电磁阀开关由泄压位置转到升压位置,同时将跑车退至最后位置,进入下一根钢管轧制工序。
(五)定径:1、轧制后的钢管通过中料架输送到定径机输送辊处,启动输送电机、主电机、中频,降下上输送辊,驱动钢管旋转前行,通过感应圈加热后,进入主轧辊轧制定径,同时升起上输送辊。
酸连轧操作规程
酸洗操作规程<一>准备站 (开车前应启动五辊矫直机润滑泵)(1)天车将原料摆放在鞍座上,人工剪去打包带,只留下一根纵向打包带。
(2)操作小车将料卷安放在地辊中央,反转地辊将料卷头部转到引料板刀板下。
(3)将引料板抬起至料卷相贴部位,正转地辊将打包带铲开,然后反转地辊将打包带甩出地辊,将板头放在原来位置。
(4)抬起引料板,正转地辊,送进一部分板头,引料板压下,板头进入五辊矫直机,联动五辊矫直—地辊,将板头送出切头剪。
(5)按规定将不合格的板头对中切掉。
(6)然后,反转五辊-地辊联动,将板头退回原来位置,使用小车将料卷送往开卷。
(两个准备站操作相同)<二>开卷(开车前,应启动开卷、九辊润滑泵、开卷EPC油泵)(1)打开活动支撑,用小车将料卷选好位置,送进开卷机并同时正转开卷机(此时卷筒为缩径)(2)用小车将料卷放在卷筒相应位置,卷筒涨开,注:待完全涨实后再落下小车,然后将压辊压下。
(3)反转开卷机,将板头放在导板上,通过起升,伸缩导板,把板头引进九辊矫直机。
(4)点动开卷-九辊联动,将矫直好的板头点进夹送辊。
<三>上下通道联动(1)点动联动、夹送辊压下,将带钢送进汇合夹送辊处。
(2)板尾出九辊后,可在切尾剪,对中切除不合格的板尾。
<四>焊机(1)焊机操作箱1、焊机选择半自动状态,板尾甩出开卷后,焊机室撤掉开卷-1#张力辊张力点动焊机出口段联动,将板尾点至双刃剪的切尾剪处,焊机出口活套辊抬起,三号对中装置启动、对中、剪后对中装置对中,切除板尾,然后打开对中、点动出口联动、板尾至出口电极。
2、同时点动入口联动,使板头至双刃剪切头剪处,剪前对中,将板头切除,然后打开对中将板头带到焊机入口前。
3、定缝刀下降、抬起至档位、出口活套辊抬起、点动出口段位置、在活套辊处起套、3#对中装置对中、横移3#对中、、将板尾与定缝刀相贴、不留间隙(对正),最后,压下出口电极压下,入口联动至定缝刀、入口活套辊起套,将入口电极压下、横移出口电极,将焊缝两侧对正查看其间隙应在2.5mm以内,可进行焊接。
- 1、下载文档前请自行甄别文档内容的完整性,平台不提供额外的编辑、内容补充、找答案等附加服务。
- 2、"仅部分预览"的文档,不可在线预览部分如存在完整性等问题,可反馈申请退款(可完整预览的文档不适用该条件!)。
- 3、如文档侵犯您的权益,请联系客服反馈,我们会尽快为您处理(人工客服工作时间:9:00-18:30)。
酸轧机组设备工艺操作规程(DOC 44页)1、酸洗轧机联合机组概述1.1 酸轧联机的原料条件1.1.1 原料材质原料钢种:热轧低碳钢、超低碳钢(IF钢)及高强度钢等。
产品品种:CQ、DQ、DDQ、EDDQ、S-EDDQ及HSS。
强度级别::max.270 N/mm2软钢:σsσ:max.390 N/mm2b:max.590 N/mm2高强钢:σs:max.800 N/mm2σb1.1.2 机组入出口钢卷数据1.2 机组具有的带钢变规格的能力1.2.1 带钢宽度变化范围:从窄料向宽料变化时,最大范围 100mm ;从宽料向窄料变化时,最大范围 150mm 。
O 5表面质量等级的带钢,宽度必须从宽向窄变化;O 3表面质量等级的带钢,宽度可以从宽向窄、也可以从窄向宽变化。
1.2.2 入口带钢厚度变化的范围:相对值(d2-d1)/d1*100%≤25% (d2数大,d1数小);绝对值 d2-d1≤0.8 mm(其中d为带钢厚度)。
1.2.3 出口带钢厚度变化的范围:相对值(d2-d1)/d1*100%≤30% (d2数大,d1数小);绝对值 d2-d1≤0.5mm(其中d为带钢厚度)。
1.2.4 带钢屈服强度变化的范围:从硬钢到软钢为30%,即(y2-y1)/y1*100% ≤30%从软钢到硬钢为45%,即(y2-y1)/y1*100% ≤45%(其中y为带钢的屈服强度,y2数大,y1数小)中不能直接检查的项目如宽度、厚度、板形和凸度表面质量等应在生产过程中检查),发现问题再进行判定,退料或处理掉不合格部分。
2.2.1.4库工操作要点:2.2.1.4.1收料:对经质检站判合格或签收的钢卷进行收料,并及时在计算机上输入储位。
2.2.1.4.2.钢卷的堆放:1.同一批料必须堆放在一起。
2.底层与第二层垂直错位不得超过100mm,卷垛中心线与轨道平行度偏差小于200mm。
2.2.1.4.3.对于不能生产的钢卷要及时吊走,进行处理。
2.2.1.4.4.机组上料:1.严格按生产程序表找料,自编号要用粉笔描写在钢卷上方,发现异常卷不能上机组生产,要及时通知机组取消该卷生产计划,以免混钢,并等待处理。
2. 不合格的钢卷不准上料,如扁卷、内折边卷、折叠、大散卷、高温卷等。
3.生产中取消卷要及时吊回原料库,整齐的堆放在指定跨待处理。
4.检查督促吊车按生产计划顺序上料,杜绝混钢、混号。
2.2.2 生产准备:2.2.2.1 主要任务确认钢卷及外形质量、拆除钢卷捆带、弯带头、将钢卷从1#步进梁运送至钢卷小车。
2.2.2.2 主要设备技术参数①1#步进梁: 10个卷位最大载重量: 10×38t=380t步进行程: 3m提升高度: 200 mm周期时间: 55 s②旋转台最大载重量: 38t旋转角度: 90度③2#步进梁: 5个卷位最大载重量: 5×38t=190t步进行程: 3m提升高度: 200 mm周期时间: 55 s④钢卷测宽测径装置:宽度测量行程:950 mm宽度测量精度:±5 mm外径测量行程:1000 mm外径测量精度:±5 mm⑤钢卷对中装置:对中行程:±200mm对中精度:±5 mm⑥自动拆捆机:捆带规格:宽度:31.75mm;厚度:0.8—1.2 mm;强度:600—1000N/ mm2捆带位置: 一根捆带:钢卷中心; 二根捆带:距钢卷中心±400 mm,偏差±50 mm拆捆周期:一根捆带:55 s;二根捆带:105.5 s废捆带斗容积:1 m3⑦1#、2#地辊站:辊子尺寸:Ø400×2300 mm转速: 50rpm⑧运卷小车:运输距离:到1#钢卷小车:2m到2#钢卷小车:4m最大行走速度:300 mm/sec.2.2.2.3 操作要点:2.2.2.3.1在条件具备的正常生产情况下,所有设备的操作模式均应选择为自动模式,不允许随意使用手动和维护模式。
2.2.2.3.2 钢卷准备及输送:1.指挥吊车在1#步进梁1—10号卷位上料,确认钢卷放置位置偏差不超过±200mm 范围。
2.根据生产计划对1#步进梁上钢卷的基本信息和外形质量进行确认,对不符合上卷质量要求的钢卷应及时通知原料库工处理,同时告知入口主控工。
3.对钢卷输送过程、测宽测径过程、对中过程、拆捆过程和弯带头过程、钢卷从2#步进梁输送至运卷小车等自动生产过程进行监控,在异常情况下进行必要的人工干预。
4.在手动操作模式下操作步进梁区域送料时,注意1#、2#步进梁与旋转台的连锁条件以及2#步进梁、旋转台与运卷小车的连锁条件。
2.2.2.3.3自动拆捆机操作:1.确认钢卷的捆带数,确认捆带的位置及间距,确认锁扣不在9时20分到11时30分的位置范围以及带头位于7点钟左右的位置,监视自动拆捆机的全自动拆捆过程。
2.对于捆带不在地辊凹槽处,应采取人工拆捆。
3. 对于锁扣在9时20分到11时30分的位置范围或带头不在7点钟左右位置的钢卷,通知入口主控工,待钢卷到达1#地辊站地辊上时,将2#步进梁和拆捆机选择手动操作模式,手动点动1#地辊站地辊,使锁扣不在9时20分到11时30分的位置范围或将带头转到7点钟左右的位置,然后将拆捆机选择到半自动操作模式,待拆捆机完成自动拆捆过程后,在拆捆机操作盘上按下“完成”按钮,再将2#步进梁选择到自动操作模式,同时通知入口主控工。
2.2.3 入口主操2.2.3.1 主要任务:按计划将经生产准备岗位操作工核实的钢卷号输入HMI的同步画面中作生产待用,未能跟队生产的钢卷经确认后及时在HMI画面中取消。
对正在运行的带钢进行监控,当带钢甩尾时,在七辊矫直机处对带尾矫直,在入口双切横剪处剪切带尾缺陷。
在下卷带钢穿带时,将带钢从钢卷小车处上卷至开卷机并开卷,穿带至七辊矫直机对带头矫直,在入口双切横剪处剪切带头缺陷,作好焊接准备。
待焊接完成后控制带钢在酸洗头部的运行,控制拉矫机的机械破鳞效果,与圆盘剪岗位和轧机主操岗位协调控制机组生产运行。
2.2.3.2 主要设备技术参数①钢卷小车:最大行走距离:约6m最大行走速度:最大提升高度:约1.2 m最大速度: 300 mm /s②开卷机:卷筒公称尺寸:Ø762 mm涨缩范围: 660一800 mm卷轴长度: 2465 mm传动:变频电机外支轴承:液压收缩,液压缸行程:450 mm ③防皱辊:防皱辊:1个,Ø 134×2300 mm支撑辊:12个,Ø 120×225 mm④夹送辊:尺寸:Ø 400×2300 mm开口度:100 mm上辊传动,下辊从动,并起导向作用穿带速度:60 m/min⑤七辊矫直机上辊:3个,Ø 180×2300 mm下辊:4个,Ø 150×1835 mm穿带速度:60 m/min甩尾速度:120 m/min啮合精度:±0.1 mm⑥入口双切横剪:剪刃长度:2300 mm剪刃高度:100 mm剪刃最大厚度:30 mm剪刃最小厚度:22 mm剪刃间隙:200 mm剪切带钢最大厚度:7.0 mm剪切带钢最大宽度:2100 mm剪切带钢强度:340—800N/m2剪切废料长度:800—1500 mm⑦拉矫机:延伸率:最大4.0%,精度0.1%带钢张力:最大600kN型式:两弯一矫弯曲单元:2套弯曲辊:80 mm(直径)×2300 mm支撑辊:120 mm(直径)×205 mm矫直单元:1套上辊:2个,300 mm(直径)×2300mm下辊:1个,80 mm(直径)×1900mm支撑辊:120 mm(直径)×225 mm2.2.3.3 操作要点:1. 在条件具备的正常生产情况下,所有设备的操作模式均应选择为自动模式,不允许随意使用手动和维护模式。
2. 在确认电气、机械液压条件具备的情况下,接通开卷机和入口活套张力,并启动除尘系统,然后开机运行。
3. 通过HMI画面和工业电视监控上卷、开卷、穿带或甩尾、带头尾矫直、带头尾剪切等自动上卷并穿带的全自动过程,同时在异常情况下进行必要的人工干预。
4. 监控带头尾在七辊矫直机处的矫直情况,如矫直效果不利于穿带,应对七辊矫直机的辊缝间隙进行必要调整,或通知维护人员检查辊子状况并作相应处理,以保证顺利自动穿带,必要时应选择就地点动穿带。
5. 监控带钢表面质量,并将有关缺陷通知焊接和圆盘剪岗位处理,对于带头尾缺陷应在入口双切横剪处剪切处理。
6. 监控带钢在拉矫机处的张力和延伸率变化情况,控制机械破鳞和板形改善效果。
7. 通过HMI画面观察入口活套套量,与圆盘剪主控岗位协调机组的运行速度,尽量避免酸洗工艺段的停车。
2.2.4 焊机主操2.2.4.1主要任务:对前后两卷带钢的头尾进行焊接,控制焊接质量,控制带钢在机组头部的运行,观察带钢在焊机1#张力辊处和从入口活套至2#张力辊段的跑偏情况,并告知入口主控岗位调整。
2.2.4.2 焊机2.2.4.2.1技术数据带钢尺寸:带钢宽度 830 — 2080 mm 偏差 0—+ 20 mm带钢厚度 1.5 — 6.0 mm 偏差 + / - 10%焊接限制条件:厚度差 (d2- d1)/ d2 = 30 % max (d=带钢厚度) d2-d1 = 1.0 mm (绝对值)宽度差焊接没有限制,但对于冲月牙max. 150 mm 每边带钢生产方向从左到右开口度:垂直 140 mm水平 2300 mm焊接小车行走速度(连续调节) min. 1 m / min.max. 15 m / min.碾平设备碾平力约50 kN激光焊接头压力约40 kN剪子剪切力约800 kN剪刃距离 140 mm夹紧装置主夹力约400 kN (每边)冲孔孔径 20 mm月牙剪与焊缝中心距离 2340 mm冲力约300 kN液压站推荐用油 HLP46 满足 DIN 51504粘度 4.5 o E (46 cSt) at 50 ℃压力 180 bar流量 260 l/min气动系统压力4.5 bar消耗415 l/min激光气及纯度 CO2 99,995 %He 99,996 %N2 99,999 %保护气 He 99,996 %电气参数主连接电压 380V/50Hz 3 相,允许偏差:max±10% V max± 1 Hz 主连接功率 600 kVA 3 phase控制电压 220V, 50 Hz电磁阀和PLC电压 24V DC; 220V AC接近开关 /光电管 24V DCUPS 220 V / 50 Hz ,2.5 kW外形尺寸(焊机主体) 宽度约10 m高度约7 m深度约14 m机器重量约200 t2.2.4.2.2操作要点:1、操作前的准备工作(1) 主电室送电①由主电室送上激光器、PLC、泵站和控制系统等各部分电源;②启动HMI(人机界面)计算机,进入“机器数据”屏幕;③启动QCDS(质量控制数据系统)计算机,进入质量数据曲线显示屏幕;④激光器控制面板将自动启动;(2) 启动液压泵站在HMI(人机界面)上先启动循环泵,待油温正常(无油温报警)后再启动一台主泵,在设定时间后将达到正常油压。