火焰切割机的电气设计(一)讲解
管道火焰切割机结构设计及计算

切割嘴的三种形式 前两种切割枪的火焰内有短的白色火焰,只有充分接近铸坯时才能切割。外 混式切割枪其火焰的焰心为白色长线状,一般切割嘴距铸件 50mm 即可切割。这 种切割枪长时间使用割嘴不会过热;切缝小而且切割表面平整,金属损耗小;因 预热洋气和燃气喷出后在空气中混合燃烧, 不会产生回火、 灭火, 工作安全可靠, 并且长时间使用切割嘴不会产生过热。 本次设计采用的外混式。 外混式切割枪,它形成的火焰焰心为白色长线状,切割嘴可距工件 50~100mm 内切割;外混式切割枪具有铸坯热清理效率高,切缝小,切割枪寿命长等优点。 切割枪是用铜合金制造,并通水冷却。
注:固体成分,含量中百分数皆指质量分数,气体成分含量皆指体积分数。
三.传动机构
1.链条的分类 类别 链条按不同的用途和功能区分为传动链、 输送链、 曳引链和专用特种链四种。 传动链: 主要用于传递动力的链条。 输送链: 主要用于输送物料的链条。 曳引链: 主要用于拉曳和起重的链条。 专用特种链: 主要用于专用机械装置上的、具有特殊功能和结构的链条。 传动链 A 系列传动用短节距精密滚子链,B 系列传动用短节距精密滚子链,加重系列 传动用短节距精密滚子链,石油钻机传动滚子链,传动用短节距精密套筒链,传动 用双节距精密滚子链,重载传动用弯板滚子链,传动用齿形链,摩托车链,自行车 链。 输送链 短节距精密滚子输送链, 双节距滚子输送链, 长节距输送链, 输送用平顶链, 输送用短节距精密套筒链,轻型双铰接悬挂输送链 易拆链 埋乔板输送链,工程用钢制滚子输送链,工程用钢制套筒输送链,农用滚子 输送链,农机用夹持输送链 曳引链 板式链,起重用圆环链,矿用高强度圆环链,提升机圆环链,销轴链,冷拔 机链,块式重载位曳链,滚子曳引链,曳引用弯板链
1.2065
63.438
火焰切割
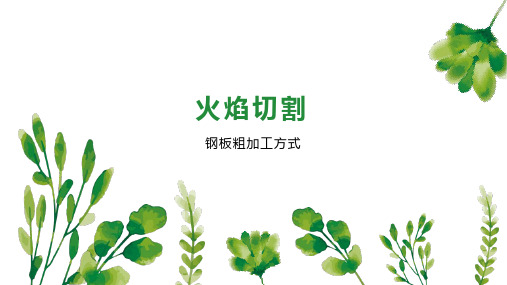
切割气体
火焰切割气体常用的有乙炔、丙烷、液化气、焦炉煤气、天然气等,从污染性、耗能量、成本比等各方面综 合考虑的话,天然气是目前最适合用于切割的气体。但天然气也有其局限性,就是火焰温度不高,这就造成了切 割效率不如乙炔。为了弥补这一缺憾一般用天然气切割的厂家都是选择在天然气中加入增效剂,以提高火焰温度, 改善切割效率。如包钢、中铁山桥集团用的是加入了神麒增益剂的增效天然气,包钢生产的中厚板因为平整度高 中标了文昌卫星中心项目,而中铁山桥用增效天然气是为珠港澳大桥的建设做准备,由此,增效天然气的效果很 显著。
火焰切割
钢板粗加工方式
01 介绍
03 切割气体
目录
02 分类 04 工具
05 发展趋势
07 影响因素
目录
06 流程
火焰切割(Flame Cutting)是钢板粗加工的一种常用方式。火焰切割即气切割,传统的是使用乙炔气切割, 后来用丙烷,现在出现了天然气切割,并且由于天然气储量丰富、价格便宜、无污染等特性,已经成为火焰切割 的首选。天然气火焰切割一般会加入天然气添加剂,生成新型火焰切割气,用该气进行火焰切割可使切割效果更 好,提高了切割效率,降低了切割成本。
流程
1.检查工作场地是否符合安全要求,割炬、氧气瓶、乙炔瓶(或乙炔发生器及回火防止器)橡胶管、压力表等 是否正常,将气割设备按操作规程连接好。
机械毕业设计(论文)-火焰切割机设计【全套图纸三维】
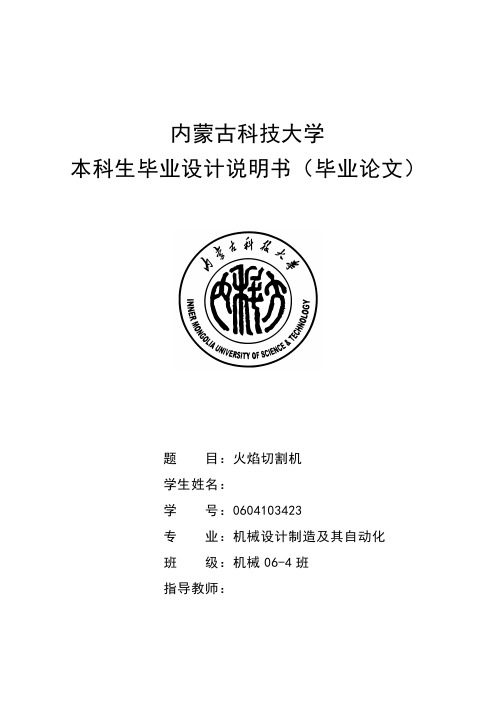
内蒙古科技大学本科生毕业设计说明书(毕业论文)题目:火焰切割机学生姓名:学号:0604103423专业:机械设计制造及其自动化班级:机械06-4班指导教师:摘要:随着工业现代化的发展,设备自动化系统在工业工程中占有越来越重要的地位。
在钢铁冶金中,火焰切割机是最传统的热切割方法,不论是钢坯加工还是钢板加工,都有广泛应用。
本设计是基于对由德国GEGA公司生产,提供给包钢炼钢厂使用的大型小车式火焰切割机的研究、理解、和仿效而完成的。
其中包括了总体分析、机架设计、小车设计、电机选取等部分的设计、计算及校核。
关键字:火焰切割机、设计、校核、测量滚、同步运行、Abstract:目录摘要: (1)Abstract: (1)第一章绪论 (7)1.1 火焰切割 (7)1.1.1 工艺过程 (7)1.1.2 必要条件 (7)1.1.3 材质 (7)1.2 关于火焰切割机的术语级名词解释 (7)第二章火焰切割机具体说明 (9)2.1 火焰切割机总体描述 (9)2.1.1 火焰切割机作用 (9)2.1.2 火焰切割机同步运行 (9)2.1.3 火焰切割机设备说明 (9)2.2 火焰切割机技术说明 (9)2.2.1 火焰切割机设备结构 (9)2.2.1.1 火焰切割机框架结构 (10)2.2.1.2 火焰切割机的包括运行驱动装置在内的箱体 (11)2.2.1.3 火焰切割机切割枪小车——圆坯铸机 (13)2.2.1.4 火焰切割机切割枪小车——方坯铸机 (14)2.2.1.5 火焰切割机的夹紧 (14)2.2.1.6 火焰切割机限位开关装置 (15)2.2.1.7 火焰切割机的机器位置编码器 (15)2.2.1.8 火焰切割机的粒化 (15)2.2.1.9 测量辊 (16)2.2.2 火焰切割机的气体——工艺设备 (17)2.2.2.1 火焰切割机的气体控制盘(每台设备一个) (17)2.2.2.2 火焰切割机通往机器的介质供给 (18)2.2.2.3 火焰切割机机器上的介质供给 (18)2.2.2.4 火焰切割机装有SDS 36F 烧嘴的SB 500F 重型切割枪 (19)第三章总体方案设计 (20)3.1 火焰切割设备的特点 (20)3.2 切割设备方案 (20)3.2.1 火焰切割设备 (20)3.2.1.1 切割机的结构方案 (20)3.2.1.2 切割枪方案 (21)3.2.1.3 切割枪传动方案 (23)3.2.1.4 同步机构方案 (24)3.2.1.5 端面检测器方案 (27)3.2.1.6 自动定尺装置方案 (27)第四章火焰切割主要参数的确定 (28)4.1 气体压力(切割操作台前) (28)4.2 气体消耗量(按一个切割枪) (28)4.3 最小切割长度 (29)4.4技术数据 (30)4.4.1火焰切割机的详细说明 (30)4.4.1.1 尺寸 (30)4.4.1.2 速度 (30)4.4.1.3 铸坯尺寸 (31)4.5 火焰切割机小车夹紧力 (32)第五章立柱设计 (33)5.1机架设计准则: (33)5.2机架设计的一般要求: (34)5.3 立柱的设计 (35)5.3.1 立柱外形 (35)5.3.2 立柱截面形状 (35)5.3.3立柱热处理 (36)第六章电机的选择 (37)6.1 变速方式 (37)6.1.1无级变速 (37)6.1.2 有级变速 (38)6.2 步进电机启动有突跳启动和升速启动。
火焰切割机

如果金屬熔點低於燃點,金屬就會在切割時熔化,使溫度不能繼續上升, 導致在切割氧的作用下並不產生燃燒反應,如果金屬先融化也會使切口不整 齊。
而含C量增加時,熔點會降低,燃點會升高,當含C量≧0.7%的高碳鋼, 燃點與熔點相近,對切割不利,因此對不銹鋼、鑄鐵等燃點高於熔點的金屬 切割應使用特殊的切割法。
• 燃氣:乙炔、丙烷、天然氣、液化石油氣與焦爐煤氣等,以成本與熱 值來選擇。切割過程中,85%熱量由金屬燃燒時所提供,燃氣熱值的 考量是較其次的。
• 天然氣有比空氣輕、便宜等優點,但火燄溫度低,相對要求預熱時間 長。
• 鐵粉載流氣體:N2或經乾燥的壓縮空氣。 • 燃氣壓力與消耗量,預熱時間,切割速度,所能切割的最小尺寸,這
2020/5/12
10
火焰切割取樣
• 鑄胚內部品質判定要靠取樣切割,進行硫印(含S量、偏析程度)與酸 浸試驗。 *硫印法可參考GB/T4236-1984《鋼的硫印檢驗方法》、ISO4986︰ 1979《鋼-硫印低倍檢驗方法》。 *酸浸法GB/T226-1991《鋼的低倍組織及缺陷酸浸檢驗法》 、 ISO4969︰1980《鋼-強礦物酸腐蝕下的宏觀檢驗》 。
• 噴鐵粉火焰切割方法同低碳鋼的氧-乙炔切割,只是設備上多了噴鐵 粉的裝置,一開始先以火焰預熱鋼胚,同時鐵粉伴隨切割氧同時輸出, 噴射到鋼胚上的切割位置,鐵粉受到火焰的預熱,加熱至燃點,鐵粉 在火焰中進行著氧化反應,放出大量熱能,使氧化膜融化,熱量往鋼 胚下層傳遞,使鑄胚產生金屬燃燒反應放出大量熱能,而高壓切割氧 會把熔融的金屬氧化物吹開形成切縫,切割槍沿厚度方向切開,切割 過程中不斷的噴鐵粉,完成切割。
火焰切割在电气设备中的应用
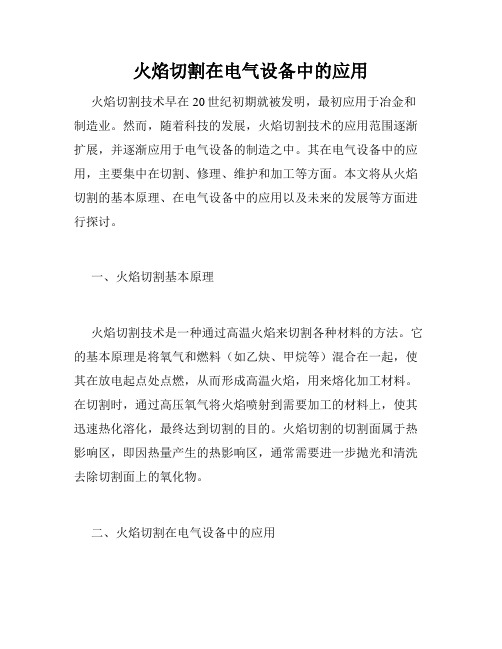
火焰切割在电气设备中的应用火焰切割技术早在20世纪初期就被发明,最初应用于冶金和制造业。
然而,随着科技的发展,火焰切割技术的应用范围逐渐扩展,并逐渐应用于电气设备的制造之中。
其在电气设备中的应用,主要集中在切割、修理、维护和加工等方面。
本文将从火焰切割的基本原理、在电气设备中的应用以及未来的发展等方面进行探讨。
一、火焰切割基本原理火焰切割技术是一种通过高温火焰来切割各种材料的方法。
它的基本原理是将氧气和燃料(如乙炔、甲烷等)混合在一起,使其在放电起点处点燃,从而形成高温火焰,用来熔化加工材料。
在切割时,通过高压氧气将火焰喷射到需要加工的材料上,使其迅速热化溶化,最终达到切割的目的。
火焰切割的切割面属于热影响区,即因热量产生的热影响区,通常需要进一步抛光和清洗去除切割面上的氧化物。
二、火焰切割在电气设备中的应用1.切割:火焰切割技术可以应用于各种金属和合金的切割。
在电气设备中,常需要对铁、铜、铝等材料进行切割,以满足产品加工和生产需要。
火焰切割可以切割各种厚度和形状的工件,能够完成自动化和定制化的生产任务。
2.维护:火焰切割技术可以应用于电气设备的修理和维护。
例如,在变电站中,如果设备的金属外壳出现损坏,需要立即进行修复,以确保设备的正常运转。
火焰切割技术可以用来修复或更换损坏的部分,使设备能够恢复正常工作状态。
3.加工:火焰切割技术可以应用于电气设备的加工。
例如,在导线制造和线缆制造生产中,常需要对铜和铝等导体材料进行切割和加工。
火焰切割可以快速、高效地完成这些加工任务,减少生产成本和提高加工效率。
三、火焰切割技术未来的发展随着科技的不断发展,火焰切割技术在未来的发展方向上也将逐渐发生变化。
其中最为明显的变化是技术的自动化处理。
自动化的火焰切割技术可以使生产过程更加高效和节约成本。
它能够实现对工件的自动精准定位和切割,大幅降低人工干预的需要,从而提高生产效率和质量。
另外,近年来还出现了一些新型的火焰切割技术,如等离子切割和激光切割技术等。
龙门式数控火焰切割机横向进给系统的设计设计
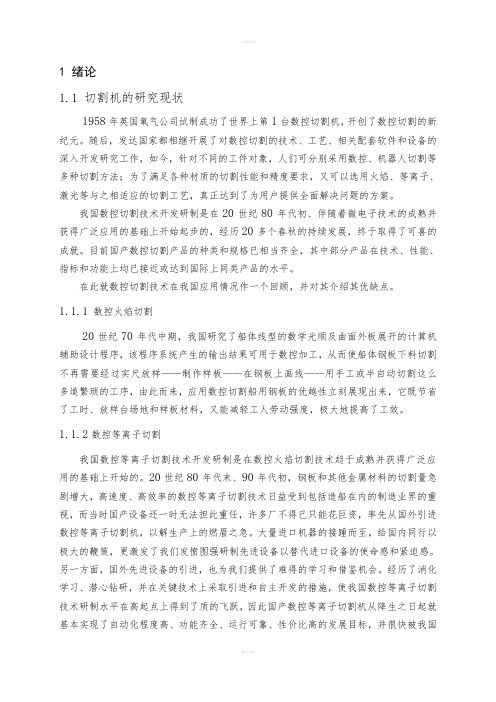
1 绪论1.1 切割机的研究现状1958年英国氧气公司试制成功了世界上第1台数控切割机,开创了数控切割的新纪元。
随后,发达国家都相继开展了对数控切割的技术、工艺、相关配套软件和设备的深入开发研究工作,如今,针对不同的工件对象,人们可分别采用数控、机器人切割等多种切割方法;为了满足各种材质的切割性能和精度要求,又可以选用火焰、等离子、激光等与之相适应的切割工艺,真正达到了为用户提供全面解决问题的方案。
我国数控切割技术开发研制是在20世纪80年代初、伴随着微电子技术的成熟并获得广泛应用的基础上开始起步的,经历20多个春秋的持续发展,终于取得了可喜的成就。
目前国产数控切割产品的种类和规格已相当齐全,其中部分产品在技术、性能、指标和功能上均已接近或达到国际上同类产品的水平。
在此就数控切割技术在我国应用情况作一个回顾,并对其介绍其优缺点。
1.1.1数控火焰切割20世纪70年代中期,我国研究了船体线型的数学光顺及曲面外板展开的计算机辅助设计程序,该程序系统产生的输出结果可用于数控加工,从而使船体钢板下料切割不再需要经过实尺放样——制作样板——在钢板上画线——用手工或半自动切割这么多道繁琐的工序,由此而来,应用数控切割船用钢板的优越性立刻展现出来,它既节省了工时、放样台场地和样板材料,又能减轻工人劳动强度,极大地提高了工效。
1.1.2数控等离子切割我国数控等离子切割技术开发研制是在数控火焰切割技术趋于成熟并获得广泛应用的基础上开始的。
20世纪80年代末、90年代初,钢板和其他金属材料的切割量急剧增大,高速度、高效率的数控等离子切割技术日益受到包括造船在内的制造业界的重视,而当时国产设备还一时无法担此重任,许多厂不得已只能花巨资,率先从国外引进数控等离子切割机,以解生产上的燃眉之急。
大量进口机器的接踵而至,给国内同行以极大的鞭策,更激发了我们发愤图强研制先进设备以替代进口设备的使命感和紧迫感。
另一方面,国外先进设备的引进,也为我们提供了难得的学习和借鉴机会。
培训教材(火焰切割机)
(2)定位运动 •
点动操作不能进行精准的定位,要 让设备准确的移动到某一坐标,就需 要定位运动操作。定位运动可以让选 定的对象准确地运动至给定的坐标处。 可以单个移动体定位,即单轴定位; 也可以多个移动体同时定位,即多轴 定位。
每个小车、废边和大车电机均可进 行单轴定位。只需给定移动速度和定 位位置,点击“确认启动”按钮,就 可启动定位操作,此时除“定位中止” 按钮,所有控制按钮均不可用。设备 运动至定位位置后,控制按钮恢复正 常状态。也可以点击“定位中止”按 钮来强行结束当前的定位运动。
切割机行程重叠范围: 1#~2#切割机 10000 mm 2#~3#切割机
2.4 性能参数
• • • •
最小位移单位:0.1 mm 钢板轮廓扫描精度:详细技术协议书 钢板切割精度:详细技术协议书 切割厚度:40-100mm 纵向最大移动速度:24m/min;横向最大移动速度: 12m/min; • 切割速度 :0-700mm/min (详见切割速度表) • 工作环境温度:60 0C • 切割钢板最高温度:3000C
(3)离合器
•
带废边枪的小车1、2、3、4 上的主枪位置是可变的,可以用废 边电机来带动。离合器off时,主 枪不随废边电机运动;离合器on 时,进行废边的点动和定位操作可 以改变废边枪的位置,同时带动主 枪运动,即主枪和废边枪相对位置 保持不变。
(4)主枪归零
•
通常,非斜切废边的时候,主枪的 位置应该一直处于废边电机坐标原点 处。因人工操作使离合器on或切割过 程中止造成主枪位置离开零点会带来 不便。点击“主枪归零”按钮会自动 启动主枪归零操作,利用废边电机和 离合器把主枪带回零点,并把废边枪 也开回零点,自动归零过程中其余按 钮变为不可用。归零完成后恢复正常。 也可点击“归零中止”来强行中止自 动归零过程
火焰切割机中自动定尺装置设计
自动定尺装置为把铸坯切割成规定的定尺长度,在切割小车中装有自动定尺装置。
定尺机构是由过程控制计算机进行控制。
图3.8 是用于铸坯连铸机的定尺机构。
气缸推动测量辊,使之顶在铸坯下面,靠摩擦力使之转动。
利用脉冲发生器发出脉冲信号,换算出铸坯长度,达到规定长度时,计数器发出脉冲信号,开始切割铸坯。
图3.8自动定尺装置(1)定尺辊受的滚动摩擦力计算:KNm g G kg V m S l V m S VT S S T T T 8.68.94942878.5648.07626m 1152.05.461.061.0kg/7626 )2738008358.08523 273M)t 0.8358-8523[19]m5.406.407.05858323≈⨯===⨯===⨯⨯===+-=+===⨯===+=ρρ切割方坯体积:((知文献钢的密度计算,由参考取切割位移:用时间:由前面计算可知切割所预切如下图3.9运输辊受力分析:图3.9运动辊受力简图查机械手册可知圆柱形车轮滚动摩擦因素为mm 6.0=δ;滑动摩擦因素为f=0.4. 取运输辊直径d=180mm 运输辊做纯滚动时:r f f 11==F M δ N F G F 28.7 29000866.0 r /f 2/111=⨯⨯===δ当运输辊做纯滑动时摩擦力:N F 1720200864.0f f 12=⨯=⨯=即摩擦力f :28.7<f<1720取f=40N 定尺辊做纯滚动,在这里我们取定尺辊直径为d=120mm 。
因此即可算出气缸的推力推FKgGKN F F M 3.4246.06040frfr f =<=⨯====δδ推推因此取f=40N 合理(2)气缸的设计当气缸以推力作功时,缸径的大小根据公式ηπS P F D 推4=(3.23)气缸公称压力系列(GB7938-1987)选择Ps = 1.5MPa)(65.2%805.114.340004mm D =⨯⨯⨯=根据查参考文献[15]选取气缸内径为D=80mm活塞杆直径d 与气缸内径D 比查参考文献[15] 取0.2 ~ 0.32.0/=D d得到 d = 16mm可认只按强度条件计算活塞直径d 。
PLC自动控制火焰切割机
[摘要]:利用欧姆龙CPM1A系列PLC控制螺旋焊管在生产过程中的切割,实现工业自动化。
螺旋焊管的生产过程中,其以螺旋线式前进的。
当电源接通,按下启动开关后,切管机便在PLC控制下进行跟踪切割。
接近开关发出定尺信号,通过电磁阀使随动轮与螺旋管接触,整体机构跟随螺旋管同步前进,PLC控制继电器发出点火信号,控制点火电路产生电火花点燃乙炔,产生预热火焰,点火完成。
同时启动KC5型跟踪电机使预热火焰跟踪钢管同步旋转来预热,预热完毕,吹氧阀打开将预热的熔化点吹开,开始切割,并停止跟踪。
切割完毕由轨道行程开关或手动停止按钮发出信号控制停止,关闭氧气阀,乙炔阀,气缸阀,然后跟踪返回,小车返回。
关键词:CAPMIA PLC,自动化,触发,整流,KC5跟踪电机。
[ABSTRACT]:The design is using Programmable Logic Controller(PLC) , which is one of CPM1A series made by the Omron company ,to control the spiral welded pipes' production.PLC controls the cutting machine to cut the spiral welded pipes automatically.During the production process of the spiral welded pipes , the pipe rotated itself and at the same time went along straight line ,and its movement trial was helical line. When the power is connected and the operator presses the start switch, the PLC will control the cutters and following motor to cut the pipes .The proximity switches detect the signal and then input them to the PLC, then the PLC sends out controlled signal.The following wheel will contact with the pipe under the magnetic valve's control ,the following wheel will follow the pipe rotating synchronously.The spark coil will ignite the ethyne under the signal sended out by the PLC. While the KC5(the following motor) started to track the rotated pipe synchronously,the flame will preheat the pipe. When the preheating is over and then the oxygen valve is opened under the control signal, then began to cut the pipe open, and at the same time stop tracking.Signal is made by the travel switch or stop button to stop, then close the oxygen control valve, the ethyne control valve and the pneumatic cylinder, and then the following motor returns, the vehicle back.Key words:CAPMIA PLC, automation, trigger and rectification, KC5 track motors.第1章绪论1. 1课题背景可编程控制器(Programmable Logic Controller)是计算机家族的一员,是为工业控制应用而设计制造的通用控制器。
火焰切割机的电气设计(一)
火焰切割机的电气设计(一)论文关键词:火焰切割机火焰切割机电气控制火焰切割机PLC论文摘要:火焰切割机是利用燃气和氧气将铸坯快速燃烧,达到切断铸坯的目的,其优点是在线设备轻,一次性投资省,适应铸坯的温度宽;缺点是切割渣不易处理,金属损耗大,但当铸坯较长时,金属损耗则较少。
本次课题实际内容主要是针对火焰切割机的电气控制部分进行研究和设计,本文引用电气控制PLC原理,通过各种电气元件的选型和计算,以及PLC程序的编译,简单的介绍了该火焰切割机电气控制方面的设计过程和设计方法。
火焰切割机的电气设计包括PLC、变频器、控制变压器、低压电气元件的选型以及STEP 7的程序编译。
1 绪论1.1 连续铸钢的概念连续铸钢是一项把钢水直接浇铸成形的节能新工艺,它具有节省工序、缩短流程,提高金属收得率,降低能量消耗,生产过程机械化和自动化程度高,钢种扩大,产品质量高等许多传统模铸技术不可比拟的优点。
自从20世纪50年代连续铸钢技术进入工业性应用阶段后,不同类型、不同规格的连铸机及其成套设备应运而生。
20世纪70年代以后,连铸技术发展迅猛,特别是板、方坯连铸机的发展对加速连铸技术替代传统的模铸技术起到了决定性作用。
1.2 连铸比的概念连铸坯的吨数与总铸坯(锭)的吨数之比叫做连铸比,它是衡量一个国家或一个钢铁工厂生产发展水平的重要标志之一,也是连铸设备、工艺、管理以及和连铸有关的各生产环节发展水平的综合体现。
1.3 国内外连铸技术的发展1.3.1 国外连铸技术的发展概况20世纪50年代,连铸开始用于钢铁工业生产。
连铸坯产量仅有110万t 左右,连铸比约为0.34%20世纪60年代,弧型连铸机问世,连铸进入了稳步发展时期。
年产铸坯能力达4000万t以上,连铸比达5.6%。
20世纪70年代,世界范围的两次能源危机促进了连铸技术大发展,连铸进入了迅猛发展时期。
铸坯产量已逾2亿t,连铸比上升为25。
8%。
20世纪80年代,连铸进入完全成熟的全盛时期。
- 1、下载文档前请自行甄别文档内容的完整性,平台不提供额外的编辑、内容补充、找答案等附加服务。
- 2、"仅部分预览"的文档,不可在线预览部分如存在完整性等问题,可反馈申请退款(可完整预览的文档不适用该条件!)。
- 3、如文档侵犯您的权益,请联系客服反馈,我们会尽快为您处理(人工客服工作时间:9:00-18:30)。
[ 09-09-16 10:28:00 ] 作者:未知编辑:studa090420论文关键词:火焰切割机火焰切割机电气控制火焰切割机PLC论文摘要:火焰切割机是利用燃气和氧气将铸坯快速燃烧,达到切断铸坯的目的,其优点是在线设备轻,一次性投资省,适应铸坯的温度宽;缺点是切割渣不易处理,金属损耗大,但当铸坯较长时,金属损耗则较少。
本次课题实际内容主要是针对火焰切割机的电气控制部分进行研究和设计,本文引用电气控制PLC原理,通过各种电气元件的选型和计算,以及PLC程序的编译,简单的介绍了该火焰切割机电气控制方面的设计过程和设计方法。
火焰切割机的电气设计包括PLC、变频器、控制变压器、低压电气元件的选型以及STEP 7的程序编译。
1 绪论1.1 连续铸钢的概念连续铸钢是一项把钢水直接浇铸成形的节能新工艺,它具有节省工序、缩短流程,提高金属收得率,降低能量消耗,生产过程机械化和自动化程度高,钢种扩大,产品质量高等许多传统模铸技术不可比拟的优点。
自从20世纪50年代连续铸钢技术进入工业性应用阶段后,不同类型、不同规格的连铸机及其成套设备应运而生。
20世纪70年代以后,连铸技术发展迅猛,特别是板、方坯连铸机的发展对加速连铸技术替代传统的模铸技术起到了决定性作用。
1.2 连铸比的概念连铸坯的吨数与总铸坯(锭)的吨数之比叫做连铸比,它是衡量一个国家或一个钢铁工厂生产发展水平的重要标志之一,也是连铸设备、工艺、管理以及和连铸有关的各生产环节发展水平的综合体现。
1.3 国内外连铸技术的发展1.3.1 国外连铸技术的发展概况20世纪50年代,连铸开始用于钢铁工业生产。
连铸坯产量仅有110万t左右,连铸比约为0.34%20世纪60年代,弧型连铸机问世,连铸进入了稳步发展时期。
年产铸坯能力达4000万t以上,连铸比达5.6%。
20世纪70年代,世界范围的两次能源危机促进了连铸技术大发展,连铸进入了迅猛发展时期。
铸坯产量已逾2亿t,连铸比上升为25。
8%。
20世纪80年代,连铸进入完全成熟的全盛时期。
世界连铸比由1981年的33。
8%上升到1990年的64。
1%。
连铸技术的进步主要表现在对铸坯质量设计和质量控制方面达到了一个新水平。
20世纪90年代以来,近终形连铸受到了实际各过的普遍关注,近终形薄板坯连铸与连扎相结合,形成紧凑式短流程,其发展速度之快,非人们所料及。
1.3.2 我国连铸发展概况近几年,我国连铸发展很快。
除海南、西藏和宁夏,都有了连铸。
2000年,连铸坯产量达到11450万吨,突破一亿吨,位居各国之首。
连铸比88.08%,超过了世界连铸比的平均数87.2%。
从1996~2000年的五年,连铸坯的产量增加7017万吨,平均年增1403万吨,连铸比比1995(46.48%)增长41.6个百分点 ,平均年增8.32个百分点.这个增速在世界上也是罕见的.2000年,全连铸单位达到130个占有连铸单位的总数165个的78.8%(没有连铸的单位仅12个);高效和较高效连铸机占连铸机总数339台的约50%.在品种质量方面,可以说除个别品种外都能生产并满足质量要求。
进入新世纪,连铸生产发展更快.2001年连铸坯产量达13820万吨,连铸比达92.8%,比2000年猛增2370万吨,增长21%,连铸比增长4.72个百分点。
2002年预计将产连铸坯16500万吨连铸比将达94%左右,全连铸单位将达157个,占当前有连铸的单位总数175的89.7%.2002年预计将新增连铸机60台200流,产能3500万吨以上.到2002年在线连铸机将达444台,产能共19450万吨.预计到2005年连铸机产能将达23500万吨,产量将达21000万吨,连铸比将达97%.现在新建的钢长起步都是全连铸,新建的连铸机基本上都是高效的,而且达产很快。
1.4 今后我国连铸发展要求1.提高品质.国内市场所需的品种应能自己生产并保证质量,充分满足市场要求,并有利于扩大出口。
2.提高效率.还有近半数的连铸机需要进行高效化改造,已改造的效率需进一步提高,新建连铸机必须高效化且一步到位,提高近终型连铸的比率,进一步提高效率。
3.提高连铸比.尤其是提高特钢连铸比, 进一步发展全连铸.目前,影响我国连铸比的主要是几个大的钢铁企业和一批老的特钢企业,包钢和攀钢可望于2003或2004年实现全连铸,宝钢可望于2006年实现全连铸,太钢也正在努力。
4.流程最佳化.炉外精炼、铸坯热装、连轧成材,连铸是中间环节和中心环节,力求匹配、衔接最佳化,使之充分发挥炼钢及轧钢的能力,缩短工艺流程,降低各项消耗,提高劳动生产率,增加经济效益。
1.5 连铸机的组成连铸机主要由钢包运载装置、中间包、中间包运载装置、结晶器、结晶器振动装置、二次冷却装置、拉坯矫直机、引锭装置、切割装置和铸坯运出装置等部分组成。
弧形连铸机1-钢包转台; 2-中间罐; 3-结晶器; 4-二次冷却及导向装置; 5-结晶器振动装置6-拉矫机; 7-引锭存放装置; 8-切割装置; 9-铸坯运出装置1.6 弧形连铸机的生产流程连续浇注时,钢水罐中的钢液经过中间罐注入水冷铜板结晶器内,结晶器的底部由引锭头承托,使引锭头与结晶器壁密封后便可开始浇注。
注入结晶器的钢水受到水冷铜模的强烈冷却,迅速成为具有一定厚度坯壳的铸坯。
当钢液浇至规定高度时,开动拉矫机,拉锟夹住引锭杆以一定速度把铸坯连续拉出结晶器。
为了防止铸坯坯壳被拉断,并减少结晶器内的拉坯阻力,在浇注过程中,结晶器始终要进行往复振动。
铸坯拉出结晶器以后,进入二次喷水冷却区,直到完全凝固。
当铸坯拉出拉矫机后,脱去引锭装置,铸坯经过矫直,再经过割机切成定尺长度,由输送锟道运走,这一整个过程是连续进行的。
铸坯切割装置处于整个连铸装置的末端,也是整个连铸流程的结尾部分,负责把连铸坯按照轧钢机的要求切割成定尺或倍尺长度。
铸坯是在连续运行中完成切割,因此切割装置必须与铸坯同步运动。
1.7切割设备的技术要求1.把被矫直的铸坯,按要求切割成一定长度。
2.铸坯切口应与铸坯长度方向垂直,切面平整,切头不应有大于原铸坯断面的变形。
3.切割能力应适应铸坯温度的变化。
1.8切割设备的类型及特点1.8.1 种类小方坯连铸机采用的切割设备种类较多,有电动机械剪,液压剪,火焰切割机等。
1.8.2火焰切割机原理火焰切割机是利用燃气和氧气将铸坯快速燃烧,达到切断铸坯的目的,其优点是在线设备轻,一次性投资省,适应铸坯的温度宽;缺点是切割渣不易处理,金属损耗大,但当铸坯定尺较长时,金属损耗则较少,因而目前有些中、小企业又趋向建火焰切割机。
1.8.3 火焰切割机的种类火焰切割机用于小方坯铸机的机型目前有三种:其一自动化程度较高,投资也较大的为全自动化的火焰切割机,切割枪的摆动,切割小车的随动及返回,以及自动计数定尺,都由微机控制。
电动或气压做动力源。
另两种近来较流行的经济型的火焰切割机:一种称无动力型火焰切割机,另一种称夹坯型火焰切割机。
(1)无动力型火焰切割机这种火焰切割机不同于全自动的火焰切割机,除切割小车返回使用液压缸外,其余全无动力源,是靠铸坯带动产生各种动作,当撞头落在锟道线上,铸坯运行一个定尺长度至撞头处,则顶动撞头并带着切割小车前进,切割小车上装切割枪,切割枪的摆动运动来源于摆动机构上有一个导轮,当切割小车被铸坯带动前进时,此导轮将沿着一个固定的靠模曲线前进,因曲线的起伏使导轮带动切割枪,产生切割摆动运动。
定尺撞头的上部装在定尺导杆上,由于定尺不同,撞头在定尺导杆上的位置可以通过调节装置进行调节,导杆的末端有释放导模,当撞头走到导杆末端时,完成尺切割后,撞头将因导模的作用,自动释放抬起。
则被切断的铸坯经锟道送出。
撞头及切割小车又被液压缸带动返回原处,而撞头落下成等待位置,全部切割过程结束。
该切割机的动力来源是铸坯,铸坯不顶到撞头,则切割小车不会行走,切割枪不会摆动,无法进行切割,显然该机不能进行非定尺的切割,如切头、切尾,或事故切割,这是该机的最大弱点。
(2)夹坯型火焰切割机为了克服上述切割机的缺点,一种新型的切割机对随动运动作了改进,不用被动的顶坯方式,而改为主动的夹坯随动方式,并用汽缸作动力,解决了不能切头、切尾的问题。
夹坯型火焰切割机,切割机前设置里夹坯锟,夹坯夹头,火焰切割枪的摆动仍是由摆动机构和靠模完成,切割小车返回用液压缸或用气动马达,夹坯夹头杠杆通过转轴,靠汽缸传动,产生夹紧或放松的动作,而气缸的进排气则由工人遥控,或由定尺装置发出信号,显然该机应另配备定尺发信号装置。
目前小方坯连铸机采用这种带有主动夹坯机构的火焰切割机日渐增多。
1.8.4 切割枪割炬又称为切割枪,是火焰切割机的重要部件。
切割枪是由枪体和切割嘴组成。
而切割嘴是它的核心部件。
外混式切割枪,它形成的火焰焰心为白色长线状,切割嘴可距铸坯50~100mm内切割;外混式切割枪具有铸坯热清理效率高,切缝小,切割枪寿命长等优点。
切割枪是用铜合金制造,并通水冷却。
一般当铸坯宽度小于600mm时,用单枪切割;宽度大于600mm的铸坯,用双枪切割。
但要求两支切割枪在同一条直线上移动,以防切缝不齐。
切割时割枪应能横向运动和升降运动。
当铸坯宽大于300mm时,切割枪可以平移,见图a,当坯宽小于300mm时,割枪可做平移或扇形运动,见图b,割枪的扇形运动的一个优点是切割先从铸坯角部开始,使角部得到预热有利于缩短切割时间,同时在板坯切割时先做约5°的扇形运动,割枪转到垂直位置后,再做快速平移运动,见图C。
图1.2 割枪运动1.8.5 铸坯自动定尺装置锟子通过气缸与铸坯接触,铸坯带动锟子转动并发出脉冲信号,由计数器按定尺发出信号开始切割。
1.9 切割机的选用火焰切割机,在线设备简单,一次性投资低,切头比较平整,不受铸坯温度的限制,但金属损耗高,有烟尘和切割渣的污染,需要增加额外的投资。
这里选用了夹坯型火焰切割机。
图1.3 火焰切割装置图1.4 夹钳式同步机构简图1.10 课题关键问题及难点这次课题关键问题及主要难点有:1.工作环境温度高,零部件的选用与保护。
2.变频器的参数设置。
3. 电气元件的选用。
4.火焰切割机机械部件与PLC控制系统的搭配。
5.电气图主要技术参数的计算。
6.STEP 7的编程。
2 火焰切割机机械控制2.1 切割机机架由轨道和轨道梁、走行和检查平台、横梁和立柱、能介管道和电缆等组成。
1.轨道采用高架形式,每流两根。
安装轨道的轨道梁断面为“日”字形,内部通有冷却水,火切机轨道梁公用一个大机架。
2.行和检修平台。
平台盖板上部为钢制花纹板,下部为钢板。
3.分布在铸流两侧,为了保证切割操作工有良好的操作视线,横梁采用下置式安放。
4.机能介管道和电缆设置在远离拉矫机一侧,如配置测量辊装置空气管和电缆设置靠拉矫机一侧。