(英文)无掩膜光刻的模式生成系统
光刻的四条技术路线

光刻的四条技术路线
1. 接触式光刻(Contact Lithography):此技术路线将掩模直接与光刻胶接触,通过紫外光照射来传导图案。
接触式光刻具有高分辨率和高精度的特点,但会产生掩模和光刻胶之间的化学反应。
2. 脱接触式光刻(Proximity Lithography):在脱接触式光刻中,光刻胶和掩模之间仅存在微小的距离,而不接触彼此。
当紫外光照射时,通过距离短暂拉近并拉开来传递图案。
脱接触式光刻比接触式光刻更容易控制化学反应,但相对于接触式光刻的分辨率和精度较低。
3. 投影式光刻(Projection Lithography):这是最常用的光刻技术路线之一。
先通过光学方式将掩模上的图案投射到光刻胶的表面上。
投影式光刻的特点是具有高分辨率和高通量,但需要复杂的光学系统。
4. 电子束光刻(Electron Beam Lithography,EBL):电子束光刻是一种高分辨率光刻技术,利用聚焦的电子束直接写入图案。
电子束光刻具有非常高的分辨率,但速度较慢,适用于制造高级芯片和小批量生产。
这些光刻技术路线在微电子器件制造中起着重要的作用,根据不同的需求和应用领域选择合适的技术路线。
光刻机设备原理

光刻机设备原理
光刻机(Photolithography Equipment)是一种用于集成电路制造的关键设备,它在半导体工艺中用于将图案或模式投影到光敏剂涂覆的硅片(或其他基片)上。
以下是光刻机设备的基本原理:
1. 掩膜制作:首先,根据设计要求,制作一个光刻掩膜(Photomask),其中包含了所需的图案或模式。
掩膜通常由玻璃或石英材料制成,上面涂覆有光刻胶,形成所需的图案。
2. 光刻胶涂覆:将待加工的硅片(或其他基片)放入光刻机中,使用旋涂工艺将光刻胶均匀地涂覆在硅片表面上。
光刻胶是一种敏感的聚合物材料,可以在接受光照后发生化学或物理变化。
3. 掩膜对准:将光刻掩膜放置在光刻机上,然后通过对准系统将掩膜上的图案对准到硅片上。
对准系统使用精确的光学技术来确保图案的精确位置和对齐度。
4. 曝光和照明:光刻机使用紫外线光源照射光刻掩膜,通过透过掩膜的透明区域,将光照射到覆盖在硅片上的光刻胶上。
透过光刻掩膜的不同图案区域,可以形成所需的微小结构或图案。
5. 显影和刻蚀:曝光后,将硅片放入显影液中进行显影。
显影液的化学性质使得光刻胶在显影过程中发生溶解或物理变化,使得光刻胶的暴露部分被去除,形成所需的图案结构。
6. 清洗和检验:在光刻过程结束后,对硅片进行清洗,将未固化或残留的光刻胶和其他杂质去除。
然后,使用检验设备对光刻后的硅片进行检查和测试,以确保图案的质量和准确性。
这些步骤构成了光刻机设备的基本原理。
光刻机在半导体工艺中起到至关重要的作用,通过精确的光刻技术,可以制造出微小且高度精密的电子元件和电路结构,实现了集成电路的微米级或纳米级制造。
微纳米无掩膜光刻微纳光刻

微纳米无掩膜光刻微纳光刻
微纳米无掩膜光刻微纳光刻,是一种在微米、纳米甚至亚纳米级别
进行制作的技术。
本文将从方法、优势和应用的角度介绍微纳米无掩
膜光刻微纳光刻。
一、方法
传统的光刻技术需要使用掩模(即光刻面板)来实现图形转移,由于
掩模的制作和管理困难,很难应对纳米级别以上的加工需要。
而无掩
膜光刻不需要掩模,通过特殊的光源照射和化学反应,实现了在基片
上直接制作出所需的结构。
其制作过程包括基片处理、预上粘结剂、
光刻图案曝光、显影、表面改性等步骤,大大简化了制作流程,同时
也减小了加工成本。
二、优势
1. 高精度。
由于无掩膜光刻不需要掩模,可以避免掩模的缺陷和误差
对加工精度的影响,因此可以实现亚纳米级别的加工精度。
2. 高效率。
无掩膜光刻制作流程简单,省去了掩模的制作和管理过程,提高了制作效率和加工速度。
3. 低成本。
无掩膜光刻可以避免掩模的使用和管理成本,减小了加工
成本,同时也减小了加工流程对环境的影响。
4. 能够实现多层结构。
无掩膜光刻可以通过重复制作曝光和显影的过程,实现多层结构的加工。
三、应用
无掩膜光刻可以应用于集成电路、纳米器件制备、微流控芯片等领域。
由于其高精度、高效率的优势,可以实现更为精细的器件制备和更加
灵活的设计,为微纳米加工领域的研究和应用提供了有效的手段。
总之,微纳米无掩膜光刻微纳光刻是一项广泛应用于纳米科技领域的
制作技术,它的出现为纳米加工领域提供了无限可能,具有重要的研
究和应用价值。
光刻工艺的几种模式

光刻工艺的几种模式光刻工艺是一种在半导体器件制造过程中使用的核心技术。
通过将光刻胶(photoresist)涂覆在硅片表面,然后使用光刻机将光投射到光刻胶上,形成模式,最后使用化学蚀刻(chemical etching)或蒸发镀膜(metallization)等工艺将模式转移到硅片上。
光刻工艺在半导体制造中有多种不同模式,下面将详细介绍其中几种常见的模式。
1.1X模式:1X模式是最早使用的光刻工艺模式。
在这种模式下,光源中的紫外光通过凸面光刻掩膜(photomask)投射到光刻胶层上。
光源与掩膜的比例通常为1:1,因此被称为1X模式。
这种模式需要较高的分辨率和更高的光刻机精度。
2.5X模式:5X模式是现代光刻工艺中更常见的一种模式。
在这种模式下,光源中的光通过凹面光刻掩膜的五倍镜投射到光刻胶层上。
光源与掩膜的比例为5:1,因此被称为5X模式。
这种模式相对于1X模式具有更高的成像能力和更好的分辨率。
3.并行光刻模式:并行光刻模式是一种可以同时处理多片硅片的光刻工艺模式。
在这种模式中,光源通过一个分束器(beam splitter)将光分成多个光束,然后通过反射镜照射到多个硅片上。
这种模式可以显著提高生产效率,但对于光刻胶和光刻机的要求也更高。
4.双折射光刻模式:双折射光刻模式是一种使用光的双折射性质来增强分辨率的光刻工艺模式。
在这种模式中,光源发出的光通过一个偏振器(polarizer)来过滤其中的一种偏振光。
经过投射到硅片上后,光通过另一个偏振器,选择性地透过或反射出来。
这种模式可以提高成像的分辨率,但需要更精确的光刻掩膜和光刻机。
总的来说,光刻工艺有多种模式,包括1X模式、5X模式、并行光刻模式和双折射光刻模式等。
每种模式都有其特点和适用范围,在不同的半导体制造应用中选择适合的模式是非常重要的。
光刻版的形成方法与流程

光刻版的形成方法与流程
光刻版(Photomask)的形成方法与流程如下:
1. 制作基底:首先,根据设计要求选择合适的基底材料,如石英玻璃或聚合物。
然后,将基底进行清洗和抛光,以确保表面平整和清洁。
2. 电子束曝光:使用计算机辅助设计软件(CAD)来设计光
刻版中的图案。
将设计好的图案转化为数字化的信息,然后使用电子束曝光设备,通过控制电子束的扫描路径,将图案准确地写入基底上。
3. 显影:将其暴露在化学溶液中,使曝光的部分获得显影作用。
曝光的部分将发生化学反应,从而将基底上的图案清晰地显现出来。
4. 蒸镀:将金属或其他合适的材料蒸镀到显影后的基底上。
这一步的目的是增加图案的反射率和耐久性。
5. 清洗:将光刻版进行清洗,以去除在之前步骤中产生的化学残留物和污染物。
清洗后,光刻版将变得干净且透明。
6. 检查和修复:对光刻版进行检查,如果发现任何缺陷或损坏,可以尝试修复。
修复通常涉及使用特殊的修复剂将局部区域填充或覆盖。
7. 最终检验:最后,对光刻版进行仔细的最终检验,以确保图
案的质量和准确性。
检验可以使用显微镜、光学仪器或其他相关工具进行。
8. 包装和保护:完成光刻版的制作后,将其放入适当的包装盒中,并采取必要的措施来保护光刻版,以防止损坏或污染。
以上是光刻版的形成方法与流程的基本概述,但实际的制作流程可能因不同的光刻技术、设备和应用领域而有所差异。
(英文)无掩膜光刻的模式生成系统
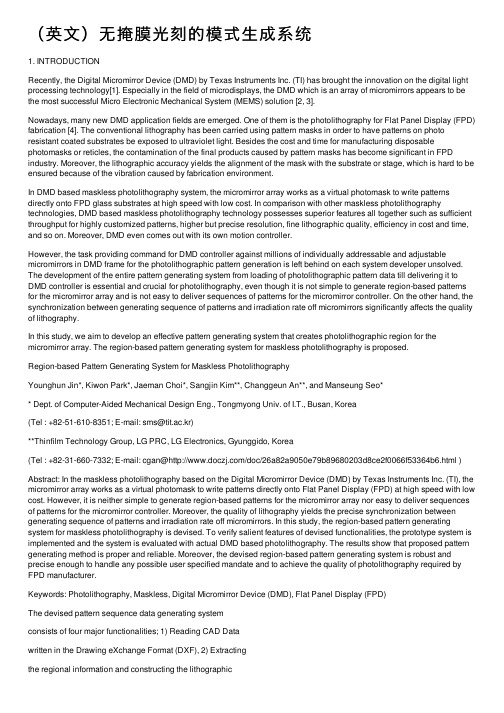
(英⽂)⽆掩膜光刻的模式⽣成系统1. INTRODUCTIONRecently, the Digital Micromirror Device (DMD) by Texas Instruments Inc. (TI) has brought the innovation on the digital light processing technology[1]. Especially in the field of microdisplays, the DMD which is an array of micromirrors appears to be the most successful Micro Electronic Mechanical System (MEMS) solution [2, 3].Nowadays, many new DMD application fields are emerged. One of them is the photolithography for Flat Panel Display (FPD) fabrication [4]. The conventional lithography has been carried using pattern masks in order to have patterns on photo resistant coated substrates be exposed to ultraviolet light. Besides the cost and time for manufacturing disposable photomasks or reticles, the contamination of the final products caused by pattern masks has become significant in FPD industry. Moreover, the lithographic accuracy yields the alignment of the mask with the substrate or stage, which is hard to be ensured because of the vibration caused by fabrication environment.In DMD based maskless photolithography system, the micromirror array works as a virtual photomask to write patterns directly onto FPD glass substrates at high speed with low cost. In comparison with other maskless photolithography technologies, DMD based maskless photolithography technology possesses superior features all together such as sufficient throughput for highly customized patterns, higher but precise resolution, fine lithographic quality, efficiency in cost and time, and so on. Moreover, DMD even comes out with its own motion controller.However, the task providing command for DMD controller against millions of individually addressable and adjustable micromirrors in DMD frame for the photolithographic pattern generation is left behind on each system developer unsolved. The development of the entire pattern generating system from loading of photolithographic pattern data till delivering it to DMD controller is essential and crucial for photolithography, even though it is not simple to generate region-based patterns for the micromirror array and is not easy to deliver sequences of patterns for the micromirror controller. On the other hand, the synchronization between generating sequence of patterns and irradiation rate off micromirrors significantly affects the quality of lithography.In this study, we aim to develop an effective pattern generating system that creates photolithographic region for the micromirror array. The region-based pattern generating system for maskless photolithography is proposed.Region-based Pattern Generating System for Maskless PhotolithographyYounghun Jin*, Kiwon Park*, Jaeman Choi*, Sangjin Kim**, Changgeun An**, and Manseung Seo** Dept. of Computer-Aided Mechanical Design Eng., Tongmyong Univ. of I.T., Busan, Korea(Tel:+82-51-610-8351;E-mail:**********.kr)**Thinfilm Technology Group, LG PRC, LG Electronics, Gyunggido, Korea(Tel : +82-31-660-7332; E-mail: cgan@/doc/26a82a9050e79b89680203d8ce2f0066f53364b6.html ) Abstract: In the maskless photolithography based on the Digital Micromirror Device (DMD) by Texas Instruments Inc. (TI), the micromirror array works as a virtual photomask to write patterns directly onto Flat Panel Display (FPD) at high speed with low cost. However, it is neither simple to generate region-based patterns for the micromirror array nor easy to deliver sequences of patterns for the micromirror controller. Moreover, the quality of lithography yields the precise synchronization between generating sequence of patterns and irradiation rate off micromirrors. In this study, the region-based pattern generating system for maskless photolithography is devised. To verify salient features of devised functionalities, the prototype system is implemented and the system is evaluated with actual DMD based photolithography. The results show that proposed pattern generating method is proper and reliable. Moreover, the devised region-based pattern generating system is robust and precise enough to handle any possible user specified mandate and to achieve the quality of photolithography required by FPD manufacturer.Keywords: Photolithography, Maskless, Digital Micromirror Device (DMD), Flat Panel Display (FPD)The devised pattern sequence data generating systemconsists of four major functionalities; 1) Reading CAD Datawritten in the Drawing eXchange Format (DXF), 2) Extractingthe regional information and constructing the lithographicregion, 3) Transforming constructed lithographic region intobinary data, 4) Delivering binary data to DMD controller forlithography.To evaluate proposed functionalities, the prototype systemis implemented, and actual DMD based photolithographyusing the system is carried. The results show that proposedpattern generating method is proper and reliable. Moreover,the implemented region-based pattern generating system isprecise enough to achieve the quality of photolithographyrequired by FPD manufacturer.2. DMD BASED MASKLESSPHOTOLITHOGRAPHY EQUIPMENTThe DMD based maskless photolithography equipmentconsists of three major devices. The first one is the radiationdevice. The second is the irradiation device including DMDcontroller, DMD, focusing optics, photo resistant coated glasssubstrate, and base stage assembly and its controller. The lastis the dynamic pattern control device being composed with thephotolithographic pattern generating system, the radiationcontrol unit, and the stage control unit.Figure 1 shows the schematic diagram of DMD basedmaskless photolithography equipment. The eXtended GraphicArray (XGA) 1024X768 Array DMD manufactured by TI has13.68 µm of one Pixel Field Of View (FOV) and it is enlargedto 40 µm in present work. As shown in Fig. 1, micromirrors ofDMD are exposed to incoming radiation released from theultraviolet light source. The reflection off the micromirrors isdetermined upon the signal from the photolithographic patterngenerating system to DMD controller. Then, the light reflectedoff the micromirrors is projected through focusing optics ontothe photo resistant material coated on top of the glass substratelaid on x-y scrolling base stage. Throughout DMD basedmaskless photolithography in concern, all DMD controllerdoes is only digital control of the light reflection formicromirrors i.e., it gives the approval of reflection as on or off. Therefore, the operation of the maskless photolithography equipment might be thought so simple.However, in reality, it is not. Sending the approval of on/off reflection for each of millions of micromirrors to DMD controller is more complicated than thought. Especially when reflection by the rotated DMD frame is unavoidable and/or in case when projection into the scrolling object is required, it is even troublesome to construct the proper lithographic region. Unfortunately through the maskless photolithography in concern, both reflection by the rotated DMD frame and projection into the scrolling object are imposed. Therefore, devising a customized pattern generating system entirely from loading of photolithographic pattern data till delivering it to DMD controller is inevitable.In this study, we focused our attention on the development of an effective pattern generating system that gives signals to DMD controller for the generation of photolithographic pattern, at prescribed radiation signal upon the irradiation intensity and stage control signal adjusted upon the pitch proper to the angle of DMD rotation and resolution. The region-based pattern generating system for DMD based maskless photolithography is proposed.3. LITHOGRAPHIC PATTERN GENERATIONThe region-based pattern generating system in present study consists of four major functionalities. Figure 2 shows the region-based pattern generating flow. The first is loading Computer Aided Design (CAD) data written in the Drawing eXchange Format (DXF) through the recognition of geometric entities as lines and arcs. The second is associated with three routines. The extraction of pattern boundary is performed through the reconstruction process of geometric entities with open loops into closed loops. The construction of region-based pattern is done upon polygonal set operation of computational geometry. The confirmation of photolithographic region is carried in accordance with geometric and technological constraints upon substrate and micromirror conditions. The third is the transformation of constructed photolithographic region into binary data upon DMD controller configuration. The last is the delivery of binary data to DMD controller for lithography in accordance with the DMD performance and glass substrate scrolling speed. 3.1 DXF formatted CAD data LoadingTo ensure the capabilities of devised pattern generating method, the testing of pattern generation is performed before it is applied to the actual DMD based maskless photolithography process. The test CAD data in DXF format loaded into memory. Through the recognition, the geometric entities are considered as lines, arcs, circles. Each of the recognized geometric entity is reconstructed as the entity defined in this study, which is abstract entity for polygonal region.3.2 Extraction of pattern boundaryThe boundary of the pattern is extracted with the conversion of geometric entities with open loops into polygonal entities forming closed loops. Figure 3 shows the extracted boundary of the pattern from the test CAD data. The diameter of circle is in between 50µm and 700µm, and the space between them is given in between 50µm and 200µm. The width of polygons representing lines lies in between 30µm and 50µm, and the space between them is given in between 30µm and 50µm.3.3 Construction of region-based patternThe construction of region-based pattern proceeds as follows. Each enclosed area extracted from the pattern boundary corresponds to each of polygonal entity. In case if there are overlapping polygons, the intersected area needs to be excluded from region-based pattern. In order to discard the intersected region, polygonal set operation in computational geometry is performed. Finally, to construct the region-based pattern, the interior area is considered as the area stands for photolithographic pattern.3.4 Confirmation of photolithographic regionIn general, the maskless photolithography system uses the resolution improvement mechanism by virtue of the rotated DMD frame (i.e., micromirror array) and the scrolling substrate. To satisfy the specification required by the FPD manufacturer, the system in concern uses the same mechanism. Figure 4 shows the configuration of DMD rotation and substrate scrolling. In present study based on XGA 1024 x 768 Array DMD, one DMD frame is made up with total of 786432 (longitudinally 1024 / horizontally 768) micromirrors with 40Fig. 2 Region-based pattern generating flowFig. 1 DMD based maskless photolithographic equipmentµm of enlarged FOV. The DMD frame is rotated clockwise from the longitudinal axis assigned as substrate scrolling direction. The pattern region is considered as being rotated counterclockwise from the longitudinal axis due to the clockwise rotation of DMD frame. The region projected onto DMD frame is extracted from pattern region. As a result, the extracted part of the region is mapped to lithographic region at each scrolling step.Fig. 3 Extracted boundary of the test pattern1 DMD Array Exposure LengthLongitudinal DirectionFig. 4 Configuration of DMD rotation and substrate scrollingFig. 5 Confirmed photolithographic region3 .5 Transformation of region into binary dataThe transformation of photolithographic region into binary data is performed upon DMD controller configuration. In present study, to match the lithographic region with DMD resolution, one DMD pixel is subdivided into 100 sub-pixels. The approval of on/off reflection for the mirror pixel on DMD is carried upon the number of sub-pixels occupied by the confirmed photolithographic pattern.Figure 5 shows the confirmed photolithographic region generated by devised method. To generate testing patterns, the pitch is assigned to be 5 with 40µm of enlarged FOV to have irradiation every 8µm scrolling. The area threshold value for binary data creation is hold at 80% and the bit depth is held at 768 and up with 5 degrees rotation of DMD frame. The total number of 9250 frames is used to irradiate the total area of the testing pattern. The results show that proposed method is capable of generating proper photolithographic pattern for DMD. 3 .6 Transfer binary data to DMD controllerThe binary pattern data is transferred to DMD controller in accordance with substrate scrolling step and DMD performance.The PCI board with the data transit speed 1200 frame per second (fps) is selected to play a role for delivery.4. IMPLEMENTATIONIn order to attain our aims to make region-based pattern generation feasible for actual DMD based maskless photolithography, the prototype photolithographic pattern generating system is implemented. The implemented system is mainly composed of the lithographic pattern generation module discussed in section 3, the signal interchange module that handles the real time communication with hardware components of the radiation control unit and the stage control unit, and the Graphical User Interface (GUI) that enables the photolithography equipment operator to view and control various operations of the system.Figure 6 shows the main window of GUI for the photolithographic pattern generating system. The management toolbar, the irradiation control sub-window, the pattern display sub-window, and the processing message sub-window are shown on the top, on the left, on the right middle, and on the right bottom, respectively. As shown in fig.6, the user specified input to the implemented system is the origin of the coordinate system, angle of DMD rotation, angle of substrate misalignment, two-directional DMD resolution, irradiation accuracy or pitch upon scrolling step, threshold value for binary data creation, and selection for normal/flip/mirror conversion of CAD data. Therefore, the system is robust enough to handle any possible user specified mandate and even substrate misalignment.To ensure the capabilities in devised system, the system is then applied to the generation of photolithographic pattern for FPD glass fabrication. Figure 7 shows the FPD glass photolithography process upon our system. Throughout the management toolbardisplay processing irradiation pattern window message windowcontrol windowFig. 6 Photolithographic pattern generating system(a)(b)(d)Fig. 7 Actual FPD glass photolithography processFPD pattern generation, the lithographical conditions are kept to be identical to those of the test pattern generation discussedin section 3, except the total number of frames needed to have the total area of FPD pattern be exposed to irradiation is shifted to 9250 frames. The CAD data of the pattern for FPD glass, with the minimum of 140µm line space (L/S), is shown in fig.7-(a). The illustrative example showing the accumulation of 16000 frames is appeared in fig.7-(b). The confirmed photolithographic region for FPD pattern is in fig.7-(c), and marked four sections are enlarged in fig.7-(d) to show the predicted photolithographic pattern in detail. The obtained FPD pattern shows that the implemented system based on region-based pattern generating method is capable to produce the actual pattern for DMD based maskless photolithography.Fig. 8 Enlarged portions of electron microscope imagesresulted from actual FPD photolithography5. RESULTS AND DISCUSSIONFor the validation of devised photolithographic pattern generating system, the DMD based maskless photolithography is carried to fabricate actual FPD glass using the system. Figure 8 shows the enlarged portions of electron microscope images from the actual FPD photolithography results obtained by the system discussed in section 4. The boundary of the final pattern appears to be clear enough insisting the accuracy of the devised system. Moreover, no manifestation of discrepancies between input from CAD data and output resulted from the actual photolithography is found.Overall, the result of actual FPD pattern photolithography verifies that the implemented system is capable of generating photolithographic pattern precise enough to acquire the high qualification from FPD manufacturer.ACKNOWLEDGMENTSThis work was supported by the LG Electronics Co. under Grant to IAMTEN Laboratory, Tongmyong University of Information Technology. We thank to the LG Electronics Co. for letting us share the confidential contents.REFERENCES[1]D. Dudley, W. Duncan, and J. Slaughter, “Emerging Digital Micromirror Device (DMD) Applications”, Proceedings of The International Society for Optical Engineering, V ol. 4985, 2003.[2] K.F. Chan, Z. Feng, R. Yang, A. Ishikawa, W. Mei,“High-resolution maskless lithography,” Journal of Microlithography, Microfabrication, and Microsystems, pp.331-339, 2003.[3] R. H?fling , E. Ahl, “ALP : universal DMD controllerfor metrology and testing” Proceedings of The International Society for Optical Engineering, V ol. 5289, May 2004.[4] S. H. Jung, “Maskless Photolithography Device,” KoreaPatent No.2003-0059705, in process, written in Korean, 2002。
掩模曝光DMD无掩模数字光刻更新
➢计算机将所需的光刻图案通过图形生成器输入到DMD芯片中,根据图形中黑 白像素的分布来改变DMD 中微反射镜的转角,并通过准直光源照射DMD表面 形成与所需图形一致的光图像,利用相应的光刻镜头将该图像投影到基片表面 并通过控制样品台的扫描运动,实现任意形状的大面积微结构制备。
➢投影物镜
➢曝光光源能量分布实际测试图
➢利用特殊的衍射匀光光学元 件和405nm激光,形成高均 匀、高效照明光源
➢丰富的投影光刻物镜光学、光机设 计经验以及成熟的精密装调工艺, 保证每一个投影光刻物镜的成像质 量。 ➢标准物镜: ➢1X:分辨力10.8μm,曝光面积21X10.5mm2
➢数值孔径NA=0.1
(2013.04.17 授权公告日) 授权
数字处理方面: 一种用于数字光刻系统的光强不均匀性测量与校正方法 刘华;卢振武 (已提交)
系统装调方面: DMD光学系统光源位置的定位辅助装置及光源位置装调方法 刘华 谭向全 党博石 发明专利
201510263495 用于定位DMD光刻系统中相机焦平面位置的新型分划板 刘华 谭向全 党博石 卢振武 发明专
利201510316684.0
发表论文:
Xiao-Duo Wang HuaLiu*、 Zhen-WuLu Li-WeiSong Tai-shengWang Bo-Shi Dang XiangQianQuan Yun-PengLi Design of a spectrum-folded Hadamard transform spectrometer in nearinfrared band Opt. Commu. 333. 80-83 (2014)
➢核心技术3——数据处理
(国内同类产品形成固定数据,分块存储,国外同类产品形成滚动数据,分块存储。)
光刻过程专业术语SMIF
光刻过程专业术语SMIF
:
SMIF(Standard Mechanical Interface)是一种标准机械接口,主要用于微电子制造过程中的光刻工艺。
SMIF是一种模块化设计,由一系列标准化的模块组成,包括衬板、营养板、搅拌槽等。
SMIF系统由多个部件组成,包括搅拌槽、衬板、营养板、结晶量子点膜层处
理槽等。
这种模块化设计可以大大减少工艺设备的边角,从而提高生产效率。
SMIF在光刻过程中被广泛应用,其标准化夹具可以确保微电子部件之间的精确连接,可
以有效提高工作效率,减少因料机不准确而造成的损失。
此外,SMIF在光刻过程中可以
有效地保护光刻物料,减少粉尘污染。
此外,SMIF的优点在于它可以有效地提高光刻过程的精度和可靠性。
它可以减少光刻涂
料的气孔率,从而有效提高产品的精度和可靠性。
此外,它还可以显著减少光刻过程中的
机械压力,从而改善产品质量。
总之,SMIF是一种很有效的标准机械接口,它大大提高了微电子制造过程中的光刻工艺
的性能,是一种现代化的微电子生产解决方案。
它的特性使其在微电子制造过程中受到了
广泛的应用,从而带来了很多好处,起到了很大的作用。
掩膜版(mask)的制造
维持原先所设定要求的洁净度、温湿度及压力等性能之特
性。
目前公司光刻室温度控制在23±0.5℃、其它洁净室温 度控制在23±1℃,相对湿度控制在45%~70%RH。
1.净化车间相关基础
洁净室洁净度等级的定义 洁净度等级(Class) 目前有公制和英制两种定义方式
Rigidity
Material Rigidity
Sodalite 540
Silicon-Boride 657
Quartz 615
Heat Expansion(ppm/oC)
Material Soda lime
Coefficient
9.4
Silicon-Boride 3.7
Quartz 0.5
1. 硼硅玻璃,优点不突出,很少使用;
掩膜版 (mask 或 光罩)
干版 (精度适中、耐用性适中、价格适中)
菲林 (精度低、不耐用、价格低)
凸版(APR)版 (主要用来转移PI液等)
2. 掩膜版制作流程
图案形成工程
检查修正工程
客
激
光
光
户
光
罩
罩
数
曝
化
尺
据
光
学
寸
处
描
制
量
理
绘
程
测
图档处理
生产
光
光清
罩
罩洗
缺
缺包
陷
陷装
检
修出
验
补货
品质
2. 掩膜版制作流程
ULPA (Ultra Low Particulate Penetration Air-filter) 0.15um的微粒子捕捉率至少为99.9995%;
光刻的基本原理
光刻的基本原理1. 光刻技术概述光刻(photolithography)是一种在微电子制造工艺中广泛应用的技术,用于将电路图案转移至硅片上。
它是一种光影刻蚀技术,通过使用特殊的光刻胶和掩膜来实现。
2. 光刻的基本步骤光刻的基本步骤包括掩膜制备、光刻胶涂布、曝光、显影和刻蚀等步骤。
2.1 掩膜制备掩膜是光刻中的一种重要工具,它由透明光刻胶和不透明掩膜板组成。
掩膜板的图案决定了最终在硅片上形成的电路。
2.2 光刻胶涂布在光刻过程中,需要将光刻胶均匀涂布在硅片上。
涂布需要控制好厚度,并保持均匀性。
2.3 曝光曝光是将掩膜上的图案转移到光刻胶层的过程。
曝光时,光源会将光刻胶层中的敏化剂激活,使其变得可显影。
2.4 显影显影是将曝光后的光刻胶层中未被曝光的部分去除,从而显现出所需图案的过程。
显影液会溶解未暴露于光的区域,使其变为可刻蚀的区域。
2.5 刻蚀刻蚀是将显影后的光刻胶层外的材料去除的过程。
通过刻蚀,可以形成所需的电路图案。
3. 光刻的基本原理光刻的基本原理可以分为光学透射原理和化学反应原理两个方面。
3.1 光学透射原理光学透射原理是光刻的基础,也是光刻胶和掩膜的关键。
光刻胶对于不同波长的光有不同的吸收特性,而掩膜上的图案会通过光刻胶的吸收和透射来形成图案。
当掩膜上的图案被光照射时,光刻胶中的敏化剂会被激活,从而改变光刻胶的溶解性质。
3.2 化学反应原理化学反应原理是光刻胶显影和刻蚀的基础。
在显影过程中,显影液与光刻胶表面的未暴露区域发生化学反应,使其溶解。
而在刻蚀过程中,刻蚀液与未被光刻胶保护的硅片表面或者下一层材料发生化学反应,使其被去除。
4. 光刻的影响因素光刻的效果受到多个因素的影响,主要包括曝光能量、曝光时间、光刻胶厚度、显影液浓度等因素。
4.1 曝光能量和曝光时间曝光能量和曝光时间决定了光刻胶的显影深度,对图案的清晰度和精度有重要影响。
4.2 光刻胶厚度光刻胶厚度会影响曝光和显影的效果,太厚会导致曝光不足,太薄则可能导致显影不均匀。
- 1、下载文档前请自行甄别文档内容的完整性,平台不提供额外的编辑、内容补充、找答案等附加服务。
- 2、"仅部分预览"的文档,不可在线预览部分如存在完整性等问题,可反馈申请退款(可完整预览的文档不适用该条件!)。
- 3、如文档侵犯您的权益,请联系客服反馈,我们会尽快为您处理(人工客服工作时间:9:00-18:30)。
1. INTRODUCTIONRecently, the Digital Micromirror Device (DMD) by Texas Instruments Inc. (TI) has brought the innovation on the digital light processing technology[1]. Especially in the field of microdisplays, the DMD which is an array of micromirrors appears to be the most successful Micro Electronic Mechanical System (MEMS) solution [2, 3].Nowadays, many new DMD application fields are emerged. One of them is the photolithography for Flat Panel Display (FPD) fabrication [4]. The conventional lithography has been carried using pattern masks in order to have patterns on photo resistant coated substrates be exposed to ultraviolet light. Besides the cost and time for manufacturing disposable photomasks or reticles, the contamination of the final products caused by pattern masks has become significant in FPD industry. Moreover, the lithographic accuracy yields the alignment of the mask with the substrate or stage, which is hard to be ensured because of the vibration caused by fabrication environment.In DMD based maskless photolithography system, the micromirror array works as a virtual photomask to write patterns directly onto FPD glass substrates at high speed with low cost. In comparison with other maskless photolithography technologies, DMD based maskless photolithography technology possesses superior features all together such as sufficient throughput for highly customized patterns, higher but precise resolution, fine lithographic quality, efficiency in cost and time, and so on. Moreover, DMD even comes out with its own motion controller.However, the task providing command for DMD controller against millions of individually addressable and adjustable micromirrors in DMD frame for the photolithographic pattern generation is left behind on each system developer unsolved. The development of the entire pattern generating system from loading of photolithographic pattern data till delivering it to DMD controller is essential and crucial for photolithography, even though it is not simple to generate region-based patterns for the micromirror array and is not easy to deliver sequences of patterns for the micromirror controller. On the other hand, the synchronization between generating sequence of patterns and irradiation rate off micromirrors significantly affects the quality of lithography.In this study, we aim to develop an effective pattern generating system that creates photolithographic region for the micromirror array. The region-based pattern generating system for maskless photolithography is proposed.Region-based Pattern Generating System for Maskless PhotolithographyYounghun Jin*, Kiwon Park*, Jaeman Choi*, Sangjin Kim**, Changgeun An**, and Manseung Seo** Dept. of Computer-Aided Mechanical Design Eng., Tongmyong Univ. of I.T., Busan, Korea(Tel : +82-51-610-8351; E-mail: sms@tit.ac.kr)**Thinfilm Technology Group, LG PRC, LG Electronics, Gyunggido, Korea(Tel : +82-31-660-7332; E-mail: cgan@)Abstract: In the maskless photolithography based on the Digital Micromirror Device (DMD) by Texas Instruments Inc. (TI), the micromirror array works as a virtual photomask to write patterns directly onto Flat Panel Display (FPD) at high speed with low cost. However, it is neither simple to generate region-based patterns for the micromirror array nor easy to deliver sequences of patterns for the micromirror controller. Moreover, the quality of lithography yields the precise synchronization between generating sequence of patterns and irradiation rate off micromirrors. In this study, the region-based pattern generating system for maskless photolithography is devised. To verify salient features of devised functionalities, the prototype system is implemented and the system is evaluated with actual DMD based photolithography. The results show that proposed pattern generating method is proper and reliable. Moreover, the devised region-based pattern generating system is robust and precise enough to handle any possible user specified mandate and to achieve the quality of photolithography required by FPD manufacturer.Keywords: Photolithography, Maskless, Digital Micromirror Device (DMD), Flat Panel Display (FPD)The devised pattern sequence data generating systemconsists of four major functionalities; 1) Reading CAD Datawritten in the Drawing eXchange Format (DXF), 2) Extractingthe regional information and constructing the lithographicregion, 3) Transforming constructed lithographic region intobinary data, 4) Delivering binary data to DMD controller forlithography.To evaluate proposed functionalities, the prototype systemis implemented, and actual DMD based photolithographyusing the system is carried. The results show that proposedpattern generating method is proper and reliable. Moreover,the implemented region-based pattern generating system isprecise enough to achieve the quality of photolithographyrequired by FPD manufacturer.2. DMD BASED MASKLESSPHOTOLITHOGRAPHY EQUIPMENTThe DMD based maskless photolithography equipmentconsists of three major devices. The first one is the radiationdevice. The second is the irradiation device including DMDcontroller, DMD, focusing optics, photo resistant coated glasssubstrate, and base stage assembly and its controller. The lastis the dynamic pattern control device being composed with thephotolithographic pattern generating system, the radiationcontrol unit, and the stage control unit.Figure 1 shows the schematic diagram of DMD basedmaskless photolithography equipment. The eXtended GraphicArray (XGA) 1024X768 Array DMD manufactured by TI has13.68 µm of one Pixel Field Of View (FOV) and it is enlargedto 40 µm in present work. As shown in Fig. 1, micromirrors ofDMD are exposed to incoming radiation released from theultraviolet light source. The reflection off the micromirrors isdetermined upon the signal from the photolithographic patterngenerating system to DMD controller. Then, the light reflectedoff the micromirrors is projected through focusing optics ontothe photo resistant material coated on top of the glass substratelaid on x-y scrolling base stage. Throughout DMD basedmaskless photolithography in concern, all DMD controllerdoes is only digital control of the light reflection formicromirrors i.e., it gives the approval of reflection as on or off. Therefore, the operation of the maskless photolithography equipment might be thought so simple.However, in reality, it is not. Sending the approval of on/off reflection for each of millions of micromirrors to DMD controller is more complicated than thought. Especially when reflection by the rotated DMD frame is unavoidable and/or in case when projection into the scrolling object is required, it is even troublesome to construct the proper lithographic region.Unfortunately through the maskless photolithography in concern, both reflection by the rotated DMD frame and projection into the scrolling object are imposed. Therefore, devising a customized pattern generating system entirely from loading of photolithographic pattern data till delivering it to DMD controller is inevitable.In this study, we focused our attention on the development of an effective pattern generating system that gives signals to DMD controller for the generation of photolithographic pattern, at prescribed radiation signal upon the irradiation intensity and stage control signal adjusted upon the pitch proper to the angle of DMD rotation and resolution. The region-based pattern generating system for DMD based maskless photolithography is proposed.3. LITHOGRAPHIC PATTERN GENERATIONThe region-based pattern generating system in present study consists of four major functionalities. Figure 2 shows the region-based pattern generating flow. The first is loading Computer Aided Design (CAD) data written in the Drawing eXchange Format (DXF) through the recognition of geometric entities as lines and arcs. The second is associated with three routines. The extraction of pattern boundary is performed through the reconstruction process of geometric entities with open loops into closed loops. The construction of region-based pattern is done upon polygonal set operation of computational geometry. The confirmation of photolithographic region is carried in accordance with geometric and technological constraints upon substrate and micromirror conditions. The third is the transformation of constructed photolithographic region into binary data upon DMD controller configuration. The last is the delivery of binary data to DMD controller for lithography in accordance with the DMD performance and glass substrate scrolling speed. 3.1 DXF formatted CAD data LoadingTo ensure the capabilities of devised pattern generating method, the testing of pattern generation is performed before it is applied to the actual DMD based maskless photolithography process. The test CAD data in DXF format loaded into memory. Through the recognition, the geometric entities are considered as lines, arcs, circles. Each of the recognized geometric entity is reconstructed as the entity defined in this study, which is abstract entity for polygonal region.3.2 Extraction of pattern boundaryThe boundary of the pattern is extracted with the conversion of geometric entities with open loops into polygonal entities forming closed loops. Figure 3 shows the extracted boundary of the pattern from the test CAD data. The diameter of circle is in between 50µm and 700µm, and the space between them is given in between 50µm and 200µm. The width of polygons representing lines lies in between 30µm and 50µm, and the space between them is given in between 30µm and 50µm.3.3 Construction of region-based patternThe construction of region-based pattern proceeds as follows. Each enclosed area extracted from the pattern boundary corresponds to each of polygonal entity. In case if there are overlapping polygons, the intersected area needs to be excluded from region-based pattern. In order to discard the intersected region, polygonal set operation in computational geometry is performed. Finally, to construct the region-based pattern, the interior area is considered as the area stands for photolithographic pattern.3.4 Confirmation of photolithographic regionIn general, the maskless photolithography system uses the resolution improvement mechanism by virtue of the rotated DMD frame (i.e., micromirror array) and the scrolling substrate. To satisfy the specification required by the FPD manufacturer, the system in concern uses the same mechanism. Figure 4 shows the configuration of DMD rotation and substrate scrolling. In present study based on XGA 1024 x 768 Array DMD, one DMD frame is made up with total of 786432 (longitudinally 1024 / horizontally 768) micromirrors with 40Fig. 2 Region-based pattern generating flowFig. 1 DMD based maskless photolithographic equipmentµm of enlarged FOV. The DMD frame is rotated clockwise from the longitudinal axis assigned as substrate scrolling direction. The pattern region is considered as being rotated counterclockwise from the longitudinal axis due to the clockwise rotation of DMD frame. The region projected onto DMD frame is extracted from pattern region. As a result, the extracted part of the region is mapped to lithographic region at each scrolling step.Fig. 3 Extracted boundary of the test pattern1 DMD Array Exposure LengthLongitudinal DirectionFig. 4 Configuration of DMD rotation and substrate scrollingFig. 5 Confirmed photolithographic region3 .5 Transformation of region into binary dataThe transformation of photolithographic region into binary data is performed upon DMD controller configuration. In present study, to match the lithographic region with DMD resolution, one DMD pixel is subdivided into 100 sub-pixels. The approval of on/off reflection for the mirror pixel on DMD is carried upon the number of sub-pixels occupied by the confirmed photolithographic pattern.Figure 5 shows the confirmed photolithographic region generated by devised method. To generate testing patterns, the pitch is assigned to be 5 with 40µm of enlarged FOV to have irradiation every 8µm scrolling. The area threshold value for binary data creation is hold at 80% and the bit depth is held at 768 and up with 5 degrees rotation of DMD frame. The total number of 9250 frames is used to irradiate the total area of the testing pattern. The results show that proposed method is capable of generating proper photolithographic pattern for DMD. 3 .6 Transfer binary data to DMD controllerThe binary pattern data is transferred to DMD controller in accordance with substrate scrolling step and DMD performance. The PCI board with the data transit speed 1200 frame per second (fps) is selected to play a role for delivery.4. IMPLEMENTATIONIn order to attain our aims to make region-based pattern generation feasible for actual DMD based maskless photolithography, the prototype photolithographic pattern generating system is implemented. The implemented system is mainly composed of the lithographic pattern generation module discussed in section 3, the signal interchange module that handles the real time communication with hardware components of the radiation control unit and the stage control unit, and the Graphical User Interface (GUI) that enables the photolithography equipment operator to view and control various operations of the system.Figure 6 shows the main window of GUI for the photolithographic pattern generating system. The management toolbar, the irradiation control sub-window, the pattern display sub-window, and the processing message sub-window are shown on the top, on the left, on the right middle, and on the right bottom, respectively. As shown in fig.6, the user specified input to the implemented system is the origin of the coordinate system, angle of DMD rotation, angle of substrate misalignment, two-directional DMD resolution, irradiation accuracy or pitch upon scrolling step, threshold value for binary data creation, and selection for normal/flip/mirror conversion of CAD data. Therefore, the system is robust enough to handle any possible user specified mandate and even substrate misalignment.To ensure the capabilities in devised system, the system is then applied to the generation of photolithographic pattern for FPD glass fabrication. Figure 7 shows the FPD glass photolithography process upon our system. Throughout themanagement toolbardisplay processingirradiation patternwindowmessagewindowcontrol windowFig. 6 Photolithographic pattern generating system(a)(b)(d)Fig. 7 Actual FPD glass photolithography processFPD pattern generation, the lithographical conditions are kept to be identical to those of the test pattern generation discussed in section 3, except the total number of frames needed to have the total area of FPD pattern be exposed to irradiation is shifted to 9250 frames. The CAD data of the pattern for FPD glass, with the minimum of 140µm line space (L/S), is shown in fig.7-(a). The illustrative example showing the accumulation of 16000 frames is appeared in fig.7-(b). The confirmed photolithographic region for FPD pattern is in fig.7-(c), and marked four sections are enlarged in fig.7-(d) to show the predicted photolithographic pattern in detail. The obtained FPD pattern shows that the implemented system based on region-based pattern generating method is capable to produce the actual pattern for DMD based maskless photolithography.Fig. 8 Enlarged portions of electron microscope imagesresulted from actual FPD photolithography5. RESULTS AND DISCUSSIONFor the validation of devised photolithographic pattern generating system, the DMD based maskless photolithography is carried to fabricate actual FPD glass using the system. Figure 8 shows the enlarged portions of electron microscope images from the actual FPD photolithography results obtained by the system discussed in section 4. The boundary of the final pattern appears to be clear enough insisting the accuracy of the devised system. Moreover, no manifestation of discrepancies between input from CAD data and output resulted from the actual photolithography is found.Overall, the result of actual FPD pattern photolithography verifies that the implemented system is capable of generating photolithographic pattern precise enough to acquire the high qualification from FPD manufacturer.ACKNOWLEDGMENTSThis work was supported by the LG Electronics Co. under Grant to IAMTEN Laboratory, Tongmyong University of Information Technology. We thank to the LG Electronics Co. for letting us share the confidential contents.REFERENCES[1]D. Dudley, W. Duncan, and J. Slaughter, “Emerging Digital Micromirror Device (DMD) Applications”, Proceedings of The International Society for Optical Engineering, V ol. 4985, 2003.[2] K.F. Chan, Z. Feng, R. Yang, A. Ishikawa, W. Mei,“High-resolution maskless lithography,” Journal of Microlithography, Microfabrication, and Microsystems, pp.331-339, 2003.[3] R. Höfling , E. Ahl, “ALP : universal DMD controllerfor metrology and testing” Proceedings of The International Society for Optical Engineering, V ol. 5289, May 2004.[4] S. H. Jung, “Maskless Photolithography Device,” KoreaPatent No.2003-0059705, in process, written in Korean, 2002。