压铸模标准DiecastingStandard
压铸件k模相关标准

压铸件k模相关标准
压铸件K模相关标准涉及到压铸件的生产和质量控制标准,主要包括国际标准、行业标准和国家标准。
以下是一些常见的压铸件K模相关标准:
1. 国际标准,国际上常用的压铸件K模相关标准包括ISO 8062(有关铸造尺寸公差的标准)、ISO 945(有关表面粗糙度的标准)等。
这些国际标准通常被广泛应用于压铸件的生产和检测过程中。
2. 行业标准,不同国家和地区的压铸件行业会制定一些行业标准,以规范压铸件的生产和质量控制。
例如,美国的NADCA(North American Die Casting Association)制定了一系列与压铸件生产相关的标准,包括产品设计、模具设计、工艺控制等方面的标准。
3. 国家标准,各个国家也会制定相关的国家标准,以确保压铸件的质量和安全。
例如,中国国家标准化管理委员会发布了GB/T 15115-2009《压铸铝合金技术条件》和GB/T 15114-2009《压铸锌合金技术条件》等标准,用于规范压铸铝合金和压铸锌合金件的生产和质量要求。
总的来说,压铸件K模相关标准涵盖了压铸件的材料、尺寸、表面质量、工艺要求等方面,这些标准的制定和遵循对于保证压铸件的质量和可靠性具有重要意义。
厂家在生产压铸件时需严格遵循相关标准,以确保产品质量和安全性。
压铸模具技术标准及要求
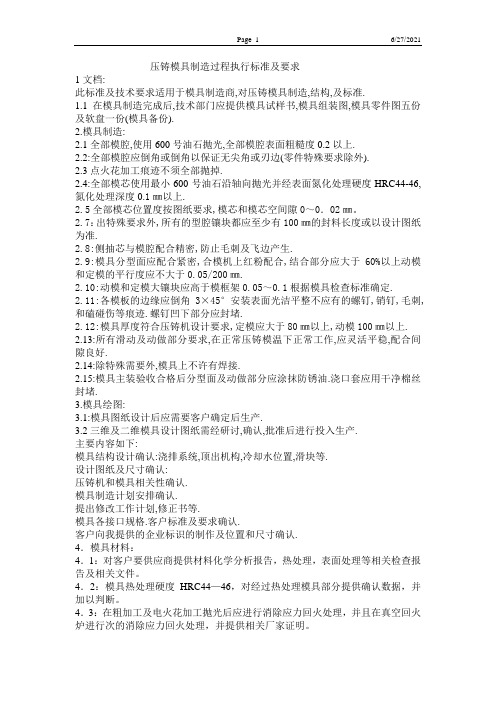
压铸模具制造过程执行标准及要求1文档:此标准及技术要求适用于模具制造商,对压铸模具制造,结构,及标准.1.1在模具制造完成后,技术部门应提供模具试样书,模具组装图,模具零件图五份及软盘一份(模具备份).2.模具制造:2.1全部模腔,使用600号油石抛光,全部模腔表面粗糙度0.2以上.2.2:全部模腔应倒角或倒角以保证无尖角或刃边(零件特殊要求除外).2.3点火花加工痕迹不须全部抛掉.2.4:全部模芯使用最小600号油石沿轴向抛光并经表面氮化处理硬度HRC44-46,氮化处理深度0.1㎜以上.2.5全部模芯位置度按图纸要求,模芯和模芯空间隙0~0.02㎜。
2.7:出特殊要求外,所有的型腔镶块都应至少有100㎜的封料长度或以设计图纸为准.2.8:侧抽芯与模腔配合精密,防止毛刺及飞边产生.2.9:模具分型面应配合紧密,合模机上红粉配合,结合部分应大于60%以上动模和定模的平行度应不大于0.05/200㎜.2.10:动模和定模大镶块应高于模框架0.05~0.1根据模具检查标准确定.2.11:各模板的边缘应倒角3×45°安装表面光洁平整不应有的螺钉,销钉,毛刺,和磕碰伤等痕迹.螺钉凹下部分应封堵.2.12:模具厚度符合压铸机设计要求,定模应大于80㎜以上,动模100㎜以上. 2.13:所有滑动及动做部分要求,在正常压铸模温下正常工作,应灵活平稳,配合间隙良好.2.14:除特殊需要外,模具上不许有焊接.2.15:模具主装验收合格后分型面及动做部分应涂抹防锈油.浇口套应用干净棉丝封堵.3.模具绘图:3.1:模具图纸设计后应需要客户确定后生产.3.2三维及二维模具设计图纸需经研讨,确认,批准后进行投入生产.主要内容如下:模具结构设计确认:浇排系统,顶出机构,冷却水位置,滑块等.设计图纸及尺寸确认:压铸机和模具相关性确认.模具制造计划安排确认.提出修改工作计划,修正书等.模具各接口规格.客户标准及要求确认.客户向我提供的企业标识的制作及位置和尺寸确认.4.模具材料:4.1:对客户要供应商提供材料化学分析报告,热处理,表面处理等相关检查报告及相关文件。
压铸模具标准

压铸模具标准压铸模具是用于生产金属零件的重要工具,其质量和精度直接影响着产品的质量和成本。
因此,制定和遵循严格的压铸模具标准对于保证产品质量、提高生产效率至关重要。
首先,压铸模具的材料选择是至关重要的。
优质的模具材料应具有高强度、高硬度、良好的热稳定性和热疲劳抗性。
常见的模具材料有工具钢、热作模具钢、硬质合金等。
在选择模具材料时,需要根据具体的压铸工艺和产品要求进行合理的选择,以确保模具的使用寿命和生产效率。
其次,压铸模具的设计和加工也是非常重要的环节。
模具的设计应充分考虑产品的结构特点和生产工艺要求,保证产品的成型精度和表面质量。
同时,在模具加工过程中,需要使用先进的加工设备和工艺,确保模具的精度和表面质量。
此外,还需要对模具进行严格的热处理和表面处理,以提高模具的耐磨性和抗腐蚀性。
另外,模具的安装和调试也是影响产品质量的重要环节。
在模具安装过程中,需要严格按照标准操作流程进行,确保模具的定位和装配精度。
在模具调试阶段,需要根据具体的压铸工艺和产品要求进行合理的调整,以保证产品的成型精度和表面质量。
最后,对于压铸模具的管理和维护也是至关重要的。
模具在使用过程中,需要定期进行检查和维护,及时发现和排除模具的问题,延长模具的使用寿命。
同时,还需要建立完善的模具管理制度,对模具的使用、维护和更换进行规范管理,以提高模具的利用率和生产效率。
总之,严格遵循压铸模具标准,从模具材料选择、设计加工、安装调试到管理维护,都是保证产品质量和提高生产效率的关键。
只有不断提高模具的质量和精度,才能更好地满足市场需求,提升企业竞争力。
压铸模检验标准

驗收項目 驗收內容
模具外觀&結構& 模具外觀& 結構& 材質
模具標示 一.模具外 觀 模具表面 尺寸 尺寸 ( 重量 重量 ( 模具壽命 模仁硬度 二.模具材質 滑塊 模胚 模仁材质 1.中心机嘴 三.模具型式 2.机嘴偏心 1.1穴 四.模穴 2.2穴 3.4穴 4.其它 1.自動 五.生產方式 2.半自動 3.手動 1.顶针 六.頂出系統 2.顶出系统回位 3.頂針间隙 1.根据客户要求. 2.产量满足生产需求. 3.产品结构复杂程度. 1.產品需自動脫料,不可粘模,機械手夾取方便. 2.能自動生產進行 1.每块模板TOP面打上模号,AB板上还需加上产品名称 1.模具表面無嚴重撞傷,凹陷,變形,鏽跡 )mm )KG 八.冷卻系統 1.冷卻要求 2.水道间距尺寸 3.连接方式
H13类热作钢(2344,8407,SKD61),不允许有补焊情况. 1.满足产品质量要求。 2.符合相应压铸机参数要求。
成型產品
1.尺寸(FAI/CPK) 一.產品結構 2.后加工结构 3.产品边角 1.冷紋或波纹 2.邊緣毛邊片 3.裂痕 4.氣孔或缩孔 抛光后FAIpassed& CPK>1.67 模具上不做的后加工结构开模前须知会 产品上不要有利角,尽量满足凸起部分R1,凹 下部分R2 符合客戶允收標準或抛光后没有 便于打磨加工 不允許或抛光后没有 不允許 不允許,抛光后没有且满足强度要求 不允許,模具需定期进行去积碳处理 不允許 不允許 产品上小于直径2.5的细长孔模具上如不加工, 而采用后机械加工方式,需先经SQCC确定,且 模具上需加工定位孔 分型面上尽量不要有凹坑,框/孔边不要做倒 角,AB板间隙做到0.1MM
4.牙型如没另行要求则做PT牙
压铸模具标准
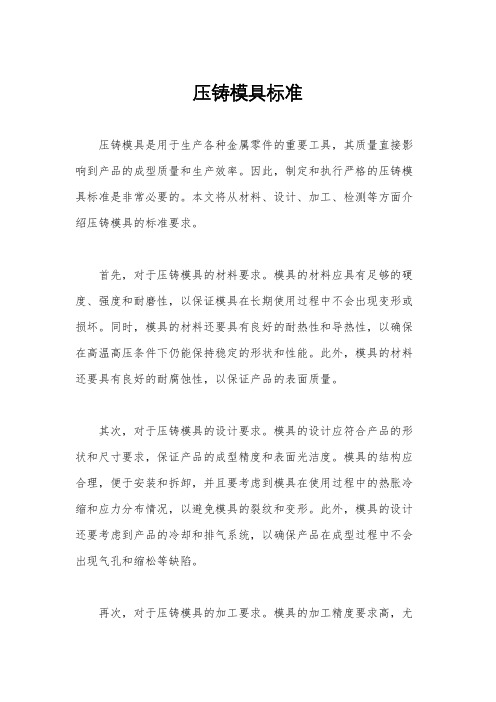
压铸模具标准压铸模具是用于生产各种金属零件的重要工具,其质量直接影响到产品的成型质量和生产效率。
因此,制定和执行严格的压铸模具标准是非常必要的。
本文将从材料、设计、加工、检测等方面介绍压铸模具的标准要求。
首先,对于压铸模具的材料要求。
模具的材料应具有足够的硬度、强度和耐磨性,以保证模具在长期使用过程中不会出现变形或损坏。
同时,模具的材料还要具有良好的耐热性和导热性,以确保在高温高压条件下仍能保持稳定的形状和性能。
此外,模具的材料还要具有良好的耐腐蚀性,以保证产品的表面质量。
其次,对于压铸模具的设计要求。
模具的设计应符合产品的形状和尺寸要求,保证产品的成型精度和表面光洁度。
模具的结构应合理,便于安装和拆卸,并且要考虑到模具在使用过程中的热胀冷缩和应力分布情况,以避免模具的裂纹和变形。
此外,模具的设计还要考虑到产品的冷却和排气系统,以确保产品在成型过程中不会出现气孔和缩松等缺陷。
再次,对于压铸模具的加工要求。
模具的加工精度要求高,尤其是对于模具的芯部和腔部,其加工精度和表面粗糙度都会直接影响到产品的质量。
因此,模具的加工过程需要采用先进的加工设备和工艺,以保证模具的尺寸和形状精度。
同时,模具的表面还需要进行表面处理,以提高其耐磨性和耐腐蚀性。
最后,对于压铸模具的检测要求。
模具在使用过程中需要进行定期的检测和维护,以确保其性能和精度。
模具的检测主要包括外观检查、尺寸检测、材料分析和磨损分析等内容,以发现模具的损坏和磨损情况,并及时进行修复和更换。
总之,严格执行压铸模具标准对于保证产品质量、提高生产效率和降低生产成本具有重要意义。
只有在材料、设计、加工和检测等方面都符合标准要求,才能保证模具在长期使用过程中保持稳定的性能和精度。
因此,压铸模具的标准化工作还需要在各个环节上加强,以逐步提高国内压铸模具的质量水平。
NADCA北美压铸标准

壓鑄公司的首家學會是北美壓鑄學會(NADCA).北美壓鑄學會是一個國際技朮和教育組織, 成員大部分來自美洲從事壓鑄件生產的公司, 也有來自其他洲的成員. 在壓鑄工藝和科學方面, 在金屬的表面處理方面和同類工藝方面壓鑄學會致力于改善和知識的傳播.壓鑄學會的初始目標是提高團体的壓鑄知識, 培訓教育課程, 鼓勵新產品的研究, 通過教育和研究促進壓鑄工業的發展和成長.NADCA(以前為SDCE)于1955年在密執安州法律的指導下作為一個非贏利組織組成學會. 現在在美國、加拿大和拉丁美洲已有24家分會. 由于對NADCA的活動感興趣, 其他的分會仍在組織之中.(4) 壓鑄工業(THE DIE CASTING INDUSTRY)在北美有350多家壓鑄廠商, 很多壓鑄廠商都是專業生產壓鑄件的獨立公司. 這些公司通過計件竟標獲得業務. 這些“習慣”上稱為壓鑄厂的規模小到只有三、四台小型壓鑄机, 大到具有許多大型壓鑄机厂的股份公司.有些壓鑄公司已開發了具有專利的生產線使他們的生產能力大大提高. 如果一旦成為壓鑄公司, 或者確定生產, 那么就包含在壓鑄之中. 因為這是生產他們產品的最佳途徑. 當一個公司內有壓鑄廠支持其活動時, 壓鑄操作就認為是“鑄造”操作. 在北美大約一半的壓鑄厂都屬于這种范疇.汽車、小發動机、船舶外裝產品和建筑商五金工業都有大型的壓鑄設施. 有些厂具有100多台壓鑄机, 其合模力可達32MN(3.500吨). 同樣, 大部分小功率電子感應電動机的制造厂商也具有壓鑄設施.很多其他金屬生產公司也有壓鑄厂, 它們又有一台小型壓鑄机從事大量的制造, 与此同時這些公司實質上也可以專門從事壓鑄制造了.因為壓鑄操作要求專門的工程技朮且培訓從事設備維修人員要求高, 所以壓鑄厂通常最經濟的作法是至少要有12台中等大小的壓鑄机. 壓鑄机的數量太少已証明是得不到技朮人員和設施合理支持的. 如果壓鑄操作僅限于合模力小于10MN(100ton3)的壓鑄机, 那么經濟狀況就不一樣了, 經濟的作法是統一大小, 數量為三到四台壓鑄机.(5) 開發歷史(HISTORICALDEVELOPMENT)在1849年, 斯特吉斯(Sturgiss)介紹了和壓鑄相似的工藝, 并利用名為“鉛壺”(圖示1)的机器生印刷業中的鉛字而獲專利首次知曉壓鑄是在1868年, 一個英國發明家查爾斯‧波伯哥(Charls Babbage)開發出了壓力壓鑄工藝, 給當圖示1-1. 這是由斯特吉斯(Sturgiss)于1849年獲得專利的“鉛壺”. 早期這种壓鑄机把鉛鑄造成型.今計算机先驅 “机械計算机”生產精密的零部件, 這些零件中有一件非常薄, 直徑為6.5英寸, 有80齒的齒輪. 在1877年, 一台手工操作的壓鑄机由都森波利(Disenbery)在美國制造出來, 生產机車頭軸承殼(圖示1-2).批量生產產品的需求隨著消費品市場的需求在增長, 如愛迪生電報机, 電報机的零部件早在1892年就開始壓鑄,与此同時, 像現金出納机這樣的業務机器又為壓鑄開辟了新的市場. 壓鑄工藝的成長和技朮開發大約從1904年開始,H ‧H 富蘭克林公司開始給汽車工業生產連杆軸承. 主要的開發是在1922年,新澤西的鋅公司把鋅合金引入壓鑄業中才清除了早期出現的問題.鋁合金首次鑄造大約是在1914年,使用空氣壓力把熔化金屬壓入模中(圖示1-3). 鋁合金的熔點高且和鐵反應,使這種金屬的廣泛應用一直推遲至二十世紀三直年代初 “冷室”工藝開發出來.這种工藝減少了鋁和机器的鐵成分接觸的時間, 從而大大減少了鋁和鐵反應的机會.我們現在知道, 二十世紀三十年代做出的很多開發部是現代壓鑄工業開始的年代. 這些開發是: (1)首次黃銅壓鑄; (2)高純度鋅的利用; (3)自動壓鑄机出現;(4)商用壓鑄机的大小和复雜化程度潛在增長; (5)二氧化硫配比裝置的開發使鎂的壓鑄成為可能.壓鑄工業增長速度最快的時候是在二十世紀五十年代和二十世紀六十年代初. 汽車工業和應用工業需要零件數量最多的部分是壓鑄. 認真研究程序, 目的在于找到使過程更有效、更具竟爭的方法. 在二十世紀七十年代把工業帶進一個复雜化的時代。
压铸模具标准
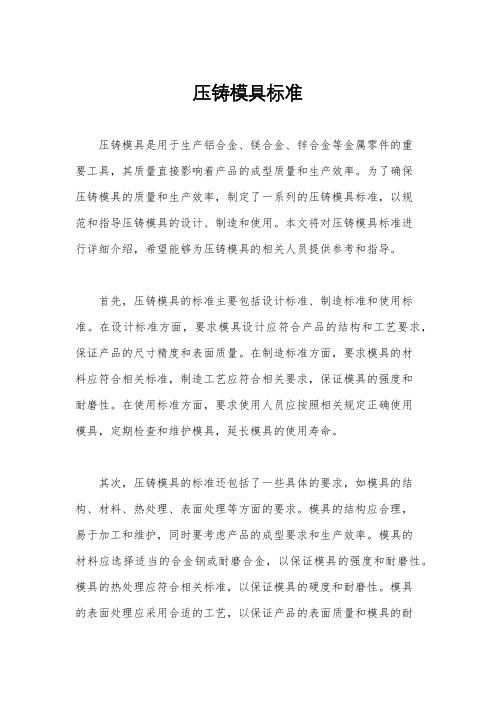
压铸模具标准压铸模具是用于生产铝合金、镁合金、锌合金等金属零件的重要工具,其质量直接影响着产品的成型质量和生产效率。
为了确保压铸模具的质量和生产效率,制定了一系列的压铸模具标准,以规范和指导压铸模具的设计、制造和使用。
本文将对压铸模具标准进行详细介绍,希望能够为压铸模具的相关人员提供参考和指导。
首先,压铸模具的标准主要包括设计标准、制造标准和使用标准。
在设计标准方面,要求模具设计应符合产品的结构和工艺要求,保证产品的尺寸精度和表面质量。
在制造标准方面,要求模具的材料应符合相关标准,制造工艺应符合相关要求,保证模具的强度和耐磨性。
在使用标准方面,要求使用人员应按照相关规定正确使用模具,定期检查和维护模具,延长模具的使用寿命。
其次,压铸模具的标准还包括了一些具体的要求,如模具的结构、材料、热处理、表面处理等方面的要求。
模具的结构应合理,易于加工和维护,同时要考虑产品的成型要求和生产效率。
模具的材料应选择适当的合金钢或耐磨合金,以保证模具的强度和耐磨性。
模具的热处理应符合相关标准,以保证模具的硬度和耐磨性。
模具的表面处理应采用合适的工艺,以保证产品的表面质量和模具的耐蚀性。
最后,压铸模具的标准还包括了一些检验和测试的要求,如模具的出厂检验、使用前检验、定期检验等。
模具的出厂检验应包括模具的尺寸检验、材料检验、热处理检验等,以保证模具的质量。
使用前检验应包括模具的装配检验、润滑检验、保养检验等,以保证模具的正常使用。
定期检验应包括模具的尺寸检验、磨损检验、裂纹检验等,以保证模具的使用寿命。
总之,压铸模具标准是保证压铸模具质量和生产效率的重要依据,对压铸模具的设计、制造和使用都有着重要的指导作用。
压铸模具的相关人员应严格按照相关标准执行,以保证产品质量和生产效率,推动压铸模具行业的健康发展。
希望本文所介绍的压铸模具标准能够为相关人员提供参考和指导,推动我国压铸模具行业的发展。
压铸模具制造标准

压铸模具制造标准为规范模具制造,保证模具质量,特制定此标准一、总体要求:1、所有零件按二维图纸尺寸、技术要求制作,检验依据二维图纸2、 CNC加工采用按3D编程,相关公差按二维图要求制作3、组立组要按总装图要求组合模具及配模4、发现二维图纸少尺寸、3D与2D不符、制作中出错、安装干涉等情况,及时上报质量组和设计组,由设计组及时做出解决方案,并下发新资料。
质量组确认后,有新资料时电脑上错误资料第一时删除。
5、所有零件热处理按图纸要求操作、6、所有零件表面处理按图纸要求操作7、所有零件上机加工分中、打表规定,打表要求打长面复查短面,分中要求在毎面中心分中(中心误差超10mm),同时用量具复查尺寸。
二、模芯、滑块1、材材为H13或DIEVR2、模芯应图纸硬度要求,要淬火处理。
淬火会造成变形及材料内部硬度达到要求,制作工艺路线为粗加工、淬火、精加工、去应力回火(高温腐蚀会造成应力),才能达图纸3、开粗前外形保证六面垂直度0.1mm、平行度0.02mm以内,4、外形淬火前放精加工余量,外形按最长面来计算,规定如下:长度宽度300mm以内长宽均放1mm,厚放1.2MM。
300~500mm长宽均放1~1.5mm,厚放1.5MM。
500~800mm长宽均放1.5~2mm,厚放2MM。
800mm以上长宽均放2~2.5mm,厚放2.5MM。
5、CNC编程按图编制合理精粗程序,保证质量同时缩短加工时间,减少不必要空刀(采用分段加工)。
CNC操机员按程序参数全部开到100%,不得改度参数,有问题向编程员反映。
6、CNC开粗留单边留1~1.5mm,厚1.5~2MM的淬火后精加工余量,注意不能产生内清角(最小不得小于R2),与外形贯通的槽深不足30mm,宽不足60的不做保护措施,超过时要求两侧底角最小为R15或口部连筋,具体分析后确认。
反面倒角C7,4个R角、分流锥(留有效高度30mm)、料筒等反面台阶处辟空淬火前加工到位。
- 1、下载文档前请自行甄别文档内容的完整性,平台不提供额外的编辑、内容补充、找答案等附加服务。
- 2、"仅部分预览"的文档,不可在线预览部分如存在完整性等问题,可反馈申请退款(可完整预览的文档不适用该条件!)。
- 3、如文档侵犯您的权益,请联系客服反馈,我们会尽快为您处理(人工客服工作时间:9:00-18:30)。
压铸标准一、总体要求………………………………………………P3二、设计制造流程…………………………………………P5三、模芯……………………………………………………P6四、模架...………………………………………………P6五、滑块……………………………………………………P7六、型芯…………………………………………………P10七、顶出……………………………………………………P10八、冷却……………………………………………………P12九、浇注和分型面…………………………………P12十、模具检查表……………………………………………P14十一、压铸模具各部分名称………………………………P15 十二、模具备料与外购放余量的规范……………………P15十三、铸造公差表…………………………………………P17这些在于给压铸模具设计者和制造者在模具设计和制造的过程中提供满足压铸的要求而必须控制的项目,有利于减少设计失误、提高模具制造的质量和效率。
在设计和制造的过程中任何有与本不符的项目必须得到技术主管或制造主管的同意。
本应随技术的不断改进、制造工艺的提高定期更新。
并注明版本号。
的常规模具报价以此为基础,特殊情况另外注明。
一、总体要求:1、如采用H13电渣重熔钢材料必须按认可的上钢五厂的牌号供应,如采用其他的厂商或品牌,需得到的书面许可。
进口模芯材料需专营商供应。
2、按的压机尺寸设计外形,防止干涉。
(125T~1600T)(压机尺寸表正在编写过程中)或另见表单中。
3、吊装孔至少为M30深60的,顶部至少2个,大型模具动定模架上要各2个,需设于模具的重心上(每半模),以利于吊装时的安全。
4、动定模上方距分型线8处设计宽15深5的脱模剂残液排出槽一直延伸到模架边缘。
(除5、模具压夹槽,最小30×30(400T以下),40×40(400T以上),到型板高最小25(400T以下),40(400T以上)。
6、跨距大于150时都应考虑加支撑柱。
支撑柱直径(或宽)不小于75,尽可能靠近压射变形位。
7、减小变形,动模架支撑模芯的厚度至少为悬空位宽度的三分之一(大于50)。
8、安装防止飞水挡水板,一般设于前、后、上三侧。
9、分流锥和浇口套按的设计,400T以下为化浇口套,400T以上为整体压室。
下图为400T以下压铸机化浇口套:下图为500T以上压铸机化整体压室:二、压铸模设计制造流程:1、产品分析:对客户提供的产品图纸或样品进行分析,确认如下项目:A、精度等级、加工装配基准。
B、加工余量、分型位置、顶出位置、浇口位置等客户是否认可。
2、模具设计:2D模具结构设计和3D造型分模同时进行。
3、模具制造:按的模具制造实施。
4、设计制造流程图造型设计技术加工电极制作技术研磨技术检查评价铸造工艺电极设计技术技术技术刀具电火花加工技术焊接技术技术设计技术工艺设计技术相关技术线切割技术装配调整技术钻床机加工中心线切割焊机测量仪管理技术(日程管理、品质管理)三、模芯:1、用上钢五厂H13电渣重熔钢材料或进口8407、W302、2344等材料。
2、模芯尺寸以5进制控制长、宽、高尺寸,尾数只能出现5或0的数据。
3、加工后热处理前做去应力处理。
真空淬火热处理硬度800吨及以上模具为44-46,800吨以下模具为46-48。
精加工后按模具工艺之具体规定再做去应力处理,表面是否做软氮化处理根据的要求决定。
4、省模和抛光按客户的要求粗糙度和出模方向执行。
5、最小圆角R0.5,最小拔模斜度1.5°~2°。
6、多腔模模芯可以分为两块制造,制造配合间隙在0.1以内。
7、除非客户不同意,动模型腔部位或顶针上都应设置日期销,圆形日期销或方形日期销设计在模芯指定位置,按3年有效期设置。
其格式如下图所示:圆形日期标方形日期标8、多腔模必须设计型腔号,型腔号按W1 、W2 设置。
设计时在型腔上表示出来。
压铸材料除12外在分流锥上表示出来。
9、模芯的厚度至少大于型腔深度的一倍以上。
除非设计主管批准。
10、模芯的紧固螺钉400T以下机用M12,400T以上机用M16。
四、模架:1、模架材料为50#钢(或球墨铸铁)。
调质热处理硬度28~35。
2、模架入厂必检项目如下图:动模架动模定模定模架3、精框根部R3,与之相配的模芯则倒角5×45°。
4、除非与压铸机大杆干涉,模架四周倒角统一为10×45°。
五、滑块1、滑块芯材料采用H13电渣重熔钢或指定的热作模具钢材料,滑块座材料采用P20或45#钢,如果浇道从滑块座进入,则滑块座也采用H13电渣重熔钢或热作模具钢材料。
2、尽量采用油缸抽芯,如果抽芯距离小于20或滑块投影面积较小可采用斜杆抽芯。
3、抽芯油缸采用压铸模油缸(如下图所示)。
油封必须指定。
4、楔紧块用T8或45#钢,热处理硬度48-52,与滑块的整个宽度贴合,到模架的边缘至少40,用螺钉连接在模架上。
(参阅下图)抽芯与模芯的楔合长度至少50,单边斜度5°。
5、抽芯距离需避开顶针的干涉,选用的油缸必须满足前进和后退的整个距离,防止发生机械故障。
6、桥式连接的油缸与滑块座用半圆活块连接,钻M16的吊装螺钉孔。
7、油缸上的行程开关的使用需由指定,安装后不能和压铸机大杠发生干涉,其位置调节好后要能保持固定。
8、设计时考虑滑块上的抽芯要作到不拆卸桥式连接的油缸就可以取下,抽芯与滑块座的连910、必须设置轨道使滑块在其上滑动,轨道材料为45#钢,热处理48~52,嵌合在模架上,用螺钉锁紧。
滑块座与导轨磨擦面需表面淬硬。
六、型芯1、用H13型芯或61顶针做型芯。
2、型芯的定位不采用简易的螺钉锁紧,该方法仅用于不重要的小型芯上。
轴向浮动在0.02以内。
3、型芯根部R0.5。
4、形成通孔的型芯碰穿面让开0.25,以免合模时压伤。
5、表面是否做软氮化处理由工程部决定。
6、拔模斜度单边0.5度,图纸许可时可以大一些。
7、其他考虑:(在设计评审时研讨) 1)小于ø4,5的孔不铸造出来,可设置引针孔用加工的方法钻出。
除非长度小于直径便可铸出。
2)动模的型芯是否容易顶出。
3)型芯和滑块是否可以安装冷却水。
4)避免型芯在浇口处被冲刷。
七、顶出1、顶出板后限位不能和压铸机的顶出杆发生干涉。
2、通常500T以下压铸机顶出板托板的厚度35,保持板厚度25,500T以上压铸机顶出板托板的厚度50,保持板厚度30。
3、顶出板拉回装置按下图做。
顶出距离小于30或简易的模具也可以不设置拉回装置。
4、顶出板应足够大,可连接压铸机的四个顶出杆,具体参见压铸机动型板孔系图。
5、顶针的大小:尽可能大一点,最小选ø5ø5 & ø6 如果不是很短,采用阶梯顶针用61的顶针,如:ø5, ø6, ø8, ø10, ø12, ø16, ø20, ø25.6、顶出距离:顶出铸件离开最高点至少6。
除非单独要求。
对薄壁件,顶针尽量不要布在面上,最好布在筋上。
7、型腔上顶针孔直径12 以下的孔,间隙为0,025/0,05直径12 以上的孔,间隙为0,05/0,075配合段25/30孔间的模具钢壁厚至少4,尽可能10。
重要点:顶针孔和顶出板必须保持垂直,复杂和精度高的模具顶出板要设置导柱和导套,顶针和顶针孔保持在一条直线上,型腔热处理后采用线切割加工顶针孔。
顶针不能与顶针孔的避空位接触。
8、顶出板用M12的螺钉紧固,间隔距离不大于150。
9、顶出板向前运动时不能损坏模具和冷却水管。
10、对安装的顶针进行编号。
八、冷却1、尺寸:1)直通冷却:用ø10的水冷通道,¼” 的锥管螺纹连接。
2)点式冷却:点冷采用专用点式冷却管。
2、冷却水进出口采用集中汇流,要避开连接螺钉、顶针,统一连接到模具上方的汇流排。
如附图模架3、冷却水到型腔的距离,到型腔和复杂的滑块表面以及浇道为:22,到顶针孔、螺钉孔的距离可以为8,距离型腔转弯或尖角处必须大于40。
4、型芯冷却,尽可能的采用,根据型芯的大小和距浇道的位置决定。
5、冷却图纸,用A4图纸随模具完工后一起下发。
6、冷却通道的标识,模具上需清楚标明,如:1 1 , 5 5九、浇注和分型面1、这很重要,在设计开始必须做两种以上的方案,由技术主管召集压铸工艺、机械加工工艺、模具制造工艺等相关工程师进行设计评审。
2、浇注方案必须有相应的铸造条件表。
3、除12材料外,其他的压铸材料必须在横浇道上刻出合金材料的名称,字高2,如:24, 2等。
4、横浇道的形状:如下图所示其中400T以下压铸机W取20~405、浇道上必须有圆角,不能有尖角,按的做。
6、溢流槽的设计按下图进行7、分流锥和浇口套的设计选用的浇口套设计分流锥。
8、分型面按最大投影面作为分型面的原则选取,顶针位置和浇口位置的选择最好取得客户的认可。
十、模具检查表冷却水汇流排(冷卻水集中パイプ)十一、压铸模各部分的名称十二、模具备料规范。
为了备料的统一,以免增加不必要的加工余量,按下述规范备料:1、模芯料:工程部备料时,模芯料长宽方向备净尺寸,高度方向留2mm余量。
营销部接到工程部备料单后,1)若是进口8407料则长宽高方向总尺寸再放0.6余量;2)若是进口白皮料(如:2344)长宽高方向总尺寸再放1mm余量;3)若是其它锻打黑皮料,长宽高方向总尺寸再放3~5余量。
2、铜公料工程部下铜公料长宽高方向为净尺寸,但净尺寸必须把夹位也考虑进去,一般单边加15mm。
营销部接到铜公料单后,1)若是进口优质铜公,则长宽高方向总尺寸再放1~2mm余量;2)若是其它铜公料,则长宽高方向总尺寸再放2~3mm余量。
3、45#钢及其它普钢料工程部下45#钢及其它普通钢料,长宽高方向为净尺寸,营销部接到45#钢及其它普通钢料单后,则长宽高方向总尺寸再放5~6mm.十三、铸造公差:8062(一般公差已在图纸右上角注明): A 20 a 5 20 ±0.21。
(例如:20为基本尺寸,它的5级的一般公差为20 ±0.21。
)。