电极焙烧及相互要点
负极焙烧工艺

负极焙烧工艺全文共四篇示例,供读者参考第一篇示例:负极焙烧工艺是一种重要的电池制造工艺,主要用于生产锂离子电池的负极材料。
在电池领域,负极材料是电池性能的关键之一,其制备工艺的优劣将直接影响到电池的性能和循环寿命。
负极焙烧工艺是负极材料制备中的一个重要环节,通过高温烘烤来处理活性负极材料,使其达到理想的结构和性能,从而提高电池的功率密度和循环性能。
一般来说,负极焙烧工艺包括原料处理、混合、成型、烘烤和焙烧等步骤。
首先是原料处理,通常使用的原料主要包括石墨、导电剂、粘结剂等。
这些原料经过混合、成型后形成负极片,然后进行烘烤,在低温下去除水分和挥发物,以保证负极片不在高温下发生爆炸或变形。
最后是焙烧,通过在高温下处理负极片,使其结构更加稳定,从而提高电池的性能。
负极焙烧工艺的关键在于控制好烘烤和焙烧的温度、时间和氛围。
烘烤和焙烧的温度应根据负极材料的性质和要求来确定,通常在200-600摄氏度之间。
时间的控制也非常重要,短时间内提高温度会导致负极片内部产生应力,从而影响电池的性能。
氛围的控制也不可忽视,负极焙烧通常在惰性气氛下进行,以防止氧化反应发生。
在负极焙烧工艺中,还需要考虑到负极材料的化学稳定性和结构稳定性。
化学稳定性是指负极材料在电池中长期循环过程中不会发生不可逆的化学反应,从而影响电池的寿命和循环性能。
而结构稳定性则是指负极材料在高温下不会结构热变形或发生相变,以保证电池在高温下仍能正常工作。
在负极焙烧工艺中,需要严格控制热处理的温度和时间,以保证负极材料的化学和结构稳定性。
负极焙烧工艺是电池制造中一个至关重要的环节,通过这一工艺可以提高负极材料的性能和循环寿命,从而提高电池的整体性能。
随着科技的不断发展和创新,负极焙烧工艺也在不断地完善和优化,为电池制造业的发展提供了更好的支持和保障。
希望在未来的电池领域中,负极焙烧工艺可以不断地创新和进步,为我们的生活带来更多的便利和可能性。
第二篇示例:负极焙烧工艺是一种重要的电池生产工艺,主要用于生产钴酸锂电池负极材料。
电极糊的使用及生产要点介绍

电极糊的使用及生产要点介绍一、电极糊的使用:电极糊也称自焙电极,它是依靠矿热炉内的热量完成焙烧的,因此,电极的消耗速度与焙烧速度相匹配是电极糊使用的关键,由于,矿热炉技术的发展,逐步向大型化、密闭化方向发展,电极在焙烧过程中由过去开放式炉型获得的较多的传导热和辐射热减少只有为传导热一种,因此电极从炉内获得的热量大幅减少,这就要求提高电极糊的烧结性能来弥补这一不足。
对于电极糊使用厂家来说,最为忌讳的两大问题就是电极软断和硬断,其中软断更为可怕,容易造成事故。
硬断是电极糊烧结后强度不够造成的;软断是电极烧结速度不及消耗速度,下放过快,电极未完全烧结承受不了电极下部的拉伸和侧向冲击,造成断裂。
这两个问题与碳素生产厂家电极糊的性能有直接的关系,也与使用过程中操作有关。
电极糊的生产主要环节只有两个,即配料和混捏。
其中混捏目前基本大同小异,只要混捏设备是正规设备(2000L以上间断式双轴混捏锅)/工艺上把握好混捏温度和时间即可。
而配料的关键是合理的配方;原料的选择、粒度配比,尤其重要的是粘结剂沥青的软化点和粘结剂的使用量。
目前来讲,困扰生产厂家的主要问题是电极糊焙烧速度过慢,因此有的厂家采用降低沥青使用量的方法。
这种办法在一定程度上有效,但是沥青量过低造成电极糊的流动性变差,电极糊不易在电极筒内充实,烧结后密实程度较差易造成硬断,另外一种方法是降低沥青的软化点,提高电极烧结速度,可是沥青软化点也不是可以无限制地降低,因为过低软化点的沥青使得沥青结焦率降低,电极的强度同样要降低,还是要出现硬断现象。
因此电极糊的生产除了要恰如其分地掌握好以上两种手段外,还要通过配方的调整来提高电极的烧结速度,如配方中适当增加导电、传热性能好的石墨质原料,来增加电极从炉内获取的传导热量,以加快焙烧速度,同时设法降低电极的消耗来减少电极下放的速度也可以达到电极消耗与焙烧的匹配。
本人从上世纪八十年代开始研究电极糊的生产技术,为西北金昌公司的电镍炉生产电极糊进行试验,也采取在沥青中添加一定添加剂,同样有一定的效果。
电极焙烧及相关要点

电极焙烧及相关要点电极电极是电石炉的心脏,只有充分地了解电极的组件,才能更好的控制、操作及保护好电极,才能更好的完成生产任务。
电极好比人的身体,电极壳是躯干、电极糊好比营养、那么电流就是精神,只有控制好这三样,才能更好的把电极保护好。
1.电极壳电极壳是自焙电极的关键部分。
电极壳的完好与否直接关系到生产能否安全、连续、稳定运行,是生产过程中必不可少的保障因素。
25500KV A密闭型电石炉自焙电极是以¢1250mm电极壳为铠装,进行电极的自焙。
在电极焙烧过程中,电极壳不仅使电极成型而且还兼起导电作用。
(根据有关资料介绍,由于钢质材料的导电系数大以及在导电过程中的集肤效应,电极壳中通过的电流为总电流的80%左右)因此,电极壳在电石生产中成为不可或缺的器件。
电极壳的构成是有均匀的12片3mm的筋板;12片2mm的弧形板和12跟¢18mm厚的圆钢,经过裁剪、冲压、折弯、缝焊而成。
1.1电极壳的导电特性(1)外壳有效导电截面积约1250×3.14×2=7850㎜2(2)外筋板有效导电截面积大约30×7×12=2520㎜2(3)内筋板有效导电截面积约185×2×12=4440㎜2(4)圆钢有效导电截面积约81×3.14×12=3052㎜2电极壳的有效导电截面积=17862㎜2钢材的电流密度为2.2~2.4A/㎜2故电极壳的有效导电截面积可承受的电流为39296~42869A与《埃肯手册》中所提到的:在电极焙烧初期为防止电极壳烧损,操作电流应控制在40000A以内基本相符。
1.2电极壳的物理特性由于电极壳为钢质材料制成,故其物理特性与钢材相符,据查找相关钢材特性为:密度 7.86g/㎝3;软化点 450~550℃;熔点1535℃;沸点 2750℃1.3电极壳外筋板最大可输入电流接触元件夹紧外筋片面的有效长度约为435㎜,夹电极壳外筋板厚度约为 7㎜电极壳外筋板可输入的最大电流为S=435×7×12=36540㎜2电极壳外筋板可输入的最大电流为I=36540×(2.2~2.4 A/㎜2)=(80388~87700)A常温下。
焙烧电极
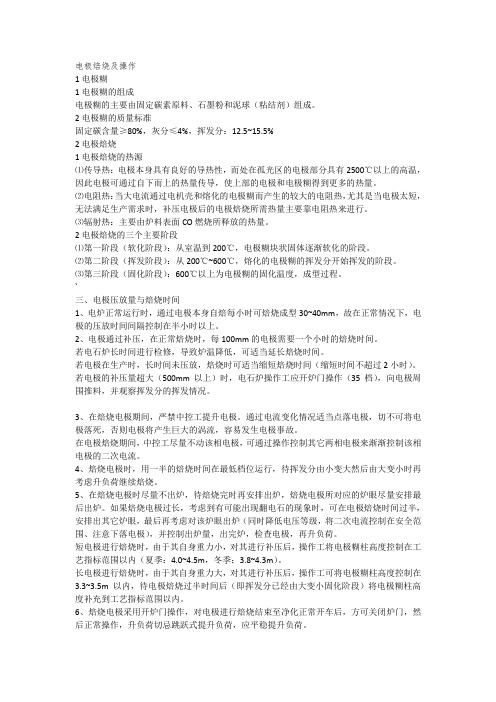
电极焙烧及操作1电极糊1电极糊的组成电极糊的主要由固定碳素原料、石墨粉和泥球(粘结剂)组成。
2电极糊的质量标准固定碳含量≥80%,灰分≤4%,挥发分:12.5~15.5%2电极焙烧1电极焙烧的热源⑴传导热:电极本身具有良好的导热性,而处在孤光区的电极部分具有2500℃以上的高温,因此电极可通过自下而上的热量传导,使上部的电极和电极糊得到更多的热量。
⑵电阻热:当大电流通过电机壳和熔化的电极糊而产生的较大的电阻热,尤其是当电极太短,无法满足生产需求时,补压电极后的电极焙烧所需热量主要靠电阻热来进行。
⑶辐射热:主要由炉料表面CO燃烧所释放的热量。
2电极焙烧的三个主要阶段⑴第一阶段(软化阶段):从室温到200℃,电极糊块状固体逐渐软化的阶段。
⑵第二阶段(挥发阶段):从200℃~600℃,熔化的电极糊的挥发分开始挥发的阶段。
⑶第三阶段(固化阶段):600℃以上为电极糊的固化温度,成型过程。
`三、电极压放量与焙烧时间1、电炉正常运行时,通过电极本身自焙每小时可焙烧成型30~40mm,故在正常情况下,电极的压放时间间隔控制在半小时以上。
2、电极通过补压,在正常焙烧时,每100mm的电极需要一个小时的焙烧时间。
若电石炉长时间进行检修,导致炉温降低,可适当延长焙烧时间。
若电极在生产时,长时间未压放,焙烧时可适当缩短焙烧时间(缩短时间不超过2小时)。
若电极的补压量超大(500mm以上)时,电石炉操作工应开炉门操作(35档),向电极周围推料,并观察挥发分的挥发情况。
3、在焙烧电极期间,严禁中控工提升电极。
通过电流变化情况适当点落电极,切不可将电极落死,否则电极将产生巨大的涡流,容易发生电极事故。
在电极焙烧期间,中控工尽量不动该相电极,可通过操作控制其它两相电极来渐渐控制该相电极的二次电流。
4、焙烧电极时,用一半的焙烧时间在最低档位运行,待挥发分由小变大然后由大变小时再考虑升负荷继续焙烧。
5、在焙烧电极时尽量不出炉,待焙烧完时再安排出炉,焙烧电极所对应的炉眼尽量安排最后出炉。
石墨电极的工艺流程详解

石墨电极的工艺流程详解下面我为大家介绍一下各种工序原料:用于炭素生产的原料有哪些在炭素生产中,通常采用的原料可分为固体炭质原料和粘结剂及浸渍剂两类。
固体炭质原料包括石油焦、沥青焦、冶金焦、无烟煤、天然石墨和石墨碎等;粘结剂和浸渍剂包括煤沥青、煤焦油、蒽油和合成树脂等。
此外生产中还使用一些辅助物料,如石英砂、冶金焦粒和焦粉。
生产一些特种炭和石墨制品(如炭纤维、活性炭、热解炭和热解石墨、玻璃炭)则采用其他一些特殊原料。
煅烧:什么叫煅烧?哪些原料需要煅烧?碳质原料在隔绝空气的条件下进行高温(1200-1500°C)热处理的过程称为煅烧。
煅烧是炭素生产的第一道热处理工序,煅烧使各种炭质原料的结构和物理化学性质发生一系列变化。
无烟煤和石油焦都含有一定数量的挥发份,需要进行煅烧。
沥青焦和冶金焦的成焦温度比较高(1 000°C以上),相当于炭素厂内煅烧炉的温度,可以不再煅烧,只需烘干水分即可。
但如果沥青焦和石油焦在愀烧前混合使用,则应与石油焦一起送入煅烧炉煅烧。
天然石墨和炭黑则不需要进行愀烧。
压型:挤压成型原理是怎样的?挤压过程的本质是在压力下使糊料通过一定形状的横嘴后受到压实和塑性变形而成为具有一定形状和尺寸的毛胚。
挤压成型过程主要是糊料的塑性变形过程。
糊料挤压过程是在料室(或称糊缸)和圆弧式型嘴内进行的。
装入料室内的热糊料在后部主柱塞的推动下。
迫使糊料内的气体不断排除,糊料不断密实,同时糊料向前运动。
当糊料在料室的圆筒部分运动时,糊料可看作稳定流动,各颗粒料层基本上是平行移动的。
当糊料进入到具有圆弧变形的挤压嘴子部位时,紧贴嘴壁的糊料前进中受到较大的摩擦阻力,料层开始弯曲,糊料内部产生精心整理不相同的推进速度,内层糊料推进超前,导致制品沿径向密度不均匀,因此在挤压块内产生内外层流速不同而引起的内应力。
最后糊料进入直线变形部分而被挤出。
焙烧:什么是焙烧?焙烧的目的是什么?焙烧是压型后的生制品在加热炉内的保护介质中,在隔绝空气的条件下,按一定的升温速度进行加热的热处理过程。
电极焙烧三个阶段

电极焙烧三个阶段一、电极焙烧三阶段(1)电极糊融化阶段:电极糊融化的热源主要来自电流通过电极壳产生的电阻热、电流通过电极糊产生的电阻热、电极加热元件的产生的热量、料面辐射热。
此阶段操作时根据电极消耗速度适当压放电极,应严格控制负荷的增长,只要听到轻微的放电声即可。
要防止电流过大产生明弧并刺破铁皮,造成电极糊流出。
操作时间应控制在30-40小时,安全电流应控制在小于5kA,功率应控制在小于2000kW。
(2)电极烧结阶段:此阶段应严格操作,防止电极糊中的挥发份过快挥发。
操作时间应控制在110-120小时,安全电流应控制在小于55kA,功率应控制在小于3500kW。
(3)电极石墨化阶段:此阶段主要是增强自焙电极的导电性能及机械强度。
操作时间应控制在18-26小时,安全电流应控制在小于65kA,功率应控制在小于6000kW。
二、电极焙烧注意事项1、电极焙烧要严格按照《电极焙烧曲线图》进行,同时必须保持三相电极平衡焙烧,特别注意电极焙烧期间禁止上提电极;2、根据气体逸出量的多少并结合经验判断电极的烧结情况,要正确调节电流或添加炭材,控制操作电流,使负载增加速度与电极焙烧程度相适宜;3、当电极位置降至250mm以下时,可人工向启动缸内添加适量的焦炭,防止烧损设备或电流过低;4、依据电极成熟情况适当压放电极长度,但电极压放量不得超过操作规程中规定的相应负荷最大压放量(压放电极主要是为了活动铜瓦,避免被焦油粘住)。
5、变压器档位的调整要依据电流的增加而调整,原则上以满足电极电流平稳并达到焙烧电极所需要的电流值。
变压器调整范围在1-4档,二次电压值114.9V-132.9V,电极电压66.3V-76.7V(空负荷状态值)。
6、在焙烧电极过程中,为了稳定电极和电炉负荷,可以在内外三角区和中心区适当加入焦炭;7、随着电极的不断消耗,可以适当压放电极,但必须保持电极工作端的长度在2300-2500mm之间;8、随着电极的不断消耗和筒内电极糊的软化,应适当加入电极糊,使电极糊柱高保持在3500-4000mm之间(以底环下沿为基准)。
自焙电极操作规程1
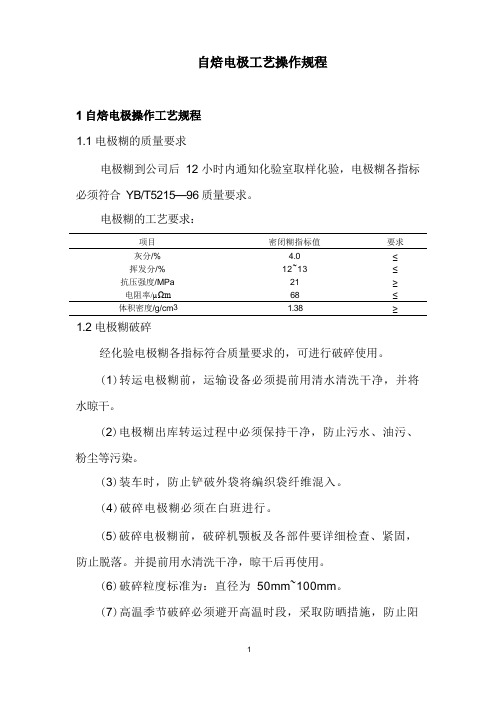
1.1 电极糊的质量要求电极糊到公司后12 小时内通知化验室取样化验,电极糊各指标必须符合YB/T5215—96 质量要求。
电极糊的工艺要求:项目密闭糊指标值要求灰分/% 4.0 ≤挥发分/% 12~13 ≤抗压强度/MPa 21 ≥电阻率/µΩm68 ≤体积密度/g/cm3 1.38 ≥1.2 电极糊破碎经化验电极糊各指标符合质量要求的,可进行破碎使用。
(1)转运电极糊前,运输设备必须提前用清水清洗干净,并将水晾干。
(2)电极糊出库转运过程中必须保持干净,防止污水、油污、粉尘等污染。
(3)装车时,防止铲破外袋将编织袋纤维混入。
(4)破碎电极糊必须在白班进行。
(5)破碎电极糊前,破碎机颚板及各部件要详细检查、紧固,防止脱落。
并提前用水清洗干净,晾干后再使用。
(6)破碎粒度标准为:直径为50mm~100mm。
(7)高温季节破碎必须避开高温时段,采取防晒措施,防止阳光直射温度升高电极糊粘连。
(8)电极糊出库后需及时全部破碎,避免增加转运等环节带来污染。
(9)破碎完毕后,破碎工必须及时将破碎好的电极糊装袋入库备用。
(10) 破碎工在电极糊装袋后应及时用标签标注电极糊批次、破碎时间、破碎人等信息。
(11) 入库前,库管员须对电极糊清洁情况进行详细检查,符合清洁要求后方可按入库程序验收入库。
2.1 电极筒制作(1)设备人员严格按照电极筒设计图纸及制作技术要求制作电极筒。
(2)用于制作电极筒的钢板要清洁,厚度均匀平整,不能有生锈现象。
(3)电极筒制作规格要准确,以便于接长,焊口必须坚固且光洁。
(4)接长电极壳时,必须对准中心线,筋片吻合并要插入一小部份,焊口表面光洁,以防止电极糊下入时卡住,造成悬糊。
(5) 为扩大电极糊和电极壳的接触面积,提高电极的烧结质量,在电极壳内部设有6-7 个筋片。
(6)制作电极壳的具体参数如下:电极壳大圆直 径/mm电极壳小圆直 径/mm钢板厚度/mm 筋片数量/个 筋片高度 /mm 触舌数 量/个触舌尺寸 /mm800-37200--2.2 电极筒安装(1)在电极筒进行装接前,必须认真检查,如发现变形、生锈 应将电极筒进行校圆、除锈后再进行安装(变形严重无法校正、焊缝 脱落或者生锈严重的不能进行安装)。
炭素,碳素,电极,焙烧,煅烧,浸渍,石墨化

标题:探讨炭素材料的制备和特性摘要:炭素作为一种重要的材料,在电化学、材料科学和能源领域具有广泛的应用,其制备方法和性质特点备受关注。
本文将从炭素的定义和特性开始,探讨其制备过程中的焙烧、烧结和浸渍等关键步骤,最终展望其在未来科技发展中的潜在应用。
通过全面评估和深度分析,以期为读者提供更加全面、深刻和灵活的理解。
1. 炭素的定义和特性在自然界中,炭素是一种非常常见且重要的元素,其化学性质和物理性质使得其在材料科学中具有重要地位。
炭素可以以多种形态存在,包括金刚石、石墨、纳米碳管等,每种形态都具有不同的特性和应用领域。
2. 石墨化的制备过程石墨是一种典型的炭素形态,其制备过程主要包括焙烧和烧结两个关键步骤。
在高温下对原料进行焙烧,使得原料中的杂质得以氧化或挥发;接着进行烧结,将焙烧后的物质经过高温处理形成石墨结构。
对石墨材料进行浸渍处理可以改善其电化学性能,提高其在电极中的应用性能。
3. 炭素材料的应用展望基于石墨化炭素的制备过程和特性特点,其在电化学储能、光伏发电、导热材料等方面具有广泛的应用前景。
石墨电极作为锂离子电池、超级电容器等电化学储能装置的关键材料,具有很好的循环稳定性和电化学性能;石墨材料在光伏发电和导热材料领域也发挥重要作用,为可再生能源和高性能材料的发展提供重要支撑。
结论炭素材料作为一种重要的材料,在能源、材料和环境领域具有广泛的应用前景。
其制备过程中的焙烧、烧结和浸渍等关键步骤对其性能具有重要影响,因此对这些步骤的深入了解和优化将有助于提高炭素材料的性能和应用价值。
未来,随着科技的不断进步,炭素材料必将在更多领域展现出其巨大的潜力。
个人观点作为一种重要的功能材料,炭素材料的研究和应用一直备受关注。
石墨化炭素作为其重要形态之一,在能源、材料和电化学等领域具有广泛的应用前景。
对石墨化炭素制备过程和特性的深入理解和研究,将有助于推动其在各个领域的应用和发展。
我对炭素材料的未来发展充满期待,相信其一定会发挥出更多的潜力。
- 1、下载文档前请自行甄别文档内容的完整性,平台不提供额外的编辑、内容补充、找答案等附加服务。
- 2、"仅部分预览"的文档,不可在线预览部分如存在完整性等问题,可反馈申请退款(可完整预览的文档不适用该条件!)。
- 3、如文档侵犯您的权益,请联系客服反馈,我们会尽快为您处理(人工客服工作时间:9:00-18:30)。
电极电极是电石炉的心脏,只有充分地了解电极的组件,才能更好的控制、操作及保护好电极,才能更好的完成生产任务。
电极好比人的身体,电极壳是躯干、电极糊好比营养、那么电流就是精神,只有控制好这三样,才能更好的把电极保护好。
1.电极壳电极壳是自焙电极的关键部分。
电极壳的完好与否直接关系到生产能否安全、连续、稳定运行,是生产过程中必不可少的保障因素。
25500KV A密闭型电石炉自焙电极是以¢1250mm电极壳为铠装,进行电极的自焙。
在电极焙烧过程中,电极壳不仅使电极成型而且还兼起导电作用。
(根据有关资料介绍,由于钢质材料的导电系数大以及在导电过程中的集肤效应,电极壳中通过的电流为总电流的80%左右)因此,电极壳在电石生产中成为不可或缺的器件。
电极壳的构成是有均匀的12片3mm的筋板;12片2mm的弧形板和12跟¢18mm厚的圆钢,经过裁剪、冲压、折弯、缝焊而成。
1.1电极壳的导电特性(1)外壳有效导电截面积约1250×3.14×2=7850㎜2(2)外筋板有效导电截面积大约30×7×12=2520㎜2(3)内筋板有效导电截面积约185×2×12=4440㎜2(4)圆钢有效导电截面积约81×3.14×12=3052㎜2电极壳的有效导电截面积=17862㎜2钢材的电流密度为2.2~2.4A/㎜2故电极壳的有效导电截面积可承受的电流为39296~42869A与《埃肯手册》中所提到的:在电极焙烧初期为防止电极壳烧损,操作电流应控制在40000A以内基本相符。
1.2电极壳的物理特性由于电极壳为钢质材料制成,故其物理特性与钢材相符,据查找相关钢材特性为:密度 7.86g/㎝3;软化点 450~550℃;熔点1535℃;沸点 2750℃1.3电极壳外筋板最大可输入电流接触元件夹紧外筋片面的有效长度约为435㎜,夹电极壳外筋板厚度约为 7㎜电极壳外筋板可输入的最大电流为S=435×7×12=36540㎜2电极壳外筋板可输入的最大电流为I=36540×(2.2~2.4 A/㎜2)=(80388~87700)A常温下。
考虑到电极壳软化温度在450℃,假设,电极壳温度升高全靠电流输入提供热量,不考虑传导热,那么经过计算,电极壳外筋板可输入最大电流为84000~91312A。
电极壳外壳允许通过电流为17270~18840A。
电极壳外筋板输入电流即为操作电流。
1.4导致电极壳烧损的原因有一下几点:1)当电极温度超过电极壳的耐热温度;2)当电极还未完全焙烧好时,通过较大电流;3)电极壳再制造和焊接过程中存在质量问题;4)电极壳与接触元件之间的接触压力变小或元件本体上有孔隙,造成元件与电极壳打弧。
5)电极壳制造所用钢材存在缺陷;6)通过把持器的冷却水量小或阻塞,导致局部温升过高等;7)工艺参数控制不好,造成料面温度过高(即超过700℃)。
2.电极糊电极对电极糊的要求比较高,电极必须具有高度的耐氧化性和导电性,膨胀系数尽量要小,小的电阻系数,小的气孔率,高的机械强度。
由此对电极糊也有了相关的要求。
2.1电极糊质量对电极的影响1)电极糊灰分高,电极糊的粘结力度差,灰分集中的地方,粘结力更差,这个地方消耗快,而且容易机械拉伤造成硬断。
故灰分应保持指标小于等于32)电极糊软化点偏低的话,电极糊烧结后的结焦值低,电极强度也差,易造成电极事故。
3)电极糊电阻率偏高,表示电极糊的石墨化程度低,导电性差,电极抗氧化能力差,焙烧后的电极刚性强,电极也容易折断。
2.2 电极糊粒度的影响电极糊粒度大,在电极筒内加糊时容易造成电极糊架空现象,从而造成电极糊在电极筒内非均匀下沉,非均匀溶化,影响电极糊烧结后强度的均匀性;其次粒度大,电极糊在电极筒内焙烧时候不易溶化,烧结速度慢,使电极糊焙烧速度跟不上电极消耗速度,造成电极事故。
因此一般力度应小于等于75㎜2.3 糊柱高度的影响糊柱高度低,电极糊溶化后沉积不密实,焙烧后电极密度小,导致电极强度低,电极消耗快;糊柱高度过低,容易在电极筒内糊柱表层产生稀糊,当糊柱表层产生稀糊时,硬糊加进去会沉到底层,被稀糊包住,不能很好的熔化,整个糊柱不是均匀地熔化、烧结,影响电极焙烧质量,焙烧不透的电极极易产生电极事故。
根据外省研究的糊柱高度指标一般在4.0米以上。
3.电极烧结电极糊烧结时升温速度一般以10~20℃每小时的速度升温,进入接触元件上部时,电极糊温度为500~600℃,以保证电极正确烧结位置。
温度上移促使电极过烧,温度下移电极呈现欠烧,电极糊烧结时应保持0.05兆帕的压力(相当于4米高的糊柱压力)以保证电极烧结密度,同时电极糊挥发气体压力的增高,有利于缩合反应进行,因此在烧结过程中保持其压力,有利于提高电极的强度,减少事故。
3.1电极烧结过程分为三个阶段:1.温度从室温升到350℃,此阶段固体电极糊熔化,此间的水分和低沸点的成分开始挥发,此时电极糊的电阻为最大。
2.温度从350℃升高到750℃时,熔化的电极糊中的粘合剂开始分解挥发,一般挥发物从电极壳焊缝、电极壳与电极之间缝焊、电极壳上口等地方排出,由于挥发,电极糊变稠,有熔融态变成固态3.温度从750℃到1200℃时,进一步排出挥发物,粘结剂中大量香分子和其它原子团结成焦炭,经一步致密化,之后电极糊烧结完成。
3.2烧结好的电极温度分布:1)料面以上,底环以下最高温度最好控制在1000℃以内2)接触元件以内最高温度应控制在800℃以内3)接触元件以上电极糊温度在350℃左右,向上依次降低。
4.电极消耗电极在电弧的高温下不断气化电离,以维持电弧的稳定燃烧,一部分碳的气体参与了电石生产的反应,其余部分则通过炉料孔隙而逸出,电极的消耗速度与下列因素有关:1)电极的固定碳含量高时消耗慢;2)电极烧结后的气孔率低时消耗慢;3)炉料焦比高、杂质少时消耗慢;4)电极深入料层时消耗慢;5)电极电流密度小时消耗慢5.电极事故原因及处理方法5.1 电极硬断原因如下:1)电极糊所含灰分过高,杂质较多,所含的挥发分较少,造成过早烧结或粘结性差,引起电极硬断;2)热停炉次数多,停电时又没有采取保护措施,造成电极开裂和烧结分层而引起电极硬断;3)电极壳内落入的灰尘较多,送电后没有清理,造成电极分层而引起电极硬断;4)停电时间较长时,电极露出部分没有用炉料保护好,电极受到严重氧化造成电极硬断;5)长时间停电后,送电时提动电极,造成电极机械拉伤而产生硬断;6)电极下放过长,自重产生的拉力过大也会引起电极硬断;7)电极把持筒内风量小,导电鄂板内冷却水量太小,造成电极熔化过度,影响电极的烧结强度,引起电极硬断。
5.2 电极硬断处理方法1)如果断头很长,又没有歪倒在炉内,可把导电鄂板松开,将断头夹进鄂板内,然后急需送电生产,这种方法很少使用;2)如果断头很短时,在料面以下,可以通过加压使电极增长,等电极焙烧好后慢慢把断头压入炉内烧掉;3)如果断头露在料面以上,但又不是很长,就只能放炮炸掉,然后从新加压焙烧。
5.3 电极软断原因如下1)电极糊所含挥发物过多,造成电极不易烧结,强度差而引起软断;2)电极壳铁板太厚或太薄。
太厚了会造成铁壳和电极芯部接触不紧密而引起软断;太薄了会因外力作用电极壳破裂,造成电极铁壳在压放时折叠或漏糊而软断;3)电极铁壳焊接质量不好,引起破裂,导致漏糊软断;4)压放电极时负荷降低得太少,或压放电极后负荷升得过快而引起电极软断,前者出现事故情况较少。
5)压放电极过于频繁,或压放电极时过长而引起软断;6)添加电极糊时,糊块过大,在筋片上搁住而架空,也可能引起软断;5.4 电极软断的处理方法1)发现电极软断停电后,应迅速将电极落下,深入炉内,设法使电极糊不外流,如果可以尽量使电极与断头相连接,弄掉漏下的电极糊硬块,然后送电,低负荷焙烧6小时后,不出意外的话就可以将断头接上,此过程中严禁提升电极。
2)停电后如果没法止住电极糊外流,应迅速用灭火器防止三层半压放油管着火,封掉电极壳顶端出口。
等火熄灭后处理炉内电极糊硬块。
焊接电极壳下端头,重新加糊,送电低负荷焙烧。
6. 总结由以上相关知识,可以总结相关操作如下:1)正常生产时操作电流应控制在84000A~91312A以下2)焙烧电极时操作电流应控制在 42869A 以下,未烧结好时,严禁快速提升负荷,或剧烈提动电极。
3)尽量避免热停电的次数,不需要停电处理的事不停电。
4)电极深入料层,把持器不得低下限运行,防止底环打弧漏水。
5)确保巡检力度,对各元件、底环的循环水量、水温做到心里有数,严禁无水运行。
6)电极压放要少量多次,高负荷运行下也不得60㎜每次每小时的压放,低负荷运行时,根据负荷大小,可以20㎜每次每小时或几小时压一次。
7)压放电极时,每次压放时要注意电极是否正常下压,是否有下滑现象,压放完检查夹紧油缸是否对电极壳有刮伤或刺破。
8)一天准确测量一次电极,当班班长及操作工要做到电极工作长度心里有数。
学会通过听电流声音来判断电极的工作状态9)每次接班测量一次糊柱高度,做到对糊柱心里有数,确保在4米左右;测量糊柱时,应注意电极壳内糊柱是否有架空现象,是否出现稀糊,是否有杂质混入。
10)加糊时,严禁把大量电极糊灰铲入电极壳内,严禁多种电极糊同时加入同一电极壳内。
11)长时间停电,应用混合料包住电极,保护好电极,停电前应将电极尽量下插;用盖板盖住电极壳上端口,防止大量杂物落入。