整车制动力计算
制动系统计算说明书

制动器的计算分析整车参数2、制动器的计算分析前制动器制动力前制动器规格为ɸ310×100mm,铸造底板,采用无石棉摩擦片,制动调整臂臂长,气室有效面积。
当工作压力为P=6×105Pa时,前制动器产生的制动力:F1=2*A c*L/a*BF*ɳ*R/R e*P桥厂提供数据在P=6×105Pa时,单个制动器最大制动力为F1=3255kgf以上各式中:A c—气室有效面积L—调整臂长度a—凸轮基圆直径BF—制动器效能因数R—制动鼓半径R e—车轮滚动半径ɳ—制动系效率P—工作压力后制动器制动力后制动器规格为ɸ310×100mm,铸造底板,采用无石棉摩擦片,制动调整臂臂长,气室有效面积。
当工作压力为P=6×105Pa时,前制动器产生的制动力:F2=2*A c*L/a*BF*ɳ*R/R e*P桥厂提供数据在P=6×105Pa时,单个制动器最大制动力为F2 =3467kgf满载制动时的地面附着力满载制动时的地面附着力是地面能够提供给车轮的最大制动力,正常情况下制动气制动力大于地面附着力是判断整车制动力是否足够的一个标准。
地面附着力除了与整车参数有关之外,还与地面的附着系数有关,在正常的沥青路面上制动时,附着系数ϕ值一般在~之间,我们现在按照路面附着系数为来计算前后地面附着力:Fϕ前=G×ϕ+G×ϕ2满1=2200×+6000××=2002kgfFϕ后=G满2×ϕ-G×ϕ23800×××==1487kgf因为前面计算的前后制动器最大制动力分别为F1=3255kgfF2=3467kgf3、制动器热容量、比摩擦力的计算分析单个制动器的比能量耗散率的计算分析前制动器的衬片面积A1=2×πR1××L1=式中(L1=100mm摩擦片的宽度w1=110°)后制动器的衬片面积A2=2×πR2××L2=式中(L2=100m m 摩擦片的宽度w2=)比能量耗散率e1=β=e2=β=上式中:G—满载汽车总质量V1—制动初速度,计算时取V1=18m/sβ—满载制动力分配系数t—制动时间,计算时取t=鼓式制动器的比能量耗散率以不大于mm2为宜,故该制动器的比能量耗散率满足要求。
制动力计算公式

制动力计算公式
一、一轴(前轴)制动力
一轴制动率=(左前轮制动力+右前轮制动力)/ [(左前轮荷重+右前轮荷重) ×9.8] 当一轴制动率>=60% 为合格
一轴不平衡率=(左前轮过程差最大制动力-右前轮过程差最大制动力)/ 两个前轮中最大制动力
当一轴不平衡率<=20% 为合格
二、二轴(后轴)制动力
二轴制动率=(左后轮制动力+右后轮制动力)/ [(左后轮荷重+右后轮荷重) ×9.8] 二轴制动率不做判定
当二轴制定率>=60%时,二轴不平衡率用下式计算;
二轴不平衡率=(左后轮过程差最大制动力-右后轮过程差最大制动力)/ 两个后轮中最大制动力
二轴不平衡率<=24% 为合格
当二轴制定率<60%时,二轴不平衡率用下式计算;
二轴不平衡率=(左后轮过程差最大制动力-右后轮过程差最大制动力)/ [(左后轮荷重+右后轮荷重) ×9.8]
二轴不平衡率<8%时为合格
三、手制动力(手刹)
手制动率=(左轮制动力+右轮制动力)/四个车轮荷重之和×9.8
手制动率>=20%为合格
四、整车制动
整车制动率=四个车轮制动力之和/四个车轮荷重之和×9.8
整车制动率>=60% 为合格。
制动力计算方法

《机动车运行安全技术条件》(GB7258-2004)有关制动方面的:1.1 台试检验制动性能1.1.1 行车制动性能检验1.1.1.1 汽车、汽车列车在制动检验台上测出的制动力应符合表 6 的要求。
对空载检验制动力有质疑时,可用表 6 规定的满载检验制动力要求进行检验。
摩托车及轻便摩托车的前、后轴制动力应符合表 6 的要求,测试时只允许乘坐一名驾驶员。
检验时制动踏板力或制动气压按7.13.1.3 的规定。
表 6 台试检验制动力要求1.1.1.2 制动力平衡要求(两轮、边三轮摩托车和轻便摩托车除外)在制动力增长全过程中同时测得的左右轮制动力差的最大值,与全过程中测得的该轴左右轮最大制动力中大者之比,对前轴不应大于20% ,对后轴(及其它轴)在轴制动力不小于该轴轴荷的60% 时不应大于24%;当后轴(及其它轴)制动力小于该轴轴荷的60% 时,在制动力增长全过程中同时测得的左右轮制动力差的最大值不应大于该轴轴荷的8% 。
依据国标要求,对前轴以外的制动力平衡计算分两种情况:1、当该轴制动制动率 >= 60%时,过程差最大差值点的两个力分别为f1和f2,如果f1 >= f2 不平衡率 = (f1 –f2)/f1 * 100 ;如果f1 < f2不平衡率 = (f2 –f1)/f2 * 1002、当该轴制动制动率 < 60%时,过程差最大差值点的两个力分别为f1和f2,如果f1 >= f2 不平衡率 = (f1 –f2)/轴重 * 100 ;如果f1 < f2不平衡率 = (f2 –f1)/轴重 * 100注意:以上为简约的计算,较为准确的计算要注意单位之间的换算:轴重是kg,制动力的单位是10N例如:轴重最大左最大右差值左差值右制动率不平衡率2074 543 508 543 508 50.7 1.7二轴不平衡率( 543-508)*10/(2074*9.8)*100= 1.722%有关制动台仪表制动台仪表的不平衡率算法说明书没有给出,不清楚其算法,对于前轴有可能是对的,对于后轴等仪表算法可定是错误的,制动台本身不能得到车辆的轴重,也就不能判断制动率是否 >=60,也就不能得出不平衡率。
制动计算公式
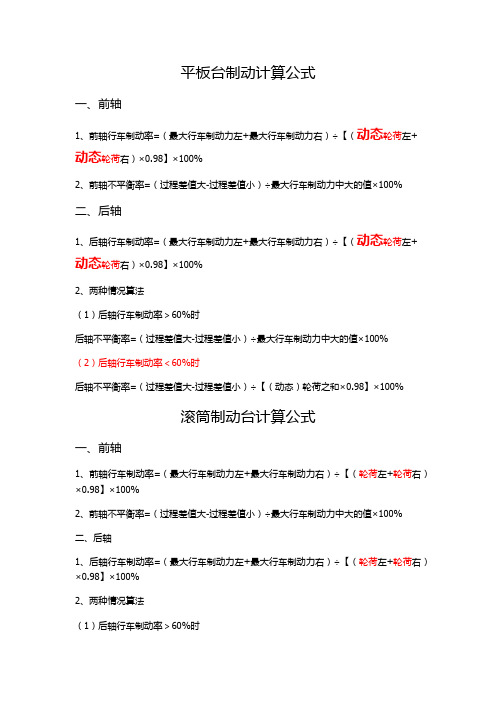
平板台制动计算公式一、前轴1、前轴行车制动率=(最大行车制动力左+最大行车制动力右)÷【(动态轮荷左+动态轮荷右)×0.98】×100%2、前轴不平衡率=(过程差值大-过程差值小)÷最大行车制动力中大的值×100%二、后轴1、后轴行车制动率=(最大行车制动力左+最大行车制动力右)÷【(动态轮荷左+动态轮荷右)×0.98】×100%2、两种情况算法(1)后轴行车制动率>60%时后轴不平衡率=(过程差值大-过程差值小)÷最大行车制动力中大的值×100%(2)后轴行车制动率<60%时后轴不平衡率=(过程差值大-过程差值小)÷【(动态)轮荷之和×0.98】×100%滚筒制动台计算公式一、前轴1、前轴行车制动率=(最大行车制动力左+最大行车制动力右)÷【(轮荷左+轮荷右)×0.98】×100%2、前轴不平衡率=(过程差值大-过程差值小)÷最大行车制动力中大的值×100%二、后轴1、后轴行车制动率=(最大行车制动力左+最大行车制动力右)÷【(轮荷左+轮荷右)×0.98】×100%2、两种情况算法(1)后轴行车制动率>60%时后轴不平衡率=(过程差值大-过程差值小)÷最大行车制动力中大的值×100% (2)后轴行车制动率<60%时后轴不平衡率=(过程差值大-过程差值小)÷【轮荷之和×0.98】×100% 注:(1)机动车纵向中心线位置以前的轴为前轴,其他轴为后轴;(2)挂车的所有车轴均按后轴计算;(3)用平板台测试并装轴制动力时,并装轴可视为一轴整车制动率整车制动率=最大行车制动力÷(整车轮荷×0.98)×100%驻车制动率驻车制动率=驻车制动力÷(整车轮荷×0.98)×100%台式检验制动率要求(空载)台式检验制动力要求(加载)台式检验制动力不平衡率要求(空载和加载)。
制动力计算公式

制动力计算公式
一、一轴(前轴)制动力
一轴制动率=(左前轮制动力+右前轮制动力)/ [(左前轮荷重+右前轮荷重)x9.8]
当一轴制动率>=60% 为合格
一轴不平衡率=(左前轮过程差最大制动力-右前轮过程差最大制动力)/ 两个前轮中最大制动力
当一轴不平衡率<=20% 为合格
二、二轴(后轴)制动力
二轴制动率=(左后轮制动力+右后轮制动力)/ [(左后轮荷重+右后轮荷重)x9.8]
二轴制动率不做判定
当二轴制定率>=60%时,二轴不平衡率用下式计算;
二轴不平衡率=(左后轮过程差最大制动力-右后轮过程差最大制动力)/ 两个后轮中最大制动力
二轴不平衡率<=24% 为合格
当二轴制定率<60%时,二轴不平衡率用下式计算;
二轴不平衡率=(左后轮过程差最大制动力-右后轮过程差最大制动力)/ [(左后轮荷重+右后轮荷重)x9.8]
二轴不平衡率<8%时为合格
三、手制动力(手刹)
手制动率=(左轮制动力+右轮制动力)/四个车轮荷重之和X9.8
手制动率>=20%为合格
四、整车制动
整车制动率=四个车轮制动力之和/四个车轮荷重之和X9.8
整车制动率>=60% 为合格。
制动率和不平衡率

二轴不平衡率<=24% 为合格
当二轴制定率<60%时,二轴不平衡率用下式计算;
二轴不平衡率=(左后轮过程差最大制动力-右后轮过程差最大制动力)/ [(左后轮荷重+右后轮荷重)x9.8]
二轴不平衡率<8%时 为合格
三、手制动力(手刹)
手制动率=(左轮制动力+右轮制动力)/四个车轮荷重之和X9.8
一、一轴(前轴)制动力
一轴制动率=(左前轮制动力+右前轮制动力)/ [(左前轮荷重+右前轮荷重)x9.8]
当一轴制动率>=60% 为合格
一轴不平衡率=(左前轮过程差最大制动力-右前轮过程差最大制动力)/ 两个前轮中最大制动力
当一轴不平衡率<=20% 为合格
二、二轴(后轴)制动力
二轴制动率=(左后轮制动力+右后轮制动力)/ [(左后轮荷重+右后轮荷重)x9.8]
二轴制动率不做判定
当二轴制定率>=60%时,二轴不平衡率用下式计算;
二轴不平衡率=(左后轮过程差最大制动力-右后轮过程差最大制动力)/ 两个后轮中最大制动力
手制动率>=20%为合格
四、整车制动
整车制动率=四个车轮t;=60% 为合格
五、灯光
两灯制 新车 光强>18000
两灯制 旧车 光强>15000
四灯制 新车 光强>15000
汽车制动系统计算

后
b.
F1
Gb L hg
jd1 max
F1 m
g b L hg
前
F 2
Ga L hg
j d 2 max
F 2 m
g a L hg
制
S
1 3.6
(t1
t2 ) v 2
v2 25.92 jmax
根
a
2
b
L
g g
0 .8
各个设计方案均能满足法规对行车制动性能的要求,同时也满足设计要求。 4 ) 助施力器失效时,制动力完全由人力操纵踏板产生,最大踏板力要求:N1类车700N。 加
△g2—鼓式制动器的蹄、鼓间隙
△g3—鼓式制动器摩擦衬片的厚度公差
(3)储油壶总容量Vmax
空载同步附着系数
0
车满载同步附着系数
' 0
型
标杆
方案
P201-NAM-SD-DP-G3-2
选配方案(四轮盘式)
Fif
Fir
图2 车型的I曲线与β线 ©版权归江淮汽车股份有限公司所有 未经授权禁止复制
第 4 页,共 13 页
制动系统方案设计计算说明书
P201-NAM-SD-DP-G3-2
通 过 1、在空载状态下,地面附着系数为0.8,标杆管路压力达到6MPa,管路压力达到5MPa,选 配方案管路压力达到5MPa,制动器发生抱死,此时后轴早于前轴抱死,这时整车稳定性非常差 。需要ABS进行调节。
n1、n2—前、后制动器单侧油缸数目(仅对盘式制动器而言)
Kv—考虑软管膨胀时的主缸容积系数,汽车设计推荐:轿车 =1.1,货车 =1.3
其中 要根据制动器的类型、参考同类车型确定,对鼓式制动器:汽车设计推荐δ=2-2.5mm;汽车工 程手册推荐3.5-5.5(考虑软管膨胀量及磨损间隙不能自调的影响),公司目前车型均可实现间隙
整车制动力计算

45%的坡道 0.422
116731 339329
下 PX70 =
汽车满载质量(t)
100 空载质量
轮胎半径 (m)
轴距L(m)
0.719 4.595
附着系数 重心高hg
0.5 2.57
0
理想(前中 后先后或同
整车所需制动力 前桥制动力
时抱死) 中后桥制动力
456060 78905
377155
满载时,前桥至重 重力加速
心的距离a
475528 82273
时抱死) 中后桥制动力
393255
一 TL100 定
汽车满载质量(t)
轮胎半径 (m)
轴距L(m)
100
0.769
4.45
坡
空载质量
附着系数 重心高hg 0.5 3.032
度 理想(前中 整车所需制动力
情 后先后或同
456060
况 时抱死)
下
坡
度 理想(前中
情 后先后或同 前桥制动力 况 时抱死) 中后桥制动力
0.5 3.032
情 理想(前中 整车所需制动力 后先后或同 前桥制动力
475528 121714
况 时抱死) 中后桥制动力
353814
下 PX70
汽车满载质量(t)
轮胎半径 (m)
轴距L(m)
100
0.719 4.595
空载质量
附着系数 重心高hg
=
0.5 2.57
0
理想(前中 后先后或同
整车所需制动力 前桥制动力
3.8
9.81
整车产生制动力矩 前桥产生制动力矩 中后桥产生制动力 矩
359500 N·m 162733 N·m