克服环氧树脂胶固化物的内在气泡问题
环氧树脂气泡消除方法

环氧树脂气泡消除方法
在环氧树脂制品中出现气泡是很常见的问题,但可以通过以下方法来消除气泡:
1. 搅拌:在制做环氧树脂混合物之前,应仔细搅拌两个组分(树脂和固化剂)以确保彻底混合。
使用机械搅拌器快速搅拌将有助于去除其中的气泡。
2. 震动:在倒入环氧树脂混合物之前,可以先将容器轻轻震动以帮助气泡从混合物中浮出。
可以使用震动盘、震动工具或者将容器放在振动平台上。
3. 真空脱气:将混合好的环氧树脂放入真空脱气罐中,并进行真空脱气处理。
这将帮助去除混合物中的气泡。
在真空脱气过程中,气泡会被拉伸和破裂,在真空中释放出。
4. 加热:在特定情况下,通过轻微加热树脂混合物也可以消除气泡。
加热可以降低混合物的粘度,从而使气泡更容易从混合物中升出。
5. 密实性检查:在制做环氧树脂制品时,尽量避免材料与模具之间的缝隙。
检查模具的密封性可以防止气泡在模具内部形成。
6. 慢搅拌:在搅拌和固化过程中,尽量使用缓慢的搅拌速度。
过快的搅拌会引入更多的空气,而慢搅拌可以减少气泡的形成。
在执行这些方法前,重要的是了解您使用的具体环氧树脂的特
性和制作过程的各个环节。
一般来说,通过精心操作和适当的处理方法,可以有效地消除气泡并制作出高质量的环氧树脂制品。
环氧水晶胶里产生气泡要如何处理?

环氧水晶胶所制出的产品透明如玻璃,适用于浇注、装饰、表面涂层或上光,但浇注工艺掌握不好易产生气泡,那么如何消除水晶胶里的气泡呢?环氧水晶胶:粘度低、流动性好、成形方便;接强度好,工艺性好,可常温或加温固化,操作方法,无色,无毒,无溶剂。
环氧水晶胶主要由环氧树脂和固化剂(也就是常说的AB料配置而成,在运输、搅拌过程中会产生少量的气泡,尽管物料中的消泡剂会对其起到很大的扼制作用,但由于某种原因仍难全部消除。
经专家介绍说,其原因主要有:大量的溶剂在物料中挥发而带出大量的气泡,粘度大。
气泡不容易释放,温度低,使水晶胶的粘度大大增加,气泡释放困难,固化过程太快而来不及释放气泡,浇注体复杂,固化物太厚,气泡无法从模腔和料体中跑出。
针对以上原因,处理的办法其实并不复杂:一、是尽可能使用无溶剂的水晶胶,杜绝使用物理性添加溶剂的产品,如添加无机溶剂的料,更不能为了降低成本而添加苯、丙酮、醇类等有毒有害的产品,从根本上消除气泡的产生根源;二、是在施工的应许下尽可能选择粘度低的水晶胶(环氧ab胶)(在非平面体上加工只能另当别论,在平面上加工且物料浇的厚度不是特别厚的。
就无需一定抽真空,只需要用吹头发的吹风机的热风在物料浇注好了后的1小时内,常温将浇注后的产生的泡泡吹掉,或用针捅掉汽泡再用电吹风将浇注体吹平即可;三、气温低会使物料粘度变大,特别是冬天气泡更加不容易排出,为此可以先将AB料分别装在不同的容器中加温,其中A剂预35-40度,这样会使物料粘度变小,气泡得到释放,但一定要等加温的物料冷却至30度以下才能称量将AB料相拌,否则会使常固化的物料变相成为加温固化,引起急剧固化,造成浪费物料,当然也可单一的加温A或B料,但同样需要按冷却后才能相拌。
AB物料在相溶搅拌过程中也会产生少量气泡,所以搅拌时不要太猛烈,搅拌均匀后可以静止一会,不抽真空的不要马上浇注,加温固化时不要把温度一下加的很高,因为过高的温度会使物料表面很快凝胶,使里面的气泡无法跑出来,相反一个适当的温度会使物料粘度很稀,固化过程较慢,放热反应产生的气泡很少,而这些气泡又很容易在低粘度的物料中跑出来,按照经验,30-35度5小时后再升温完全固化是较好的。
降低封胶起泡故障的工艺优化

降低封胶起泡故障的工艺优化发布时间:2021-04-12T10:08:22.500Z 来源:《科学与技术》2020年36期作者:孔义,吕耀哥,刘承盟[导读] 在汽车零部件加工过程中,为保证密封效果或固定作用孔义,吕耀哥,刘承盟摘要:在汽车零部件加工过程中,为保证密封效果或固定作用,封胶是一种常见工艺,但密封胶固化后表面容易产生起泡故障,一直困扰着工艺设计人员。
本文主要针对双组份环氧树脂类密封胶,介绍起泡故障的原因分析,使用一种封胶工艺方案,可降低密封胶固化后的起泡故障。
关键词:封胶; 起泡; 工艺优化1、密封胶使用及起泡现象1.1、密封胶说明双组份环氧树脂胶由A组分(树脂)和B组分(固化剂)按一定比例混合使用,具有优良的机械和电绝缘性能,可室温或加温固化,粘度低,易灌封,其固化物表面光泽好,无白雾,适用于多种电子电器封装与粘接。
1.2、起泡现象该密封胶灌封至体积较小的一种传感器腔体内,经过室温固化后,表面存在气泡破开(图1)或鼓起(图2)现象,比例约4%~5%。
2、原因分析2.1、初步分析结合其他密封胶的的使用经验,分析气泡产生主要有以下三个原因:通过上表,锁定了七个怀疑原因:①密封胶料桶内有气体、②搅拌产生气泡、③灌输管路有气体、④产品设计凹槽、⑤产品设计憋气、⑥塑料件注塑不良、⑦密封胶与环境潮气反应产生气体。
2.2、原因锁定2.2.1、密封胶有气泡的原因确认原因①确认:从料桶内倒出密封胶,观察密封胶表面,未发现气泡(图3),排除原因①;原因②确认:密封胶搅拌后,观察密封胶表面,存在较多细小气泡,在灌封及固化的过程中,这些气体没有排出,在表面形成了气泡,表现为针眼状(图4),锁定原因②;原因③确认:将搅拌后的密封件通过抽真空后,细小气泡消失,灌封后观察密封胶表面,未发现气泡,或一段时间后未发现气泡冒出,排除原因③;2.2.2、工件内部有气体的原因确认原因④确认:观察灌封的工件内腔,插针根部存在凹槽(图5),锁定原因④;原因⑤确认:调查此类工件,为金属与塑料件铆压成型,金属底端不透气,铆接后工件内部存在憋气现象(上下不通气),锁定原因⑤;原因⑥确认:X光下观察起泡工件的塑料件,为发现气泡,解剖后也未发现气泡(图6),排除原因⑥;其中,针对原因④和⑤,密封胶灌封后,若工件内部有气体或有凹槽,固化过程中工件内部的气体很难排出,如果密封胶灌封厚度较厚的话,气体更不容易排出,表现为鼓起状。
双组份环氧树脂胶的固化方式

双组份环氧树脂胶的固化方式
双组份环氧树脂胶的固化方式主要包括以下步骤:
1. 混合:将配制好的环氧树脂和固化剂按照一定的比例混合在一起。
混合可以采用手工搅拌或机械搅拌的方式,确保两个组分充分混合。
2. 化学反应:混合后的环氧树脂和固化剂发生化学反应,这是固化反应的关键步骤。
固化剂中的活性基团与环氧树脂中的环氧基团发生开环反应,形成交联结构。
这个反应过程称为环氧树脂的固化或聚合。
3. 固化时间:从混合开始到胶水完全固化所需的时间称为固化时间。
这个时间取决于胶水的配方、环境温度和固化剂的活性等因素。
根据不同的胶水类型和配方,固化时间可以从几分钟到几小时不等。
此外,为了确保双组份环氧树脂胶的顺利固化,还需要注意以下几点:
1. 施胶:将混合好的胶水涂布在需要粘接的表面上,可以使用刷子、滚筒或喷涂等方式进行施胶,确保胶水均匀覆盖整个粘接面。
2. 温度:温度是影响双组份环氧树脂胶固化速率的重要因素。
在适当的温度范围内,较高的温度可以加快固化反应速率。
但是,温度过高可能会导致胶水出现焦化或变色等不良现象。
3. 排气:在施胶过程中,应将胶水中的气泡排出,以免对固化过程产生不良影响。
可以将混合好的胶水放置在真空室中进行排气处理。
4. 操作时间:双组份环氧树脂胶的操作时间是指在一定时间内,胶水仍保持良好的工艺性能,可以进行施胶操作的时间。
操作时间的长短取决于胶水的配方和环境温度等因素。
通过遵循以上步骤和注意事项,可以有效地实现双组份环氧树脂胶的顺利固化,并获得良好的粘接效果。
环氧树脂的固化——高化实验报告

环氧树脂的固化2011011743 分1 黄浩一、实验目的1.了解高分子化学反应的基本原理及特点2.了解环氧树脂的制备及固化反应的原理、特点二、实验原理环氧树脂(epoxy resins),是指分子中带有两个或两个以上环氧基的低分子量物质及其交联固化产物的总称,是一种热固性树脂。
其最重要的一类是双酚A型环氧树脂,它是由环氧氯丙烷与双酚A 在氢氧化钠作用下聚合而成:如下图所示,双酚A环氧树脂中末端的活泼的环氧基和侧羟基赋予树脂反应活性,使它可以与交联剂作用,从而交联成三维结构,即固化;双酚A的苯环骨架提供强韧性和耐热性,亚甲基链赋予树脂柔韧性,这使得它的综合性能优异,可以用作特种塑料;羟基和醚键的高度极性,使环氧树脂分子与相邻界面产生了较强的分子间作用力,而且因环氧基的高活性,使得它固化速度很快,从而可以作为粘结剂,商业上称作“万能胶”。
因为环氧树脂在未固化前是呈热塑性的线型结构,要实现它的各种功能,必须加入固化剂,与环氧树脂的环氧基等反应,变成网状结构的大分子,成为不溶不熔的热固性成品。
固化剂的种类很多,可以根据分子结构分为如下三类:1、胺类固化剂:胺类固化剂可分为脂肪胺型和芳香胺型。
脂肪胺型使用比较普遍,硬化速度快、黏度低、使用方便,但固化剂本身的毒性较大、易升华,固化后形成的胶层脆性大、粘结强度不高、耐热性和介电性较差等。
芳香胺型形成的固化物可在100~150℃长期使用,粘接强度高,耐化学试剂和耐老化性能好,但作为结构胶使用韧性不够,还需要增韧改性。
根据有机化学的知识,要使环氧开环成羟基,必须使用一二级胺,因为它们含有活泼氢原子,使环氧基开环生成羟基,生成的羟基再与环氧基起醚化反应,最后生成网状或体型聚合物。
三级胺只可进行催化开环,环氧树脂的环氧基被叔胺开环变成阴离子而非羟基,一般而言,不直接用作固化剂,常常与酸酐类固化剂联用。
2、酸酐类固化剂:硬化反应较平稳,硬化过程中放热少,使用寿命长,毒性较小,硬化后树脂的力学性能较好。
环氧树脂气泡消除方法
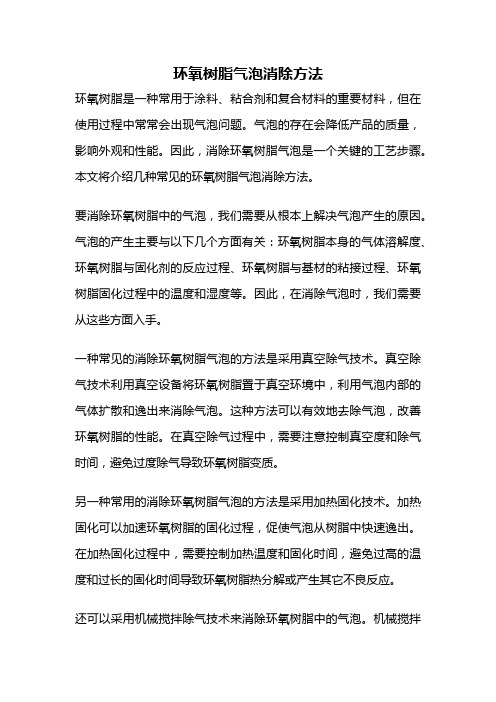
环氧树脂气泡消除方法环氧树脂是一种常用于涂料、粘合剂和复合材料的重要材料,但在使用过程中常常会出现气泡问题。
气泡的存在会降低产品的质量,影响外观和性能。
因此,消除环氧树脂气泡是一个关键的工艺步骤。
本文将介绍几种常见的环氧树脂气泡消除方法。
要消除环氧树脂中的气泡,我们需要从根本上解决气泡产生的原因。
气泡的产生主要与以下几个方面有关:环氧树脂本身的气体溶解度、环氧树脂与固化剂的反应过程、环氧树脂与基材的粘接过程、环氧树脂固化过程中的温度和湿度等。
因此,在消除气泡时,我们需要从这些方面入手。
一种常见的消除环氧树脂气泡的方法是采用真空除气技术。
真空除气技术利用真空设备将环氧树脂置于真空环境中,利用气泡内部的气体扩散和逸出来消除气泡。
这种方法可以有效地去除气泡,改善环氧树脂的性能。
在真空除气过程中,需要注意控制真空度和除气时间,避免过度除气导致环氧树脂变质。
另一种常用的消除环氧树脂气泡的方法是采用加热固化技术。
加热固化可以加速环氧树脂的固化过程,促使气泡从树脂中快速逸出。
在加热固化过程中,需要控制加热温度和固化时间,避免过高的温度和过长的固化时间导致环氧树脂热分解或产生其它不良反应。
还可以采用机械搅拌除气技术来消除环氧树脂中的气泡。
机械搅拌可以通过剧烈的搅拌运动来破坏气泡的表面张力,使气泡快速破裂和逸出。
在机械搅拌过程中,需要注意搅拌速度和时间的控制,避免过高的速度和过长的时间导致环氧树脂的过度剪切和变质。
还可以采用添加消泡剂的方法来消除环氧树脂中的气泡。
消泡剂是一种能够降低液体表面张力的物质,可以有效地破坏气泡的表面张力,使气泡快速破裂和逸出。
在使用消泡剂时,需要注意添加剂的种类和用量的选择,避免过量添加剂导致环氧树脂性能的下降。
消除环氧树脂中的气泡是一个关键的工艺步骤。
我们可以采用真空除气、加热固化、机械搅拌和添加消泡剂等多种方法来消除气泡。
在具体操作中,需要根据环氧树脂的特性和工艺要求选择合适的方法,并注意控制各个参数,避免产生其它问题。
环氧树脂固化反映阻碍固化反映的因素

环氧树脂固化反映--阻碍固化反映的因素在环氧树脂固化反映中,环氧树脂、固化剂及固化增进剂的结构是阻碍固化反映的内在因素;固化反映温度、空气中二氧化碳及溶剂等是阻碍固化反映的外在条件。
在固化反映体系中,内在因素与外在条件交互作用,使环氧树脂固化反映呈现出不同的历程。
因此,科学地把握、合理地运用各类阻碍因素,是实现理想固化反映的任务。
一、反映物结构的阻碍1.环氧树脂结构环氧树脂分子主链结构区别专门大,如双酚A 型环氧树脂分子主链上主若是双酚A 重复单位结构;脂环族环氧树脂分子主链上主若是脂肪环结构;缩水甘油氨型环氧树脂分子中含有氮原子;有机硅乡试性环氧树脂分子中含有硅原子;酮醛环氧树脂分子主链上主若是环己酮(含羰基的脂肪环)重复单位结构等等。
另外采纳丙烯酸或不饱和脂肪酸与环氧树脂反映,取得丙烯酸环氧酯或脂肪酸环氧酯的分子中含有碳-碳双键,与含环氧基的环氧树脂具有完全不同的固化反映机理。
环氧树脂(含环氧酯)由于分子结构不同,在与含活泼氢化合物、含质子给予体化合物、合成树脂及引发剂等进行固化反映时具有不同的活性。
双酚A 型环树脂和脂肪族柔性环氧树脂与胺别离进行加成固化反映时,其固化反映速度前者大于后者;被选取E-4 酮醛环氧树脂、HW-28 有机硅改性环氧树脂和E-44 双酚A 型环氧树脂与300聚酰胺在30~35℃下进行固化反映时,其配方组成为环氧树脂:300聚酰胺1:0.5(eq),固化反映结果见表2-13。
表2-13 环氧树脂固化成效比较环氧树脂名称固化成效(硬度/h)E-44 环氧树脂0.75/40 HW-28 有机硅环氧树脂0.75/150 E-4 酮醛环氧树脂0.50/218 由表2-13 知,由于三种环氧树脂分子结构各异,那么与同种胺类进行固化反映时,达到规定硬度值的时刻相差专门大,尤其是E-4 酮醛环氧树脂与300聚酰胺反映218h 后,硬度值只达到0.50。
环氧树脂分子中含有吸电子基团时,会投闲置散加与路易斯碱(亲核试剂)固化剂的反映速度、而降低与路易斯酸(亲电试剂)固化剂的反映速度;环氧树脂分子中含有给电子基团时,会增加与路易斯酸固化剂的反映速度,降低与路易斯碱固化剂的反映速度。
双组份环氧胶_固化机理_解释说明以及概述

双组份环氧胶固化机理解释说明以及概述1. 引言1.1 概述双组份环氧胶作为一种常见的结构胶,广泛应用于各个领域,具有良好的粘接性能和耐化学品腐蚀性。
它由两个成分组成:环氧树脂和固化剂。
在固化过程中,这两个组分发生化学反应,形成胶体并硬化。
本文将重点讨论双组份环氧胶的固化机理,并探讨影响固化过程的因素以及解决方法。
1.2 文章结构本文共分为五个部分进行阐述。
在引言部分,我们将对双组份环氧胶进行概述,并介绍文章的结构和目的。
其次,在第二部分中,我们将详细介绍双组份环氧胶的基本概念、特点、成分和性质以及应用领域。
第三部分将解析双组份环氧胶的固化机理,包括固化剂与环氧树脂反应机制、温度和压力对固化过程的影响以及添加剂对固化速度和性能的影响。
接着,在第四部分中,我们将讨论影响环氧固化反应的主要阻碍因素,并提供相应的解决方法。
最后,在第五部分中,我们将对双组份环氧胶的固化机理进行总结,展望其未来应用,并提出未来研究方向和建议。
1.3 目的本文的目的是通过深入研究和详细解释双组份环氧胶的固化机理,使读者了解其基本概念、特点和成分,并了解其在各个领域中的应用。
同时,本文还旨在探讨固化过程中遇到的问题,并提供相关的解决方法。
通过本文的阐述,读者将能够更好地理解双组份环氧胶固化机理,并为未来研究和应用提供参考和指导。
2. 双组份环氧胶的基本概念和特点2.1 双组份环氧胶的定义双组分环氧胶是由两种不同成分组成的一种胶粘剂,其中一种成分为环氧树脂,另一种成分为固化剂。
这两种成分在使用之前需要分别储存在两个不同的容器中,混合使用时发生化学反应,形成坚固耐用的胶体。
2.2 双组份环氧胶的成分和性质(1)环氧树脂:环氧树脂是双组份环氧胶中的一部分,在固化过程中起到主要结构形成的作用。
它具有良好的粘接性、机械性能和耐腐蚀性,并且在低温下也能够硬化。
(2)固化剂:固化剂是双组份环氧胶中的另外一个关键部分,它与环氧树脂发生反应并使其硬化。
- 1、下载文档前请自行甄别文档内容的完整性,平台不提供额外的编辑、内容补充、找答案等附加服务。
- 2、"仅部分预览"的文档,不可在线预览部分如存在完整性等问题,可反馈申请退款(可完整预览的文档不适用该条件!)。
- 3、如文档侵犯您的权益,请联系客服反馈,我们会尽快为您处理(人工客服工作时间:9:00-18:30)。
克服环氧树脂胶固化物的内在气泡问题
环氧树脂胶固化物肯定将要产生起泡问题,假如是表面的气泡还只是导致表观或者是密封性的问题,假如是内在的气泡,简要影响到机械性能和电气性能,本文并未讨论生产胶的厂家对气泡的处理,只是简单的谈到了使用者碰到的问题,那么我们就先要了解下真空的概念和设备然后是气泡的克服问题。
真空定义指没有任何实物粒子存在的空间,地球上什么都没有的空间是不存在的就是真空不空,所以气泡对环氧树脂胶影响只能降到最低,不能完全消除。
真空度:压强低于101325帕斯卡(也即一个标准大气压强约101KPa)的气体状态,真空度的标识通常有两种方法:1、是用“绝对压力”、“绝对真空度”(即比“理论真空”高多少压力)标识;在实际情况中,真空泵的绝对压力值介于0~101.325KPa之间。
绝对压力值需要用绝对压力仪表测量,在20℃、海拔高度=0的地方,用于测量真空度的仪表(绝对真空表)的初始值为101.325KPa(即一个标准大气压)。
2、是用“相对压力”“相对真空度”(即比“大气压”低多少压力)来标识。
"相对真空度"是指被测对象的压力与测量地点大气压的差值。
用普通真空表测量。
在没有真空的状态下(即常压时),表的初始值为0。
当测量真空时,它的值介于0到-101.325KPa(一般用负数表示)之间。
例如:真空泵测量值为-75KPa,则表示泵可以抽到比测量地点的大气压低75KPa的真空状态,国际真空行业通用的“真空度”,也是最科学的是用绝对压力标识;指得是“极限真空、绝对真空度、绝对压力”,但“相对真空度”(相对压力、真空表表压、负压)由于测量的方法简便、测量仪器非常普遍、容易买到且价格便宜,因此广泛应用。
理论上二者是可以相互换算的,两者换算方法如下:相对真空度=绝对真空度(绝对压力)-测量地点的气压,例如:真空泵的绝对压力为80KPa,则它的相对真空度约为80-100=-20Kpa,(测量地点的气压假设为100KPa)在普通真空表上就该显示为-0.02MPa,常用的真空度单位有Pa、Kpa、Mpa、大气压、公斤(Kgf/cm2)、mmHg、mbar、bar、PSI等。
近似换算关系如下:1MPa=1000KPa 1KPa=1000Pa 1大气压=100KPa=0.1MPa 1大气压=1公斤(Kgf/cm2)=760mmHg 1大气压=14.5PSI 1KPa=10mbar 1bar=1000mbar 1Torr=133.3Pa 1Pa=0.0075torr=0.0075mmHg=0.01mbar=0.0000001Mpa
现在常用的真空形式为:旋片真空泵,其出口绝对真空是0.05Pa,而上图中的真空显示形式为相对真空,把绝对真空0.05Pa换算为相对真空即为:0.00025KPa-101.325KPa =-101.32475KPa,其相对真空就是-0.10132475MPa,所以该表无法显示旋片泵的绝对真空。
生产时候的真空使用生产时生产设备和工艺原因造成电子灌封胶进入大量的空气,其微小的填料和树脂结合处的空隙、机械混入空气、树脂体系的微量低分子挥发物,对于近于绝对的真空状态,再微小的空气都是巨大的,成本导致生产真空设备的真空度只能为:100-1000Pa,是无法满足客户使用时候的真空要求,以对电子灌封胶要求最高的行业“高压包”为例,这种产品需要选用高温体系固化的环氧体系,原因是其高温下电气特性好,并在A/B混合后有较长的使用时间和在混合后可以加温A/B混合物,而使粘度更低利于脱泡,工艺制定为A 组份在60-80℃,真空度在100-250Pa,脱泡至液体表面无气泡升起为止。
B料一般在40-50 ℃脱泡,真空度为100-250Pa ,因为其挥发比较大,此处真空就是为去除混合料液的时候产生的气泡,当然我们非常愿意配合客户研制有更高真空生产和最低的挥发物的产品,除泡后的A/B料液在真空度100-250Pa的条件下混合,混合物的温度控制在50-70 ℃,混合温度高流动性好,更容易浇注和脱泡,但会缩短最低流动时间。
把被灌封的元件在高温110 ℃下除尽潮气,在元件还是>70 ℃的时候灌封,在元件灌封前应在真空100Pa的条件下真空保压60秒或越久越好,为避免料液飞溅在真空500-2000Pa下浇注,视产品要求和料液的溢流状态,然后保压在100-2000Pa,真空越低越好,时间越久越好。
非常值的关注的是,旋片真空系统是依靠真空油达到最佳真空,是不适宜化学方面使用的,因为物料中挥发的化学分子和各种因素下带来的水汽积容易破坏真空油,导致真空失效和真空油的损失,水非常容易乳化真空油,其在50 ℃时真空12000Pa已经会汽化被真空机泵收集,在真空600Pa时候,即便是0 ℃的水也会被真空泵收集,但旋片真空是目前最高真空、最经济的形式,如此在真空容器和真空泵见应加有气化的液体收集器是唯一选择。