493 回转盘工艺规程设计及镗孔工序夹具设计
回转盘工艺规程设计及镗孔工序夹具设计

二.回转盘的结构功用分析(一)零件的作用:回转盘是钻床主轴上的一个重要零 件,钻床主轴通过回转盘与钻关相连,回转盘与主轴用四个螺 钉联接,实现钻床的正确联接。
回转盘的轴套孔中安装齿轮齿条,轴套中安装弹簧,钻床 工作时,主轴带动回转盘中的齿轮运动,通过齿轮齿条实现钻 头的纵向进给,利用弹簧的回弹作用实现钻头的自动复位。
(二)零件的工艺分析该零件的材料为 HT180,该材料具有较高的耐磨性,强度,耐 热性及减振性.该零件的材料主要加工面为 R.N 面及φ370 +0.027 , φ62 02 . 0 01 . 0 + - , φ72 02 . 0 01 . 0 + - 等。
孔φ55,φ72 的中心线对端面尺在 500mm 上的平行度直接 影响到主轴的配合精度和运转精度,因此对孔φ55,φ72 的孔 应同时镗出,保证其同轴度,使平行度公差降到最小。
φ62 对φ90 的同心性允差为 0.02,将直接影响孔与轴的 配合,因此在加工时,最好在一次装夹内完成。
车削φ50mm 的端面保持其尺寸 108,将直接影响方孔内各 孔的正确定位以及齿轮运动时的空间。
φ90 轴线与 R 面垂直度 允差为 0.03,φ72 对φ55 的圆心允差为 0.05,φ37 对φ55 的圆心允差为 0.05,影响回转盘生与主轴联接的正确定位,从 而影响主轴传动齿轮与变速箱的锥齿轮的啮合精度。
由参考文献《机械制造工艺设计简明手册》中的有关和孔 加工的径向精度及机床达到的位置精度可知,上述要求可以达 到,零件的结构工艺性是可行的。
(三)回转盘的生产纲领,生产类型和其它给定条件 根据零件的材料确定毛坯为铸件,其生产类型为中批生 产,由《机械制造工艺设计简明手册》可知,毛坯的铸造方法 采用砂型机械造型,又由于零件的内腔及φ50,φ55,φ37 等 孔均须铸出,故应安放型芯,此外,为消除残余应力,铸出后 还应安排人工时效处理。
参考文献《机械制造工艺设计简明手册》表 2.2-5,该种 铸件的公差等级为 CT8-10 级,加工余量等级 MA 为 G 级,故取 CT 为 9 级,MA 为 G 级。
电机座的工艺及其镗孔夹具设计工艺

电机座的工艺及其镗孔夹具设计工艺电机座是电机的重要组成部分,用于安装电机并支撑其运行。
在电机座的制造过程中,有许多工艺需要遵循,并且在镗孔部分还需要设计适用的夹具。
首先,电机座的工艺包括材料选择、铸造或加工、精加工和表面处理等几个关键步骤。
材料选择应根据电机座的使用环境、负载要求和制造成本等因素综合考虑,常见的材料有铜、铝合金和钢等。
然后,通过铸造或加工的方式制造电机座的初始形状,一般通过压力铸造或铸造铸造来实现。
接下来,进行精加工,例如铣削、车削和钻削等,以确保电机座的精确尺寸和形状。
最后,对电机座进行表面处理,如喷漆、电泳涂覆或阳极氧化等,以提高电机座的耐腐蚀性和美观度。
在电机座的镗孔过程中,为了确保镗孔的精确度和稳定性,需要设计适用的夹具。
夹具的设计应考虑以下几个方面。
首先,夹具的材料选择应具有足够的刚度和耐磨性,以确保夹具的长期使用性能。
材料常选用钢、铝合金或高强度工程塑料等。
其次,夹具的基座应具有稳定的结构和良好的固定能力,以确保夹具在使用过程中不发生位移或摇晃。
再次,夹具的夹持方式应根据镗孔的特点选择,如机械夹紧、液压夹紧或气动夹紧等。
此外,夹具的刀具定位和夹持力的调整也是夹具设计中需要考虑的因素。
在完成夹具设计后,对电机座进行镗孔的具体工艺流程一般包括以下几个步骤。
首先,根据设计要求和加工设备的能力选择合适的切削刀具和切削参数。
接下来,通过定位夹具将电机座固定在加工设备上,并通过夹持装置夹紧。
然后,根据夹具的切削刀具定位,设置加工设备的坐标轴和刀具路径。
在进行切削操作时,要注意切削刀具的切削速度、进给速度和切削深度等参数的控制,并及时冷却切削区域以防止工件过热。
最后,通过测量和检验等方法验证镗孔的精确度和质量。
总之,电机座的工艺是确保电机座质量和性能的关键。
而夹具设计工艺则是镗孔过程中的重要环节,需要综合考虑材料选择、夹持方式和切削参数等因素,以保证镗孔的精确度和稳定性。
通过严格的工艺控制和夹具设计,可以生产出具有高品质和可靠性的电机座产品。
机械工艺夹具毕业设计49普通车床转盘的工艺编制及车夹具设计

目录序言----------------------------------------------------------------------1 第一章零件的分析------------------------------------------------ 3§1-1 零件的作用---------------------- ------------------------ 3§1-2 零件的工艺分析------------------------------------------3§1-3 零件的材质、热处理及机械加工的工艺性--------- 4第二章零件工艺规程设计--------------------------------------- 7§2-1 确定零件生产类型--------------------------------------- 7§2-2 确定零件毛坯的制造形式------------------------------ 7§2-3 制定工艺路线--------------------------------------------- 8§2-4 基准的选择---------------------------------------------- 13§2-5 确定机械加工余量、工序尺寸及毛坯尺寸--15§2-6 各工序工艺装备、切削用量及工时定额---- -------19§2-7 数控程序编制----------------------------- ------------26第三章夹具设计------------------------------------- ------------33§3-1 概述--------------------------------------------------------33§3-2 方案设计---------------------------------------------------33主要参考文献---------------------------------------------------------39结束语------------------------------------------------------------------40前言机械制造工艺及机床夹具设计是大学四年来最后一次实践教学环节,此次毕业设计为了我们对所学的工艺夹具知识进一步深化,指导老师分配了《车床转盘机械制造工艺及夹具设计》的题目,为的是对所学的各课程深入的、综合性的总复习,也是一次理论联系实际的训练。
转盘机加工工艺规程及夹具设计

引言三年在校的专业学习接触到了机械行业的很多知识,通过学习专业课程后,学习到机械工业相关的基础知识。
通过老师的介绍与工厂的实习对机械行业有了更多的探索,机械工业是为国民经济提供装备和为人民生活提供耐用消费品的产业。
它的技术水平和规模是衡量一个国家科技水平和经济实力的重要标志。
然而机床是先进制造技术的载体和装备工业的基本生产手段,是装备制造业的基础设备。
因此机床工业技术的高低又展示着一个国家机械工业水平的高低。
作为一名工科院校且学习数控相关技术的学生对机床相关的知识与讯息了解更多一些。
深知目前国内自主研发的相关技术与世界发达国家相比之下还很薄弱,从机床的设计规模到高端的精密技术都与国际水平存有差距。
回顾历史,英国的工业革命完成了生产从工场手工业向机器大工业过渡的阶段。
实现了机器取代人力,以大规模工厂化生产取代个体工场手工生产的一场生产与科技革命。
让西方国家得到了很迅速的发展,但当时的中国却还处于手工生产的阶段。
随着时间的推移差距越来越大,导致后来面对西方坚船利炮等先进的武器时悲惨的牺牲!但历史终将过去,国人用顽强的毅力与无穷的智慧最终胜利的抵御了列强的侵略。
通过历史的教训也让我们认识到科技的重要性,经过先辈们多年的努力我国的科技水平取得了很好的成绩。
作为一名中国青年我们有责任为国家的工业发展添砖加瓦贡献自己的一份力量。
从最近几年的发展情况看,国内机床工业的发展越来越快,正向着高速,高精密,大型,综合型的方向发展。
这也给研究人员带来了无限的挑战,不过相信通过相关科研人员不懈的努力我们一定能实现科技振兴国家的宏伟目标与愿望!第一章零件工艺性分析1.1工件的结构特点及其作用普通的车床转盘,该零件位于刀架部件的上刀架与下刀架之间,它是上刀架的导向件,当需要用小刀架车锥面时,可通过转盘相对于下刀架的转动来调整锥角。
1.2零件的分析由零件图(附件零件图02)可知其材料为HT200的灰铸铁,该材料有极高的强度、耐磨度及抗振性,适应于要求支撑较大压力,要求耐磨,符合零件工作要求。
转盘机加工工艺规程及夹具设计

引言三年在校的专业学习接触到了机械行业的很多知识,通过学习专业课程后,学习到机械工业相关的基础知识。
通过老师的介绍与工厂的实习对机械行业有了更多的探索,机械工业是为国民经济提供装备和为人民生活提供耐用消费品的产业。
它的技术水平和规模是衡量一个国家科技水平和经济实力的重要标志。
然而机床是先进制造技术的载体和装备工业的基本生产手段,是装备制造业的基础设备。
因此机床工业技术的高低又展示着一个国家机械工业水平的高低。
作为一名工科院校且学习数控相关技术的学生对机床相关的知识与讯息了解更多一些。
深知目前国内自主研发的相关技术与世界发达国家相比之下还很薄弱,从机床的设计规模到高端的精密技术都与国际水平存有差距。
回顾历史,英国的工业革命完成了生产从工场手工业向机器大工业过渡的阶段。
实现了机器取代人力,以大规模工厂化生产取代个体工场手工生产的一场生产与科技革命。
让西方国家得到了很迅速的发展,但当时的中国却还处于手工生产的阶段。
随着时间的推移差距越来越大,导致后来面对西方坚船利炮等先进的武器时悲惨的牺牲!但历史终将过去,国人用顽强的毅力与无穷的智慧最终胜利的抵御了列强的侵略。
通过历史的教训也让我们认识到科技的重要性,经过先辈们多年的努力我国的科技水平取得了很好的成绩。
作为一名中国青年我们有责任为国家的工业发展添砖加瓦贡献自己的一份力量。
从最近几年的发展情况看,国内机床工业的发展越来越快,正向着高速,高精密,大型,综合型的方向发展。
这也给研究人员带来了无限的挑战,不过相信通过相关科研人员不懈的努力我们一定能实现科技振兴国家的宏伟目标与愿望!第一章零件工艺性分析1.1工件的结构特点及其作用普通的车床转盘,该零件位于刀架部件的上刀架与下刀架之间,它是上刀架的导向件,当需要用小刀架车锥面时,可通过转盘相对于下刀架的转动来调整锥角。
1.2零件的分析由零件图(附件零件图02)可知其材料为HT200的灰铸铁,该材料有极高的强度、耐磨度及抗振性,适应于要求支撑较大压力,要求耐磨,符合零件工作要求。
法盘镗孔夹具课程设计
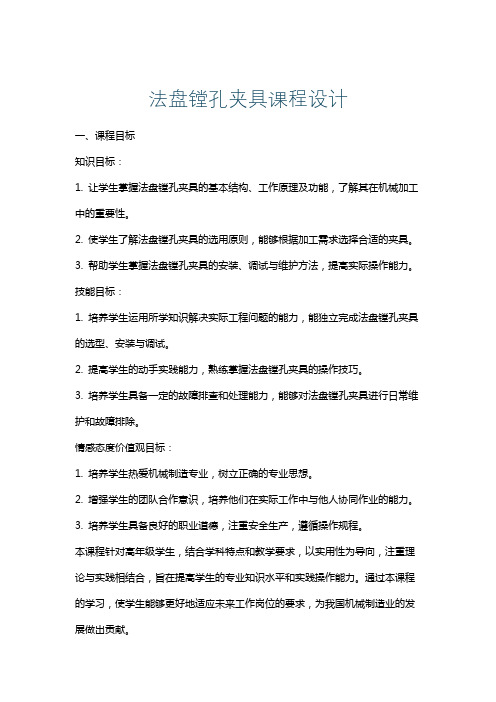
法盘镗孔夹具课程设计一、课程目标知识目标:1. 让学生掌握法盘镗孔夹具的基本结构、工作原理及功能,了解其在机械加工中的重要性。
2. 使学生了解法盘镗孔夹具的选用原则,能够根据加工需求选择合适的夹具。
3. 帮助学生掌握法盘镗孔夹具的安装、调试与维护方法,提高实际操作能力。
技能目标:1. 培养学生运用所学知识解决实际工程问题的能力,能独立完成法盘镗孔夹具的选型、安装与调试。
2. 提高学生的动手实践能力,熟练掌握法盘镗孔夹具的操作技巧。
3. 培养学生具备一定的故障排查和处理能力,能够对法盘镗孔夹具进行日常维护和故障排除。
情感态度价值观目标:1. 培养学生热爱机械制造专业,树立正确的专业思想。
2. 增强学生的团队合作意识,培养他们在实际工作中与他人协同作业的能力。
3. 培养学生具备良好的职业道德,注重安全生产,遵循操作规程。
本课程针对高年级学生,结合学科特点和教学要求,以实用性为导向,注重理论与实践相结合,旨在提高学生的专业知识水平和实践操作能力。
通过本课程的学习,使学生能够更好地适应未来工作岗位的要求,为我国机械制造业的发展做出贡献。
二、教学内容1. 法盘镗孔夹具概述:介绍法盘镗孔夹具的定义、分类、应用领域及发展现状。
教材章节:第一章第一节2. 法盘镗孔夹具的结构与工作原理:详细讲解法盘镗孔夹具的各个组成部分及其作用,分析其工作原理。
教材章节:第一章第二节3. 法盘镗孔夹具的选用原则:阐述如何根据工件加工需求、设备条件等因素选择合适的法盘镗孔夹具。
教材章节:第一章第三节4. 法盘镗孔夹具的安装与调试:讲解法盘镗孔夹具的安装方法、调试步骤及注意事项。
教材章节:第二章第一节5. 法盘镗孔夹具的操作技巧:介绍法盘镗孔夹具在实际操作中的技巧和要点,提高加工效率。
教材章节:第二章第二节6. 法盘镗孔夹具的维护与故障排除:讲解法盘镗孔夹具的日常维护方法、常见故障原因及排除方法。
教材章节:第二章第三节7. 实践操作:组织学生进行法盘镗孔夹具的安装、调试与操作练习,巩固所学知识。
镗孔的加工工艺及夹具设计
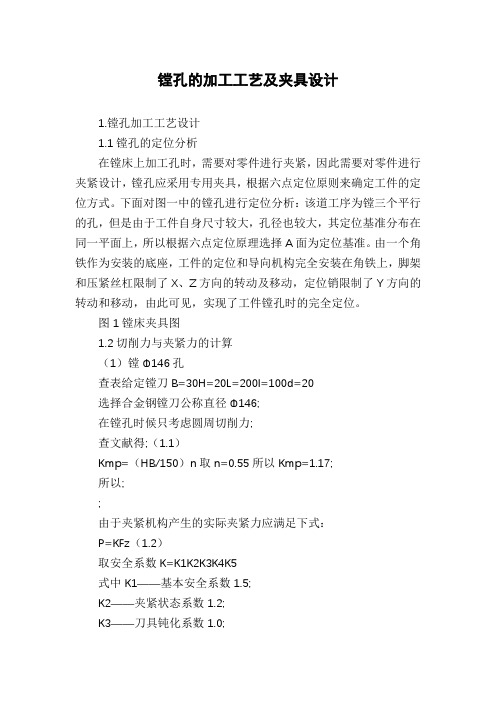
镗孔的加工工艺及夹具设计1.镗孔加工工艺设计1.1镗孔的定位分析在镗床上加工孔时,需要对零件进行夹紧,因此需要对零件进行夹紧设计,镗孔应采用专用夹具,根据六点定位原则来确定工件的定位方式。
下面对图一中的镗孔进行定位分析:该道工序为镗三个平行的孔,但是由于工件自身尺寸较大,孔径也较大,其定位基准分布在同一平面上,所以根据六点定位原理选择A面为定位基准。
由一个角铁作为安装的底座,工件的定位和导向机构完全安装在角铁上,脚架和压紧丝杠限制了X、Z方向的转动及移动,定位销限制了Y方向的转动和移动,由此可见,实现了工件镗孔时的完全定位。
图1镗床夹具图1.2切削力与夹紧力的计算(1)镗Φ146孔查表给定镗刀B=30H=20L=200I=100d=20选择合金钢镗刀公称直径Φ146;在镗孔时候只考虑圆周切削力;查文献得;(1.1)Kmp=(HB/150)n取n=0.55所以Kmp=1.17;所以;;由于夹紧机构产生的实际夹紧力应满足下式:P=KFz(1.2)取安全系数K=K1K2K3K4K5式中K1——基本安全系数1.5;K2——夹紧状态系数1.2;K3——刀具钝化系数1.0;K4——考虑夹紧动力稳定性系数1.0;K5——尽在有力矩企图使用回转时开考虑支撑面接触情况的系数1.0;所以得到K=K1K2K3K4K5=1.9,得到P=KFz=1.9X365.18=693.88N (2)镗Φ48孔选择高速钢镗刀公称直径Φ48;查表给定镗刀B=25H=30L=170I=80d=15在镗孔时候只考虑圆周切削力;查文献得;Kmp=(HB/150)n取n=0.55所以Kmp=1.17;所以;;由于夹紧机构产生的实际夹紧力应满足下式:P=KFz取安全系数K=K1K2K3K4K5式中K1——基本安全系数1.5;K2——夹紧状态系数1.2;K3——刀具钝化系数1.0;K4——考虑夹紧动力稳定性系数1.0;K5——尽在有力矩企图使用回转时开考虑支撑面接触情况的系数1.0;所以得到K=K1K2K3K4K5=1.9,得到P=KFz=1.9X223.2=424.08N <ol> 镗Φ80孔</ol>镗Φ80孔的计算过程与上边量孔的方法是一样的,就是选择高速钢镗刀公称直径Φ80的镗刀,最后计算结果为P=KFz=569.23N 根据上边的计算夹紧力不是很大,且夹具选择的种类为组合夹具,所以动力选择手动夹紧。
转速器盘制造工艺及夹具设计
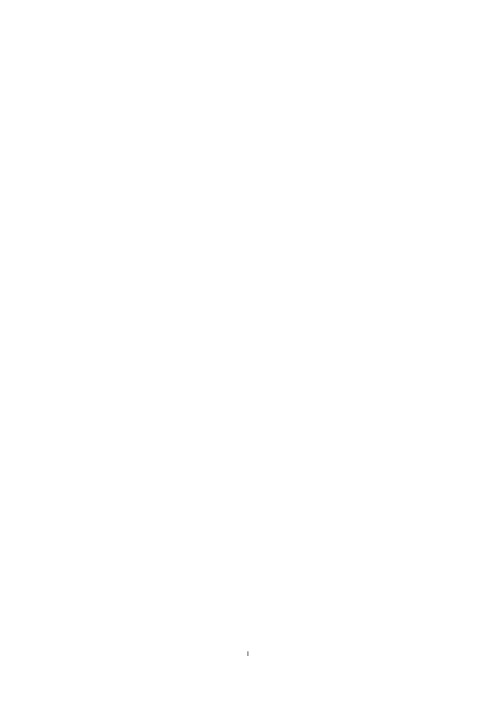
转速器盘制造工艺及夹具设计1 引言机械制造工艺学课程设计是在学完了机械制造工艺学(含机床夹具设计)和大部分专业课,并进行了生产实习基础上进行的一个教学环节。
这次设计使我们能够综合运用机械制造工艺学的基础理论,并结合生产实习中学到的实践知识,独立分析和解决工艺问题,初步具备了设计一个中等复杂程度的零件(转速器盘)的工艺规程的能力和运用夹具设计手册与图表等技术资料及编写技术文件等基础技能的一次时间机会,为今后的毕业设计及外来从事的工作打下良好的基础。
毕业设计是在我们学完了大学的全部基础课、技术基础课以及全部专业课之后进行的。
这是我们对所学各课程的一次深入的综合性的总复习,也是我们在走进社会工作岗位前的一次理论联系实际的训练。
因此,它在我们四年的大学生活中占有重要的地位。
就我个人而言,我希望能通过这次毕业设计对自己未来将从事的工作进行一次适应性训练,从中锻炼自己分析问题,解决问题的能力,为今后参加祖国的“四化”建设打下一个良好的基础。
本毕业设计的内容是制订转速器盘加工工艺规程及夹具设计。
详细讨论转速器盘从毛坯到成品的机械加工工艺过程,分析总结转速器盘的结构特点、主要加工表面,并制定相应的机械加工工艺规程;针对转速器盘零件的主要技术要求,设计钻孔用的钻床夹具。
本着力求与生产实际相结合的指导思想,本次毕业设计达到了综合运用基本理论知识,解决实际生产问题的目的。
由于个人能力所限、实践经验少、资料缺乏,设计尚有许多不足之处,恳请各位老师给予指教。
2 零件分析2.1 零件的作用恒压供水泵站一般需设多台水泵及电机,这比设单台水泵及电机节能而可靠。
配单台电机和水泵时,它们的功率必须足够的大,在用水量少时开一台大电机肯定是浪费,电机选小了用水量大时供水不足。
而且水泵和电机都有维修的时候,备用泵是必要的。
恒压供水的主要目标是保持管网水压的恒定,水泵电机的转速套跟随用水量的变化而变化,这就要用变频器为水泵供电。
这也有两种配置方式,一是为每台水泵电机配一台变频器,这当然方便,电机与变频器间不需要切换,但是购买变频器的费用较高。
- 1、下载文档前请自行甄别文档内容的完整性,平台不提供额外的编辑、内容补充、找答案等附加服务。
- 2、"仅部分预览"的文档,不可在线预览部分如存在完整性等问题,可反馈申请退款(可完整预览的文档不适用该条件!)。
- 3、如文档侵犯您的权益,请联系客服反馈,我们会尽快为您处理(人工客服工作时间:9:00-18:30)。
.回转盘的结构功用分析(一)零件的作用:回转盘是钻床主轴上的一个重要零 件,钻床主轴通过回转盘与钻关相连,回转盘与主轴用四个螺 钉联接,实现钻床的正确联接。
回转盘的轴套孔中安装齿轮齿条,轴套中安装弹簧,钻床 工作时,主轴带动回转盘中的齿轮运动,通过齿轮齿条实现钻 头的纵向进给,利用弹簧的回弹作用实现钻头的自动复位。
(二)零件的工艺分析该零件的材料为 HT180,该材料具有较高的耐磨性,强度,耐 热性及减振性.该零件的材料主要加工面为 R.N 面及φ370 +0.027 , φ62 02. 0 01 . 0 + - ,φ72 02. 0 01 . 0 + - 等。
孔φ55,φ72 的中心线对端面尺在 500mm 上的平行度直接 影响到主轴的配合精度和运转精度,因此对孔φ55,φ72 的孔 应同时镗出,保证其同轴度,使平行度公差降到最小。
φ62 对φ90 的同心性允差为 0.02,将直接影响孔与轴的 配合,因此在加工时,最好在一次装夹内完成。
车削φ50mm 的端面保持其尺寸 108,将直接影响方孔内各 孔的正确定位以及齿轮运动时的空间。
φ90 轴线与 R 面垂直度 允差为 0.03,φ72 对φ55 的圆心允差为 0.05,φ37 对φ55 的圆心允差为 0.05,影响回转盘生与主轴联接的正确定位,从 而影响主轴传动齿轮与变速箱的锥齿轮的啮合精度。
由参考文献《机械制造工艺设计简明手册》中的有关和孔 加工的径向精度及机床达到的位置精度可知,上述要求可以达 到,零件的结构工艺性是可行的。
(三)回转盘的生产纲领,生产类型和其它给定条件 根据零件的材料确定毛坯为铸件,其生产类型为中批生 产,由《机械制造工艺设计简明手册》可知,毛坯的铸造方法 采用砂型机械造型,又由于零件的内腔及φ50,φ55,φ37 等 孔均须铸出,故应安放型芯,此外,为消除残余应力,铸出后 还应安排人工时效处理。
参考文献《机械制造工艺设计简明手册》表 2.2-5,该种 铸件的公差等级为 CT8-10 级,加工余量等级 MA 为 G 级,故取 CT 为 9 级,MA 为 G 级。
铸件的分型面选择:通过 R 基准的孔轴线且与φ90 轴线垂 直的面,并在φ230mm 处安装一个离心棒,使φ230mm 以下部 分与左边部分合为一体。
浇冒口位置:位于φ70mm 的轴心线上,各表面总余量。
说明:底面 双侧加工孔 降一级,双 侧加工. 加工表面 基本尺寸 加工余量等级 加工余量数值 R 面 382 G 4.5N 面 230 G 4.5φ37 37 H 3.0φ50 50 H 3.0105 方孔 105 H 4.0 φ62 孔 62 H 3.0φ72 孔 72 H 3.0φ60 孔 60 H 3.0φ55 孔 55 H 3.0φ80 孔 80 H 3.0φ75 孔 75 H 3.0续表:加工表面 基本尺寸 加工余量等级 加工余量数值φ90 孔 90 H 3.0φ230 230 H 5.0由参考文献《机械制造工艺设计简明手册》表 2.2-1,可得铸 件主要尺寸公差如下表所示:主要面尺寸 零件尺寸 总余量 毛坯尺寸 公差等级R 面的轮廓尺寸 382 9 391 3.2N 面的轮廓尺寸 15 4.5 19.5 1.6φ90 顶面至底面 151 3 154 2.5 φ230 230 10 240 2.8φ90 90 6 96 2.2φ50 50 6 56 2.0φ80 80 6 86 2.2其零件毛坯合图(附 A,图纸一张)四 工艺规程设计(一)定位基准的选择回转盘 R 面和φ55mm 孔的轴心线既是装配基准又是设计基 准,用它们作精基准能使加工遵循“基准重合”原则,实现箱 体零件“一面两孔”的典型定位方式。
其余各面和孔也能用它 作定位,这样使加工又遵循了“基准统一”原则,另外 R 面的 面积较大,定位比较稳定可靠,夹紧方案也比较简单,可靠, 操作方便。
粗基准的选择可以考虑以下几点要求:1)如果必须首先保证工件上加工表面与不加工表面之间的位置要求, 应以不加工表面作为粗基准;如果在工件上有很多不须加工的表 面,则应以其中与加工面的位置精度要求较高的表面作为粗基准。
2)如果必须首先保证某很重要表面与不加工面之间的位置要求,应以 首先保证某重要表面的加工余量,均应选择表面作为粗基准。
3)如果需保证各加工面都有足够的加工余量应选加式余量较小的表面 作为粗基准。
4)选择粗基准的表面应平整,没有浇冒口,习砂等缺陷,以便定位可 靠。
5)粗基准一般只能使用一次,特别是主要定位基准面,以免产生较大 的位置公差。
综上所述,分析零件,选择φ100 和φ70 端面作为粗基 准。
最先进行机械加工表面上 R 面和φ55,φ72 的孔,可利用 压极装夹的和专用夹具装夹。
(二)零件表面加工方法的选择:零件表面加工方法选择应考虑以下问题:1)零件表面的加工方法,主要取决于加工表面的技术要求 。
这些技术 要求 还包括由于基准不重合而提高了作为精基准的技术要求。
2)选择加工方法应考虑每种加工方法的加工经济精度范围,材料的性 质及可加工性,工件的结构,形状及尺寸大小,生产纲领及批量生 产现有设备条件等。
3)应考虑各种加工方法的经济精度各表面加工方法的经济精度各表面加工方法 的选择如下:R面:粗刨两次方孔:粗刨,精刨φ105 孔:粗刨,精刨, 锪平φ50:粗车φ62:粗车,半精车,精车φ72:粗镗,半精镗,精镗φ60:粗镗φ55:粗镗,精镗,研磨φ80:粗镗φ37:粗镗,半精镗,精镗φ75:粗车,半精车,精车φ90:粗车,半精车,精车4-φ13:钻 锪平 4-φ32各螺纹孔及其它小孔均用钻床钻孔。
(三)加工顺序的安排因孔φ55 及φ72 的中心线对端面尺在 500mm 上的平行必误 差 0.05,故它们 的加工宜采用工序集中的原则 ,即分别在一 次装夹下将 R 面的两孔同时加工出来,以保证其位置精度。
根据“先面后孔”“先主后次”“先粗后精”的加工原则,将 R 面φ50,φ105,φ80 等孔的粗加工放在前面,精加工放在 后面,各面上和螺纹孔等次要表面,放在最后加工工艺路线如 下:一、 铸,铸造,翻砂,注意检查缺陷二、 油漆,清砂,刷底面,自然时效三、 划下列各尺位的刨位加工线1.以φ72,φ55 外圆毛坯定两孔中心线;2.以φ230 背面向上,将工件顶起,校平各面加工线;3.工件转 90°以φ72,φ55,,中心线找正划各加工线; 4.划φ230 外圆线;5.各孔的中心线对毛面的偏移允差不大于 1.5。
四 刨 压板 装夹 校正1.刨方孔及φ105 端面保持 61.1 5 . 0+ 表面粗糙度 6.32. 刨φ100 端面, 表面粗糙度 12.5;3. 刨φ70 端面,保持尺寸;4.精刨方孔,及φ105 端面主尺寸要求;五.粗车,四爪及胎具夹压1.切平φ230 2 . 0+ 端面保持尺寸为 122;2.切平φ90 端面保持尺寸 29,151 为 152;3.车φ230 为φ231 5. 0 + 4.车φ90 为 90.1 5. 0 + 5.50 至尺寸;6.车φ62 至φ60 5 . 0 + ,保持长 38 2 . 0 + 为 37 5 . 0 + ;7.车平φ50 端面,保证尺寸 108。
六 精车1.光车φ62 端面;2.车φ62 02 . 0 01 . 0 + - 至要求保持尺寸 38 2. 0 + ;3.倒角 1×45°在φ54 处倒角 2×45°切槽 2×0.5;4.车φ90 015. 0 038 . 0 - - 及端面,保持长 30 为 28,及 151 至尺寸要求,精车φ230 2 . 0 + 及端面,保持证长 30 尺寸;5.切槽 4´0.5,φ90 倒角 1×45°七 铣 铁槽 12×5 刻线 360°八 钳 钻 4-φ13 刮 32九 1.粗镗φ37 孔2.精镗φ37 孔至尺寸线3.镗 φ80 2 . 0 + 孔至尺寸,保持尺寸 26 3 . 0 + ;4.倒内角 1×45°;5.粗镗φ55 和φ72 的孔;6.精镗φ55 φ72 的孔,保持φ72 至φ60 的尺寸为 62;7.调头镗 60 至尺寸线8.倒内角 1×45°十 1.钻模 钻孔 攻丝 2.打字码3.研磨φ55 孔至尺寸线十一 油漆,补灰十三 钳,装配,按工艺部装及总装四)选择加工设备及刀具,夹具,量具由于是中批生产,因大部分选择通用机床,辅以专用机床,其 生产方式以通用机床加专用夹具为主,辅以少量专用机床的流 水生产线,工件各机床上的装卸及各个机床间的传递由人工完 成;粗刨 R 面方孔,φ105mm 的端面以及精刨方孔φ105 端面选 择龙门刨床,其型号:BQ208A,刀具为机床强力刨刀,材料为YG168,粗镗φ37, φ80, φ60, φ55, φ72 孔采用坐标,镗床 型号 T4163 选择镗通孔的镗力,专用夹具,游标卡尺,内径一 平分尺;铣槽 12×5,考虑到工件的定位夹紧方案及夹具结构 设计等问题,采用立铣×52K,选择卡盘铣刀,专用夹具和内 径平分尺。
切平φ230 2 . 0+ 端面及φ90 端面选 CA6140 通用车床,选择硬 质合金车刀,其材料为 YG6 通用四爪卡盘;夹具的游标卡尺。
φ230 2 . 0+ ,φ90 等孔,选择 CA6140 车床,刀具选择回转位车 刀;φ50,φ62 等孔,选择 CA6140 车床,刀具选择圆形镗 刀,通用夹具,游标卡尺和外径平分尺;刮成 4×32 的孔,选 择通用直径为φ32mm 带可换导柱锥柄平底锪钻,导柱直径为 φ13,钻 4×13 孔选择摇臂钻床,Z3025 选择锥柄麻花钻,选 用锥柄机用铰刀,专用夹具,快换夹头及塞规,各螺纹孔和螺 栓都选用 Z3025 钻床。
M螺纹孔用塞规检验。
8五)加工工序设计1.工序:粗刨方孔及端面,精刨方孔及φ105 端面,刨削用量 的计算。
a.刨φ100mmr 端面,取粗加工余量为 4.5mm,一次刨削成功, 取 a P =45mm,f=1.5mm/2st 刀杆截面 16×25,刀片厚度是 4mm,查文献[2]7-2-14 得刨削速度 V= kvfg ap p c v xv m r. . . 切削力: z z yz z kF F f F cap F ´ = N 切削功率;4 10 6´ = VFP z m kw,由于刨刀(机夹强力刨刀),材料为 YG 硬质合金,取主偏角 r k =45°取 k=10,刀具耐度 T=60mm,切削速度确定:查文献[2]表 7.2-14,7-2-5 取 6 . 129 = v C , 15 . 0 = Xv , 4 . 0 = Yv ,m=0.2, 15 . 1 = Kv 则:kv apXVfYv T CrV m = = 15 . 1 15 5 . 4 60 6. 129 4 . 0 15 . 0 2 . 0 ´ ´ ´ =34.96 minm切削力的计算:z z yz z z kF F f F ap CF F ´ = N查文献[2]表 7.2-14,7-2-5 取0 . 1 , 75 . 0 , 0 . 1 , 9000 = = = = Z Z Z Z KF YF XF CF 则Fz=900×4.5×1.5 75 . 0 ×1=5489.38N 切削功率的计算:2 .3 10 64 = ´ = FzV Pm kw通过上述计算查表 7-2-18刨削速度 V=3.5 min m 刨削力 Fz=8140N刨削功率 Pm=4.72kwb.粗刨φ105 端面,取粗加工余量为 2mm,查文献[2]表7.2-12 取 p a =2mm,f=2 dst mm 则: 刨削速度 V= min6 . 29 15 . 1 2 2 60 6. 129 15 . 0 2 . 0 m = ´ ´ ´ 刨削功率 Pm= 4 10 6´ FzV=1.5kw查文献[2]表 7-2-18 刨削速度 V=31 minm 刨削力 Fz=5640N刨削功率 Pm=2.88kw精刨φ105 端面取精加工余里为 0.5mm,查文献[2]表 7-2-14,7-2-15 取 5 . 0 = p a f=10 dst mm 则刨削速度 V= 15 . 1 10 5 . 0 60 6. 129 15 . 0 2 . 0 ´ ´ ´ =7.3 minm 刨削力 Fz=900 2530 1 0 . 1 5 . 0 75 . 0 0 . 1 = ´ ´ ´ N 刨削功率 Pm= 4 10 6´ FzV=0.31kw查文献,[2]表 7-2-19 取 V=15 min m ,Fz=8535N,Pm=2.0kw由以上机床功率计算表明该机床功率足够2.工序五,粗车的工序设计1)粗车φ230 端面已知加工材料 HT180 工件尺寸毛坯件.D=240mm,车削 后 d=230mm,加工长度 L=15加工要求:车削后表面粗糙度为 Rc=1.6mm车床:CA6140,加工两端支承在顶尖上,由于工件及铸 造毛坯加工余量达 6mm 而加工要求又较高 Rc=1.6mm,故分两次走刀,粗车加工量取 4mm,精车加工余量为 1mm a. 选择刀具1. 选择机夹转位车刀2. 根据《机械制造工艺设计指导书》表 1.1 CA6140 车床的中心高为 400mm 故选刀杆尺20×30,厚度为 83. 根据表 1.2 粗车(精度)带外皮的铸件毛坯,可选 择 YG6 牌号硬质合金.4. 车刀几何尺寸表(1.3)选择平面带倒棱型车刀 kr=45°,kr=10°,x 0 =60°,y 0 =8° s l =-10°y e =1.0mm y 0 =-10°,by≤ 0.5fb. 选择切削用量1. 确定切削深度ap 由于粗加工余量仅为 4mm,因在 一次走刀内完成故 mmap 4 2 230240 = - = 2. 确定进给量 f,根据表 1-4,在粗车时,刀杆尺 20×30 , ap =3~5mm,以及工件直径为 100~ 600mm,取 f=1.2 r mm 确定的进给量须满足车床进 给要求,故须进行校验根据 1.21 当铸铁的强度 S b >212,ap 4 £ ,f≤4, f≤1.2 r mm kr=45°,进给力 Ff=1930N,由于 Ff 修正系数为 ky 0 . 1 0 = Ff ,k 0. 1 = sFf l 11 . 1 = kkrfF 故实际进给力 Ff=1.2 r mm ,可用选择 车刀磨钝标准及寿命最大磨损量取为:1 表 1.9 车刀寿命 T=30min,确定 切削速度 Vc 根据表 1-10δ P ≤4,f≤1.34 r min 切削速度 Vc(根据表 1-10, δ P ≤4) 切削速度的修正系数为0 . 1 , 65 . 0 = = v kk ktr r , 0 . 1 = ksv 15 . 1 = ktr , 0. 1 = kkv 故.Vc / = kv v t =50´0.65´1.0´0.8´1.15´1.0=29.9minm ,车床主轴 CA6140 车床说明书,当 n min 40 r c = .车床主轴允许功率 Pz=5.9kw,因 Pc<Pz,故所选择的切削用量均可,最后决定的车 削用量为 min 40 , 2 . 1 , 4 r n r mm f mm ap = = = ,min 1 . 30m v c = f)计算基本工时, nf l t m = ,L+L+y+Δ L=15 根据 《机械制造工艺学课程设计》表 1.26 车削时入切 量及超切量:y+s=6mm,则 + + = y L L Δ=21mm故 m t = min 17 . 1 2 .1 5 . 1 21 = ´ 2)粗车φ90 端面,保持尺寸 30 为 29,151 为 152, 已知:工件尺寸坯件 D=96 车削后 d=90,加工长度 34.5.加工要求:车削后表面粗糙度 Ra=32 车床:CA6140,工件两端面支承在顶尖上由于工件 余量达 3mm.而加工要求又较高故分两次走刀,粗 车加工余量为 2.5mm 精车余量为 0.5mm a).选择刀具1.选择机夹可转位车刀2.选择刀杆尺寸为 20×30.刀片厚度为 8.3.根据表 1.2 粗车带外皮的铸件毛坯,可选择 YG6 牌号硬质合金.4.车刀几何尺寸,选择平面带倒棱型车刀 kr=45°,kr=10°,x 0 =60°,y 0 =8° s l =-10° y e =1.0mm y 0 =-10°,by≤ 0.5f b)选择切削用量.1.由于粗加工余量为2.5,在一次走刀内完成,故ap =2.5mm2.确定进给量,根据表 1-4,在粗车铸铁时,刀杆尺寸 20×30, ap ≤3mm,以及工件直径小于 100mm 时,f=0.9~1.3 r mm 按 CA6140 车床说明书,选择 f=0.96 确定的进给量尚须满足车床进给机构强度要 求,故须进行校验根据表 1.22 当铸铁的强度, δ P =208~248MPaap ≤3.2,f≤0.96 rmv ,kr=45°,F f =1140N 切削时的进给力小于车床进给机构允许的进给力, 故所选 f=0.96 n mm ,可用选择车刀磨钝标准及寿命 磨损量取 1mm 车刀寿命 T=30min确定切削速度 Vc,根据《机械设计制造工艺学指导 书》表 1.27 V kv apXVfYv T Crm=式中: ksvkkv ktv kmv kv . . . = 20. 0 15 . 0 2 . 0 96. 0 5 . 2 30 189´ ´ =c v kv其中 0. 1 , 0 . 1 = = krv ktv 15 . 1 96. 0 5 . 2 30 8. 189 20 . 0 15 . 0 2 . 0 ´ ´ ´ =vc ×0.63×0.8=48.9 r mm min 2 . 162 909. 48 1000 rn = ´ ´ = p 按 CA6140 车床说明书选择 Nc=160 minr 这时 2. 48 100016096 1000= ´ ´ ==p p pnc vc 校验机床功率,当δ P =208~1420, ap ≤2.8Vc≤49 min mm Pc=1.7kw切削功率的修正系数 0. 1 = = kkrFc kkrpc 0 . 1 0 0 = = c c F ky p ky 故实际切削功率为 Pc=1.7 根据 CA6140 车床说明书,当 min 160 r n c = 车床主轴允许功率 P E 大于 1.7 故可行最后决定的车削用量ap =2.5mm,f=0.96,n=160,Vc=48.2 minm计算本工时:nflt m = L=30 车削时,入切量及超切量Y+Δ=5.0mm,L=30+5.0=35mm 故 min 227 . 096 . 0 160 35 = ´ = m t 3).车φ62 至φ60+0.5,保持尺寸长 38 2 . 0 为 37 5 . 0 + 已 知工件尺寸坯件 D=66mm 车削后: d=60mm,工件长 度 L=38mm加工要求:车削后表面粗糙度为 Ra=1.6加工余量为 3mm 而加工要求又较高,故分两次走刀, 粗车加工余量为 2mm 精车加工余量为 1mma) 选择刀具查《机械制造工艺学课程设计指导书》 可选取圆形镗刀,刀杆直径为 20mm,刀片厚度 为 8mm,材料为 YG6 牌号硬质合金。