DKBA04500040-C钣金冲压件质量要求
企业精品资料:钣金件质量检验技术要求(图文并茂)

目录1.技术要求 (4)1.1.外观及表面状态一般要求 (4)1.1.1.零件的毛刺面朝向要求 (4)1.1.2.冲裁类平板零件圆角要求 (4)1.1.3.零件上止裂孔、工艺槽要求 (5)1.1.4.弯曲零件未注圆角R要求 (5)1.1.5.翻边攻丝质量要求 (5)1.1.6.自铆质量要求 (7)1.1.7.零件表面的外观要求 (8)1.2.钣金冲压件毛刺的要求 (8)1.2.1.毛刺的高度定义 (8)1.2.2.结构件的毛刺区域分类 (8)1.2.3.钣金冲压件毛刺质量要求 (12)1.2.4.钣金冲压件的熔渣要求 (13)1.2.5.钣金冲压件的接刀痕的要求 (13)1.3.钣金冲压件公差要求 (13)1.3.1.公差要求 (13)1.3.2.钣金件冲压公差等级代号及数值 (14)1.3.3.其它说明 (18)2.检验规则 (19)2.1.检验类别 (19)2.1.1.一般检验 (19)2.1.2.补充检验 (19)2.2.检验原则 (19)2.3.检验规定 (19)图目录图 1 折弯件毛刺方向示意图 (4)图 2 平板件的尖角示意图 (4)图 3 止裂孔直径示意图 (5)图 4 工艺槽口示意图 (5)图 5 翻边攻丝示意图 (6)图 6 薄板连接用带锥台翻边攻丝孔结构示意图 (6)图 7 自铆连接示意图 (7)图 8 钣金件毛刺示意图 (8)图 9 户外机柜类A、B类区域判断示意图 (10)图 10 室内机柜类A、B类区域判断示意图 (11)图 11 插箱类A、B类区域判断示意图 (11)图 12 拉手条及面板等小五金类A、B类区域判断示意图 (12)图 13 盒式类A、B类区域判断示意图 (12)图 14 倒角高度示意图 (13)表目录表 1 平板件圆角半径r值 (4)表 2 普通翻边高度H值和螺纹最少反复打入次数 (6)表 3 薄板连接用带锥台翻边攻丝孔翻边高度H值和螺纹最少反复打入次数 (6)表 4 自铆参数表 (7)表 5 自铆连接点最小承力表 (7)表 6 毛刺高度的极限值 (12)表 7 钣金公差数值表 (14)错误!未找到引用源。
五金冲压件技术要求标准
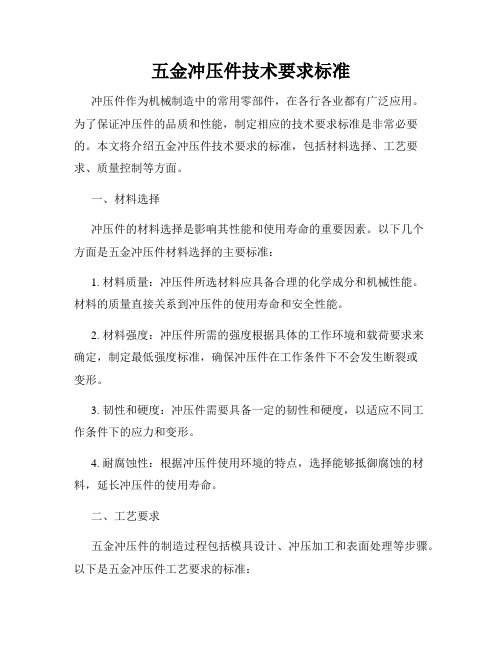
五金冲压件技术要求标准冲压件作为机械制造中的常用零部件,在各行各业都有广泛应用。
为了保证冲压件的品质和性能,制定相应的技术要求标准是非常必要的。
本文将介绍五金冲压件技术要求的标准,包括材料选择、工艺要求、质量控制等方面。
一、材料选择冲压件的材料选择是影响其性能和使用寿命的重要因素。
以下几个方面是五金冲压件材料选择的主要标准:1. 材料质量:冲压件所选材料应具备合理的化学成分和机械性能。
材料的质量直接关系到冲压件的使用寿命和安全性能。
2. 材料强度:冲压件所需的强度根据具体的工作环境和载荷要求来确定,制定最低强度标准,确保冲压件在工作条件下不会发生断裂或变形。
3. 韧性和硬度:冲压件需要具备一定的韧性和硬度,以适应不同工作条件下的应力和变形。
4. 耐腐蚀性:根据冲压件使用环境的特点,选择能够抵御腐蚀的材料,延长冲压件的使用寿命。
二、工艺要求五金冲压件的制造过程包括模具设计、冲压加工和表面处理等步骤。
以下是五金冲压件工艺要求的标准:1. 模具设计:在冲压件制造过程中,模具设计起到至关重要的作用。
模具设计应确保冲压件的精度和表面质量,减少废品率和生产成本。
2. 冲压加工:冲压加工要保证加工过程中冲片的精度和一致性。
加工过程中需要注意工艺参数的控制,避免冲压件的变形和损坏。
3. 表面处理:根据冲压件的用途和客户要求,选择合适的表面处理方法。
表面处理包括镀锌、喷漆、电镀等,旨在提高冲压件的耐腐蚀性和外观质量。
三、质量控制五金冲压件的质量控制是确保其性能和可靠性的关键环节。
以下是五金冲压件质量控制的标准:1. 材料检测:对冲压件所需材料进行磁粉检测、拉伸测试等,确保材料质量达到要求。
2. 产品检测:对冲压件进行外观质量检验、尺寸检测等,确保产品的准确度和一致性。
3. 产品性能测试:根据冲压件的使用要求,进行强度、韧性、硬度等性能测试,确保产品能够承受相应的工作条件。
4. 质量管理:建立和执行严格的质量管理体系,包括产品追溯、异常处理和质量持续改进等,以确保冲压件的质量稳定和可控。
钣金质量检验标准
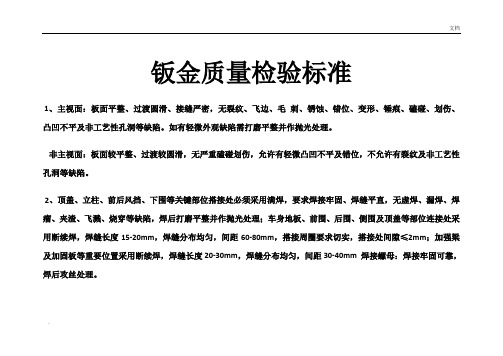
钣金质量检验标准
1、主视面:板面平整、过渡圆滑、接缝严密,无裂纹、飞边、毛刺、锈蚀、错位、变形、锤痕、磕碰、划伤、凸凹不平及非工艺性孔洞等缺陷。
如有轻微外观缺陷需打磨平整并作抛光处理。
非主视面:板面较平整、过渡较圆滑,无严重磕碰划伤,允许有轻微凸凹不平及错位,不允许有裂纹及非工艺性孔洞等缺陷。
2、顶盖、立柱、前后风挡、下围等关键部位搭接处必须采用满焊,要求焊接牢固、焊缝平直,无虚焊、漏焊、焊瘤、夹渣、飞溅、烧穿等缺陷,焊后打磨平整并作抛光处理;车身地板、前围、后围、侧围及顶盖等部位连接处采用断续焊,焊缝长度15-20mm,焊缝分布均匀,间距60-80mm,搭接周圈要求切实,搭接处间隙≤2mm;加强梁及加固板等重要位置采用断续焊,焊缝长度20-30mm,焊缝分布均匀,间距30-40mm 焊接螺母:焊接牢固可靠,焊后攻丝处理。
.
3、车门:铰链安装牢固、转动灵活,车门启闭可靠,无干涉、卡滞及异响现象,车门闭合后周边间隙均匀,车门密封间隙15±2mm。
4、前风窗:弧度与封样玻璃吻合良好,周边间隙均匀一致(5~6mm),风窗对角线偏差≤3mm。
5、轮罩:以轮轴中心线为基准,前后偏差不超过5mm,上下偏差不超过5mm,内外偏差不超过5mm。
6、灯框、门框、门洞周圈、前围周圈等能够影响外观质量的部位要打磨圆滑,不能影响刮腻子及后道工序的施工。
其他:风道宽度误差≤5mm,车身左右偏移≤7mm,左右高度偏差≤7mm。
7、车身无漏焊、漏件,材料厚度及其他装配尺寸严格按图纸要求执行
.。
钣金加工质量控制

钣金加工质量控制钣金加工质量控制是指在钣金加工过程中,通过一系列的控制措施和方法,确保钣金产品的加工质量符合预期要求。
钣金加工质量控制是钣金加工过程中非常重要的一环,能够有效提高产品的质量稳定性和生产效率,降低生产成本,提高客户满意度。
1. 设计和规范要求钣金加工质量控制的第一步是明确产品的设计和规范要求。
根据客户需求和产品特性,制定详细的设计和规范要求,包括产品尺寸、材料、表面处理、装配要求等。
设计和规范要求的明确性和准确性对于后续质量控制非常关键。
2. 原材料检验钣金加工的质量控制从原材料开始。
对于每批次的原材料,需要进行严格的检验,确保其符合设计和规范要求。
原材料检验的内容包括外观质量、尺寸精度、材料成分、力学性能等。
只有合格的原材料才能进入下一步的加工工序。
3. 加工工艺控制钣金加工的工艺控制是确保产品质量的关键环节。
在加工过程中,需要制定详细的工艺流程和操作规范,包括切割、冲压、折弯、焊接等工艺参数的控制。
钣金加工过程中的工艺控制包括设备的调试和维护、操作人员的培训和管理等方面。
4. 检测和测量钣金加工质量控制的另一个重要环节是检测和测量。
通过使用合适的检测设备和工具,对加工过程中的关键尺寸和质量特性进行检测和测量。
常用的检测方法包括三坐标测量、影像检测、硬度测试等。
通过检测和测量,及时发现和纠正加工中的问题,确保产品的质量稳定性。
5. 过程控制钣金加工质量控制需要对加工过程进行全面的控制。
通过建立和执行严格的过程控制措施,确保每个环节的加工质量符合要求。
过程控制包括设备的调试和维护、工艺参数的控制、操作规范的执行等。
通过过程控制,可以降低加工过程中的变异性,提高产品的一致性和稳定性。
6. 最终检验和出厂检验钣金加工质量控制的最后一步是最终检验和出厂检验。
在最终检验中,对钣金产品进行全面的检验,确保其质量符合设计和规范要求。
出厂检验则是对产品进行最后的确认,确保产品可以安全出厂。
最终检验和出厂检验的结果是决定产品是否合格的关键。
钣金件质量验收标准

钣焊件制作及验收标准一、依据标准1、依据中华人民共和国国家标准:GB/T706-2008《热轧型钢》。
2、依据中华人民共和国国家标准:GB/T709-2006《热轧钢板和钢带的尺寸、外形、重量及允许偏差》。
3、依据中华人民共和国国家标准:GB/T19804-2005《焊接结构的一般尺寸公差和行为公差》。
二、具体要求(一)钣金件焊前要求1、所有原材料不得低于国家标准的要求,否则不得下料制作。
2、要求焊接型钢不直度不超过2/1000,总弯曲度不大于总长度的0.3%。
3、钣金件焊接前,必须对钢板、型钢进行除锈或抛喷丸处理。
处理后若有不直、不平现象则必须校直、校平后再焊接。
4、特殊工件焊接后喷不到底漆的,喷丸校直、校平后应首先喷涂底漆。
5、在进行焊接前,应根据零件大小、材料厚度、焊缝要求的大小等不同选用粗细规格不等的焊条。
6、保证折弯部分圆滑,尤其是大圆弧。
保证外观美观,保证尺寸要求。
(二)焊接过程的要求1、按图纸、技术、工艺要求制作焊接,因看图纸有误,导致工件焊错,需重新焊割的,该件按次品处理。
2、焊接时,要求该坡口(根据设计或工艺需要,在焊件的待焊部位加工并装配成的一定几何形状的焊缝成形槽,K型坡口,V型坡口,U型坡口等,但大多要求保留一定的钝边。
)的地方必须坡口,加工周转件没有坡口的、或者焊接型材等,应根据情况用磨光机进行坡口。
需机加工坡口的应进行加工坡口处理。
3、焊接时应保证工件外形尺寸和形位公差,非加工面形位公差按IT15级执行,保证型钢、钢板对接时错位量不超过厚度的2%。
4、焊接时需要代料的,未经技术部门的书面同意,不能代料。
5、焊接时的焊缝严格按图纸要求,该连续焊的连续焊,该断续焊的一定要断续焊。
如图纸没有要求的断续焊尺寸长度,则每间隔150mm焊50mm。
点焊时各焊点距离必须均匀一致。
6、连续焊缝要求平直光滑,不能有明显的高低不平现象,不能有焊穿、焊偏、焊疤、气孔、咬边(咬边将减少母材的有效截面积、在咬边处可能引起应力集中、特别是低合金高强钢的焊接)等现象。
钣金冲压件质量要求

DKBA 华为技术有限公司内部技术规范DKBA0.450.0040 REV C钣金冲压件质量要求Specification For Sheet-metalPunching Part2012年07月30日发布 20012年09月1日实施华为技术有限公司Huawei Technologies Co., Ltd.版权所有侵权必究All rights reserved修订声明Revision declaration 本规范拟制与解释部门:整机工程部基础平台部本规范的相关系列规范或文件:无相关国际规范或文件一致性:无替代或作废的其它规范或文件:无相关规范或文件的相互关系:无目录1.技术要求 (7)1.1.外观及表面状态一般要求 (7)1.1.1.零件的毛刺面朝向要求 (7)1.1.2.冲裁类平板零件圆角要求 (7)1.1.3.零件上止裂孔、工艺槽要求 (7)1.1.4.弯曲零件未注圆角R要求 (8)1.1.5.翻边攻丝质量要求 (8)1.1.6.自铆质量要求 (10)1.1.7.零件表面的外观要求 (11)1.2.钣金冲压件毛刺的要求 (11)1.2.1.毛刺的高度定义 (11)1.2.2.结构件的毛刺区域分类 (11)1.2.3.钣金冲压件毛刺质量要求 (15)1.2.4.钣金冲压件的熔渣要求 (16)1.2.5.钣金冲压件的接刀痕的要求 (16)1.3.钣金冲压件公差要求 (16)1.3.1.公差要求 (16)1.3.2.钣金件冲压公差等级代号及数值 (17)1.3.3.其它说明 (21)2.检验规则 (22)2.1.检验类别 (22)2.1.1.一般检验 (22)2.1.2.补充检验 (22)2.2.检验原则 (22)2.3.检验规定 (22)图目录图 1 折弯件毛刺方向示意图 (7)图 2 平板件的尖角示意图 (7)图 3 止裂孔直径示意图 (8)图 4 工艺槽口示意图 (8)图 5 翻边攻丝示意图 (9)图 6 薄板连接用带锥台翻边攻丝孔结构示意图 (9)图 7 自铆连接示意图 (10)图 8 钣金件毛刺示意图 (11)图 9 户外机柜类A、B类区域判断示意图 (13)图 10 室内机柜类A、B类区域判断示意图 (14)图 11 插箱类A、B类区域判断示意图 (14)图 12 拉手条及面板等小五金类A、B类区域判断示意图 (15)图 13 盒式类A、B类区域判断示意图 (15)图 14 倒角高度示意图 (16)表目录表 1 平板件圆角半径r值 (7)表 2 普通翻边高度H值和螺纹最少反复打入次数 (9)表 3 薄板连接用带锥台翻边攻丝孔翻边高度H值和螺纹最少反复打入次数 (9)表 4 自铆参数表 (10)表 5 自铆连接点最小承力表 (10)表 6 毛刺高度的极限值 (15)表 7 钣金公差数值表 (17)钣金冲压件质量要求Specification For Sheet-metal Punching Part范围Scope:本规范规定了华为的钣金冲压件(表面处理前)的质量要求、检验规则。
钣金(五金)产品质量的控制
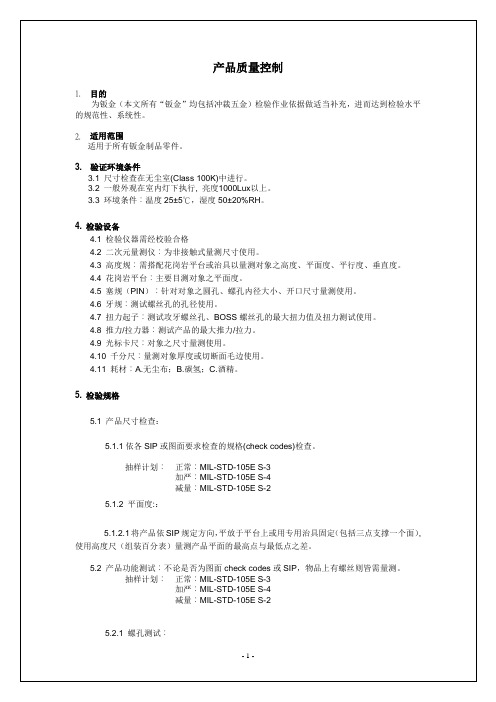
6.5.1尺寸:
用螺纹规检测螺孔。
6.5.2外观:
A.依照客户要求。
B.检查内容:漏攻牙、滑牙、攻错孔、攻偏(攻偏是否影响外观面)、漏工序等。
6.6铆轴检测内容
6.6.1尺寸:
依照图面标准/治具/客供样品。
6.6.2外观:
A.依照客户要求。
B.检查内容:轴歪、轴松、轴间隙、轴缺料、漏铆轴、漏工序等。
6.9打磨检测内容:
6.9.1尺寸:
依照图纸要求/治具/样品。
6.9.2外观:
A.依照样品客户要求/样品。
B.检查内容:脱焊、焊位偏、焊穿、漏焊、变形、压伤、打磨后平面度、角度、直线度、漏工序等。
6.10包装检测内容:
6.10.1尺寸:
特殊情况下,依照客户要求,按图面要求检验,或用治具全检。
6.10.2外观:
6.2数冲检测内容
6.2.1尺寸:
依照图面标准/治具/客供样品。
6.1.2外观:
A.依照客户要求。
B.检查内容:是否要求贴保护膜、压伤、划伤/擦伤、毛刺/毛边、变形、花料、刀痕、节点、模印、字印不清(与图纸要求/样板是否一致)、色差、凸凹痕、色拉凸起、斑点、漏工序等。
6.3冲压检测内容
6.3.1尺寸:
A.依照图纸要求/治具/样品。
B.检查内容:所有钣金(五金)外观缺陷。
19.轴间隙:轴铆接后根部有间隙。
20.轴松动:轴铆接后松动的现象。
21.色差:实际颜色与标准颜色有差异。
22.凸凹痕:表面异常凸起或凹陷。
23.薄膜残留:在电镀/烤漆前,或依据客户要求在包装前应撕除保护膜,而没有去除保护膜干净的不良。
24.针孔:电镀/烤漆表面出现的细小圆孔。
钣金加工质量控制
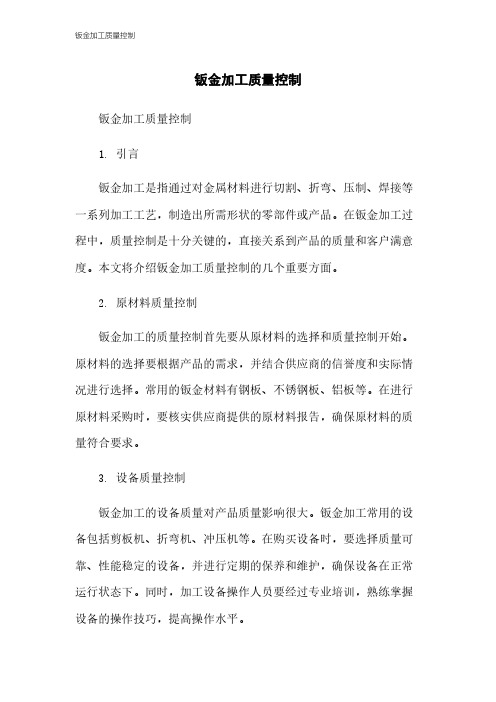
钣金加工质量控制钣金加工质量控制1. 引言钣金加工是指通过对金属材料进行切割、折弯、压制、焊接等一系列加工工艺,制造出所需形状的零部件或产品。
在钣金加工过程中,质量控制是十分关键的,直接关系到产品的质量和客户满意度。
本文将介绍钣金加工质量控制的几个重要方面。
2. 原材料质量控制钣金加工的质量控制首先要从原材料的选择和质量控制开始。
原材料的选择要根据产品的需求,并结合供应商的信誉度和实际情况进行选择。
常用的钣金材料有钢板、不锈钢板、铝板等。
在进行原材料采购时,要核实供应商提供的原材料报告,确保原材料的质量符合要求。
3. 设备质量控制钣金加工的设备质量对产品质量影响很大。
钣金加工常用的设备包括剪板机、折弯机、冲压机等。
在购买设备时,要选择质量可靠、性能稳定的设备,并进行定期的保养和维护,确保设备在正常运行状态下。
同时,加工设备操作人员要经过专业培训,熟练掌握设备的操作技巧,提高操作水平。
4. 工艺参数控制钣金加工的工艺参数对产品的质量有着重要影响。
常见的工艺参数包括切割速度、折弯角度、冲压压力等。
在加工过程中,要根据产品的要求,严格控制各项工艺参数,确保产品符合设计要求。
在设备调试和加工过程中,要进行工艺参数的检测和调整,及时发现并解决问题。
5. 加工过程控制钣金加工的每个环节都需要进行严格的控制,以确保产品的质量。
在切割过程中,要选择合适的刀具,控制切割速度和切割深度,避免切割产生毛刺。
在折弯过程中,要选择合适的模具,控制折弯角度和折弯力度,保证产品的平整度和精度。
在冲压过程中,要控制冲压力度和冲压次数,避免产生裂纹和变形等缺陷。
6. 检验和检测控制钣金加工的质量控制还包括产品的检验和检测。
常用的检验手段有目视检查、尺寸测量、外观检验等。
通过对产品进行检验和检测,可以及时发现和纠正问题,确保产品符合要求。
此外,还可以利用先进的非接触式测量仪器,如三坐标测量仪、光学测量仪等,提高测量的精度和效率。
7. 增强员工意识和培训质量控制还需要在企业内部进行员工意识的培养和提高。
- 1、下载文档前请自行甄别文档内容的完整性,平台不提供额外的编辑、内容补充、找答案等附加服务。
- 2、"仅部分预览"的文档,不可在线预览部分如存在完整性等问题,可反馈申请退款(可完整预览的文档不适用该条件!)。
- 3、如文档侵犯您的权益,请联系客服反馈,我们会尽快为您处理(人工客服工作时间:9:00-18:30)。
DKBA 华为技术有限公司内部技术规范DKBA0.450.0040 REV C钣金冲压件质量要求Specification For Sheet-metalPunching Part2012年07月30日发布 20012年09月1日实施华为技术有限公司Huawei Technologies Co., Ltd.版权所有侵权必究All rights reserved修订声明Revision declaration 本规范拟制与解释部门:整机工程部基础平台部本规范的相关系列规范或文件:无相关国际规范或文件一致性:无替代或作废的其它规范或文件:无相关规范或文件的相互关系:无规范号主要起草部门专家主要评审部门专家修订情况DKBA0.450.0040 REV C 基础平台部:潘建军(00118387)肖春秀(00053994) 整机工程部:郭天次(0014571)许志敏(00114402),黄涛(00121968)张实(00118600),钟宏辉(00121959),张润孝(00049797)MQE:陈亮(00068994)SQE:王进(00151357)1、增加了自铆质量要求;2、刷新了钣金件公差要求。
DKBA0.450.0040 REV B 质量成本管理部:肖春秀53994 整机工程部:周伟 00123276,郑玲 00119690李俊周 00123308,魏华 00102167杨曦晨 00152131,和永超57041MQE:曾松来00125372TQC:马宝兴39736CEG:郑连东 001149491、将外观表面的定义引用于DKBA0.400.00212、增加了翻边攻丝的质量要求;DKBA0.450.0040 REV1.0 质量成本管理部:肖春秀53994 质量成本管理部:盛辉21628、周伟16271结构平台开发部:郑玲15593MQE:陈军17658TQC:马宝兴39736新归档目录1.技术要求 (6)1.1.外观及表面状态一般要求 (6)1.1.1.零件的毛刺面朝向要求 (6)1.1.2.冲裁类平板零件圆角要求 (6)1.1.3.零件上止裂孔、工艺槽要求 (7)1.1.4.弯曲零件未注圆角R要求 (7)1.1.5.翻边攻丝质量要求 (8)1.1.6.自铆质量要求 (9)1.1.7.零件表面的外观要求 (10)1.2.钣金冲压件毛刺的要求 (10)1.2.1.毛刺的高度定义 (10)1.2.2.结构件的毛刺区域分类 (10)1.2.3.钣金冲压件毛刺质量要求 (14)1.2.4.钣金冲压件的熔渣要求 (15)1.2.5.钣金冲压件的接刀痕的要求 (15)1.3.钣金冲压件公差要求 (15)1.3.1.公差要求 (15)1.3.2.钣金件冲压公差等级代号及数值 (16)1.3.3.其它说明 (20)2.检验规则 (22)2.1.检验类别 (22)2.1.1.一般检验 (22)2.1.2.补充检验 (22)2.2.检验原则 (22)2.3.检验规定 (22)图目录图 1 折弯件毛刺方向示意图 (6)图 2 平板件的尖角示意图 (6)图 3 止裂孔直径示意图 (7)图 4 工艺槽口示意图 (7)图 5 翻边攻丝示意图 (8)图 6 薄板连接用带锥台翻边攻丝孔结构示意图 (8)图 7 自铆连接示意图 (9)图 8 钣金件毛刺示意图 (10)图 9 户外机柜类A、B类区域判断示意图 (12)图 10 室内机柜类A、B类区域判断示意图 (13)图 11 插箱类A、B类区域判断示意图 (13)图 12 拉手条及面板等小五金类A、B类区域判断示意图 (14)图 13 盒式类A、B类区域判断示意图 (14)图 14 倒角高度示意图 (15)表目录表 1 平板件圆角半径r值 (6)表 2 普通翻边高度H值和螺纹最少反复打入次数 (8)表 3 薄板连接用带锥台翻边攻丝孔翻边高度H值和螺纹最少反复打入次数 (9)表 4 自铆参数表 (9)表 5 自铆连接点最小承力表 (9)表 6 毛刺高度的极限值 (15)表 7 钣金公差数值表 (16)钣金冲压件质量要求Specification For Sheet-metal Punching Part范围Scope:本规范规定了华为的钣金冲压件(表面处理前)的质量要求、检验规则。
本规范适用于华为所有的钣金冲压件(表面处理前),设计图中有注明的要求以设计图为准,图中未注明的按此规范为准。
简介Brief introduction:规定了钣金冲压件(零件级)的质量要求及检验规则。
关键词Key words:外观、表面状态、工艺槽口、圆角半径、A类区域、B类区域、毛刺、毛刺高度华为技术文件优先级说明:华为产品生产执行的技术文件有:华为图纸、华为企业标准规范、通信设备行业标准、中国国家标准、国际标准。
这些标准的优先级别从高到低依次为:华为图纸--华为企业标准规范--通信设备行业标准--中国国家标准--国际标准。
如果各级文件之间有不一致的地方,应按最高级别的文件执行。
在华为企业标准规范中,产品专用标准优先于通用技术标准。
缩略语Abbreviations 英文全名 Full spelling 中文解释 Chinese explanationA类区域Class A Area 在钣金供应商交货时,产品在正常工作位置手能触膜到的边角区域;以及设计图中特别要求的部位。
B类区域Class B Area 不属于A类的区域都为B类区域毛刺Burr 指板料冲裁后留在冲裁件断面边缘锋利的凸起,毛刺高度Height Of Burr 指板料冲裁后留在冲裁件断面边缘锋利的凸起的高度毛刺面Surface of Burr 指边缘有毛刺的冲裁件平面。
对于落料,毛刺面是接触凸模的平面;对于冲孔,毛刺面是接触凹模的平面。
1级表面Class 1 Surface 重要外观表面,体现产品外观形象,具有装饰性,可以直接正视到的主要外观表面。
主要包括机柜、插框(包括一体化机箱和数通机箱)、无线射频模块、盒式结构、拉手条等的正面和正面上主要零部件的外表面、机柜前门开门后的正视面、高度小于、等于1.8米的机柜顶面(如Hert中机柜顶面)等。
2级表面Class 2 Surface 主要外表面,半装饰性的经常可见的外观表面。
主要包括机柜方孔条正面、机柜外部侧面、机柜后面、插框(包括缩略语Abbreviations 英文全名 Full spelling 中文解释 Chinese explanation一体化机箱和数通机箱)、无线射频模块的外部侧面和后面及防护网等处经常被打开的可视面等。
小五金件、机柜机箱附件等均定义为2级表面。
3级表面Class 3 Surface 次要外表面和内表面,不是以装饰为目的,表面质量要求不高的结构表面。
主要包括机柜、插框(包括一体化机箱和数通机箱)、无线射频模块、盒式结构、拉手条等的内表面和底面、高度大于1.8米的机柜顶面以及安装支架、绑线架、内部框架、内部焊件的所有表面等。
除1、2级表面外的表面均为3级表面。
1.技术要求1.1.外观及表面状态一般要求1.1.1.零件的毛刺面朝向要求毛刺面朝向零件里面,如图1:图 1 折弯件毛刺方向示意图特殊情况:按编码级分析零件之间的装配关系,零件的毛刺面应在里面或非功能面;如“L”型的零件为滑道,则毛刺面应在零件的外面,与上图相反。
1.1.2.冲裁类平板零件圆角要求图样上未注明的外形和内缘小于或等于90°的尖角处应制成圆角(见错误!未找到引用源。
),其圆角半径r按0规定。
图 2 平板件的尖角示意图表 1 平板件圆角半径r值材料厚度t ≤0.3 >0.3~0.5 >0.5~1 >1~2 >2~3 >3圆角半径r≤0.2 0.3 0.5 1 1.5 0.5t1.1.3.零件上止裂孔、工艺槽要求当设计文件或图样上注明允许开止裂孔或工艺槽口时,其止裂孔直径和工艺槽口尺寸,按下列要求选择:1、止裂孔直径d(见图3)不大于2t;图 3 止裂孔直径示意图2、工艺槽口尺寸L和b(见04);当t>0.5mm时,1mm<b≤1.5 t (如1.5t<1,则b=1);当t≤0.5mm时,b=1mm。
L≥t+r+0.5b图 4 工艺槽口示意图1.1.4.弯曲零件未注圆角R要求当图样上未注明弯曲半径时,允许按内弯曲半径R不大于t(t为材料厚)且最小值为0.2。
1.1.5.翻边攻丝质量要求1、普通翻边高度H值和螺纹寿命满足以下要求:图 5 翻边攻丝示意图表 2 普通翻边高度H值和螺纹最少反复打入次数螺纹规格板厚T翻边高度H(公差+0.3~0)内圆角R最大值最少反复打入次数M30.8 1.80.3 121.0 2 30 1.22.2 30 1.5 2.4 30M4 1.0 2.4 30 1.2 2.6 30 1.5 3 30M5 1.2 2.4 30 1.5 2.7 302、薄板连接用的带锥台翻边攻丝该翻边攻丝孔用于薄板连接的场景,实现M3国标沉头螺钉在0.8、1.0mm板材上不凸出板面,使翻边高度H值和螺纹寿命满足以下要求图 6 薄板连接用带锥台翻边攻丝孔结构示意图表 3 薄板连接用带锥台翻边攻丝孔翻边高度H值和螺纹最少反复打入次数螺纹规格材料板厚T 翻边后底孔内径D1(参考)翻边高度H(公差+0.2~0)沉头孔大径D3(公差±0.1)最少反复打入次数M3 钢<0.8 不允许 M3 翻边攻丝0.8 Φ2.5 2.5 Φ4.5121.0 Φ2.5 2.5 Φ4.530 ≥1.2不需采用带锥台翻边攻丝,即可实现沉头螺钉无凸出3、翻边后孔边不允许有裂纹、口部不齐等缺陷。
不需采用带锥台翻边攻丝,即可实现沉头螺钉无凸出1.1.6.自铆质量要求1、自铆工艺参数参照以下表和图:表 4 自铆参数表序号被铆板厚T2 翻边孔高度h1 0.6 1.12 0.8 1.23 1 1.44 1.2 1.6图 7 自铆连接示意图2、铆合孔内不允许有铁屑存在,自铆处不允许出现铆偏(肉眼可视),裂纹数不超过3条。
3、板厚T2≥0.8mm时,铆合后表面不允许凸起;被铆板厚T2<0.8mm时,被铆板不沉孔,允许表面凸起,凸起高度不超过T1。
4、铆合后两板之间能承受拉力符合下表要求。
表 5 自铆连接点最小承力表T1+T2 0.8+0.8及以下0.8+1.0 1.0+1.0 1.0+1.2及以上拉力≥250N ≥350N ≥450N ≥600N1.1.7.零件表面的外观要求按相应产品(机箱、机柜、拉手条等)质量要求。
1.2.钣金冲压件毛刺的要求1.2.1.毛刺的高度定义毛刺高度是指冲裁后冲件断面边缘锋利的凸起的高度(h),详见0。