钻杆失效
焊接修复钻杆的失效分析及预防措施_黄成

[收稿日期]2010-02-10 [作者简介]黄成(1974-),男,1994年胜利石油学校毕业,工程师,现从事钻井管具的使用与维护工作。
焊接修复钻杆的失效分析及预防措施黄 成,何元君 (胜利石油管理局黄河钻井总公司,山东东营257000)唐洪发 (川庆钻探工程有限公司培训中心,四川成都610059)王晓晓 (中国石油大学石油工程学院,山东青岛266555)[摘要]概述了摩擦焊修复钻杆的基本情况,通过对胜利油田16起修复钻杆的失效事故进行了统计,分析发现修复钻杆管体失效事故70%发生在内加厚过渡区消失部位,失效原因是结构不合理造成应力集中,产生腐蚀疲劳。
钻杆管体中部失效事故占30%,失效原因是由于磨料磨损造成壁厚变薄及蚀坑造成的腐蚀共同作用的结果。
针对修复钻杆失效的原因,提出了详尽的预防措施和方法。
[关键词]摩擦焊修复钻杆;失效分析;预防;应力集中;腐蚀疲劳[中图分类号]T E28[文献标识码]A [文章编号]1000-9752(2010)03-0312-03钻杆摩擦对焊是利用钻杆管体与接头端面摩擦生热而融合粘结的一种热压焊接法[1]。
我国通过摩擦对焊修复Á127mm 钻杆已有十几年的历史。
修复了大量的钻杆,解决了钻井急需,大大缓解了钻杆供求矛盾,在油田广泛使用,创造了很好的经济效益。
对焊修复钻杆连续使用几年后相继出现了一些问题,如管体或内加厚过渡区部位刺穿、刺断等事故,造成了一定的损失。
鉴于此,笔者对修复钻杆失效原因进行了研究分析,找出了解决措施。
1 对焊修复钻杆失效情况统计钻杆作为钻柱的重要组成部分在井下的受力十分复杂[2]。
钻具涡动引起的钻柱与井壁间的摩擦和高频撞击,钻杆磨损现象十分严重,包括:管体均匀磨损、偏磨、内外表面腐蚀、硬伤等缺陷。
如果这样的钻杆再连续使用上万小时,累计进尺十多万米后,则很可能在薄弱位置发生刺穿、断裂事故。
笔者对胜利油田近年来对焊钻杆管体发生了失效的事故进行了统计。
钻杆失效分析及超声检测技术分析
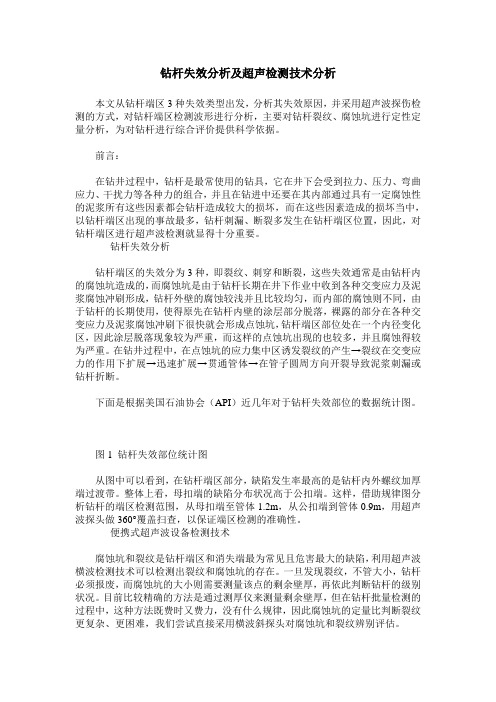
钻杆失效分析及超声检测技术分析本文从钻杆端区3种失效类型出发,分析其失效原因,并采用超声波探伤检测的方式,对钻杆端区检测波形进行分析,主要对钻杆裂纹、腐蚀坑进行定性定量分析,为对钻杆进行综合评价提供科学依据。
前言:在钻井过程中,钻杆是最常使用的钻具,它在井下会受到拉力、压力、弯曲应力、干扰力等各种力的组合,并且在钻进中还要在其内部通过具有一定腐蚀性的泥浆所有这些因素都会钻杆造成较大的损坏,而在这些因素造成的损坏当中,以钻杆端区出现的事故最多,钻杆刺漏、断裂多发生在钻杆端区位置,因此,对钻杆端区进行超声波检测就显得十分重要。
钻杆失效分析钻杆端区的失效分为3种,即裂纹、刺穿和断裂,这些失效通常是由钻杆内的腐蚀坑造成的,而腐蚀坑是由于钻杆长期在井下作业中收到各种交变应力及泥浆腐蚀冲刷形成,钻杆外壁的腐蚀较浅并且比较均匀,而内部的腐蚀则不同,由于钻杆的长期使用,使得原先在钻杆内壁的涂层部分脱落,裸露的部分在各种交变应力及泥浆腐蚀冲刷下很快就会形成点蚀坑,钻杆端区部位处在一个内径变化区,因此涂层脱落现象较为严重,而这样的点蚀坑出现的也较多,并且腐蚀得较为严重。
在钻井过程中,在点蚀坑的应力集中区诱发裂纹的产生→裂纹在交变应力的作用下扩展→迅速扩展→贯通管体→在管子圆周方向开裂导致泥浆刺漏或钻杆折断。
下面是根据美国石油协会(API)近几年对于钻杆失效部位的数据统计图。
图1 钻杆失效部位统计图从图中可以看到,在钻杆端区部分,缺陷发生率最高的是钻杆内外螺纹加厚端过渡带。
整体上看,母扣端的缺陷分布状况高于公扣端。
这样,借助规律图分析钻杆的端区检测范围,从母扣端至管体1.2m,从公扣端到管体0.9m,用超声波探头做360°覆盖扫查,以保证端区检测的准确性。
便携式超声波设备检测技术腐蚀坑和裂纹是钻杆端区和消失端最为常见且危害最大的缺陷,利用超声波横波检测技术可以检测出裂纹和腐蚀坑的存在。
一旦发现裂纹,不管大小,钻杆必须报废,而腐蚀坑的大小则需要测量该点的剩余壁厚,再依此判断钻杆的级别状况。
钻具常见失效形式
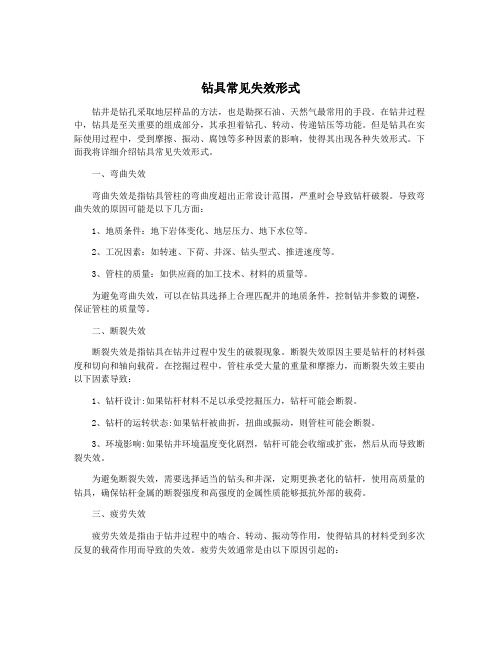
钻具常见失效形式钻井是钻孔采取地层样品的方法,也是勘探石油、天然气最常用的手段。
在钻井过程中,钻具是至关重要的组成部分,其承担着钻孔、转动、传递钻压等功能。
但是钻具在实际使用过程中,受到摩擦、振动、腐蚀等多种因素的影响,使得其出现各种失效形式。
下面我将详细介绍钻具常见失效形式。
一、弯曲失效弯曲失效是指钻具管柱的弯曲度超出正常设计范围,严重时会导致钻杆破裂。
导致弯曲失效的原因可能是以下几方面:1、地质条件:地下岩体变化、地层压力、地下水位等。
2、工况因素:如转速、下荷、井深、钻头型式、推进速度等。
3、管柱的质量:如供应商的加工技术、材料的质量等。
为避免弯曲失效,可以在钻具选择上合理匹配井的地质条件,控制钻井参数的调整,保证管柱的质量等。
二、断裂失效断裂失效是指钻具在钻井过程中发生的破裂现象。
断裂失效原因主要是钻杆的材料强度和切向和轴向载荷。
在挖掘过程中,管柱承受大量的重量和摩擦力,而断裂失效主要由以下因素导致:1、钻杆设计:如果钻杆材料不足以承受挖掘压力,钻杆可能会断裂。
2、钻杆的运转状态:如果钻杆被曲折,扭曲或振动,则管柱可能会断裂。
3、环境影响:如果钻井环境温度变化剧烈,钻杆可能会收缩或扩张,然后从而导致断裂失效。
为避免断裂失效,需要选择适当的钻头和井深,定期更换老化的钻杆,使用高质量的钻具,确保钻杆金属的断裂强度和高强度的金属性质能够抵抗外部的载荷。
三、疲劳失效疲劳失效是指由于钻井过程中的啮合、转动、振动等作用,使得钻具的材料受到多次反复的载荷作用而导致的失效。
疲劳失效通常是由以下原因引起的:1、超负荷:如果管柱承受超出其载荷极限的应力,随着时间的推移,它们将在高载荷情况下疲劳。
2、变形:如果管柱在钻井过程中出现变形,如扭曲、振动等,其疲劳极限会降低。
3、环境因素:诸如温度、酸碱性等环境因素可能导致钻具的材料受到损害。
为了避免疲劳失效,以下是几个重要的措施:1、选择尽可能高的钻杆金属强度。
2、控制切削转速,减少外部载荷情况下的功率。
钻杆接头失效分析

前言2007年1月底,井下作业公司在用φ127(接头NC50)钻杆发生失效,失效形式为螺纹缺损,粘着以及接头密封台肩面撕裂性缺损。
委托方提供的钻杆工作参数为:进尺1243m,钻压4~6T,泵压10Mpa,转速80r/min。
据委托方说明该批钻杆为新产品,第一次使用。
事故发生后,该批钻杆集中放置于井下作业工司油管厂场地,经查看125根钻杆中有9组接头存在损伤,其中严重损伤2组,呈现螺纹被冲刺缺损,而且其中1组有螺纹粘着、撕毁现象;其余7组存在不同程度的接头密封台肩面黏着撕裂性缺损现象。
一、外观形貌分析1严重失效2组钻杆外观形貌如图1~4所示。
螺纹粘着、撕毁图1第1组外螺纹接头外观形貌螺纹粘着、撕毁图2第1组内螺纹接头外观形貌冲击起始区图3第2组内螺纹接头外观形貌图4第2组内螺纹接头外观形貌如图所示:第一组钻杆失效形式为螺纹缺损,粘扣。
从缺损形貌可见,图示内外钻杆接头对应部位同时存在对应的螺纹缺损和黏着形貌,因此图示内外钻杆接头为工作时对接的接头。
外螺纹接头自密封面起第6、7、8扣粘结,内螺纹自密封面起第4、5、6扣粘结;从螺纹缺损形貌分析,可以断定螺纹缺损由高压钻井液冲刺造成。
第一组钻杆失效形式为螺纹缺损,从螺纹缺损形貌分析,可以断定螺纹缺损由高压钻井液冲刺造成。
2接头密封面损伤接头密封面损伤外观形貌如图5~6所示。
7组接头密封面存在图示的撕脱性损伤。
撕脱性损伤图5密封面撕脱性损伤一撕脱性损伤图6密封面撕脱性损伤二自图1所示的接头,按照《SY/T5290-2000石油钻杆接头》之规定,采取材质、机械性能、硬度及金相试样,逐个进行实验。
二、材质分析按照《SY/T5290-2000石油钻杆接头》取样后经直读光谱分析结果如下表1:《SY/T5290-2000石油钻杆接头》规定接头材质为合金钢,且对S,P作出规定,含量不超过0.030%,从检测结果看来,符合标准要求。
三、机械性能按照《SY/T5290-2000石油钻杆接头》取样后,依据《GB/T228金属拉伸试验法》进行试验测得结果如表2。
塔里木油田用钻杆失效原因分析及预防措施

Investigation of Failure Causes for Drill Pipes Used in Tarim Oil Field and Relevant Preventative Actions
Zhou Jie 1, Lu Qiang 1, L ü Shuanlu 1,2, Su Jianwen 1, Feng Shaobo 1, Xie Juliang 1, Wang Zhongsheng 1
48
技术交流
塔里木油田用钻杆失效原因分析及预防措施
周 杰 1, 卢 强 1, 吕拴录 1,2, 苏建文 1, 冯少波 1, 谢居良 1, 王中胜 1
( 1. 塔里木油田 , 新疆 库尔勒 841000 ; 2. 中国石油大学机电工程学院 , 北京 100249 )
摘 要 : 塔里木油田 钻 井 条 件 苛 刻 , 钻 杆 受 力 情 况 复 杂 , 容 易 发 生 钻 杆 失 效 事 故 。 分 析 了 钻 杆 失 效 的 原 因 ,
[6-8]
图 3 钻杆内螺纹接头表层摩擦热裂纹及摩擦热影响区形貌
图 4 钻杆内螺纹接头表面白亮淬火层和高温回火层组织
盘转速超过 70 r/min 时钻柱剧烈扭摆震动 , 甩打井 口 , 严重影响了钻井的正常生产 。 钻杆管体和接头由摩擦焊接在一起 , 钻杆的直 线度是由管体直线度和管体与接头对焊后的同轴度 两部分决定的 。 钻杆管体直线度偏差越大 , 则钻杆 管体与对焊接头的同轴度偏差就越大 , 钻杆的直线 度偏差也就越大 ; 管体两端镦粗加厚部分不同方向 的外径差值越大 , 则对焊后管体与接头的同轴度偏 差就越大 。 钻杆管体是按 API Spec 5D 标准 [9]生产和检验 的 。 API Spec 5D 标 准 规 定 所 有 Φ 114.3 mm 及 更
石油钻杆的应力失效分析
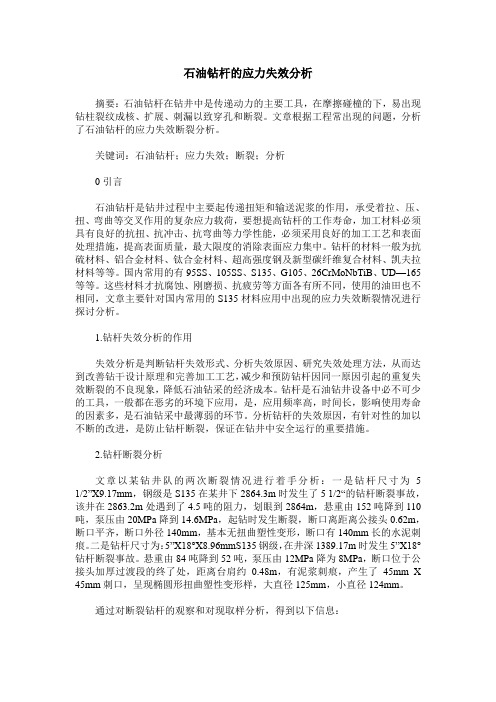
石油钻杆的应力失效分析摘要:石油钻杆在钻井中是传递动力的主要工具,在摩擦碰橦的下,易出现钻柱裂纹成核、扩展、刺漏以致穿孔和断裂。
文章根据工程常出现的问题,分析了石油钻杆的应力失效断裂分析。
关键词:石油钻杆;应力失效;断裂;分析0引言石油钻杆是钻井过程中主要起传递扭矩和输送泥浆的作用,承受着拉、压、扭、弯曲等交叉作用的复杂应力载荷,要想提高钻杆的工作寿命,加工材料必须具有良好的抗扭、抗冲击、抗弯曲等力学性能,必须采用良好的加工工艺和表面处理措施,提高表面质量,最大限度的消除表面应力集中。
钻杆的材料一般为抗硫材料、铝合金材料、钛合金材料、超高强度钢及新型碳纤维复合材料、凯夫拉材料等等。
国内常用的有95SS、105SS、S135、G105、26CrMoNbTiB、UD—165等等。
这些材料才抗腐蚀、刚磨损、抗疲劳等方面各有所不同,使用的油田也不相同,文章主要针对国内常用的S135材料应用中出现的应力失效断裂情况进行探讨分析。
1.钻杆失效分析的作用失效分析是判断钻杆失效形式、分析失效原因、研究失效处理方法,从而达到改善钻干设计原理和完善加工工艺,减少和预防钻杆因同一原因引起的重复失效断裂的不良现象,降低石油钻采的经济成本。
钻杆是石油钻井设备中必不可少的工具,一般都在恶劣的环境下应用,是,应用频率高,时间长,影响使用寿命的因素多,是石油钻采中最薄弱的环节。
分析钻杆的失效原因,有针对性的加以不断的改进,是防止钻杆断裂,保证在钻井中安全运行的重要措施。
2.钻杆断裂分析文章以某钻井队的两次断裂情况进行着手分析:一是钻杆尺寸为 5 1/2”X9.17mm,钢级是S135在某井下2864.3m时发生了5 1/2“的钻杆断裂事故,该井在2863.2m处遇到了4.5吨的阻力,划眼到2864m,悬重由152吨降到110吨,泵压由20MPa降到14.6MPa,起钻时发生断裂,断口离距离公接头0.62m,断口平齐,断口外径140mm,基本无扭曲塑性变形,断口有140mm长的水泥刺痕。
钻具断裂的失效分析及预防

2017年09月钻具断裂的失效分析及预防张孝兵海照新陈保民(川庆钻探工程公司长庆钻井总公司,陕西西安710018)摘要:油气田勘探开发过程中钻具受力状态十分复杂,所以其失效形式也多种多样。
如过量变形、断裂、表面磨损等。
发生井下钻具断裂事故,处理费用数额大,更甚者会发生打捞失败而弃井。
通过多年井下钻具断裂事故的处理经验、案例分析及试验研究总结出,大多数的钻杆断裂事故都是由于疲劳而引起的。
关键词:失效;疲劳;过量变形;钻具断裂1钻具断裂事故发生的一般规律在钻井实践中观察到的大量钻杆断裂现象可概括为:①钻杆大多数的断裂事故发生于旋转钻进过程中或在钻进后立即提离井底的时候;②大多数断裂发生在据钻杆接头1.2米的范围内;③管体的疲劳和腐蚀疲劳断裂均发生在内加厚过渡区消失处;④在有腐蚀性的洗井液中将引起管体或接头严重坑蚀,从断裂面上看到的这些裂纹是从内表面的腐蚀斑点开始的;⑤上提遇卡而拔断钻杆,断裂位置通常发生在已经产生疲劳裂纹,但尚未发展成为断裂的部位;⑥钻杆接头螺纹的疲劳断裂多发生于内螺纹接头大端第一和第二螺纹牙根部或外螺纹接头大端第一和第二螺纹牙根部。
2钻具断裂事故中钻具的失效形式2.1钻杆管体的疲劳和腐蚀疲劳断裂钻杆发生疲劳和腐蚀疲劳断裂破坏的主要原因是由于钻杆在弯曲井眼中旋转时发生周期性交变旋转弯曲应力以及井下腐蚀介质共同作用所致。
影响钻杆疲劳和腐蚀疲劳断裂的主要因素:①钻杆材料的抗拉强度和疲劳极限的影响;②钻杆材料冲击韧性的影响;③钻杆表面质量的影响;④腐蚀环境的影响;⑤拉伸和弯曲的组合影响;⑥累计疲劳。
2.2钻杆内加厚过渡区刺穿失效事故在钻杆管端镦粗加厚工艺控制过程中,由于内加厚过渡区太短,在钻杆使用中,在该区产生严重的应力集中,进而导致腐蚀集中并形成较深的腐蚀坑。
在旋转钻井过程中,钻杆受到旋转弯曲交变载荷的作用,在腐蚀坑底产生疲劳裂纹,最终导致钻杆刺穿或断裂,这属于钻杆的腐蚀疲劳断裂。
2.3内涂层钻杆加厚过渡区刺穿失效事故(内刺穿)由于钻杆(内涂层)内加厚过渡区的形状不良,在钻杆使用时导致局部涂层脱落并产生集中腐蚀(涂层脱落处的腐蚀速率要远远高于正常的腐蚀速率),很快会产生较深的腐蚀坑。
钻杆及其接头的早期失效分析与措施研究
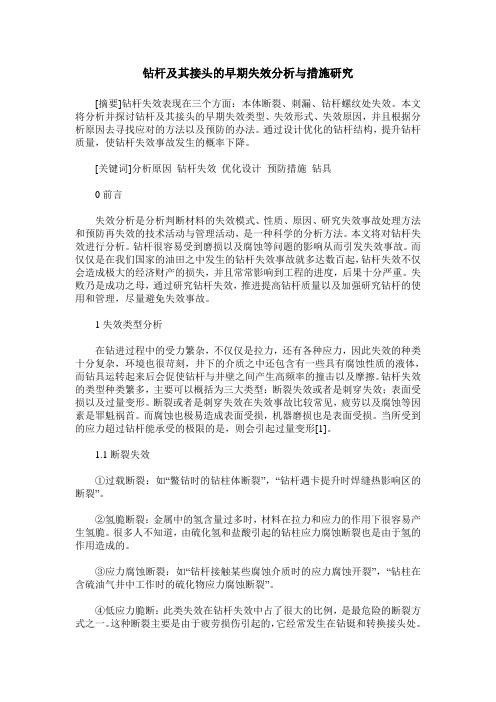
钻杆及其接头的早期失效分析与措施研究[摘要]钻杆失效表现在三个方面:本体断裂、刺漏、钻杆螺纹处失效。
本文将分析并探讨钻杆及其接头的早期失效类型、失效形式、失效原因,并且根据分析原因去寻找应对的方法以及预防的办法。
通过设计优化的钻杆结构,提升钻杆质量,使钻杆失效事故发生的概率下降。
[关键词]分析原因钻杆失效优化设计预防措施钻具0前言失效分析是分析判断材料的失效模式、性质、原因、研究失效事故处理方法和预防再失效的技术活动与管理活动,是一种科学的分析方法。
本文将对钻杆失效进行分析。
钻杆很容易受到磨损以及腐蚀等问题的影响从而引发失效事故。
而仅仅是在我们国家的油田之中发生的钻杆失效事故就多达数百起,钻杆失效不仅会造成极大的经济财产的损失,并且常常影响到工程的进度,后果十分严重。
失败乃是成功之母,通过研究钻杆失效,推进提高钻杆质量以及加强研究钻杆的使用和管理,尽量避免失效事故。
1失效类型分析在钻进过程中的受力繁杂,不仅仅是拉力,还有各种应力,因此失效的种类十分复杂,环境也很苛刻,井下的介质之中还包含有一些具有腐蚀性质的液体,而钻具运转起来后会促使钻杆与井壁之间产生高频率的撞击以及摩擦。
钻杆失效的类型种类繁多,主要可以概括为三大类型:断裂失效或者是刺穿失效;表面受损以及过量变形。
断裂或者是刺穿失效在失效事故比较常见,疲劳以及腐蚀等因素是罪魁祸首。
而腐蚀也极易造成表面受损,机器磨损也是表面受损。
当所受到的应力超过钻杆能承受的极限的是,则会引起过量变形[1]。
1.1断裂失效①过载断裂:如“鳖钻时的钻柱体断裂”,“钻杆遇卡提升时焊缝热影响区的断裂”。
②氢脆断裂:金属中的氢含量过多时,材料在拉力和应力的作用下很容易产生氢脆。
很多人不知道,由硫化氢和盐酸引起的钻柱应力腐蚀断裂也是由于氢的作用造成的。
③应力腐蚀断裂:如“钻杆接触某些腐蚀介质时的应力腐蚀开裂”,“钻柱在含硫油气井中工作时的硫化物应力腐蚀断裂”。
④低应力脆断:此类失效在钻杆失效中占了很大的比例,是最危险的断裂方式之一。
- 1、下载文档前请自行甄别文档内容的完整性,平台不提供额外的编辑、内容补充、找答案等附加服务。
- 2、"仅部分预览"的文档,不可在线预览部分如存在完整性等问题,可反馈申请退款(可完整预览的文档不适用该条件!)。
- 3、如文档侵犯您的权益,请联系客服反馈,我们会尽快为您处理(人工客服工作时间:9:00-18:30)。
三、避免钻杆非正常失效的措施
钻杆的基本力学工况钻杆在内外充满钻井液的狭长井眼里工作,通常承受压、弯、扭、液力等载荷。
如果钻杆所受应力小于每平方米206.8牛顿时,钻杆虽经过无数次的弯曲,也不会产生疲劳裂纹。
钻井时钻杆承受弯曲、扭转和拉伸应力组成的复合应力很大,特别是在大位移定向井及水平井中扭矩极大,钻杆在100万次弯曲次数时便产生疲劳微裂纹;微裂纹产生后便不断扩大延伸,此时如果具有腐蚀作用的高压钻井液进入微裂纹中,就会加速裂纹扩展,最终导致钻井液刺穿钻杆的失效事故。
刺穿发展的结果,使钻杆有效断面不断缩小,刺孔加裂纹的总长度超过其临界裂纹尺寸时,即发生断裂。
除旋转向下的运动,同时还有钻杆的各种振动和涡动。
根据钻杆的失效原因分析,钻杆除正常磨损而失效外,钻杆的非正常失效原因可分为为两个方面:工人操作原因和钻杆自身质量原因。
因此,我们可以从提高钻杆质量和规范操作两方面来避免钻杆非正常失效。
1.提高钻杆质量
(1)钻杆材料选择:为适应钻杆的受力分析,钻杆杆体应有较高的抗拉强度、较好抗弯性能和较好的冲击韧性。
杆体材料应选择中碳合金结构无缝钢管,合金元素中应含有较多的Cr、Mo等元素以提高材料的抗拉强度和冲击韧性,含有Mn、Si等元素以提高材料的弹性
(即抗弯性能)。
有时还含有微量的B、V等元素以提高材料的淬透性。
常用的杆体材料有:36Mn2V、35CrMo、42MnMo7、35CrMnSi、45MnMoB等。
用于杆体的无缝钢管的壁厚均匀度和轧制缺陷也是影响钻杆质量的重要因素。
如轧制的钢管壁厚均匀情况严重,当钻杆较大的扭力作用时,容易在壁厚较薄处纵向裂开。
有的钢管有重皮、气孔等缺陷,钻杆易从此处产生应力集中断裂或刺漏。
钻杆接头受力最为复杂,接头材料须有很高综合机械性能。
钻杆接头多采用35CrMo或42CrMo.30CrMnSiA棒料制造,但经过锻造的接头材料能大大提高其综合机械性能。
(2)加工工艺选择:目前国内钻杆从加工工艺分主要有整体锻造钻杆(简称整体钻杆)、镦粗+摩擦焊钻杆(简称镦焊钻杆)和单纯摩擦焊钻杆(简称摩擦焊钻杆)。
三种钻杆的优缺点比较如表二。
表二
性能、价格摩擦焊钻杆整体钻杆镦焊钻杆
丝扣耐磨性好差好
接头强度高中高
接头加工精度高差高
保定尺长度易难易
焊缝强度低——高
整体性能差(易断)较好很好
价格低高低
性价比低中高
(3)镦粗加厚段的处理:不管是整体钻杆还是镦焊钻杆,镦厚部分与未镦厚部分之间的过渡段处理好坏是影响镦锻质量的主因素。
过渡段应有足够的长度,壁厚过渡均匀、光滑,无折皱。
杆体经镦锻后最好进行整体调质处理,以去除过渡段内应力,并提高其综合机械性能。
(4)接头结构型式
a. 应力分散槽:试验研究表明,导向、定向钻杆受循环弯曲应力作用而疲劳断裂是钻杆的主要失效形式,而这种失效主要发生在钻杆公接头根部或公接头螺纹根部。
在钻杆公接头根部设计应力分散槽可有效地减小该处应力集中,从而提高其抗弯能力。
此外,尽量增大螺纹直径、锥度螺纹设计和加大螺纹丝底圆弧半径也能明显改善钻杆公接头根部的抗弯能力。
b. “双顶”结构:所谓“双顶”结构,即在钻杆公、母扣拧紧时母扣端部与公扣台肩处顶紧的同时,母扣的内台肩处也与公扣的端部顶紧。
“双顶” 结构钻杆的加工难度大,但它与“单顶”钻杆相比具有多方面的优越性:
l 密封效果好钻进液由内向外泄漏需经两个密封面,泄漏阻力大。
2 能承受更大的扭矩“双顶”钻杆提供两个抗扭台肩,其台肩总接触面积远大于普通钻杆,因而承受的扭矩也远大于普通钻杆。
3 提高钻杆的使用寿命普通钻杆往往因为接头磨损,母扣端部变薄而被公扣锥成喇叭口,从而使整根钻杆失效。
“双顶”钻杆在接头磨损严重后内台肩仍有效地起作用,钻杆仍能继续使用。
(5)丝扣的表面处理:丝扣表面氮化处理能有效地防止粘扣,还能提高丝扣的耐磨性,从而提高其使用寿命。
氮化层厚度一般在0.2~0.3mm,厚度过大容易产生碎性裂纹,厚度过小则抗粘扣效果差。
整体钻杆无法进行氮化处理,取而代之的是层厚小得多的磷化处理。
(6)螺纹加工精度:接头螺纹应在数控车床上用成形螺纹车刀加工,应尽量提高螺纹牙的表面质量,降低其表面粗糙度值(Ra≤1.6μm)提高光洁度,减少应力集中且有利保证钻杆的互换性。
接头螺纹紧密距应控制在合理的范围之内,保证丝扣啮合良好。
2. 预防螺纹牙断裂所采取的措施
螺纹牙断裂失效约占钻杆失效的70%,根据螺纹牙断裂失效的原因分析,采取以下预防措施可有效降低该类失效形式的发生率:
(1.)加工螺纹时,要避免在螺纹终端(退刀处)产生不完全螺纹,防止在该处产生应力集中,致使螺纹牙疲劳破坏。
(2.)在接箍底部和外螺纹内端部采取合适的密封措施,尽量避免管道内的流质进入螺纹接合处,减少腐性磨损,防止螺纹牙锈蚀而导致其强度不足。
(3.)对加工出的螺纹进行射线检测或者磁粉探伤等无损检测,及时发现管道螺纹部位的表面和内部缺陷,避免有缺陷的螺纹扣下井。
(4.)选用大小合适的扭矩旋紧螺纹,避免因预紧力过大而超出螺纹材料的强度极限造成螺纹牙折断。
3.施工工艺的改进
(1)规范操作:施工中要严格按照各种钻杆所允许的拉力、扭矩和曲率半径来使用钻杆。
对于施工企业来说,只有按规范使用钻杆,才能有效避免钻杆的非正常失效。
(2)过渡杆的作用:在扩孔和拉管过程中,与扩孔钻头连接的那根钻杆的曲率半径很可能远小于钻孔设计的曲率半径(如图1),即r<<R< span>,从而使这根钻杆在回转并受拉力作用下而受到较大的循环应力作用,使其疲劳损伤,进而产生裂纹而断裂。
这种断裂多发生在距钻杆公接头0.3~0.8m之间。
在普通钻杆与扩孔钻头之间连接过渡杆,可使扩孔钻头与普通钻杆之间的小曲率过渡由加过渡杆来承担,从而保护了普通钻杆。
过渡杆的这种作用往往被用户所忽视,但是很多看似无法解释的断钻杆事故其原因就在于此。
(3)防止钻杆失稳:钻杆是力学中的细长杆,在受压力作用下有失稳的趋势。
因此,在导向孔施工阶段要对处于自由状态的钻杆进行约束,防止在造斜顶进过程中钻杆失稳而弯曲失效。
钻杆失稳情况多发生在钻机夹持器至入地点之间的钻杆段,应尽量缩短该段长度,或采取适当的约束措施。
为防钻杆失稳,一般应使钻杆自由段长度小于钻杆直径的20倍。
(4)丝扣油的使用:质量好的丝扣油能有效防止钻杆粘扣、减小卸扣扭矩、减少扣面磨损。
(5)冲洗液的使用:在砂层、卵砾石层中钻进时,应用优质泥浆作冲洗液。
泥浆在钻杆外壁形成泥皮,起润滑作用,能减小钻进扭矩,减少钻杆磨损,对保护钻杆起到非常重要的作用。
(6)钻杆的检查:钻杆使用一段时间后,就应检查钻杆的磨损、弯曲、表面划痕等情况,要及时淘汰磨损过度、明显弯曲及表面划痕较深的钻杆。
尤其要仔细检查镦锻过渡段的磨损情况,该处往往最易被磨损变薄而断裂。